
m0935
.pdf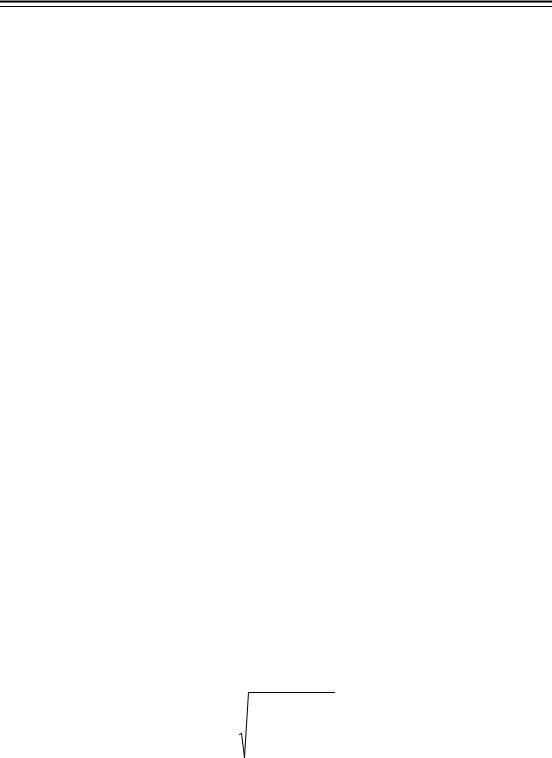
Л.Н. Степанова, Е.С. Тенитилов
происходящими в реальных объектах контроля (ОК) при эксплуатационных нагрузках [3–5].
Методы нагружения играют очень важную роль, так как для инициирования источников сигналов АЭ необходима нагрузка, превышающая рабочую на 10–25 %. В контролируемых зонах конструкции за счет действия нагрузки обеспечивается напряженное состояние, вызывающее появление акустических сигналов из дефектных зон.
В процессе развития дефекта выделяется энергия, распространяющаяся по ОК в виде акустических волн, которые регистрируются преобразователями акустической эмиссии (ПАЭ), неподвижно установленными на объект и образующими пьезоантенны, которые покрывают его в виде сетки.
Значительный уровень шумов датчиков, нагружающих устройств (НУ) и самой конструкции снижает чувствительность метода и затрудняет расчет координат дефектов, а проводимая фильтрация может привести к пропуску полезных сигналов. Во время АЭ-контроля регистрируются не только связанные с дефектами шумы, но и посторонние. Поэтому большое число зарегистрированных сигналов относятся к акустическим помехам, а данный метод требует тщательной методической проработки и проведения предварительных испытаний. Обработка результатов АЭ-контроля показала, что даже опасные дефекты могут быть относительно слабыми источниками упругих волн, которые регистрируются ПАЭ. Это связано с протяженными зонами контроля, литой структурой металла, расположением дефекта, величинами нагрузок, большим затуханием сигналов АЭ и т.д. [6–8].
Применение более совершенных методов обработки сигналов АЭ позволило уточнить их начало и с меньшими погрешностями решать локационные задачи. Для повышения точности расчета координат дефектов разработан способ определения времени прихода сигналов АЭ на основе алгоритма временного окна (рис. 1), передвигающегося по реализации. При этом выбирается реализация сигнала АЭ в виде Т отсчетов аналого-цифрового преобразователя (АЦП) и анализируется уровень сигналов в этом окне. При превышении сигналом в окне заранее установленного порога cелекции регистрируется момент времени его прихода. В качестве основного параметра выбирается среднеквадратическое отклонение (СКО) σ [9]:
i t2
(xii xср )2
|
i t1 |
|
, |
(t2 t1 |
|
||
|
1) |
i
где xi – текущее значение реализации сигнала АЭ; хср – среднее значение реа-
лизации сигнала АЭ во временном окне; t1, t2 – номера отсчетов АЦП, соответствующие моменту начала и окончания установки временного окна.
151
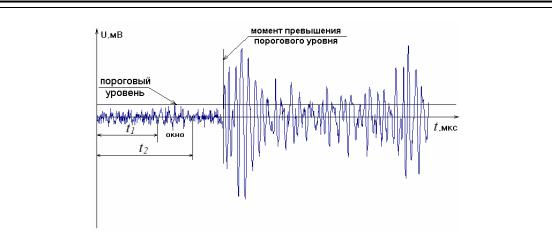
Диагностика и неразрушающие методы контроля
Рис. 1. Определение времени прихода сигнала АЭ по его форме
При этом случайные единичные выбросы в реализации сигнала АЭ практически не оказывают влияния на точность расчета времени его прихода. Такой метод обработки позволяет локализовать сигналы АЭ с затянутыми фронтами, что характерно для удаленных источников. Для сигналов АЭ от усталостных трещин, а также шумовых сигналов используется кластерный анализ, позволяющий распределять их по зонам активности. Кроме того, для каждой отдельной зоны рассчитываются коэффициенты взаимной корреляции по форме и спектру. В качестве целевой функции выбрана корреляционная функция вида [9]:
|
n |
xj,k xj |
|
1 |
xi,k xi |
||
k 0 |
|
, |
|
n xi |
|
||
|
xj |
где n – размерность массива с цифровой реализацией сигнала; xi,k, xj,k – значение амплитуды сигналов i и j в момент времени k в его цифровой реализации; xi, xj – выборочные средние значения амплитуды сигналов i и j в цифровой реализации; xi , xj – дисперсия амплитуды сигналов i и j в цифровой реализации.
Средства АЭ-контроля строятся на основе микропроцессорной техники, осуществляющей автоматическое измерение, обработку и постановку диагноза ОК в режиме реального времени [10].
Основой методики контроля боковых рам, применяемой в системе СЦАД-16.03 (свидетельство об утверждении типа средств измерений RU.C.27.007.A № 39729, зарегистрирована в Государственном реестре средств измерений под номером 18892-10), является статистическая обработка банка данных. Методика контроля включает определение координат дефектов и расчет интегрального коэффициента опасности R [6]. Для практического использования данной методики разработана программная расчетная модель, при использовании которой на зоны контроля наносятся локационные сетки (рис. 2, а), задающие поля уровней браковки. Размер ячейки локационной сетки опре-
152
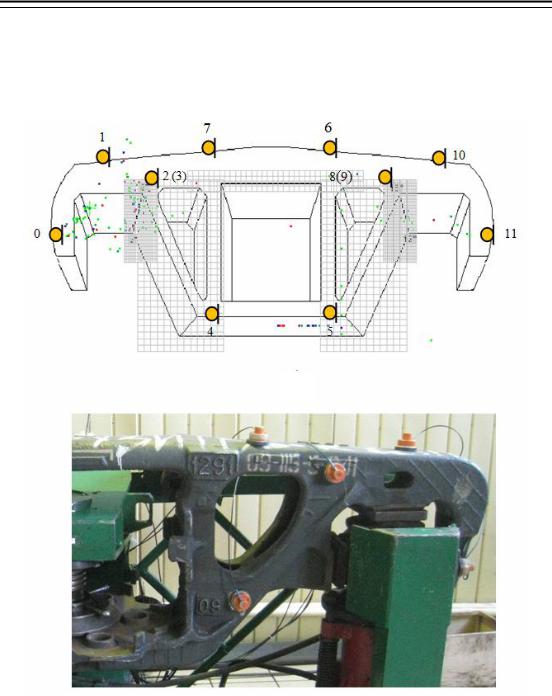
Л.Н. Степанова, Е.С. Тенитилов
деляется исходя из скорости распространения акустического сигнала в материале ОК и реализуемой точности локализации источника сигналов АЭ. Сигналы, регистрируемые из зоны разрушения, анализируются на принадлежность к одному источнику, для чего используются их спектральные характеристики, амплитуда, форма и корреляционная связь между ними [6].
а)
б)
Рис. 2. Нанесение локационной сетки на боковую раму: а – схема; б – фотография
Разработанная методика браковки боковых рам основана на подсчете числа сигналов N, попавших в зону браковки. В каждой ячейке браковочной сетки число сигналов сравнивалось с пороговым числом nпор. При выполнении неравенства N > nпор ячейки помечались как дефектные или подозрительные.
153

Диагностика и неразрушающие методы контроля
Интегральный коэффициент опасности RM находился в результате статистической обработки коэффициентов опасности по всем группам сигналов.
По результатам локализации дефектов выделяется группа сигналов, каждой их которых предположительно соответствует один микроисточник, для которого рассчитывается интегральный коэффициент опасности R и ставится ди-
агноз [11–13].
Для каждого из источников по амплитуде Ai, частоте fi и времени нарастания переднего фронта tпфi рассчитывается интегральный коэффициент опасности R [6]:
N
R d RA(Ai ) Rf ( fi ) Rпф(tпфi ) ,
i 1
где d – групповой признак, определяющий принадлежность сигналов к группе с близкой локализацией; N – число сигналов в группе; RA(Аi), Rf(fi), Rпф(tпфi) – аналитические зависимости, характеризующие вклад соответствующих параметров сигнала АЭ в коэффициент опасности R.
В процессе диагностики в главном окне программы выбирается режим «диагноз» и АЭ-система анализирует все локализованные сигналы, образуя из них группы, объединенные в кластеры. Степень опасности дефекта оценивается по наиболее развитой группе источников, обладающих максимальным коэффициентом опасности R, определяемым по приведенной выше формуле.
Параметры сигналов АЭ коррелируют с кинетикой развития дефектов под нагрузкой, поэтому данный метод позволяет получать объективную информацию о динамике развития дефекта, прочности и надежности конструкций. Однако при распространении по конструкции сигналов АЭ происходит их искажение, связанное с наличием дисперсии, переотражений и структурных неоднородностей материала. Поэтому качество испытаний боковых рам в значительной степени зависит от методики, позволяющей фильтровать ложные сигналы. Решение задачи по идентификации сигналов АЭ и определению их принадлежности к одному источнику требует разработки способов, обеспечивающих их достоверную и устойчивую локализацию [11–13].
На рис. 2, б показана находящаяся в депо боковая рама коробчатого сечения с установленными ПАЭ. В процессе АЭ-контроля ее нагружают двумя типами нагрузок. Первое нагружение осуществляют горизонтальной силой Fг = 120 кН, распирающей буксовый проем. В процессе горизонтального нагружения контролируются внутренние и наружные углы буксовых проемов. Второе нагружение производят вертикальной силой Fв = 560 кН, прикладываемой к опорным поверхностям буксовых проемов с упором в рессорном проеме. При вертикальном нагружении контролируется внутренний угол буксового проема, кромки технологических отверстий, наклонный пояс и углы рессорного проема.
154
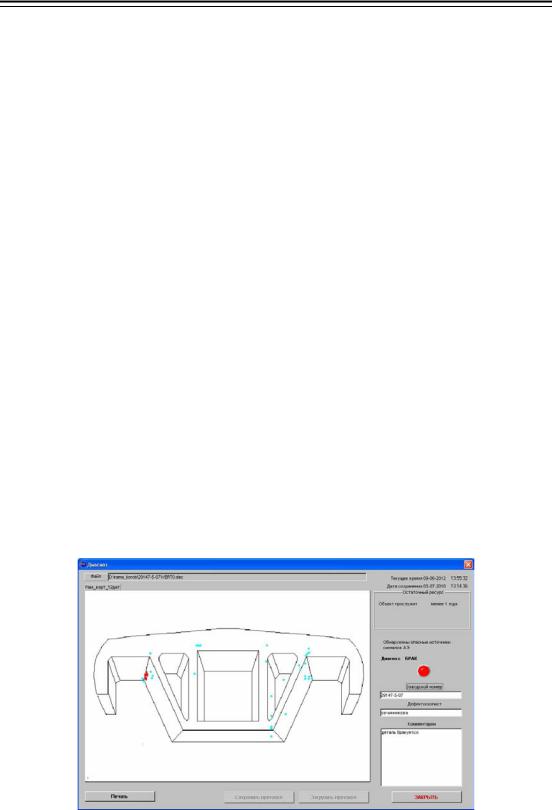
Л.Н. Степанова, Е.С. Тенитилов
Акустические сигналы, не связанные с развитием усталостных дефектов в материале боковой рамы коробчатого сечения, возникают вследствие трения, наличия внутри формовочной смеси, цемента и загрязнений в местах взаимодействия НУ с ее опорными поверхностями [4–5]. Форма помех, их амплитудные, временные и частотные характеристики определяются акустическими свойствами ОК, ПАЭ и параметрами измерительных каналов АЭ-системы. В условиях депо такие помехи часто оказываются идентичными сигналам от развивающихся дефектов, поэтому их сложно исключать из суммарного потока.
В 2011 г. на ОАО «НПК “Уралвагонзавод”» были проведены испытания четырех боковых рам коробчатого сечения, забракованных при ТО-3 в ВЧДР Ленинск-Кузнецкий Западно-Сибирской ДРВ. Перед их нагружением был проведен визуальный и магнитопорошковый контроль. Магнитным индикатором являлась суспензия на основе КМС «Диагма-1100». Напряженность поля в центре намагниченного участка R-55 составила 25 А/см. Затем с использованием АЭ-системы СЦАД-16.03 (зав. № 32, свидетельство о поверке № 034388) были уточнены координаты дефектов.
На рис. 3 показаны зоны локализации сигналов АЭ, на основании которых выполнена браковка боковой рамы коробчатого сечения № 29147, изготовленной заводом с клеймом 5 в 2007 г.
Затем в местах локализации сигналов АЭ данная боковая рама была разрезана (рис. 4, а). В ее в левом и правом углах буксового проема (см. рис. 4, б, в) обнаружены раковины размерами 25 15 мм и 27 14 мм и глубиной более 40 мм. На основании визуального осмотра разрезанных фрагментов в углах буксовых проемов боковой рамы были обнаружены допустимые и недопустимые литейные дефекты, забракованные АЭ-методом.
Рис. 3. Пример браковки боковой рамы № 29147 коробчатого сечения
155
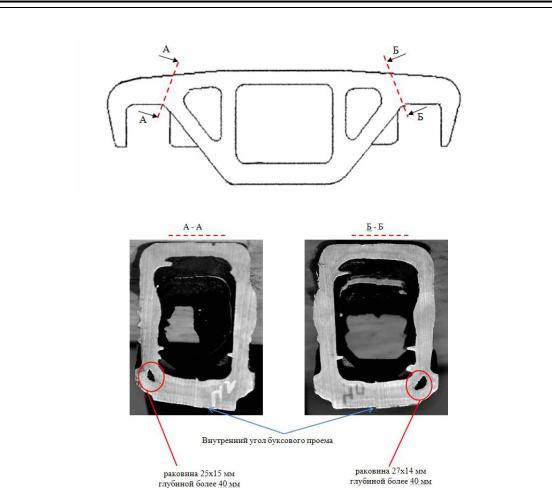
Диагностика и неразрушающие методы контроля
а)
б) |
в) |
Рис. 4. Результаты разрезки боковой рамы № 29147:
а – схема разрезки; б – фотография сечения левого буксового угла; в – фотография сечения правого буксового угла
Для корректировки методики АЭ-контроля из верхнего пояса забракованных боковых рам коробчатого сечения были изготовлены образцы размером 200 100 10 мм с пропилом длиной 45 мм. На рис. 5 показан внешний вид образца с раковиной, установленного в электрогидравлическую машинуMTS-50.
По схеме, имитирующей процесс эксплуатации боковых рам коробчатого сечения, к образцу попеременно прикладывали циклическую и статическую нагрузки. После наработки определенного числа циклов нагрузкой Р1 = 25 кН с частотой 5 Гц образец нагружался статической нагрузкой Р2 = 30 кН. Чередование циклической и статической нагрузок приводило к зарождению усталостной трещины, ее дальнейшему развитию и разрушению образца.
156
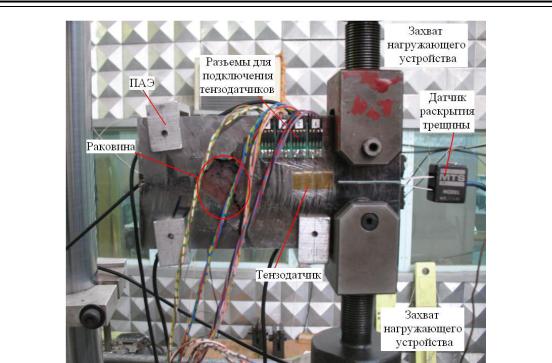
Л.Н. Степанова, Е.С. Тенитилов
Рис. 5. Внешний вид образца с раковинами, установленного в нагружающую машину MTS-50
Запись АЭ-информации осуществляли АЭ-системой СЦАД-16.10 с плавающим порогом селекции (свидетельство RU.C.27.007.A № 40707, зарегистрировано в Государственном реестре средств измерений под номером 45154-10) при приложении как циклической, так и статической нагрузок на всем протяжении испытаний образца [10]. Среди преимуществ микропроцессорной многоканальной АЭ-системы СЦАД-16.10 следует отметить, что частота оцифровки сигналов может программно изменяться до 8 МГц. Кроме того, автоматическая калибровка позволяет сократить время установки ПАЭ на боковую раму и осуществляет локализацию с учетом смещения координат датчиков. При этом плавающие пороги селекции исключают переход измерительных каналов системы в режим насыщения.
Одновременно с регистрацией АЭ-информации при статическом и циклическом нагружениях образца осуществляли измерение деформаций в зоне концентратора напряжений. Для этого в районе пропила на пути развития усталостной трещины были наклеены четыре проволочных тензодатчика типа ПКС сопротивлением R = 120 Ом, с базой L = 8 мм и коэффициентом тензочувствительности К = 2,12 (сертификат RU.C.007.A № 30935, зарегистрирован в Государственном реестре средств измерений под номером 37343-08). Измерение деформаций (рис. 6, а) проводили многоканальной микропроцессорной тензометрической системой ММТС-64.01 (свидетельство RU.C.34.007.A № 44412, регистрационный номер № 21760-01).
157
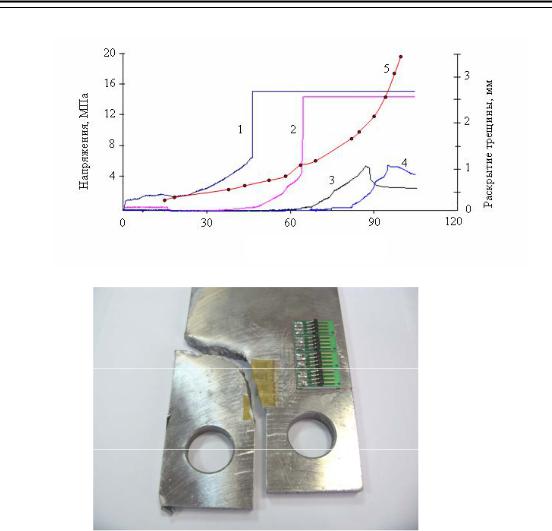
Диагностика и неразрушающие методы контроля
а)
Число циклов п ∙ 103
б)
Рис. 6. Результаты испытаний образца № 6:
а– показания тензодатчиков и датчика раскрытия трещины в зависимости от числа циклов;
б– внешний вид разрушенного образца; 1, 2, 3, 4 – номера тензодатчиков;
5 – датчик раскрытия трещины
При первом нагружении, которое продолжалось 7,2∙103 циклов, незначительное изменение напряжения на образце почувствовал только самый близкий к концентратору тензодатчик. Через 46∙103 циклов усталостная трещина продвинулась на 5 мм, прошла под тензодатчиком 1 и он перешел в неработоспособное состояние. Скорость развития трещины увеличилась, и через 14∙103 циклов после разрушения первого тензодатчика разрушился второй тензодатчик. Затем усталостная трещина изменила направление продвижения, в результате чего тензодатчики 3 и 4 оставались работоспособными до конца испыта-
ний (см. рис. 6, б) [6].
Размер раскрытия усталостной трещины контролировали штатным датчиком электрогидравлической машины MTS-50. На рис. 7 показаны графики
158
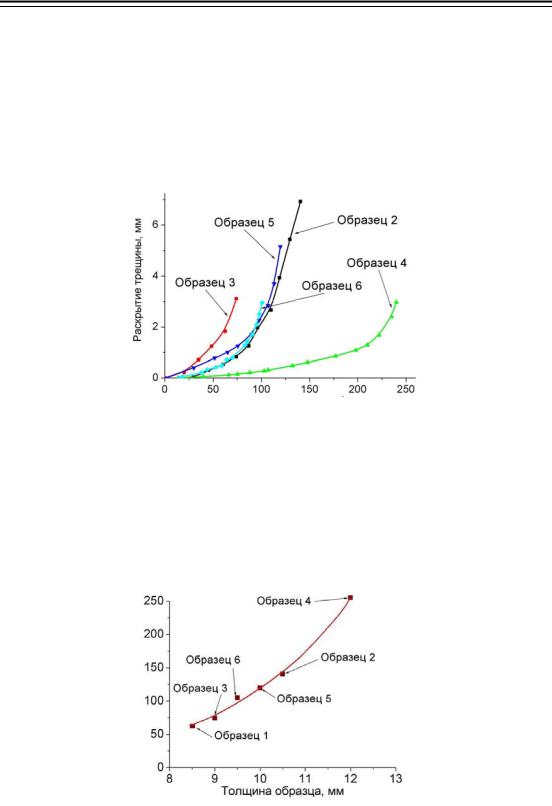
Л.Н. Степанова, Е.С. Тенитилов
зависимости раскрытия усталостной трещины от числа циклов нагружения. Усталостные трещины у всех образцов развивались по экспоненциальному закону, но обладали разной зависимостью величины раскрытия от числа циклов нагружения. Различие в величинах раскрытия объясняется разнонаправленностью распространения усталостных трещин и большим разбросом в скорости их продвижения в образцах. Это можно объяснить как разбросом по толщине образцов, которая изменялась от 8,5 до 12,5 мм, так и наличием дефектов в материале образцов.
Число циклов п ∙ 103
Рис. 7. График зависимости раскрытия усталостной трещины от числа циклов нагружения
На рис. 8 показана экспоненциальная экспериментальная зависимость числа циклов, при которых произошло разрушение образов, от их толщины. Наибольшее число циклов (250 тыс.) выдержал образец № 4 толщиной 12,5 мм, наименьшее – (60 тыс.) выдержал образец № 1 толщиной 8,5 мм. Количество циклов до разрушения образцов связано экспоненциальной зависимостью с их толщиной.
Число циклов п ∙ 103
Рис. 8. Зависимость числа циклов, при которых произошло разрушение образцов, от их толщины
159

Диагностика и неразрушающие методы контроля
Как следует из рис. 8, изменение толщины образца на 3,5 мм приводит к увеличению числа циклов до его разрушения более чем в три раза. Это необходимо учитывать при разработке конструкции боковой рамы для определения оптимальной толщины стенок коробчатого сечения, которая позволила бы существенно повысить живучесть конструкции.
По результатам проведенного исследования сделаны следующие выводы:
1.Проведены АЭ-испытания боковых рам коробчатого сечения в вагонных ремонтных депо на штатных АЭ-комплексах. Методом АЭ подтверждены трещины, обнаруженные штатными методами контроля, что позволило скорректировать критерий браковки.
2.Проведены испытания боковых рам коробчатого сечения на ОАО «НПК “Уралвагонзавод”». В результате разрезки боковой рамы коробчатого сечения по внутреннему углу буксового проема были обнаружены литейные дефекты, ранее зарегистрированные АЭ-методом с использованием системы СЦАД-16.03.
3.Системой СЦАД-16.10 с «плавающим» порогом селекции записывались сигналы АЭ как при циклическом, так и при статическом нагружении образцов, выполненных из верхнего пояса забракованных боковых рам коробчатого сечения. Локализацию сигналов АЭ осуществляли как в устье развивающейся трещины, так и в зоне расположения пор. Анализ результатов испытания образцов показал, что количество циклов, при которых образцы разрушались, существенно зависит от их толщины. Увеличение толщины образцов на 3,5 мм позволило повысить число циклов до разрушения образцов в 3,3 раза.
Библиографический список
1.Грассман С.А., Больчанов А.А., Степанова Л.Н. и др. Акустико-эмиссионный контроль боковой рамы тележки грузового вагона // Железнодорожный транспорт. 2011. № 12. С. 45–47.
2.Конькова Т.Е., Беловодский А.Б., Великанов А.В. О путях повышения эксплуатационной надежности стальных литых деталей тележек грузовых вагонов // Вестник ВНИИЖТ. 2009.
№1. С. 22–26.
3.Акустико-эмиссионный контроль железнодорожных конструкций / А.Н. Серьезнов, Л.Н. Степанова, В.В. Ивлиев и др. Новосибирск: Наука, 2011. 272 с.
4.Степанова Л.Н., Бобров А.Л., Кабанов С.И. и др. Расширение возможностей использования метода акустической эмиссии для диагностики литых деталей подвижного состава // Дефектоскопия. 2010. № 1. С. 64–72.
5.Степанова Л.Н., Грассман С.А., Кабанов С.И. и др. Акустико-эмиссионный контроль боковых рам коробчатого сечения // Дефектоскопия. 2011. № 3. С. 10–16.
6.Муравьев В.В., Степанова Л.Н., Кареев А.Е. Оценка степени опасности усталостных трещин при акустико-эмиссионном контроле тележки грузового вагона // Дефектоскопия. 2003.
№1. С. 63–68.
7.Верескун В.Д., Степанова Л.Н., Бехер С.А. и др. Акустико-эмиссионный контроль боковых рам тележек грузовых вагонов при деповском ремонте // Контроль. Диагностика. 2013.
№1. С. 67–71.
160