
7245
.pdf-20-
Очищенные стенки формовочного отсека перед установкой в него арматурного каркаса должны быть смазаны для предотвращения прилипа-
ния к ним твердеющего бетона. Смазку наносят на поверхности формовоч-
ного отсека с помощью "удочек"- или "пистолетов"-распылитетелей. В ка-
честве смазки чаще всего используется смазка ОЭ-2 (обратные эмульсии -
масло в воде), изготавливаемая на основе эмульсолов ЭКС. Такая смазка обеспечивает минимальное сцепление бетона с металлом. Смазка ОЭ-2
включает 20 % эмульсола ЭКС, 53 % раствора извести (1 г оксида кальция на 1 л воды) и 27 % воды. Воду и раствор извести подогревают до 50...60 ° С и интенсивно перемешивают с эмульсолом в механических или гидро-
динамических диспергаторах в течение 10...15 мин. Расход такой смазки со-
ставляет 150...200 г/м2.
Более высокое качество поверхностей достигается при применении смазки ОПЛ-С. Основным ее компонентом является паста ОПЛ (отходы производства ланолина) - смесь природных восков. Смазка включает 15 %
пасты ОПЛ, 5 % эмульсола ЭКС и 80 % воды. Расход смазки 50...100 г/м2.
В последнее время предложена смазка типа "Липор" на основе водо-
растворимых синтетических смол. Перед употреблением смазка подогре-
вается до 30...40 ° С и смешивается с водой в соотношении 1 : 15. Расход такой смазки составляет 100...150 г/м2. Однако с течением времени смазка образует на поверхности форм водонерастворимую пленку и расход смазки существенным образом уменьшается.
Кроме того в производстве могут использоваться и другие виды сма-
зок:
-разогретая до 50 ° С смесь парафина и керосина в соотношении 1: 3; -смесь машинного масла и керосина в соотношении 1 :1 и др.
-21-
1.2.2. Установка арматурных каркасов и образование каналов
скрытой электропроводки
После смазки в формовочные отсеки устанавливаются арматурные каркасы и закладные детали. Точность расположения арматуры опре-
деляет прочность панелей внутренних стен и несущую способность пере-
крытий.
Арматурные каркасы с фиксаторами поставляют к кассетным уста-
новкам в контейнерах, уложенными в той последовательности, в какой они должны поступать в формовочные отсеки. В формовочные отсеки каркасы подаются с помощью мостового крана.
Для образования защитного слоя бетона и фиксации арматурного каркаса в проектном положении в формовочном отсеке применяют, как правило, пластмассовые фиксаторы. Фиксаторы должны быть расположе-
ны в шахматном порядке так, чтобы расстояние между ними было не более
800 мм. В противном случае каркас может сместиться от проектного поло-
жения или даже выйти на поверхность изделия.
Для образования каналов для скрытой электропроводки в формовоч-
ные отсеки устанавливаются круглые арматурные стержни диаметром 14
ммс надетыми на них виниловыми трубками с внутренним диаметром 16
мми наружным 22 мм. Стержни, а затем и трубки извлекают перед распа-
лубкой изделий. На заводе КПД №4 г. Н.Новгорода и ряде других заводов для образования каналов скрытой электропроводки используется неизвле-
каемая гофрированная поливиниловая трубка и распределительные ко-
робки.
После установки во всех формовочных отсеках арматурных каркасов,
закладных деталей и каналообразователей производится сжатие пакета
-22-
формовочных и тепловых отсеков с помощью механизма сборки и разборки и запираются замки. После этого кассетная установка готова к бетони-
рованию.
1.2.3. Формование изделий
Важнейшим элементом формования изделий в кассетах является по-
рядок заполнения формовочных отсеков бетонной смесью и ее виброуп-
лотнение. Известно, что под действием вибрации бетонная смесь ведет се-
бя как вязкая жидкость. Возникающее при этом гидростатическое давление воспринимается стенками формовочного отсека. Если формовочный отсек заполняется бетонной смесью, а соседний остается незаполненным, то в этом случае может деформироваться разделительная стенка. Для исклю-
чения возможных деформаций формовочных отсеков под действием дав-
ления бетонной смеси необходимо, чтобы разница в уровнях бетонной смеси в соседних отсеках не превышала 0,5 м. Если по каким-либо причи-
нам соседний отсек нельзя заполнять бетонной смесью, то в нем должна быть оставлена панель от предыдущего цикла формования.
Бетонная смесь к кассетной установке может подаваться пнев-
мотранспортом, бетононасосами, по ленточным конвейерам или с помо-
щью консольного бетонораздатчика. От гасителя (в случае подачи бетон-
ной смеси пневмотранспортом) через гибкий шланг или специальную теч-
ку (в случае подачи бетонной смеси по ленточным конвейерам или кон-
сольным бетонораздатчиком) смесь поступает в формовочные отсеки. Бе-
тонирование следует вести с одной стороны кассетной формы, подавая бе-
тонную смесь одновременно во все отсеки.
-23-
Следует отметить, что пневмотранспорт бетонной смеси не нашел широкого применения из-за целого ряда недостатков:
- подача бетонной смеси по трубопроводам, как правило, носит пе-
риодичный характер. При перерывах в подаче бетонной смеси более 20. ..40
мин возникает необходимость промывки системы трубопроводов и гасите лей и, как следствие, необходимость в очистке промывочной воды и утили-
зации отходов; - при эксплуатации пневмотранспорта возникает возможность появ-
ления гидравлического удара и разрыва трубопровода с выбросом бетон-
ной смеси в цех.
Уплотняется бетонная смесь вибрацией при включении навесных вибраторов, укрепленных на консолях разделительных стенок.
После укладки и уплотнения бетонной смеси верхнюю открытую по-
верхность изделий заглаживают и укрывают пленкой или брезентом, чтобы предотвратить испарение влаги из бетона, уменьшить усадку и термиче-
ские напряжения при тепловой обработке.
Особенностью формования изделий из горячих бетонных смесей яв-
ляется то, что смесь должна подаваться и укладываться со скоростью не менее, чем 0,5 м3 за 1 мин. Перерывы в формовании не должны превышать 3
мин., так как уложенная и зависшая на арматурных каркасах смесь очень быстро теряет свою подвижность, что создаёт дополнительные трудности при формовании, а в изде лиях могут появиться зоны недоуплотненного бе-
тона.
Как уже отмечалось выше, уплотнение бетонной смеси в кассетах осуществляется, как правило, вибрацией при включении навесных вибра-
торов. Однако из-за жесткой фиксации разделительных листов бортосна-
сткой и упорными конусами интенсивность вибрации оказывается сравни-
тельно низкой. Латвийскими учеными разработан и предложен метод вер-
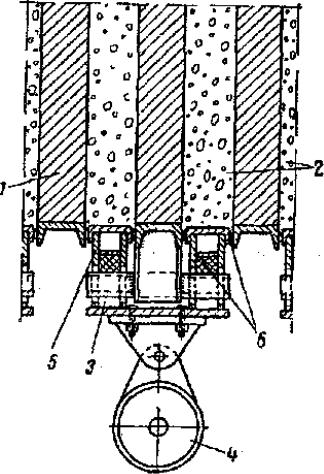
-24-
тикального формования изделий путем послойного уплотнения бетонной смеси колебаниями, которые передаются смеси от вибромеханизма снизу,
через вибрирующее днище формы, в то время как вертикальные ее стенки
(разделительные листы) не вибрируют (рисунок 7). Днище формы, являю-
щееся своеобразным "поршнем" (метод назван авторами вибропорпшевым уплотнением), отделено от стенок и опирается на упругие амортизаторы. К
днищу крепятся вибраторы, возбуждающие вертикально направленные коле-
бания, которые от днища передаются бетонной смеси нижнего слоя и далее,
по мере наращивания слоев, от нижних уплотненных слоев к более рыхлым верхним. Высота слоев бетонирования должна быть при этом 150...200 мм.
Рисунок 7 - Уплотнение бетонной смеси вибропоршневым методом
1 - разделительные стенки кассетной формы; 2 - бетонная смесь; Э - вибрирующие элементы днища (вибропоршни); 4 - маятниковый вибратор; 5 - амортизаторы; 6 - резиновые уплотнители.
-25-
Вследствие изменения массы уплотняемой бетонной смеси при по-
степенной укладке ее в форму слоями по высоте, вместо непрерывного за-
тухания амплитуды колебаний по мере удаления от источника вибрации создаются узлы и пучности амплитуды, что обеспечивает однородность уплотнения по высоте изделий. Проверка этого метода в производст-
венных условиях подтвердила его преимущество по сравнению с вибриро-
ванием при помощи навесных вибраторов на вертикальных разделитель-
ных листах кассетной формы. Однако были выявлены и существенные недостатки этого метода, главным из которых является трудности с обес-
печением герметичности формовочного отсека со стороны "поршня" из-за быстрого выхода из строя резинового уплотнения, что приводит к вытека-
нию цементного теста и образованию зон с пониженной прочностью бето-
на.
Более эффективным является применение комплексного уплотнения,
когда наряду с вибрированием бетонной смеси через разделительные стенки применяют виброуплотнение с помощью глубинных вибраторов, под-
вешенных на гребенке и опускаемых в отсек с помощью мостового крана.
Такое уплотнение позволяет применять смеси с более низкой подвижно-
стью (6...8 см осадки конуса), более экономичных с точки зрения расхода цемента.
1.2.4.Тепловая обработка
Вусловиях почти полностью замкнутого формовочного отсека
(1,5...6,0 % открытой поверхности изделия) создаются наиболее благопри-
ятные условия для твердеющего при повышенной температуре бетона.
Возникающее избыточное давление в порах бетона почти полностью вос-
принимается жесткими стенками отсека. Нарушения структуры бетона при
-26-
этом оказываются минимальными. Именно поэтому в ряде случаев появля-
ется возможность отказаться от предварительной выдержки перед тепловой обработкой, более интенсивно проводить стадию нагрева изделий, что в конечном итоге приводит к существенному сокращению продолжи-
тельности тепловой обработки. Верхнюю, открытую поверхность изделий,
чтобы защитить бетон от высыхания, необходимо укрывать брезентом, ре-
зиной, пленками, колпаками или заливать водой после схватывания цемен-
та.
Режимы тепловой обработки назначаются в соответствии с [16] и
уточняются в ходе освоения выпуска изделий.
Для интенсификации изготовления изделий в кассетных установках следует применять двухэтапную тепловую обработку. Первый этап тепло-
вой обработки при этом проводится в кассете до достижения бетоном из-
делия распалубочной прочности (5,0...7,5 МПа), Затем после распалубки изделия твердеют в камерах дозревания, длительность технологического цикла при этом сокращается на 2...3 часа, а в некоторых случаях и более.
Камеры дозревания могут быть ямного типа с внутренним утеплением.
Они устраиваются напротив каждой кассетной установки.
1.2.5. Выбор и обоснование режима тепловой обработки
От правильного выбора режима тепловой обработки (максимальной температуры изотермической выдержки и продолжительности отдельных стадий тепловой обработки) зависит не только производительность и число тепловых установок, удельные расходы теплоносителя, но и в сильной сте-
пени качество пропариваемых изделий, их долговечность, прочность, мо-
розостойкость. Цикл тепловой обработки принято подразделять на сле-
дующие стадии;

-27- - стадия предварительной "выдержки (τ пв ) ;
-стадия подъема температуры среды в камере до принятой наи-
высшей(τ 1 ) ; -стадия изотермической выдержки, т.е. выдерживание изделий при
наивысшей принятой температуре с подачей тепла в тепловые отсеки
(τ 2 );
-стадия выдерживания изделий без подачи пара в тепловые отсеки кассетной установки (стадия снижения температуры или стадия охлажде-
ния изделий) (τ 3 ) .
Продолжительность тепловой обработки принято выражать суммой длительностей отдельных стадий в часах, т.е.;
(1)
Выбор режима тепловой обработки заключается в установлении не-
обходимой для получения максимальной прочности бетона данного соста-
ва продолжительности отдельных стадий, а также в определении рацио-
нальной температуры изотермической выдержки с учетом минералогиче-
ского состава цемента, его активности; предъявляемых к изделию спе-
циальных требований (повышенная морозостойкость, водонепроницае-
мость и т.д.); вида изделий и его армирования и др.
Предварительная выдержка изделий является, как правило, необ-
ходимым условием получения качественных изделий после тепловой обра-
ботки. Эта выдержка необходима для достижения бетоном некоторой кри-
тической прочности, при которой он способен сопротивляться разру-
шающему воздействию внутрипорового избыточного давления, возни-
кающего на стадии подъема температуры. Следует отметить, что вели-
чина этой прочности не является величиной постоянной и определяется ин-
тенсивностью (скоростью) подъема температуры в тепловом агрегате.

-28-
Время предварительного выдерживания, которое необходимо для достижения такой "критической" прочности колеблется в широких пределах и зависит от многочисленных факторов (активность и вид цемента, В/Ц бе-
тона, температура уложенного в форму бетона и температура окружающей среды, наличие в бетоне добавок - ускорителей твердения и т.д.). По-
вышение активности применяемого цемента, увеличение температуры све-
жеуло-женного бетона и окружающей среды, снижение водоцементного отношения бетона, введение в его состав ускорителей твердения приводят к сокращению длительности предварительного выдерживания. Введение в состав бетона поверхностно-активных веществ (пластификаторов), боль-
шинство из которых в той или иной степени замедляет твердение бетона,
использование пластифицированных и гидрофобных цементов, а также це-
ментов с активными минеральными добавками увеличивает продолжи-
тельность предварительной выдержки. Следует отметить, что нормативной литературой [ 15... 17] предварительная выдержка при тепловой обработке в кассетах не предусматривается.
Отсутствие предварительной выдержки и интенсивный подъем тем-
пературы обусловливается выполнением следующих условий:
-твердение изделий в практически замкнутом формовочном отсеке
(всего 2...5 % открытой поверхности) значительным образом способствует уменьшению деструктивных процессов в бетоне при интенсивном подъеме температуры;
-применение повторной вибрации для восстановления нарушенной,
вследствие протекания деструктивных процессов, структуры твердеющего бетона.
Однако, как свидетельствует практика работы предприятий сборного железобетона, повторная вибрация твердеющего бетона оказывается труд-
но осуществимой из-за быстрого выхода из строя навесных вибраторов.
-29-
Кроме того, даже при применении повторной вибрации прочность бетона в верхней части изделия оказывается ниже прочности бетона в ни-
жележащих слоях бетона, а на поверхности изделий появляются дефекты в виде канавок, образовавшихся при выдавливании воды из пор бетона внутрипоровым давлением. Поэтому в заводской практике для получения качественных изделий тепловая обработка изделий в кассетах сопровожда-
ется 1...2-часовой предварительной выдержкой и увеличением продолжи-
тельности стадии подъема температуры до 2...3 часов.
Отрицательное воздействие на бетон деструктивных процессов, воз-
никающих в основном на стадии подъема температуры, может быть суще-
ственно уменьшено путем рационального ее повышения. Подъем темпера-
туры среды в тепловом отсеке лучше всего осуществлять в прогрессивно возрастающем темпе: в первый час на 10...15 ° С, во второй - на 15...20 ° С, в
третий - на 20...30 ° С. Следует отметить, что время подъема температуры можно значительно сократить при применении для бетонирования предва-
рительно разогретых бетонных смесей.
На стадии изотермической выдержки оптимальной температурой для рядовых портландцементов следует считать 90...95 ° С. Продолжительность изотермического прогрева для достижения требуемой после тепловой об-
работки прочности определяется видом применяемого цемента, его ми-
нералогическим составом, температурой изотермической выдержки и во-
доцементным отношением бетона. Применение быстротвердеющих и акти-
визированных домолом цементов позволяет на 20...40% уменьшить про-
должительность изотермической выдержки.
Продолжительность периода изотермического выдерживания изде-
лий (стадия выдерживания изделия с подачей пара в тепловые отсеки) и
периода снижения температуры (стадия выдерживания изделий без подачи пара в тепловые отсеки) должны назначаться в соответствии с рекомен-