
8007
.pdfПримерный перечень элементов затрат на качество может быть следующим.
1. Затраты на предупредительные мероприятия 1.1. Управление качеством:
–затраты на планирование системы качества;
–затраты на преобразование ожиданий потребителя в технические характеристики.
1.2. Управление процессом:
–затраты на установление средств управления процессом;
–затраты на изучение возможностей процесса;
–затраты на осуществление технической поддержки производственному персоналу в применении планов по качеству.
1.3. Планирование качества другими подразделениями. 1.4. Контрольное и измерительное оборудование:
–разработка и усовершенствование оборудования;
–обслуживание и калибровка оборудования;
–обслуживание и калибровка технической оснастки, приспособлений, шаблонов и пр.
1.5. Обеспечение качества поставок:
–оценка потенциальных поставщиков и материалов;
–техническая подготовка проверок и испытаний закупленных материалов;
–техническая поддержка поставщиков, направленная на достижение ими требуемого качества.
1.6. Аудит системы качества:
–внутренний аудит системы качества;
–аудит системы качества потребителем;
–аудит системы качества третьей стороной (сертификация).
1.7.Программа улучшения качества.
1.8.Обучение вопросам качества.
1.9.Затраты, не учтённые где-либо еще:
-заработная плата секретарей и служащих;
-организационные расходы и т.п.
2. Затраты на контроль
2.1.Проверки и испытания;
2.2.Проверки и испытания поставляемых материалов;
2.3.Материалы для тестирования и проверок;
2.4.Контроль процесса;
2.5.Приём продукции заказчиком:
–затраты на тестирование готовой продукции на производстве для сдачи её заказчику перед поставкой;
–затраты на приёмочные испытания продукции у заказчика до её сдачи. 2.6. Проверка сырья и запасных частей.
2.7. Аудит продукта.
51
3. Внутренние потери
3.1.Отходы (стоимость материалов, которые не отвечают требованиям качества и затраты на их утилизацию и вывоз).
3.2.Переделки и ремонт
3.3.Анализ потерь (затраты на определение причин возникших несоответствий требованиям по качеству)
3.4.Взаимные уступки (затраты на допуск к применению тех материалов, которые не отвечают техническим требованиям)
3.5.Снижение сорта (снижение продажной цены на продукцию, которая не отвечает первоначальным техническим требованиям)
3.6.Отходы и переделки, возникшие по вине поставщиков.
4. Внешние потери
4.1.Продукция, не принятая потребителем:
– затраты на выявление причин отказа;
– затраты на ремонт или замену не принятой продукции.
4.2.Гарантийные обязательства
4.3.Отзыв и модернизация продукции
4.4.Жалобы:
–затраты на исследование причин возникновения жалоб;
–затраты на восстановление удовлетворения потребителя;
–затраты на юридические споры и выплаты компенсаций.
8. Методы управления качеством
8.1. Структурирование функции качества
Метод Структурирования Функции Качества (СФК) состоит в том, что требования потребителя должны «развёртываться» и конкретизироваться
52

поэтапно, начиная с прединвестиционных исследований и заканчивая предпродажной подготовкой.
Данный метод представляет собой технологию проектирования изделий и процессов, позволяющую преобразовывать пожелания потребителя в технические требования к изделиям и параметрам процессов их производства. Технология включает следующие последовательные шаги.
Планирование |
|
Планирование |
|
Проектирование |
|
|
Проектирование |
продукта |
|
компонентов |
|
процесса |
|
|
производства |
|
|
продукта |
|
|
|
|
|
|
|
|
|
|
|
|
|
|
|
Рис. 15. Принципиальная блок-схема метода СФК |
|
1.Планирование продукта. На этом этапе задача состоит в том, чтобы сделать мнение потребителя понятным для инженера-разработчика продукции. Для этого необходимо знать, что требует потребитель от продукта и как этот продукт будет использоваться. После этого определяются требуемые параметры качества.
2.Планирование компонентов продукта. На этом этапе производится ранжирование потребительских требований. Создать продукцию, отвечающую всем требованиям потребителей практически невозможно, поэтому фирма ищет компромисс. Специалисты определяют, какие требования необходимо удовлетворить обязательно, а какими можно поступиться.
3.Проектирование процесса. Разработчики определяют инженерные характеристики продукта. Уточнённый, с чёткими параметрами список характеристик продукта трансформируется в конкретные технологические операции. Определяются основные параметры каждой операции и выбор методов их контроля.
4.Проектирование производства. Разрабатываются производственные инструкции и выбираются инструменты контроля качества производства. Инструкции также должны предусматривать возможность совершенствования работы оператора в зависимости от количества замеров и измерительных инструментов.
Развёртывая качество на начальных этапах жизни продукта в соответствии с нуждами потребителя, удаётся избежать корректировку параметров изделия после его появления на рынке, что повышает эффективность производства.
Фаза планирования продукции состоит из восьми этапов, которые позволяют получить исходные данные для технического задания.
Первый этап. Выяснение и уточнение требований потребителя. Главная задача этапа выяснить у потребителя требуемые им параметры качества. Сформулированные потребителем свободным языком требования затем переводятся на инженерный язык. Например, пожелание потребителя иметь «экономичный автомобиль» можно перевести в форму: «низкая отпускная цена» и «низкая стоимость пробега». Далее их легко перевести в конкретные
53
цифровые показатели: «продажная стоимость – Х руб.», «расход бензина – У
л/100 км».
Параметры качества определяются в процессе выяснения у потребителя двух основных вопросов:
–что требует потребитель от продукта;
–как продукт будет использоваться потребителем.
В результате опроса составляется список потребительских требований к планируемой продукции. Составляется столбец «Потребительские требования» в будущей матрице СФК.
Второй этап – ранжирование потребительских требований. Для этого оценивается рейтинг потребительских требований. Ранжирование нужно для того, чтобы выявить наиболее значимые требования (с наивысшей частотой встречаемости). На таковые и ориентируются в процессе проектирования изделия. Наименее значимыми требованиями можно пренебречь, особенно если они противоречат другим требованиям.
Третий этап – разработка инженерных характеристик. На основе выявленных требований специальная команда разработчиков составляет инженерную характеристику будущего изделия. Требования потребителей к изделию приобретают вид параметров с определёнными значениями.
Четвёртый этап – производится вычисление зависимостей потребительских требований и инженерных характеристик. Для этого строится таблица-матрица, в которой отмечается зависимость требования от инженерных характеристик изделия. Например, требование для автомобиля «тратить минимум бензина» будет зависеть от таких характеристик, как «масса автомобиля», «материал корпуса», «мощность двигателя». После установления зависимости необходимо определить, насколько сильна связь между требованием и характеристикой изделия. После того, как выяснили, сильная, средняя или слабая связь между требованиями и параметрами, становится ясно, какая инженерная характеристика более всего влияет на удовлетворение требований. Характеристики, слабо влияющие на удовлетворение требований и не несущие особой функциональной роли, могут быть убраны из списка.
Пятый этап включает построение «крыши». Метод СФК часто называют «домик качества» именно из-за образа «крыши», в которой простраивается взаимосвязь между самими инженерными характеристиками. В дальнейшем эта зависимость будет учитываться при оптимизации всей системы.
На шестом этапе определяют весовые показатели инженерных характеристик с учётом рейтинга важности потребительских требований, а также зависимости между требованиями и характеристиками. Умножая относительный вес потребительских требований (рейтинг) на числовой показатель связи между потребительскими требованиями и инженерными характеристиками, определённый на четвертом этапе, выявляется относительная важность каждой инженерной характеристики. Суммируя результаты по всему столбцу соответствующей инженерной характеристики, получаем значение цели. Инженерная характеристика с наибольшим значением цели говорит о том, чему следует уделить первоочередное внимание.
54
На седьмом этапе производится учёт технических ограничений. Не все значения инженерных характеристик достижимы по техническим либо экономическим причинам. Поэтому в матрице проставляют экспертные оценки технической реализуемости тех значений инженерных характеристик, которых в наибольшей степени требуют потребители.
Восьмой этап связан с учётом влияния конкурентов. Конкурентов оценивают по тому, насколько полно они способны выполнить каждое из потребительских требований, определённых в первом шаге. По возможностям конкурентов оценивают потенциал компании на рынке.
В результате выполнения всех процедур, указанных в перечне этапов, получают исходные данные для технического задания на проектирование и разработку новой продукции.
8.2. Анализ последствий и причин отказов
Анализ последствий и причин отказов (FMEA-анализ) представляет собой технологию анализа возможностей возникновения дефектов и их влияния на потребителя. FMEA-анализ проводится для разрабатываемых продуктов и процессов с целью снижения риска потребителя от потенциальных дефектов.
Объектами FMEA-анализа процессов могут быть:
–конструкция изделия;
–процесс производства продукции;
–бизнес-процессы;
–процесс эксплуатации изделия.
FMEA-анализ конструкции может производиться как для разрабатываемой, так и для существующей конструкции. В рабочую группу входят представители отделов разработки, планирования производства, сбыта, обеспечения качества, представители опытного производства. Цель анализа – выявление потенциальных дефектов изделия и внесение изменений в конструкцию, позволяющих снизить риски.
FMEA-анализ процесса производства осуществляется службами планирования производства, обеспечения качества с участием соответствующих специализированных отделов изготовителя. Он начинается на стадии технической подготовки производства. Его цель – обеспечение выполнения всех требований по качеству процесса производства и сборки.
FMEA-анализ бизнес-процессов обычно производится в подразделениях, выполняющих данный бизнес-процесс. В этом анализе принимают участие представители службы обеспечения качества и представители подразделений, потребляющих продукт этого бизнес-процесса. Целью является обеспечение качества выполнения бизнес-процесса.
FMEA-анализ процесса эксплуатации изделия обычно проводится в том же составе, что и FMEA-анализ конструкции. Дополнительно в анализе может участвовать представитель потребителя. Целью является формирование требований к конструкции изделия, обеспечивающих безопасность и удовлетворённость потребителя.
55
Выделяют следующие этапы построения FMEA-анализа.
1.Построение моделей объекта анализа.
2.Исследование моделей. В ходе такого исследования определяются потенциальные дефекты, потенциальные причины дефектов, потенциальные последствия дефектов для потребителей и возможности контроля появления дефектов.
3.Экспертный анализ моделей. Мнение экспертов позволяет определить: параметр тяжести последствий для потребления (проставляется по 10-балльной шкале), параметр частоты возникновения дефекта (по 10-балльной шкале, где высший балл составляет более 25 % частоты возникновения дефектов), параметр вероятности необнаружения дефекта (10-балльная шкала), параметр риска потребителя (иерархия рисков).
По выявленным в процессе анализа «узким местам» разрабатываются корректирующие мероприятия.
8.3. Статистические методы
К статистическим методам относятся:
1.Элементарные статистические методы:
– контрольный лист;
– причинно-следственная диаграмма;
– гистограмма;
– диаграмма разброса;
– график разброса;
– стратификация;
– контрольная карта.
2.Промежуточные статистические методы:
– теория выборочных исследований;
– статистический выборочный контроль;
– метод применения сенсорных проверок;
– метод планирования экспериментов.
3.Методы, рассчитанные на инженеров и специалистов в области управления качеством:
– передовые методы расчёта экспериментов;
– многофакторный анализ;
– различные методы исследования операций.
Инструменты математической статистики помогают моделировать процессы и принимать решения, основанные на фактах. В то же время современные статистические методы довольно сложны для широкого практического применения. Международное сообщество приняло за основу семь наиболее простых статистических методов, предложенных учёными Японии, которые позволяют наглядно анализировать процессы.
Контрольные листки являются инструментом первичной регистрации данных. Они применяются как при контроле за качественными, так и при
56
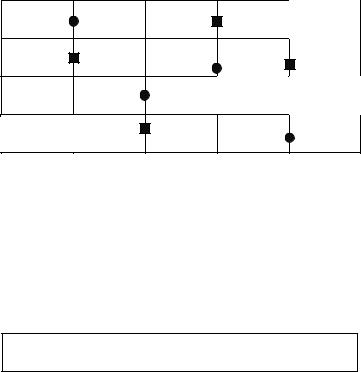
контроле за количественными признаками. Обычно они применяются при фиксировании видов дефектов и их количественных соотношений.
Причинно-следственные диаграммы (диаграмма Исикавы). Диаграммы выявляют возможное воздействие факторов на качество конечного продукта. Эти факторы делятся на несколько групп: «человек», «машина», «материал», «метод», «контроль», «среда». Применительно к решаемой задаче, для компоненты «человек» необходимо определить факторы, связанные с удобством и безопасностью выполнения операций. Если этих факторов недостаточно, то могут возникнуть проблемы с качественным выполнением работы. Для компоненты «машина» выявляют взаимоотношения элементов конструкции анализируемого изделия между собой, связанные с выполнением операции. Выявляются недочёты во взаимодействии элементов, которые могут повлиять на качество. Для компоненты «материал» отмечаются факторы, связанные с отсутствием изменений свойств материалов изделия в процессе выполнения данной операции. Для компоненты «метод» – факторы, связанные с производительностью и точностью выполняемой операции. Компонента «контроль» предполагает изучение факторов, связанных с достоверным распознаванием ошибки процесса выполнения операции. При определении компоненты «среда» рассматривают факторы, связанные с воздействием среды на изделие и изделия на среду. В результате мы получаем наглядную картину из набора факторов, сгруппированных по компонентам, которые так или иначе могут повлиять на качество изделия. Такую диаграмму называют ещё «рыбьей костью» (см. рис. 11).
Диаграммы разброса представляют собой графики в виде координатной сетки или матрицы, где отмечаются взаимосвязи показателей между собой. В результате делается вывод, насколько один показатель влияет на состояние другого показателя (рис. 16, 17).
20
15
10
5
0
0 |
1 |
2 |
3 |
4 |
Рис. 16. Диаграмма разброса: взаимосвязи показателей нет
20
57
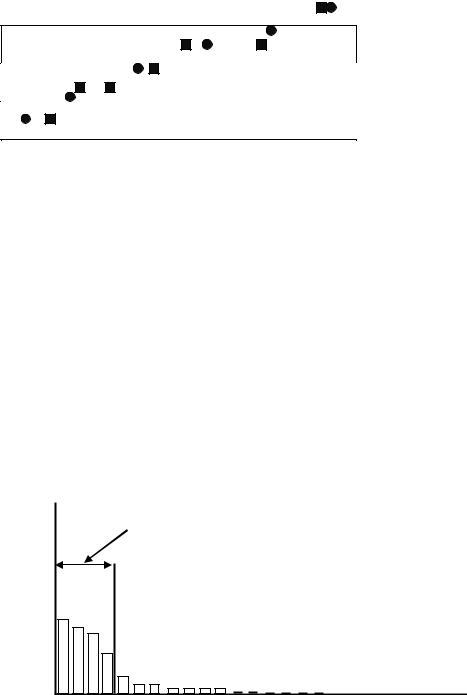
15
10
5
0
Рис. 17. Диаграмма разброса: взаимосвязь показателей имеется
Анализ Паретто. Метод построен на идее, высказанной итальянским экономистом В. Паретто, который показал, что большая часть капитала (80 %) находится в руках незначительного количества людей (20 %). Правило Паретто
– 80 на 20 является универсальным и применяется ко многим областям анализа. Анализ Паретто ранжирует отдельные области причин по значимости и важности и призывает выявить и устранить в первую очередь те причины, которые вызывают наибольшее количество проблем.
Диаграмма Паретто. Анализ Паретто иллюстрируется диаграммой Паретто (рис. 18), на которой по оси абсцисс отложены причины возникновения проблем, а по оси ординат – в количественном выражении сами проблемы, причём как в численном, так и в накопительном процентном выражении.
Количество ошибок
150 |
Область принятия первоочередных мер |
100
50 |
0 |
а б в г д е ж з и к л м н о п р с т у |
Причины возникновения несоответствий |
Рис. 18. Диаграмма Паретто
Стратификация – это процесс сортировки данных согласно некоторым критериям или переменным. Результаты стратификации часто изображают в виде диаграмм и графиков. Массивы данных можно классифицировать в различные группы (страты) с общими характеристиками, называемыми переменными стратификации. Например, возникающие проблемы с уровнем качества можно классифицировать по следующим объектам (стратам): поставщики, операторы, оборудование.
58
Стратификация является методической основой для других инструментов, таких как анализ Паретто или диаграммы рассеивания.
Контрольные карты – специальный вид диаграмм, впервые предложенный У. Шухартом. Они отображают характер изменения показателей качества во времени. Контрольные карты – самый важный метод статистического контроля качества. Управление качеством началось с контрольных карт Шухарта.
В основе метода построения контрольных карт лежит представление о вариабельности рассматриваемого процесса. Вариабельность может иметь разную природу. Если вариабельность появляется только вследствие присущего системе разброса, то можно ожидать, что результаты будут относительно стабильны и предсказуемы. В таких случаях отклонения каких-то показателей от эталонов можно рассматривать как случайные. В такой процесс не стоит вмешиваться.
Но если на естественный разброс накладывается особая вариабельность, обусловленная деятельностью людей, участвующих в процессе, то это является свидетельством того, что необходимо вмешаться и исправить недостатки процесса. Такое вмешательство приведёт к желаемым результатам – повышению качества – наиболее быстрым и дешёвым способом.
Существуют два вида контрольных карт – по качественным и количественным признакам. Контрольные карты по количественным признакам представляют собой сдвоенные карты, одна из которых изображает изменение среднего значения процесса, а другая – разброса процесса.
Контрольные карты по количественным признакам делятся на следующие виды:
–карта для доли дефектных изделий;
–карта для числа дефектных изделий;
–карта для числа дефектов в выборке;
–карта для числа дефектов на одно изделие.
9.Самостоятельная работа студента
9.1.Подготовка реферата
Примерная тематика рефератов:
1.Управление качеством инновационной продукции.
2.Влияние стандартизации, специализации и унификации производства на качество инновационной продукции.
3.Общие подходы к анализу затрат на качество инновационного продукта.
4.Экономические проблемы управления качеством инновационного продукта.
5.Методы контроля качества в процессе производства инновационной
59
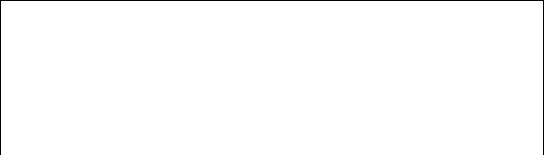
продукции.
6.Система качества как часть системы управления предприятием.
7.Управление процессами подготовки и мотивации персонала в системе менеджмента качества.
8.Показатели качества инновационной продукции и методы их определения.
9.Качество инновационной продукции и стандартизация.
10.Обеспечение качества на этапах жизненного цикла.
11.Макроэкономические |
и |
микроэкономические |
факторы |
конкурентоспособности инновационных продуктов.
Требования к структуре и оформлению реферата.
I. Структура реферата:
Титульный лист Содержание Введение
1.
2.
3.
Заключение (вывод о достижении поставленной цели и задач) Список литературы
II.Оформление реферата.
Список литературы должен быть составлен в соответствии с ГОСТ 7.0.100-2018 «Библиографическая запись. Библиографическое описание. Общие требования и правила составления» и содержать не менее 10 источников.
Общие требования к оформлению текстовой части работы.
Объем работы должен составлять 15 – 20 стр.
Текст работы должен отвечать следующим требованиям (таблица 4)
Таблица 4
Оформление работы
Стиль основного текста
Шрифт |
14, Times New Roman |
Межстрочный интервал |
Полуторный |
Отступ красной строки |
1,25 по линейке MS Word |
(абзац) |
|
Отступы до и после абзаца |
0 |
Выравнивание |
По ширине |
60