
633
.pdf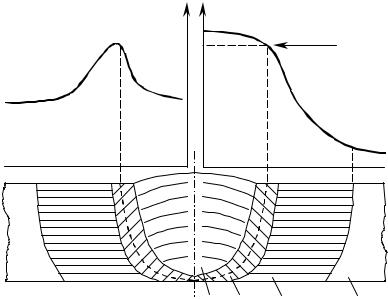
НВ |
Т °С |
а) |
1539 ° |
б) |
1 |
2 |
3 |
4 |
Рис. 2. Схема поперечного строения сварного соединения:
а— распределение твердости в сечении;
б— распределение температуры в сечении
Рассмотрим более подробно процессы, протекающие в вышеуказанных зонах, и их строение. При алюминотермитной сварке зона 1 занимает большой объем, и процессы кристаллизации определяют последующую эксплуатационную стойкость сварного соединения.
4.1. Процесс кристаллизации сварного шва
Кристаллизация металла бывает первичной и вторичной.
Под первичной кристаллизацией понимают рост кристаллов из расплава при затвердевании сварочной ванны. В результате образуется, так называемая, первичная структура. У таких металлов, как алюминий, медь, никель и их сплавов при дальнейшем охлаждении первичная структура не изменяется или меняется незначительно. Поэтому от нее зависят свойства сварного шва.
Если у металлов и сплавов, например, у сталей, в процессе охлаждения меняется тип кристаллической решетки, это значит, что при охлаждении в твердом состоянии протекает вторичная кристаллизация или рекристаллизация. В этом случае свойства вторичной структуры являются определяющими. Существует, однако, определенная связь между первичной и вторичной структурами. Кроме того, первичная структура перед кристаллизацией подвержена воздействию нагрузок, например, усадочных напряжений. Возникновение в сварных швах трещин не может быть объяснено только вторичной кристаллизацией, поэтому важно иметь представление о процессах первичной кристаллизации.
При первичной кристаллизации одновременно протекают две стадии: образование мельчайших частиц кристаллов (зародышей или центров кристаллизации) и рост кристаллов вокруг этих центров. Процесс кристаллизации схематично показан на рис. 3.
а) |
б) |
в) |
11
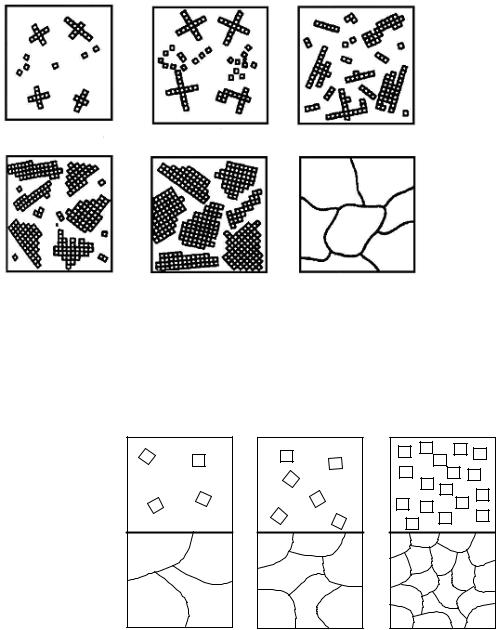
г) |
д) |
е) |
Рис. 3. Схема процесса кристаллизации
Здесь изображены этапы: зарождение из атомов металла первичных центров кристаллизации, их рост и возникновение новых зародышей (рис. 3, а, б, в, г, д), дальнейший рост кристаллов до соприкосновения их границ (рис. 3, е). В результате образуется зеренная структура металла. Величина зерен зависит от количества зародышей кристаллизации и скорости их роста. На рис. 4 схематично показано влияние скорости охлаждения на возникновение центров кристаллизации (верхний ряд) и величину зерен (нижний ряд).
а) |
б) |
в) |
Рис. 4. Влияние скорости охлаждения на процесс кристаллизации:
а— медленное охлаждение; б — ускоренное охлаждение;
в— быстрое охлаждение
При малой скорости охлаждения возникает небольшое число зародышей и в конце кристаллизации образуются крупные зерна. При большой скорости охлаждения количество зерен возрастает, и они становятся мельче.
Чем мельче зерно, тем выше прочность и особенно ударная вязкость металла. Форма и размер зерен, образующихся при кристаллизации, зависят от условий их роста, главным образом от скорости и направления отвода теплоты и температуры жидкого металла, а также от содержания примесей. В одном случае внешняя форма, не представляющая полной геометрической правильности принимает округлые формы. Такие кристаллы называются зернами.
В другом случае кристаллические образования имеют ветвистую форму с незаполненными промежутками, напоминающими дерево; их называют дендритами (от греческого слова «дерево»). Дендриты являются обычно начальной стадией образующегося кристалла. После образования зародыша, в процессе его роста концентрация примесей в прилегающей к нему жидкости увеличивается, так как зародыш растет за счет присоединения к себе атомов металла. Это затрудняет питание зародыша «строительным материалом». В таких условиях он выбрасывает во все стороны
12
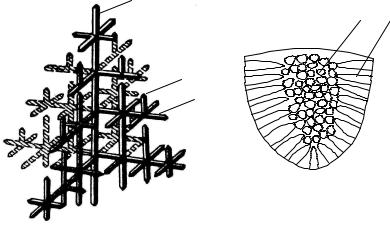
ветви (оси). Образуются оси первого порядка 1, от которых растут оси второго порядка 2, от осей второго порядка, в свою очередь, растут оси третьего порядка 3 и т.д. (рис. 5).
В последнюю очередь затвердевает металл в междендритном пространстве, и поэтому он содержит большее количество примесей, которые вытеснялись при кристаллизации дендритов в жидкую междендритную часть кристалла. Благоприятной ориентировкой роста является направление, противоположное отводу тепла (тепло отводят стенки свариваемых деталей), т.е. к центру сварного шва. Так как рост кристаллов в стороны ограничен соседними кристаллами, образуются вытянутые зерна, которые принято называть столбчатыми кристаллами (рис. 6).
1
1 2
3
2
|
Рис. 6. Схема строения сварного шва: |
|
1 — равноосные зерна; |
Рис. 5. Схема дендрита |
2 — столбчатые кристаллы |
4.2.Показатели литейных свойств материала
ивозможные дефекты в литом шве
При первичной кристаллизации металла шва в нем могут возникнуть макроскопические и микроскопические несплошности: поры, газовые пузыри, раковины, горячие трещины, неметаллические включения. Появление таких дефектов зависит от литейных свойств сварочной ванны.
Основными показателями литейных свойств материала являются: жидкотекучесть, усадка, склонность к ликвации и поглощению газов.
При алюминотермитной сварке эти показатели играют первостепенную роль, так как жидкий металл заполняет литейную форму, соприкасаясь как с торцами нагретых рельсов, так и с формовочной смесью литейной формы.
Жидкотекучесть — это способность расплава свободно течь в литейной форме, заполняя ее и точно воспроизводя ее контуры. При недостаточной жидкотекучести происходит незаполнение формы и образуются холодные спаи. Жидкотекучесть материала зависит от его химического состава и температуры в момент заливки формы. Чем выше температура заливаемого металла, тем больше его жидкотекучесть. По мере заполнения формы сплав охлаждается, его жидкотекучесть и скорость движения уменьшаются. При достижении температуры затвердевания образующиеся в сплаве кристаллы резко понижают жидкотекучесть. Полное прекращение течения металла наблюдается тогда, когда количество кристаллов в сплаве достигает 30–40 %. На жидкотекучесть влияет теплопроводность материала, из которого сделана форма. Так, сплав при заливке в сухие песчаные формы обладает большей жидкотекучестью, чем при заливке в сырые.
Усадка — свойства металлов и сплавов уменьшать свой объем при затвердевании и охлаждении; при этом происходит и соответствующее уменьшение литейных размеров отливки. Различают объемную и линейную усадку.
Объемная усадка определяется по формуле
εî |
= |
Vô −Vî òë |
100 %. |
(2) |
|
||||
|
|
Vô |
|
Линейная усадка определяется по формуле
εл |
= |
lф − lотл |
100 %, |
(3) |
|
||||
|
|
lф |
|
где Vф, Vотл, lф, lотл — объем и размеры соответственно формы и отливки.
13
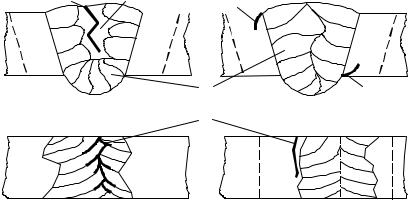
Объемная усадка в отливках является одной из причин образования усадочных раковин и пор. Величина усадки зависит от химического состава сплава и температуры его заливки.
В процессе кристаллизации металла из-за скачкообразного уменьшения его объема при переходе из жидкого состояния в твердое резко возрастают внутренние напряжения. Под действием этих напряжений металл литого шва подвергается упругопластическим деформациям. В металле шва за счет таких деформаций может произойти разрушение, по жидким прослойкам между кристаллами и в шве возникнут трещины (такие трещины называют горячими). Характерной особенностью горячих трещин является их образование на границах кристаллов, вдоль их роста. Подобные трещины могут быть поперечными (вдоль роста зерен) и продольными (по оси шва в месте стыка столбчатых кристаллов), как показано на рис. 7.
Химический состав шва оказывает первостепенное влияние на его стойкость против образования горячих трещин. Углерод резко отрицательно влияет на стойкость швов против горячих трещин. С увеличением содержания углерода увеличивается интервал температур начала и конца кристаллизации, а, следовательно, расширяется область резкого уменьшения прочности и пластичности стали. Деформация металла шва при высоких температурах в процессе его кристаллизации и последующего остывания протекает в основном из-за скольжения и поворота кристаллов относительно друг друга. Увеличение количества кристаллов в объеме металла шва за счет получения более мелкозернистой структуры приводит к активизации скольжения и, следовательно, пластичность металла шва увеличивается. Поэтому для достижения измельченной первичной структуры в сварочную ванну вводят модификаторы (например, титан, ванадий). Они способствуют изменению скорости и направления кристаллизации.
3 |
2 |
3 |
|||||||||||||
|
|
|
|
|
|
|
|
|
|
|
|
|
|||
|
|
|
|
|
|
|
|
|
|
|
|
|
|
|
|
|
|
|
|
|
|
|
|
|
|
|
|
|
|
|
|
|
|
|
|
|
|
|
|
|
|
|
|
|
|
|
|
|
|
|
|
|
|
|
|
|
|
|
|
|
|
|
|
|
|
|
|
|
|
|
|
|
|
|
|
|
|
|
|
|
|
|
|
|
|
|
|
|
|
|
|
|
|
|
|
|
|
|
|
|
|
|
|
|
|
|
|
|
|
|
|
|
|
|
|
|
|
|
|
|
|
|
|
|
|
|
|
|
|
|
|
|
|
|
|
|
|
|
|
|
|
|
|
1 |
3 |
4 |
|
Рис. 7. Горячие трещины:
1 — столбчатые кристаллы; 2 — жидкие прослойки;
3 — поперечные трещины; 4 — продольные трещины
Ликвация — это химическая неоднородность. Причиной ликвации является уменьшение растворимости примесей при его переходе из жидкого состояния в твердое. Растущие в первую очередь оси кристаллов содержат меньше примесей, а остающийся жидкий металл обогащается примесями.
В сталях, как правило, скопление вредных примесей серы S и фосфора P наблюдается в центральных зонах литого шва. Ликвация уменьшается при понижении температуры и скорости заливки и при ускорении затвердевания сплава.
Склонность к поглощению газов. В расплавленном состоянии металлы и сплавы способны активно поглощать значительное количество водорода, кислорода, азота и других газов, образующихся при плавке исходных материалов, из окружающей среды, при заливке расплава в форму и т.д. Растворимость газов с увеличением температуры повышается. При избыточном содержании газов они выделяются из расплава в виде газовых пузырей, которые могут всплыть на поверхность или остаться в отливке, образуя газовые раковины, пористость или неметаллические включения.
Для уменьшения газовых раковин и пористости целесообразно увеличивать газопроницаемость литейных форм, снижать их влажность. Наличие литейных напряжений при большой усадке, поры, газовые раковины, ликвация снижают механические свойства и герметичность литого сварного шва.
14
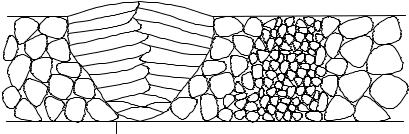
4.3. Строение металла в околошовной зоне
Если механические характеристики и эксплуатационные свойства металла шва определяются структурой шва, условиями кристаллизации, то свойства сварного соединения в целом зависят от химического состава и структуры околошовной зоны.
Зоной термического влияния (ЗТВ) называется прилегающий к шву участок основного металла, в котором произошли структурные изменения в результате нагрева до определенной температуры за счет тепла, перешедшего из металла шва. На рис. 8 показано изменение структуры металла в зоне сварки.
1500 °С |
1100 °С |
1000 °С |
900 °С |
700 °С |
500 °С |
|||||
|
|
|||||||||
|
|
|
|
|
|
|
|
|
|
|
|
|
|
|
|
|
|
|
|
|
|
|
|
|
|
|
|
|
|
|
|
|
0 |
1 |
2 |
3 |
4 |
5 |
6 |
Рис. 8. Изменение структуры металла в зоне сварки
На участке 0–1 металл имеет, как было указанно выше, столбчатую дендритную структуру изза медленного затвердевания. Участок неполного расплавления 1–2, соприкасаясь с расплавленным металлом, вследствие достаточно высокой температуры имеет крупнозернистую структуру. Участок перегрева 2–3 имеет еще довольно крупные зерна (часто игольчатой формы), уменьшающие пластичность металла. На участке 3–4 структура получается мелкозернистой с повышенными механическими свойствами по сравнению с металлом, не подвергшимся нагреву. Участок 4–5 — это участок неполной перекристаллизации. Здесь могут быть как крупные зерна, так и мелкие. Участок 5–6 содержит крупные зерна, при этом здесь наблюдается резкое падение ударной вязкости.
Чем меньше околошовная зона термического влияния, тем лучше свойства сварного шва.
При высоком содержании углерода, например, в рельсовой стали, особенно опасными являются участки 1–2 и 2–3. При ускоренном охлаждении в этих участках может происходить закалка, а, следовательно, опасность появления холодных трещин.
5. ТЕРМИЧЕСКАЯ ОБРАБОТКА СВАРНОГО СОЕДИНЕНИЯ
Термической обработкой (ТО) называют процессы теплового воздействия на материалы с целью направленного изменения их структуры и свойств. Термическая обработка может быть промежуточной операцией, улучшающей технологические свойства металла при различных его переделах (обработка давлением, резанием, сварка), и окончательной, придающей металлу или сварному соединению определенный уровень требуемых эксплуатационных характеристик (твердость, прочность, вязкость, сопротивление усталости и т.д.)
Участки сварного соединения непосредственно после сварки существенно отличаются от основного металла и друг друга по структуре, свойствам и уровню внутренних напряжений. В таких участках создаются условия для зарождения и развития трещин, которые могут приводить к разрушению соединений в процессе сварки, после нее или при эксплуатации. Поэтому для абсолютного большинства соединений углеродистых и легированных сталей (особенно соединений повышенных толщин) термическая обработка является одним из основных технологических процессов, обеспечивающих требуемый уровень качества изделий.
Виды термической обработки
Процесс ТО можно описать с помощью факторов, главные из которых — максимальная температура нагрева Тmax, время выдержки τвыд, скорость нагрева Vн и охлаждения Vохл — это, так называемые, параметры режима.
15
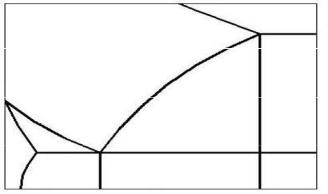
Для сварных соединений параметрами режима являются также ширина зоны нагрева и время перерыва между окончанием процесса сварки и началом ТО.
В зависимости от соотношения значений параметров различают следующие основные виды термообработки: отжиг, нормализация, закалка и отпуск.
Отжигом называется ТО, целью которой является приведение металла в устойчивое равновесное состояние. Различают отжиг I и II рода.
Отжиг I р о д а в зависимости от температуры условно можно разделить на диффузионный, рекристаллизационный и отжиг для снятия напряжений.
Параметры диффузионного отжига (Тmax = 1100 – 1200 °С, τвыд = 1,5 – 20 ч, медленное охлаждение) обеспечивают выравнивание химического состава в отдельных объемах стальных заготовок, деталях.
В процессе нагрева при сварке плавлением термообработку, сходную с диффузионным отжигом, проходят участки, близлежащие к линии сплавления. Однако время воздействия температуры выдержки τвыд при этом весьма малое и выравнивание состава не происходит. Диффузионному отжигу подвергают, как правило, сварные соединения из высоколегированных сталей.
Рекристаллизационный отжиг применяют в основном для стальных заготовок из углеродистых сталей, прошедших холодное деформирование (прокатка, штамповка, ковка) с целью снятия наклепа. Наклеп — это повышение твердости путем создания внутренних напряжений при холодной деформации. Температурный режим (Тmax 650 – 700 °С), время выдержки рассчитывают исходя из габаритов заготовки. Охлаждение после нагрева медленное.
Для сварных соединений из углеродистых сталей участок рекристаллизации в зоне термического влияния, как правило, является технически благоприятным, но при сварке высокопрочных сталей он вызывает разупрочнение.
Отжигу для снятия остаточных напряжений подвергают сварные изделия из большинства классов сталей, отливки, заготовки и детали, прошедшие обработку резанием, давлением, механическую правку. Процесс снятия напряжений основан на понижении прочности при нагреве до температуры Тmax 550 – 650 °С. При этих температурах происходит релаксация — самопроизвольное снятие напряжений.
Остаточные напряжения снимаются также и при рекристаллизационном отжиге закаленных участков сварного соединения.
Отжиг I I р о д а заключается в нагреве стали до температур, показанных на рис. 9, выше линии Ас3 или Ас1, в зависимости от содержания углерода, в выдержке и последующем медленном охлаждении.
Температура, °С
|
|
|
E |
1147 |
|
|
|
|
|
G |
|
Am |
|
|
|
|
|
|
|
Aс3 |
|
|
|
|
P |
S |
Aс1 |
|
727 |
|
|
K |
||
|
|
|
|
|
Q |
0,8 |
|
2,14 |
|
Содержание углерода, %
Рис. 9. «Стальной» участок диаграммы «железо – цементит»
В зависимости от цели отжиг II рода условно можно разделить на полный, неполный отжиг и нормализацию.
Полный отжиг заключается в нагреве до температуры Т = ТАс3 + (30 − 50) °С — для сталей с содержанием углерода до 0,8 % и Т = ТАс1 + (30 − 50) °С — для сталей с содержанием углерода более
0,8 %. После нагрева производится выдержка и последующее медленное охлаждение. В результате такого отжига вся старая структура заменяется на новую, свободную от всех внутренних напряже-
16
ний. Такая равновесная структура обеспечивает пониженную твердость и прочность и повышает пластичность и вязкость.
Чрезмерное повышение Тmax вышеуказанных линий вызывает рост зерна в стали и ухудшение свойств стали и сварного соединения.
Неполный отжиг отличается от полного тем, что сталь нагревают несколько ниже Ас3 и выше Ас1. При этом происходит частичная перекристаллизация стали. В сварных соединениях углеродистых сталей участок, подвергшийся такой обработке, обладает оптимальными свойствами.
Нормализация (Тmax 900 – 950 °С) отличается от полного отжига повышенной скоростью охлаждения (на воздухе). Этот процесс существенно измельчает крупнозернистую структуру при сварке, литье, обработке давлением, повышает сопротивление хрупкому разрушению (увеличивает вязкость). Для низкоуглеродистых сталей нормализацию применяют вместо отжига. Для средне- и высокоуглеродистых сталей нормализация сварных соединений используется вместо закалки с отпуском, что более экономично.
Закалка стали заключается в нагреве до температуры выше линии Ас3 или Ас1, выдержке при этой температуре и последующем быстром охлаждении со скоростью, обеспечивающей получение неравновесной (напряженной) структуры. В результате закалки прочность и твердость стали повышаются.
Параметры закалки:
•температура закалки такая же, как при полном отжиге;
•время выдержки зависит от степени легирования стали, размеров детали;
•скорость охлаждения должна быть высокой.
При закалке применяют разные охладители (вода, минеральное масло, расплавы солей, растворы щелочей, эмульсии). Наилучшая среда та, которая охлаждает быстро в интервале температур 500–650 °С и медленно — ниже температур 200–300 °С. На практике для охлаждения углеродистой стали используют воду, для деталей сечением меньше 5 мм и легированных сталей — масло. При несоблюдении параметров закалки возможно возникновение внутренних макронапряжений, которые могут привести к образованию трещин.
Отпуск заключается в нагреве сталей после закалки до температур ниже линии Ас1, выдержке при заданной температуре и последующем охлаждении на воздухе.
Различают три вида отпуска: низкотемпературный, среднетемпературный, высокотемпературный.
Низкотемпературный (низкий) отпуск (Тmax 150–250 °С) частично снимает внутренние напряжения. В сварных соединениях этот вид ТО часто называют «отдыхом».
Среднетемпературный (средний) отпуск (Тmax 350–500 °С) обеспечивает в несколько большей степени уменьшение внутренних напряжений после закалки. Однако у стали остаются высокие значения предела упругости и выносливости.
Высокотемпературный (высокий) отпуск проводят при Тmax 500–700 °С. Структура стали после такого отпуска обеспечивает наилучшие сочетания упругости и вязкости.
В сварном соединении (шов + зона термического влияния + основной металл) всегда присутствует тот или иной участок, прошедший под действием термического цикла одну из названных выше обработок. В связи с этим сварное соединение можно представить себе как «слоеный пирог», в котором каждый слой (участок) отличается «собственным» видом термообработки и, следовательно, свойствами. Это обстоятельство определяет трудности при назначении видов и режимов послесварочной термообработки с целью выравнивания свойств всего соединения или их улучшения.
При термообработке сварных соединений применяют главным образом высокий отпуск и нормализацию.
Высокий отпуск для сварных соединений, как правило, является самостоятельной технологической операцией, а не следующей после закалки. После высокого отпуска остаточные сварочные напряжения снижаются на 70–80 %, улучшаются структура и свойства определенных зон металла сварного соединения. Уменьшается и выравнивается по сечению твердость, увеличивается ударная вязкость.
Нормализация сварного шва включает нагрев до более высоких температур и охлаждение на воздухе. После нормализации получается более мелкое зерно металла шва и околошовной зоны, что повышает эксплуатационную стойкость сварного шва. При этом внутренние напряжения снимаются до 90 %.
17
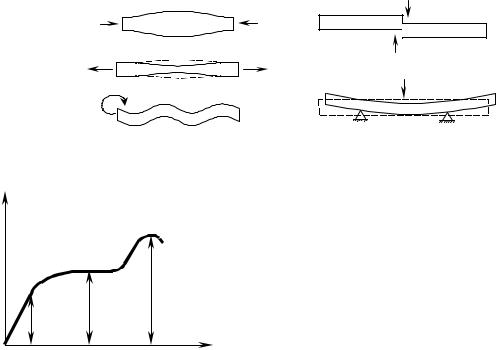
Иногда для сварных соединений применяют термообработку, состоящую из закалки и высокого отпуска (улучшение).
При этом по сравнению с нормализацией повышаются значения прочности, пластичности, ударной вязкости, уменьшается чувствительность к концентраторам напряжений. Обычно такой обработке подвергают сварные соединения из низко- и среднелегированных сталей.
При термической обработке сварные соединения в монтажных условиях и при ремонте нагревают электрическими нагревателями (печами) сопротивления, индукционным или газопламенным способом. При выборе способа нагрева следует учитывать конкретные местные условия работы, достоинства и недостатки каждого способа, наличие оборудования и энергетических ресурсов.
В заключение следует отметить, что термическая обработка сварных соединений влияет на:
•изменение фазового состояния, макро- и микроструктуры отдельных участков и всего сварного соединения;
•повышение прочности и вязкости материала, из которого выполнено сварное соединение;
•снижение уровня остаточных напряжений.
6.ИСПЫТАНИЯ МАТЕРИАЛОВ
ИСВАРНЫХ СОЕДИНЕНИЙ
|
6.1. Разрушающие методы испытаний |
||
К разрушающим методам испытаний относятся: |
|||
• механические испытания; |
|
||
• макроанализ. |
|
|
|
|
|
Механические испытания |
|
При механических испытаниях материал подвергают различным нагрузкам. Нагрузка вызывает |
|||
в материале напряжение и деформацию. |
|||
Напряжение — величина нагрузки, отнесенная к единице площади сечения испытываемого |
|||
образца. |
|
|
|
Деформация — изменение формы и размеров материала под влиянием приложенных внешних |
|||
сил. |
|
|
|
Различают деформации растяжения (сжатия), изгиба, кручения, среза (рис. 10). |
|||
а) |
г) |
|
|
б) |
|
|
|
в) |
д) |
|
|
|
|
||
|
|
Рис. 10. Виды деформации: |
|
|
а — сжатие; б — растяжение; в — кручение; г — срез; д — изгиб |
||
|
|
В результате механических испытаний определяют ме- |
|
Р |
|
ханические свойства материалов. |
|
В |
К механическим свойст-вам относятся: прочность, упру- |
||
|
|||
|
гость, пластичность, ударная вязкость, твердость и вынос- |
||
|
|
||
Б |
|
ливость. |
|
|
Для определения проч-ности материалы в виде образцов |
||
А |
|
||
|
круглой или плоской формы испытывают обычно на рас- |
||
РТ |
РВ |
||
тяжение. |
|||
|
|
||
РУ |
|
Испытания производят на разрывных машинах. В ре- |
|
|
|
зультате испытаний получают диаграмму растяжения |
|
|
ε |
(рис. 11). |
|
Рис. 11. Диаграмма растяжения: |
На оси абсцисс диаграммы откладываются значения |
||
деформации, а на оси ординат нагрузки, приложенные к |
|||
Р — нагрузка; ε — деформация |
|||
образцу. |
|||
|
|
||
18 |
|
|
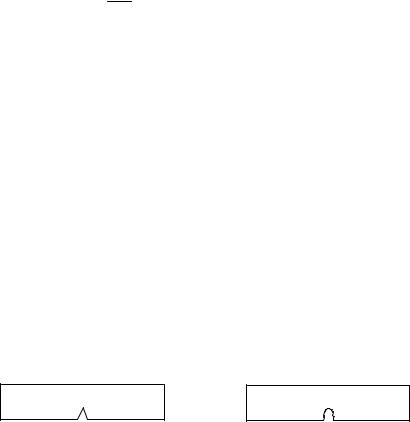
Прочность — способность материала сопротивляться разрушению под действием нагрузок. Оценивается прочность пределом прочности и пределом текучести.
Предел прочности σв, МПа, (временное сопротивление) — это напряжение, соответствующее наибольшей нагрузке, предшествующей разрушению образца:
σ |
|
= |
Рmax |
, |
(4) |
в |
|
||||
|
|
F0 |
|
||
|
|
|
|
где Pmax — наибольшая нагрузка (точка В на рис. 11), F0 — начальная площадь поперечного сечения рабочей части образца.
Предел текучести σт, МПа, — наименьшее напряжение, при котором образец деформируется без заметного увеличения нагрузки
σ |
|
= |
Рт |
, |
(5) |
|
т |
F |
|||||
|
|
|
|
|||
|
|
|
|
|
||
|
|
0 |
|
|
где Pт — нагрузка, при которой наблюдается площадка текучести (точка Б на рис. 11).
Площадку текучести имеют только пластичные материалы. Для непластичных материалов определяют условный предел текучести, при котором остаточное удлинение достигает 0,2 % от расчетной длины образца.
Р
σ0,2 = 0,2 , (6)
F0
где P0,2 — условная нагрузка предела текучести.
Пластичность — способность материала изменять форму и размеры под действием внешних сил, при этом не разрушаясь. Оценивается относительным удлинением и относительным сужением.
Относительное удлинение δ — отношение приращения lк – l0 расчетной длины образца после разрыва lк к его первоначальной длине l0, выраженное в процентах:
δ = |
lк − l0 |
100 % . |
(7) |
|
l0
Относительное сужение ψ — отношение разности начальной F0 и минимальной площади поперечного сечения образца после разрыва Fк к начальной площади, выраженное в процентах:
ψ = |
F0 − Fк |
100 % . |
(8) |
|
F0
Чем пластичнее материал, тем бо´льшее значение относительного удлинения и сужения. Ударная вязкость — это способность материала сопротивляться динамическим нагрузкам.
Испытание на удар проводят на приборе, который называется маятниковый копер. Стандартный образец с надрезом посередине устанавливают на опоры маятникового копра и наносят удар свободно падающим маятником копра. Образцы делают с надрезом в виде буквы V (рис. 12, а) или с надрезом в виде буквы U (рис. 12, б).
а) |
б) |
Рис. 12. Образцы для испытания на ударную вязкость
Определяется ударная вязкость как отношение работы маятника А, затраченной на ударный излом (изгиб) образца, к площади его поперечного сечения S0 в месте надреза, Дж/м2:
KC = |
A |
. |
(9) |
|
S0
В зависимости от типа образца ударную вязкость обозначают KCU, KCV.
Твердостью — называется способность металла сопротивляться проникновению в него другого, более твердого тела.
Твердость чаще всего измеряют способами: Бринелля, Роквелла, Виккерса.
Определение твердости по Бринеллю (рис. 13).
19
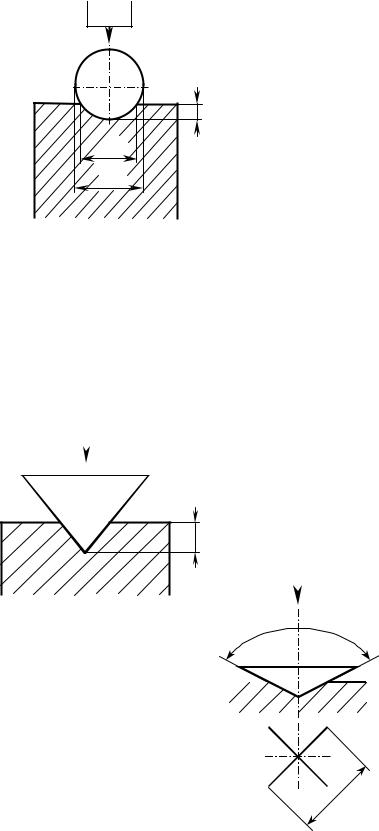
При определении твердости по Бринеллю в плоскую поверхность материала вдавливают под |
|
||
постоянной нагрузкой Р стальной шарик диаметром 2,5; 5; 10 мм. |
|
||
Р |
Для определения твердости измеряют диаметр отпе- |
|
|
чатка с помощью лупы Бринелля и по специальной |
|
||
|
|
||
|
таблице находят число твердости, соответствующее |
|
|
|
диаметру отпечатка. |
|
|
|
Метод Бринелля не следует применять для материа- |
|
|
|
лов твер-достью более НВ450, так как стальной шарик |
|
|
h |
может деформироваться и результаты будут искажены. |
|
|
|
Между числом твер-дости по Бринеллю и пределом |
|
|
d |
прочности при растяжении существует зависимость: |
|
|
Сталь НВ1250 – 1750 — σв = 0,343НВ; |
(10) |
||
|
|||
D |
Сталь (НВ более 1750) — σв = 0,362НВ. |
(11) |
|
|
|||
|
Определение твердости по Роквеллу (рис. 14). |
|
|
|
При испытаниях твердости по Роквеллу в испыты- |
|
|
Рис. 13. Схема получения отпечатка по Бринеллю: |
ваемый материал вдавливается алмазный конус с углом |
|
|
D — диаметр шарика; Р — нагрузка; |
при вершине 120° или стальной шарик диаметром 1,58 |
|
|
d — диаметр отпечатка; |
мм. Алмазный конус применяют для испытания твер- |
|
|
h — глубина вдавливания |
|
||
дых материалов, а шарик для мягких. Твердость по Ро- |
|
||
|
|
||
квеллу измеряется в условных единицах. Значение твердости отсчитывают по циферблату индика- |
|
||
тора, установленному на приборе. На циферблате имеется три шкалы: А, В, С. |
|
||
При испытании материалов с высокой твердостью применяют алмазный конус, вдавливаемый |
|
||
под нагрузкой 1500 Н. Твердость в этом случае отсчитывается по шкале С и обозначается HRC. |
|
||
Если измерение проводится стальным шариком под нагрузкой 1000 Н, твердость отсчитывается |
|
||
по шкале В и обозначается HRB. |
|
|
|
Р |
Испытание очень твер-дых тел проводят алмазным кону- |
|
сом при нагрузке 600 Н. Твердость отсчитывается по шкале А |
|
|
|
|
|
|
и обозначается HRA. |
|
|
Числа твердости по Роквеллу можно приблизительно пере- |
|
|
считать в числа твердости по Бринеллю: |
h |
Рис. 14. Схема получения отпечатка по Роквеллу: h — глубина отпечатка
вершине 136°.
Полученный отпечаток имепомощью микроскопа, встроотпечатка и по специальным ние твердости.
Этот метод обычно испольдости в тонких поверхностных твердость.
Твердость в данном случае
Макроанализ
|
HB = 10HRC. |
(12) |
|
|
|
|
|
||||||
Измерение твердости по Виккерсу (рис. 15). |
|
|
|||||||||||
|
|
|
|
|
|
|
|
Твердость |
определяют |
||||
|
|
|
|
|
|
|
|
вдав-ливанием в испытывае- |
|||||
|
|
|
|
|
|
|
|
мый материал с полированной |
|||||
|
|
|
|
α |
|
или |
шлифованной |
поверхно- |
|||||
|
|
|
|
|
стью |
четырехгранной |
алмаз- |
||||||
|
|
|
|
|
|
|
|
||||||
|
|
|
|
|
|
|
|
ной пирамиды с углом при |
|||||
|
|
|
|
|
|
|
|
ет форму ромба. Измеряют с |
|||||
|
|
|
|
|
|
|
|
||||||
|
|
|
|
|
|
|
|
енного |
в |
прибор, |
диагональ |
||
|
|
|
|
|
|
|
|
таблицам |
определяют |
значе- |
|||
|
|
|
|
|
|
|
|
зуется при определении твер- |
|||||
|
|
|
|
|
|
|
|
||||||
|
|
|
|
|
|
|
|
слоях, |
имеющих |
высокую |
|||
|
|
|
|
|
|
d |
|
|
|
|
|
|
|
|
|
|
|
|
|
|
|
обозначают HV. |
|
|
|||
|
|
|
|
|
|
|
|
|
|
Макроанализ заключается в |
|
определении строения металла |
|||
путем |
просмотра его излома |
Рис. 15. Схема получения отпечатка |
или поверхности |
(специально |
|
по Виккерсу: d – диагональ отпечатка; |
|||||
подготовленной для этой цели) |
невооруженным |
глазом или |
|||
через лупу при небольших уве- |
α — угол между противоположными |
личениях — до 30 раз. Это по- |
|||
гранями пирамиды при вершине |
|||||
зволяет |
наблюдать одновре- |
менно большую поверхность и |
|||
|
получить представление об общем строении металла и о наличии в нем определенных пороков.
20