
633
.pdf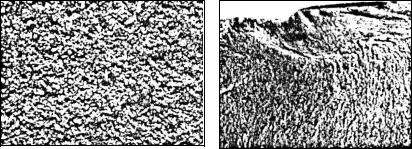
Макроскопический анализ не определяет тонкостей строения и часто является предварительным, но не окончательным видом исследования. Характеризуя многие особенности строения, макроанализ позволяет выбрать те участки, которые требуют дальнейшего микроскопического исследования.
При макроанализе изломов оценивают:
•вид и характер разрушения металлов по признакам, характеризующим качество металла;
•макронесплошности, имеющиеся в металле (шлаковые включения, поры, расслоения и др.) Изломы классифицируют по следующим признакам:
По макрогеометрии:
•однородный;
•неоднородный.
Однородный излом — излом, характеризующийся единой поверхностью разрушения (без геометрических зон, различающихся по рельефу).
Неоднородный излом — излом, характеризующийся наличием зон, отличающихся по макрорельефу.
Неоднородность в изломе может быть вызвана химической неоднородностью, а именно присутствием столбчатых кристаллов (дендритов).
Дендритный излом наблюдается обычно в отдельных зонах в поверхностных слоях. Причиной может стать перегрев металла и низкая скорость кристаллизации.
По цвету:
•светлый;
•серебристый;
•серый;
•светло-серый;
•темно-серый;
•черный.
По блеску излома:
•блестящий;
•матовый.
По степени деформации:
•хрупкий;
•вязкий;
•усталостный.
Хрупкий излом (рис. 16, а) представляет собой однородную поверхность с кристаллическим строением без заметных признаков макропластической деформации.
Поверхность разрушения, как правило, светло-серого цвета, с металлическим блеском. Утяжки (искажение формы) на боковых сторонах изломов либо отсутствуют, либо имеют очень
малую величину, что свидетельствует о незначительной пластической деформации.
б)
а)
Рис. 16. Поверхность изломов: а — хрупкий излом; б — вязкий излом
Вязкий излом (рис. 16, б) имеет волокнистое строение с явными признаками пластической деформации. Поверхность разрушения матовая (без металлического блеска), темно-серого цвета.
Усталостный излом. Усталость — это снижение прочности материала, произошедшее в результате действия циклических напряжений. Сопротивление усталости называется выносливостью.
21
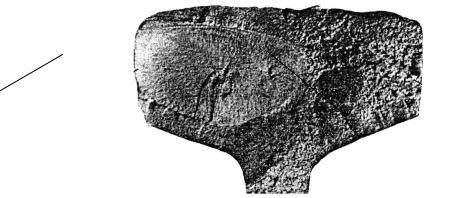
Разрушение от усталости происходит всегда внезапно вследствие накопления металлом необратимых изменений, которые приводят к возникновению микроскопических трещин – трещин усталости.
Трещины усталости возникают обычно в поверхностных зонах детали. Большое влияние на образование трещин усталости оказывает состояние поверхности. Наличие на поверхности рисок, царапин, выбоин и других дефектов, вызывающих концентрацию напряжений, способствует образованию трещин усталости.
Излом детали, разрушенной от усталости (рис. 17), состоит из зоны усталостного разрушения а и зоны долома б. В зоне усталостного разрушения вследствие трения соприкасающихся поверхностей, ограничивающих развивающуюся трещину усталости, возникает гладкая притертая поверхность. В зоне а часто наблюдаются концентрические бороздки. Это следы постепенного распространения трещины усталости. Зона долома имеет шероховатую поверхность, характерную для обычного разрушения (вязкого или хрупкого).
а
б
Рис. 17. Усталостный излом: а — зона усталости; б — зона долома
При нарушении режимов сварки в изломах можно увидеть несплошности:
•усадочная раковина — полость, не заполненная металлом и расположенная обычно в верхней части сварного шва;
•усадочная рыхлость — скопление несплошностей неправильной формы, проявляющихся в виде отдельных участков с пористым ноздреватым строением;
•поры — проявляются в виде скопления отдельных мелких несплошностей.
6.2. Неразрушающие методы испытаний
Метод неразрушающего контроля — метод, при котором не должна быть нарушена пригодность объекта к применению.
Неразрушающие методы контроля применяются для выявления в материале дефектов (явных и скрытых), которые в зависимости от этапа возникновения дефектов можно подразделить на:
•производственные дефекты, возникающие в результате нарушений технологии, например, при литье, обработке давлением, сварке, механической обработке;
•дефекты, возникающие при эксплуатации как результат изнашивания, усталости, неправильного обслуживания и т.д.
К наиболее распространенным неразрушающим методам контроля относятся:
1. Внешний осмотр, включая проверку геометрических размеров. Внешнему осмотру подвергаются 100 % сварных швов. Эту операцию выполняют невооруженным глазом или с помощью лупы 10-кратного увеличения. При этом выявляются непровары, наплывы, трещины, наличие пор, коробление и т.д.
2. Методы, позволяющие обнаружить дефекты в подповерхностных слоях и внутри объекта исследования (магнитный, радиационный, ультразвуковой и др.).
Магнитный метод
Магнитный метод контроля основан на явлении возникновения полей рассеяния в местах дефектов намагниченной детали.
Магнитные силовые линии при прохождении дефекта изменяют свое направление. На его краях возникают магнитные полосы, и создается магнитное поле рассеяния. Напряженность магнитного
22
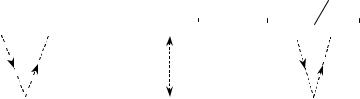
поля рассеяния зависит от размера дефекта. Задача при магнитном контроле сводится к обнаружению магнитных полей рассеяния.
Основными методами магнитного контроля являются: магнитопорошковый, феррозондовый и магнитографический.
Магнитопорошковый метод применяется для выявления подповерхностных дефектов на глубине 1,5–2 мм в деталях практически любых форм и размеров. Магнитное поле рассеяния выявляется с помощью ферромагнитного порошка, который наносится на поверхность.
Феррозондовый метод основан на обнаружении и измерении магнитных полей с помощью магнитодинамических магнитометров — феррозондов. С помощью этого метода можно определить дефекты на глубине 10–15 мм.
Феррозонды представляют собой два пермаллоевых сердечника с первичными (возбуждения) и вторичными (измерительными) обмотками. При взаимодействии двух полей внешнего измерительного поля возбуждения в измерительной обмотке появляется ЭДС, по значению которой судят о напряженности внешнего магнитного поля.
Магнитографический метод выявляет как подповерхностные, так и глубинные (до 20–25 мм) дефекты. В качестве индикатора дефектов используют магнитную ленту. Ее накладывают на контрольную деталь и производят запись дефектов при намагничивании постоянным полем. После этого воспроизводят записи с помощью магнитографического дефектоскопа.
Радиационный метод
При этом методе осуществляют контроль изделий с помощью проникающих излучений: рентгеновских и гамма-лучей. Принцип метода заключается в направлении на исследуемый объект проникающего излучения. Позади объекта помещается устройство для регистрации интенсивности излучения. В местах дефектов интенсивность будет различной в зависимости от их плотности по сравнению с общим фоном.
Ультразвуковой метод
Ультразвуковой метод основан на способности ультразвуковых волн отражаться от границы раздела двух сред с разными акустическими свойствами. Для ультразвукового контроля применяют колебания частотой до 10 МГц. В качестве излучателей и приемников используют пластины из пьезоэлектрической керамики или кварца. Пьезоэлектрический эффект заключается в том, что пьезоэлектрическая пластина под действием подведенного к ней электрического потенциала начинает колебаться, а при механических колебаниях на ее противоположных поверхностях возникает переменный электрический ток.
Аппаратура для ультразвукового контроля состоит из пьезопреобразователя (ПЭП) для излучения и приема ультразвуковых колебаний, электронного блока и вспомогательных устройств. Преобразователи могут работать по совмещенной схеме, когда один и тот же пьезоэлемент является и излучателем, и приемником, по раздельной схеме и по раздельно-совмещенной схеме (рис. 18).
а) |
|
|
|
|
|
|
|
б) |
в) |
|
|
|
Экран |
|||||||||||||||||
|
|
|
|
|
|
|
|
|
|
|
|
|
|
|
||||||||||||||||
|
|
|
И |
|
|
|
П |
|
|
|
И П |
|
|
|
|
И |
|
|
П |
|||||||||||
|
|
|
|
|
|
|
|
|
|
|
|
|
|
|
|
|
|
|
|
|
|
|
|
|
|
|
|
|
|
|
|
|
|
|
|
|
|
|
|
|
|
|
|
|
|
|
|
|
|
|
|
|
|
|
|
|
|
|
|
|
|
|
|
|
|
|
|
|
|
|
|
|
|
|
|
|
|
|
|
|
|
|
|
|
|
|
|
|
|
|
|
|
Рис. 18. Преобразователи, работающие в различных режимах:
а— раздельная схема; б — совмещенная схема;
в— раздельно-совмещенная схема; И — излучатель; П — приемник
Акустический контакт между излучателем и изделием достигается нанесением на поверхность изделия слоя минерального масла, глицерина, воды и т.д. Электронный блок предназначен для генерирования пульсирующих импульсов высокочастотного излучения, для усиления и преобразования сигналов, отраженных от дефекта, и их отображения на экране электронно-лучевой трубки. Искатели могут быть с прямыми или призматическими головками с различными углами падения УЗК (рис. 19).
При контроле сварных соединений часто используют эхо-метод и зеркальный метод.
При эхометоде преобразователь генерирует короткий импульс, который отражается от дефектов, поверхности изделия или других неоднородностей, а затем принимается искателем.
23
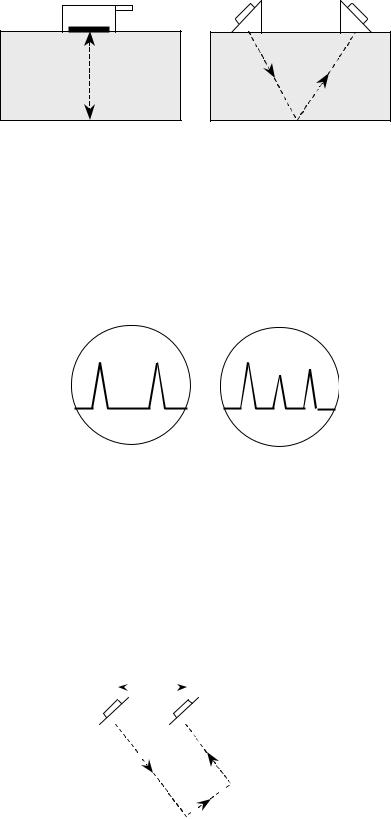
П |
И |
П |
а) |
б) |
|
Рис. 19. Способы ввода акустических колебаний: а — прямой; б — наклонный
Так, при прозвучивании рельса продольными импульсами, которые вводят со стороны поверхности катания головки, можно обнаружить дефекты, расположенные в плоскости симметрии или вблизи ее. Если на пути пучка УЗК дефектов нет, то осциллограмма на экране имеет вид, показанный на рис. 20, а. А любые нарушения сплошности металла на пути пучка продольных волн вызовут появление на экране прибора промежуточного импульса 3 (рис. 20, б), расположенного между начальным 1 и донным 2 (отраженным от противоположной поверхности) сигналами. При этом донный импульс уменьшается по высоте и при значительных размерах дефекта может даже совсем исчезнуть.
а) |
б) |
1 |
2 |
1 |
3 |
2 |
Рис. 20. Осциллограммы при контроле сварного шва рельса эхометодом
Для более эффективного обнаружения вертикально ориентированных поперечных трещин (например, контактно-усталост-ных трещин в головке рельса) целесообразно использовать зеркальный метод. Он реализуется при прозвучивании изделия двумя ПЭП, которые размещаются на поверхности сканирования таким образом, чтобы фиксировать одним ПЭП сигнал, излучаемый другим ПЭП. Сигнал, переотражаясь от противоположной поверхности изделия и плоскости дефекта, поступает на приемную пьезопластину (рис. 21). В простейшем случае в дополнение к первому ПЭП, работающему в обычном режиме излучения-приема, на определенном расстоянии В от него устанавливают второй ПЭП, который может работать только в режиме приема зеркально отраженных от плоскости дефекта сигналов. В общем случае каждый из ПЭП может работать в режи-
ме излучения и в режиме приема. |
|
|
|
|
|
|
|||||||||
Ультразвуковой |
кон- |
|
|
|
|
В |
|
|
троль |
имеет |
определенные |
||||
преимущества перед, на- |
|
|
|
|
|
|
пример, |
радиационным |
мето- |
||||||
|
|
|
|
|
|
|
|
|
|
||||||
дом, — высокая чувст- |
|
|
|
|
|
|
|
|
|
|
вительность; |
высокая |
прони- |
||
|
|
|
|
1 ПЭП |
|
|
|
2 ПЭП |
|||||||
|
|
|
|
|
|
||||||||||
кающая спо-собность (в |
|
|
|
|
|
|
|
|
|
|
стали до 2,5 м); возможность |
||||
контроля при односто- |
|
|
|
|
|
|
|
|
|
|
роннем доступе к шву; высокая |
||||
производительность; |
мо- |
|
|
|
|
|
|
|
|
|
|
бильность ап-паратуры. |
|
||
7. ЖЕЛЕЗНОДОРОЖНЫЕ |
|
|
|
|
|
|
|
|
|
|
|
РЕЛЬСЫ |
|
||
|
|
|
|
|
|
|
|
|
|
|
|
||||
7.1. Химический состав, |
|
|
|
|
|
|
|
|
|
|
механические свойства рель- |
||||
|
|
|
|
|
|
|
|
|
|
||||||
сов |
|
|
|
|
|
|
|
|
|
|
|
|
|
|
|
Все железнодорожные |
Рис. 21. Схема зеркального контроля |
рельсы, используемые на желез- |
|||||||||||||
|
|
|
|
|
|
|
|
|
|
ных дорогах России, изготавливаются в соответствии с ГОСТ Р 51685–2000 «Рельсы железнодорожные. Общие технические условия».
Железнодорожные рельсы, изготовленные в соответствии с этим стандартом, подразделяют: по типам:
• Р50;
24
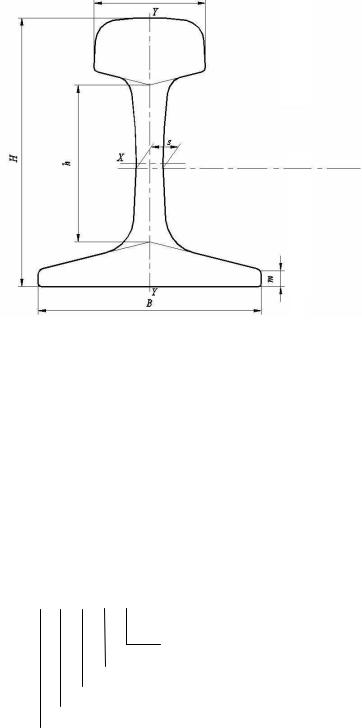
•Р65;
•Р65К (для наружных нитей кривых участков пути);
•Р75;
по категориям качества:
•В — рельсы термоупрочненные высшего качества;
•Т1, Т2 — рельсы термоупрочненные;
•Н — рельсы нетермоупрочненные;
по способу выплавки:
•М — из мартеновской стали;
•К — из конверторной стали;
•Э — из электростали;
по виду исходных заготовок:
•из слитков;
•из непрерывно-литых заготовок (НЛЗ).
Форма и основные размеры поперечного сечения рельсов соответствуют приведенным на рис. 22 и в табл. 2.
b
Линия центров радиусов
Рис. 22. Параметры поперечного сечения рельса
|
|
|
|
|
Таблица 2 |
|
Размеры поперечного сечения рельсов |
|
|
||
|
|
|
|
|
|
Наименование размера |
|
|
Значение размера для типа рельса, мм |
|
|
|
|
|
|
|
|
поперечного сечения |
|
Р50 |
Р65 |
Р65К |
Р75 |
|
|
||||
|
|
|
|
|
|
Высота рельса Н |
|
152 |
180 |
181 |
192 |
|
|
|
|
|
|
Высота шейки h |
|
83 |
105 |
105 |
104,4 |
|
|
|
|
|
|
Ширина головки b |
|
72 |
75 |
75 |
75 |
|
|
|
|
|
|
Ширина подошвы B |
|
132 |
150 |
150 |
150 |
|
|
|
|
|
|
Толщина шейки s |
|
16 |
18 |
18 |
20 |
Высота пера m |
|
10,5 |
11,2 |
11,2 |
13,5 |
Схема и примеры условного обозначения рельсов
Схема обозначения
Рельс Х– Х– Х– Х– Х– Х
Обозначение стандарта — ГОСТ Р 51685–2000
Наличие болтовых отверстий
25
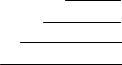
Длина рельса
Марка стали
Категория качества
Тип рельса
Примеры условного обозначения рельсов
Рельс Р65-Т1-М76Т-25-3/2 ГОСТ Р 51685–2000
рельс типа Р65, категории Т1 из стали марки М76Т, длиной 25 м с тремя болтовыми отверстиями на обоих концах рельса;
Рельс Р75-Т2-Э76Ф-25-2/1 ГОСТ Р 51685–2000
рельс типа Р75, категории Т2 из стали марки Э76Ф, длиной 25 м с двумя болтовыми отверстиями на одном конце рельса;
Рельс Р65-Н-М76-12,5-0 ГОСТ Р 51685–2000
рельс типа Р65, категории Н из стали марки М76, длиной 12,5 м без болтовых отверстий;
Рельс Р65-В-К78ХСФ-25-3/1 ГОСТ Р 51685–2000
рельс типа Р65, категории В из стали марки К78ХСФ, длиной 25 м с тремя болтовыми отверстиями на одном конце рельса.
Технические требования
Рельсы изготовляют в соответствии с требованиями ГОСТ Р 51685–2000 по техническому регламенту, утвержденному в установленном порядке.
Рельсы изготовляют из спокойной стали мартеновского, конверторного или электропечного производства.
Химический состав стали, определяемый по ковшовой пробе, должен соответствовать указанному в табл. 3.
Таблица 3
Химический состав стали
|
|
|
|
Массовая доля элементов, % |
|
|
|
|
||
|
|
|
|
|
|
|
|
|
|
|
Марка |
Угле- |
Мар- |
Крем- |
|
|
|
Фос- |
Сера |
|
Алю- |
стали |
Ванадий |
Титан |
Хром |
фор |
|
миний |
||||
|
род |
ганец |
ний |
|
|
|
|
|||
|
|
|
|
|
Не более |
|
||||
|
|
|
|
|
|
|
|
|
||
|
|
|
|
|
|
|
|
|
|
|
К78ХСФ |
0,74– |
|
0,40– |
0,05– |
|
0,40– |
0,025 |
0,025 |
|
0,005 |
Э78ХСФ |
0,82 |
|
0,80 |
0,15 |
|
0,60 |
|
|||
|
|
|
|
|
|
|||||
М76Ф |
|
|
|
|
|
|
0,035 |
0,040 |
|
|
К76Ф |
|
0,75– |
|
|
|
|
0,030 |
0,035 |
|
0,020 |
Э76Т |
0,71– |
1,05 |
0,25– |
0,03– |
|
|
0,025 |
0,030 |
|
|
М76Т |
0,82 |
|
0,45 |
0,15 |
0,007– |
|
0,035 |
0,040 |
|
|
К76Т |
|
|
|
|
|
0,030 |
0,035 |
|
|
|
|
|
|
|
0,025 |
|
|
||||
Э76Т |
|
|
|
|
|
0,025 |
0,030 |
|
|
|
|
|
|
|
|
|
|
|
|||
М76 |
0,71– |
0,75– |
0,25– |
|
|
|
0,035 |
0,040 |
|
|
К76 |
|
|
|
0,030 |
0,035 |
|
0,025 |
|||
0,82 |
1,05 |
0,45 |
|
|
||||||
Э76 |
|
|
|
0,025 |
0,030 |
|
|
|||
|
|
|
|
|
|
|
|
П р и м е ч а н и е. В марках стали буквы М, К, Э обозначают способ выплавки стали; цифры — среднюю массовую долю углерода; буквы Ф, С, Х, Т — легирование стали ванадием, кремнием, хромом и титаном.
Механические свойства рельсовой стали при испытании на растяжение и ударный изгиб должны соответствовать нормам, указанным в табл. 4.
Твердость термоупрочненных рельсов должна соответствовать нормам, указанным в табл. 5. Разность значений твердости на поверхности катания одного рельса не должна превышать 30
НВ.
26

Таблица 4
Механические свойства рельсовой стали при испытаниях на растяжение и ударный изгиб
|
Временное |
Предел |
Относи- |
Относитель- |
Ударная вяз- |
||
Кате- |
сопротивление, |
текучести, |
тельное |
ное сужение, |
кость КСК, |
||
удлинение, |
2 |
|
|||||
гория рель- |
Н/мм2 (кгс/мм2) |
Н/мм2 (кгс/мм2) |
% |
Дж/см |
2 |
||
са |
|
|
|
% |
|
(кгс м/см ) |
|
|
|
|
|
|
|
|
|
|
|
|
|
|
|
|
|
|
|
|
|
Не менее |
|
|
|
|
|
|
|
|
|
|
|
В |
1290 |
(132) |
850 (87) |
12,0 |
35,0 |
15 (1,5) |
|
|
|
|
|
|
|
|
|
Т1 |
1180 |
(120) |
800 (82) |
8,0 |
25,0 |
25 (2,5) |
|
Т2 |
1100 |
(112) |
750 (76) |
6,0 |
25,0 |
15 (1,5) |
|
|
|
|
|
|
|
|
|
Н |
900 |
(92) |
|
5,0 |
|
|
|
Таблица 5
Твердость термоупрочненных рельсов
|
Твердость рельса НВ, для категории |
|||
Место определения твердости |
|
|
|
|
|
В |
Т1 |
Т2 |
|
|
|
|
|
|
На поверхности катания головки |
363–401 |
341–401 |
321–401 |
|
|
|
|
|
|
На глубине 10 мм от поверхности |
|
Не менее 341 |
Не менее 321 |
|
катания |
|
|||
Не менее 341 |
|
|
||
|
|
|
||
На глубине 22 мм от поверхности |
Не менее 321 |
Не менее 300 |
||
|
||||
катания |
|
|||
|
|
|
||
|
|
|
|
|
В шейке и подошве |
|
Не более 388 |
|
При копровых испытаниях проба рельса должна выдерживать удар падающим грузом не менее 1000 кг с высоты, указанной в табл. 6, без излома и признаков разрушения.
Таблица 6
|
|
Высота падения груза и температура пробы |
||||||
|
|
|
при копровых испытаниях |
|||||
|
|
|
|
|
|
|
|
|
|
|
|
|
Высота падения груза, м, |
|
|
||
Категория |
Температура пробы, °С |
|
для рельса типа |
|
|
|||
рельса |
|
|
|
|
|
|
||
|
|
Р50 |
|
Р65, Р65К |
|
Р75 |
|
|
|
|
|
|
|
|
|||
|
|
|
|
|
|
|
|
|
В |
–(60±5) |
|
3,5 |
|
5,0 |
|
5,5 |
|
|
|
|
|
|
|
|
|
|
Т1, Т2 |
|
3,0 |
|
4,2 |
|
4,5 |
|
|
|
|
|
|
|
||||
Н |
от 0 до 40 |
|
6,1 |
|
7,3 |
|
8,2 |
|
7.2. Эксплуатационные дефекты рельсов
Рельсы являются основными элементами железнодорожного пути и подвергаются значительным силовым воздействиям при прохождении поездов. По мере эксплуатации в них появляются различные дефекты, угрожающие безопасности движения поездов. Причины возникновения дефектов в рельсах могут быть различными:
•недостатки технологии изготовления и сварки;
•недостатки текущего содержания пути;
•недостаточная контактно-усталостная прочность;
•нарушения при воздействии на рельсы подвижного состава.
В процессе эксплуатации в наибольшей степени выход рельсов по изломам и другим дефектам зависит от:
•груза, т бр., перевезенного по рельсам;
•нагрузки на ось подвижного состава;
•скорости движения поездов.
Изломы рельсов являются первой причиной крушений и аварий в путевом хозяйстве.
Выход рельсов по дефектам и изломам зависит также от времени года. Максимальный выход рельсов по дефектам приходится на март (в европейской части России) и на апрель (на дорогах Востока и Сибири). Он совпадает со временем резкого перепада температуры и со временем оттаивания балласта.
27
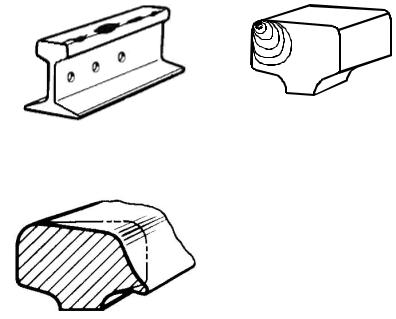
Наиболее нагруженной зоной рельса является головка. Особенно большие нагрузки испытывает участок головки рельса со стороны рабочей грани, так как именно на этот участок передается силовое воздействие колес подвижного состава.
В результате возникают контактно-усталостные трещины кодов 11 и 21 (рис. 23).
При проходе колес с большими ползунами или выбоинами, вследствие буксования или юза, а также из-за ударов по рельсу (инструментом) в головке рельса могут появиться трещины (дефекты кодов 24 и 25), способные привести к хрупкому излому, особенно при низких температурах.
Наблюдается и боковой износ головки рельсов сверх допустимых норм (рис. 24).
а) |
б) |
Рис. 23. Контактно-усталостные трещины в рельсах:
а — выкрашивание металла на боковой рабочей выкружке головки рельса (код 11); б — поперечные трещины в головке рельса в виде светлых или темных пятен (код 21)
Рис. 24. Боковой износ головки рельса (код 44)
начать развиваться в головке на
Наиболее опасными из названных дефектов являются поперечные трещины (код 21), так как они могут привести к хрупкому излому рельса под проходящим составом (поездом). Началом образования дефекта 21 является, как правило, продольная трещина, развитие которой приводит к отслоению металла (код 11).
Установлено, что продольные трещины обычно возникают на выкружке рабочей грани и распространяются в глубь рельса на 5–11 мм. От этого дефекта на глубине расположения продольной трещины развивается усталостная поперечная трещина. В месте, например, контактной сварки поперечная трещина может
любой глубине, в зависимости от расположения дефекта сварки.
8.ВИДЫ СВАРКИ РЕЛЬСОВ
Вмировой практике известны несколько способов сварки рельсов — дуговой, ванный, газопрессовый, индукционно-прес-совый, контактный и термитный. Важнейшими показателями этих способов являются: механические свойства и качество получаемых стыков, эксплуатационная стойкость и стоимость сварки рельсов, производительность и трудоемкость процесса, автоматизация, механизация и компьютеризация работ.
Дуговой ванный способ
При дуговой ванной сварке расплавление основного металла осуществляется дугой и частично за счет теплоты, передаваемой изделию перегретым жидким металлом сварочной ванны. Поэтому сварку проводят при повышенной силе тока. Сварку начинают в нижней части формы, расплавляя дугой нижние кромки стыка. В процессе сварки происходит постепенное заполнение зазора расплавленным металлом. Он образуется в общей для обоих рельсовых концов ванне и удерживается специальными формами. До окончания сварки металл в верхней части сварочной ванны стараются поддерживать в расплавленном состоянии на возможно большую глубину и обязательно на всю ширину формы. Шов наплавляют несколько выше поверхности рельсов.
Газопрессовый способ
Газопрессовая сварка рельсов производится путем нагрева концов рельсов газовым пламенем и осадки их при помощи сдавливания. При нагреве металл торцов рельсов доводится до пластического состояния. Нагрев ведется контурными многопламенными горелками. Горючими газами для них служат ацетилен, пропан-бутан, природный газ и другие, которые сжигаются в кислороде. Во избежание пережога металла и для обеспечения необходимой зоны разогрева горелка в процессе сварки должна колебаться в обе стороны стыка.
При газопрессовом способе торцевые поверхности рельсов должны быть параллельны и хорошо очищены от грязи и ржавчины; перед сваркой их промывают четыреххлористым углеродом.
28
В нашей стране с 1960 по 1970 гг. в опытном порядке одно рельсосварочное предприятие применяло газопрессовую сварку рельсов. Было сварено 660 км пути бесстыковых плетей и длинных рельсов. В связи с низкими экономическими показателями, недостаточным уровнем механизации и автоматизации процесса на дорогах России и стран СНГ газопрессовая сварка рельсов с 1971 г. не используется.
Индукционно-прессовый способ
Способ аналогичен газопрессовому по физическому смыслу, только в качестве источника нагрева используется не тепло от горения газовых смесей, а тепло от использования токов высокой частоты.
Контактный способ
Контактной сваркой называется сварка с применением давления, при которой нагрев производится теплотой, выделяющейся при прохождении электрического тока через находящиеся в контакте соединяемые части. Контактная сварка относится к видам сварки с кратковременным нагревом места соединения без оплавления или с оплавлением и осадкой разогретых заготовок. Характерная особенность этих процессов — пластическая деформация, в ходе которой формируется сварное соединение.
Место соединения разогревается проходящим по металлу электрическим током, причем максимальное количество теплоты выделяется в месте сварочного контакта.
Контактная стыковая сварка оплавлением в России применяется для сварки железнодорожных рельсов с середины XX в. Сварка выполняется как в стационарных условиях (РСП), так и в пути с помощью передвижных путевых рельсосварочных машин (ПРСМ). Сварка производится в автоматическом режиме с помощью сварочных головок при непрерывном или импульсном оплавлении. Сварочные головки снабжены гидравлическими зажимами, создающими осевое усилие осадки 330 кН. Время сварки 3–4 мин. Величина осадки 24 мм. Наибольшая температура в зоне стыка около 1250 °С. Машины оснащаются гратоснимателем. Окончательная зачистка сварного стыка производится после остывания металла шлифовальным кругом. Качество контролируется с помощью ультразвукового дефектоскопа.
Стыковая контактная сварка достаточно хорошо зарекомендовала себя при получении длинных рельсовых плетей в стационарных условиях и на перегонах. Следует отметить, что при проведении ремонтных работ рельсового пути данным способом необходимы дорогостоящие путевые рельсосварочные машины, продолжительные «окна» для их доставки на место работ и последующей эксплуатации, кроме того, требуется достаточно большая бригада рабочих. Дефицит рабочего времени в ряде случаев заставляет нарушать технологический процесс, что приводит к получению сварного стыка невысокого качества.
Одним из существенных недостатков контактной стыковой сварки является невозможность сварки стыков в районе стрелочных переводов, а также сложность проведения нормализации стыка в полевых условиях.
Термитный способ
В настоящее время для сварки стрелочных переводов безальтернативной и обеспечивающей хорошее качество сварного шва является алюминотермитная сварка (АТС) методом промежуточного литья (рис. 25).
29
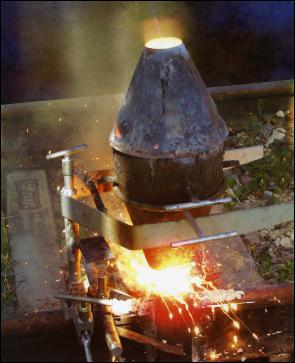
Рис. 25. Алюминотермитная сварка рельсов
Алюминотермитная сварка рельсов (АТСР) имеет ряд преимуществ перед стыковой контактной сваркой, осуществляемой с использованием путевых рельсосварочных машин: она не требует сложного дорогостоящего оборудования, большого количества рабочих, продолжительных перерывов в движении поездов. Заварку стыка рельсов выполняет бригада из трех человек.
Этот метод основан на химической реакции между оксидами алюминия и железа, в результате которой выделяется большое количество тепла. И при получаемой высокой температуре доза расплавленного стального порошка заливается в зазор между двумя рельсами, подготовленными к сварке. На концах рельсов устанавливают песчаные формы, которые удерживают расплавленный металл до затвердевания. При точном соблюдении технологии термитная сварка обеспечивает высокую прочность сварного стыка, а малые габариты и масса оборудования, в основном ручного, делают целесообразным применение этого метода даже в отдаленных местах, но преимущественно при небольшом количестве стыков.
Соединение между собой железнодорожных рельсов алюминотермитной сваркой методом промежуточного литья можно производить в любом сочетании по категориям качества рельсов (термоупрочненные между собой, термоупрочненные и нетермоупрочненные, нетермоупрочненные между собой) и разных заводов-изготовителей. Этим методом сваривают как новые, так и старогодные рельсы на путях всех категорий — главных, приемоотправочных, станционных, горочных и пр.
9. МЕТАЛЛУРГИЧЕСКИЕ ПРОЦЕССЫ ПРИ АЛЮМИНОТЕРМИТНОЙ СВАРКЕ РЕЛЬСОВ
Основная часть технологического процесса АТС заключается в том, что источником тепла, необходимого для проведения процесса сварки, являются термиты (порошкообразные смеси металлов с окислами других металлов), при горении которых происходит обменная реакция по кислороду с выделением значительного количества тепла (экзотермическая реакция).
Для сварки рельсов применяется железоалюминиевый термит, представляющий собой механическую смесь окислов железа (главным образом, закиси-окиси) и алюминиевого порошка. Источником кислорода в термите является окисел, а источником тепла (горючим) — металл, входящий в смесь в чистом виде. В качестве окислов в термитных смесях используют железную окалину, а в качестве горючих металлов — алюминий, магний. Кроме того, в термит можно вводить легирующие элементы для улучшения механических свойств термитного металла и механический наполнитель — железную обсечку — для увеличения выхода жидких продуктов термитной реакции (стали). Наибольшее распространение получили алюминиевые термиты, содержащие 20–25 % алюминиевого порошка и 75–80 % окалины. Алюминиевый порошок должен содержать: 96,5–99,7
30