
Методы и инструменты поиска инновационных решений
..pdfих реализовали в Японии. В компании Toyota была создана система, цель которой – сократить или ликвидировать деятельность, потребляющую ресурсы и не добавляющую стоимость, т.е. ту, за которую потребитель не желает платить.
Сегодня эта система известна как производственная система
Toyota (Toyota Production System – TPS), принципы и инструменты которой нашли отражение в ее американском варианте – системе бережливого производства (Lean Production). Многое из ее элементов былоещев российском варианте – научной организации труда(НОТ).
Цель – построение производства, способного быстро отвечать на изменяющиеся требования потребителей и получать прибыль при любом изменении рынка, в том числе при падении спроса; создание совершенной производственной системы, которая бы при поступлении заказа мгновенно поставляла требуемую продукцию и при этом не происходило накопления промежуточных запасов.
Бережливое производство (lean production):
–это системный подход к выявлению потерь и поиску путей их устранения, чтобы уменьшить время между заказом клиента
иотгрузкой товара;
–это бизнес-процессы, требующие меньше людских ресурсов, капитальных вложений, места для производства, материалов
ивремени на всех стадиях.
Результат использования данной системы – поставка в кратчайшие сроки требуемой продукции в случае поступления заказа без накопления промежуточных запасов. Данная методология направлена на борьбу с потерями во всех их проявлениях: излишние складские запасы, межоперационные заделы, время простоя, лишние перемещения, учитывая при этом удобство и безопасность выполнения операций для персонала.
План действий при осуществлении системы бережливого производства:
1. Определить ожидаемую ценность конкретной продукции, имеющей определенные характеристики и определенную цену путем диалога с заинтересованными потребителями.
211
2.Определить весь поток создания ожидаемой потребителем ценности для каждого типа продукции: от концепции до дошедшего до потребителя товара.
3.Организовать движение потока создания ожидаемой потребителем ценности, т.е. акцентирование внимания не на предприятии и оборудовании, а на продукции и ее «нуждах».
4.Постоянно прислушиваться к голосу потребителя, позволяя ему «вытягивать» продукцию с предприятия тогда, когда ему это требуется.
Как следует пользоваться моделью бережливого произ-
водства. При бережливом подходе необходимо сделать пять основных шагов.
1.Выявить факторы, способствующие созданию ценности. Определить, что в данном случае является ценностью, и изучить требования потребителей. Оценка факторов стоимости должна проводиться с точки зрения внутренних (персонал компании) или внешних потребителей. Ценность следует выражать в показателях того, насколько хорошо товар или услуга удовлетворяет запросам потребителей при определенной цене в определенное время.
2.Идентифицировать поток создания ценности. Установить последовательность видов деятельности, которые добавляют ценность к анализируемым товарам или услугам. Для этого необходимо составить карту потока создания ценности, на которой все нанесенные на нее виды деятельности необходимо оценить с точки зрения того, повышают они ценность товара или услуги или нет.
Инаконец, там, где это возможно, нужно исключить виды деятельности, которые не приводят к увеличению ценности.
3.Организовать поток видов деятельности. Необходимо добиться, чтобы производство обеспечивало непрерывный поток товаров и услуг. Чтобы вписать виды деятельности в поток создания ценности, потребуются дополнительные усилия по совершенствованию производства. Под потоком здесь понимается непрерывный процесс продвижения товара или услуги через систему до тех пор, пока продукт не окажется у потребителя. Основными препятствия-
212
ми для потокового подхода являются очереди на выполнение работ, серийное производство и транспортировку. Барьеры этого рода увеличивают продолжительность доставки товара или услуги потребителю. Кроме того, наличие подобных барьеров приводит к тому, что часть денег оказывается «связанной», в то время как эти средства компания могла бы потратить более эффективно.
4.Организовать дело так, чтобы потребитель «вытягивал» товар или услугу в ходе производственного процесса. Контроль за продукцией должен осуществляться на основе «вытягивающей» системы (запуск производства именно в тот момент, когда необходимо пополнить запасы или когда возникает спрос, т.е. потребитель «вытягивает» товар из системы, которая должна все время находиться с ним в контакте. Продукты должны «вытягиваться» из системы на основе фактического потребительского спроса. Поток создания ценности должен реагировать на реальное положение дел
ипредоставлять товар или услугу только тогда, когда продукт нужен потребителю не раньше и не позже.
5.Необходимо постоянно оптимизировать систему. Совершенство достигается за счет постоянного улучшения процессов (для этого используется модель кайдзен), а также за счет устранения потерь и продуманного ведения дел в целом.
Условия применения системы бережливого производства. Данной моделью может воспользоваться любая компания, если только ее руководители и менеджеры разделяют основные положения, относящиеся к бережливой философии:
♦Люди своими глазами видят весь поток создания продукции «от двери до двери», а также отдельные процессы.
♦Основным ограничением для повышения рентабельности являются потери.
♦Большое число небольших улучшений, осуществляемых быстро и последовательно, приведет к более высоким результатам, чем любое аналитическое исследование.
♦Взаимные влияния, возникающие из-за наложения процессов друг на друга, можно ослабить, если постоянно заниматься улучшением потока создания ценности.
213
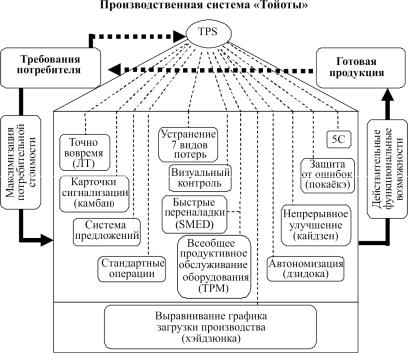
Бережливое производство – это подходы, методы, направленные на уменьшение всех возможных издержек и увеличение производительности. Эти инструменты ориентированы в первую очередь на производственную часть компании. Меняя производственную систему на базе принципов бережливого производства, мы сокращаем внутренние потери (запасы, перемещения и т.д.), при этом высвобождаются люди, помещения, энергия. Усилия персонала концентрируются на тех видах деятельности, которые не добавляют ценности продукту с точки зрения потребителя и, следовательно, не увеличивают добавленную (приростную) стоимость для компании (рис. 4.1).
Рис. 4.1. Производственная система «Тойоты»
214

Достоинства метода. Высокая организованность процессов позволяет полностью избежать ненужных затрат и успешно конкурировать в условиях современного рынка.
Недостатки метода. Невовлеченность персонала и сложность проведения изменений в компании.
1.Концепция бережливого производства очень проста для понимания, однако самое сложное – сделать так, чтобы она стала частью повседневной работы.
2.Для успешного внедрения бережливого производства необходимо изменение культуры компании.
3.Концепция бережливого производства ориентирована на максимальный учет интересов и запросов потребителей.
4.Бережливое производство – подход, направленный на качество соответствия выпускаемой продукции установленным требованиям. Принцип работы с качеством по системе TPS описывается как три НЕ: не бери в работу дефектные заготовки, не делай дефектную продукцию, не передавай дефектную продукцию на следующую операцию.
5.Аббревиатура TPS – Toyota Production System (производствен-
ная система « Тойота») расшифровывается, в частности, и так: Thinking Production System – Думающая производственная система.
4.6. БЫСТРАЯ ПЕРЕНАЛАДКА ОБОРУДОВАНИЯ
Быстрая переналадка оборудования – это один из инстру-
ментов совершенствования производства. Создан Сигэо Синго (Япония) в 70-х гг. XX в. В процессе подготовки документов TPS С. Синго – разработчик технологии быстрой переналадки оборудования ввел для нее соответствующий термин на японском – сингуру дандори, что дословно означает единичное действие, а на англий-
ском – Single Minute Exchange of Die (SMED3). Поэтому этот метод управления еще носит название Система SMED [27].
Цель этого метода управления производством – совершенствование производственной деятельности компании за счет сокращения времени переналадки оборудования.
215
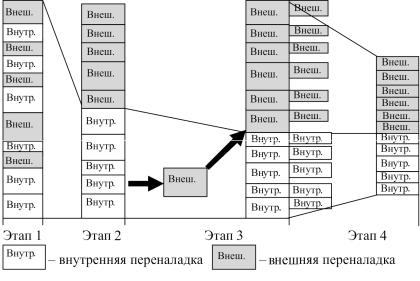
Быстрая переналадка оборудования – это процесс переналадки производственного оборудования при четком понимании различий между внутренними и внешними действиями для перехода от производства одного вида деталей (продукции) к другому за максимально короткое время. Чтобы сократить время переналадки, необходимо не только разделить ее на внутреннюю (когда останавливают оборудование) и внешнюю (производится до останова или после запуска оборудования), но и попытаться преобразовать как можно больше работ по внутренней переналадке во внешнюю. Именно это решение позволяет существенным образом повысить эффективное время использования оборудования путемсокращенияего остановов напереналадку.
Система SMED – это совершенно новый способ мышления относительно производства. Система SMED основывается как на теории, так и на многолетней экспериментальной практике. Система SMED представляет собой научный подход к сокращению времени переналадки, который можно применить на любом предприятии и любом оборудовании (рис. 4.2).
Рис. 4.2. Технология быстрой переналадки оборудования
216

План действий при реализации быстрой переналадки оборудования
1.Тщательное изучение и анализ фактических условий на рабочем месте.
2.Разделение действий на внутреннюю и внешнюю перена-
ладку.
3.Преобразование (где это возможно) внутренних действий по переналадке во внешние.
4.Упрощение и упорядочение всех элементарных внутренних
ивнешних операций переналадки на основеих подробного анализа.
5.Документирование новых процедур и действий. Разработка карты усовершенствования операций.
В случае необходимости (если переналадка занимает более 10 минут) повторение всех действий снова.
Результат. Повышение эффективности производства и обеспечение компании конкурентных преимуществ на мировом рынке.
Достоинства метода. Сокращение времени простоя оборудования, минимизация запасов, ориентация на производство малыми сериями или под заказ, быстрая адаптация к изменениям спроса.
Недостатки метода. Требует долгосрочной дисциплины и значительных управленческих навыков в области перемен. Частота и длительность пробных прогонов и корректировки зависит от квалификации инженера-наладчика. Быстрая переналадка оборудования – один из основных инструментов производственной системы «Тойота» (TPS).
1.Перед началом внедрения технологии быстрой переналадки оборудования необходимо вовлечь каждого сотрудника в этот процесс.
2.Чтобы сократить продолжительность переналадок, при выполнении которой необходимо останавливать оборудование на период не более 10 минут, может потребоваться несколько итераций процесса совершенствования переналадки.
3.Необязательно выполнять этапы 3 и 4 последовательно, их можно выполнять почти одновременно.
217

4.После завершения улучшений по системе SMED следующей задачей является внедрение OTED.
5.Самые большие сложности при переналадке оборудования заключаются в правильном выполнении наладочных операций.
6. Быстрая переналадка – это реальный инструмент борьбы
снепроизводительными затратами.
4.7.ВСЕОБЩЕЕ ПРОДУКТИВНОЕ ОБСЛУЖИВАНИЕ
Всеобщее продуктивное обслуживание (Total Productive Maintenance –ТРМ) – стратегия, ориентированная на предотвращение всех видов потерь, которая позволяет обеспечить наивысшую эффективность производственной системы на протяжении всего жизненного цикла с участием всего персонала [27].
Метод создан Сэйити Накадзима (Япония) в 60-е гг. XX в. Цель метода – совершенствование деятельности компании
за счет повышения эффективности оборудования, процессов производства, а также улучшения качества продукции и повышения производственной безопасности. Внедрение ТРМ направлено на устранение хронических потерь:
–выход из строя оборудования;
–высокое время переналадки и юстировки;
–холостой ход оборудования и мелкие неисправности;
–снижение быстродействия (скорости) вработе оборудования;
–наличие дефектных деталей;
–потери при вводе в действие оборудования.
Результатом использования этого метода управления произ-
водством является обеспечение компании конкурентных пре-
имуществ на мировом рынке.
План действий при использовании системы ТРМ
1.Принятие руководством решения о внедрении ТРМ на предприятии.
2.Формирование организационной структуры развертывания ТРМ.
218
3.Первоначальное обучение и разработка стратегии ТРМ.
4.Развертывание ТРМ по основным направлениям в нескольких подразделениях для лучшего понимания процедуры продвижения ТРМ.
5.Разработка плана внедрения системы ТРМ на предприятии.
6.Реализация плана внедрения в процессе развертывания системы ТРМ по восьми направлениям.
Существуют восемь принципов TPM.
1.Непрерывное улучшение, нацеленное на практику предотвращения 7 видов потерь.
2.Автономное содержание в исправности. Оператор оборудования должен самостоятельно проводить осмотр, работы по чистке, смазочные работы, а также незначительные работы по техническому обслуживании.
3.Планирование технического обслуживания. Обеспечение 100 % готовности оборудования, а также проведение мероприятий кайдзен в области технического обслуживания.
4.Тренировка и образование. Сотрудники должны быть обучены в соответствии с требованиями по улучшению квалификации для эксплуатации и технического ухода за оборудованием.
5.Контроль запуска. Реализовать вертикальную кривую запуска новой продукции и оборудования.
6.Менеджмент качества. Реализация цели «нулевые дефекты
вкачестве» в изделиях и оборудовании.
7.TPM в административных областях. Потери и расточительствоустраняются внепрямых производственных подразделениях.
8.Безопасность труда, окружающая среда и здравоохранение. Требование преобразования аварий на предприятии в ноль.
Автономное содержание оборудования в исправности – важнейший принцип системы TPM. Поскольку ее цель – минимизировать потери эффективности, которые возникают из-за отказов устройств, коротких остановок, брака и т.д., то все большая часть необходимой деятельности по техническому обслуживанию (чистка, смазка, технический осмотр устройств) упрощается, стандартизируется и постепенно передается на места и вменяется в обязанно-
219
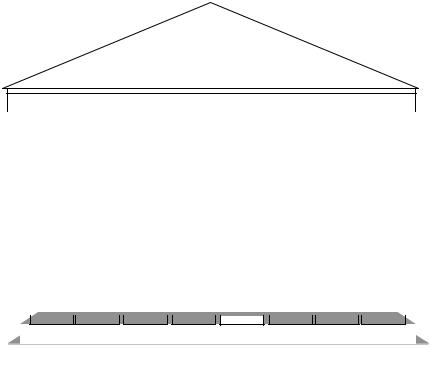
сти сотрудников. Вследствие этого сотрудники отдела главного механика освобождаются, с одной стороны, от текущей рутинной деятельности и получают больше времени для разработки и проведения мер по улучшению. С другой стороны, теперь оборудование (устройства) может обеспечиваться необходимым техническим обслуживанием, которое ранее не могло предоставляться своевременно из-за отсутствия надлежащих ресурсов (рис. 4.3).
ТРМ
8 направлений развертывания ТРМ
Системы согласования и сопровождения цели
|
|
|
|
|
|
|
|
|
|
|
|
|
|
|
|
|
|
|
|
|
|
|
|
|
|
|
|
|
Целенаправленныеулучшения (устранениепотерь16 видов) |
|
|
Самостоятельноеобслуживание оборудованияоператорами |
|
|
Плановоеобслуживание |
|
|
|
Качествообслуживания |
|
Образование ипрофессиональная подготовка |
|
|
|
Раннееуправлениеразработками оборудованияипродукции |
|
|
Безопасность, гигиенатрудаиохрана окружающейсреды |
|
|
Административные и ОбеспечивающиеслужбыТРМ |
|
|
|
|
|
|
|
|
|
|
|
|
|
|
|
|
|
|
|
|
|
|
|
|
|
|
|
|
|
|
|
|
|
|
|
|
|
|
|
|
|
|
|
|
|
|
|
|
|
|
|
|
|
|
|
|
Рабочие группы
5С
Рис. 4.3. Схема развертывания ТРМ
Однако в системе всеобщего ухода за оборудованием речь идет не только об исключительной проблеме содержания в исправности оборудования, но о широком понимании обслуживания средств производства как интеграции процессов эксплуатации итехнического
220