
- •Содержание
- •Список использованных источников
- •Список использованных источнико
- •Методики оценки технического состояния искусственных сооружений на автомобильных дорогах
- •Результаты мониторинга технического состояния металлических мостов на Забайкальской железной дороге
- •Пешеходный мост из композиционных материалов
- •Сооружение тоннелей мелкого заложения в условиях сложившейся инфраструктуры
- •Проектирование станции метро «Молодежная»
- •Опыт эксплуатации скреплений КН на Зап.-Сиб. ж.д.
- •Эксплуатация в прямых участках пути
- •Эксплуатация в кривых участках пути
- •Список использованных источнико
- •Перспективы развития стрелочных переводов
- •Список использованных источников
- •Список использованных источников
- •Результаты испытаний САУ на базе ГНСС (ГЛОНАСС/GPS) при проведении модернизации на ЗСЖД
- •Комплекты прокладок для стрелочных переводов
- •О геометрических формах частиц балласта
- •Совершенствование геометрических параметров упругих прутковых клемм
- •Армирование грунтов методом раскатки скважин
- •Работа конструкций в особых условиях
- •Высокопрочные шлакощелочные бетоны
- •Перевозка сыпучих грузов в мягких контейнерах
- •Список использованных источников
- •Список использованных источников
- •Выводы
- •Тепловой расчет салона пассажирского вагона
- •Внутреннее оборудование
- •Научное издание
ла, усилив его опорной кареткой, установленной в специальных направляющих.
Учитывая большой потенциал рабочего оборудования машины КПСМ, в 2011 г. принято решение о разработке эскизного проекта коммунальной пневмоуборочной универсальной машины (КПУМ), позволяющей производить уборку, как снега, так и засорителя, грязи и пыли.
Данная машина может использоваться для уборки проезжей части улиц и прилегающих зон круглый год.
Машина универсального типа требует как установки емкости с разгрузочными устройствами для осаждения пыли, так и перегрузочного транспортера. Наличие герметичной вакуумной емкости позволяет применить наиболее эффективную, с позиции энергозатрат, пневмоустановку всасывающего типа.
Разгрузку основной массы снега и засорителя предполагается производить непрерывно из приемного бункера с помощью роторного шлюзового устройства, а выгрузку пыли и мелкой фракции засорителя из фильтровальных камер— периодически через подвижные люки.
Для перегрузки собранного груза в транспортное средство используется конвейер.
Предполагаемая производительность машины составит 200 т/ч, как по снегу, так и по засорителю.
Выводы
Применение пневмотранспорта на машинах для уборки снега и засорителей позволяет получить большую универсальность по сравнению с другими машинами, что приводит к сокращению номенклатуры техники, применяемой для очистки проезжей части и прилегающих зон и к снижению затрат на производство работ.
Универсальность машин позволяет исключить их простои в зимний период при отсутствии снегопадов и метелей(могут быть использованы для уборки снега, скученного на прилегающих к дорогам зонах), а в летний период машины с вакуумной емкостью могут использоваться для уборки засорителя, грязи и пыли.
357
К вопросу расчета мощности привода винтового конвейера с червячным редуктором
А.В. Зайцев
Сибирский государственный университет путей сообщения, Новосибирск
Винтовые горизонтальные конвейеры получили широкое распространение в строительных, дорожных и подъемно— транспортных машинах. При проектировании винтовых горизонтальных конвейеров проектировщик решает две основные задачи:
1.Определение потребной мощности на валу винта.
2.Выбор типа привода.
При решении первой задачи необходимо выбрать метод расчета потребной мощности на валу винтового конвейера. Существует достаточно много методов расчета потребной мощности винтовых конвейеров, которые при проектировании целесообразно сравнить друг с другом и выбрать оптимальный.
При решении второй задачи, необходимо выбрать схему привода исходя из назначения, конкретных условий эксплуатации, режима работы конвейера и, после анализа достоинств и недостатков различных типов редукторов проектировщик может выбрать привод винтового горизонтального конвейера с червячным редуктором. Червячные редукторы широко применяются не только в приводах винтовых конвейеров, но и в механизмах и узлах других машин и механизмов. В настоящее время специализированные предприятия России ежегодно изготавливают около 460 тыс. червячных редукторов общего назначения. Кроме того, промышленность выпускает свыше 50 тыс. специальных червячных редукторов и несколько десятков тысяч специализированных червячных пар. Как видно, они получили широкое распространение, в последние 20 лет на них приходилось от 42 % до 49 % объема выпуска редукторов общего назначения. Несмотря на то, что предприятия-изготовители изменяют структуру выпуска редукторов общего назначения, уменьшив долю червячных до30 %, общий объем червячных и комбинированных, включающих червячные передачи редукторов и мотор — редукторов планируется увеличить, доведя их годовой выпуск до 490–520 тыс. Среди зарубежных изготовителей примером может служить завод в Фор-
358
миджине итальянской компании Motovario Group, где две полностью автоматизированные и роботизированные линии выпускают 7000 червячных редукторов в сутки. Поэтому, в связи с постоянно увеличивающимся мировым объемом производства червячных передач и редукторов, перед проектировщиком остро стоит вопрос о критериях, ориентируясь на которые следует выбрать тип редуктора.
Анализ методов, проведенный, на примере обычного винтового горизонтального конвейера показал, что более точным методом расчета потребной мощности и вращающего момента на валу винта винтового горизонтального конвейера является метод, учитывающий все виды сопротивлений, возникающих при транспортировании сыпучего груза.
КПД редуктора является одним из комплексных технико-
экономических критериев, по которому выбирается тип редуктора. При выборе типа зубчатого редуктора и проектировании новых механизмов конструктор — машиностроитель оказывается в затруднительном положении. В научно — технической литературе даются не согласованные между собой методы расчета КПД.
Точный расчет потерь в редукторе часто представляет большие затруднения и ведет или к переоценке или, наоборот, к недооценке КПД. Использование завышенных значений вызывает
ошибки при выборе типа редуктора и мощности электродвигателей, что приводит к их перегреву и преждевременному выходу из строя. По ошибочным значениям КПД составляются заниженные заявки на электроэнергию, перерасходуются выделенные лимиты, не подтверждаются расчеты экономической эффективности.
Выводы:
1.При анализе результатов, общепринятых методов расчета потребной мощности винтовых горизонтальных конвейеров выявляются достаточно высокие различия.
2.В каталогах заводов — изготовителей червячных редукторов, как правило, указываются завышенные значения коэффициентов полезного действия.
3.Расчетное значение КПД hp = 0,5310 червячного цилин-
дрического редуктора Ч-100-50-52-2-ЦТ2 — В, определенное с
359
учетом всех видов потерь на30,5 % ниже, чем значение, указанное в каталоге изготовителя = 0,77
В заключение можно отметить, что результаты определения КПД червячных редукторов по методу, учитывающему все виды потерь, значительно ниже значений, приводимых в каталогах изготовителей, что дает повод к дальнейшим исследованиям в области расчетно-экспериментальных методов определения коэффициента полезного действия червячных передач.
Оптимизация проектных технологических решений модернизации предприятий по ремонту подвижного состава методами имитационного моделирования
В.А. Смирнов
Омский государственный университет путей сообщения, Омск
Среди первоочередных задач развития производственного комплекса компании ОАО «РЖД» важную роль играет модернизация и реконструкция предприятий по ремонту подвижного состава. Разработка вариантов технологического проекта модернизации затрагивает все основные компоненты будущей производственной системы, такие как оборудование, транспорт, кадры, ресурсы.
Решение задачи выбора рациональных параметров экспертным или аналитическим методом с достаточной степенью точности не представляется возможным. Одним из наиболее эффективных методов анализа проектных решений является имитационное математическое моделирование, позволяющее получить данные о динамическом поведении технологической системы еще до фактического ее запуска в эксплуатацию.
Современное предприятие по ремонту подвижного состава железнодорожного транспорта представляет собой сложную производственную систему, содержащую подсистемы взаимосвязанных элементов: технологическое оборудование, транспорт, накопители и т.д. Использование традиционных подходов, например, основанных на теории массового обслуживания или теории графов, не всегда обеспечивает требуемую точность результатов моделирования.
360
В качестве альтернативного решения предлагается использование ориентированных паттерновых сетей. Основным понятием теории паттернов является понятие абстрактной образующей (паттернового модуля) и неотделимых от нее связей. Паттерновые сети строятся из образующих, путем попарного объединения связей различных образующих в связки. Множество всех образующих называется составом сети, а множество всех связок— структурой.
Множество G образующих сети конечно и образующие -за нумерованы. Каждая образующая g Î G полностью определяется вектором своих признаков:
a(g )= a(i, gi1 |
,..., gil |
,biin1 |
,...,bimin ,biout1 |
,...,birout ), |
|
i |
|
i |
i |
где i — порядковый номер образующей; yik , k = 1,...,li — атрибу-
ты образующей; mi |
|
и ri — количество входящих и исходящих |
|||
связей; bin , k =1,...,m |
и bout |
, k =1,...,r — показатели входных и |
|||
ik |
i |
ik |
i |
|
|
выходных связей образующей. |
|
|
|||
Атрибуты и показатели связей образующих являются пере- |
|||||
менными величинами. Множества D , |
Din |
и Dout допустимых |
|||
|
|
|
ik |
ik |
ik |
значений переменных gik ,binik иboutik определяют информационное содержимое образующей и называются доменами соответствующих переменных.
Для технологической сети образующие являются технологическими операциями. Количество входящих и исходящих связей образующей определяется типом и взаимосвязями технологической операции. Домены атрибутов образующих содержат возможные значения параметров технологических операций, условия их выполнения и другую необходимую информацию. Технологические позиции и участки представляют собой стандартные фрагменты общей сети — регулярные конфигурации, составленные из комбинаций паттерновых модулей, связи между которыми полностью определяются технологическим процессом ремонта.
Паттерновая сеть является средой для дискретного динамического моделирования технологических процессов ремонта подвижного состава. Работа модели основывается на принципе моделирования особых состояний системы— характерных собы-
361
тий, наступающих в момент возникновения заявки на транспортное обслуживание при завершении технологической операции. Событие служит условием соединения связок паттерновой сети.
По результатам имитационного моделирования оцениваются параметры и показатели, отражающие работу технологической системы: производительность, время ремонта, время работы технологического и подъемно-транспортного оборудования в течение рабочей смены, длина очереди и время ожидания транспортного обслуживания, количество деталей в накопителях.
Предлагаемая методология позволяет моделировать работу предприятий по ремонту подвижного состава с учетом их индивидуальных особенностей, при этом модульный принцип построения обеспечивает преемственность алгоритмической и информационной структуры моделей отдельных элементов, что позволяет значительно сократить время и трудоемкость их создания.
Оценка проектных решений производится по критериям технологической энергоемкости производства, совокупной длине транспортных маршрутов, времени завершения полного цикла ремонта, необходимому объему оборотного фонда ремонтируемых изделий и комплектующих.
Кроме оценки производственных параметров модернизируемых предприятий имитационное моделирование с использованием паттерновых сетей обеспечивает эффективное решение комплекса оптимизационных задач по выявлению источников производственных потерь, рациональному размещению цехов и оборудования, планированию программы ремонта и графиков производственного процесса.
Бортовые диагностические системы строительно-дорожных машин
А.А. Игумнов
Сибирский государственный университет путей сообщения, Новосибирск
Осуществление транспортной стратегии Российской Федерации предполагает крупномасштабное строительство опорнотранспортных сетей, требующих использования различных видов техники, в том числе парков строительно-дорожных машин. Уве-
362
личение количества машин обуславливает необходимость поддержания исправного состояния каждой единицы техники.
Для обеспечения эффективной работы и исключения риска внезапных отказов необходим постоянный мониторинг технического состояния узлов и агрегатов в процессе эксплуатации стро- ительно-дорожных машин вне зависимости от требований технической документации.
Простои в случае внезапного отказа строительно-дорожных машин требуют больших внеплановых затрат, поэтому экономически выгодно выполнять диагностирование в процессе работы -ма шины круглосуточно. Преимуществами бортовых диагностических систем является то, что они могут выявлять предотказное состояние машины в режиме реального времени. Оснащение машин диагностическими системами позволит увеличить производительность и показатели надежности: безотказность, долговечность.
Для обеспечения мониторинга технического состояния в процессе работы необходимо обеспечить соединение установленных на машине диагностических систем с обслуживающим персоналом, что производится при помощи беспроводных средств связи. Это поможет своевременно проводить техническое обслуживание, тем самым предупреждая незапланированный выход машины из строя, а в случае отказа— подбирать необходимые запасные части перед поездкой к неисправной машине.
Современные системы мониторинга строительно-дорожных машин проходят этап совершенствования, на котором для каждой машины не только увеличивается количество диагностируемых параметров, но и проводится комплексный анализ показаний анализаторов работы. Поэтому задачей дальнейшего исследования является оптимизация количества диагностических параметров при их минимальном количестве и максимальной информативности о техническом состоянии машины.
363
Особенности конструкции подвижного состава Алматинского метро
Ж.С. Мусаев, В.Г. Солоненко, М.Д. Габдуллин
Казахская академия транспорта и коммуникаций им. М. Тынышпаева, Алматы, Казахстан
Согласно проведенному тендеру на поставку вагонов для алматинского метро победителем была признана южнокорейская компания Ротем корпорацииHyundai. Электропоезда Алматинского метро произведены в Южной Корее на заводе компании Hyundai с учетом всех казахстанских технических требований. Вагоны спроектированы и изготовлены с расчетом не менее чем на 25-летний срок нормального использования без капитальной реконструкции, упрочнения и ремонта. Конструкция кузова вагона проверена с помощью исследования и тестирования методом конечных элементов.
Тележка Ротема разработана на основе хорошо зарекомендовавшей себя конструкции, и может выдерживать высокие осевые нагрузки, сохраняя при этом все требуемые технические характеристики. Тележка безлюлечного типа, имеет H-образную раму с пневматическими подвесками, расположенными между местом крепления корпусом вагона и тележки, и собственно рамой тележки. Тормозная система тележки фрикционного типа включает тормозной диск, установленный на оси, а также тормозные суппорты с тормозным цилиндром и тормозными колодками. Все узлы тележки были разработаны с учетом сокращения эксплуатационных расходов в течение всего срока службы изделия. Конструкция колесной пары позволит выдерживать требуемые нагрузки на оси в соответствии со стандартами EN и/или UIC.
Автоматическое сцепное устройство позволяет поезду соединяться механически и пневматически с другим поездом в автоматическом режиме. Полупостоянное сцепное устройство предназначено для обеспечения постоянного соединение железнодорожных вагонов, которые в движении образуют единое целое ,ипоэтому, требуют расцепления только в случае аварийной ситуации или для отправки в мастерскую для технического обслуживания.
364
Блок кондиционирования воздуха для обеспечения большей надежности работы системы оснащен двумя полностью герметичными спиральными компрессорами горизонтального типа и низкопрофильным воздушным кондиционером. В кабину машиниста охлажденный кондиционированный воздух поступает из пассажирского салона.
Таким образом, спроектированные с учетом требований казахстанской стороны вагоны для алматинского метро отвечают всем современным эксплуатационным требованиям, как в плане безопасности и динамики, так и в плане комфортабельности и дизайна, что подтверждено приемочными испытаниями.
Автоматизация технической подготовки производства при ремонте подвижного состава
А.В. Поздеев, Н.Ж. Кинаш
Московская железная дорога — филиал ОАО «РЖД», Москва
Анализу технического состояния подвижного состава и вопросам технической подготовки структурных единиц посвящены работы таких российских ученых как Т.К. Батюшкин, А.Т. Головатов, В.М. Лысенков, В.Н. Жданов, Б.С. Герасимов, А.Д. Шишков и др. Следует отметить, что:
1.Оценка текущего состояния структурных единиц может быть построена на базе диаграммы неисправностей отдельных единиц.
2.Существующие методы оценки технического состояния структурных единиц подвижного состава не ориентированы на информационное обеспечение автоматизированной системы технической подготовки подвижного состава.
3.Отсутствует методика объемного планирования работы корпоративной сети ремонтных предприятий для обеспечения технического состояния подвижных составов при удлинении гарантированного безаварийного пробега.
4.Недостаточно разработаны и освещены вопросы информационного обеспечения процесса технической подготовкипо движного состава и отсутствует информационная модель структурной единицы подвижного состава.
Исходя из вышеизложенного, основные цели статьи формулируются следующим образом:
365
–разработать математическую модель надежности структурных единиц подвижного состава;
–разработать надежностную модель подвижного состава при составлении поездов;
–сформировать информационную модель структурной единицы подвижного состава для автоматизации технической подготовки подвижного состава с учетом схемы сборки и разборки структурных единиц при техническом обслуживании.
Оценка технического состояния подвижного состава строится на том предположении, что процесс эксплуатации с учетом всех действующих факторов носит случайный характер, и, как следствие, исследование технического состояния должно базироваться на теории математической статистики.
Расчет вероятности отказа каждой структурной единицы подвижного состава можно построить при помощи диаграммы (графа) неисправностей. Диаграмма неисправностей структурной единицы должна быть построена на основе наличия диагностирующих средств (в отличие от схемы их узловой сборки). Используя это положение, структурную единицу подвижного состава можно представить как множество узлов, подузлов и деталей, т.е. в виде многоярусного графа.
Для планирования работы безопасного движения подвижного состава и ремонтно-профилактических работ, как на пути, так и в депо, достаточно использовать математическое ожидание случайного времени между отказами без определения доверительного интервала этой величины с заданной гарантией. В силу этого обстоятельства в качестве закона распределения вероятности отказа или безотказной работы можно принять экспоненциальный закон распределения. Поэтому для описания вероятностного поведения безотказного движения подвижного состава достаточно накапливать статистику по интервалам безотказной работы -от дельных деталей, подузлов, узлов и структурных единиц, поскольку интенсивность отказа каждой рассматриваемой единицы определяется как обратная величина математического ожидания.
Имея соответствующую статистику по подузлам, рассчитываются математические ожидания безотказной работы узла и структурной единицы подвижного состава.
366
Вероятность безотказной работы структурной единицы -по движного состава к моменту времени(t + Dt) рассчитывается на основе диаграммы неисправностей, которая задается в виде треугольной матрицы.
Если считать, что вероятности нахождения системы во всех состояниях 3-го уровня диагностирования известны(т.е. известны весовые коэффициенты вершин третьего уровня), то вероятность нахождения в исправном состоянии структурной единицы подвижного состава будет определяться по следующей формуле:
N I
P(Г ) = åa10j PIj , j =1
где: PIj — вероятность j -й вершины I уровня; PkII — веро-
ятность k -й вершины II уровня; PlIII — вероятность l-й вершины III уровня; a10j , akjI , alkII — соответствующие элементы матрицы
переходов.
Коэффициенты матрицы переходов определяются на основе статистики в процессе эксплуатации структурной единицы по количеству переходов из одного состояния в другое.
Таким образом, при помощи предложенного подхода построена надежностная модель структурной единицы, а также всего подвижного состава. На основе предложенной модели возможно построение мониторинговой системы формирования необходимого технического состояния подвижного состава и создание реальной базы для эффективного планирования работы сети депо и ремонтных предприятий дорог.
Технология автоматизированной подготовки производства ремонта грузовых вагонов
А.В. Поздеев, Н.Ж. Кинаш, Д.А. Кулаков
Московская железная дорога — филиал ОАО «РЖД», Москва
В настоящее время качество производства деповского ремонта грузовых вагонов остается насущной проблемой. Часть вагонов после прохождения деповского ремонта не отрабатывает по-
367
ложенного срока и преждевременно выходит из строя. Чаще всего поломки случаются в буксовом узле, автотормозном оборудовании. Предпринимаемые на предприятиях Вагоноремонтных компаний — дочерних акционерных обществах ОАО«РЖД» меры по укреплению контроля за качеством ремонта, несмотря на несомненный положительный эффект, не снимают полностью существующей проблемы — обеспечения надлежащего качества ремонта грузовых вагонов и оптимизации целевого состояния деятельности депо в показателях «себестоимость – качество».
В целях повышения эффективности управления деятельностью вагоноремонтного депо и роста качества ремонта грузовых вагонов разработана «Автоматизированная система управления технологическим процессом ремонта грузовых вагонов(АСУТОРО В)».
Указанная система позволяет добиться решения поставленных задач за счет:
–оптимизации процесса оперативного планирования;
–паспортизации вагона и его составных узлов;
–планирования материальных ресурсов;
–пооперационного контроля технологического цикла ремонта;
–контроля списания материально-технических ресурсов на объекты ремонта;
–контроля комплектации подвижного состава и параметров его узлов;
–формирование и ведение отчетных форм;
–расчета себестоимости ремонта грузовых вагонов. Функциональность автоматизированной системы управления
технологическим процессом ремонта грузовых вагонов реализована на базе модулей ERP-системы SAP R/3.
В рамках настоящей статьи рассмотрен один из компонентов функциональности внедренной автоматизированной системы управления технологическим процессом ремонта вагоноремонтного депо пооперационный контроль исполнения технологического процесса ремонта грузовых вагонов.
Контроль исполнения технологического процесса ремонта подвижного состава реализован путем пооперационного - кон троля следующих технологических операций ремонта подвижного состава и его составных частей:
368
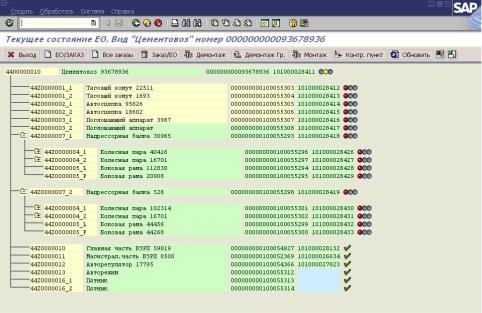
–приемка в ремонт;
–дефектация, комплектование и передача в ремонт;
–техническое диагностирование;
–ремонт и доработка;
–сборка, монтаж;
–испытания;
–выдача из ремонта.
Указанная последовательность операций определена существующими технологическими картами на ремонт вагонов и каждого из его узлов(автосцепка, колесная пара, авторегулятор и т.д.). Строгая последовательность ввода данных и иерархическая структура подписей «запирают» ответственных сотрудников в рамки технологического процесса и позволяют контролировать процесс ремонта с рабочих мест руководителей. Упрощается система контроля над исполнением всех регламентированных действий, что, несомненно, повышает качество ремонта. Структурная схема грузового вагона в системе АСУ-ТОРО В приведена на рис. 1 на примере вагона-цементовоза.
Рис. 1. Структурная схема грузового вагона
В рамках данной работы были реализованы рабочие места сотрудников вагоноремонтного депо(вагоно-сборочный цех, тележечный цех, ремонтно-заготовительный цех, колесно-роликовый
369