
Выбор абразивных инструментов и режимов резания для высокоэффективно
..pdfК целевым параметрам процесса шлифования также относятся высокое качество поверхности, незначительное усилие шлифования, высокая точность формы и короткое время шлифования. Химический и фазовый состав обрабатываемых материалов отличается высокой сложностью, в первую очередь обусловленной большим количеством легирующих элементов. С одной стороны, это позволяет значительно повысить жаропрочность, но с другой стороны, вносит свой отпечаток
втехнологический процесс последующей обработки материала. По мере повышения жаропрочности значительно снижается обрабатываемость сплавов. Стойкость инструмента при лезвийной обработке таких материалов в 10–20 раз ниже стойкости при обработке конструкционных сталей. Поэтому на сегодняшний день одним из эффективных методов обработки жаропрочных и жаростойких материалов является шлифование. Перечисленные факторы, безусловно, отражаются на эксплуатационных свойствах детали, поскольку остаточные напряжения
вповерхностном слое оказывают влияние на целый комплекс характеристик: точность обработки, статическую и динамическую прочность, а также стойкостькразличнымконтактным процессам.
Установлено, что к основным технологическим факторам, способствующим разрушению деталей газотурбинных двигателей (ГТД), относится ряд признаков технологической наследственности: повышенная степень наклепа, остаточные напряжения, локальные неоднородности структуры, наличие внутренних дефектов материала. Дефекты, приходящиеся на каждый из признаков, распределяются приблизительно следующим образом: остаточные напряжения – 35 %, неоднородность структуры – 30 %, повышенный наклеп – 25 %, высокая шероховатость – 5 %, другие причины – 5 %. Таким образом, важную роль в обеспечении заданных эксплуатационных свойств детали и ее надежности играет остаточное напряженнодеформированное состояние материала, являющееся результатом термомеханического воздействия на материал в ходе обработки. При этом практика производства ГТД показывает, что в технологическом процессе изготовления деталей особое место занимают операции шлифования, которые в некоторых случаях составляют большую часть операций, формирующих свойства поверхностного слоя.
11
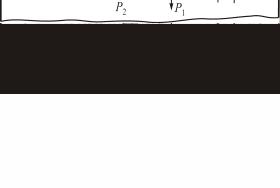
1.1.1. Особенности процесса стружкообразования при абразивной обработке
При шлифовании толщина среза измеряется сотыми и тысячными долями миллиметра. Процесс стружкообразования при снятии тонких стружек в значительной мере определяется отношением К = а / р, где а – толщина среза; р – радиус округления лезвия. Чем больше К, тем в более благоприятных условиях протекает процесс стружкообразования, он становится сходным с процессом стружкообразования при снятии толстых стружек.
Процесс стружкообразования при обработке пластичных металлов со снятием тонких стружек можно представить следующим образом (рис. 3). На округленном участке лезвия действуют нормальные силы Р1, Р2, Р3, ..., Рп. Составляющие этих сил Рс1, Рс2, …, Рсп обеспечивают скалывание элементов стружки.
Рис. 3. Процесс стружкообразования при шлифовании
В точке 1 толщина среза а = 0, также равна нулю сила Рс, а передний угол в этой точке 1 = 90°. С увеличением толщины среза при а1<а2<...<аn уменьшается отрицательный передний угол 1< 2<…< п иувеличиваются силы скалывания Рс1<Рс2<...<Рсп. При малых значениях силы, вызывающей скалывание элемента стружки, т.е. при малой величине К, срезания материала не произойдет. На этом участке слой материала, подлежащий удалению, будет сминаться, подвергаясь деформации. При этом возникают высокие удельные давления, измеряе-
12
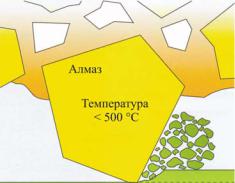
мые тысячами и десятками тысяч ньютон на миллиметр квадратный. Рассмотренную схему срезания тонкой стружки можно применять к процессу резания абразивным зерном. При шлифовании возникают мгновенные высокие температуры, вследствие чего обрабатываемый материал в зоне резания становится более пластичным. Это создает возможность срезания стружки округлым лезвием при довольно больших отрицательных передних углах, например при γ = –50°, где К = 0,5…0,6. При К = 1 процесс срезания стружки становится стабильным для всех условий. К примеру, электрокорунд зернистостью 16 имеет среднее значение ρ = 13·10–3 мм; у синтетического алмаза зернистостью 12 ρ = 2,2 · 10 –3 мм; у естественногоалмаза ρ= 3,3 · 10 –3 мм.
Таким образом, зерна алмаза являются более острыми, чем абразивные зерна. Это позволяет при использовании алмазного круга снимать более тонкие стружки.
Кроме того, чем острее лезвие, тем меньше нагрузка на зерно и ниже температура резания. Все это приводит к повышению точности и чистоты обрабатываемой поверхности. Наибольшее влияние на процесс шлифования оказывает толщина среза, так как она в значительной мере определяет удельную силовую нагрузку на абразивное зерно и износ круга. В связи с тем, что зерна в круге расположены хаотично, то как бы близко они не находились, работа двух соседних зерен происходит в разных плоскостях. В этом случае стружка имеет форму чечевицы (рис. 4).
Рис. 4. Вид стружки при обработке алмазным инструментом
13

Максимальная толщина среза (аmax, мм) определяется по формуле аmах = t ~ х ± у, где t – глубина резания; х – величина упругого отжатия шлифовального шпинделя и обрабатываемой детали в сторону уменьшения толщины стружки; у – некоторая часть выступа (+) или впадины (–), оставшейся неснятой при предыдущем проходе. Абразивные зерна выступают на поверхности круга на разную величину. Поэтому чем больше t, тем большее количество зерен участвуют
вработе и больше число царапин в единицу времени.
Сувеличением же числа царапин в единицу времени повышается чистота обработанной поверхности.
1.1.2. Процессы теплообразования при шлифовании
Большое влияние на процесс шлифования оказывает мгновенная температура в местах контакта абразивных зерен с обрабатываемым материалом. При высоких температурах (1500–1800 С) возможны изменения механических свойств и микроструктуры поверхностного слоя обрабатываемой детали (рис. 5), а также возникновение на отдельных участках обработанной поверхности напряжений, превосходящих предел прочности, что приводит к образованию трещин. В связи с этим необходимо стремиться, чтобы при шлифовании была минимальной. Мгновенная температура может быть подсчитана по следующей формуле:
1,064 p |
l Vê a , |
где – коэффициент трения; р – удельное давление на площадке контакта (определяется экспериментально); l – половина ширины прямоугольника, представляющего собой площадку контакта (определяется экспериментально);Vк – скорость шлифовального круга; а – коэффициент температуропроводности; – теплопроводность.
Исследованиями профессора Д.А. Маталина установлено, что самая большая температура концентрируется в тонком поверхностном слое. Снижение шлифования достигается применением смазочных охлаждающих технологических средств (СОТС) и выбором оптимальной характеристики шлифовального круга. При работе алмаз-
14
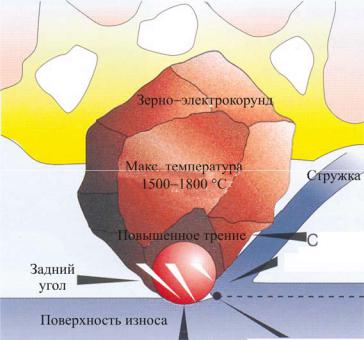
ным кругом мгновенная температура ниже, чем при шлифовании абразивным кругом. Это объясняется тем, что алмазное зерно острее абразивного, а поэтому, естественно, прилагаются меньшие усилия резания. Кроме того, алмаз обладает хорошей теплопроводностью, что способствует быстрому отводу тепла из зоны резания. Все известные исследования, направленные на предотвращение тепловых дефектов при шлифовании сплавов, склонных к тепловым дефектам, могут быть охарактеризованы с помощью схемы (см. рис. 5).
Рис. 5. Схема теплообразования при плоском шлифовании
Высокая контактная температура в зоне резания при шлифовании является не только причиной возникновения прижогов, но и главной причиной формирования в поверхностном слое заготовки остаточных напряжений растяжения, отрицательно влияющих на усталостную прочность деталей.
15
В результате анализа существующих работ определено, что одним из наиболее эффективных способов подачи СОТС при шлифовании сплавов, склонных к тепловым дефектам, является подача СОТС через впадины прерывистого шлифовального круга. Применение кругов с прерывистой рабочей поверхностью позволяет подавать СОТС к заготовке в момент прерывания резания, снизить теплонапряженность процесса и уменьшить вероятность появления шлифовочных дефектов на поверхности заготовки. Расчет и проектирование прерывистых шлифовальных кругов наиболее подробно рассмотрены в работах профессора А.В. Якимова [9]. На рис. 6 представлены основные факторы, способствующие теплообразованию в зоне резания и последующему образованию дефектов поверхностного слоя деталей в виде шлифовочных трещин и прижогов.
Шлифовочные прижоги. Прижоги бывают видимые и невидимые невооруженным глазом. Видимые прижоги определяются по цветам побежалости, являющимся следствием образования оксидной пленки, толщина которой составляет доли микрометра. Эти прижоги характеризуются наличием больших объемов металла с измененной структурой. Невидимые прижоги могут быть определены путем травления в растворах соляной или азотной кислот. Характерные виды дефектов – прижоги и трещины, полученные при неправильном выборе шлифовальных круговирежимовобработки, представлены нарис. 7.
Низкая теплопроводность обрабатываемого металла также является одной из причин появления прижогов и трещин. Наибольшей теплопроводностью обладает чистое железо. Углерод понижает теплопроводность сплава. Введение в сталь легирующих элементов также понижает ее теплопроводность. При этом минимальное влияние оказывает кобальт, более сильно понижает теплопроводность хром и никель, затем следуют Al, Si и Мn.
Структурные составляющие по теплопроводности могут быть расположены в следующий ряд: аустенит, мартенсит закалки и отпуска, перлит (сорбит, троостит), причем теплопроводность растет от аустенита к перлиту. Таким образом, образование вторично закаленного слоя с повышенным содержанием аустенита способствует появлению шлифовочных трещин.
16
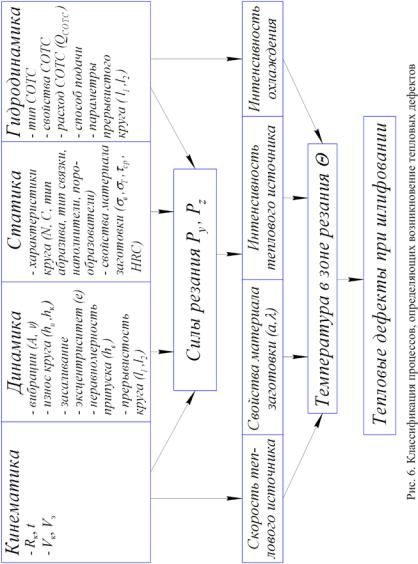
17
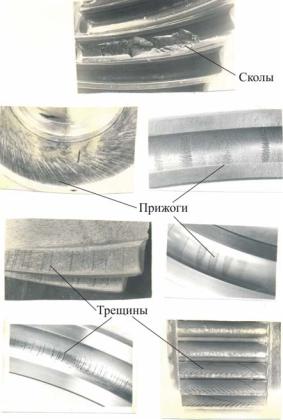
Рис. 7. Виды шлифовочных трещин и прижогов при шлифовании
Как показали многочисленные исследования и производственный опыт, в качестве допустимой степени прижога можно задавать глубину распространения от шлифованной поверхности зоны вторичного отпуска, которая определяется глубиной распространения температуры 500 °Ñ , при которой исходная структура принимает
кратковременный без выдержки отпуск.
В зависимости от степени ответственности шлифуемых деталей величина допустимой глубины распространения прижога может уточняться при проведении натурных усталостных испытаний на прочность для различных деталей машин.
18
Прижоги делятся на два класса: прижоги с отпуском и прижоги
сподкалкой. Прижоги с отпуском возникают при температуре шли-
фуемой поверхности, не превышающей критическую точку Ac1. При этом глубина прижогов отпуска может достигать 3–4 мм. Прижоги
сподкалкой возникают при разогреве шлифуемой поверхности выше температуры фазовых превращений. Глубина подкаленного слоя достигает 0,5 мм. Под закалившимся слоем находится зона отпуска.
Кроме прижогов отпуска и закалки существует ожог неполной
закалки, появляющийся при нагреве выше точки Ac1, но при скорости охлаждения ниже критической. При этом верхний сильно отпущенный слой лежит на закаленном слое, который, в свою очередь, переходит снова в отпущенный.
Существуют еще штриховые циклические прижоги – отдельные участки с измененной структурой, появляющиеся через определенные расстояния. Появление этих прижогов связывают с вибрацией или дисбалансом шлифовального круга.
Металлографические исследования показали, что слой вторичной закалки представляет собой смесь аустенита с мартенситом, отпущенный слой имеет структуру троостомартенсита, переходящего постепенно в структуру основного металла. Рентгенографические исследования распределения остаточного аустенита по глубине от поверхности показали повышенное содержание его в слое вторичной закалки (31 %) по сравнению с основным металлом. В отпущенном слое количество остаточного аустенита несколько понижается.
Шлифовочные трещины. Кроме прижогов на поверхности детали после шлифования могут появиться дефекты другого вида – трещины. Появление трещин является результатом действия суммарных внутренних остаточных напряжений в металле, возникающих при наличии неоднородной пластической деформации металла в различных зонах поверхностного слоя детали. Неоднородность деформации металла зависит как от теплового расширения и сжатия при быстром и неравномерном нагреве и охлаждении отдельных объемов металла детали, так и от неравномерных объемных изменений, вызываемых структурными превращениями. Отсюда ясно, что появление прижогов, связанное со
19
структурными превращениями и резким градиентом температур по глубине от шлифуемой поверхности, должно сопровождаться возникновением внутренних напряжений вповерхностном слое детали.
Шлифовочные трещины располагаются чаще всего перпендикулярно направлению шлифования. При особо форсированных режимах шлифовочная сетка трещин искажается, и к трещинам, расположенным перпендикулярно действию шлифовального круга, добавляются трещины, расположенные в различных направлениях. Глубина шлифовочных трещин 0,1–0,4 мм. Г.Б. Лурье отмечает, что опасность появления трещин зависит от характера шлифования. Она наибольшая при шлифовании торцом круга и наименьшая при круглом шлифовании. Принято различать три температуры шлифования:
1) среднюю температуру прошлифованной поверхности 0 ,
близкую в условиях равновесного теплового режима к средней температуре детали, так как благодаря сравнительно большому объему и хорошей теплопроводности металла установившаяся температура поверхности даже без применения охлаждения обычно не бывает высокой
0 20 150 °Ñ ;
2)контактную температуру в зоне шлифования, осреднен-
ную по ширине пятна контакта между шлифовальным кругом и де-
талью 300 1200 °Ñ ; 3) мгновенную температуру резания отдельными абразивными
зернами ç , обычно превышающую температуру закалки шлифуемой стали и даже достигающую температуры ее плавления
ç 1000 1500 °Ñ .
Появление прижогов и трещин при шлифовании непосредственно связано с увеличенной контактной температурой, превышающей
допустимую величину .
Теплофизические характеристики шлифуемых материалов довольно значительно зависят от температуры в зоне резания.
Общая механическая энергия, затрачиваемая на резание при шлифовании, практически полностью преобразуется в тепловую, которая, в свою очередь, распределяется между шлифовальным кругом, охлаж-
20