
Оперативно-производственное планирование
..pdf
Время опережения запуска партии деталей в заготовительный цех относительно их выпуска из механического цеха составит:
θ заг.зап = Тц.заг +θ заг.вып = 4 +11= 15 дн.
Пример 2. Длительность производственного цикла механической обработки составляет 10 рабочих дней, выполнения сборочных работ – 12 рабочих дней. Запас деталей перед сборкой – 24 комплекта, дневная потребность сборки – 6 комплектов в день.
Время опережения запуска на сборку
θ сб.зап =Ти.сб = 12 дн.
Время опережения выпуска из механообрабатывающего цеха
θ мех.вып =Тц.сб +θ рез =12+ 24 / 6 = 16 дн.
Время опережения запуска в механообрабатывающий
цех
θ мех.зап =Тц.мех +θ мех.вып = 10 +16 = 26 дн.
Пример 31. Цикл изготовления заготовок в заготовительном цехе Тз.ц = 7 дн., изготовления деталей в механическом цехе Тм.ц = 11 дн., сборки изделий в сборочном цехе Тс.ц = 10 дн. Резервное время между обработкой в цехах
Тр = 1 дн.
Опережение по выпуску из механического цеха
Тмо..цв =Тс.ц +Тр =10 + 1 =11 дн.
Опережение по запуску в механический цех
Тмо..цз =Тмо..цв +Тм.ц =11+ 11= 22 дн.
1 Экономика фирмы: учеб. для бакалавров / под ред. В.Я. Горфинкеля. – М.:
Юрайт, 2012. – С. 202–203.
121
Опережение по выпуску из заготовительного цеха
Тзо..цв =Тмо..цз +Тр = 22 + 1 = 23 дн.
Опережение по запуску в заготовительный цех
Тзо..цз =Тзо..цв +Тз.ц = 23 + 7 = 30 дн.
Рассмотренные календарно-плановые нормативы используются при составлении календарных планов-графиков производства продукции (работ, услуг).
3.3.Оперативно календарное планирование
вмассовом производстве
Массовое производство – производство, характеризуемое узкой номенклатурой и большим объёмом выпуска изделий, непрерывно изготовляемых или ремонтируемых продолжительное время, в течение которого на большинстве рабочих мест выполняется одна рабочая операция.
Для массового производства характерно:
−расположение рабочих мест по ходу технологического про-
цесса;
−специализация рабочих мест на выполнении одной из операций иоснащение ихспециальной высокопроизводительной оснасткой;
−осуществление тщательной технической подготовки производства;
−передача предметов труда с операции на операцию поштучно или мелкими партиями сразу же после окончания обработки;
−создание поточных линий при производстве отдельных предметов;
−ритмичность выпуска;
−синхронность операций;
−установление точных нормативов всех затрат;
−относительновысокие технико-экономические показатели.
122
Вмассовом производстве применяется подетальная система планирования. Планово-учётной единицей для предприятия в целом
ивыпускающих цехов в этой системе ОКП является изделие, а для остальных цехов – деталь, сборочная единица (узел).
Планирование в подетальной системе ОКП основывается на следующих календарно-плановых нормативах: такт и темп производства для каждой поточной линии, нормативный уровень внутрилинейных и межлинейных заделов.
Основным документом выступает план-график работы поточных линий.
С помощью задаваемого такта поточной линии методом выравнивания производительности и приведения к запланированному темпу выпуска готовой продукции достигается слаженный ход работы всех звеньев производственного процесса.
С темпом выпуска продукции в конечном цехе согласовываются темпы остальных цехов-поставщиков полуфабрикатов. Ритмичная работа находит отражение в ежедневном выпуске одинакового или равномерно нарастающего количества продукции в соответствии со сменным или часовым графиком.
Впрямоточном массовом и крупносерийном производстве штучное время выполнения операций на различных рабочих местах неодинаково и некратно. Кроме того, оно некратно такту поточной линии. По разным техническим причинам штучное время не удаётся синхронизировать, т.е. сделать равным или кратным на разных рабочих местах. Вследствие этого возникают простои оборудования
ирабочих. Чтобы их ликвидировать на рабочих местах, создаются межоперационные заделы, определяющие величину НЗП.
Заделы делятся на внутрилинейные, обеспечивающие бесперебойную загрузку рабочих мест поточной линии, и межлинейные, обеспечивающие начальную операцию смежных поточных линий.
По назначению заделы подразделяются на технологические, транспортные, оборотные и страховые.
Под технологическим заделом (Зт) понимают детали или сборочные единицы, находящиеся в процессе непосредственной обра-
123
ботки или сборки на рабочих местах, а также детали, подвергающиеся технологическому контролю на специальных рабочих местах
ОТК (nд.кон):
Зт = Кп nд + nд.кон , |
(3.26) |
где Кп – количество рабочих мест на поточной линии, занятых выполнением данной технологической операции; nд – число деталей, одновременно обрабатываемых на одном рабочем месте.
Пример. На поточной линии организовано 4 рабочих места по сборке узла из деталей, на одном рабочем месте одновременно используются 20 дет., на специализированных рабочих местах подвергаются контролю 5 дет.
Величина технологического задела
Зт = 4 20 + 5 = 85 дет.
Экономическое значение технологического задела в том, что если на начало рабочей смены или в любой час работы поточной линии на каждом рабочем месте есть расчётное число единиц объектов, прошедших обработку по предшествующим операциям, то, значит, есть условия для работы рабочих и оборудования без простоев, выполнения планового сменного задания, обеспечения расчётной эффективности поточной линии. Если же на начало смены на любом рабочем месте отсутствует деталь, то по очереди обязательно будут простои рабочих и оборудования на всех последующих операциях после «пустого» рабочего места, равные такту поточной линии, умноженному на количество отсутствующих деталей. В результате снизится эффективность работы поточной линии.
Транспортный внутрилинейный задел представляет собой об-
щее число деталей, постоянно находящихся в процессе перемещения между рабочими местами поточной линии. Величина транспортного задела поточной линии (Зтр) определяется по формуле
З |
|
= |
Дк |
n , |
(3.27) |
|
Шк |
||||
|
тр |
|
д |
|
124

где Дк – длина поточной линии (длина конвейера); Шк – расстояние между двумя обрабатываемыми друг за другом деталями на конвейере (шаг конвейера); nд – количество деталей, одновременно передаваемых с операции на операцию.
Пример. Длина поточной линии равна 20 м, шаг поточной линии составляет 2 м, с операции на операцию одновременно передаётся 10 дет.
Величина транспортного задела
Зтр = Дк П= 20 10 =100 дет.
Шк 2
Экономическое значение этого задела совпадает со значением задела технологического. При наличии в течение смены на рабочей части конвейера расчётного числа деталей (сборочных единиц), прошедших обработку по предшествующим операциям, обеспечивается работа людей и оборудования без простоев, так как через строго определённые промежутки времени, равные такту поточной линии, к каждому рабочему месту будет своевременно подаваться деталь. Если же на каком-то транспортном устройстве конвейера не будет детали, то к определённому рабочему месту поточной линии подойдёт «пустое» транспортное устройство и это рабочее место и все последующие будут по очереди простаивать в течение времени, равного такту потока.
Транспортный межлинейный задел необходим для своевре-
менной подачи деталей с одной поточной линии на следующую или из цеха-изготовителя в цех-потребитель и представляет собой запас деталей, находящийся на транспортном устройстве, связывающем две смежные поточные линии или склад с поточной линией.
Межцеховой транспортный задел (Zт) рассчитывают по форму-
лам:
− при связи линий непрерывным транспортом
Z |
т |
= |
L nд kз |
, |
(3.28) |
|
l |
||||||
|
|
|
|
|||
|
|
|
|
|
125
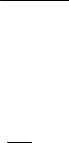
где L – длина транспортного устройства, м; nд – количество агрегатов, деталей, расположенных между двумя сборочными зонами; kз – коэффициент загрузки транспорта; l – расстояние между центрами двух сборочных зон;
− при связи линий транспортом периодического действия
Zт = |
rт |
≤ Q, |
(3.29) |
|
rп |
||||
|
|
|
где rт – периодичность транспортных рейсов между линиями; rп – такт подающей линии; Q – грузоподъёмность транспортного устройства, шт.
Пример 1. Длина непрерывного транспортного устройства равна 100 м, расстояние между центрами двух сборочных зон составляет 5 м, между двумя сборочными зонами расположено два агрегата, коэффициент загрузки транспорта равен 0,95.
Величина межцехового транспортного задела
Zт = 100 2 0,95 = 38 шт. 5
Пример 2. Периодичность транспортных рейсов между цехом по выпуску цепей для бензопил и сборочным цехом – 8 ч. Цепи доставляются в ящиках по 50 шт., максимальная грузоподъёмность транспортного средства составляет 5 ящиков. Такт подающей линии – 1 цепь в 3 мин.
Величина межцехового транспортного задела
Zт = 480 = 160 ≤ 5 50, 3
Zт = 160 ≤ 250.
Межоперационный оборотный задел – это количество деталей,
которое необходимо для обеспечения бесперебойной работы смежных рабочих мест, имеющих различную производительность. Он создаётся в том случае, если смежные операции поточной линии не синхронизированы, причём продолжительность одной из этих операций обязательно больше такта поточной линии. В таких случаях к
126

началу смены (или рабочего дня) после рабочего места поточной линии, где продолжительность операции больше такта, должен находиться запас деталей, прошедших обработку по всем предшествующим операциям, в том числе и по более трудоёмкой. Оборотный задел определяется между двумя смежными операциями. Его величина в течение смены непрерывно меняется от наивысшего своего значения в начале смены до нуля. Оборотный задел должен постоянно пополняться перед каждой сменой или рабочим днём. Можно создать межоперационный оборотный задел на несколько рабочих дней вперёд, однако это приведёт к увеличению оборотных средств в НЗП и замедлению их оборачиваемости.
Межоперационный оборотный задел (Зоб) определяется следующим образом:
Зоб = |
Р |
(1 |
− |
tкор |
) , |
(3.30) |
|
r |
tдл |
||||||
|
|
|
|
|
где Р – регламентированный период, за который определяют оборотные заделы (например, смена), мин; r – продолжительность такта поточной линии, мин; tкор – продолжительность короткой операции между двумя смежными, мин; tдл – продолжительность длинной операции между двумя смежными, мин.
Пример. Необходимо определить сменный межоперационный оборотный задел между двумя несинхронизированными смежными операциями поточной линии. Продолжительность смены 8 ч. Продолжительность такта поточной линии – 10 мин. Продолжительность короткой операции между двумя смежными составляет 5 мин, длинной – 25 мин.
Межоперационный оборотный задел
Зоб = 8 60 (1− 5 ) = 38 шт. 10 25
Межлинейный оборотный (складской) задел необходим при различной сменности работы смежных линий и при подаче деталей на поточную линию с серийного участка.
127
При различной сменности работы смежных линий межлинейный задел (Zоб.м) рассчитывается по формуле
Zоб.м = nсм (sб − sм ) , |
(3.31) |
где nсм – сменная потребность в деталях поточной линии, работающей большее число смен; sб – сменность линии, работающей большее число смен; sм – сменность линии, работающей меньшее число смен.
Пример. Необходимо определить межлинейный оборотный (складской) задел между двумя смежными поточными линиями, из которых одна работает в две смены, а вторая – в три смены. Сменная потребность в деталях поточной линии, работающей в три смены, составляет 1000 шт.
Межлинейный оборотный (складской) задел
Zоб.м =1000 (3 − 2) = 1000 шт.
При подаче деталей на поточную линию с серийного участка межлинейный оборотный (складской) задел определяется по формуле
Zоб.м = R nсм , |
(3.32) |
где R – период времени между подачей двух партий с серийного участка в сменах.
Пример. Необходимо определить межлинейный оборотный (складской) задел при подаче деталей с участка покраски на сборочный конвейер. Сменная потребность в деталях поточной линии составляет 1000 шт., с участка покраски детали передаются 2 раза в смену.
Межлинейный оборотный (складской) задел
Zоб.м = 0,5 1000 = 500 шт.
Резервным (страховым) заделом называется количество дета-
лей, хранящихся в запасе, необходимом для обеспечения непрерывности работы поточной линии в случае остановки процесса произ-
128

водства вследствие поломки оборудования или в случае несвоевременной подачи комплектующих полуфабрикатов.
Эти заделы в условиях поточного производства крайне важны, так как их отсутствие может привести к нарушению непрерывной, ритмичной работы многих рабочих мест потока. Однако во избежание необоснованного роста НЗП и замедления оборачиваемости оборотных средств страховые заделы создаются не по каждой операции, а только на наиболее ответственных участках поточных линий. Необходимость формирования страхового задела определяют исходя из опыта работы поточной линии.
Резервный (страховой) задел (Зстр) определяется по формуле
Зстр = |
Тпер |
, |
(3.33) |
|
|||
|
r |
|
где Тпер – время возможного перерыва в работе на данной операции (устанавливается опытным путём); r – такт поточной линии.
Пример. Время возможного перерыва в работе на конечной операции сборочного конвейера, установленное по опыту работы прошлых лет, составляет 0,5 смены. Продолжительность смены – 8 ч. Такт конвейера равен 20 мин. Резервный (страховой) задел по числу сборочных узлов составит:
Зстр = 0,5 8 60 =12 узлов. 20
Межлинейный страховой (резервный) задел создается между поточными линиями на случай увеличения их производительности или при задержке подачи деталей. На практике величина этого задела обычно устанавливается следующим образом: для задела между линиями внутри цеха – до 1/2 смены, между цехами – 1 смена и более.
После расчёта основных показателей поточной линии составляется план-график работы линии, который называется стандартпланом. Для однопредметных прерывных поточных линий разраба-
129

тывается пооперационный стандарт-план, для многопредметных –
подетальный стандарт-план.
Подетальные планы производства, доводимые до цехов, участков и рабочих мест, служат связующим звеном между оперативнокалендарным и технико-экономическим планированием и являются основой для текущей подготовки производства и расчётов потребности в материальных и трудовых ресурсах. Методом решения задач линейного программирования стандарт-план может быть оптимизирован по критерию минимизации суммарных величин переходящих заделов на линии. Для чёткого соблюдения такта (ритма) стандарт-плана поточной линии составляется сменное задание в почасовом разрезе – часовой график.
Комплекс задач ОКП массового производства включает в себя ряд технико-экономических расчётов1:
1.Определение потребности в деталях и сборочных единицах на товарный выпуск в натуральном выражении по предприятию на основе производственной программы предприятия и конструкторских спецификаций.
2.Планирование изменения заделов деталей, сборочных единиц по предприятию и цехам на основе технологических маршрутов
инормативов НЗП.
3.Планирование компенсации потерь по предприятию и цехам с учётом нормативов естественной убыли, планового уровня показателей брака и рекламаций.
4.Составление цеховых планов получения, изготовления и сдачи деталей, сборочных единиц, расчёт планов участков, расчёт сменно-суточных заданий.
Подетальная система ОКП предусматривает широкое внедрение средств автоматизации производства и управления: компьютерной техники, устройств автоматического ввода, вывода и отображения информации, связи и т.д. С ее помощью осуществляется коор-
динация работы всех структурных подразделений предприятия
1 Ильин А.И. Планирование на предприятии: учеб. пособие. – Минск: Новое знание, 2005. – С. 628.
130