
Выбор абразивных инструментов и режимов резания для высокоэффективно
..pdfрунд сослужил добрую службу промышленности до внедрения искусственных материалов высокого качества, появившихся благодаря развитию металлургии. Корунд имеет сравнительно низкие режущие свойства и поэтому сегодня мало применяется в абразивной промышленности. Кроме того, залежи корунда в природе ограничены. Абразивные инструменты характеризуются материалом зерен и их величиной, видом связки, твердостью, структурой, формой и размерами. Алмазные круги и бруски дополнительно характеризуются конструкцией и маркой алмазов. Более широкое применение в промышленности в настоящее время имеют искусственные абразивные материалы: электрокорунд, карбид кремния (карборунд), карбид бора, силикокарбид бора. Карбид бора В4С получают при плавке борной кислоты В2О3 и нефтяного кокса в электропечах. Применяется в виде порошков или паст для доводки твердоплавкого инструмента.
2.2.1. Естественные абразивные материалы
Гранат (маркировка 92Е) – минерал, представляющий собой соединение алюминия, железа, хрома, кальция, магния и марганца с кремнекислотой. В зависимости от примесей гранат бывает темнокрасного (пироп), красного (альмандин), оранжево-желтого (спессартин), буро-красного, черного (андрадит) или изумрудно-зеленого (уваровит) цветов. Микротвердость 1300–1650 г/см3, твердость по Моосу 6,5–7,5; плотность 3,5–4,2 кгс/см2. Получают шлифзерно
имикропорошки. Шлифзерно используют для изготовления шлифовальной шкурки, применяемой при обработке дерева, пластмасс, кожи, а также в свободном состоянии для струйной обработки материалов. Микропорошки – в свободном виде при обработке стекла
идругих материалов.
Корунд – горная порода, состоящая в основном из кристаллической окиси алюминия 85–95 % (Аl2O3) с небольшой примесью кварца и других минералов. Цвет зависит от примесей: красный, бурый, желтый, синий, серый или белый. Плотность 3,9–4,1 г/см3, микротвердость 1900–220 кгс/мм2; твердость по Моосу 9,0. Изготавливают шлифпорошки для производства абразивного инструмента и микропорошки для полировки стекла и металла.
61
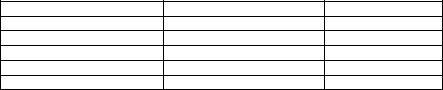
Кремень (маркировка 81Кр) – плотная горная порода, состоящая из кремнезема и микроскопических зерен кварца и примесей. Цвет от светло-серого до черного. Микротвердость 1000–1100 кгс/мм2; плотность 2,5–2,6 г/см3. Применяется в виде микропорошков и для изготовления шлифовальной шкурки, идущей для обработки кожи, эбонита, дерева.
Наждак – тонкозернистая горная порода, состоящая из корунда (до 30–60 %), магнетита с примесью гематита и кварца. Используется для шлифования и полирования в виде микропорошков свободным зерном. Наждак можно отнести к древнейшим абразивным материалам, используемымчеловеком, в частности, длямельничныхжерновов.
2.2.2. Искусственные абразивные материалы
Искусственные абразивные материалы отличаются большей стабильностью физико-механических свойств по сравнению с естественными. В настоящее время искусственные абразивные материалы практически полностью вытеснили в промышленности природные. К искусственным абразивным материалам относятся алмаз синтетический, карбид бора, карбид кремния, техническое стекло, эльбор (борозон), электрокорунд и др. Сравнительная характеристика механических свойств абразивных материалов приведена в табл. 1.
Таблица 1 Механические свойства искусственных абразивных материалов
Абразивный материал |
Микротвердость НV, кгс/мм2 |
Термостойкость, °С |
Алмаз |
10000 |
700–800 |
Кубический нитрид бора |
9000 |
до 1200 |
Карбид бора |
3700–55000 |
700–800 |
Карбид кремния |
3300–3600 |
1300–1400 |
Электрокорунд |
2000–2300 |
1700–1800 |
Карбид бора (В4С) – абразивный материал, представляющий собой химическое соединение бора с углеродом, получаемое методом плавки в электродуговых печах при температуре 2000–2350 °С. Твердость по Моосу 9,32; микротвердость 4000–4500 кгс/мм2; плот-
62
ность 2,48–2,52 кгс/см2, имеет большую хрупкость. Применяется в виде порошков и паст для доводки режущего инструмента из карбидовольфрамовых и карбидотитановых сплавов.
Карбид кремния (марки: 64С–62С и 55С–52С) – материал, представляющий собой химическое соединение кремния с углеродом (SiC: 70 % кремния и 30 % углерода), твердость по Моосу 9,1; микротвердость 3300–3600 кгс/мм2. Карбид кремния получают в печах при температуре 1800–1850 °С при плавке кварцевого песка и нефтяного кокса из кокса, антрацита, т.е. из материалов, богатых кремнеземом и высоким содержанием углерода. Плотность карбида кремния 3,48–3,52 г/см3. Карбид кремния разделяется на черный 54С (95–97 % SiС) и зеленый 63С (98–99 % SiС). Лучше из них зеленый, он имеет большую твердость и лучшие режущие кромки. Зеленый карбид кремния содержит меньше примесей, более хрупок, имеет более высокую абразивную способность. Широко используется для всех видов шлифовального инструмента. Зерна 54С имеют более высокую твердость, чем электрокорунд. Недостатки карбида кремния – высокая хрупкость и малая прочность. Поэтому при обработке сталей он почти не применяется. Карбид кремния применяется при абразивной обработке хрупких материалов: чугунов, бронзы; тугоплавких сплавов, металлоиминералокерамики.
Электрокорунд. Большая часть (~ 80 %) абразивного инструмента изготавливается из электрокорунда. Электрокорунд – материал, состоящий из кристаллической окиси алюминия (α-Аl2O3) и небольшого количества примесей. Промышленность производит несколько разновидностей электрокорунда в зависимости от процентного содержания А12О3, в том числе нормальный, белый, хромистый, титанистый, циркониевый, моно- и сферокорунд. Электрокорунд получают методом электрической плавки в дуговых печах при температуре 2000–2500 °С из материалов, богатых окисью алюминия (бокситы, глинозем). Электрокорунд (α-Аl2O3) является материалом высокой твердости из-за особой структуры атомной решетки. В этой решетке четыре атома алюминия тетраэдрически расположены вокруг атома кислорода, а каждый атом алюминия октаэдрически окружен шестью атомами кислорода. Тип решетки ромбоэдрический.
63
Выпускаются несколько разновидностей электрокорунда в зависимости от содержания примесей:
электрокорунд нормальный (94–96 % А12О3) (марки: 16А–12А);
электрокорунд белый (97–99 % А12О3) (марки: 25А–22А);
электрокорунд хромистый (марки: 34А–32А);
электрокорунд титанистый 37А(содержит 97 % А12О3 и2 % Тi2);
монокорунд, зерна которого представляют отдельные кристаллы и имеют большое число режущих граней (марки: 45А, 44А).
Титанистый электрокорунд представляет собой соединение
А12О3 + 1,5 % ТiO2, отличается от нормального электрокорунда большей прочностью, вязкостью и стабильностью свойств, что положительно для доводочно-притирочных работ, а также при черно-
вом шлифовании. Цвет кругов темно-коричневый. Плотность
3,95–4,05 г/см3.
Наиболее широко используется нормальный электрокорунд
(маркировка 16А–12А), получаемый методом плавки в электродуговых печах из бокситов (микротвердость 1900–2000 кгс/мм2, плотность 3,85–3,95 г/см3. Содержит примеси – кремнекислоту, окись титана, окись железа, окись кальция. Эти примеси ухудшают абразивную способность. Форма зерен изометрическая, имеет большие радиусы округления и углы при вершине. Рекомендуется применять для шлифования 14А и 15А, для обдирочных работ 12А и 13А. Цвет темно-серый, почти черный.
Белый электрокорунд (маркировка 25А–22А) – материал, получае-
мый методом плавки в электродуговых печах из глинозема (микротвердость 2000–2100 кгс/мм3, плотность 3,9–4,00 г/см3). Содержит намного меньше примесей, поэтому обладает лучшей режущей способностью, чем нормальный электрокорунд. Применяется для ответственных видов тонкого шлифования. Изготавливается в виде шлифовальных кругов, зерна, порошков и микропорошков. Зерна имеютостроугольнуюформу,
смножеством острых и хрупких граней, поэтому эффективно применяется при тонкомшлифовании снебольшойнагрузкой.
Корунд циркониевый (маркировка 38А) – разновидность электроко-
рунда с примесью окиси циркония ZrO2 (от10 до 45 %) (микротвердость 2300–2400 кгс/мм2, плотность 4,05–4,15 г/см3). Высокая прочность.
64
Применяется в абразивном инструменте для тяжелых обдирочных операций. Из этих видов электрокорундов производится до 80–90 % абразивного инструментасамогоразного назначения. Цвет голубой.
Монокорунд (маркировка 45А–43А) – материал, получаемый методом оксисульфидной плавки в электродуговых печах или парофазным синтезом. Шлифзерно представлено однородными монокристаллами правильной формы без острых выступов в отличие от белого электрокорунда, имеющего поликристаллическую структуру, что обеспечивает высокую режущую способность. Он получается из боксита оксисульфидным способом в виде зерен, состоящих из изометрических кристаллов корунда различной величины. Сущность способа получения монокорунда состоит в сплавлении боксита с сернистым железом и восстановителем – антрацитом или коксом в электропечах. Рекомендуется для обработки с большими съемами без прижогов. Выпускается в небольшом количестве.
Сферокорунд (маркировка ЭС) – абразивный материал в виде полых корундовых сфер, используется для обработки мягких и вязких материалов: кожи, резины, пластмассы, цветных металлов и т.д.
Формокорунд, SG-абразивы, кубитрон и др. – абразивные мате-
риалы, состоящие из микрочастиц корунда (менее 5 мкм), получаемые методами золь-гель-технологии, или корундовой спеченной керамики. Отличаются высокой режущей способностью и самозатачиваемостью, увеличенным интервалом между правками. Особенности разрушения и износа обычного и спеченного электрокорундов приведены на рис. 43.
Борсиликарбид (BI) в отличие от карбида бора не содержит вредной примеси графита, отличается большей стабильностью свойств, более прочен и дешевле. На операциях доводки показал на 30–40 % более высокую производительность, чем карбид бора.
Окись хрома – порошок темно-зеленого цвета для доводки. Получается из бихромата калия с примесью серы.
Окись железа (крокус) – тонкий полировальный порошок, состоящий в основном из кристаллической окиси железа. Получается переработкой железного купороса и щавелевой кислоты.
65
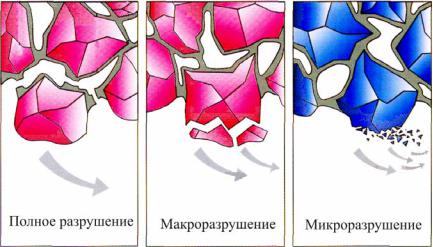
Рис. 43. Схема разрушения при износе зерен электрокорунда (розовые) и спеченного корунда 93А (голубые)
Техническое стекло (маркировка 71F) – бой листового и бутылочного стекла, после дробления и рассева получают шлифзерно и шлифпорошки, применяемые для изготовления шлифовальной шкурки для обработки дерева.
В табл. 2 приведены условные обозначения основных абразивных материалов, применяемых в России и других странах.
2.2.3. Сверхтвердые инструментальные материалы
Одним из направлений совершенствования режущих свойств инструментов, позволяющим повысить производительность труда при механической обработке, является повышение твердости и теплостойкости инструментальных материалов. Наиболее перспективными
вэтом отношении являются синтетические сверхтвердые материалы на основе алмаза или нитрида бора. Фундаментальные исследования
вобласти высоких давлений привели к созданию и освоению промышленного производства таких сверхтвердых материалов (СТМ), как синтетический алмаз и кубический нитрид бора.
66

Таблица 2
Обозначение основных абразивных материалов
|
Абразивный материал |
Россия |
США |
Англия |
Франция |
ФРГ |
Италия |
Австрия |
Швейцария |
Япония |
Чехия |
|
Абразивное зерно на |
Эльбор |
Боразон |
|
|
J11B, |
|
|
|
|
CBN |
|
основе кубического |
|
|
|
|
J43soI, |
|
|
|
|
|
|
нитрида бора |
|
|
|
|
B10A |
|
|
|
|
|
|
|
Эльбор Р |
Боразон |
|
|
|
|
|
|
|
|
|
|
|
резцовый |
|
|
|
|
|
|
|
|
|
Карбид кремния |
62С; 63С; |
39С; GC |
C |
66C; 4С |
SiCg; SCg |
CVC; |
C; CV |
Vitoсarbon |
GC |
C49 |
|
зеленый |
64С |
|
|
|
|
CW |
|
|
|
|
|
Карбидкремниячерный |
52С; 53С; |
37С; С |
BC |
55C; C |
SiC; SC21 |
CNC; C |
1C; C |
Vitoсarbon |
C |
C48 |
|
|
54С; 55С |
|
|
|
|
|
|
|
|
|
|
Монокорунд |
43А; 44А; |
32А |
|
|
|
|
|
|
|
90МА |
|
|
45А |
|
|
|
|
|
|
|
|
|
|
Электрокорунд цирко- |
68А |
68А; 66А; |
|
|
|
|
14F; |
|
|
97 ЕА |
|
ниевый |
|
ZS; ZF |
|
|
|
|
24А; |
|
|
|
|
|
|
|
|
|
|
|
28А |
|
|
|
|
Электрокорунд тита- |
37А |
|
|
|
|
|
|
|
|
|
|
нистый |
|
|
|
|
|
|
|
|
|
|
|
Электрокорунд хроми- |
32А; 33А; |
5А; 25А |
|
|
|
|
88А |
|
|
|
|
стый |
34А |
|
|
|
|
|
|
|
|
|
|
Электрокорунд вана- |
|
ЕА |
|
|
|
|
|
|
|
|
|
диевый |
|
|
|
|
|
|
|
|
|
|
|
Электрокорунд белый |
22А; 23А; |
38А; АА |
WA |
44A; 99А |
EK; EKv |
OBA; |
89A; |
Vitoneva |
WA |
99А; |
|
|
24А; 25А |
|
|
|
|
WA |
WA |
|
|
А99 |
|
Электрокорунд нор- |
12А; 13А; |
А; 16А; |
А |
А |
NK |
ONA; A |
A; 10А |
Vitoborund |
А; А-40; |
96А; |
67 |
мальный |
14А; 15А; |
44А; 57А |
|
|
|
|
|
|
ТА |
А96 |
|
16А |
|
|
|
|
|
|
|
|
|
|
|
|
|
|
|
|
|
|
|
|
|
67
Внастоящее время эти СТМ нашли самое широкое применение
впроцессах абразивной обработки широкого спектра материалов: твердого сплава, керамики, стали и сплавов, стекла, камня и других материалов. Уникальные свойства СТМ предопределили их высокую эффективность в процессах обработки различных деталей и режущих инструментов из труднообрабатываемых материалов.
Алмаз представляет собой кристаллическую модификацию углерода. Кристаллическая решетка алмаза кубическая. Она содержит 18 атомов углерода, из которых 8 расположено в вершинах куба, 6 – в центрах его граней и 4 – в центрах восьми кубов, образованных делением элементарной кубической ячейки тремя взаимно перпендикулярными плоскостями. Каждый атом в решетке связан ковалентной связью с четырьмя соседними атомами. Атом углерода в алмазе обладает чрезвычайно прочными ковалентными связями, которые обеспечивают его уникальныесвойства и, прежде всего, высокуютвердость.
Алмазы и алмазные инструменты широко используются при обработке деталей из различных материалов. Для алмазов характерны исключительно высокая твердость и износостойкость. По абсолютной твердости алмаз в 4–5 раз тверже твердых сплавов и в десятки и сотни раз превышает износостойкость других инструментальных материалов при обработке цветных сплавов и пластмасс. Кроме того, вследствие высокой теплопроводности алмазы лучше отводят теплоту из зоны резания, что способствует гарантированному получению деталей с бесприжоговой поверхностью. Однако алмазы весьма хрупки, что сильно сужает область их применения. Природные алмазы кристаллизовались на большой глубине при огромном давлении земных недр и высокой температуре (2000–2500 °С) из расплавленной магмы, содержащей углерод.
Алмаз – самый твердый из всех известных в природе материалов. Его микротвердость по Виккерсу, измеренная алмазной пирами-
дой с углом между противоположными гранями 136 , составляет 10 000 кгс/мм2. До 80 % добываемых алмазов используется на технические цели (20 % идет на изготовление ювелирных изделий). Из технических алмазов изготавливаются инструменты для шлифова-
68
ния, доводки и резки различных материалов, для бурения горных пород, обработки камня, сверления стекла и т.д. Природный алмаз А – минерал, состоящий из кристаллического углерода.
Природные технические алмазы содержат небольшие примеси окислов алюминия, железа, кальция, кремния, марганца, которые придают им различный цвет. Атомы углерода в кристаллической решетке алмаза очень прочно связаны, что обеспечивает высокую твердость и износостойкость. Твердость алмаза по шкале Мооса равна 10, микротвердость 10060 кгс/мм2, модульупругости9 · 104 кгс/см2, плотность3,52 г/см3.
Недостатки алмазов: высокая хрупкость, большая способность к адгезии с титаном, сталью и другими металлами, сравнительно низкая теплостойкость (800–900 °С). Натуральные технические алмазы применяются для изготовления алмазных резцов, наконечников к приборам, фильер для волочения, для правки шлифовальных кругов. Теплопроводность алмаза на порядок выше теплопроводности других абразивных и инструментальных материалов, а коэффициент линейного расширения в 5–10 раз меньше. На воздухе алмаз сгорает при температуре свыше 850 °С. Интенсивность окисления зависит от размера зерна и степени его совершенства. Мелкие зерна и зерна с дефектами сгорают быстрее. При высокой температуре алмаз способен к активному диффузионному взаимодействию с некоторыми металлами, в особенности с железом и сталями. Масса алмазов измеряется в каратах (1 карат равен 0,2 г). Плотность составляет 3,48–3,56 г/см3. Алмаз – самый твердый в природе минерал (105 МПа), устойчивый к физическим и химическим воздействиям. Теплостойкость алмаза сравнительно невысока ~ 700 °С (в среде кислорода).
Алмазы бывают ювелирные и технические. На технические цели идет 80 % природных алмазов. Они используются при изготовлении шлифовальных кругов и паст, а также для алмазно-металлических карандашей. Технические алмазы разделяются на бортсы, балласы и карбонадо. Наиболее лучшие из них – карбонадо. Это весьма тонкозернистые, твердыеиплотныекристаллы, имеющиеострыеребра.
Алмаз синтетический (маркировка А – АСВ, АСР) – минерал, состоящий из кристаллического углерода с кубической структурой решетки. Для изготовления режущих инструментов основное применение
69
получили искусственные алмазы, которые по своим свойствам близки к естественным. Учитывая высокую стоимость природных алмазов, а также недостаток их для промышленного применения, Институт физики высоких давлений Академии наук СССР в 1960 году синтезировал алмаз в лабораторных условиях, а Киевский институт сверхтвердых материалов в 1961 году начал промышленное производство искусственных алмазов из графита при высоких давлениях и температуре. Синтетические алмазы имеют те же химические и физико-механические свойства, чтои природные.
При больших давлениях и температурах в искусственных алмазах удается получить такое же расположение атомов углерода, как и в естественных. При изготовлении инструмента основной характеристикой является содержание или концентрация алмаза в алмазоносном слое. 100%-й концентрации соответствует его содержание в количестве 4,39 карата в 1 см3 алмазоносного слоя. Выпускают инструмент с концентрацией 50, 75, 100 %, по заказу – 25, 125 и 150 %. Масса одного искусственного алмаза обычно составляет 1/8…1/10 карата. Вследствие малости размеров искусственных кристаллов они непригодны для изготовления таких инструментов, как сверла, резцы и другие, а поэтому применяются при изготовлении порошков для алмазных шлифовальных кругов и притирочных паст.
Синтетические алмазы АС получают в виде мелких кристаллов, размерыобычно неболее1 мм. Синтезалмазов происходит врезультате воздействия на графит высоких давлений (до 50 000–100 000 кгс/см2) и высоких температур (до 2500 °С). В присутствии металлического катализатора происходит перекристаллизация углерода из гексагональной структуры графита в кубическую структуру алмаза. Время синтеза составляет от десятков секунд до нескольких часов. Синтетические алмазы в виде порошков в зависимости от прочности, хрупкости и размеров кристаллов делятся на пять марок: низкой прочности (АСО), повышенной прочности (АСР), высокой прочности (АСВ), монокристальные (АСК иАСС) идве маркимикропорошковАСМ иАСН.
Алмазы АСО применяют в алмазно-абразивном инструменте на органической связке для чистовых и доводочных операций. Алмазы хорошо удерживаются связкой и обладают высокой самозатачивае-
70