
Оборудование целлюлозно-бумажного производства Том 1. Оборудование дл
.pdfВ третьем типоразмере в настоящее время выпускается сдво енная мельница, по конструкции отличающаяся от вышеописан ных. Герметичное пространство размольной камеры у этой мель ницы (рис. 4 .8 ) образовано двумя корпусами — подвижным и не подвижным. Корпусы имеют разъем в вертикальной плоскости. Они соединены болтами в одно целое и устанавливаются на станину, причем их взаимное центрирование производится по
Рис. 4.8. Сдвоенная дисковая мельница 3-го типоразмера со средним распо ложением диска:
/ — станина; |
2 — гидроцилнндр |
присадки; 3 — корпус подвижный; 4 — статор подвижный; |
5 — гарнитура |
размалывающая; |
6 — сальник; 7 — корпус неподвижный; 8 — ротор |
обработанной направляющей поверхности станины. Подвижный корпус после его отсоединения может отводиться для обеспе чения доступа при замене и осмотре гарнитуры. Ротор мельницы также подвижен в осевом направлении («плавающий» ротор). Выходы вала из корпусов уплотнены сальниками.
Эта мельница имеет два присоединительных патрубка, через которые масса подается в зоны размола самостоятельными по токами. Из камеры может выходить через один патрубок.
При работе мельницы подвижный статор находится в рав новесии под действием осевых усилий в зонах размола и усилия трех гидроцилиндров механизма присадки.
Давление масла, определяющее усилие в гидроцилиндрах, устанавливается с помощью напорного золотника на пульте уп равления и поддерживается постоянным. При износе гарнитуры или при колебаниях количества массы, проходящей через мель ницу, статор за счет изменения зазоров в зонах размола авто матически находит равновесное состояние при постоянном уси лии гидроприсадки.
Самопроизвольное соприкосновение дисков при прекраще нии подачи массы предотвращается с помощью реле давления, датчики которого установлены на впускных патрубках мель ницы, при прекращении подачи массы или при падении давле ния ее на входе ниже заданного реле отключает приводной дви гатель и статор отводится гидроцилиндрами.-
Привод ротора от электродвигателя осуществляется через специальную роликовую муфту, обеспечивающую его сво бодное перемещение в осевом направлении. В роликовой муфте по сравнению с зубчатой возникают значительно мень шие по величине осевые нагрузки, передаваемые на вал дви гателя.
К преимуществам этой мельницы можно отнести неконсоль ное расположение диска, что желательно при значительных вра щающихся массах. Однако эта конструкция мельницы имеет ряд существенных недостатков: как у всех мельниц со средним рас положением диска недостаточно хороший доступ к размалываю щей гарнитуре, что затрудняет ее замену; сложность конструк ции и нетехнологичность в изготовлении; ограниченные воз можности варьирования схем подачи массы; необходимость применения гибкого подводного шланга или компенсирующего устройства для подачи массы в патрубок подвижного корпуса. Поэтому разработаны новые конструкции сдвоенных мельниц 3-го и 4-го типоразмеров, обладающие всеми преимуществами сдвоенных мельниц, рассмотренных ранее.
Учитывая, что частота вращения ротора сдвоенных дисковых мельниц больших величин невелика (500—600 мин-1) и что ро торный диск сдвоенной мельницы при работе как бы зажат между двумя поверхностями (через массу), консольное рас положение диска, даже при «плавающем» роторе вполне до пустимо.
Конструкция сдвоенных мельниц 3-го и 4-го типоразмеров
с консольным расположением вращающегося диска |
показана |
на рис. 4.9. Эти мельницы, как и сдвоенные мельницы |
1-го ти |
поразмера, имеют станину, отлитую из чугуна, в передней части которой выполнен чашеобразный прилив, облицованный внутри нержавеющим материалом. Прилив вместе с закрывающей его крышкой и задней стенкой образует герметичное пространство размольной камеры. Внутри камеры у задней стенки распола гается подвижный в осевом направлении извращающийся диск статора, закрепленный на трех штангах, имеющих резьбу, в ко-
торую ввинчены три винта, установленные в подшипниковых
опорах, закрепленных в станине.
Вращение от механизма присадки, размещенного в задней части станины, передается на один из винтовых механизмов, шестерня которого через центральное синхронизирующее колесо приводит во вращение два других винтовых механизма.
Ротор мельницы своим подшипниковым стаканом также ус тановлен в расточках станины, и стакан ротора зафиксирован
Рис. 4.9. Сдвоенная дисковая мельница 3-го н 4-го типоразмеров с консоль-
ным расположением дисков: |
|
|
F |
F |
/ — станина; 2 — ротор; 3 — механизм |
ппнсалки- |
л |
— размалывающая |
гарнитура; 5 — |
муфта |
ф ич д к и , |
4 |
от проворачивания, но подвижен в осевом направлении Выход вала мельницы из размольной камеры герметизирован саль ником.
Мельница имеет присоединительные патрубки через кото рые масса может подаваться в камеру и выходить из нее при
Г " “ |
Hb' |
ТРИ РШее Расс“ °Д >«™ е схемы подаИи |
массы. |
|
|
Сдвоенные дисковые мельницы новой конструкции обладают
рядом преимуществ перед ранее рассмотренной |
сдво^ной мель^ |
|
ницеи третьего типоразмера. Основными из них |
ямяются |
ме^ь- |
шая металлоемкость, лучшая тех н ш ш гтт^ |
являются, |
мень |
применение |
электромеханической |
присадки |
j* изготовления; |
и простой в эксплуатации; лучшие |
условия |
л„,°Лее наДежнои |
|
уменьшение |
габаритных размеров |
^ еТ ш е |
|
ваемого мельницей, за счет отделений |
шума, созда |
уделения |
статора от задней стенки |
и выполнения крышки камеры с двойными стенками; лучщие условия ремонта (замены подшипников, втулки защитной, муфты и др.); применение жидкой смазки подшипников мель ницы (масляной ванны) вместо консистентной, что обеспечи вает лучшие условия работы подшипников; наличие одного саль никового узла вместо двух.
Сдвоенные мельницы 5-го типоразмера найдут применение только в технологических линиях по производству древесной
массы |
из щепы. |
Эти |
мельницы |
(рис. |
4.10) в настоящее время |
|||||
{ |
2 |
3 |
4 |
5 |
6 |
7 8 9 |
J0 |
11 |
12 |
13 |
Рис. 4.10. Сдвоенная дисковая мельница 5-го типоразмера:
1, 15 — опоры ротора; 2, 14 — ленточные питатели; 3, 11 — полукорпусы; 4, /3 — отводные
паропроводы; 5, |
12 — подводные патрубки; |
6, 10 — статоры; 7, |
9 — гарнитура размалыва |
ющая; 8 — диск |
ротора; 1 6 — муфта; 17, |
19 — винтовые пары; |
18 — выпускное отверстие |
разрабатываются. Они будут иметь среднее расположение вра щающегося диска (между подшипниковыми опорами вала) и снабжены двумя электромеханическими присадками, произ водящими перемещение обоих статорных дисков и устанавли вающих необходимые зазоры в своих зонах размола. Для по дачи массы в зоны размола на валу мельницы с обеих сторон вращающегося диска установлены ленточные винтовые пита тели. Отвод пара из зон размола осуществляется через специ-. альные трубопроводы.
4.1.3. Электропривод и система управления
Для привода дисковых мельниц мощностью до 200 кВт при меняются асинхронные электродвигатели на напряжение 380, 500 и 660 В, предусмотрено также комплектование мельниц при мощности двигателей 160 и 2 0 0 кВт асинхронными двигателями на напряжение 6000 В.
Привод дисковых мельниц мощностью 250 кВт и выше осу ществляется, как правило, от синхронных закрытых электродви гателей на напряжение 6000 В при мощности двигателей до 1000 кВт и на напряжение 6000 и 10 000 В при мощности дви гателей 1000 кВт и более. Возбуждение синхронных двигателей осуществляется от тиристорных возбудительных устройств.
Синхронные закрытые электродвигатели разработаны спе циально для привода дисковых мельниц. Они имеют замкну тую систему вентиляции через встроенный охладитель, преду смотрена также возможность подвода свежего воздуха внутрь двигателя. Это позволяет при установке мельниц в помещениях с агрессивной средой обеспечить их надежную и долговечную работу.
Синхронные закрытые электродвигателя укомплектовы ваются датчиками температуры охлаждающего воздуха и воды, а при мощности двигателей Л000 кВт и более, кроме того, дат чиками температуры подшипников, железа и обмоток каждой фазы статора.
На трубопроводах подачи охлаждающей воды в воздухоох ладитель двигателя предусмотрена установка регулятора тем пературы, обеспечивающего поддержание постоянного тепло вого режима во время работы двигателя и автоматическое от ключение воды после его останова.
Мельницы могут комплектоваться системами местного уп равления или автоматического. Автоматическая система управ ления содержит те же узлы, что и система местного управле ния, и отличается лишь тем, что в шкаф местного управления дополнительно устанавливаются блоки программного пуска и автоматической присадки. Блок программного пуска обеспе чивает автоматическое включение и отключение механизмов мельницы по определенной программе по команде оператора или управляющей вычислительной машины. Блок автоматиче ской присадки осуществляет автоматическую присадку (или от садку) дисков в зависимости от мощности приводного двига теля мельницы и поддерживает заданную мощность автома тически.
Во время работы мельницы электрическая схема управления обеспечивает также контроль нормальной работы всех механиз мов и узлов мельницы и осуществляет предупредительную сиг нализацию или отключение мельницы при каких-либо наруше ниях в работе.
4.1.4. Размалывающая гарнитура для дисковых мельниц
Размалывающая гарнитура — основной рабочий орган мель ницы, осуществляющий непосредственное воздействие на во локна в процессе их обработки. Рабочая поверхность гарни туры характеризуется числом и размерами ножей и канавок
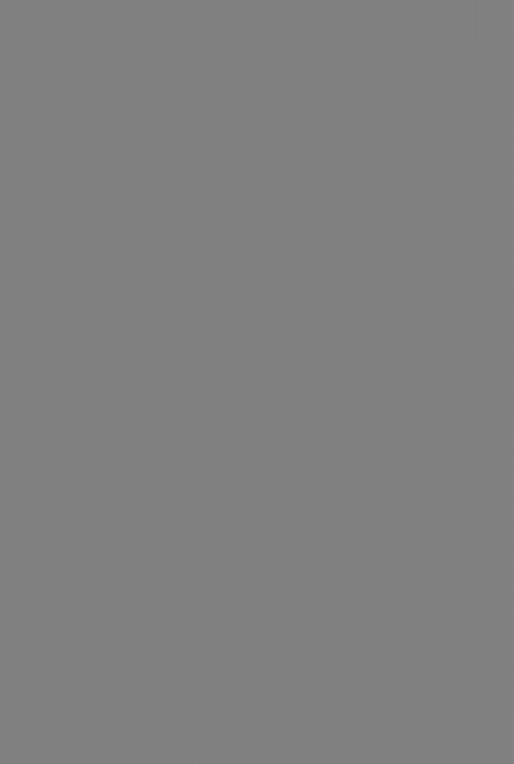
и их расположением на поверхности. В совокупности с частотой вращения роторного диска и потребляемой мощностью параметры гарнитуры определяют качество размола массы, транс портирующую способность мельницы, ее технико-экономические
показатели.
В мировой практике разработано большое число различных типов гарнитуры, отличающихся конфигурацией рабочей по верхности. К сожалению, несмотря на накопленный опыт, вы бор оптимального для данного процесса варианта гарнитуры часто осуществляется эмпирическим путем.
Основное значение при размоле массы низкой концентрации имеет количество и длина ножей на рабочей поверхности гар нитуры. При заданной частоте вращения эти параметры одно значно определяют секундную режущую длину мельницы.
С точки зрения числа метрорезов можно выделить три ос новных разновидности гарнитуры: с максимальным, средним и минимальным числом метрорезов. Первый тип гарнитуры при прочих равных условиях способствует преимущественному фибриллированию волокон, третий — укорочению, второй тип гар нитуры оказывает то и другое действие.
Второй тип гарнитуры подходит для большинства видов раз мола. В тех случаях, когда требуется увеличить режущее дей ствие этой гарнитуры, необходимо увеличить загрузку мельницы (уменьшить зазор в зоне размола), когда режущее действие нежелательно, загрузку надо уменьшить (увеличить зазор). Лишь в тех случаях, когда невозможно достичь желаемых ре зультатов на оптимальном типе гарнитуры, следует применять другие ее разновидности.
Наиболее характерные схемы расположения ножей на ра бочей поверхности гарнитуры, применяемой на отечественных дисковых мельницах, представлены на рис. 4.11. Характери стика основных типов гарнитуры для различных типоразмеров мельниц приведена в табл. 4.3.
Гарнитура для отечественных дисковых мельниц, применя емых для размола массы низкой концентрации, по количеству ножей приближается ко второму условному типу гарнитуры. Она имеет три зоны (реже две)— заходную, среднюю и пери ферическую. Заходная зона служит для создания определенной направленности потока массы и на результаты размола влия ния не оказывает. Средняя зона имеет, как правило, более крупные и реже расположенные ножи, чем периферическая.
Рис. 4.11. Гарнитура размалывающая для дисковых мельниц:
а — нарезная |
из цельных дисков; |
б — для размола щепы |
и массы высокой |
концентра |
|
ции; в — радиальная; г — с параллельно расположенными |
ножами и с перемычками; |
д — |
|||
шнпообразная; |
е — радиальная со |
спирально расположенными перемычками; |
ж — с |
па |
раллельно расположенными ножами и с разделительной канавкой; з — радиальная с пере мычками для предварительного размола
4.3. Характеристика основных типов гарнитуры для дисковых мельниц отечественного производства
Типо |
|
размер |
Обозначение гарнитуры |
мель |
|
ницы |
|
0 0 |
МДС-00.00.002 |
|
(МДС-00.00.004) |
|
МДС-00.00.002-01 |
|
(МДС-00.00.004-01) |
0 |
Р-500.001 |
|
(Р-500.002) |
|
Р-500.005 |
1 |
Р-630.002 |
|
(Р-630.004) |
|
Р-630.007 |
2Р-800.003 Р-800.011
(Р-800.012) Д-800.001
3Р-1000.002 Р-1000.013
(Р-1000.014) МД-56.01.005 У1
Ширина |
Ширина |
Наличие |
Режу |
Коли |
|
перего |
щая |
чество |
|||
ножа, |
канавки, |
родок |
длина за |
секторов |
|
|
мм |
мм |
в канав |
1 оборот, |
в диске, |
|
|
|
ке |
км |
шт. |
|
3 |
3 |
|
0,96 |
1 |
|
4 |
4 |
— |
0,56 |
1 |
I |
3 |
4 |
+ |
2,46 |
4 |
|
4 |
5 |
+ |
1 ,2 |
4 |
}* |
4,5 |
+ |
5,9 |
6 |
|
|
4 |
6,3 |
|
2 , 0 |
6 |
|
3 |
4 |
+ |
7,1 |
6 |
|
|
5 |
|
9,6 |
6 |
|
3 |
8 |
|
1,9 |
6 |
|
3 |
5 |
-4 - |
1 8 ,0 |
8 |
|
|
||||
| |
2 ,6 |
5,2 |
— |
19,0 |
8 |
|
3 |
8 |
+ |
4,0 |
8 |
П р и м е ч а н и е . В скобках указана гарнитура для второй зоны сдвоен ных мельниц. Она подобна предыдущей, но имеет другой угол наклона ножей.
Опыт эксплуатации гарнитуры с различной конфигурацией рисунка рабочей поверхности на массном размоле полуфабри катов показывает, что с точки зрения пропускной способности и равномерности износа рабочей поверхности, расположение но
жей |
по рис. |
4.11, |
г и ж является |
более оправданным, |
чем по |
|
рис. |
4.11, в. |
Ножи |
и канавки этой |
гарнитуры |
имеют |
одинако |
вое |
сечение |
вдоль |
радиуса, поэтому наличие |
местного износа |
из-за неравномерности проходного сечения на гарнитуре этого типа, как правило, не наблюдается.
Для интенсификации размола за счет увеличения пути дви жения волокон в рабочем зазоре используют гарнитуру с пере городками в межножевых канавках, которые препятствуют сквозному продвижению массы по канавкам и выводят ее в зону размола. Перегородки в целях исключения неравномер ного износа поверхности устанавливают, как правило, по спи рали. При отсутствии перегородок в межножевых канавках ра бочую поверхность гарнитуры иногда разделяют кольцевой канавкой, которую располагают на расстоянии 70—100 мм от периферии диска. Наличие такой канавки изменяет площадь проходного сечения в основной рабочей зоне и приводит к пере распределению скоростей потока массы. Это способствует интен
сификации воздействия на волокна режущих кромок ножей, расположенных на периферии диска.
Для размола грубой массы (отходов сортирования, древес
ной |
массы для древесноволокнистых плит на второй ступени |
и т. |
п.) при низкой концентрации и при работе мельниц с ма |
лой |
производительностью также рекомендуется использовать |
гарнитуру с перемычками в канавках (рис. 4.11, е и г). Подоб ная же гарнитура применяется на предварительном размоле целлюлозы и полуфабрикатов высокого выхода, но размол при этом осуществляется при больших зазорах.
Для размола щепы и массы высокой концентрации приме няется гарнитура, имеющая не менее трех зон размола, что обеспечивает постепенную обработку материала (роспуск на пучки волокон, потом на волокна, затем обработку волокон). По сравнению с гарнитурой для низкой концентрации массы эта гарнитура (рис. 4.11, б) имеет узкий плоский участок на периферии. Остальная часть выполнена конусной, в средней ча сти конусность составляет 1—2°, в заходной 5—15° Заходная часть выполняется более развитой, что необходимо для обеспе чения транспортирующей способности мельниц.
В канавках гарнитуры в средней и периферической зонах располагаются перегородки, высота которых к периферии по степенно увеличивается до высоты ножей.
Для предварительного размола полуцеллюлозы, пропарен ной щепы в производстве древесноволокнистых плит ( 1 -я сту пень размола) применяется размалывающая гарнитура (рис. 4.11, з), которая имеет небольшое количество высоких ножей, перемычки и развитую заходную зону. Реже для этих же целей применяется шипообразная гарнитура (рис. 4.11, д).
На отечественных дисковых мельницах применяется в ос новном размалывающая гарнитура, выполненная в виде от дельных секторов методами точного литья в оболочковые формы (литая гарнитура). Лишь для самых маленьких мельниц (ти поразмеры 00 и 0 ) гарнитура выполняется путем нарезки но жей механической обработкой (нарезная гарнитура, рис. 4.11, а) в виде цельных дисков. Гарнитура поставляется термически и механически обработанной, комплекты гарнитуры, устанав ливаемые на ротор мельницы, подвергаются баланси
ровке.
В зависимости от требуемой коррозионной стойкости литая гарнитура изготавливается из специальной стали 40Х17Н2М, легированной хромом, никелем и молибденом, или из стали 95X18. Твердость отливок 400—500 НВ. Нарезная гарнитура изготавливается из сталей 12Х18Н9ТЛ с твердостью 220 300 НВ. Толщина диска такой гарнитуры значительно больше толщины секторов литой гарнитуры. Это позволяет методами механической обработки производить перенарезку ее рабочей поверхности повторно (до 3—4 раз). Ввиду малой твердости
рабочей поверхности нарезной гарнитуры износостойкость ее как правило, значительно ниже, чем литой.
В последнее время в нашей стране и за рубежом прово дятся широкие исследования по использованию новых, б0лее износостойких материалов для изготовления гарнитуры, таких например, как высокопрочный чугун, легированный бором!
Предпринимаются попытки использования и неметаллических материалов (керамических, базальтовых и др.).
4.1.5. Применение дисковых мельниц
Изготавливаемые отечественными заводами дисковые Мель ницы позволяют укомплектовать любые технологические по токи, базирующиеся как на традиционной, так и на появив шейся в последние годы новой технологии производства Полу фабрикатов.
Все виды обработки (размола) волокнистых материалов, ко торые осуществляются на дисковых мельницах, можно разде лить на следующие группы: предварительный размол, разделе ние непроваренной щепы, сучков, пучков волокон, костры на волокна, этот вид обработки осуществляется в основном в ва
рочных цехах; массный |
размол — основной вид |
размола_ |
||
обеспечивает |
придание |
волокнам |
определенных |
технологиче |
ских свойств |
и осуществляется в |
размольно-подготовительных |
цехах, может проводиться как при низкой, так и при высокой концентрации массы; размол щепы в производстве древес ной массы термомеханическим и другими способами для раз личных видов бумаги, картона, древесноволокнистых плит (сюда же необходимо отнести размол химической древесной массы, полуцеллюлозы высокого выхода); размол отходов сор тирования древесномассного и целлюлозного производств, пред варительный размол крупных кусков древесины и пучков волокон осуществляется в основном при высокой концентрации, а пос ледующий их размол при низкой концентрации; размол массы перед подачей на бумагоделательные и картоноделательные машины с целью расщепления сгустков волокон и выравнива ния массы; прочие виды размола, например размол маку латуры после ее термодисперсионной обработки, размол макула туры после гидроразбивателей, дополнительный размол дефибрерной массы, размол тряпичной полумассы после тряпкорубок и др.
Предварительный размол. Этот вид размола осуществляется в варочных цехах; может быть одностадийным или двухста дийным. Одна из стадий дефибрирования, как правило, прово дится до промывки полуфабриката в присутствии щелока, вто рая — после промывки. Двухстадийный процесс подготовки массы на дисковых мельницах в варочных цехах находит все большее применение в связи с тем, что разработаны различные