
m0935
.pdf
В.В. Муравьев
Диагностирование рельсов на рельсосварочном предприятии. Метод АЭ использован для повышения надежности контроля качества сварных соединений рельсов в условиях рельсосварочного предприятия РСП-29 ЗСЖД. (участвовали Т.В. Муравьев, С.А. Бехер, М.В. Муравьев). Контроль зоны сварного соединения производился в процессе изменения термических напряжений при остывании сварного шва. Выявленные закономерности в распределении параметров АЭ от различных дефектов использованы при разработке методики АЭ контроля.
Доказана возможность проведения АЭ контроля сварных соединений на рельсосварочной линии сразу после процесса сваривания и снятия града. По результатам работы создано методическое обеспечение для АЭ мониторинга процесса остывания соединения рельсов после контактно-стыковой сварки плавлением, основанное на анализе постоянства АЭ потоковых характеристик качественного сварного шва.
Впериод работы автора с 2006 по 2008 гг. на должности начальника на- учно-внедренческого центра и профессора кафедры «Технология сварки, материаловедение, износостойкость деталей машин» МИИТа по заданию ОАО «РЖД» в МИИТе совместно с СибНИА была продолжена начатая в 2003 г. раз-
работка АЭ стендов и технологий контроля колесных пар и автосцепки ва-
гонов с доведением до приемочных испытаний [20].
Следует отметить, что при разработанной схеме нагружения колесных пар АЭ метод позволяет выявлять практически все дефекты, которые могут быть обнаружены любым из традиционных методов контроля, предусмотренных регламентом. С внедрением автоматизированных диагностических АЭ стендов появилась возможность сокращения объемов ручного дефектоскопирования. К основным преимуществам разработанного автоматического диагностического стенда АЭ следует отнести отсутствие влияния человеческого фактора, автоматизацию обработки с анализом и протоколированием результатов контроля.
Основная деталь автосцепки – тяговый хомут испытывает высокие нагрузки до 300 тс, сочетающиеся с ударными. В 2005 г. начата разработка методики и устройства для нагружения, в основе которого лежит принцип распирания тягового хомута изнутри клиновым механизмом с помощью гидроцилиндра (участвовали сотрудники СибНИА, гл. инженер ЗапсибДРВ С.А. Грассман).
Вдекабре 2007 г. проведены приемочные испытания АЭ стенда контроля тяговых хомутов автосцепных устройств вагонов в ремонтном вагонном депо Инская Западно-Сибирской дирекции по ремонту грузовых вагонов. АЭ контроль надежно выявил дефекты сварки и усталости. По результатам испытаний стенд рекомендован для широкомасштабного внедрения на сети железных дорог России.
131

Диагностика и неразрушающие методы контроля
Основные достижения научной школы «Диагностика и неразрушающие методы контроля» состоят в следующем.
1.Исследовано влияние структурных факторов и напряженнодеформированного состояния металлических объектов на основные характеристики объемных ультразвуковых волн и волн Рэлея. Разработаны и внедрены на ряде ТЭЦ и железных дорог методики и более ста приборов ИСП-12 для диагностирования структурного состояния, твердости и механических свойств, для оценки реального и предельного состояний металла паропроводов.
2.Теоретически обоснованы и разработаны методы, изготовлены и внедрены в вагонных ремонтных депо более 80 акустических приборов типа УДССИН для определения плотности посадки колец подшипников на шейках осей колесных пар.
3.Разработаны автоматизированные стенды акустико-эмиссионной диагностики и продления срока службы боковых рам и надрессорных балок тележек грузовых вагонов на основе СЦАД16.03. Вагонные ремонтные депо железных дорог России оснащены ста пятью стендами. Внедрение стендов по продлению срока службы литых деталей тележек позволило сэкономить ОАО «РЖД» более 12 млрд р. за пять лет их эксплуатации.
4.Разработаны методики и изготовлены стенды акустико-эмиссионной диагностики колесных пар вагонов, тяговых хомутов автосцепных устройств вагонов, карданных валов локомотивов ЧС-2 и серповидных подвесок электропоездов, колец подшипников, сосудов давления. Методики и стенды прошли приемочные испытания и рекомендованы для широкомасштабного внедрения на сети железных дорог России.
5.Разработаны методики, изготовлены и апробированы опытные образцы оборудования на основе метода акустической эмиссии и тензометрии для диагностирования элементов железнодорожных сварных мостов; рельсов, уложенных на железнодорожном мосту; сварных соединений рельсов на рельсосварочных предприятиях РЖД.
6.Приборы внесены в государственный реестр средств измерений и в отраслевой реестр средств измерений, допущенных к применению на железнодорожном транспорте.
Развитие научного направления «Диагностика и неразрушающие методы контроля»
Начиная с 2006 г. происходит резкое увеличение числа сходов и крушений из-за изломов боковых рам. В основном ломаются боковые рамы коробчатого сечения нового изготовления. Качество литых деталей с каждым годом ухудшается, что подтверждается статистикой изломов боковых рам тележек грузовых вагонов в движении (рис. 5, а). Большинство изломов боковых рам в
132
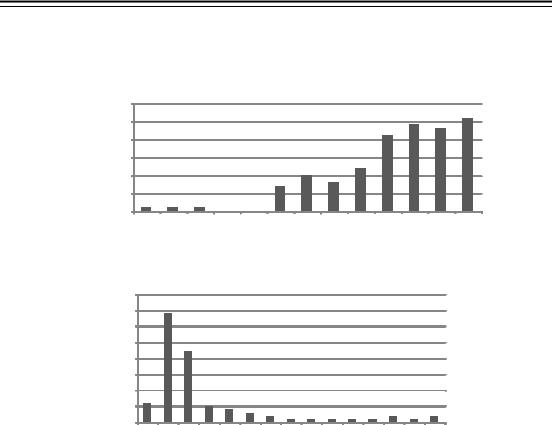
В.В. Муравьев
пути следования с гарантийным сроком эксплуатации до пяти лет приходится на первые 2–3 года эксплуатации (рис. 5, б).
а)
Количество изломов, шт. |
|
|
|
|
|||
30 |
|
|
|
|
24 |
23 |
26 |
25 |
|
|
|
|
|||
|
|
|
|
21 |
|
|
|
20 |
|
|
|
|
|
|
|
15 |
|
|
|
10 |
12 |
|
|
10 |
|
|
7 |
8 |
|
|
|
5 |
1 |
1 |
1 |
|
|
|
|
0 |
2001200220032004200520062007200820092010201120122013за 3 мес. |
||||||
|
|
|
|
Год |
|
|
за 3 |
|
|
|
|
|
|
месяца |
|
|
|
|
Год разрушения |
|
б)
Количество изломов,шт.
40
35
30
25
20
15
10
5
0
1 |
2 |
3 |
4 |
5 |
6 |
7 |
8 |
9 |
10 |
11 |
12 |
13 |
14 |
15 |
|
Возрастбоковых рамкмоментуразрушения,лет |
|
|
Рис. 5. Количество изломов боковых рам в пути следования по годам (а), в зависимости от возраста изделий к моменту излома (б)
В период 2006–2013 гг. изломалось 102 шт. (см. рис. 5, б) новых боковых рам (с гарантийным сроком эксплуатации до пяти лет). Статистика разрушений по заводам-изготовителям распределяется следующим образом:
33 шт. – ОАО НПК «Уралвагонзавод»,
28 шт. – ЧАО «Азовэлектросталь», 13 шт. – ПАО «Кременчугский сталелитейный завод», 11 шт. – ОАО «Алтайвагонзавод»,
11 шт. – ООО «Промтрактор-Промлит», 4 шт. – ОАО «Мариупольский ЗТМ»,
1 шт. – ООО ПК «Бежицкий сталелитейный завод», 1 шт. – Китай (приемка ОАО «Азовобщемаш»).
На рис. 6 представлен типичный излом в области буксового проема по внутреннему радиусу R55, где присутствуют скопления металлургических дефектов усадочного происхождения с наличием рыхлот и газовой пористости.
133
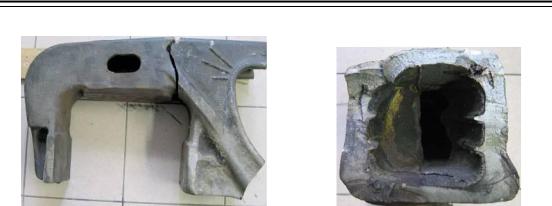
Диагностика и неразрушающие методы контроля
а) |
б) |
Рис. 6. Излом: боковой рамы коробчатого сечения в пути следования – а, усталостный с наличием металлургических дефектов – б
Следует отметить, что дефектоскопия на заводах-изготовителях проводится визуальным и электромагнитными методами неразрушающего контроля, которые обеспечивают обнаружение лишь поверхностных дефектов определенной ориентации и размеров.
Несмотря на неоспоримые преимущества, широкое использование метода АЭ сдерживается отсутствием обоснованных критериев чувствительности метода. Предложены подходы к обоснованию критериев чувствительности аку- стико-эмиссионного метода контроля к развивающимся дефектам боковой рамы тележки грузового вагона с позиций теории упругости, теории статической
идинамической прочности [22–24].
Спозиций теории упругости сопоставление амплитуд электрических импульсов АЭ с уровнями сигналов АЭ, регистрируемых в ходе реальных испытаний боковых рам тележки грузового вагона (рис. 7, а), позволяет оценить размеры скачков трещин, выявляемых методом АЭ, и сопоставить по уровню чувствительности магнитопорошковый и акустико-эмиссионный методы кон-
троля. Уровень регистрируемых напряжений Uэл = 1–6 мВ соответствует диапазону скачков S = 1,5∙10–8–6∙10–8 м2 или длине трещины l = 0,3–6 мм при раз-
мере усталостной бороздки = 0,1–3 мкм. Рассчитанные значения размеров трещин соответствуют ГОСТ Р 52727–2007 и удовлетворительно совпадают с принятыми критериями браковки магнитопорошковым методом в соответствии с РД 32.159–2000.
Использование положений статической теории прочности (рис. 7, б) позволяет оценить характер напряженного состояния вблизи вершины трещины в области внутреннего угла буксового проема боковой рамы, а также размеры начальных очагов и уровень механических напряжений, достаточный для излучения волн АЭ. При уровне нагружения по внутреннему углу буксового проема 80 МПа коэффициент запаса прочности, эквивалентный коэффициенту концентрации напряжений, составляет ~ 6 и обозначает уровень, начиная с которого микротрещины будут развиваться, а следовательно, излучать волны АЭ.
134
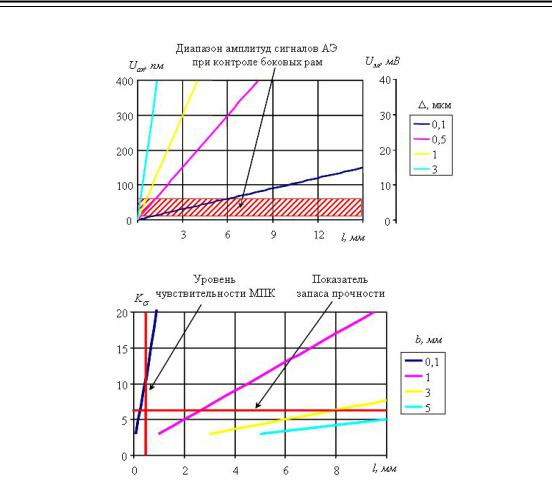
В.В. Муравьев
а)
б)
Рис. 7. Зависимость амплитуд электрического и акустического импульсов АЭ от размеров прироста трещины (а); зависимость коэффициента концентрации напряжений в вершине дефекта с полуосями l и b (б)
Согласно усталостному критерию на основании кинетической диаграммы усталостного разрушения построены зависимости скорости роста и абсолютной длины усталостной трещины от числа циклов нагружения (рис. 8, а), согласно которой может быть оценено влияние длины начальной трещины в детали на ее циклическую долговечность (рис. 8, б).
135
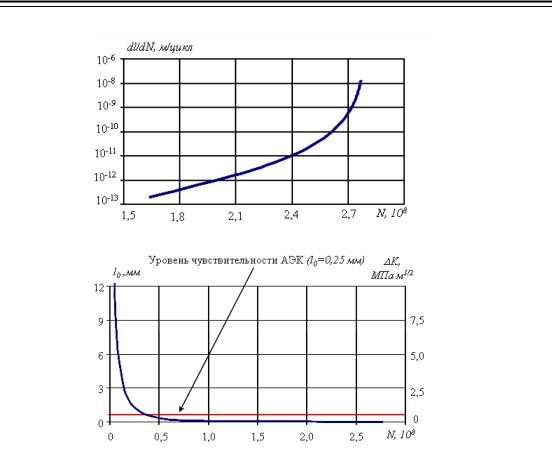
Диагностика и неразрушающие методы контроля
а)
б)
Рис. 8. Зависимость скорости роста усталостной трещины (а) и длины начальной трещины от числа циклов нагружения (б)
Предложенные подходы позволили оценить предельную чувствительность метода акустической эмиссии к размерам скачков усталостных трещин; размеры начальных очагов зарождения усталостной трещины и уровень механических напряжений, достаточный для излучения волн АЭ; влияние размеров начальной трещины в детали на ее циклическую долговечность.
Заключение
Исследования автора в области акустической структуроскопии, начатые в НИИЖТе–СГУПСе, продолженные в МИИТе и в ИжГТУ, развиваются достаточно успешно.
Более 20 учеников, защитивших диссертации по этому направлению, продолжают исследования, разрабатывая приборы и методики контроля металлов и сплавов, подготавливая их к сертификации, внедряя в промышленность.
Количество статей по структуроскопии в рецензируемых журналах превышает 130 наименований, опубликовано 10 монографий, 20 патентов на изобретения и полезные модели.
136

В.В. Муравьев
Научная школа «Физические методы и средства структуроскопии, технической диагностики, материаловедение» в конкурсе научных школ, проводимом в ИжГТУ в 2012 г., получила первое место.
Результаты исследований и разработок используются не только на железнодорожном транспорте, но и в ряде отраслей металлургической, машиностроительной, газовой, нефтяной промышленности, теплоэнергетике и др.
Библиографический список
1. Муравьев В.В., Ноева М.Р., Шарко А.В. Исследование процесса распада пересыщенного твердого раствора в алюминиевом сплаве Д16 // Физика металлов и металловедение. 1978. Т. 46. № 4. С. 746 749.
2. Конюхов Г.П., Бедарев А.С., Муравьев В.В. и др. Влияние закалки в новых средах на свойства и структуру алюминиевых сплавов // Металловедение и термическая обработка металлов. 1980. № 10. С. 26 30.
3. Комаров К.Л., Муравьев В.В., Салаев А.В., Шарко А.В. Исследование мешающих факторов при акустическом контроле термообработки сплава Д1 // Дефектоскопия. 1980. № 8. С. 53 56.
4.Серегин Г.В., Муравьев В.В. Способ определения предела ограниченной выносливости материала А. С. СССР, SU № 1033919 А. Бюл. № 29, 1983, Москва, ВНИИПИ. 4 с.
5.Серегин Г.В., Муравьев В.В. Способ определения предела ограниченной выносливости материала А. с. СССР, SU № 1111064 А, Бюл. № 32, 1984, Москва, ВНИИПИ. 4 с.
6.Серегин Г.В., Муравьев В.В. Структурные состояния и механические свойства диспер- сионно-твердеющего коррозионностойкого сплава 36НХТЮ // Известия вузов. Черная метал-
лургия. 1987. № 12. С. 77 80.
7.Муравьев В.В. Скорость звука и структура сталей и сплавов / В.В. Муравьев, Л.Б. Зуев, К.Л. Комаров. Новосибирск: Наука, 1996. 183 с.
8.Акустический контроль долговечности стальных образцов и восстановление их ресурса / Л.Б. Зуев, О.В. Соснин, Д.З. Чиракадзе, В.Е. Громов, В.В. Муравьев // Прикладная механика и техническая физика. 1998. Т. 39. № 4. С. 180–183.
9.Зуев Л.Б., Целлермаер В.Я., Громов В.Е., Муравьев В.В. Ультразвуковой контроль накопления усталостных повреждений и восстановление ресурса деталей // Журнал технической физики. 1997. Т. 67. № 9. С. 123–125.
10.Зуев Л.Б., Муравьев В.В., Данилова Ю.С. О признаке усталостного разрушения сталей // Журнал технической физики. 1999. Т. 25. № 9. С. 31–34.
11.Серегин Г.В., Муравьев В.В. Ускоренный метод оценки предела выносливости транспортных металлов // Контроль. Диагностика. 2001. № 11. С. 11–13.
12.Смирнов А.Н., Герике Б.Л., Муравьев В.В. Диагностирование технических устройств опасных производственных объектов. Новосибирск: Наука, 2003. 244 с.
13.Акустико-эмиссионная диагностика конструкций / А.Н. Серьезнов, Л.Н. Степанова, В.В. Муравьев и др.; Под ред. Л.Н. Степановой. М.: Радио и связь, 2000. 280 с.
14.Муравьев В.В., Муравьев М.В., Бехер С.А. Применение новой методики обработки сигналов АЭ для повышения точности локализации дефектов // Дефектоскопия. 2002. № 8. C. 15 (53–65).
15.Муравьев В.В., Степанова Л.Н., Кареев А.Е. Оценка степени опасности усталостных трещин при акустико-эмиссионном контроле литых деталей тележки грузового вагона // Дефектоскопия. 2003. № 1. C. 63–68.
137

Диагностика и неразрушающие методы контроля
16.Диагностика объектов транспорта методом акустической эмиссии / А.Н. Серьезнов, Л.Н. Степанова, В.В. Муравьев и др.; Под ред. Л.Н. Степановой, В.В. Муравьева. М., 2004. 368 с.
17.Степанова Л.Н., Муравьев В.В., Круглов В.М. и др. Способ диагностирования мостовых металлических конструкций и устройство для его осуществления // Патент РФ № 2240551 С2 RU. Дата регистрации: 20.06.2001. Опубл. Бюл. № 32, 27.06.2003. Москва, ФИПС. 20с.: ил.
18.Степанова Л.Н., Серьезнов А.Н., Круглов В.М., Муравьев В.В. Многоканальная аку- стико-эмиссионная система диагностики конструкций // Патент РФ RU № 2217741 С2. Дата регистрации: 13.03.2001. Бюл. № 33. 27.11.2003. Москва, ФИПС. 18 с.
19.Муравьев М.В., Муравьев В.В., Степанова Л.Н. и др. Способ диагностирования рель-
совых плетей |
металлического моста |
и устройство для его осуществления // Патент RU |
№ 2284519 С1 |
РФ. Дата регистрации: |
14.02.2005. Опубл. Бюл. № 27, 27.09.2006. Москва, |
ФИПС. 14 с.: ил.
20.Степанова Л.Н., Ивлиев В.В., Муравьев В.В. и др. Акустико-эмиссионный способ диагностирования колесных пар железнодорожного подвижного состава и устройство для его осуществления // Патент RU № 2296320 С1 РФ. Дата регистрации: 07.09.2005. Бюл. № 9, 27.03.2007. Москва, ФИПС. 16 с.: ил.
21.Муравьев В.В., Муравьев М.В., Муравьев Т.В. К возможности диагностирования рельсов в эксплуатации акустико-эмиссионным методом // Дефектоскопия. 2008. № 1. С. 42–50.
22.Муравьев В.В., Муравьева О.В. Чувствительность метода акустической эмиссии к развивающимся трещинам в боковых рамах тележек грузовых вагонов // В мире неразрушающего контроля. 2011. № 2. C. 27–31.
23.Муравьев В.В. Анализ результатов эксплуатации акустико-эмиссионных стендов для контроля литых деталей тележек железнодорожных грузовых вагонов // Интеллектуальные системы в производстве. 2013. № 1. C. 136–143.
УДК 620.179.17.008.6 : 621.791.05
Л.Н. Степанова, К.В. Канифадин, И.С. Рамазанов
Акустико-эмиссионный контроль cварных швов в процессе сварки с использованием методов кластерного анализа
Широкое применение сварочных технологий при создании ответственных машиностроительных конструкций потребовало внедрения более совершенных методов диагностики, способных своевременно обнаруживать в них дефекты. В качестве основных методов диагностики сварных швов в промышленности используются традиционные методы неразрушающего контроля (НК) – ультразвуковой (УЗ) и магнитный [1]. Эти методы определяют координаты и условные размеры, но не могут оценить степень опасности обнаруженного дефекта. Кроме того, для применения УЗ-метода необходимо исключить шероховатость поверхности контроля исследуемого объекта, а магнитный метод регистрирует в основном поверхностные дефекты.
138
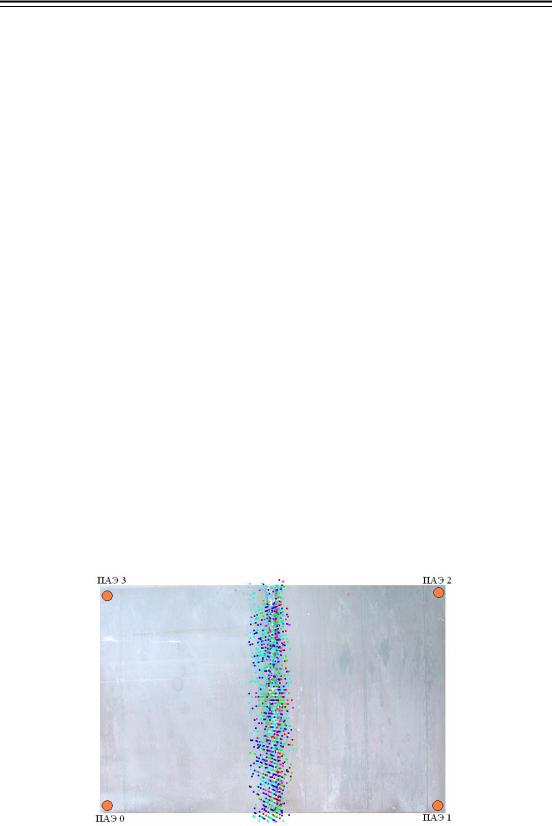
Л.Н. Степанова, К.В. Канифадин, И.С. Рамазанов
Современные методы диагностики позволяют осуществлять контроль не только после остывания сварного шва, но и в процессе сварки. К их числу относится метод акустической эмиссии (АЭ), являющийся наиболее перспективным методом и позволяющий определять внутренние дефекты сварного шва в процессе сварки и остывания, оперативно исправлять их с минимальным объемом выборки металла. При этом процесс АЭ-контроля осуществляется автоматически [2–3].
Однако для метода АЭ характерна высокая активность акустических сигналов, а так как процесс сварки сопровождается большим количеством паразитных источников (горение дуги, истечение защитного газа, плавление и т.д.), измерительные каналы АЭ-системы могут находиться в состоянии насыщения. Для исключения возможности перехода каналов в состояние насыщения была разработана АЭ-система СЦАД-16.10 (свидетельство RU.C.27.007.A № 40707, зарегистрирована в Государственном реестре средств измерений под номером 45154-10) с «плавающим» порогом селекции. В данной системе частота оцифровки сигнала может изменяться программно до 8 МГц, а чувствительность каждого канала системы может калиброваться с использованием встроенного имитатора сигналов АЭ.
Отработка методики АЭ-контроля дефектов сварки выполнялась на образцах из стали Ст3 с двусторонними швами. В работе использовался аппарат для полуавтоматической сварки ПДГО-510 и легированная проволока Св-08Г2С. Сигналы АЭ регистрировались АЭ-системой СЦАД-16.10 с использованием широкополосных преобразователей акустической эмиссии (ПАЭ) типа ПК 02-05 с полосой пропускания 100…700 кГц.
На рис. 1 показана локализация сигналов АЭ в момент сварки и остывания сварного шва, по которой невозможно сделать вывод о присутствии в сварном шве дефектов.
Рис. 1. Общая картина локализации сигналов АЭ при контроле процесса сварки
139
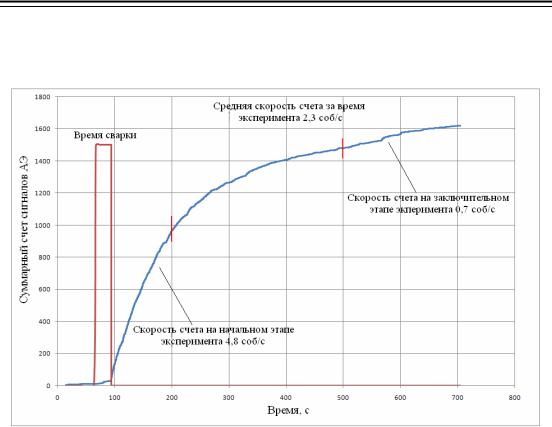
Диагностика и неразрушающие методы контроля
Запись сигналов АЭ продолжалась в течение 10 мин, так как по окончании данного временного промежутка скорость счета АЭ-сигналов уменьшилась в семь раз и в дальнейшем продолжала уменьшаться (рис. 2).
Рис. 2. График суммарного счета сигналов АЭ, зарегистрированных при контроле сварки
Для имитации дефектов в корень сварного шва при сварке добавлялись инородные включения (титановые и дюралюминиевые вставки). Оценка качества полученного сварного соединения выполнялась на основе анализа распределения суммарного счета (рис. 3, а) и энергетических параметров (см. рис. 3, б) зарегистрированных сигналов АЭ. На рис. 3, а показаны два максимума суммарного счета сигналов АЭ, значительно превышающие уровень шумов и соответствующие высокой концентрации источников акустических сигналов. Эти максимумы совпадают с координатами введенных в сварной шов титановых вставок.
Для более детального анализа на рис. 3, б приведено распределение энергии сигналов АЭ при локализации вдоль сварного шва. Только одному из максимумов суммарного счета соответствует значительное число сигналов с высоким уровнем энергии. Наличие совпадающих пиков на распределении суммарного счета и энергии обусловлено титановыми вставками, введенными в соответствующих зонах сварного шва. Однако подобная процедура анализа места расположения дефектов может занимать большой интервал времени, так как для построения различных распределений используются вспомогательные программы. Все это приводит к невозможности устранения дефекта в режиме ре-
140