
9657
.pdf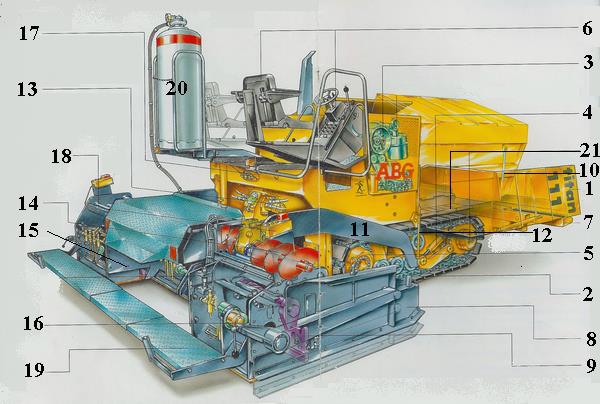
10
Принципиальная схема устройства современного асфальтоукладчика по-
казана на рис. 2.2.
Рис. 2.2. Принципиальная схема устройства асфальтоукладчика: 1 – приемный бункер; 2 – ходовая часть; 3 – двигатель; 4 – нивелировочный гидроцилиндр; 5 – привод ходовой ча-
сти; 6 – центральный пульт управления; 7 – толкающие ролики; 8 – боковой щит (скользящая опалубка); 9 – трамбующий брус; 10 – гидроцилиндр приемного бункера; 11 – тяговый брус (лонжерон); 12- нивелировочная шкала; 13 – приводы питателя и распределительных шнеков; 14 – распределительный шнек; 15 – выглаживающая плита; 16 – привод уплотняющих органов; 17 – блок подключения автоматики нивелирования; 18 – выносной пульт управления; 19 – рабочий настил; 20 – газобалонное оборудования системы обогрева плиты; 21 – цепной питатель
Двигатель является «сердцем» асфальтоукладчика. С его помощью через коробку передач или аксиально-поршневые гидронасосы приводятся в действие ходовая часть и система подачи смеси в шнековую камеру. Дизельные двигате-
ли получили наибольшее распространение по сравнению с другими. Следует отметить, что известны модели укладчиков, на которых установлены трехфаз-
ные электродвигатели. По сути, такие двигатели представляют собой пере-
движные электростанции, отличающиеся высоким коэффициентом полезного действия, долговечностью, простотой эксплуатации и экологичностью. В связи с фактическим отсутствием шума в процессе работы их применение наиболее
11
оправдано в местах жилой застройки или природоохранных зонах. Тем не ме-
нее пока они не нашли широкого распространения.
Основными элементами гидросистемы асфальтоукладчика являются:
гидронасосы, преобразующие энергию крутящего момента от дизельного дви-
гателя в энергию потока жидкости, и гидродвигатели, непосредственно приво-
дящие во вращение ходовую часть, питатели и шнеки укладчика. Дополнитель-
но в систему включены приводы уплотняющих органов и шести гидроцилин-
дров для подъема рабочего органа, поворота стенок бункера и подъема (опус-
кания) концов тяговых брусьев.
Электрооборудование асфальтоукладчика служит для: запуска двигателя машины и контроля режима его работы; контроля температуры рабочей жидко-
сти в баке гидросистемы, сигнализации и освещения; включения в работу трам-
бующего бруса; управления системами автоматики нивелирования, питателей и шнеков, подъемом стенок бункера и рабочего органа, подогрева плиты.
Центральный пульт управления современных асфальтоукладчиков отли-
чается хорошим круговым обзором и повышенным удобством работы операто-
ра. Эргономичное, комфортное и амортизирующее кресло машиниста оборудо-
вано регулирующим устройством, что позволяет ему вместе с пультом переме-
щаться в поперечном направлении к любому краю машины даже за пределы рабочей площадки. Пульт при этом скользит по специальным направляющим
(см. рис. 2.3), а кресло имеет два (три) фиксируемых положения. На главную панель пульта выведены кнопки управления всеми системами и агрегатами укладчика. Управление движением машины осуществляется с помощью руле-
вого колеса или джойстика. Два дополнительных пульта управления автомати-
кой нивелирования вынесены на внешние края выглаживающей плиты, что позволяет персоналу при необходимости оперативно регулировать толщину и ширину укладываемой полосы.
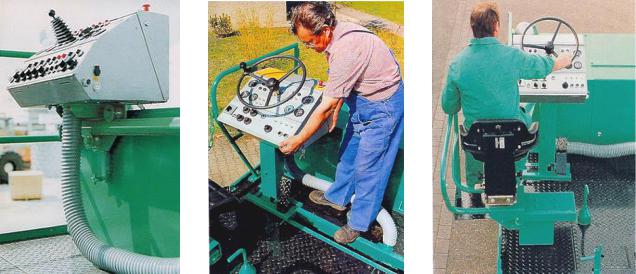
12
Рис. 2.3 Центральный пульт управления
Ниже приводятся главные конструктивно-технологические особенности шасси и рабочих органов современных асфальтоукладчиков.
2.2. Шасси
Шасси обеспечивает передвижение асфальтоукладчика, прием и распре-
деление смеси по ширине укладки. При этом все сборочные единицы шасси располагаются на нижней и верхней рамах, соединенных между собой стойка-
ми. Процесс заводской сборки шасси асфальтоукладчика показан на рис. 2.4. На верхней раме (выше туннеля питателей), как правило, расположены двигатель с муфтой сцепления, пульты управления, гидросистема, электрооборудование,
сиденье оператора, тент (кабина).
Нижняя рама 6 (см. рис. 2.5) является основой машины и представляет собой цельносварную металлоконструкцию, шарнирно опирающуюся на две балки ходовой части 2 и поперечную балку 5. Соединение рамы с балками осу-
ществляется посредством опор в шарнирах 1, 3, 4. Подобная конструкция креп-
ления допускает перемещение ходовой части по вертикали при неровностях ос-
нования с равномерным восприятием рамой нагрузки от агрегатов машины и асфальтобетонной смеси при её выгрузке в бункер автосамосвалами. На ниж-
ней раме размещаются приемный бункер с питателями, распределительные шнеки и трансмиссия на привод хода, шнеков и питателей.
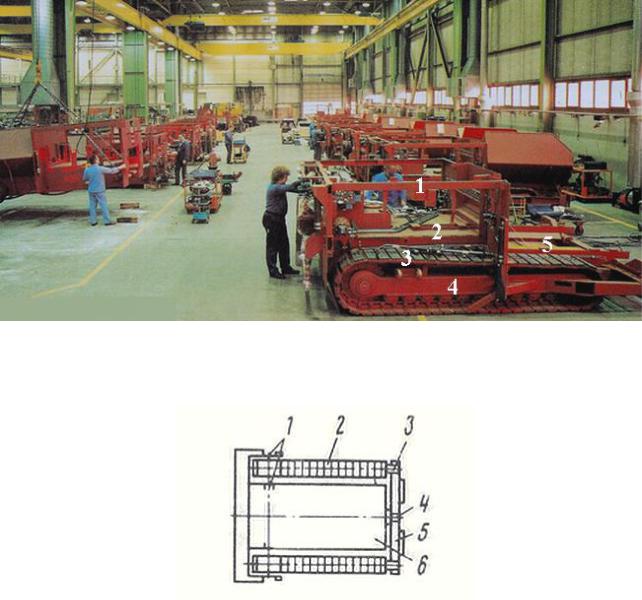
13
Рис. 2.4 Сборка шасси асфальтоукладчика:
1 – несущие элементы верхней рамы; 2 – нижняя рама; 3 – ходовая часть; 4 – балка ходовой части; 5 – скребковый питатель
Рис. 2.5 Схема опирания нижней рамы
Ходовая часть большинства моделей гусеничных асфальтоукладчиков I и II классов является двухопорной, а широкозахватных – четырехопорной с при-
водом на все гусеницы (см. рис. 2.6а). Колесные асфальтоукладчики бывают двух, трех и четырехосные с одной или двумя ведущими осями. Кинематиче-
ская схема ходовой части колесных асфальтоукладчиков приведена на рис.
2.6б. Комбинированные асфальтоукладчики с гусенично-колесным ходом, как правило, легкого типа применяют на работах с частым переходом с одного объ-
екта на другой.

14
1) |
|
2) |
|
|
||
|
|
|
|
|
|
|
|
|
|
|
|
|
|
|
|
|
|
|
|
|
|
|
|
|
|
|
|
3) |
4) |
5) |
7 |
6
Рис. 2.6 Кинематическая схема ходовой части асфальтоукладчиков:
1 – двухопорных; 2 – четырехопорных; 3 – двухосных; 4 – трехосных; 5 – четырехосных; 6 – ведущее колесо; 7 – рулевое колесо
На гусеничных асфальтоукладчиках применяются тележки маятникого типа с независимым гидроприводом. Гусеничная лента выполнена из пластико-
вых или резиновых опорных плит (башмаков) шириной от 189 до 400 мм
(см. рис. 2.7). Маневрирование асфальтоукладчика производится путем измене-
ния скоростей лент. При этом ленты могут двигаться в разных направлениях с различными скоростями. Радиус поворота укладчика задается с пульта управ-
ления. Необходимую разность скоростей или синхронность работы лент при движении по прямой контролирует электронный регулятор.
Управление движением колесных асфальтоукладчиков осуществляется с помощью передних поворотных колес (см. рис. 2.8). Наличие балансирных ры-
чагов, качающихся в продольном направлении и подвешенных к балансирной балке, качающейся в поперечном направлении, позволяют оставаться рулевым колесам всегда в полном контакте с основанием, даже при наличии на нем не-
ровностей. Сцепление ведущих колес с основанием обеспечивается за счет большой опорной площади шин с глубоким протектором и дополнительным оборудованием заднего моста блокируемым дифференциалом. Система автома-
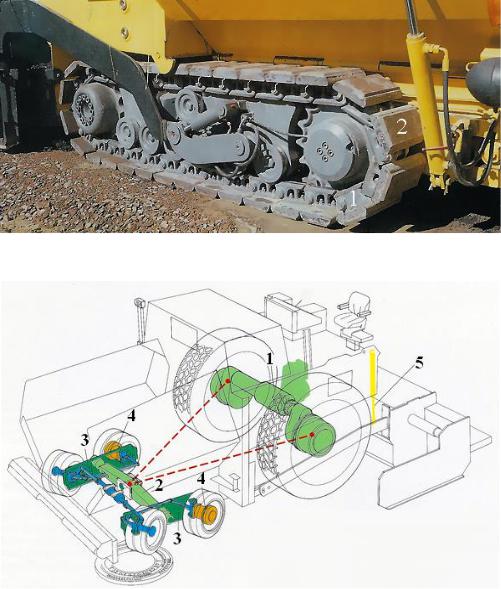
15
тически позволяет плавно регулировать разгон до заданной скорости, сохраняя
её затем постоянной при различных нагрузках.
Рис. 2.7 Ходовая часть гусеничных асфальтоукладчиков: 1 – гусеничная лента; 2 – опорный башмак
Рис. 2.8 Схема рулевого управления колесного асфальтоукладчика:
1 – дифференциал ведущего моста; 2 – поперечная балансирная балка; 3 – качающийся балансирный рычаг; 4 – рулевой механизм; 5 - гидроподъемник
Приемный бункер служит для выгрузки смеси из автосамосвала. Емкость приемного бункера в зависимости от модификации асфальтоукладчика может меняться от 1,5 до 17,5 тонн. Бункер образован (см. рис. 2.9) левой и правой бо-
ковинами, складывающимися вовнутрь при помощи гидроцилиндров, задней стенки, функцию которой выполняет передняя часть нижней рамы и дном из листовой стали. По листам, закрепленным на раме, смесь перемещается из пе-
редней в заднюю часть машины. Поворотные боковины позволяют увеличить
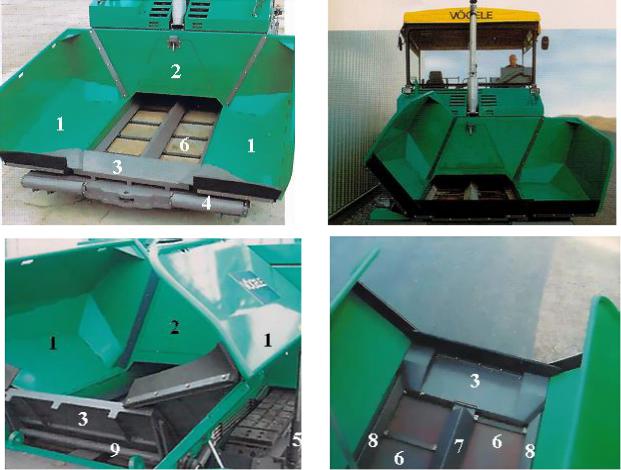
16
вместимость бункера без увеличения ширины питателей. При этом смесь, нахо-
дящаяся у краев бункера, скатывается к центру под действием собственного ве-
са при внутреннем наклоне боковин. В передней части бункера поверх боковин установлен дополнительный щит, который также поворачивается (складывает-
ся) внутрь за счет штанги, шарнирно закрепленной на внешней грани боковин.
На некоторых модификациях асфальтоукладчиков вместо переднего щита ис-
пользуют открылки, установленные на боковинах. Положение автосамосвала относительно укладчика контролируется с помощью качающихся передних толкающих роликов. Применяя специальные зацепы, можно с помощью гид-
равлики прочно захватывать обода колес самосвала и удерживать его во время движения укладчика.
Рис. 2.9 Приемный бункер асфальтоукладчика:
1 – боковины; 2 – задняя стенка; 3 – дополнительный передний щит; 4 – толкающие ролики; 5 – гидроцилиндр; 6 – скребковый конвейер-питатель; 7 – средняя направляющая; 8 – левый (правый) защитный кожух; 9 – штанга
17
На дне бункера расположены цепные скребковые конвейеры-питатели,
разделенные между собой средней направляющей. Направляющая, как и за-
щитный кожух, предохраняют приводную часть питателя от попадания на неё смеси. Оба конвейера работают раздельно (независимо) по принципу погру-
женных скребков. При работе скребки скользят по поверхности стальных ли-
стов, перемещая смесь из бункера в шнековую камеру. Конвейерная лента со-
стоит из двух (одной) тяговых цепей. На отдельных моделях асфальтоукладчи-
ков цепная передача приводит в действие пластинчатый конвейер из нихарда.
Производительность питателя может регулироваться заслонками шиберного типа (см. рис. 2.10) вручную либо автоматически с помощью датчиков лопаст-
ного типа, установленных в задней части конвейера.
На современных асфальтоукладчиках каждый питатель (см. рис. 2.11),
как впрочем, и распределительные шнеки, оснащены отдельными гидростати-
ческими приводами, что позволяет подавать смесь в соответствии с требуемой производительностью укладки. Это возможно даже когда с одной стороны необходимо уложить больше материала из-за разной толщины слоя или асим-
метричного уширения рабочего органа. Каждый привод включает гидронасос,
гидродвигатель, понижающий редуктор и цепную передачу, объединенные в общий замкнутый контур. Работа отдельных агрегатов изменяется пропорцио-
нально отклонению запаса (уровня) смеси в шнековой камере от заданного зна-
чения. При этом фактическое количество смеси при подаче питателями (шне-
ками) определяется расположенными над ними щупами - лопастными датчика-
ми контактного типа. Любое изменение их положения потенциометрами преоб-
разуется в импульсы управления работой питателей и (или) шнеков.
Установка в режим работы «Автомат» или «Ручное» питателей и шнеков производится с помощью соответствующих переключателей для левых и пра-
вых органов машины, расположенных на пульте управления. В автоматическом режиме работа ведется по сигналам датчиков уровня материалов 7 рис. 2.11,
установленных по концам обоих шнеков. При наращивании уширителей шне-
ков датчики могут перемещаться на трубчатых опорах. Датчики работают в
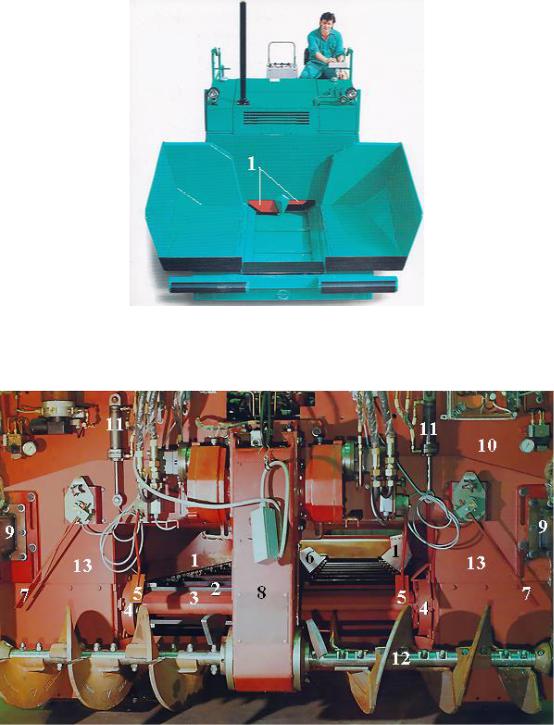
18
двухконтактном режиме. Их конструкция позволяет регулировать положение
щупа и его поворота вокруг оси в зависимости от толщины укладываемого
слоя.
Рис. 2.10 Регулировка подачи смеси с помощью шиберных заслонок: 1 – шиберные заслонки
Рис. 2.11 Туннель скребкового питателя (вид со стороны шнековой камеры):
1 – защитный кожух; 2 – скребок; 3 – лента питателя; 4 – привод питателя; 5, 7 – лопастные датчики уровня смеси на ленте питателя и в шнековой камере соответственно; 6 –средняя направляюшая; 8 – привод шнеков; 9 – кронштейн крепления шнека; 10 – рама асфальтоукладчика; 11 – гидроцилиндр подъема шнеков; 12 – распределительный шнек; 13 – передний щит шнековой камеры
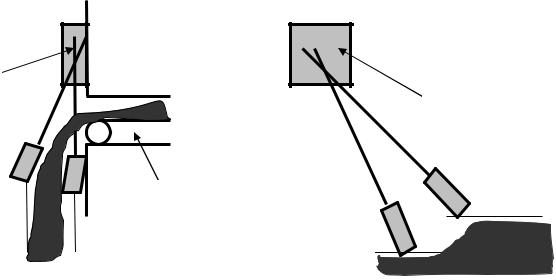
19
Правильная настройка датчиков предупреждает переполнение шнековой камеры, предохраняя износ шнеков, и исключает образование раковин в покры-
тии из-за недостатка материала перед выглаживающей плитой. При пустой шнековой камере щуп под собственным весом находится в крайнем нижнем положении, замыкая контакты включения гидроприводов питателей и шнеков
(см. рис. 2.12). При заполнении шнековой камеры, когда смесь переместит щуп в крайнее верхнее положение, управляющая система обесточивается, останав-
ливая работу гидропривода того или иного контура (обоих сразу). Нормальной считается работа, при которой щуп занимает промежуточное положение между крайними заданными точками.
1 |
1 |
|
|
2 |
MAX |
|
|
|
|
|
MIN |
MAX |
MIN |
|
Рис. 2.12 Регулировка подачи смеси с помощью лопастных датчиков:
1 – лопастной датчик; 2 - скребковый конвейер; min, max- уровень смеси
Другим вариантом контроля процесса является применение ультразвуко-
вых или сенсорных датчиков (см. рис. 2.13). Они отличаются высокой точно-
стью измерений, простотой регулировки заданной толщины (количества) укла-
дываемого (подаваемого) материала без соприкосновения с ним.
Для исключения прессования смеси при её транспортировке в шнековую камеру ленточным питателям придается дополнительный наклон назад. Ско-
рость ленты регулируется плавно в интервале 0 - 24 м/мин. Дальнейшее рас-
пределение смеси по ширине укладки ведется при помощи двух независимых
винтовых конвейеров или шнеков. Каждая секция имеет свою навивку спирали -