
633
.pdf% Al; 0,47 % Fe; 0,36 % Si; 1 % Al2O3. Железная окалина, используемая в термите, является сложным химическим соединением, состоящим из нескольких окислов: от окиси железа Fe2O3 плотностью 5,1 г/см3 и температурой плавления 1556 °С до закиси железа FeO плотностью 5,7 г/см3 и температурой плавления 1420 °С. Химический состав порошка железной окалины после смешивания трех фракций должен быть следующим: Fe > 68,6 %; Mn = 0,3 – 0,6 %; Si = = 0,4–0,45 %; прочие примеси ≤ 0,30 %; O2 ≤ 28,65 %; ≤ 14 % FeO.
Реакция горения термита выражается так:
2Al + Fe2O3 = Al2O3 + 2Fe + Q, |
(13) |
2Al + 3FeO = Al2O3 + 3Fe + Q, |
(14) |
где Fe — термитное железо; Al2O3 — шлак; Q — выделенное тепло.
Количественное соотношение исходных компонентов и продуктов реакции показано в табл. 7.
Таблица 7
Соотношение исходных компонентов и продуктов реакции
|
Массовое соотношение компонентов, % |
Тепловой |
Температура |
|||
|
|
|
|
|
||
Окислитель |
До реакции |
В продуктах реакции |
эффект, |
процесса, |
||
|
|
|
|
|
Дж/моль |
°С |
|
Алюминий |
Окиси |
Железо |
Шлак |
||
|
|
|
||||
|
|
|
|
|
|
|
Fe2O3 |
25,24 |
74,76 |
52,28 |
47,72 |
752 |
2670 |
FeO |
20 |
80 |
62,2 |
37,8 |
775,6 |
2260 |
|
|
|
|
|
|
|
В процессе термитной реакции происходит выгорание ряда компонентов — углерода до 30 %, кремния до 20 %, марганца до 80 %. Для увеличения содержания этих элементов в термитную смесь (шихту) вводят в измельченном виде добавки: ферромарганец с содержанием марганца 76– 80 %, ферросилиций с содержанием кремния 40–80 %, углерод в виде графитового порошка и гранулированную малоуглеродистую сталь. Могут быть внесены и такие элементы, как ферромолибден, ферротитан, феррованадий.
При сгорании алюминиевый термит может развивать температуру до 3000 °С.
На тепловой эффект оказывает влияние гранулометрический состав, степень уплотнения и равномерность перемешивания литейного компонента. Плотность термита составляет 3,2–3,4 г/см3. Размеры частиц компонентов лежат в пределах: алюминий — 0,1…1 мм; железная окалина — 0,05…1 мм; стальной наполнитель — около 1 мм; лигатура — 0,25…0,6 мм.
10. ГАЗОПЛАМЕННОЕ ОБОРУДОВАНИЕ, ИСПОЛЬЗУЕМОЕ ПРИ АЛЮМИНОТЕРМИТНОЙ СВАРКЕ РЕЛЬСОВ
Важной особенностью технологического процесса АТСР является предварительный подогрев рельсов. На качество сварного соединения может влиять окружающая среда, погода. В ненастную, сырую погоду в сварном шве возможно появление газовых пор, снижающих прочность соединения. Это явление наблюдается и в тех случаях, когда недостаточно хорошо просушены формы. Наличие влаги в формовочном материале может вызвать дополнительные реакции между алюминием, присутствующим в термитном металле, и влагой. Реакции с влагой протекают бурно, с выплесками металла из форм. Даже просушенные при небольшой температуре сварочные формы могут вызвать появление газовой пористости в сварном шве.
Помимо этого предварительный подогрев необходим для того, чтобы создать наиболее благоприятные условия для заливки расплавленного термитного металла, уменьшить температурный перепад между заливаемым расплавленным металлом и зоной сварки, сократить расход термита. А также для удаления влаги, которая, помимо форм, может быть в смеси, применяемой для промазки мест сопряжения сварочных полуформ с рельсами.
С увеличением концентрации углерода в свариваемом металле и в шве необходимая температура предварительного нагрева рельсовой стали ~ 900 °С.
Для проведения операции предварительного подогрева используется специальная горелка, а в качестве горючего могут использоваться бензин или природные газы. Наибольшее распространение получила смесь кислорода и пропана, так как при применении бензина происходит образование засорений во внутренних каналах и нагара в узких местах горелки, что приводит к внезапным нарушениям установленного режима работы горелки.
31
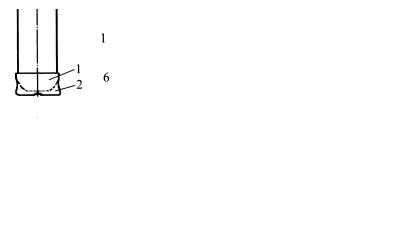
10.1. Назначение, устройство и принцип действия баллонов, вентилей, редукторов, газопламенной горелки
Баллоны
Баллоны предназначены для хранения и перевозки сжатых, сжиженных и растворенных газов. Требования к баллонам для сжатых газов регламентируются правилами Госгортехнадзора. Бал-
лоны окрашивают снаружи в условные цвета, в зависимости от рода газа:
•кислород – голубой;
•ацетилен – белый;
•пропан – красный.
Часть верхней сферы баллона не окрашивают и на ней выбивают паспортные данные: товарный знак предприятия-изго-товителя; номер баллона; дату (месяц, год) изготовления; год следующего испытания, которые проводятся каждые пять лет; массу порожнего баллона, кг; емкость баллона, дм3; клеймо ОТК.
Баллоны для пропана изготавливают сваркой из листовой углеродистой стали с толщиной стенки 3 мм, емкостью 40 и 55 дм3, они рассчитаны на максимальное рабочее давление 1,6 МПа. Кислородные баллоны изготавливают из бесшовных труб, они рассчитаны на давление 10–20 МПа. Устройство баллонов показано на рис. 26.
а) |
б) |
в) |
3
Рис. 26. Баллоны для сжатых газов:
а— кислородный; б — ацетиленовый; в — (сварной) для пропан-бутана; 1 – днище; 2 – башмак; 3 – корпус; 4 – горловина; 5 – вентиль; 6 – колпак; 7 – пористая масса; 8 – подкладные кольца; 9 – паспортная табличка
Вентили
Вентили для кислородных баллонов (рис. 27, а) изготавливают из латуни.
Стали для деталей вентиля, соприкасающихся с кислородом, применять нельзя, так как сталь сильно корродирует в среде сжатого влажного кислорода. В вентиле для кислородных баллонов вследствие случайного попадания масла или при воспламенении от трения самодельной прокладки сальника возможно загорание стальных деталей, потому что сталь может гореть в струе сжатого кислорода.
Латунь не горит в кислороде, ее применение в кислородных вентилях безопасно. Маховички, заглушки и другие детали вентилей изготавливают из алюминиевых сплавов или пластмасс.
Вентили для пропан-бутановых баллонов (рис. 27, б) имеют либо стальной, либо латунный корпус, клапан и шпиндель, соединенные эластичным резиновым манжетом, который обеспечивает герметичность сальниковой гайки.
а) |
б) |
32
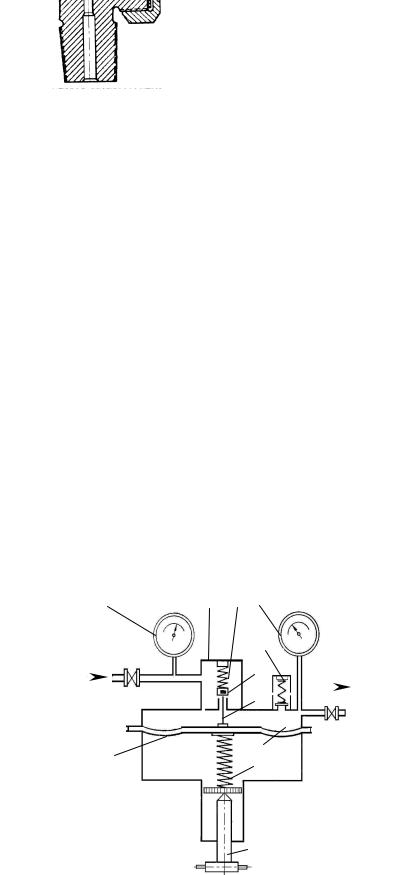
Рис. 27. Запорная аппаратура:
а— вентиль для кислородного баллона;
б— вентиль для пропан-бутанового баллона; 1 — корпус; 2 — маховичок; 3 — шпиндель; 4 — гайка; 5 — пружина;
6 — муфта; 7 — клапан; 8 — сальниковая гайка; 9, 11 — прокладка;
10 — заглушка; 12 — клапан
Редукторы
Редукторы (рис. 28) служат для понижения давления газа, отбираемого из баллона или газопровода, и поддержания этого давления постоянным, независимо от снижения давления газа в баллоне.
Редукторы для кислорода, водорода и ацетилена применяют для работы при температуре от –25 до +50 °С.
Редукторы для пропана и метана применяют для работы при температуре от –15 до +45 °С. Промышленностью выпускаются редукторы однокамерные и двухкамерные. В двухкамерных
(двухступенчатых) редукторах давление понижается в двух ступенях: в первой ступени давление понижается с начальной величины 15 МПа (150 кгс/см2) до промежуточного значения 4 МПа (40 кгс/см2), а во второй — до окончательного давления 0,3–1,5 МПа (3–15 кгс/см2). Двухступенчатые редукторы обеспечивают практически постоянное давление газа в горелке и менее склонны к «замерзанию», однако они сложнее по конструкции, чем однокамерные, и значительно дороже.
10 |
1 |
11 |
4 |
|
|
|
|
|
|
|
3 |
|
|
Из |
|
|
2 |
К |
||
|
|
|
|
|||
|
|
|
|
|
||
баллона |
|
|
|
|
|
|
|
|
|
|
9 |
горелке |
|
8 |
|
|
5 |
|
|
|
|
|
6 |
|
|
||
|
|
|
|
|
|
7
Рис. 28. Схема устройства однокамерного редуктора:
1 — камера высокого давления; 2 — клапан высокого давления; 3 — предохранительный клапан; 4, 10 — манометры;
5 — камера низкого давления; 6, 11 — пружины; 7 — регулирующий винт; 8 — мембрана; 9 — толкатель
33
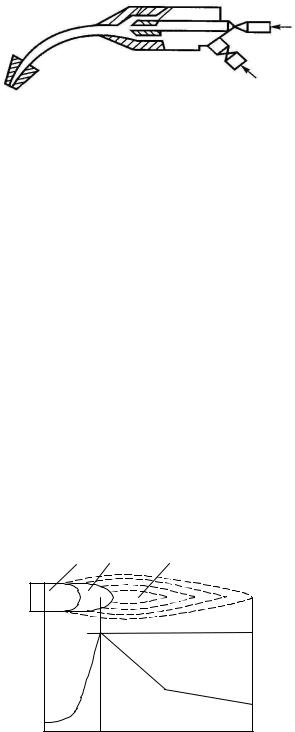
Рукава
Рукава (шланги) служат для подвода газа в горелку. Их делают резиновыми с нитяным каркасом.
Горелки
Горелка предназначена для смешивания кислорода в необходимых количествах с горючим газом, подачи горючей смеси к месту сварки (нагрева) и создания пламени с необходимой температурой.
По способу подачи кислорода, горючего газа и конструкции узла их смешивания различают два типа горелок: инжекторные и безынжекторные.
Чаще используются инжекторные горелки (рис. 29).
Кислород
Пропан
Рис. 29. Схема инжекторной горелки
В инжекторной горелке смесительная камера начинается небольшим участком цилиндрической формы, плавно переходящим в более удлиненный конусный участок.
Подача пропана в смесительную часть инжекторной горелки осуществляется за счет подсоса его струей кислорода, выходящей с большой скоростью из отверстия сопла, называемого инжектором. Кислород под давлением поступает по каналу в сопло инжектора. При истечении кислорода с большой скоростью из сопла создается разряжение в канале, по которому подсасывается пропан.
Кислород и пропан поступают в смесительную камеру, имеющую конически расширяющийся канал, где смешиваются и образуют горючую смесь, которая по трубке идет в мундштук горелки, создавая на выходе из него при сгорании сварочное пламя.
10.2. Строение сварочного пламени
Изменяя соотношение кислорода и пропана в горючей смеси, можно получить три основных вида сварочного пламени:
•науглероживающее (с избытком пропана);
•нормальное (называемое восстановительным);
•окислительное (с избытком кислорода).
При нагреве стыков рельсов используют нормальное пламя. Нормальное пламя (рис. 30) имеет светлое ядро 1, несколько темную восстановительную зону 2 и факел 3. Ядро имеет четко очерченную форму, близкую к форме цилиндра с закругленным концом, и ярко светящуюся оболочку, которая состоит из раскаленных частиц углерода. Сгорание этих частиц происходит в наружном слое оболочки. Размерами ядра пламени являются его диаметр и длина. Диаметр ядра определяется диаметром канала мундштука и расходом горючей смеси. Горелки комплектуются набором мундштуков нескольких номеров. Чем больше номер мундштука и расход горючей смеси, тем больше диаметр ядра.
|
1 |
2 |
3 |
Т,°С |
2400 |
|
|
|
|
|
х, мм |
|
Рис. 30. Строение сварочного пламени |
34
Восстановительная зона имеет более темный цвет, отличающийся от цвета ядра и остальной части пламени. Она занимает пространство в пределах 20 мм от конца ядра, в зависимости от номера мундштука.
Восстановительная зона состоит из окиси углерода и водорода и имеет наиболее высокую температуру в точке, отстоящей на 2–6 мм от конца ядра. Этой зоной пламени и нагревают металл.
Остальная зона пламени, расположенная за восстановительной зоной, называется факелом и состоит из углекислого газа, паров воды и азота, которые появляются в пламени при сгорании окиси углерода и водорода восстановительной зоны за счет кислорода окружающего воздуха. Температура факела значительно ниже температуры восстановительной зоны.
Таким образом, в восстановительной зоне, в точке, отстоящей чуть дальше от конца ядра, достигается максимальная температура пламени.
Кислородно-пропановое пламя достигает максимальной температуры 2400 °С на расстоянии 2,5 длины ядра от среза мундштука.
Признаком окислительного пламени является укороченное заостренное ядро с менее резкими очертаниями и бледным цветом.
В науглероживающем пламени размеры зоны сгорания увеличиваются, ядро теряет очертания, становится расплывчатым, восстановительная зона светлеет и почти сливается с ядром, пламя принимает желтоватую окраску. Во избежание сильного науглероживания металла ядро пламени не должно касаться поверхности металла.
Характер пламени определяется сварщиком «на глаз» по форме и цвету пламени.
10.3. Техника предварительного нагрева при алюминотермитной сварке рельсов
Первый этап — подготовка баллона. Для этого открывают колпак; отвинчивают штуцеры; осматривают вентиль, чтобы убедиться, нет ли следов жира или масла.
Если на вентиле замечено наличие масла, то таким баллоном пользоваться нельзя. Сварщик должен отставить данный баллон и сообщить о дефекте мастеру или руководителю работ.
Если вентиль исправен, его штуцер продувают кратковременным поворотом маховичка на небольшой угол, при этом нужно стоять сбоку от штуцера вентиля.
Если вентиль не открывается или имеет утечку газа (травит), баллон следует отставить для отправления обратно на кислородный завод для ремонта.
Далее проверяют состояние накидной гайки редуктора и присоединяют редуктор к вентилю баллона, затем ослабляют регулирующий винт редуктора.
Медленным вращением маховичка открывают вентиль баллона и устанавливают рабочее давление кислорода с помощью регулирующего винта редуктора.
Регулировка давления на редукторах кислорода и пропана производится при открытых вентилях на горение. Горелка зажигается после установки ее на вспомогательную стойку. Нельзя зажигать горелку, держа ее в руке.
При зажигании горелки сначала на ручке горелки следует открыть вентиль подачи кислорода, затем открыть вентиль подачи пропана и после кратковременной продувки закрыть вентиль подачи кислорода. После поджога пропана снова открыть вентиль подачи кислорода и после этого отрегулировать пламя до нормального горения. Отрегулированная горелка должна давать устойчивое сварочное пламя. Если горение неровное, пламя отрывается от мундштука, гаснет или дает обратные удары и хлопки, следует тщательно отрегулировать вентилями подачу кислорода и пропана. Если после регулировки неполадки не устраняются, то причиной их являются неисправности в самой горелке: неплотности в соединениях, повреждение выходного канала мундштука или инжектора, неправильная установка деталей горелки при сборке, засорение каналов и т.д.
Давление кислорода на кислородном редукторе должно быть 4,5–5,0 атм (0,45–0,5 МПа); на пропановом — 1–1,2 атм (0,1–0,12 МПа).
После того как пламя отрегулировано, газовая горелка помещается на комбинированную стойку в зоне сварки для нагрева концов рельсов. Продолжительность прогрева для рельса Р65 составляет 7–9 мин. Торцы рельсов при этом нагреваются до 800–900 °С. Контроль осуществляется визуально (светло-красный цвет металла) либо пирометром.
За одну минуту до конца подогрева концов рельсов нагревают литниковый мостик формы, удерживая его специальными щипцами. После прогрева литникового мостика горелка снимается и устанавливается на вспомогательную стойку.
35
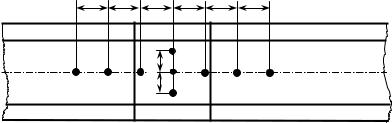
Во время работы с горелкой нужно следить, чтобы газовые рукава не попали на горячий металл или пламя горелки.
Не следует во время и после подогрева стыка касаться форм.
При тушении горелки сначала прекращается подача пропана, а затем кислорода. Делать это надо только на стойке горелки.
При перерывах в работе пламя горелки должно быть потушено, а вентили на ней закрыты. Во время дополнительных перерывов в работе следует закрывать вентили на баллонах.
11.ПОСЛЕДОВАТЕЛЬНОСТЬ ВЫПОЛНЕНИЯ ОПЕРАЦИЙ ПРИ АЛЮМИНОТЕРМИТНОЙ СВАРКЕ РЕЛЬСОВ
11.1.Подготовительные операции
11.1.1. Контрольная сварка
Для производства работ по алюминотермитной сварке рельсов службой пути должна быть организована бригада, состоящая из трех сварщиков-литейщиков (как минимум двух), имеющих свидетельство на проведение указанных работ, и монтеров пути под руководством бригадира для выполнения путевых работ, сопутствующих процессу сварки. Руководителем объединенной бригады назначается инженерно-технический работник в должности не ниже дорожного мастера, на него возлагается ответственность за качество работ и соблюдение техники безопасности при выполнении алюминотермитной сварки.
Перед выполнением специальных работ по алюминотермитной сварке рельсов в пути осуществляется проверка готовности и квалификации бригады, работоспособности оборудования и качества расходных материалов, которые будут использованы для сварки в пути. Для этого производится контрольная сварка по принятому технологическому процессу на четырех контрольных образцах рельсов с последующим неразрушающим и разрушающим контролем качества литейного шва.
Для подготовки контрольных образцов отрезаются куски рельсов длиной 550–630 мм в количестве восьми штук из тех же типов рельсов, которые подлежат соединению в пути [12].
Измерение твердости производят в середине литейного шва (по три отпечатка с промежутками между ними 15 мм по ширине головки рельса) и в обе стороны от него на длине 75 мм (по одному отпечатку) на приборе Бринелля с применением шарика диаметром 10 мм или переносными твердомерами. Схема замеров показана на рис. 31.
Твердость металла в литейном шве в зоне головки рельса должна быть на одном уровне с твердостью основного металла головки соответствующей категории рельсов.
Допускается снижение твердости в зоне литейного шва и в околошовной зоне, имеющей протяженность до 75 мм от оси сварного шва в обе стороны, относительно нижней границы нормативной твердости прокатанных рельсов на 15 % (при сварке термоупрочненных рельсов с нетермоупрочненными за нормативную твердость принимается твердость термоупрочненных рельсов).
25 |
25 |
25 |
25 |
25 |
25 |
|
|
15 |
|
|
|
|
|
15 |
|
|
|
Рис. 31. Схема контроля твердости металла литейного шва
Испытания на статический поперечный изгиб проводят на тех же четырех контрольных образцах, на которых определяли твердость. Испытания выполняют на рельсосварочном предприятии под руководством главного инженера службы пути (дирекции по ремонту пути). Эти работы производят на прессе, имеющем действующее свидетельство о его поверке. Схема проведения испытаний показана на рис. 32.
36
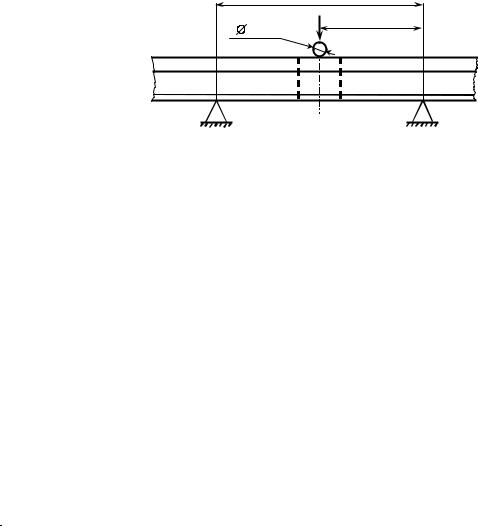
1000 |
|
Р |
500 |
≥ 30 |
|
Рис. 32. Схема проведения испытаний на статический изгиб
Контрольные образцы устанавливают на опоры цилиндрической или полуцилиндрической формы с диаметром не менее 50 мм. Расстояние между опорами 1000 мм. На середину испытываемого шва через ролик пуансона (диаметром не менее 50 мм) передается нагрузка. Скорость перемещения плунжера должна быть не более 10 мм в минуту. Два контрольных образца нагружают так, чтобы растяжение было в подошве, и два других — с растяжением головки.
Сварные контрольные образцы доводят до излома с определением прочности (разрушающая нагрузка) и пластичности (стрела прогиба) литейного шва. Результаты испытаний контрольных образцов должны соответствовать требованиям, указанным в ТУ 0921-127-011 24323–2005.
Нормативные значения показателей прочности и пластичности рельсов, сваренных АТС, приведены в табл. 8.
Таблица 8
Нормативные значения показателей прочности и пластичности рельсов, сваренных термитным способом
|
Разрушающая нагрузка не менее, кН, — числитель |
|||
Зона растяжения |
Стрела прогиба не менее, мм, — знаменатель |
|||
натурных образцов |
|
|
|
|
|
Тип рельсов по ГОСТ Р 51685–2000 |
|||
на пролете 1 м |
|
|||
|
|
|
|
|
|
Р50 |
|
Р65 |
Р75 |
|
|
|
|
|
Подошва (нагруже- |
840/18 |
|
1340/16 |
1500/14 |
ние на головку) |
|
|||
|
|
|
|
|
|
|
|
|
|
Головка (нагружение |
700/14 |
|
1220/13 |
1250/11 |
на подошву) |
|
|||
|
|
|
|
П р и м е ч а н и е. Для старогодных рельсов типов Р50, Р65 и Р75 допускается снижение разрушающей нагрузки до 2 % на 1 мм износа рельса, но не более 20 % при максимальном износе рельса до 10 мм.
Результаты замеров твердости, разрушающей нагрузки и величина стрелы прогиба заносятся в таблицу (прил. А).
При отклонении показателей, полученных на одном из четырех контролируемых образцов, испытание повторяют на двух дополнительных контрольных образцах. В случае отклонения показателей, полученных на двух или более образцах, производят повторные испытания на четырех дополнительных образцах.
Если при этом параметры хотя бы одного дополнительного образца не удовлетворяют требованиям, указанным в табл. 8, то сварка в пути не разрешается.
Совместно с разработчиком технологии выполняется анализ и выявляются причины, приводящие к низкому качеству сварки.
После их устранения испытания повторяются на четырех контрольных образцах. При положительных результатах принимают решение о выполнении сварочных работ в пути.
На изломах контрольных образцов после испытаний их на статический поперечный изгиб проводится макроанализ. Определяется характер излома (хрупкий, вязкий или смешанный). Если излом смешанный, то определяется доля хрупкой и вязкой составляющей.
В изломе по месту сварки не допускается наличие дефектов: пор, непроваров, шлаковых включений, газовых пузырей, усадочных раковин и т.д. в количестве свыше трех общей площадью более 15 мм2.
11.1.2. Подготовка к алюминотермитной сварке на месте проведения работ
Перед началом производства работ по сварке необходимо провести осмотр и сушку тигля, предназначенного для плавильного процесса. При осмотре тигля контролируется отсутствие тре-
37
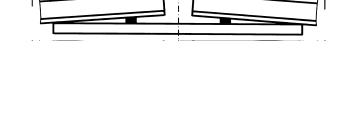
щин, сколов и других дефектов. Исправный тигель вставляется в обечайку, места контакта с обечайкой уплотняются формовочной смесью, и производится сушка при температуре не менее 25–30 °С в течение 24 ч (для сокращения времени просушки рекомендуется перед доставкой тигля на рабочее место просушить его при температуре 50–70 °С не менее 12–16 ч в сушильной камере или термостате). После этого тигель устанавливается на вспомогательной стойке.
На месте проведения работ с персоналом бригады проводится инструктаж по технике безопасности, пожарной безопасности и охране труда на рабочем месте; контролируется закрытие движения поездов на участке сварочных работ.
После этого непосредственно к месту проведения сварки подаются материалы и технологическое оборудование, которое устанавливается в удобном для работы положении с соблюдением норм безопасности.
Место производства работ ограждается в соответствии с инструкциями: по безопасности движения поездов, по производству путевых работ, по сигнализации, по правилам технической эксплуатации.
После окончания подготовительных операций производится демонтаж стыка и формирование стыкового зазора между торцами рельсов.
Демонтаж стыка выполняется в следующей очередности:
•разболчиваются по три шпалы в каждую сторону от стыка;
•разболчиваются и снимаются накладки;
•удаляется мазут и грязь со свариваемых поверхностей на расстоянии 100–120 мм от торца свариваемого рельса.
Формирование стыкового зазора между торцами рельсов 25 (± 1) мм проводится в такой последовательности:
•замеряется существующий зазор;
•при необходимости механическим способом обрезаются рельсы до величины стыкового зазора, при этом расстояние от торца рельса до края ближайшего болтового отверстия должно быть не менее 50 мм для рельсов Р65 и Р75 и не менее 23 мм для рельсов Р50;
•торцы рельсов очищаются от ржавчины металлической щеткой.
Для производства алюминотермитной сварки с целью компенсации просадки сварного шва рельсы необходимо выправить в рабочее положение. Для этого нужно обеспечить возвышение концов рельсов с помощью клиньев по вертикальной оси стыка на высоту 2,0 (± 0,5) мм.
Контроль установки концов рельсов перед сваркой выполняется линейкой длиной 1 м, штангенциркулем или щупом (рис. 33).
Рис. 33. Схема измерения высоты установки концов рельсов перед сваркой
Тигель перед началом сварки необходимо дополнительно просушить кислородно-пропановым пламенем с избытком кислорода. В процессе сушки горелку кольцевыми движениями по спирали нужно перемещать до верхних краев тигля в течение 55–60 с.
После окончания процесса сушки в реакционном тигле, расположенном на вспомогательной стойке, с помощью фрезы производится очистка отверстия для установки литника. Литниковый запор устанавливается в нижнем отверстии тигля таким образом, чтобы верхние его кромки находились на 8–10 мм выше днища тигля (рис. 34). На литниковый запор устанавливается оправка, и место соприкосновения литникового запора с тиглем уплотняется магнезитным порошком.
В тигель засыпается подготовленная порция литейного компонента, соответствующего типу свариваемых рельсов, и удаляется оправка.
38
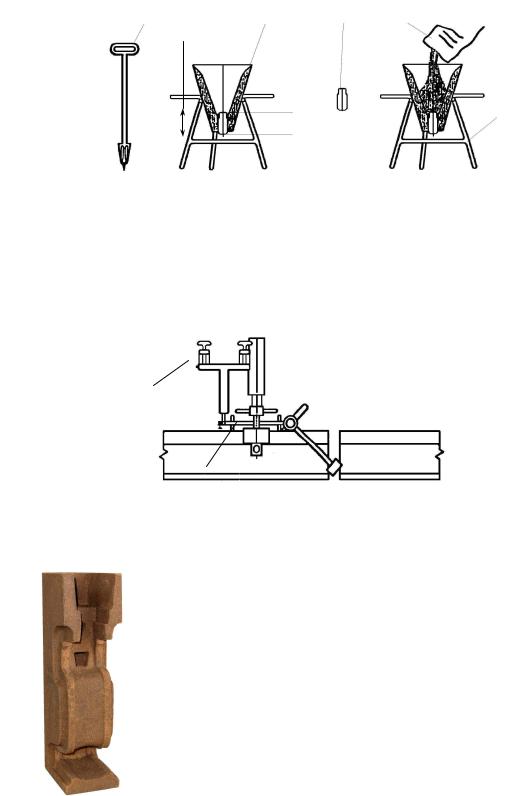
1 |
2 |
3 |
4 |
|
|
8–10 мм |
|
5
5
Рис. 34. Схема подготовки тигля к работе: 1 — фреза; 2 — тигель; 3 — литниковый запор;
4 — литниковый компонент; 5 — стойка вспомогательная
11.2. Сварочные операции
Технологическое оборудование для сварки в зоне стыка устанавливается в определенном порядке:
• Комбинированная стойка устанавливается на головку рельса таким образом, чтобы держатели частей литейной формы находились сбоку по оси свариваемого зазора (рис. 35).
1
2
Рис. 35. Установка комбинированной стойки:
1 — комбинированная стойка; 2 — держатель литейной полуформы
•На комбинированную стойку устанавливается механизм настройки горелки вместе с горелкой
ирегулируется положение сопла относительно свариваемого зазора.
•На свариваемом стыке устанавливается литейная форма, состоящая из двух полуформ (рис. 36). Для этого предварительно две полуформы необходимо очистить от упаковки, проверить визуально целостность их функциональных частей и вложить в металлические держатели, соблюдая соответствие правой и левой сторон. На одной полуформе убирается ослабленная стенка литейного желоба для отвода шлака. Полуформы фиксируются относительно стыкового зазора так, чтобы центр зазора совпал с вертикальной осью литейной формы, а сами полуформы прилегали друг к другу без ступенек по всему периметру стыковки.
•Проверяется возможность установки литникового мостика в соответствующий паз литейной формы. Он должен свободно входить в паз и располагаться горизонтально. При необходимости напильником обрабатываются боковые поверхности литникового мостика (рис. 37).
Рис. 36. Литейная полуформа
39
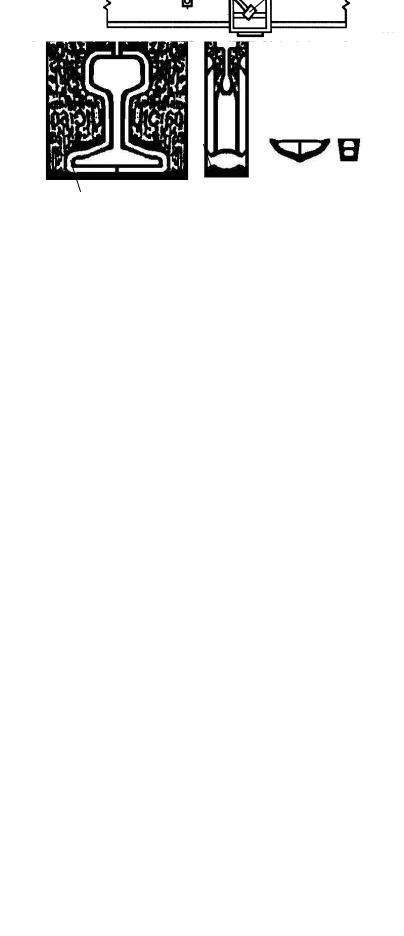
1
2
Рис. 37. Литейная форма:
1 — литниковый мостик; 2 — литейная полуформа
•Место контакта литейной формы с рельсом вручную уплотняется формовочным материалом.
•На литейную форму со стороны желоба отвода шлаков устанавливается ковш, внутренняя поверхность которого обмазывается формовочной смесью толщиной 5 мм. При сварке в пути ковш устанавливается с внутренней стороны колеи.
•Производится обмазка с целью уплотнения места контакта ковша с литейной формой.
•Устанавливается подготовленный тигель с литейным компонентом, который переносится со вспомогательной стойки на комбинированную, и проверяется центровка литника относительно вертикальной оси свариваемого зазора. При необходимости производится регулировка для совмещения осей литника и зазора. Контроль в данном случае осуществляется визуально. После этого
необходимо повернуть тигель на 90° в сторону от зазора.
• Подготавливаются две лопатки с формовочной смесью для заделки свища в случае его образования в процессе литья в литейной форме.
После установки сварочного оборудования производится подогрев концов рельсов. Для этого на газовых редукторах необходимо установить давление пропана 1–1,2 атм (0,1–0,12 МПа) и давление кислорода 4,5–5,0 атм (0,45–0,5 МПа), потом зажечь газовую горелку, отрегулировать пламя до нормального горения и установить газовую горелку на вспомогательную стойку (рис. 38). Для нагрева концов рельсов газовая горелка с нормально отрегулированным пламенем перемещается в зону сварки на комбинированную стойку (рис. 39).
Рис. 38. Подготовка газовой горелки для подогрева концов рельсов: 1 — газовая горелка; 2 — стойка вспомогательная;
3 — манометры на баллонах с пропаном и кислородом
40