
633
.pdf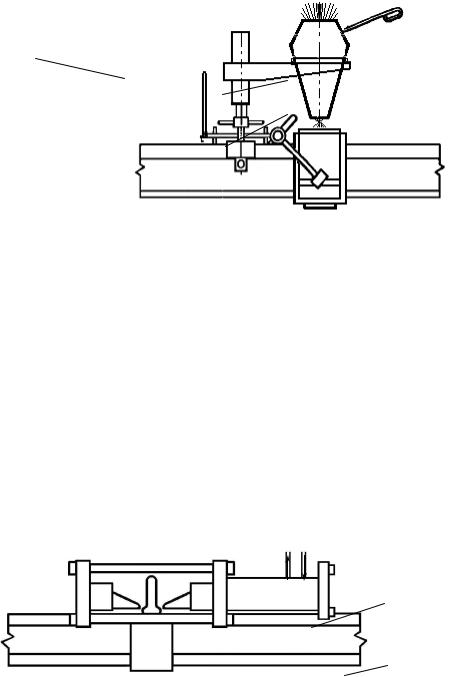
Рис. 39. Подогрев концов рельсов: 1 — газовая горелка; 2 — литейная форма;
3 — держатель литейной формы; 4 — комбинированная стойка
Технология плавильного процесса рельсов следующая:
•газовая горелка снимается с комбинированной стойки;
•нагретый литниковый мостик устанавливается в литейную форму;
•тигель с литейным компонентом поворачивается и устанавливается таким образом, чтобы ось литника совпадала с осью зазора (рис. 40);
•от пламени горелки зажигается термитная спичка, вставляется в литейный компонент, находящийся в тигле, и тигель накрывается конической крышкой с отверстием для выпуска газов;
•горелка устанавливается на вспомогательную стойку.
При проведении работ необходимо визуально и по времени контролировать процесс плавления литейного компонента и выпуск расплавленного металла в литейную форму, который происходит через 20–28 с автоматически. Контролируется также время кристаллизации металла литейного шва, которое в зависимости от массы порции литейного компонента для рельсов Р65 длится 3,0– 3,5 мин.
3 |
|
2 |
|
||
|
1 |
|
|
4 |
Рис. 40. Плавка литейного компонента и промежуточное литье: 1 — тигель; 2 — крышка тигля;
3 — комбинированная стойка; 4 — литейная форма
11.3.Формирование профиля рельса
взоне сварного шва после окончания кристаллизации
После окончания плавильного процесса проводится демонтаж литейного оборудования. Для этого необходимо снять ковш со шлаком, запустить двигатель гидроагрегата и подключить обрезное приспособление.
Тигель переносится на вспомогательную стойку, а комбинированная стойка и держатели литейных полуформ снимаются.
Для демонтажа верхней части литейной формы предварительно производится очистка зубилом бокового и верхнего контуров головки рельсов от формовочной смеси и шлака. После этого верхняя часть литейной формы отделяется с помощью кузнечных клещей, а головка рельса очищается от песка металлической щеткой.
При формировании профиля головки рельса в зоне литейного шва предварительно необходимо удалить прибыльную часть литейного шва. Для этой операции используется специальное гидравлическое обрезное приспособление. Схема процесса показана на рис. 41, техническая характеристика станка приведена в табл. 9.
1
2
41
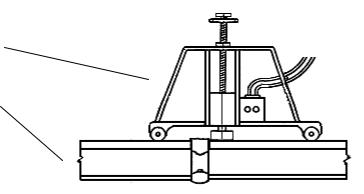
Рис. 41. Приспособление гидравлическое для удаления прибыльной части литейного шва:
1 — обрезной станок; 2 — рельс
Излишки шлака, обрезки металла убираются, с помощью молотка и зубила или гидравлических ножниц срезаются остатки литниковой системы, и в горячем состоянии подрубаются литники.
После завершения этих операций на поверхности головки рельса устанавливается специальный гидравлический шлифовальный станок и выполняется предварительное шлифование прибыльной части литейного шва до высоты приблизительно 1 мм над верхом головки рельса (рис. 42). Технические показатели гидравлического шлифовального станка приведены в табл. 9.
После формирования требуемого профиля головки рельса литейный шов выдерживается до полного остывания, пока температуры металла шва и рельса на расстоянии 2 м от шва не будут одинаковыми. Ориентировочное время остывания составляет 90–120 мин и колеблется в зависимости от температуры окружающего воздуха.
1
2
Рис. 42. Шлифовальный станок для шлифования головки рельса: 1 — шлифовальный станок; 2 — рельс
Таблица 9
Специальное оборудование для алюминотермитной сварки
Наименование |
Обозна- |
Габариты, |
Назначение |
Техническая |
|
|
чение |
Д×Ш×В, мм |
|
характеристика |
|
|
|
|
|
|
|
Станок |
|
|
Обрезка при- |
Усилие резания, кН |
|
обрезной |
СОГ-1 |
880×335×340 |
быльной части |
190 |
|
гидравличе- |
Масса, кг |
||||
|
|
литейного шва |
|||
ский |
|
|
|
75 |
|
Станок |
|
|
Шлифование |
Частота вращения |
|
|
|
рабочего вала, об/мин |
|||
шлифоваль- |
СШГ-1 |
1066×500×985 |
сварных швов |
3000 |
|
ный гидрав- |
|
|
рельсов |
Масса, кг |
|
лический |
|
|
|
||
|
|
|
43 |
||
|
|
|
|
||
|
|
|
Привод для |
Мощность двигате- |
|
Агрегат |
|
|
ля, кВт |
||
|
ТУ 4145-003- |
обрезного |
|||
гидравличе- |
АГ-1 |
4,5 |
|||
53904871–2005 |
и шлифоваль- |
||||
ский |
|
Масса, кг |
|||
|
|
|
ного станков |
75 |
|
|
|
|
|
42
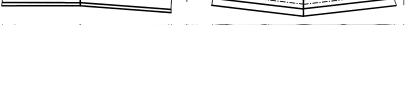
Окончательное шлифование выполняется на полностью остывшем рельсе. Перед проведением окончательного шлифования отбиваются литники, а литейный шов металлической щеткой тщательно очищается от остатков литейной формы и песка. После шлифования поверхность головки рельса не должна иметь дефектов типа «поджог». Завершив шлифование, необходимо прикрепить рельс к шпалам в зоне литейного шва.
После завершения сварочных работ ремонтируемый участок рельса приводится в работоспособное состояние — устанавливаются предохранительные накладки на рельс в зоне литейного стыка.
Сварочное оборудование демонтируется, на месте производства сварочных работ собирается инструмент, включая клинья для выправки рельсов, убираются остатки литейных материалов.
Технологическая карта с перечнем операций для проведения сварочных работ на стрелочном переводе, как наиболее сложной конструкции пути, приведена в прил. Б.
12. КОНТРОЛЬ КАЧЕСТВА АЛЮМИНОТЕРМИТНОЙ СВАРКИ РЕЛЬСОВ НА МЕСТЕ ПРОИЗВОДСТВА РАБОТ
Качество обработки литейного шва сварного стыка после завершения процесса промежуточного литья контролируют визуально и с помощью ультразвука.
12.1. Визуально-измерительный контроль
Визуально-измерительный контроль стыков АТСР выполняют после обрезки прибыльной части сварного шва, удаления литниковой системы и шлифовки сварного шва в области головки.
Визуальный контроль сварного стыка проводят с применением лупы, зеркала (для контроля со стороны подошвы), переносной лампы для освещения стыка.
Качество поверхности считается удовлетворительным, если на поверхности катания и боковых поверхностях головки рельсов отсутствуют остатки литниковой системы и обрезки металла сварного шва.
Сварной шов должен иметь чистую, без заусенцев поверхность, не содержать видимых раковин, шлаковых включений, непроваров и трещин. Поверхность после шлифовки не должна иметь дефектов типа «поджога».
Прямолинейность поверхности катания и боковых граней головки рельсов в зоне алюминотермитной сварки контролируется с помощью металлической линейки, которая имеет длину 1 м с ценой деления 1 мм, штангенциркулем или щупом в соответствии с требованиями ТУ 2-034-225–87. Схема контроля прямолинейности рельсов в зоне соединения показана на рис. 43.
а) |
б) |
Рис. 43. Схема контроля прямолинейности рельсов:
а — в вертикальной плоскости; б — в горизонтальной плоскости
Местные неровности на длине 1 м после шлифовки не должны быть более ± 0,2 мм.
12.2. Ультразвуковой контроль
Ультразвуковой контроль сварных стыков осуществляют до установки на них накладок при температуре металла в области сварного стыка не более 60 °С и при температуре окружающей среды воздуха не ниже +5 °С [14].
Дефекты в стали рельса и стыка в виде газовых пузырей, трещин и шлаковых включений имеют шероховатые границы и могут быть обнаружены эхометодом ультразвукового контроля (УЗК).
Отсутствие диффузии металла термита в металл рельса приводит к образованию вертикальных трещин с гладкими границами. Эти дефекты могут быть обнаружены зеркальным методом УЗК.
Перед началом сварки концы рельсов необходимо тщательно осмотреть, болтовые отверстия проверить дефектоскопом, используя эхометод УЗК с применением пьезоэлектрического преобразователя.
Для выявления внутренних дефектов металла термитного шва эхометодом выполняется следующий основной контроль:
43
•прямым искателем с двумя пьезоэлементами по раздельной схеме контроля на поверхности катания для выявления дефектов в виде горизонтальных трещин в шейке и ее продолжении в головку и подошву;
•наклонным под углом 70° искателем на поверхности перьев подошвы, а также в головке рельса с поверхности катания и ее боковых поверхностей для выявления дефектов в виде шероховатых поперечных трещин;
•наклонным под углом 45° искателем в головке, шейке и в подошве под проекцией шейки с поверхности катания для выявления дефектов в виде шероховатых поперечных дефектов.
Для выявления дефектов в соединении металла шва и металле основного рельса зеркальным методом контроль выполняется двумя искателями (тандемом): один из них излучает зондирующие импульсы, а второй принимает эхосигналы. Этим методом контроль выполняется:
•двумя под углом 45° искателями на поверхности катания для выявления дефектов зеркального вида в сварном шве шейки и ее продолжении в головку и подошву;
•двумя под углом 70° искателями с боков головки рельса для выявления дефектов зеркального вида в сварном шве головки.
Контроль сварных стыков, сваренных термитом, должны выполнять два оператора ультразвукового контроля, один из которых должен иметь квалификацию не ниже второго уровня.
Cтыки, в которых во время ультразвукового контроля обнаружены дефекты, должны быть исследованы всеми способами контроля и установлены основные характеристики дефектов:
•координаты дефекта: глубина и расстояние от точки выхода преобразователя до места расположения дефекта;
•условные величины дефекта: длина, ширина и высота;
•минимальная чувствительность, при которой дефект фиксируется всеми индикаторами дефектоскопа [четкий импульс на экране ЭЛТ (монитора) и срабатывание индикатора звука].
При установлении внутренних дефектов в сварном стыке, обнаруженных во время ультразвукового контроля, решение о замене рельса с дефектoм или дальнейшей эксплуатации его в пути принимает начальник цеха дефектоскопии вместе с оператором, который обнаружил этот дефект.
При ультразвуковом контроле для признания рельса годным к эксплуатации протяженность дефекта не должна превышать более 4 мм в любом направлении.
Ультразвуковой контроль качества литейного шва на отсутствие внутренних дефектов выполняется в течение 10 дней после проведения сварочных работ.
Оформление рабочих результатов
Результаты каждого выполненного контроля сварного стыка записываются в «Рабочий журнал дефектоскопа».
На каждую новую группу сварных стыков, если у них одинаковые характеристики, в присутствии старшего сварщика заполняется акт установленной формы (прил. В), в который записываются основные данные по выполнению сварки и контроля.
Если в сварном стыке обнаружен дефект (трещина), то во всех случаях заполняются установленной формы «Сообщение о дефектном рельсе» и «Корешок сообщения о дефектнoм рельсе». Первое вручается дорожному мастеру или бригадиру, и данная информация сообщается оперативному дежурному структурного подразделения, который делает запись в «Журнале учета работы средств дефектоскопии». В «Корешке сообщения о дефектнoм рельсе» подписывается мастер/бригадир, и во время отчета корешок передается мастеру цеха дефектоскопии, который проверяет, правильно ли и своевременно ли был заменен рельс.
В зависимости от величины дефекта и установленной скорости движения поездов на участке дефектное место, где обнаружен дефект и планируется использовать термитный стык, можно укрепить накладками утвержденной конструкции и дальше эксплуатировать его в установленном порядке (прил. Г).
Все повторные проверки записываются в «Рабочий журнал дефектоскопа», и сведения о выполненной работе передаются оперативному дежурному дистанции структурного подразделения, который делает запись в «Журнале учета работы средств дефектоскопии».
12.3.Возможные дефекты литого сварного шва
испособы их устранения
Нарушение технологии алюминотермитной сварки стыков рельсов является недопустимым, так как может привести к образованию дефектов сварки.
44
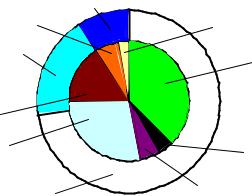
Все дефекты, которые могут возникнуть в результате АТС, приведены в табл. 10 с описанием особенностей, причин возникновения и мер их предотвращения.
Наличие в рельсах дефектов сварки может вызвать их преждевременный выход из-за развития, прежде всего, усталостных трещин в подошве и шейке головки. Согласно работе [1] 73 % дефектов рельсов, сваренных алюминотермитной сваркой, относятся к поперечным трещинам, зарождающимся в подошве рельса. Неоднородности металла шва, вызывающие поперечные трещины в подошве, обусловлены преимущественно непроваром (неполным проплавлением металла сварного шва и свариваемых рельсов) и осевым сжатием, произошедшим вследствие относительного смещения рельсов в стыке при затвердевании металла. В числе других причин возникновения поперечных трещин — пористость и концентрация напряжений. На рис. 44 показано количественное соотношение видов и причин повреждений швов, выполненных алюминотермитной сваркой.
Горизонтальные трещины |
|
|
8 % |
|
|
Газовые пузыри |
Вздутия |
|
Поперечные трещины в |
|
|
шейке |
Непровар |
|
19 % |
||
|
||
Трещины |
|
|
в припое |
|
|
Осевая усадка |
Концентрация |
|
напряжений |
||
|
||
Поперечные трещины |
Пористость |
вподошве 73 %
Рис. 44. Виды и причины дефектов в швах, выполненных АТС
Дефекты обработки после сварки также вызывают повреждение сварных рельсов в пути. При эксплуатации усталостные трещины в головке и шейке сваренных рельсов могут появиться от забоин, задиров при шлифовании крупнозернистыми камнями, несоблюдении режимов нормализации и т.д.
Качество поверхности сварного шва после АТС считается удовлетворительным, если на поверхности катания и боковых поверхностях головки рельсов отсутствуют остатки литниковой системы и обрезки металла сварного шва.
Таблица 10
|
|
|
|
Возможные дефекты литейного шва |
||||||
|
|
|
|
|
|
и способы их устранения |
||||
|
|
|
|
|
|
|
|
|
|
|
|
Наименование |
|
|
|
|
|
|
|
|
|
№ |
дефекта, внешнее |
|
|
|
|
|
|
|
|
|
проявление и |
Вероятная причина |
Способ устранения |
|
|||||||
п/п |
|
|||||||||
дополнительные |
|
|
|
|
|
|
|
|
|
|
|
|
|
|
|
|
|
|
|
|
|
|
признаки |
|
|
|
|
|
|
|
|
|
|
|
|
|
|
|
|
|
|
|
|
1 |
2 |
|
|
3 |
|
|
|
4 |
|
|
|
|
|
|
|
|
|
|
|
||
1 |
Газовые раковины, |
Бурная |
реакция |
в |
тигле, |
Проверить |
грануляцию ли- |
|
||
|
пузыри, поры в ли- |
выброс |
расплавленного ме- |
тейного компонента в соот- |
|
|||||
|
тейном шве |
талла через |
край |
обечайки |
ветствии |
с |
требованиями |
|
||
|
|
тигля из-за нарушения ре- |
ТУ 0783-001-59033294–2004, |
|
||||||
|
|
цептуры литейного |
компо- |
качество упаковки и соблю- |
|
|||||
|
|
нента |
или разгерметизации |
дение условий хранения |
|
|||||
|
|
упаковки порции с попада- |
|
|
|
|
||||
|
|
нием влаги |
|
|
|
|
|
|
|
|
|
|
Присутствие влаги в ли- |
Просушить литейную форму |
|
||||||
|
|
тейной форме |
|
|
|
|
|
|
|
|
|
|
Уменьшенная |
газопроница- |
Уменьшить плотность набив- |
|
|||||
|
|
емость |
формовочной |
смеси, |
ки литейной формы, прове- |
|
||||
|
|
нарушена рецептура смеси |
рить качество |
формовочной |
|
|||||
|
|
|
|
|
|
|
смеси |
|
|
|
|
|
Уменьшен размер |
межсты- |
Установить межстыковой за- |
|
|||||
|
|
кового зазора |
|
|
|
зор 25 (± 1) мм |
|
|
||
|
|
|
|
|
||||||
2 |
Перегрев металла, оп- |
Завышено время нагрева |
Уменьшить время нагрева |
|
||||||
|
лавление подошвы |
Неправильно установлена го- |
Выровнять |
температурное |
|
|||||
|
|
релка |
|
|
|
|
поле с помощью механизма |
|
||
|
|
|
|
|
|
|
настройки горелки |
|
45
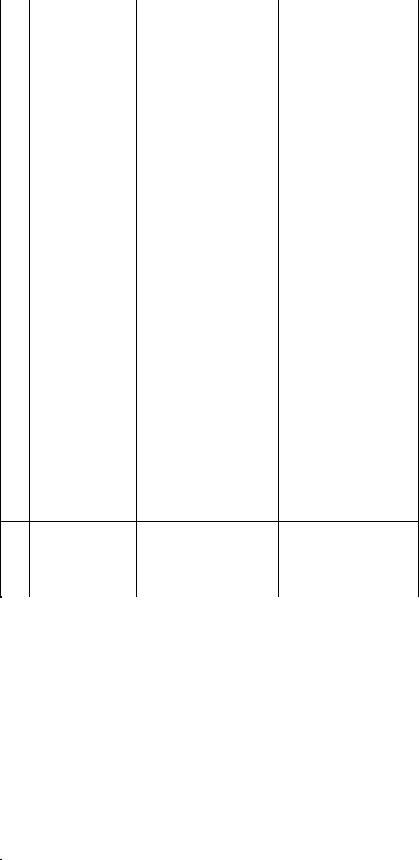
|
|
|
Уменьшен |
размер межсты- |
Установить межстыковой за- |
|
||||||
|
|
|
кового зазора |
|
зор 25 (± 1) мм |
|
|
|
||||
3 |
Непровар. Литейный |
Недостаточный предваритель- |
Проверить |
работу горелки, |
|
|||||||
|
металл не сварился с |
ный подогрев |
|
при |
необходимости |
увели- |
|
|||||
|
рельсом |
|
|
|
|
чить |
время |
предваритель- |
|
|||
|
|
|
|
|
|
ного нагрева |
|
|
|
|||
|
|
|
|
|
|
|
|
|
|
|
|
Продолжение табл. 10 |
|
|
|
|
|
|
|
|
|
|
|
|
|
1 |
2 |
|
|
|
3 |
|
|
|
4 |
|
|
|
|
|
|
|
|
|
|||||||
|
Места непровара име- |
Засоренность нижних проду- |
Тщательно |
контролировать |
||||||||
|
ют темную |
поверх- |
вочных каналов в литейной |
чистоту продувочных кана- |
||||||||
|
ность, наличие на по- |
форме |
|
|
лов перед установкой литей- |
|||||||
|
дошве рельса шаро- |
|
|
|
ной формы |
|
|
|
|
|||
|
образных включений |
Оседание шлака на сва- |
Проверить |
качество |
литни- |
|||||||
|
от 0,5 до 3,5 мм |
риваемые поверхности из-за |
кового зазора, при необхо- |
|||||||||
|
|
|
раннего выпуска металла из |
димости |
заменить |
другим; |
||||||
|
|
|
тигля; замедленный выпуск |
откалибровать |
диаметр лит- |
|||||||
|
|
|
металла из тигля |
ника |
|
|
|
|
|
|
||
|
|
|
Плавка в холодном, предва- |
Прокалить |
тигель |
перед |
||||||
|
|
|
рительно |
не |
прокаленном |
засыпкой |
литейного |
компо- |
||||
|
|
|
тигле |
|
|
нента |
|
|
|
|
|
|
|
|
|
Загрязнение свариваемых по- |
Тщательно |
прочистить сва- |
|||||||
|
|
|
верхностей |
|
|
риваемые поверхности перед |
||||||
|
|
|
|
|
|
сваркой |
|
|
|
|
|
|
|
|
|
Недостаточный подогрев кон- |
Обеспечить |
температурный |
|||||||
|
|
|
цов свариваемых рельсов |
режим нагрева концов рель- |
||||||||
|
|
|
|
|
|
сов перед сваркой |
|
|
||||
4 Горячие трещины в ли- |
Быстрое охлаждение из-за не- |
Выполнить |
нагрев |
концов |
||||||||
|
том металле, усадоч- |
достаточного |
подогрева |
рельсов до температуры 800– |
||||||||
|
ная раковина в го- |
концов рельсов |
900 °С. Цвет нагретого рель- |
|||||||||
|
ловке шва |
|
|
|
|
са должен быть светло-крас- |
||||||
|
|
|
|
|
|
ный |
|
|
|
|
|
|
5 |
Шлаковые включения. Попадание несгоревшего ли- |
Перемешать |
литейный ком- |
|||||||||
|
Шлак не успел отде- |
тейного компонента в литей- |
понент с целью равномер- |
|||||||||
|
литься от металла и |
ную форму |
|
|
ного распределения фракций |
|||||||
|
выплыть на |
поверх- |
|
|
|
в объеме литейной порции |
||||||
|
ность |
|
Наличие в литейном компо- |
Нормализовать фракционный |
||||||||
|
|
|
||||||||||
|
|
|
ненте крупных фракций |
состав литейного компонента |
||||||||
|
|
|
|
|
|
в соответствии с требованиями |
||||||
|
|
|
|
|
|
ТУ 0783-001-59033294–2004 |
||||||
|
|
|
Применение увлажненного тер- |
Проверить |
качество |
хране- |
||||||
|
|
|
мита |
|
|
ния литейного компонента и |
||||||
|
|
|
|
|
|
исключить попадание влаги |
||||||
|
|
|
Быстрая кристаллизация ме- |
Установить нормируемый за- |
||||||||
|
|
|
талла в нижнем сечении рель- |
зор 25 (± 1) мм |
|
|
|
|||||
|
|
|
са вследствие уменьшенного |
|
|
|
|
|
|
|
||
|
|
|
зазора |
|
|
|
|
|
|
|
|
|
|
|
|
Пониженная |
огнеупорность |
Применить |
|
формовочные |
|||||
|
|
|
формовочных материалов |
материалы с большей огне- |
||||||||
|
|
|
|
|
|
упорностью |
|
|
|
|
6Недостача металла в Неполновесная порция литейПрименить порцию литейно-
|
литейном шве |
ного компонента |
|
го компонента, предназначен- |
||
|
|
|
|
ную для свариваемой катего- |
||
|
|
|
|
рии рельсов; проверить герме- |
||
|
|
|
|
тичность упаковки порции ли- |
||
|
|
|
|
тейного компонента |
||
|
|
|
|
|
|
Окончание табл. 10 |
|
|
|
|
|
|
|
|
|
|
|
|
|
|
1 |
2 |
3 |
|
|
4 |
|
|
|
|
|
|
||
|
|
Увеличен межстыковой зазор |
Установить нормируемый за- |
|
||
|
|
|
|
зор 25 (± 1) мм |
|
|
|
|
Увеличен объем |
облива за |
Более тщательно устанавли- |
|
|
|
|
счет образования |
неплотно- |
вать литейные полуформы и |
|
|
|
|
стей в местах стыка литей- |
выполнять |
их уплотнение |
|
|
|
|
ных полуформ |
|
формовочной смесью |
|
|
|
|
Частичный выброс или утеч- |
Более тщательно выполнять |
|
||
|
|
ка металла через неплотно- |
обмазку и заделывать неплот- |
|
||
|
|
сти обмазки |
|
ности в процессе литья фор- |
|
|
|
|
|
|
мовочной смеси |
|
|
|
|
Порча литейного компонента |
Обеспечить хранение литей- |
|
||
|
|
из-за плохого хранения, в |
ного компонента при темпе- |
|
||
|
|
результате чего нарушается |
ратуре + 10 °С и относитель- |
|
||
|
|
равновесие между окалиной |
ной влажности не выше 50 % |
|
||
|
|
и алюминием |
|
|
|
|
|
|
|
|
|
|
|
7 |
Повышенная хруп- |
Повышенное содержание алю- |
Привести |
содержание алю- |
|
|
|
кость металла литей- |
миния в литейном компо- |
миния в соответствие с ре- |
|
46
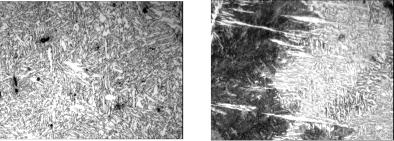
|
ного шва |
ненте |
|
|
|
цептурой |
|
|
Неравномерное |
распределе- |
Обеспечить тщательное пе- |
||
|
|
ние алюминия в объеме ли- |
ремешивание фракций |
|||
|
|
тейного компонента |
|
|
||
|
|
Перегрев |
металла |
газовой |
Изменить режим предвари- |
|
|
|
горелкой |
при предваритель- |
тельного нагрева |
||
|
|
ном нагреве |
|
|
|
|
8 |
Дефекты облива – сме- |
Литейные |
полуформы при |
Тщательно устанавливать ли- |
||
|
щение половин обли- |
установке смещены |
относи- |
тейные полуформы |
||
|
ва как одной относи- |
тельно оси межстыкового за- |
|
|||
|
тельно другой, так и |
зора |
|
|
|
|
|
всего облива относи- |
|
|
|
|
|
|
тельно центра меж- |
|
|
|
|
|
|
стыкового зазора |
|
|
|
|
|
|
|
|
|
|
|
|
9 |
Прочие дефекты: |
|
|
|
|
|
|
углы в сварном сты- |
Неправильно выставлены сва- |
Тщательно формировать сты- |
|||
|
ке, смещение головок |
риваемые концы рельсов |
ковой зазор перед сваркой |
|||
|
рельсов по поверхно- |
Неисправность |
шлифоваль- |
Исправить шлифовальный ста- |
||
|
сти катания, смеще- |
ного станка |
|
|
нок, заменить шлифовальный |
|
|
ние по рабочим гра- |
|
|
|
|
круг |
|
ням; |
|
|
|
|
|
|
зарубы и ненормаль- |
|
|
|
|
|
|
ности шлифовки |
|
|
|
|
|
12.4. Строение литого шва при алюминотермитной сварке
Термитный стык представляет собой вертикальный слой легированной стали толщиной 24–26 мм, за ним идет диффузионная зона толщиной 3–5 мм и затем уже рельсовая сталь.
В результате проведенных исследований [7] установлено, что наиболее существенное влияние на структуру металла шва и околошовной зоны при АТС оказывают такие технологические параметры, как тепловая мощность газового пламени при подогреве, продолжительность предварительного подогрева, продолжительность технологической паузы между подогревом и заливкой.
Структура термитного металла в головке и шейке рельса представляет собой литую крупнокристаллическую структуру игольчатого малоуглеродистого сорбита с ферритом по междендритным прослойкам (рис. 45, а).
На линии сплавления за счет повышенной скорости охлаждения перьев подошвы образуются закалочные структуры (мартенсит и бейнит). В остальных сечениях рельса этих структур незначительные количества. В зоне термического влияния структура состоит из сорбита (рис. 45, б).
а) |
|
б) |
|
|
|
Рис. 45. Микроструктура литого сварного шва (×500): а — термитный металл; б — зона сплавления
Таким образом, микроструктура рельсов, сваренных АТС, близка к микроструктуре термоупрочненных рельсов.
Однако, если увеличить мощность газового пламени и снизить продолжительность этапа подогрева, на периферийных участках подошвы рельса могут образовываться в большом количестве закалочные структуры (мартенсит). Это приведет, в свою очередь, к разрушению при эксплуатации сваренного стыка.
47
13. ПРАВИЛА БЕЗОПАСНОСТИ ПРИ ПРОВЕДЕНИИ АЛЮМИНОТЕРМИТНОЙ СВАРКИ РЕЛЬСОВ
13.1. Безопасность при подготовке и выполнении алюминотермитной сварки рельсов
При выполнении алюминотермитной сварки рельсов методом промежуточного литья должны строго выполняться правила техники безопасности, пожарной безопасности и охраны труда [3, 13].
К выполнению алюминотермитной сварки рельсов могут быть допущены работники, прошедшие специальный курс обучения, получившие свидетельство сварщика-литейщика и прошедшие проверку знаний на право производства работ. К выполнению сварочных работ допускаются лица не моложе 18 лет.
Работники, допущенные к производству алюминотермитной сварки рельсов, перед проведением работ должны пройти медицинский осмотр и получить разрешение врача.
При алюминотермитной сварке рельсов они должны использовать личные защитные средства:
•спецодежду сварщика-литейщика;
•огнестойкие перчатки;
•защитную маску;
•сварочные очки;
•сапоги или ботинки;
•теплую спецодежду для работы в холодное время;
•сигнальные жилеты для выполнения работ в пути.
При работе с технологическим оборудованием: гидравлическим агрегатом, шлифовальным, обрезным, рельсорезным станками, горелкой газовой — необходимо строго соблюдать инструкции по эксплуатации на это оборудование и меры безопасности, указанные в этих инструкциях.
В процессе подготовки и выполнения алюминотермитной сварки рельсов запрещается:
• засыпать порцию литейного компонента во влажный (непросушенный) тигель и поджигать
ее;
•поджигать литейный компонент, не установив тигель над литейной формой;
•применять автоматический выпуск расплавленного литейного компонента во влажную литейную форму;
•после предварительного нагрева концов рельсов в литейной форме и воспламенения литейного компонента ставить влажный (непросушенный) мостик;
•носить термические спички в кармане рабочей одежды;
•хранить термические спички совместно с литейным компонентом в одном складе;
•устанавливать ковш с горячим шлаком на влажную землю и переносить ковш с горячим шлаком наклоненным;
•порции литейного компонента хранить совместно с другими легковоспламеняющимися веществами;
•сильно нагретый или жидкий шлак, снятый с литейного шва, бросать в воду, снег или на влажные места;
•в случае пожара на складе, где хранится литейный компонент, применять воду и жидкостные огнетушители.
Перед воспламенением литейного компонента сварщик-ли-тейщик должен предупредить остальных работников о возгорании и иметь место для быстрого отхода от тигля, в котором происходит активная химическая реакция, на расстояние не менее трех метров.
Литейный компонент должен складироваться на рабочем месте на расстоянии не менее шести метров от места сварки. Категорически воспрещается хранение литейного компонента совместно с легковоспламеняющимися и горючими жидкостями, горючими газами, окисляющими и кислородосодержащими веществами.
Место проведения алюминотермитной сварки перед началом работ должно быть обеспечено средствами пожаротушения: порошковым огнетушителем, лопатой, песком.
При работе с литейным компонентом необходимо строго соблюдать правила пожарной безопасности, принимая во внимание, что:
•температура при горении литейного компонента достигает 2300–2800 °С;
•линейная скорость горения составляет 5 мм/с;
48
•горение литейного компонента сопровождается выбросом горячих частиц, способных зажечь легковоспламеняющиеся вещества;
•при разрушении уплотнительной обмазки или литейной формы возможно вытекание расплавленного металла вне зоны сварки;
•при увлажнении литейного компонента в процессе реакции возможна резкая интенсификация горения за счет взаимодействия алюминия и воды с выделением водорода.
Запрещается тушить литейный компонент огнетушащими порошками общего назначения, водой и водопенными смесями. Для локализации горения литейного компонента должен быть применен огнетушащий порошок ПХК по ТУ 10968236-06–94.
При проведении работ по алюминотермитной сварке рабочее место должно быть очищено от горючих веществ в радиусе 5 м.
Газовые баллоны и подводящие шланги, а также конструкции и механизмы, находящиеся в зоне алюминотермитной сварки, должны быть защищены металлическим экраном или сеткой с ячейкой размером не более 1×1 мм.
13.2. Правила хранения и транспортировки расходных материалов, оборудования и инструмента
Хранение расходных материалов
Литейные компоненты, термитные спички должны храниться в самостоятельных 1-й или 2-й степени огнестойкости бесчердачных одноэтажных зданиях с полами из негорючих материалов. В исключительных ситуациях допускается хранение в отдельном отсеке общего склада 1-й или 2-й степени огнестойкости.
Литейные компоненты, ввиду высокой температуры горения, необходимо складировать на расстоянии не менее 0,5 м от несущих конструкций склада и не менее трех метров от горючих материалов и веществ. Расстояние от светильников до хранящихся упаковок с литейным компонентом должно быть не менее 0,5 м.
Напротив дверных проемов складских помещений должны оставаться свободные проходы шириной, равной ширине дверей, но не менее 1 м. Через каждые 6 м в складах следует устраивать, как правило, продольные проходы шириной не менее 0,8 м.
Электрооборудование складов по окончании рабочего дня должно обесточиваться. Аппараты, предназначенные для отключения электроснабжения склада, должны располагаться вне складского помещения на стене из негорючих материалов или на отдельно стоящей опоре, помещаться в шкаф или нишу с приспособлением для опломбирования и должны быть закрыты на замок. Эксплуатация газовых плит, электронагревательных приборов и установка штепсельных розеток в помещении склада не допускается.
В зависимости от площади склада и количества хранящегося литейного компонента в каждом конкретном случае определяется необходимое количество огнетушителей согласно ППБ-01–93.
Ящики с песком или глиноземом, используемые в целях пожарной безопасности, должны комплектоваться совковой лопатой, а их конструкция обеспечивать удобство извлечения тушащих средств и исключать попадание осадков.
Вспомогательные материалы: термитные спички, литейные формы и мостики, магнезитный порошок, формовочная смесь, — должны храниться в помещении при температуре воздуха не ниже +10 °С и относительной влажности не выше 50 %. Допускается в весенне-летний период увеличение относительной влажности воздуха в помещении до 65 %.
Для контроля температуры и влажности воздуха в помещении должны быть установлены термометр и прибор для измерения влажности (психрометр или гигрометр).
Хранение оборудования и инструмента
Хранение оборудования и инструмента, включая оснастку, должно осуществляться в соответствии со средними условиями «С» по ГОСТ 15150–69.
Количество ярусов хранящихся в упаковке оборудования и инструмента не должно быть более трех.
В месте хранения расходных материалов обязательно ведите журнал ежедневного контроля температуры и влажности воздуха в помещении.
49
Транспортирование расходных материалов
Транспортирование литейных компонентов, термитных спичек, литейных форм, формовочной смеси, магнезитного порошка должно осуществляться согласно Правилам перевозки грузов по железным дорогам, а также автомобильным транспортом РФ.
Тара (упаковка) должна быть прочной, исправной, герметичной, исключающей попадание влаги, рассыпание литейного компонента, обеспечивающей сохранность и безопасность перевозки.
Материалы, из которых изготовлены тара и упаковка, должны быть инертными по отношению к содержимому, например, полимерная пленка.
Литейные компоненты при транспортировании в железнодорожных крытых вагонах в мешках до 10 кг должны быть дополнительно упакованы в жесткую транспортную тару (контейнеры, металлические или фанерные барабаны). При использовании автомобильного транспорта кузова и прицепы должны быть защищены от попадания влаги.
Транспортные средства, подаваемые под погрузку, должны быть сухими и очищенными от посторонних веществ.
Транспортирование оборудования и инструмента
Оборудование и инструмент (включая оснастку) транспортируются только в упакованном виде всеми транспортными средствами в соответствии с действующими правилами перевозок грузов на данный вид транспорта:
Условия транспортирования по ГОСТ 15108–80 жесткие «Ж». Высота штабеля не должна превышать двух ярусов.
Погрузка и разгрузка упакованного оборудования и инструмента может быть выполнена с помощью подъемных кранов или автопогрузчика.
ЗАКЛЮЧЕНИЕ
Центры алюминотермитной сварки железнодорожных рельсов, применяющие технологию, материалы и оборудование компании «СНАГА», работают по всей сети железных дорог России.
Технология, материалы и оборудование для алюминотермитной сварки, разработанные и поставляемые фирмой «СНАГА», позволяют выполнять высококачественную cварку железнодорожных рельсов любых типов и категорий, в том числе S49, UIC60.
В настоящее время «СНАГА» преобразована в группу специализированных компаний, каждая из которых эффективно работает в своем направлении деятельности, обеспечивая совместное решение всего комплекса поставленных задач и качественное выполнение технологического процесса алюминотермитной сварки рельсов.
Ведется постоянная работа над усовершенствованием конструкций оборудования и оснастки. Все технические решения по алюминотермитной сварке, предложенные компанией «СНАГА», защищены патентами Российской Федерации № 2088390, 2119854, 2124424, 2163184, действую-
щими на всей территории России.
Разработанные компанией «СНАГА» инструменты защищены свидетельствами Российской Федерации на полезные модели № 16653, 16661, 16662, 16669.
Материалы и оборудование выпускаются по техническим условиям, зарегистрированным в Госстандарте России.
50