
Выбор абразивных инструментов и режимов резания для высокоэффективно
..pdf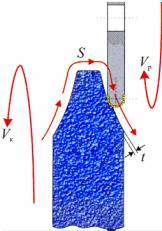
щие свойства шлифовального круга, что обеспечивает максимальную производительность на операциях предварительного шлифования. При встречном вращении круга и правящего ролика шероховатость шлифуемой поверхности снижается на 20 %. На качество обработанной поверхности детали существенно влияет соотношение скоростей ролика и круга. Отношение частоты вращения ролика и круга не должно быть кратно целому числу. В противном случае все дефекты рабочей поверхности ролика и погрешности его установки будут скопированы на рабочей поверхности круга, что неизбежно приведет к ухудшению качества обработанной поверхности. При правке алмазными роликами по методу шлифования встречная правка является предпочтительнее попутной.
Очень часто вместо метода врезной правки алмазным роликом применяют метод профилирования путем обката профильной поверхности круга алмазным диском. Особенности правки алмазными правящими кругами приведены на рис. 59. Преимущество такой правки заключается в том, что износ правящего круга намного меньше, чем карандашей или роликов, а качество поверхности правящихся кругов после правки лучше, шероховатость поверхностей шлифовальных кругов после такой правки ниже.
Рис. 59. Схема правки алмазными кругами
111
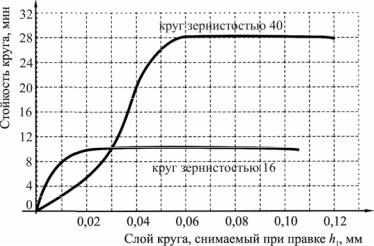
4.2. Выбор рациональных режимов правки
Для обеспечения высокой стойкости правящих инструментов и требуемого качества правки необходимо правильно назначать режимы и условия правки. Часто толщина снимаемого при правке слоя h1 устанавливается в несколько раз большей, чем это необходимо для восстановления режущих свойств и формы рабочей поверхности круга. При завышенном значении h1 не только излишне расходуются абразивные круги и правящий инструмент, но и значительно повышается технологическое время правки. Очевидно, что наибольшая глубина, на которую необходимо углубиться при правке шлифовального круга, составляет не более половины диаметра поры. Например, при правке шлифовального круга зернистостью 40 максимальное значение слоя h1 не должно превышать 0,1 мм. Практически круг можно править на значительно меньшую глубину 0,05–0,07 мм, а для круга зернистостью 16 достаточен съем слоя 0,03–0,04 мм. Удаление слоя большей толщины не улучшает условий шлифования и поэтому совершенно излишне. На рис. 60 представлена зависимость периода стойкости абразивного круга от величиныслояh1, удаленного при правке.
Рис. 60. Зависимость периода стойкости абразивного круга от величины слоя h1, удаленного при правке
112
Так как количество зерен в единице объема круга и величина отдельных пор зависят в большей степени от зернистости, чем от структуры и твердости круга, то величина снимаемого при правке слоя может быть определена исходя из размеров абразивных зерен: h1 = (0,15–0,2) d3, где d3 – средний размер абразивных зерен в поперечнике, мм. При врезном и продольном шлифовании величина снимаемого при правке слоя увеличивается и определяется в зависимости от износа рабочих кромок круга или профиля круга.
На чистовых операциях шлифования износ круга зависит от вида правящего инструмента и режимов правки. Установлено, что чем больше воздействие правящего инструмента на слой, граничащий с удаляемым слоем, тем больше разрушение этого слоя и тем больше при шлифовании износ круга по радиусу.
При правке алмазным инструментом коэффициент k примерно равен 1. Таким образом, общий расход шлифовального круга за цикл его работы (стойкостная наработка круга) после правки алмазным инструментом составляет: h = h1 + h2 = (0,2 + 0,05) · dз = 0,25 · dз.
За время шлифования деталей рабочий, как правило, самостоятельно определяет момент, когда круг либо затуплен, либо потерял форму и необходимо произвести правку рабочей поверхности круга. Для этого на станок устанавливается правящее приспособление, подводится правящий инструмент к кругу, включается подача (если правка осуществляется приводом станка), либо правка производится вручную.
Правка производится с применением СОЖ в несколько проходов согласно рекомендациям или опыту рабочего. После этого отключается правящее приспособление и настраивается станок на шлифование партии заготовок. На эти приемы уходит много времени, что снижает производительность операции. В современных станках процесс правки автоматизирован и осуществляется вне цикла шлифования и без нарушения настройки станка.
Отдельные параметры режима правки по-разному влияют на качественные показатели процесса шлифования и износ алмазного правящего инструмента. Зависимость удельной производительности
113
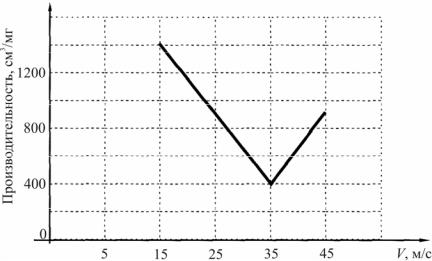
правящего алмазного инструмента (отношение объема, снятого при правке абразива, к массе алмаза, изношенного при правке, см3/мг) от окружной скорости круга приведена на рис. 61.
Рис. 61. Зависимость удельной производительности правящего алмазного инструмента от окружной скорости круга
С увеличением скорости с 15 до 35 м/с удельная производительность уменьшается, а при дальнейшем увеличении скорости до 50 м/с увеличивается. Повышение скорости круга в процессе правки обеспечивает более низкую шероховатость обработанной поверхности при шлифовании.
Как правило, правку абразивных кругов проводят при той же скорости, что и шлифование деталей. Поэтому расширение области скоростного шлифования (45–60 м/с) обеспечивает сокращение расхода алмазного правящего инструмента, повышение производительности и качества шлифования. Установлено, что с увеличением продольной и поперечной подач удельная производительность уменьшается. При этом продольная подача при правке больше влияет на износ правящего инструмента, чем поперечная. Поэтому целесообраз-
114
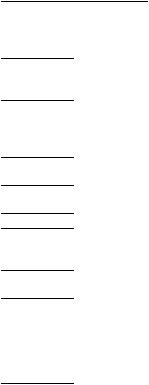
нее повышать производительность процесса правки за счет увеличения поперечной подачи (до 0,04–0,05 мм/дв. ход), а не продольной. При этом увеличение поперечной подачи оказывает меньшее влияние на шероховатость шлифуемой поверхности, чем увеличение продольной подачи.
В табл. 10 приведены режимы правки шлифовальных кругов алмазными и алмазно-металлическими карандашами методом обтачивания.
Таблица 1 0
Режимы правки шлифовальных кругов алмазными и алмазно-металлическими карандашами методом обтачивания
Вид |
Шерохова- |
|
Скорость подачи |
|
Число проходов |
||
шлифования |
тость Rа, |
|
продольной, |
поперечной, |
|
рабочих |
выхажива- |
|
мкм |
|
м/мин |
мм/дв. ход |
|
|
ющих |
|
|
|
Правка алмазным |
карандашом |
|
|
|
Круглое бес- |
1,25–0,32 |
|
0,3 |
0,02 |
|
6 |
4 |
центровое, |
0,32–0,16 |
|
0,2 |
0,01 |
|
5 |
4 |
плоское |
|
|
|||||
|
|
|
|
|
6 |
|
|
Внутреннее |
1,25–0,32 |
|
1,0 |
0,02 |
|
4 |
|
|
0,32–0,16 |
|
0,5 |
0,01 |
|
5 |
4 |
Резьбошли- |
0,63–0,16 |
|
0,2 |
0,025 |
|
6 |
2 |
фование |
|
|
|||||
|
|
|
|
|
4 |
|
|
Шлицешли- |
1,25–0,32 |
|
0,3 |
0,03 |
|
4 |
|
фование |
0,32–0,16 |
|
0,2 |
0,01 |
|
5 |
4 |
Профильное |
1,25–0,32 |
|
0,2 |
0,02 |
|
6 |
4 |
0,32–0,16 |
|
0,1 |
0,01 |
|
8 |
4 |
|
|
Правка |
алмазно-металлическим карандашом |
|
||||
Круглое бес- |
1,25–0,32 |
|
0,4 |
0,03 |
|
4 |
4 |
центровое, |
0,32–0,16 |
|
0,3 |
0,02 |
|
3 |
4 |
плоское |
|
|
|||||
|
|
|
|
|
|
|
|
Внутреннее |
1,25–0,32 |
|
1,5 |
0,03 |
|
4 |
4 |
0,32–0,16 |
|
|
|||||
Резьбошли- |
0,63–0,16 |
|
– |
– |
|
– |
– |
фование |
|
|
|
4 |
|
||
|
|
|
|
|
|
||
Шлицешли- |
1,25–0,32 |
|
0,4 |
0,03 |
|
4 |
|
фование |
0,32–0,16 |
|
0,3 |
0,02 |
|
3 |
4 |
Профильное |
1,25–0,32 |
|
0,3 |
0,03 |
|
4 |
4 |
|
0,32–0,16 |
|
0,2 |
0,02 |
|
4 |
4 |
115
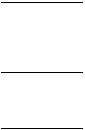
Алмазные правящие инструменты находят также применение при правке шлифовальных эльборовых кругов. Наиболее эффективна правка алмазными карандашами кругов из эльбора на керамической связке, обеспечивающая высокую производительность процесса правки и режущие свойства рабочей поверхности круга.
4.3. Рекомендации по выполнению правки алмазных кругов
Правка (профилирование) алмазоносного слоя кругов производится для восстановления точности формы, удаления дефектов рабочей поверхности, образования требуемого профиля. Как правило, правку производят без охлаждения. Наиболее эффективным видом правки является шлифование алмазоносного слоя абразивными кругами (табл. 11). Правка производится кругами из электрокорунда белого и карбида кремния зеленого на керамической связке зернистостью на один-два номера выше зернистости круга из сверхтвердого материала (табл. 12). Твердость кругов СМ1-М1 для правки инструмента на органической связке и С1-СМ1 – для инструмента на металлической связке, причем, чем мельче зернистость круга из сверхтвердого материала, тем мягче должен быть круг, применяемый для правки.
Таблица 1 1 Режимы правки алмазоносного слоя абразивными кругами
Положение |
|
|
Режимы правки |
|
||||
алмазного круга |
Окружная скорость, м/с |
Продольная |
Поперечная |
|||||
|
|
|
|
абразивного |
алмазного |
подача, |
подача, |
|
|
|
|
|
круга |
круга |
м/мин |
мм/дв. ход |
|
Алмазный |
круг |
уста- |
|
|
|
|
||
новлен |
на |
оправках |
|
|
|
|
||
или в центрах кругло- |
25–35 |
0,5–1,0 |
1,0–2,0 |
0,02–0,04 |
||||
шлифовального |
или |
|
|
|
|
|||
заточного станка |
|
|
|
|
|
|||
Алмазный |
круг |
уста- |
|
|
|
|
||
новлен |
на |
шпинделе |
30–40 |
25–35 |
0,5–1,0 |
0,02–0,04 |
||
шлифовального |
или |
|||||||
|
|
|
|
|||||
заточного станка |
|
|
|
|
|
116

Таблица 1 2
Характеристики абразивных кругов на керамической связке для правки алмазоносного слоя
Характеристика алмазоносного слоя |
Характеристика круга для правки |
|||
Вид связки |
Зернистость алмазов |
Марка абразива |
Зернистость |
Твердость |
|
|
|
абразива |
|
Органическая |
160/125–125/100 |
Электрокорунд |
20; 16; 12 |
С1-СМ2 |
|
100/80–80/63 |
22А, 23А, 15А, |
12; 10; 8 |
СМ2-СМ1 |
|
63/50–50/40 |
16А |
8; 6; 4 |
СМ1-СМЗ |
|
|
|
|
|
|
40/28–14/10 |
|
М40; М28 |
МЗ |
Керамическая, |
250/200–200/160 |
Карбид кремния |
40; 32 |
СТ1-С2 |
металлическая |
160/125–125/100 |
62С, 63С, 64С |
25; 20 |
СТ2-С1 |
|
100/80–80/63 |
|
16; 12 |
С1-СМ2 |
|
63/50 и ниже |
|
10; 8; 6 |
СМ2-СМ1 |
Вопросы для самопроверки
1.Перечислите основные методы правки шлифовальных кругов.
2.Каковы особенности правки методом обтачивания алмазными карандашами?
3.Каковыособенностипрофильнойправки алмазнымироликами?
4.Назовите основные принципы выбора рациональных режимов правки.
5.Перечислите особенности применения правки алмазных кругов
117
ГЛАВА 5. ВЫБОР ОПТИМАЛЬНОЙ ХАРАКТЕРИСТИКИ АБРАЗИВНОГО ИНСТРУМЕНТА ДЛЯ РАЗЛИЧНЫХ ВИДОВ ОБРАБОТКИ
Повышение эффективности различных процессов абразивной обработки при обеспечении требуемого качества поверхностного слоя является одной из главных задач в области чистовой окончательной обработки ответственных деталей современных машин. Основными путями ее решения являются: назначение оптимальных режимов обработки, правильный подбор абразивного инструмента с характеристиками, обеспечивающими требуемое качество обработки, высокую стойкость и режущую способность, высокий коэффициент шлифования и т.д. Этого можно достичь, обеспечив работу абразивного инструмента в режиме экономного самозатачивания, в процессе которого рабочая поверхность инструмента самопроизвольно восстанавливает свою режущую способность.
5.1. Основные параметры выбора
Для оптимально правильного выбора абразивного инструмента необходимо учитывать следующие параметры:
1)характеристику обрабатываемого материала (химсостав, фи- зико-механические свойства и т.д.);
2)геометрические параметры и форму шлифуемой поверхности (сплошная, прерывистая, требуемая шероховатость и точность обработки);
3)припуск на обработку, исходное состояние шлифуемой поверхности (в том числе шероховатость);
4)тип станка и его параметры;
5)условия обработки (скорость круга и изделия, тип и диапазон подач, охлаждение и т.д.);
6)эффективность обработки (производительность, необходимая стойкость инструмента, потери на правку, затраты на электроэнергию и т.д.).
118
5.1.1. Обрабатываемый материал
Химический состав обрабатываемого материала, особенно металла, существенно влияет на качество шлифования, степень окисления стружки и качество обрабатываемой поверхности. Например, алюминий, кремний, никель и другие способны образовывать химически устойчивую пленку, увеличивая стойкость сплавов к окислению. Наоборот, повышение содержания углерода снижает устойчивость сплавов против окисления и тем самым способствует процессу образования стружки и облегчает ее удаление с поверхности круга. Таким образом, повышение степени окисления облегчает процесс шлифования, а понижение затрудняет. Поэтому углеродные стали, например, лучше шлифуются, чем легированные конструкционные и инструментальные. Легирующие присадки способствуют образованию в сталях карбидных соединений, повышают их твердость и температуру плавления. Это ухудшает обрабатываемость сталей абразивными инструментами, увеличивает степень затупления абразивных зерен, понижает стойкость кругов между правками.
Немаловажное значение для процесса шлифования имеют и физи- ко-механические свойства материала: теплопроводность и теплостойкость, прочность, твердость и вязкость. Так, обработка сплавов с низкой теплопроводностью происходит при высоких температурах, что делает их труднообрабатываемыми. Высокая прочность в сочетании с большой вязкостью также затрудняет процессы шлифования. Например, серый чугун обрабатывается значительно легче, чем отбеленный или легированный. Повышенная твердость сталей и сплавов приводит к быстрому износу иразрушению абразивныхинструментов.
Большое влияние на процесс шлифования оказывают характеристика абразивного инструмента и структура обрабатываемого материала. Например, стали по обрабатываемости шлифованием в зависимости от структуры можно расположить в следующем порядке: аустенитные, мартенситные, троститные, сорбитные, перлитные. Исходя из этого, шлифование аустенитных сталей целесообразнее осуществлять кругами из электрокорунда белого. При опасности появления прижогов и шлифовочных трещин применяются круги откры-
119
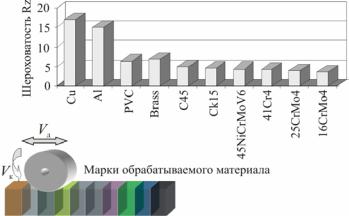
тых структур, иногда круги из карбида кремния зеленого. Характерный пример влияния свойств обрабатываемого материала на параметры шероховатости при шлифовании одним и тем же абразивным инструментом показан на рис. 62. Наименьшая шероховатость при шлифовании кругом из кубического нитрида бора образуется на деталях из нержавеющей стали.
Рис. 62. Влияние марки обрабатываемого материала на шероховатость Rz поверхности при шлифовании
В настоящее время для шлифования труднообрабатываемых сталей и сплавов применяются инструменты из эльбора. Они позволяют исключить при шлифовании термические удары и прижоги. Обработка твердых сплавов производится инструментами из карбида кремния и алмазов. Применение алмазных инструментов исключает появление шлифовочных трещин, обеспечивает высокие классы точности обработки и качество поверхности.
Многообразие сочетаний обрабатываемых материалов по химическому составу, физико-механическим свойствам и структуре с геометрическими параметрами деталей и кинематическими связками при шлифовании не позволяет однозначно устанавливать характеристику абразивного инструмента. Так, для обдирки стального ли-
120