
m0935
.pdf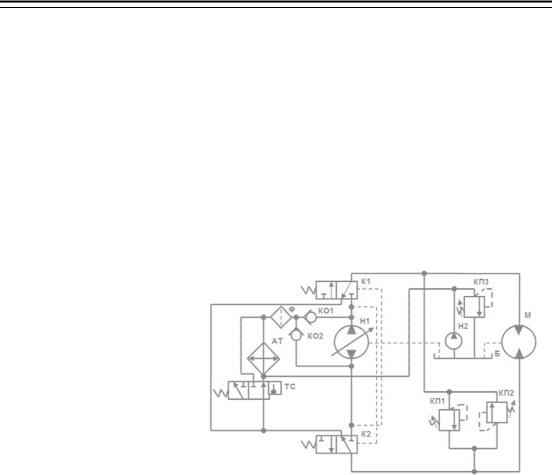
Н.В. Мокин, Н.А. Маслов, В.С. Воробьев
Совершенствование системы охлаждения замкнутой реверсивной гидропередачи
В замкнутой гидропередаче силовой поток масла циркулирует в контуре: насос – гидромотор – насос. В типовых схемах из линии на пути гидромотор – насос на охлаждение отводится примерно 20 % подачи силового насоса. В установившемся тепловом режиме температура этого потока должна быть понижена в охладителе настолько, чтобы на входе в силовой насос при смешивании малого охлажденного и большого неохлажденного потоков получить близкую к оптимальной температуру масла, например 50 оС. В тяжелом режиме работы гидропередачи и при высокой температуре воздуха добиться этого невозможно. Эта проблема еще более актуальна для гидропередач с номинальным дав-
лением 32 МПа и более. |
|
|||
|
Если замкнутая гид- |
|
||
|
|
|||
ропередача нереверсивная, |
|
|||
задача решается постанов- |
|
|||
кой охладителя в силовой |
|
|||
контур. Чтобы в реверсив- |
|
|||
ной |
передаче |
пропустить |
|
|
весь поток силового кон- |
|
|||
тура |
через |
охладитель, |
|
|
разработана иная принци- |
|
|||
пиальная |
схема передачи |
|
||
(рис. 2). |
|
|
Рис. 2. Схема замкнутой реверсивной гидропередачи |
|
|
Весь поток силового |
|||
контура |
при |
любом на- |
с охлаждением всего потока силового контура |
|
|
правлении вращения вала гидромотора направлен через охладитель с помощью клапанов К1, К2, КО1 и КО2. Насос Н2 предназначен для возврата в силовой контур через охладитель АТ только дренажных утечек насоса Н1 и гидромотора М. Если насос Н1 подает масло в сторону клапана К1, последний своей пружиной будет переведен в позицию, пропускающую поток к гидромотору М. Силовой (он же охлаждаемый) поток течет через элементы: Н1 – К1 – М – К2 – термостат ТС – АТ – Ф – КО2 – Н1. Насос Н2 возвращает дренажные утечки в силовой контур по пути: Б – Н2 – АТ – Ф – КО2 – Н1. Если насос Н1 подает масло в сторону клапана К2, силовой поток течет через элементы: Н1 – К2 – М – К1 – термостат ТС – АТ – Ф – КО1 – Н1. Клапаны К1 и К2 автоматически переключаются при смене направления подачи насосом Н1.
Энергосберегающие стенды для испытания гидромоторов и насосов методом замкнутого контура
Приемо-сдаточные, послеремонтные испытания объемных гидромоторов и насосов выполняют в основном методом разомкнутого контура, в котором нагрузку на вал гидромотора создают тормозными устройствами или насосами,
51
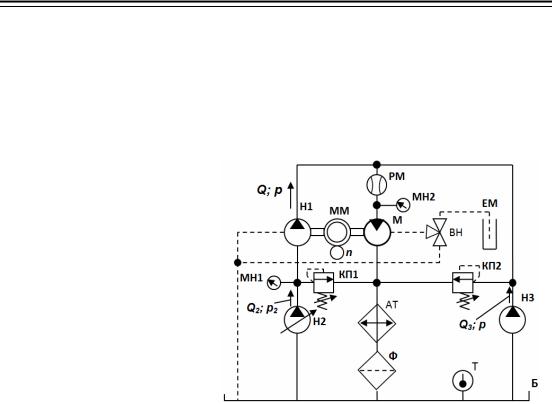
Системы машин на транспорте и в транспортном строительстве
работающими на дроссельную нагрузку [4]. Для таких испытаний требуется много энергии и времени. Авторами исследованы два иных метода испытаний, которые лишены указанных недостатков. Это испытания гидромотора и насоса:
а – в замкнутом контуре на номинальную квазистатическую нагрузку; б – в замкнутом контуре на инерционную нагрузку.
В разработанной схеме стенда, работающего по методу а (рис. 3), валы испытуемых гидромотора М и насоса Н1 соединены между собой, а напорная линия насоса Н1 соединена с напорной линией мотора М.
При вращении валов гидромотора и насоса в контуре Н1 – М – Н1 циркулирует необходимая для испытаний мощность, если:
– в напорную линию |
|
|
контура насосом Н3 подает- |
|
|
ся расход, равный расходу |
|
|
дренажных утечек из мото- |
Рис. 3. Схема стенда для испытания гидромотора |
|
ра М, и поддерживается не- |
||
и насоса методом замкнутого контура |
||
обходимое в этой линии ис- |
|
|
пытательное давление; |
|
– во всасывающую линию насоса Н1 насосом Н2 подается расход, равный сумме расходов в напорной линии насоса Н1 и дренажных утечек из насоса Н1. Давление этой подачи должно быть достаточно для преодоления механических и гидромеханических потерь энергии в контуре Н1 – М – Н1. Этим же давлением контур Н1 – М – Н1 запускается в работу.
Кпримеру, при давлении в напорной линии 25 МПа и расходеQ = 0,004 м3/с
вконтуре Н1 – М – Н1 циркулирует мощность 100 кВт.
Энергия, необходимая для циркуляции мощности в контуре Н1 – М – Н1, подается насосами Н2 и Н3. Мощность привода насоса Н2 мала, так как мало необходимое давление во всасывающей линии насоса Н1. Мощность привода насоса Н3 тоже мала, так как мала его подача – примерно 5 % от расхода дренажных утечек Q в моторе М.
Наличие моментомера ММ, расходомера РМ, частотомера n и манометра МН позволяет измерить параметры, необходимые для вычисления наиболее информативного диагностического параметра – КПД испытуемых гидромашин.
При испытании гидромотора М мощностью 100 кВт суммарная мощность электродвигателей стенда (приводы насосов Н2 и Н3) не превышает 40 кВт. При использовании же стенда с разомкнутым потоком энергии необходимы
52
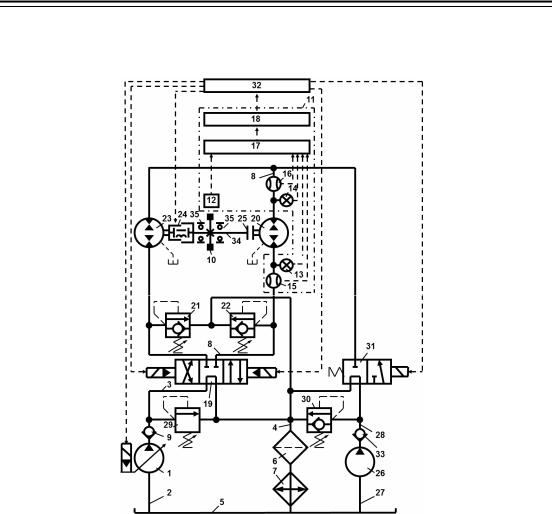
Н.В. Мокин, Н.А. Маслов, В.С. Воробьев
электродвигатель привода насоса Н1 мощностью примерно 130 кВт и устройство мощностью 100 кВт для нагружения гидромотора М.
Рис. 4. Предлагаемая схема энергосберегающего стенда для испытаний гидромашин
В разработанной схеме стенда, работающего по методу б (рис. 4), валы испытуемых гидромотора 20 и насоса 23 соединены управляемой муфтой 24, а напорная линия насоса 23 соединена с напорной линией мотора 20. На валу 24 установлен нагрузочный маховик 10 [5]. Назначение стенда – испытания обратимой объемной гидромашины на динамическую нагрузку сначала в режиме гидромотора, затем – насоса.
Элементы стенда: 1 – регулируемый насос; 2, 3 – всасывающая, напорная линии насоса 1; 4 – сливная линия; 5 – бак; 6 – фильтр; 7 – охладитель; 8 – рабочие линии; 9, 33 – обратные клапаны; 10 – маховик; 11 – измерительная система; 12 – датчик частоты вращения маховика; 13, 14 – датчики давления; 15, 16 – датчики расхода; 17 – модуль ввода сигналов (аналого-цифровой преобразователь); 18 – вычислительное устройство; 19, 31 – распределители; 20 – испытываемая гидромашина; 21 и 22 – обратно-предохранительные клапаны; 23 – дополнительная гидромашина; 24 – управляемая муфта; 25 – муфта; 26 – насос; 27, 28 – всасывающая и напорная линии насоса 26; 29 – предохранительный
53

Системы машин на транспорте и в транспортном строительстве
клапан; 30 – обратно-предохранительный клапан; 32 – управляющий модуль вывода команд (цифро-аналоговый преобразователь); 34 – вал нагрузочноизмерительного устройства; 35 – подшипники вала.
Работа стенда. Перед началом испытаний вал гидромашины 20 соединяют муфтой 25 с валом 34 маховика 10, вход и отвод гидромашины – с рабочими линиями 8. Через вычислительное устройство 18 и управляющий модуль вывода 32 муфта 24 замыкается и соединяет вал гидромашины 23 с валом 34 маховика; гидрораспределители 19 и 31 переводятся в главные позиции.
Испытания гидромашины 20 в режиме гидромотора. При включении на-
сосов 1 и 26, переводе распределителей 19 и 31 в рабочие позиции потоки масла из бака 5 проходят через насосы 1 и 26, обратные клапаны 9 и 33, распределители 19 и 31, поступают в контур 23–20–23. При этом валы гидромашин 20 и 23 вращаются, а в контуре 23–20–23 циркулирует энергия при условиях, описанных выше.
Возрастающий поток в контуре 23–20–23 проходит через датчики расхода 16 и давления 14, гидромашину 20, датчики давления 13 и расхода 15, а убывающий – через обратно-предохранительный клапан 21. Маховик 10, приводимый во вращение испытываемой гидромашиной 20, разгоняется.
Сигналы с датчиков частоты вращения маховика 12, давления 13 и 14, расхода 15 и 16 поступают через модуль ввода сигналов 17 на вычислительное устройство 17, где с малым шагом t регистрируются текущие значения расхода, давления в напорной и сливной линиях гидромашины и частоты вращения валов гидромашины 20 и маховика 10. По приращению угловой скорости ΔωМ за промежуток времени t вычислительное устройство 18 определяет текущие значения углового ускорения ε разгона вала гидромашины и маховика, а затем и среднее за время t значение вращающего момента ТМ на валу. Затем строят графики изменения главного диагностического параметра – полного КПД гидромашины 20 в функции времени η = f(t) и частоты вращения вала η = f(nМ), а также графики изменения дополнительного диагностического параметра – гидромеханического КПД гидромашины 20 в функции времени ηМГМ = f(t) и частоты вращения вала ηМГМ = f(nМ).
Испытания гидромашины 20 в режиме насоса. По окончании разгона ма-
ховика 10 и гидромашины 20 через вычислительное устройство 18 и управляющий модуль вывода команд 32 муфта 24 размыкается, а распределитель 19 переводится в нейтральную позицию.
Маховик 10, запасший энергию во время разгона, приводит во вращение гидромашину 20 (для испытания ее в режиме насоса), при этом масло из сливной линии 4 проходит через обратно-предохранительный клапан 30, распределитель 31, датчики расхода 16 и давления масла 14, гидромашину 20, датчики давления 13 и расхода масла 15, обратно-предохранительный клапан 22, выполняющий роль нагрузочного дросселя.
Затем строят графики изменения дополнительного диагностического параметра – полного КПД гидромашины в режиме насоса в функции времени ηН = f(t) и частоты вращения вала ηН = f(nМ) при заданной нагрузке.
54

Н.В. Мокин, Н.А. Маслов, В.С. Воробьев
По полученным графикам η = f(t), η = f(nМ), ηМГМ = f(t), ηМГМ = f(nМ), ηН = f(t) и ηН = f(nМ) судят о качестве ремонта или изготовления гидромашины.
По окончании испытаний насосы 1 и 26 отключают, а остановку маховика 10 и гидромашин 23 и 20 производят обратно-предохранительным клапаном 21 или 22.
Технико-экономические преимущества предлагаемого стенда [6]:
–снижение энергоемкости испытания (время испытания в динамическом режиме меньше времени испытания в квазистатическом режиме в 2 раза
иболее);
–дополнительное снижение энергоемкости испытания гидромашины в режиме гидромотора при замкнутой циркуляции мощности (в 3–4 раза по сравнению со стендами с разомкнутым потоком энергии в квазистатическом режиме и в 2 раза по сравнению со стендами с разомкнутым потоком энергии в динамическом режиме);
–существенное упрощение нагрузочного (приводного) устройства испытываемой гидромашины (присоединенная к валу маховая масса);
–точность определения КПД гидромашины (не грубее ±1,5…2 %) без применения дорогостоящих измерителей вращающего момента;
–уменьшение стоимости стенда (в 1,5…4 раза по сравнению с известными аналогами);
–возможность испытания объемных гидромашин в режимах гидромотора
инасоса.
Библиографический список
1.Пат. 2198325 Российская Федерация, МПК7 F 15 B 1/26. Бак гидросистемы / В.С. Лукашов, В.В. Макаров, А.В. Макаров, К.Я. Фудиман; заявитель и патентообладатель Акционерное общество «Ковровский экскаваторный завод». №2000111114/06; заявл. 05.05.2000; опубл. 10.02.2003. 12 с.: ил.
2.Пат. 4064911 США, МПК2 F 16 L 55/04. Hydraulic fluid reservoir for closed hydraulic system / David E. Albrecht; заявитель и патентообладатель David E. Albrecht. № US19760742584 19761117; заявл. 17.11.76; опубл. 27.12.77. 9 с.: ил.
3.Матвеенко А.М., Зверев И.И. Проектирование гидравлических систем летательных аппаратов. М.: Машиностроение, 1982. 296 с.
4.Пономаренко Ю.Ф. Испытание гидропередач. М., 1969. 287 с.
5.Пат. 127135 Российская Федерация, МПК7 F 04 B 51/00. Стенд для динамических испытаний насосов / Н.А. Маслов; заявитель и патентообладатель Сиб. гос. ун-т путей сообщения. № 2012142457/06; заявл. 04.10.12; опубл. 20.04.13, Бюл. № 11. 2 с.: ил.
6.Маслов Н.А. Обоснование принципиальной схемы стенда для испытаний объемных гидромашин // Главный механик. 2013. № 5. С. 43–49; № 6. С. 56–60.
55
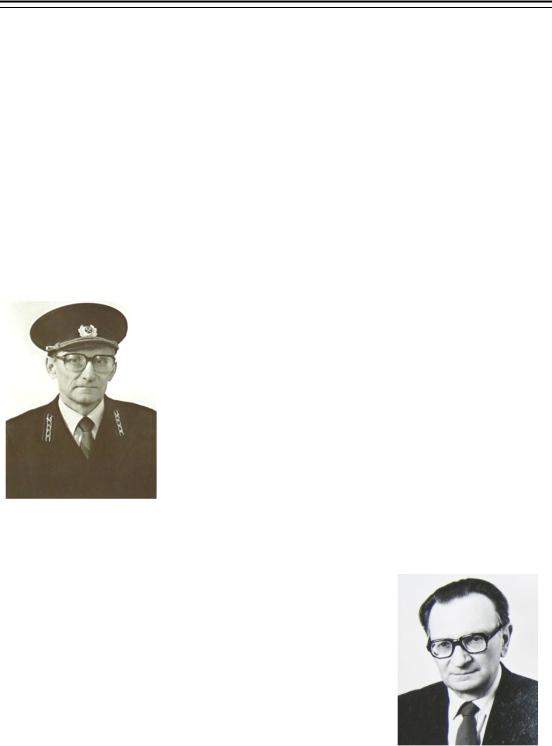
Системы машин на транспорте и в транспортном строительстве
УДК 625
Б.Н. Смоляницкий, Ю.Н. Сырямин
Фундаментальные основы комплексной механизации специальных работ в строительстве
и на железной дороге
Устойчивые связи с академической наукой были положены в основу при организации нового факультета «Строительные и путевые машины» в НИИЖТе (НИВИТе). Об этом свидетельствует тот факт, что у истоков создания факультета стояли крупные ученые-машиноведы В.М. Владимиров и А.Д. Костылев – сотрудники Института горного дела Сибирского отделения АН СССР. Первым же деканом факультета был Р.Ф. Саблин, который многие годы выполнял с ними совместные научные исследования.
Вадим Михайлович Владимиров читал курс лекций «Основы проектирования строительных машин», вел по этой дисциплине научный кружок, руководил дипломным проектированием.
Его лекции привлекали новизной излагаемого материала. Он доступно рассказывал студентам не только о машинах сегодняшнего дня, но и раскрывал перспективы их развития на основе собственных научных разработок.
А.Д. Костылев читал лекции по механике разрушения пород и буровым установкам, долгое время возглавлял ГАК факультета. Интересно отметить, что В.М. Владимиров был лауреатом Государственной
премии СССР, а А.Д. Костылев – заслуженным изобретателем РСФСР и заслуженным изобретателем СССР
(всего в Советском Союзе такое звание получили 11 человек). Высокий научный потенциал этих ученых, несомненно, привлекал к ним студентов и аспирантов.
Несколько лет ГЭК по специальности возглавлял Анатолий Яковлевич Тишков – незаурядная личность, доктор технических наук, профессор, заслуженный изобретатель Российской Федерации.
Многие годы руководил дипломным проектированием, а затем и преподавал на выпускающей кафедре д-р техн. наук П.А. Михирев, также сотрудник Института горного дела СО РАН (ИГД).
56
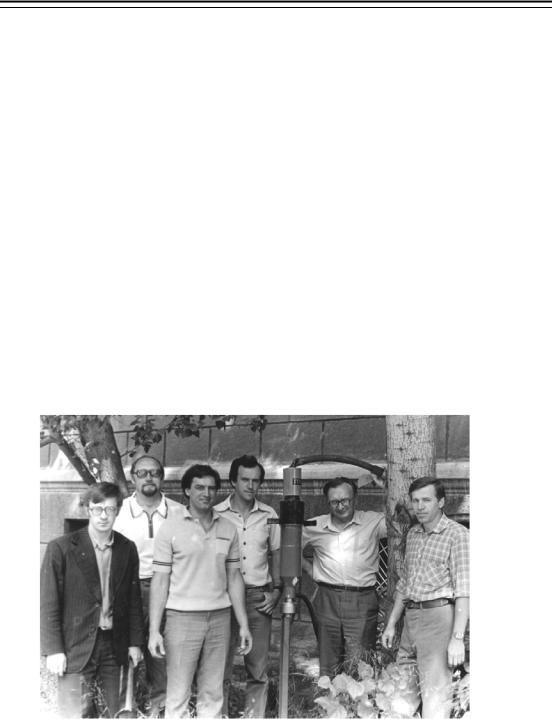
Б.Н. Смоляницкий, Ю.Н. Сырямин
Возникает вопрос, почему ведущие научные сотрудники ИГД и факультета СДМ всегда понимали необходимость сотрудничества и совместного воспитания будущих специалистов? Дело в том, что основатель Сибирского отделения Академии наук академик М.А. Лаврентьев положил в основу его создания принцип треугольника, вершины которого составляли академические институты, университет и другие вузы, а также производственные предприятия, необходимые для производства опытных образцов новых изделий и последующего их серийного производства. Такое построение позволяло выполнять не только фундаментальные научные исследования, но и совместными усилиями готовить высококвалифицированную научную смену.
Неформально действующий многие годы научно-образовательный центр ИГД СО РАН – СГУПС в 2007 г. получил официальный статус. Постановлением Президиума СО РАН от 14.06.2007 г. на основе двусторонних договоров ИГД СО РАН с ведущими университетами Новосибирска был создан Горный научно-образовательный центр. СГУПС является одним из его создателей и активных участников. Научная школа машиноведов на факультете СДМ неразрывно связана с функционированием этого центра. Сотрудники ИГД СО РАН – выпускники факультета (24 человека) ведут с кафедрой «Подъемнотранспортные, путевые, строительные и дорожные машины» (ППСДМ) совместные исследования, преподают, руководят производственной и преддипломной практикой, дипломным проектированием.
А.Д. Костылев с учениками (слева направо В.В. Червов, В.П. Богинский, Б.Б. Данилов, Б.Н. Смоляницкий, А.Д. Костылев, Ю.Н. Сырямин)
Многие преподаватели факультета прошли обучение в аспирантуре ИГД СО РАН, защитили в его ученом совете свои кандидатские и докторские диссертации. На изобретения, сделанные выпускниками факультета, получены сотни авторских свидетельств СССР, патентов Российской Федерации и зару-
57

Системы машин на транспорте и в транспортном строительстве
бежных государств. Машины, созданные на основе их исследований, экспортируются во многие ведущие страны мира.
Значимость полученных научных и практических результатов у этой школы в области машин ударного действия несомненна. Можно отметить комплекс мобильных пневмоударных машин и оборудования, позволяющих осуществить:
–лечение земляного полотна автомобильных и железных дорог без закрытия по ним движения [1];
–закрепление оснований и откосов грунтовых инженерных сооружений экономичными и экологичными способами [2];
–релаксацию напряжений различной природы возникновения на локальных участках рельсовой плети бесстыкового железнодорожного пути [3];
–прокладку или замену коммуникаций в земляном полотне дороги без предоставления технологических окон [4].
Первые два вида работ связаны с погружением в грунт стержневых элементов малой жесткости, которые при торцевом приложении нагрузки из-за потери устойчивости очень трудно внедрить в грунт. Специфика работ может быть связана со стесненными условиями на объекте, необходимостью их выполнения на откосах котлованов или насыпей, ограничениями по времени выполнения технологических операций.
Проблема становится разрешимой при воздействии на элемент в сечении, определяемом условиями устойчивости, с учетом технологической целесообразности. Важно, что при ударном воздействии энергия реализуется в весьма малом (десятки микросекунд) промежутке времени. Это позволяет при незначительных силах, прикладываемых к ударнику на протяжении относительно длительного времени разгона, получить значительные импульсные усилия на ударяемом теле.
Выдвинутая выпускниками факультета СДМ (В.П. Богинским, Б.Н. Смоляницким и Ю.Н. Сыряминым) идея агрегатирования пневмоударного устройства с зажимным механизмом для передачи стержню энергии удара оказалась плодотворной, что в итоге обеспечило решение сложной инженерной задачи.
Оригинальная динамическая система построения новых машин до сих пор не имеет аналогов в мире. При работе такая машина, имеющая сквозной осевой канал для погружаемого элемента, может осуществлять передачу ему энергии удара в любом поперечном сечении и автоматическую передвижку (перестановку машины) по мере погружения стержня в грунт. Это исключает потерю стержнем устойчивости, позволяет работать в стесненных условиях и существенно расширяет технологические возможности применения таких машин. Серийно выпущено более 2 000 машин. Они запатентованы в России, США, ФРГ и других странах. Об их достоинствах говорят поставки на экспорт
ипродажа лицензии в ФРГ.
58
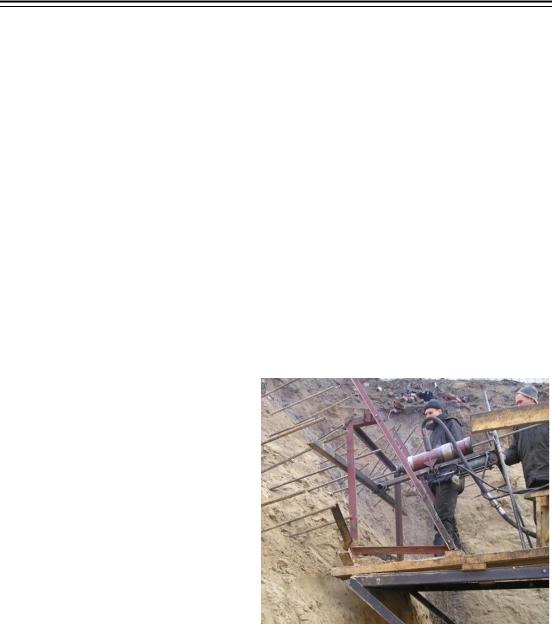
Б.Н. Смоляницкий, Ю.Н. Сырямин
Разработанные машины позволили реализовать один из наиболее эффективных и экономичных вариантов укрепления грунтовых откосов котлованов в промышленном и гражданском строительстве – стержневое (нагельное) крепление. Сущность метода заключается в армировании грунтового массива, слагающего откос, металлическими стержнями, что многократно повышает его устойчивость и создает, по сути, грунтостальную подпорную стену большой собственной массы.
Использование стержневой крепи в качестве временного крепления откосов котлованов позволяет отказаться от громоздкого и металлоемкого свайного крепления в благоприятных инженерно-геологических условиях.
В Новосибирске на нескольких объектах (при строительстве метрополитена на станциях «Речной вокзал», «Студенческая», «Проспект Маркса», укреплении откосов котлованов под здания торговых центров на ул. Восход, ул. Красный проспект) была использована технология стержневого крепления. В грунт погружались арматурные стержни-нагели (диаметры 19…28 мм).
Основным техническим средством реализации технологии нагельного крепления были пневмоударные машины ПУМ-3 и ПУМ-65 (рис. 1). С их помощью в откосы котлованов были забиты тысячи стержней. Длина закрепленного участка, например, на станции «Проспект Маркса» равнялась 600 м. Угол наклона откоса к горизонту составил 80°.
Глубина котлована достигала 21 м. От эрозии поверхность откосов была защищена бетонными плитами размером 1 1 м, связанными с нагелями. Долговременное наблюдение за поведением грунтового массива показало, что в течение шес-
тилетнего ведения строительных |
Рис. 1. Сооружение стержневого крепления |
работ не происходило вывалов, |
откоса котлована под здание торгового центра |
сползаний грунта и других нару- |
в Новосибирске машиной ПУМ-65 |
шений. |
|
По оценкам специалистов ЗАО «Новосибирскметропроект», стержневая крепь по сравнению со свайной дает экономию средств до 45 % (даже с учетом 85 % возврата металла при свайном креплении). При этом на 30–40 % сокращается время работы машин. На каждом квадратном метре закрепляемой поверхности трудозатраты сокращаются на 3,0–3,5 чел./дня, экономия металла составляет до 38,5 кг, экономия цемента – до 0,7 м3.
59
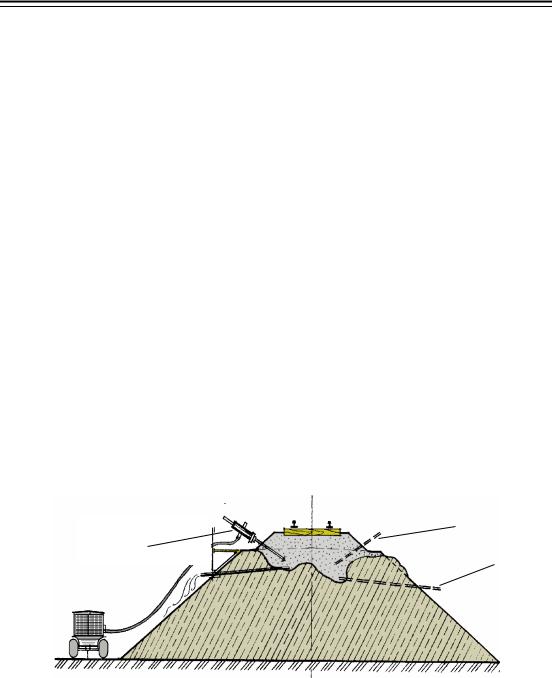
Системы машин на транспорте и в транспортном строительстве
Совершенствованием пневмоударных машин со сквозным осевым каналом продолжают заниматься выпускники факультета недавних лет Д.С. Воронцов, П.Ю. Сырямин, А.Ю. Примычкин, А.С. Смоленцев. Их разработки связаны с повышением удельной энергии удара для повышения эффективности работ и расширения области применения.
К настоящему времени накоплен большой опыт разнообразного применения пневмоударных машин в строительстве. Появление новых технологических процессов для эффективной борьбы с распространенными на дорогах Западной Сибири деформациями земляного полотна (балластные мешки, карманы и корыта и др.), во многом обязано использованию в них машин со сквозным осевым каналом. «Лечение» осуществляется нагнетанием в соответствующие зоны цементно-песчано-глинистого раствора через специальные забивные инъекторы. В этом случае нет необходимости в дорогостоящих и громоздких буровых установках, в грузоподъемных механизмах, которые сложно установить на высоких откосах насыпей и выемок. Возможно погружение в грунт инъектора целиком или отрезками любой длины. Открытый торец у погружаемого элемента позволяет совмещать при работе различные технологические операции, производя одновременно с забиванием или извлечением инъектора подачу в грунт различных материалов (технологических жидкостей, растворов, сухих смесей и т.п.) или устанавливать в образовавшуюся скважину необходимые элементы.
Схема производства работ по ликвидации балластного «мешка» напорными инъекциями показана на рис. 2.
Инъектор
Пневмоударная машина Водоотводящая
труба
Рис. 2. Схема производства работ по ликвидации балластных «мешков» напорными инъекциями с предварительным отводом воды
«Прорывной» стала разработка выпускниками нашего факультета (В.В. Червов, Б.Н. Смоляницкий, И.В. Тищенко, А.В. Червов) пневмоударных молотов «Тайфун» [4], предназначенных для забивания в грунт стальных труб и выполнения специальных работ в строительстве, связанных с погружением в грунт стальных профилей различного поперечного сечения (рис. 3).
60