
m0935
.pdf
Чернов Николай Меркурьевич
ском авиационном производственном объединении им. В.П. Чкалова и Сибирском государственном университете путей сообщения под научным руководством д-ра техн. наук, проф. В.А. Аксенова.
Основным результатом научных исследований Николая Меркурьевича явилось то, что был создан принципиально новый технологический процесс литья по выплавляемым моделям с кристаллизацией под давлением (ЛВМКД), обеспечивающий изготовление тонкостенных стальных деталей транспорта с гарантированной конструкционной прочностью при статических и циклических нагрузках. Создание способа литья по выплавляемым моделям с кристаллизацией под давлением можно квалифицировать как крупное научнотехническое достижение, не имеющее аналогов в мире, открывающее новое научное направление в развитии управляемых процессов литья.
В 2000 г. Николай Меркурьевич приглашен на должность профессора в Сибирский государственный университет путей сообщения на кафедру «Технология транспортного машиностроения и эксплуатация машин». С приходом на кафедру доктора технических наук, профессора Н.М. Чернова получило развитие новое научное направление – процессы формообразования многослойных керамических форм и формирования тонкостенных стальных деталей транспорта с кристаллизацией под давлением.
Основная научная идея данного направления заключается в следующем. Формирование мелкодисперсной однородной литой структуры и стабильных механических свойств в разных по толщине частях детали обеспечивается заливкой сплавов при температуре, близкой к ликвидус, с принудительным заполнением и кристаллизацией отливок под давлением, предельно допускаемая величина которого определяется гидравлической прочностью керамических форм. По результатам данного спектра исследований создана технология ЛВМКД, использование которой решает проблему изготовления тонкостенных стальных деталей особо ответственного назначения с гарантированной конструкционной прочностью в режиме длительной эксплуатации при циклических нагрузках.
Предложены также новые материалы, техпроцессы, установки и методы испытаний при изготовлении многослойных керамических форм, обеспечивающие получение в деталях без механической обработки гладких пазов и карманов, длинномерных отверстий малого диаметра. В автоматических линиях изготовления таких керамических форм исключается применение дорогостоящих робототехнических комплексов. Кроме того, теоретические исследования Николая Меркурьевича позволили впервые научно обосновать технологические параметры процессов изготовления выплавляемых моделей, многослойных оболочковых форм, плавки и заливки стали с кристаллизацией под давлением.
41

Биографии ученых-механиков СГУПСа
Важным научным и практическим результатом исследований Н.М. Чернова является также то, что им была разработана технология ЛВМКД для изготовления биметаллического режущего инструмента «сталь – твердый сплав ВК8», что открывает новую область применения процесса ЛВМКД для создания композиционных материалов на основе стали с уникальными свойствами. Технологические процессы литья по выплавляемым моделям предназначены для производства отливок особо ответственного назначения для железнодорожного транспорта, авиакосмической и атомной промышленности.
Результаты исследований Н.М. Чернова подтверждены шестью патентами
ивосемью авторскими свидетельствами. Список научных публикаций Н.М. Чернова включает 72 наименования. Интерес к научным разработкам и спектр творческого сотрудничества Николая Меркурьевича довольно широк. Это подтверждают его творческие связи с сотрудниками организаций ВИАМ, ВИЛС, НИАТ, Института горного дела СО РАН, заводами «Алмаз», Авиаинструмент, ОАО «НЗХК» и др.
Под научным руководством Н.М. Чернова на кафедре «Технология транспортного машиностроения и эксплуатация машин» были выполнены и в 2006 г. защищены две кандидатские диссертации.
Николай Меркурьевич Чернов, известный ученый в области технологии литейного производства и педагог высшей школы, был еще и замечательным человеком, простым и доброжелательным в общении, щедро отдающим знания
итворческие идеи своим последователям, ученикам.
Основные труды
1.Формирование биметаллического режущего инструмента сталь – твердый сплав литьем с кристаллизацией под давлением / Н.М. Чернов, Ю.П. Савинов, К.А. Медведев и др. Красноярск: Сиб. федеральный ун-т, 2008. 145 с.
2.Чернов Н.М., Аксенов В.А. Технологические основы процессов изготовления тонкостенных стальных деталей транспорта. Новосибирск: Изд-во СГУПСа, 2001. 155 с.
Доцент кафедры ТТМ и ЭМ, канд. техн. наук Г.Г. Ядрошникова
42
Раздел 2
НАУЧНЫЕ СТАТЬИ
43
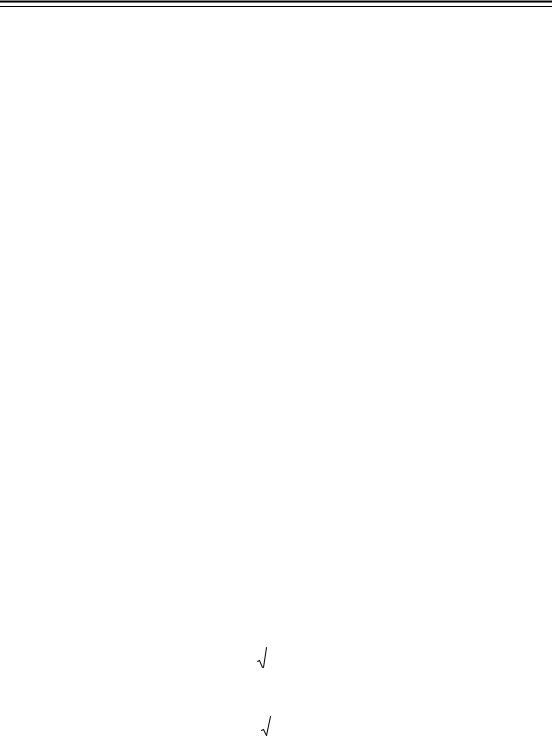
В.Н. Анферов
НАПРАВЛЕНИЕ «СИСТЕМЫ МАШИН НА ТРАНСПОРТЕ И В ТРАНСПОРТНОМ СТРОИТЕЛЬСТВЕ»
УДК 621.8
В.Н. Анферов
Расчетно-экспериментальные методы при проектировании спироидных передач
вмеханизмах машин
Кчислу основных эксплуатационных показателей зубчатых передач, определяющих их надежность, относятся нагрузочная способность, стойкость к динамическим и ударным нагрузкам, износостойкость и КПД. Последние два показателя оказывают существенное влияние на работоспособность передач зацеплением, особенно червячного типа.
Для передачи, параметры которой выбраны оптимально и которая эксплуатируется в условиях, соответствующих заданию на проектирование, износ зубьев является основным критерием утраты работоспособности. Поэтому оценка ресурса передачи является чрезвычайно важной и имеет во многих случаях решающее значение для определения ее долговечности.
В данной статье приводится методология оценки ресурса по износу наиболее применяемой в механизмах машин ортогональной передачи с цилиндрическим червяком, получившей название спироидной. Расчет ресурса по износу особенно актуален из-за повышенного скольжения в зоне зацепления. Метод расчета ресурса базируется на использовании принципиальной схемы расчета ресурса по износу различных узлов трения (подшипники скольжения, кулачковые механизмы, фрикционные и зубчатые передачи) [1].
Ресурс звеньев передачи по износу L, ч, может быть определен по форму-
лам [2]:
– для червяка
L1 |
|
|
|
[h1]V1 |
|
; |
(1) |
|||||
135J |
|
|
|
|
V n k |
|||||||
1 |
|
q |
||||||||||
|
|
|
|
|
|
|
s 1 |
|
|
|
||
– для колеса |
|
|
|
[h2 ]V2 |
|
|
|
|||||
L2 |
|
|
|
|
, |
(2) |
||||||
|
|
|
|
|
|
|
|
|
|
|||
135J2 |
|
|
q Vs n2 k |
|||||||||
|
|
|
|
|
|
где [h1], [h2] – допустимая величина износа червяка и колеса соответственно; V1, V2, Vs – значения окружных скоростей червяка, колеса и скорости скольжения соответственно в некоторой выбранной расчетной точке М(x, y, z); J1, J2 – интенсивность изнашивания материалов червяка и колеса соответственно (безразмерная характеристика линейного износа, связанная с толщиной h изно-
45
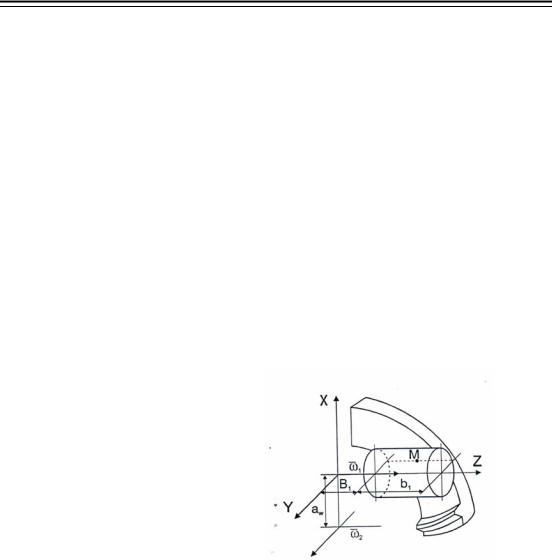
Системы машин на транспорте и в транспортном строительстве
шенного слоя зависимостью h = SJ, где S – путь трения скольжения в контакте зубьев); – упругая постоянная материалов контактирующих звеньев, связанная с коэффициентом Пуассона и модулем упругости Е первого рода мате-
риалов червяка и колеса зависимостью |
1 2 |
1 2 |
; q – нагрузка, прихо- |
|
1 |
|
2 |
||
|
E2 |
|||
|
E1 |
|
дящаяся на единицу длины контактной линии; – приведенный радиус кривизны контактирующих поверхностей в выбранной точке М в общем нормальном сечении, перпендикулярном контактной линии (для рассматриваемой передачи контакт зубьев теоретически является линейным); n1, n2 – частота вращения червяка и колеса, мин–1; k – число зон зацепления (k = 1 для одновенцовой передачи).
В соответствии с представленной на рис. 1 расчетной схемой и характерным для рассматриваемых передач расположением контактных линий и полей зацепления (рис. 2) можем принять следующие допущения:
–расчетная точка находится на делительном цилиндре червяка радиуса r1
всередине зацепляющейся части червяка длиной b1 и имеет координаты x = 0, y = –r1, z = B1 + 0,5b1, где B1 – уда-
ление зацепляющейся части червяка
от межосевой линии передачи;
– длина поля зацепления практически равна длине b1, а число контактных линий в одновременном зацеплении (коэффициент перекрытия) равно e = b1 / p mx, где р – винтовой параметр; mx – осевой модуль витков червяка;
– линии контакта на правых (R) и левых (L) боковых поверхно-
стях витков имеют расположение на червяке, близкое к радиальному; в связи с этим длину контактных линий l можно определить по формулам:
l |
R |
2h*m |
K |
R |
, |
l |
L |
2h*m |
K |
L |
, |
(3) |
|
a x |
|
|
|
a x |
|
|
|
где ha* – коэффициент высоты головки витка червяка (зуба колеса), принимае-
мый обычно ha* 1; KR, KL – поправочные коэффициенты (KR = 0,95…1,05;
KL = 1,25…1,4), которые с увеличением передаточного числа u уменьшаются;
– значения приведенного радиуса кривизны , которые зависят от множества исходных параметров (в большей степени от межосевого расстояния aw, углов профиля правых и левых боковых поверхностей витков R, L), можно
определить по следующим эмпирическим зависимостям: |
|
R (0,65 0,01 R )aw , |
(4) |
46
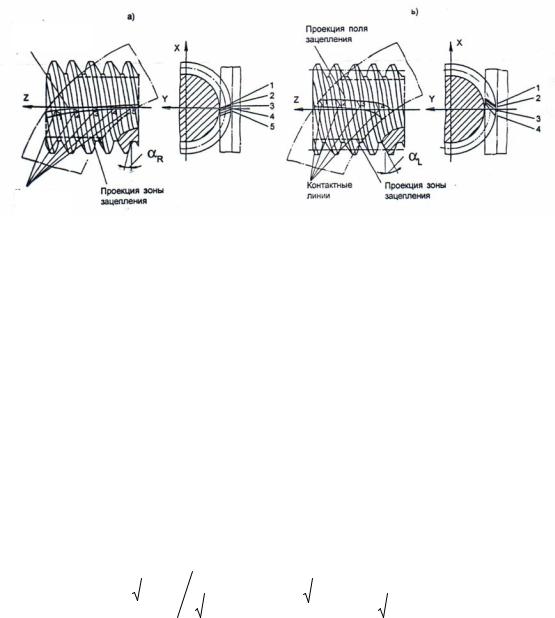
|
В.Н. Анферов |
|
|
L (3,5 0,065 L)aw , |
(5) |
где R , L – безразмерные коэффициенты, равные по величине абсолютным значениям углов R и L, град.
а) |
б) |
Проекция поля зацепления
Контактные
линии
Рис. 2. Расположение контактных линий и полей зацепления при работе правыми (а)
илевыми (б) боковыми поверхностями витков червяка
Сучетом принятых допущений, а также близкого к реальности предположения, что в предварительно приработанной передаче суммарная нагрузка G равномерно распределена по длине поля зацепления, интенсивность q нагрузки равна:
q |
G |
, |
(6) |
|
l
где l – суммарная длина контактных линий, которую будем определять по формуле
q |
G |
KK , |
(7) |
|
|||
|
2b1 KR,L |
|
где KK – коэффициент концентрации нагрузки (KK = 1,0…1,3), зависящий от точности передачи (для идеально точной передачи KK = 1,0).
Значение суммарной силы G в зацеплении с учетом сил трения в расчетной точке М найдем по формуле
|
|
|
|
f r2 u |
|
|
f a |
w |
|
|
|
|
|
p r cos |
|
||||
|
|
|
|
|
|
|
|
|
|
||||||||||
G T |
1 f 2 |
|
|
|
1 |
|
|
|
|
p2 |
r2 |
|
|
1 |
|
|
, |
(8) |
|
|
|
|
|
|
|
|
|
|
|
|
|||||||||
2 |
|
|
|
p2 |
r2 |
|
|
p |
|
|
|
1 |
|
|
p2 cos2 |
r2 |
|
||
|
|
|
|
|
|
|
|
|
|
|
|
|
|||||||
|
|
|
|
|
1 |
|
|
|
|
|
|
|
|
|
|
1 |
|
|
|
где T2 – нагрузочный момент на валу колеса; f – коэффициент трения скольжения; p – винтовой параметр (p = 0,5mx z1, где z1 – число заходов червяка); – угол профиля витка червяка в точке М.
Наконец, формулы для определения V1, V2, Vs в точке М для принятого расположения векторов (см. рис. 1) имеют вид:
47
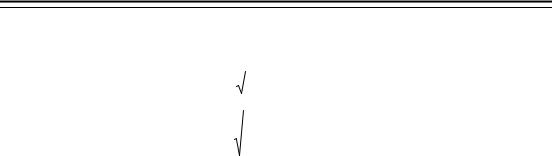
Системы машин на транспорте и в транспортном строительстве
V |
n1 r1 |
, |
|
|
|
|
|
|
|
|
|
|
|
|
(9) |
||||||
30 |
|
|
|
|
|
|
|
|
|
|
|
|
|
||||||||
1 |
|
|
|
|
|
|
|
|
|
|
|
|
|
|
|
|
|
|
|
||
|
|
|
n2 |
|
|
|
|
|
|
|
|
|
|
|
|
|
|
|
|||
V |
|
|
|
|
|
a2 |
|
(B 0,5b )2 |
, |
|
|
|
|
(10) |
|||||||
30 |
|
|
|
|
|
|
|||||||||||||||
2 |
|
|
|
|
|
|
w |
|
|
|
1 |
|
1 |
|
|
|
|
|
|
||
|
|
|
|
|
|
|
|
|
|
|
|
|
|
|
|
||||||
V |
|
|
n |
|
a |
w |
2 |
B |
0,5b |
r |
|
2 |
|
|
|||||||
|
|
1 |
|
|
|
|
|
|
|
1 |
|
1 |
|
. |
(11) |
||||||
30 |
|
|
|
|
|
u |
|
||||||||||||||
s |
|
|
|
|
4 |
|
|
|
|
1 |
|
|
|
|
Из приведенных зависимостей (1)–(11) видно, что при заданных исходных параметрах aw, u, b1, B1, r1, mx, R, L, n1, определяющих геометрию и кинематику передачи, ключевым параметром для определения ее ресурса по износу является интенсивность изнашивания J. Величину J можно находить расчетным путем. Однако известные аналитические методы расчета J дают лишь весьма приближенную оценку, в связи с чем эксперимент следует считать основным источником нахождения его корректного значения.
Эффективным способом накопления информации по интенсивности изнашивания является физическое моделирование, позволяющее с минимальными материальными и временными затратами получить количественные данные для различных сочетаний конструкционных и смазочных материалов [3].
Метод физического моделирования базируется на общности физикомеханических процессов трения, происходящих в зоне контакта звеньев передачи, и простых по геометрической форме экспериментальных образцов. Моделируя спироидное зацепление, мы оценивали антифрикционные свойства трансмиссионных масел для спироидной передачи, работающей в непрерывном и повторно-кратковременном режимах. Рассчитанные по результатам экспериментов коэффициенты трения в контакте образцов использовались для расчета сил, действующих в спироидном зацеплении, коэффициента полезного действия, ресурса по износу, а также для теплового расчета редукторов со спироидной передачей.
Библиографический список
1.Дроздов Ю.Н. К расчету зубчатых передач на износ // Машиноведение. 1969. № 2.
С. 26–33.
2.Дроздов Ю.Н., Анферов В.Н. К расчету спироидных передач по износу // Расчетноэкспериментальные методики оценки трения и износа. М.: Наука, 1980. С. 19–22.
3.Анферов В.Н. Исследование износостойкости спироидных цилиндрических передач методом роликовой аналогии // Вестник машиностроения. 1981. № 6. С. 27–29.
48
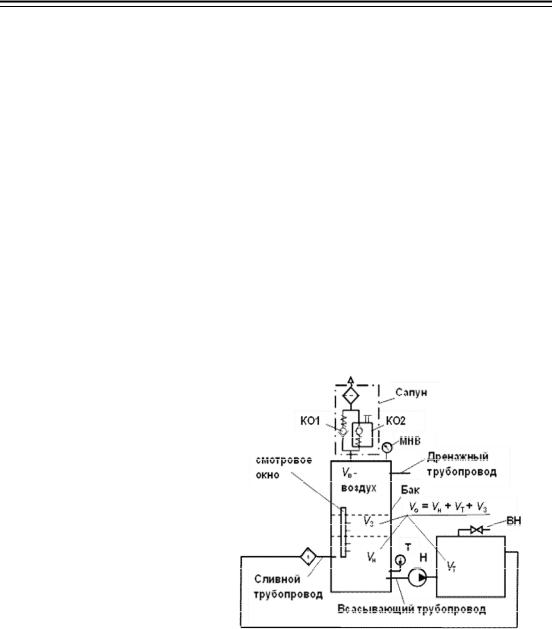
Н.В. Мокин, Н.А. Маслов, В.С. Воробьев
УДК 621.2
Н.В. Мокин, Н.А. Маслов, В.С. Воробьев
Совершенствование гидропривода машин
За последние годы на кафедре «Подъемно-транспортные, путевые, строительные и дорожные машины» выполнены работы, посвященные закрытым гидропередачам, тепловой защите гидропередач, энергосберегающим стендам для испытания гидромашин.
Закрытые гидропередачи
Объемные гидропередачи большинства технологических машин выполнены открытыми, т.е. их масляные баки сообщены с атмосферой воздушным фильтром, через который в гидросистему проникают воздух, пыль и пары воды. Это сокращает срок службы масла, насосов, клапанов, увеличивает затраты на обслуживание и ремонт.
Известны устройства для герметизации масляного бака гидропередач [1, 2], однако широкое применение они нашли в основном в гидропередачах летательных аппаратов [3].
Один из способов герметизации бака – использование запертого в нем воздуха, упругие свойства которого позволяют вмещать переменный объем масла.
На рис. 1 изображена упрощенная схема такой гидросистемы. Фильтр снабжен двумя клапанами: КО1 ограничивает избыточное давление в баке, КО2 ограничивает вакуум. При известных допустимых давлениях можно настрой-
кой клапанов и выбором объема воздуха Vв исключить или существенно ограничить соединение бака с атмосферой.
Максимально возможное приращение объема масла в баке определено применительно к гидросистеме одноковшового экскаватора. В качестве условий расчета приняты два предельных состояния:
а – штоки всех гидроцилиндров выдвинуты, температура масла минимальная, например, Тmin = –30 оС (243 К), объем масла в баке минимальный;
49

Системы машин на транспорте и в транспортном строительстве
б – штоки всех гидроцилиндров втянуты, температура масла максимальная, например, Тmax = 80 оС (353 К), объем масла в баке максимальный.
Максимальное приращение объема масла при переходе из состояния а в состояние б равно: ∆V = ∆VЦ + ∆VТ, где ∆VЦ – сумма разностей объемов поршневых и штоковых полостей гидроцилиндров рабочего оборудования машины; ∆VТ – приращение объема масла при повышении его температуры на величину
∆Т = (Тmax – Тmin).
Величина ∆VT = α∆ТVО, где α – коэффициент теплового расширения масла; VО – объем масла в системе, включающий в себя (см. рис. 1): VН – минимально необходимый объем масла в баке при температуре Тmin; VТ – объем масла в трубопроводах, клапанах и гидродвигателях при полностью выдвинутых штоках гидроцилиндров; VЗ – объем масла, принимаемый в качестве запаса для учета погрешностей расчета и компенсации возможных утечек из системы.
Состояние а принято за исходное при определении необходимого объема воздуха в баке. Давление масла и воздуха после заправки – атмосферное. Если после заправки клапаны КО1 и КО2 закрыты, масса воздуха в баке постоянная. Его параметры описаны уравнением pV/T = const, где р – абсолютное давление, Па; V – объем, м3; Т – температура, К.
При переходе из состояния а в состояние б давление в баке повышается от pатм до pmax, а объем воздуха уменьшается от максимального начальногоVВН до минимального конечного VВК, при этом pатмVВН /Тmin = pmaxVВК /Тmax. Отно-
шение конечного объема воздуха к начальному: |
|
VВК /VВН = pатмТmax /(Тminpmax). |
(1) |
Разность объемов воздуха VВН – VВК равна суммарному приращению объ-
ема масла ∆V при переходе гидросистемы из состояния а в состояние б: |
|
∆V = VВН – VВК = VВН(1 – pатм Тmax /(pmaxТmin)). |
(2) |
Величина 1 – pатмТmax /(pmaxТmin) = δ – относительное уменьшение началь- |
ного объема VВН воздуха в баке. Из уравнения (2) VВН = ∆V / δ.
Герметизация бака описанным выше способом возможна, а объем воздуха в баке приемлем, если допустимое давление в баке не менее 0,2 МПа (таблица).
Необходимые начальные объемы воздуха в баке при различных давлениях рmax настройки клапана избыточного давления
Вместимость элементов |
pmax, МПа |
VТ, л |
VЦ, л |
ΣΔV, л |
δ |
VВН, л |
||||
гидросистемы машины, л |
||||||||||
VН |
VЗ |
VТ |
VО |
|
|
|
|
|
|
|
|
|
|
|
0,15 |
|
|
|
0,022 |
8636 |
|
500 |
50 |
300 |
830 |
0,20 |
82 |
108 |
190 |
0,267 |
712 |
|
0,25 |
0,414 |
459 |
||||||||
|
|
|
|
|
|
|
||||
|
|
|
|
0,30 |
|
|
|
0,511 |
372 |
50