
Выбор абразивных инструментов и режимов резания для высокоэффективно
..pdf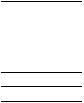
|
|
|
Таблица 2 4 |
Концентрация абразивных паст КТ |
|
||
|
|
|
|
Зернистость порошка КТ, мкм |
Массовая доля порошка КТ в пасте, % |
||
|
Н |
|
П |
630/500–50/40 |
50 |
|
60 |
60/40–14/10 |
30 |
|
40 |
10/7–1/0 |
20 |
|
30 |
В зависимости от состава основы пасты выпускаются:
1.Смываемые органическими (О) растворителями (керосином, бензином, спиртом и т.п.), которые разбавляются индустриальными маслами, керосином или их смесью.
2.Смываемые водой (В) – разбавляются и смываются водой.
3.Универсальные, смываемые как водой, так и органическими растворителями (ВО), разбавляются и смываются дистиллированной водой, спиртом, индустриальными маслами, бензином, керосином.
Выбор зернистостей и расход пасты зависят от вида обработки
(табл. 25).
|
|
|
|
Таблица 2 5 |
Расход пасты в зависимости от ее зернистости |
||||
|
при различных видах обработки |
|
||
|
|
|
|
|
Вид обработки |
Зернистость |
Расход пасты, |
Шероховатость поверхности |
|
|
пасты, мкм |
г/см2 |
Rа, мкм |
|
|
|
|
до обработки |
после обработки |
Шлифование, |
630/500–50/40 |
0,8–1,5 |
1,6 |
0,32 |
черновая доводка |
|
|
0,32 |
|
Получистовая |
60/40–20/14 |
0,4–1,5 |
0,125 |
|
доводка |
|
|
0,125 |
|
Чистовая доводка |
14/10–5/3 |
0,2–0,6 |
0,05 |
|
Полирование |
3/2–1/0 |
0,1–0,4 |
0,05 |
0,025 |
В зависимости от зернистости порошка карбида титана абразивная способность паст и шероховатость обработанной поверхности указаны в табл. 26.
Каждая изготовленная партия абразивных паст из порошков КТ проходит испытания на абразивную способность и шероховатость обработанной поверхности, на консистенцию паст, согласно методикам, приведенным в ТУ 2-037-273–88.
151

Таблица 2 6 Эксплуатационные показатели работы паст
|
|
Абразивная способность пасты, |
Шероховатость поверхно- |
|||
Зернистость порошка |
|
|
мг, не менее |
сти Rа, мкм, не более |
||
КТ, мкм |
|
Н |
|
П |
до обработки |
после |
|
|
|
|
обработки |
||
|
|
|
|
|
|
|
630/500–200/160 |
– |
|
– |
– |
– |
|
160/12 |
|
50 |
|
55 |
– |
– |
125/100 |
|
45 |
|
50 |
– |
– |
100/80 |
|
40 |
|
45 |
– |
– |
80/63 |
|
37 |
|
43 |
– |
– |
63/50 |
|
34 |
|
40 |
– |
– |
50/40 |
|
30 |
|
38 |
– |
– |
60/40 |
|
29 |
|
37 |
0,32 |
0,25 |
40/28 |
|
28 |
|
36 |
0,25 |
0,20 |
28/20 |
|
26 |
|
34 |
0,20 |
0,16 |
20/14 |
|
22 |
|
32 |
0,16 |
0,125 |
14/10 |
|
19 |
|
28 |
0,125 |
0,100 |
10/7 |
|
18 |
|
27 |
0,100 |
0,080 |
7/5 |
|
14 |
|
20 |
0,080 |
0,063 |
5/3 |
|
11 |
|
16 |
0,063 |
0,050 |
3/2 |
|
– |
|
– |
0,050 |
0,040 |
2/1 |
|
– |
|
– |
0,040 |
0,032 |
1/0 |
|
– |
|
– |
0,032 |
0,025 |
Для эффективного использования паст из порошков карбида титана необходимо применять притиры из чугуна СЧ 18-36, стали, меди, латуни, стекла ЛН 5, дерева (березы, дуба, бука), винипласта, фетра, замши, текстолита и др.
Пример условного обозначения пасты из порошков карбида титана зернистостью 10/7 нормальной концентрации, смываемой органическими растворителями, мазеобразной консистенции: КТ 10/7
НОМ ТУ 2-037-273–88.
5.4. Выбор абразивных брусков для хонингования
Характеристики алмазных хонинговальных брусков (АБХ) выбирают в зависимости от вида обрабатываемого материала, требований к точности и чистоте обработки, припуска на обработку, а также с учетом производительности и себестоимости процесса хонингования. Бруски, как правило, состоят из корпуса и закрепленного на нем алмазоносного слоя (рис. 69).
152

Рис. 69. Общий вид алмазных хонинговальных брусков (L, W, T – длина, ширина, высота бруска; X – толщина алмазного слоя; R – радиус слоя)
Основными характеристиками АБХ являются: размеры бруска; марка связки; марка и зернистость алмаза; концентрация алмаза в алмазном слое.
Условное обозначение брусков включает в себя все их геометрические размеры и характеристики алмазоносного слоя. Например,
АБХ 75-5-3-1,5-30 АС 65 160/125 100 % М2-01: АБХ – алмазный брусок хонинговальный; 75 – длина бруска (L); 5 – ширина бруска (W); 3 – высота бруска (Т); 1,5 – толщина алмазного слоя (X); 30 – радиус (R); АС 65 – марка синтетического алмаза; 160/125 – зернистость; 100 % – концентрация; М2-01 – связка.
На ЗАО «Полтавский алмазный инструмент» освоено производство АБХ со сплошным алмазоносным слоем (монослой). Данные бруски идеально подходят для массового и серийного производства. Больший ресурс сокращает количество переустановок брусков в хонинговальную головку (далее – хонголовка), увеличивая производительность хонингования в целом.
Как правило, перед хонингованием необходимо произвести подготовку (шлифовку) поверхности брусков в сборе с хонголовкой, устранив криволинейность (прогиб) поверхности алмазного слоя брусков (рис. 70). Отсутствие стрелы прогиба бруска по длине значительно сокращает время на подготовку хонголовки, позволяя снизить затраты на вспомогательные операции хонингования.
При выборе ширины алмазных брусков в хоне целесообразно принимать ширину исходя из соотношения
W · N = (0,15…0,35)· D,
где W – ширина бруска; N – количество брусков; D – диаметр обрабатываемого отверстия.
153
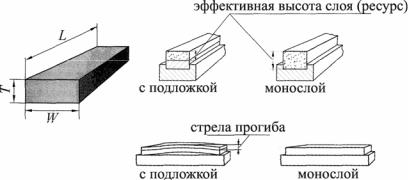
Рис. 70. Схема подготовки поверхности брусков в сборе с хонголовкой и устранения криволинейности (прогиба) поверхности алмазного слоя брусков
Длину бруска L выбирают в зависимости от соотношения между длиной обрабатываемого отверстия – Ld и диаметром отверстия D:
при Ld /D<1 |
L = (0,7…1) · Ld; |
при 1,5 > Ld /D > 1 |
L = (0,60…25) · Ld; |
при 3 ≥ Ld /D > 1,5 |
L = (0,5…0,75) · Ld. |
Выбор связок рабочего слоя АБХ. Основные требования к связ-
кам для хонингования следующие: надежное закрепление алмазного зерна, ограничения максимальной силы резания на зерне вследствие микровыкрашивания, образования пространства для размещения и выхода стружки; минимальное внешнее трение; хорошая теплопроводность.
Выбор марки связки зависит от обрабатываемого материала, требований к качеству обработанной поверхности, производительности процесса хонингования, а также условий хонингования (СОЖ и т.д.):
М2-01 – хонингование чугунов, сталей, твердых сплавов; М5-01 – хонингование закаленных легированных сталей; М5-04 – хонингование сталей и чугунов; М5-05 – хонингование изделий из легированных сталей;
М5-06 – хонингование серых и легированных чугунов; В2-04 – чистовое хонингование деталей дизельных двигателей.
Алмазоносный слой изготавливается из шлифпорошков и микропорошков на металлических и органических связках.
154
Выбор концентрации и зернистости хонинговальных брусков.
В зависимости от вида хонингования, обрабатываемого материала, требований к качеству обрабатываемой поверхности и припуска на обработку выбирают концентрацию, марку алмазного порошка и зернистость порошка. Чем выше размер алмазного порошка (зернистость), тем выше параметры шероховатости и производительность. При съеме больших припусков применяется алмазный порошок крупной фракции и меньшей концентрации, а для получения высокой чистоты обрабатываемой поверхности – алмазный порошок мелкой фракции и большей концентрации.
Рекомендуемые припуски и достигаемая шероховатость обрабатываемой поверхности для чугунов и сталей в зависимости от зернистости алмазного порошка приведены в табл. 27.
Таблица 2 7
Припуск и шероховатость обрабатываемой поверхности в зависимости от зернистости хонинговальных брусков
Зернистость хон. брусков, мкм |
Припуск, мм |
Шероховатость обрабатывае- |
|
|
мой поверхности Rа, мкм |
|
Сталь |
|
400/315–315/250 |
0,15 |
5 |
250/200–200/160 |
0,10 |
2,5 |
160/125–125/100 |
0,08 |
2,5–1,32 |
100/80–80/63 |
0,06 |
1,32–0,63 |
63/50–50/40 |
0,01 |
0,63–0,32 |
40/28–28/20 |
0,001 |
0,32–0,16 |
20/14–14/10 |
0,005 |
0,16–0,08 |
|
Чугун |
|
400/315–315/250 |
0,20 |
5 |
250/200–200/160 |
0,15 |
5–2,5 |
160/125–125/100 |
0,10 |
2,5 |
100/80–80/63 |
0,08 |
2,5–1,75 |
63/50–50/40 |
0,03 |
1,32–0,63 |
40/28–28/20 |
0,002 |
0,63–0,32 |
20/14–14/10 |
0,01 |
0,32–0,16 |
Выбор режимов хонингования. Назначение режимов хонинго-
вания состоит в выборе давления, с которым бруски прижимаются к обрабатываемой детали (Р, кгс/см2), скорости возвратно-поступа-
155
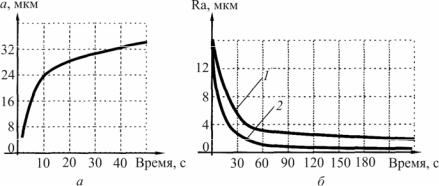
тельного перемещения хона вдоль оси шпинделя (V1, м/мин) и окружной скорости хона (V, м/мин).
Скорость возвратно-поступательного движения хонголовки на предварительных операциях для обеспечения наибольшей производительности выбирают максимально возможной. На чистовых операциях хонингования скорость V1 должна быть на 20–50 % меньше, чем при предварительных. Скорость вращения хонинговальной головки V выбирают исходя из соотношения V/V1: 2–4 при хонинговании стали и 3–5 при хонинговании чугуна.
Производительность хонингования с увеличением скорости V1 повышается. С увеличением окружной скорости хона V производительность вначале повышается, а затем, при достижении некоторого критического значения, снижается. Производительность хонингования интенсивно растет с увеличением удельного давления брусков на обрабатываемую поверхность. Однако для каждой характеристики алмазных брусков существует предельное давление, выше которого происходит засаливание брусков. На предварительных операциях удельное давление р = 10…14 кгс/см2. Для снижения шероховатости поверхности следует принимать меньшие удельные давления брусков (3–8 кгс/см2). На рис. 71 представлена зависимость величины съема (а) и шероховатости (Ra) поверхности отвременихонингования.
Рис. 71. Зависимость величины съема от времени обработки (V = 63 м/мин, р = 25 кг/см2) (а) и зависимость шероховатости поверхности от времени хонингования при различной зернистости(б) (1 – 125/100; 2 – 40/28)
156
Как следует из представленных зависимостей, величина съема в начале процесса хонингования резко растет, а затем резко замедляется. Аналогичным образом и шероховатость обработанной поверхности резко снижается в первые 30 с обработки, а затем существенно не изменяется. Поэтому технологический процесс должен строиться таким образом, чтобы длительность операции хонингования составляла 30–60 с. Рекомендации по выбору режимов алмазного хонингования различных материалов приведены в табл. 28.
Таблица 2 8
Режимы алмазного хонингования
|
|
|
|
|
|
|
Обрабатываемый |
Характер |
V, м/мин |
V1, м/мин |
р, кгс/см2 |
S, |
|
материал |
операции |
|
|
|
мкм/дв.ход |
|
Серый закаленный |
Предварительная |
50–80 |
16–18 |
13–15 |
– |
|
Получистовая |
45–70 |
16–18 |
13–15 |
– |
||
чугун |
||||||
Окончательная |
40–45 |
12–16 |
5–9 |
– |
||
|
||||||
Серый чугун |
Предварительная |
50–80 |
15–18 |
8–12 |
2–3 |
|
Окончательная |
40–70 |
8–12 |
4–6 |
0,6–0,8 |
||
|
||||||
Незакаленные стали |
Предварительная |
25–35 |
6–12 |
4–6 |
1–2 |
|
Окончательная |
25–35 |
3–8 |
2–4 |
0,4–0,6 |
||
|
||||||
Закаленные стали |
Предварительная |
40–50 |
5–8 |
8–14 |
1–3 |
|
Окончательная |
40–55 |
4–6 |
4–8 |
0,4–0,6 |
||
|
||||||
Хром |
Предварительная |
12–20 |
6–8 |
4–6 |
– |
|
Окончательная |
12–20 |
5–7 |
3–5 |
– |
||
|
||||||
Анодированный |
Окончательная |
20–25 |
10–12 |
3–4 |
– |
|
алюминий |
||||||
|
|
|
|
|
Выбор СОЖ при хонинговании. Применение смазочно-
охлаждающих жидкостей (СОЖ) позволяет интенсифицировать процесс хонингования, повысить стойкость алмазных брусков, а также повысить качество обрабатываемой поверхности.
При алмазном хонинговании требуется интенсивное охлаждение в количестве до 20 л/мин, в зависимости от размеров обрабатываемого отверстия.
Основными функциями СОЖ при хонинговании являются: охлаждение; уменьшение трения (смазывание); удаление продуктов обработки из рабочей зоны (смывание).
157
В большинстве случаев лучших результатов при хонинговании стали и чугуна достигают при применении в качестве СОЖ керосина или керосина с добавлением масел, скипидара, олеиновой кислоты. Однако керосин пожароопасен, сравнительно дорог и вреден. В настоящее время заменяют керосин на СОЖ, содержащие поверхностно-активные вещества и ингибиторы коррозии: слабоконцентрированные (1–3 %) водные растворы солей неорганических кислот (кальцинированной соды, хлористого натрия, хлористого кальция, тринатрийфосфата, буры, нитрата натрия и др.) и органических поверхностно-активных веществ (триэтаноламинаэтиленгликоля и др.) с добавками ингибиторов коррозии (нитрата натрия и др.).
Рекомендуется СОЖ подводить с двух сторон (снизу и сверху). Это особенно важно при обработке отверстий малых диаметров, где зазор между корпусом хонголовки и стенками отверстия невелик.
При недостаточном охлаждении увеличивается трение и происходит нагрев детали и хонголовки, а также засаливание алмазных брусков, что отрицательно сказывается на режущий способности.
Рекомендации по эксплуатации алмазных брусков для хонин-
гования. Технологическую подготовку алмазного хонингования начинают с точной размерной установки и крепления алмазных брусков на стальные державки (колодки). Вследствие высокой износостойкости металлических связок бруски очень медленно прирабатываются в процессе хонингования. Во время их приработки на деталях резко снижается точность хонингования и производительность обработки. Поэтому при установке и креплении брусков очень важно предотвратить разновысотность брусков в одном комплекте. Необходимо, чтобы их режущие поверхности при сборке в хонголовке располагались на одной окружности. Для этого хонголовку в сборе шлифуют на круглошлифовальном станке абразивным кругом. Подготовленными к работе считают такие бруски, поверхность контакта с обрабатываемым отверстием которых составляет не меньше 60 % всей номинальной их режущей поверхности
158
и обеспечивается полный контакт по всей длине. Алмазные бруски
кметаллическим колодкам крепят, как правило, путем припайки (припой ПОС61 или ПОС40). В отдельных случаях их приклеивают
кколодкам клеем (эпоксидный клей и др.).
Хонинговальные бруски подвижно закрепляются в пазах хонголовки, в результате чего инструмент и деталь самоустанавливаются, что обеспечивает высокую точность обрабатываемых отверстий. При этом отпадает необходимость правки инструмента, а припуски могут быть сведены до минимума. Однако в некоторых случаях режущая способность брусков с течением времени в результате засаливания (налипания продуктов обработки) резко снижается, и происходит задирание обрабатываемой поверхности. Чтобы быстро восстановить ее, рекомендуется периодически изменять направление вращения хонголовки (реверсирование). Окончательно алмазные бруски по радиусу прирабатывают на хонинговальном станке по отверстию хонингуемой заготовки.
5.5. Выбор абразивных материалов для отрезных кругов
Основными абразивными материалами, применяемыми при изготовлении отрезных кругов на бакелитовой связке, являются электрокорунд нормальный марки 14А и его модификации (специального качества, прокаленный, упрочненный и т.д), циркониевый электрокорунд марки 38А, карбид кремния черный марки 54С. Реже применяются шлифматериалы белого и легированных электрокорундов (марок 25А, 37А,93А и др.), в основном в определенном соотношении с электрокорундом нормальным. Диапазон зернистостей вышеуказанных шлифовальных материалов достаточно узок, ввиду специфики применения отрезных кругов: шлифзерно F24, F30, F36, F46 и F60. Используются также комбинации этих зернистостей и различных абразивных материалов, но это является «эксклюзивом» каждого производителя отрезных кругов, поэтому необходимо ориентироваться на параметры шлифматериалов, которые приведены в стандартной маркировке.
159
Рекомендации по выбору основных типов материалов и зернистостей и по их применению представлены в табл. 29.
Таблица 2 9
Абразивные материалы для изготовления отрезных кругов на бакелитовой связке
Вид абразивного |
Зернис- |
Назначение |
материала |
тость |
|
Электрокорунд |
F24 |
Для многоцелевой отрезки стальных заготовок, в т.ч. |
нормальный мар- |
|
литейных и большого сечения, чугунного литья и т.п. |
ки 14А и его мо- |
F30 |
Дляотрезкистальныхзаготовокизвысокопрочных, инст- |
дификации |
|
рументальных, жаростойкихмароксталей, чугуна, атакже |
|
|
заготовокцветныхметалловбольшогосеченияит.п. |
|
F36 |
Для отрезки стальных заготовок из высокопрочных, |
|
|
инструментальных, жаростойких марок сталей (в т.ч. |
|
|
трубы, стальной лист), чугуна, а также заготовок цвет- |
|
|
ных металлов небольшого сечения, нержавеющих и |
|
|
кислотоустойчивых марок стали |
|
F46, F60 |
Для отрезки тонкого металлического листа, тонкостен- |
|
|
ных труб и профилей, в т. ч. из нержавеющей, инстру- |
|
|
ментальной стали и алюминия |
Карбидкремния |
F24 |
Для отрезки заготовок из титана и его сплавов, асфаль- |
черныймарки54С |
|
та, железобетона, гранита, мрамора, базальта |
|
F30 |
Дляотрезкидеталейифрагментовизбетонаипемзобето- |
|
|
на, гранита, керамики, фарфора, черепицы, шифера, кера- |
|
|
мическихтруб, огнеупорного истроительногокирпича |
|
F36 |
Для операций отрезки заготовок небольшого сечения из |
|
|
гранита, технической керамики, электрофарфора, чере- |
|
|
пицы, шифера, керамических труб, спецстекла, поли- |
|
|
мерных материалов |
|
F46 |
Для тонкой отрезки керамической и другой плитки, |
|
|
стеклянных изделий, полимерных материалов и т.п. |
Циркониевый |
F24 |
Для высокопроизводительной отрезки заготовок боль- |
электрокорунд |
|
шого сечения из специальных и высокопрочных марок |
марки 38А |
|
сталей, а также чугунного и стального литья (резание с |
|
|
большими подачами) |
|
F30, F36 |
Для высокопроизводительной отрезки заготовок не- |
|
|
большого сечения из специальных и высокопрочных |
|
|
марок сталей, а также чугунного и стального литья |
160