
Оперативно-производственное планирование
..pdf
КА = |
20 |
=1,00; |
КБ = |
35 |
=1,75; |
КВ = |
38 |
=1,90. |
|
|
|
||||||
20 |
|
20 |
|
20 |
|
Производственная программа в пересчёте на изделие А составит:
N =1200 1,00 + 850 1,75 + 400 1,90 = 3448 шт.
Обоснованность программы, её соответствие производственной мощности можно оценить, определив потребность оборудования по видам обработки и сравнив её с наличным оборудованием.
Потребность в оборудовании р-й группы (nр) находят по формуле
|
|
|
|
n |
ti пл |
|
|
|
= |
Tпр |
= |
∑ Ni |
|
||
np |
i=1 |
|
, |
(2.22) |
|||
Fд |
Fд |
|
|||||
|
|
|
|
|
|
где Тпр – трудоёмкость производственной программы, ч; Fд – действительный фонд времени работы ведущей группы оборудования, ч; Ni – количество выпускаемого i-го вида продукции, шт.; ti пл – плановая трудоёмкость выпуска i-го вида продукции, ч/шт.
Пример. На участке установлено 10 сверлильных станков, годовой действительный фонд времени работы каждого составляет 3900 ч. В соответствии с производственной программой на станках за год должно быть обработано 100 тыс. шт. деталей А и 90 тыс. шт. деталей Б. Трудоёмкость обработки детали А составляет 0,2 ч/шт., детали Б – 0,3 ч/шт.
Потребность в станках для выполнения производственной программы составит:
np = 100 000 0,2 + 90 000 0,3 = 12 ст. 3900
Это на 2 ст. больше, чем фактически установлено на участке.
51
Расчёт также может вестись с учётом коэффициента выполнения норм:
|
|
|
|
n |
ti пл |
|
|
|
= |
Tпр |
= |
∑ Ni |
|
||
np |
i =1 |
|
. |
(2.23) |
|||
Fд Кв.н |
|
|
|||||
|
|
|
Fд Кв.н |
|
Пример. На участке установлено 10 сверлильных станков, годовой действительный фонд времени работы каждого составляет 3900 ч. В соответствии с производственной программой на станках за год должно быть обработано 100 тыс. шт. деталей А и 90 тыс. шт. деталей Б. Трудоёмкость обработки детали А составляет 0,2 ч/шт., детали Б – 0,3 ч/шт. Коэффициент выполнения норм равен 1,2.
Потребность в станках для выполнения производственной программы составит:
np |
= |
100 000 0,2 + 90 000 0,3 |
= 10 ст. |
|
|||
|
|
3900 1,2 |
Станков на участке достаточно для выполнения производственной программы.
Недостача наличного оборудования в сравнении с требуемым оборудованием будет указывать на завышенную программу («узкое место»), излишек оборудования – на недостаточную его загрузку («широкое место»).
Производственная мощность конвейерных (поточных) линий
(Мк) рассчитывается исходя из такта поточной линии (r):
Мк |
= |
Fд |
. |
(2.24) |
|
||||
|
|
r |
|
Пример. Конвейерная линия предприятия по сборке бензопил работает 248 дн. в году в две смены продолжительностью по 7,5 ч каждая, потери времени на плановопредупредительный ремонт составляют 5 %, такт поточной линии равен 0,15 ч на изделие.
52

Производственная мощность конвейерной линии составляет:
Мк = 248 2 7,5 0,95 = 23 560 шт. 0,15
Производственная мощность сборочного цеха определяется его полезной площадью и временем использования этой площади. Под полезной площадью понимают ту площадь, на которой происходят сборочные операции. Для получения полезной площади из общей площади цеха необходимо вычесть площадь проходов, подъездных путей, площадь, занятую складами и конторами цеха.
Производственная мощность сборочного цеха рассчитывается по формуле
Мсб |
= |
|
Fд |
, |
(2.25) |
|
Si |
Tцi |
|||||
|
|
|
|
где Fд – действительный фонд времени использования полезной площади цеха, м2 ч или м2 дн.; Si – площадь под сборку одного i-го изделия, м2/шт.; Тцi – длительность цикла сборки изделия, ч (илидн.).
Fд = Sц Fд′, |
(2.26) |
где Sц – полезная площадь сборочного цеха, м2; Fд′ |
– действитель- |
ный фонд времени использования 1 м2 полезной площади цеха, ч или дн.
Пример. Общая площадь сборочного цеха составляет 2500 м2. Цех работает 240 дн. в году. Площадь проходов, подъездных путей, площадь, занятая складами и конторами цеха, составляет 15 % от общей площади цеха. Площадь, отводимая под сборку одного изделия, составляет 15 м2, длительность цикла сборки – 2 дн.
Производственная мощность сборочного цеха составляет:
Мсб = 2500 0,85 240 = 17000 изд. 15 2
53

Обоснованность производственной программы также оценивается путём сопоставления необходимой сборочной площади на всю производственную программу со сборочной площадью, которой располагает цех. Если требуемая на программу площадь больше площади цеха, то программа завышена («узкое место»). Если площадь цеха больше, чем требуемая площадь на программу, то мощность сборочного цеха используется не полностью («широкое место»), т.е. программа занижена.
Полезную площадь сборочного цеха Sц (м2 ), необходимую для выполнения годовой программы, определяют по формуле
n
∑ Ni Si Tцi
Sц = |
i =1 |
|
, |
(2.27) |
|
Fд′ |
|||
|
|
|
|
где n – число наименований изделий; Si – площадь под сборку одного изделия, м2/шт.; Tцi – цикл сборки одного изделия, ч; Fд′ – дейст-
вительный фонд времени использования 1 м2 полезной площади цеха.
Пример. Полезная площадь сборочного цеха составляет 2125 м2. Цех работает 240 дн. в году. Площадь, отводимая под сборку одного изделия, составляет 15 м2, длительность цикла сборки – 2 дн. Производственной программой предприятия на плановый период предусмотрена сборка 16 тыс. шт. изделий.
Полезная площадь сборочного цеха, необходимая для выполнения производственной программы,
Sц = 16 000 15 2 = 2000 м2 . 240
Мощность литейных цехов при машинной формовке рассчитывают так же, как и мощность механических цехов, а при ручной формовке в земляные формы – так же, как и мощность сборочных цехов.
54
Результаты расчётов производственноймощности используются:
1)для разработки научно обоснованных оптимальных планов производства и реализации продукции;
2)определения потребности в оборудовании и разработки планов его распределения;
3)выявления возможностей расширения кооперирования производства;
4)выявления внутрипроизводственных резервов на предпри-
ятии;
5)выявления «узких мест» на предприятии;
6)планирования капитальных вложений для расширения и реконструкции предприятия.
Для наиболее полного использования производственной мощности предприятия, установленной по ведущим цехам, необходимо, чтобы мощности ведущих цехов предприятия полностью соответствовали пропускной способности других производственных цехов
ивспомогательных цехов (служб, участков). Поэтому производственную мощность предприятия следует определять с учётом ликвидации «узких мест» в производстве с разработкой организационнотехнических мероприятий по модернизации оборудования, совершенствованию технологических процессов и норм, сокращению номенклатуры работ за счёт кооперированных поставок, увеличению сменности работ на отдельных участках и т.д.
2.4.Расчёт загрузки и пропускной способности оборудования и сборочных площадей
Расчёт загрузки и пропускной способности оборудования и сборочных площадей необходим для оценки возможности выполнения производственной программы цеха, предприятия.
Расчёт загрузки и пропускной способности оборудования
Загрузку оборудования (Zоб) определяют по каждой р-й группе оборудования в нормо-часах по формуле
55
|
|
|
|
n |
tip |
|
|
|
|
|
= |
∑ Ni |
|
||
|
Z |
об |
i =1 |
|
, |
(2.28) |
|
|
|
|
|||||
|
|
|
60 Кв.н |
|
|||
|
|
|
|
|
|||
где Ni – |
программа выпуска (обработки) изделия i-го наименова- |
||||||
ния, шт.; |
tip – норма времени обработки изделия i-го наименования |
на р-й группе оборудования, мин/шт.; Кв.н – коэффициент выполнения норм; n – число наименований изделий.
Пропускную способность оборудования (Роб, ч) определяют по
каждой р-й группе оборудования по формуле |
|
Роб = Fд nр , |
(2.29) |
где Fд – действительный фонд времени работы единицы оборудования в плановом периоде, ч; np – количество единиц оборудования в р-й группе.
Коэффициент загрузки оборудования р-й группы (Кз) рассчи-
тывается по формуле
К |
з |
= |
Zоб |
. |
(2.30) |
|
|||||
|
|
Р |
|
||
|
|
|
об |
|
|
При Кз > 1 отмечается перегрузка оборудования, т.е. |
Zоб > Роб , |
чтоозначает наличие «узкогоместа» поданнойгруппеоборудования. При Кз < 1 отмечается недогрузка оборудования, т.е. Zоб < Роб ,
что означает наличие «широкого места» по данной группе оборудования.
Пример. Число рабочих дней в плановом году – 248, режим работы двухсменный, плановая продолжительность смены 8 ч. Регламентированный процент простоев в связи с переналадкой и планово-предупредительным ремонтом составляет 4 %. На участке установлено 10 шлифовальных станков, производительность одного станка равна 5 дет./ч,
плановая |
трудоемкость |
обработки одной детали равна |
12 мин/шт. |
Коэффициент |
выполнения норм равен 110 %. |
56
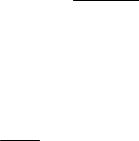
Производственной программой предусмотрена обработка 220 тыс. деталей за год.
Загрузка оборудования составит:
220000 12
Zоб = = 40000 н.- ч 60 1,1
Пропускная способность оборудования
Роб = 248 2 8 0,96 10 = 38093 н.- ч,
Коэффициент загрузки шлифовальных станков соста-
вит:
Кз = 40000 =1,0501, или 105,01 % – « узкое место». 38093
Расчет загрузки и пропускной способности сборочных площадей
Загрузка сборочных площадей (Zпл) определяется суммарной площадью, требуемой для сборки изделий, закреплённых за участком, по формуле
n |
|
Zпл = ∑ Ni Si Tпрi , |
(2.31) |
i=1
где Ni – количество собираемых изделий i-го наименования, шт.; Si – площадь, необходимая для сборки i-го изделия, м2/ед.; Тпрi – длительность производственного цикла сборки i-го изделия, дн. (ч.).
Пропускная способность сборочных площадей (Рпл) определя-
ется по формуле |
|
Pпл = Sц Fд, |
(2.32) |
где Sц – полезная производственная площадь цеха, м2; Fд – действительный фонд времени, дн.
Коэффициент загрузки производственной площади (Кз) опре-
деляется отношением загрузки производственной площади к её пропускной способности:
57

К |
з |
= |
Zпл |
. |
(2.33) |
|
|||||
|
|
Р |
|
||
|
|
|
пл |
|
При Кз > 1 отмечается перегрузка производственной площади, т.е. Zпл > Рпл , что означает наличие «узкого места».
При Кз < 1 отмечается недогрузка производственной площади, т.е. Zпл < Рпл , что означает наличие «широкого места».
Пример. Производственной программой предусмотрена сборка 17 тыс. изделий в год. Полезная площадь сборочного цеха составляет 2125 м2. Цех работает 248 дн. в году. Площадь, отводимая под сборку одного изделия, составляет 15 м2, длительность цикла сборки равна 2 дн.
Загрузка сборочных площадей
Zпл = 17 000 15 2 = 510 000 м2 дн.
Пропускная способность сборочных площадей
Pпл = 2125 248 = 527 000 м2 дн.
Коэффициент загрузки производственной площади
Кз = 510 000 = 0,9677, или 96,77 % . 527 000
На основе представленных объёмных расчетов принимаются соответствующие управленческие решения по ликвидации «узких» и «широких» мест.
При наличии «узких мест» в производстве предусматриваются мероприятия, позволяющие устранить их путём пересмотра технологических маршрутов и режимов обработки, введения дополнительных смен, совершенствования организации труда, материального стимулирования и обслуживания рабочих мест, а иногда – модернизации оборудования. При наличии «широких мест» разрабатываются мероприятия по дополнительной загрузке оборудования.
58
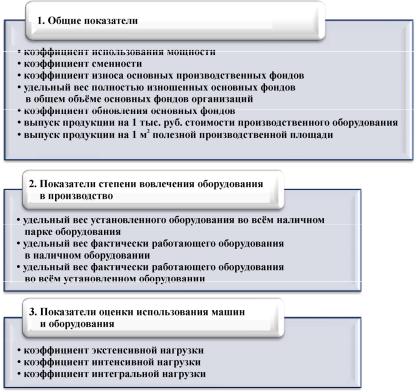
2.5. Показатели использования
производственной мощности
Показатели использования производственной мощности подразделяются на три группы (рис. 2.1).
Рис. 2.1. Показатели использования производственной мощности
1. Общие показатели использования производственной мощности. Для наиболее общей оценки использования производственной мощности применяется коэффициент использования мощности (Кисп), который определяется как отношение планового или
59
фактического объёма выпущенной продукции (В) к рассчитанной величине мощности (Мр) по формуле
К |
|
= |
В |
. |
(2.34) |
исп |
|
||||
|
|
Мр |
|
Учитывая тот факт, что производственная мощность представляет собой максимальный объём выпуска продукции, при нормальных условиях эксплуатации оборудования коэффициент использования производственной мощности не может превышать единицы
(или 100 %).
Пример. Годовой планируемый объём выпуска равен 7 000 000 деталей. Расчётная мощность цеха составляет 7 800 000 деталей в год. Тогда плановый коэффициент использования мощности
7 000 000 / 7 800 000 = 0,8974, или 89,74 %.
Использование оборудования во времени характеризует коэффициент сменности, который определяется двумя способами:
1)отношением общего количества отработанных за сутки во всех сменах станко-часов к действительному расчётному фонду времени работы оборудования в одну смену;
2)отношением количества отработанных станко-смен к количеству установленного оборудования.
Более точным является первый способ расчёта, так как он не учитывает фактические простои оборудования в течение смены, в отличие от второго способа, который всегда даёт завышенные результаты.
В качестве общих показателей использования производственной мощности, помимо рассмотренных выше, выступают:
− коэффициент износа основных производственных фондов; − удельный вес полностью изношенных основных фондов
вобщем объёме основных фондов организаций;
−коэффициент обновления основных фондов;
60