
- •Содержание
- •Список использованных источников
- •Список использованных источнико
- •Методики оценки технического состояния искусственных сооружений на автомобильных дорогах
- •Результаты мониторинга технического состояния металлических мостов на Забайкальской железной дороге
- •Пешеходный мост из композиционных материалов
- •Сооружение тоннелей мелкого заложения в условиях сложившейся инфраструктуры
- •Проектирование станции метро «Молодежная»
- •Опыт эксплуатации скреплений КН на Зап.-Сиб. ж.д.
- •Эксплуатация в прямых участках пути
- •Эксплуатация в кривых участках пути
- •Список использованных источнико
- •Перспективы развития стрелочных переводов
- •Список использованных источников
- •Список использованных источников
- •Результаты испытаний САУ на базе ГНСС (ГЛОНАСС/GPS) при проведении модернизации на ЗСЖД
- •Комплекты прокладок для стрелочных переводов
- •О геометрических формах частиц балласта
- •Совершенствование геометрических параметров упругих прутковых клемм
- •Армирование грунтов методом раскатки скважин
- •Работа конструкций в особых условиях
- •Высокопрочные шлакощелочные бетоны
- •Перевозка сыпучих грузов в мягких контейнерах
- •Список использованных источников
- •Список использованных источников
- •Выводы
- •Тепловой расчет салона пассажирского вагона
- •Внутреннее оборудование
- •Научное издание
Опыт эксплуатации скреплений КН на Зап.-Сиб. ж.д.
Д.В. Величко,
Сибирский государственный университет путей сообщения, Новосибирск
В.В. Дрокин
Западно-Сибирская дирекция инфраструктуры, Новосибирск
Современными типами промежуточными рельсовыми скреплениями в настоящее время на железных дорогах России являются — КБ-65, КН-65, ЖБР-65, АРС-4, скрепление немецкой фирмы Фоссло W-30.
На Западно-Сибирской железной дороге к 2012 г. доля новых скреплений с упругими клеммами составляют1014,2 км главных путей, из них: ЖБР-65 — 158,6 км, ЖБР-65Ш — 695,9 км, КН-65, КН-65 ШД — 100,8 км, W-30 — 45,9 км.
Путеобследовательской станцией №1 ЦП ОАО «РЖД», совместно с СГУПС с 2005 г. по 2011 г. производились наблюдения за опытными участками пути, с уложенными скреплениями КН-65 и контрольными — со скреплениями КБ-65 участками пути с близкими условиями эксплуатации в прямых и кривых участках пути.
Эксплуатация в прямых участках пути
Опытный участок со скреплением КН-65 находился на Среднесибирской магистрали, перегон Краснозерское – Зубково, 453– 454 км, I путь, план — прямая, профиль — до 6,0 ‰.
Контрольный участок со скреплением КБ-65 находился на том же направлении, перегон Чебачий–Зубково, 387–388 км, I путь, план – прямая, профиль – площадка.
Эксплуатационная характеристика обоих сравниваемых участков: классификация пути — 1Б2, грузонапряженность 95 млн т км бр./км в год, скорость движения поездов— 100/80 км/ч, осевая нагрузка — 217 кН/ось. Конструкции пути: бесстыковая, рельсы Р65, железобетонные шпалы, эпюра — 1840 шт./км, щебеночный балласт.
Результаты наблюдений за работой скреплений выявили значительные технико-экономические эффекты в эксплуатации КН-65. Интенсивность ослабления затяжки болтов скрепления КН меньше, чем интенсивность скрепления КБ в1,5–2 раза, что определяет
119
снижение затрат на текущее содержание и увеличение периодичности выполняемых работ. Уровень затяжки болтов скрепления КН превышает КБ в среднем на 30 %. Угон рельсовой плетей отсутствует на обоих участках. Эксплуатация скреплений КН-65 способствует снижению трудозатрат на содержание пути в среднем в 2 раза, снижению уровня балловой оценки — в 1,5–2,5 раза, в среднем до 10 баллов. На опытном участке со скреплениями КН-65 выхода дефектных элементов нет.
На контрольном участке скрепления КБ-65 в 2007 г. была произведена замена скреплений до 1 % на протяжении опытного участка. После наработки тоннажа 525в млн т, состояние подрельсовой прокладки — неудовлетворительное (обрыв реборд, микротрещины, смятия, пригары). В 2006–2007 гг. произведена замена 26 % подрельсовых и 13 % нашпальных прокладок. В 2010 г. подрельсовые прокладки были полностью заменены на прокладки повышенной долговечности.
Динамика изменения количества неисправностей на участках укладки скреплений КН и КБ(43 км) — среднее количество неисправностей пути: КН — 0,98 шт./км, КБ — 1,97 шт./км. Это определяет существенное снижение объемов работ по текущему содержанию пути, что с рядом других достоинств этого скрепления значительно уменьшает затраты на эксплуатацию. В однотипных условиях эксплуатации среднее число дефектных рельсов на участках с КБ-65 составляет — 1,73 шт./км, на участках с КН-65 — 0,8 шт./км.
Эксплуатация в кривых участках пути
Опытный участок со скреплением -65КН находился на направлении Новосибирск–Барнаул, II путь, перегон Искитим– Ложок, 65–66 км, в кривой R = 623 м; профиль — 1,5–9 ‰. Классификация пути — 1В2. Установленная скорость движения поездов — 100/80 км/ч, осевая нагрузка — 162 кН/ось. Конструкция пути: бесстыковая, плети длиной 449 м, рельсы Р75, железобетонные шпалы, эпюра — 2000 шт./км, щебеночный балласт.
Контрольный участок со скреплением -КБ65 находился на направлении Инская – Сокур, II путь, перегон Издревая – Жеребцово, 9–10 км, в кривой R = 590 м; профиль — 8,1 ‰. Классификация пути — 2Б4. Установленная скорость движения поездов— 70/60 км/ч, осевая нагрузка — 161 кН/ось. Конструкция пути: бес-
120
стыковая, плети длиной с перегон, рельсы Р65, железобетонные шпалы, эпюра — 2000 шт./км; щебеночный балласт.
Путь на опытном участке находился в хорошем состоянии, угона рельсовых плетей не наблюдалось, отказов металлических элементов скреплений КН-65 не было. Нашпальные прокладки армированные волокнами лавсана («РТИ» г. Барнаул) находились в хорошем состоянии, отказов не было. Подрельсовые прокладки («АРТИ» г. Тамбов) имели смятия в средней части 2-3 мм, разрывы с выдавливанием из-под рельса, к концу 2007 г. и требовали замены до 5 %. На участке со скреплениями КН-65, пропустив 211,4 млн т груза, подрельсовые прокладки имели общее неудовлетворительное состояние, поэтому в 2009 г. они были заменены на прокладки повышенной долговечности. В 2008 г. в кривом участке со скреплениями КБ-65 были уложены подрельсовые прокладки повышенной долговечности. На конец 2010 г. состояние подрельсовых и нашпальных прокладок на обоих участках — хорошее.
Сравнительные измерения ширины рельсовой колеи в прямой и кривых участках пути со скреплениями КН -65: в прямой — 1523–1525 мм, износ рельсов отсутствует; в кривой R = 590 м — с учетом бокового износа (4–5 мм) — 1522–1527 мм; в кривой R = = 623 м — с учетом бокового износа (7–10 мм) — 1530–1534 мм. Эксплуатация скреплений КН-65 в кривых участках пути способствует снижению трудозатрат на содержание пути в среднем в 2 раза, снижению уровня балловой оценки — в 1,5–2,5 раза, в среднем до 10 баллов.
На основании анализа работы скрепления КН-65 на ЗападноСибирской железной дороге, можно сделать вывод, что скрепление КН зарекомендовало себя как стабильная, технологичная и надежная конструкция в эксплуатации не только в прямых но и в кривых участках пути.
121
Современный уровень геодезического обеспечения капитального ремонта,
модернизации и управления техническим состоянием железных дорог
В.В. Щербаков
Сибирский государственный университет путей сообщения, Новосибирск
Уровень и структура геодезического обеспечения капитального ремонта (модернизации) возрастает с повышением требований к геометрическим параметрам рельсовой колеи. Поэтому развитие высокоскоростного движения, повышение качества ремонта(модернизации) железных дорог связано с развитием средств и методов геодезического обеспечения железных дорог. Геодезические работы трудоемки и при больших объемах работ, например натурных проверках плана и профиля станционных путей, которые выполняются один раз в 10 лет, затраты по ОАО «РЖД» составляют около 1 млрд р. При этом натурные проверки не самые затратные статьи расходов на инженерно-геодезические работы, например в сравнении с инженерно-геодезическими изысканиями для модернизации (капитального ремонта) пути. Так стоимость проектноизыскательских работ, включая инженерно-геодезические изыскания, составляет около 500 тыс. р. за один километр.
Учитывая приведенные данные, а также исходя из временных ограничений и других факторов, основным направлением развития уровня геодезического обеспечения инфраструктуры железных дорог связано с повышением производительности и качества работ. Одним из наиболее эффективных способов повышения производительности работ является автоматизация, особенно наиболее трудоемких процессов, выполняемых в больших объемах. Автоматизация геодезических измерений, включая железные дороги, всегда актуальна и многое в данном направлении сделано.
В настоящее время большое значение разработчиками и производителями геодезических приборов уделяется автоматизации, так созданы роботы-тахеометры, лазерные сканеры, различного типа дальномеры. При этом особое значение в развитии инженерной геодезии получили приборы и системы, созданные на базе Глобальных навигационных спутниковых систем(ГНСС) ГЛО-
122
НАСС/GPS. Геодезисты получили принципиально новые средства измерений, имеющие очевидные преимущества. Одним из таких преимуществ ГНСС является полная автоматизация измерений, включая возможность позиционирования в реальном времени. Новые функциональные возможности обеспечили развитие принципиально нового направления в инженерной геодезии— создание систем автоматизированного управления(САУ) строительной техникой. САУ в отличии от традиционных методов, связанных с разбивочными работами, операционным контролем строительно-монтажных работ позволяет в3–5 раз повысить производительность, минимизировать отрицательное влияние человеческого фактора, сократить затраты более чем в 2 раза.
Ведущие мировые фирмы, разрабатывающие геодезическое оборудование Leiсa, Topcоn, Trimble и другие создали линейку измерительных систем для автоматизированного управления строительной техникой. В настоящее время САУ на базе ГНСС оборудованы бульдозеры, автогрейдера, экскаваторы, асфальтоукладчики и другие типы машин.
СГУПС (НИЛ «Диагностики дорожных одежд и земляного полотна») на базе опыта полученного при создании СТК-РП, АПК «Профиль», мобильного лазерного сканера «Сканпуть», ПТ «Волна», а также опыта создания цифровых моделей пути (ЦМП), электронных карт и в целом опыта ежегодного выполнения около 1000 км. различного вида инженерно-геодезических изысканий с применением ГНСС (ГЛОНАСС/GPS) в 2011–2012 гг. успешно выполнил НИОКР по созданиюCАУ для строительной железнодорожной техники (ЩОМ, RM. ЭЛБ). Разработанные и изготовленные в СГУПС САУ (ЩОМ, ЭЛБ, RM) для ЗСДРП, в настоящее время находятся в опытной эксплуатации.
Кроме того, в НИЛ «Диагностики дорожных одежд и земляного полотна» на базе ГНСС и ГИС разработали технологию создания масштабных планов и продольных профилей, измерительный комплекс для высокоточных измерений рельсовых плетей, мониторинга железных дорог.
Таким образом, ГНСС (ГЛОНАСС/GPS) существенно изменили уровень инженерно-геодезических работ при обеспечении развития инфраструктуры железных дорог. Дальнейшее развитие геодезического обеспечения также связано с расширением при-
123
менения ГНСС. Учитывая, что в ближайшие 5лет будут развернуты Китайская и Европейская ГНСС, функциональные возможности и соответственно область применения ГНСС на железных дорогах значительно расширится, а стоимость приборов и оборудования снизиться.
Перспективы развития производства железобетонных шпал
Д.В. Величко
Сибирский государственный университет путей сообщения, Новосибирск
Н.Н. Горбунов
Горновский завод «Спецжелезобетон», Горный
Основная деятельность ОАО«БетЭлТранс» — производство железобетонных шпал и брусьев для железных дорог общего пользования. Обществом не только полностью выполнен корпоративный заказ нашего главного заказчика— ОАО «РЖД», но и установлен рекорд производства шпальной продукции— 9350,5 млн железобетонных шпал (в том числе для ОАО «РЖД» 8994 тыс. шт., или 96 % от выпуска) и 5571 комплект железобетонного бруса (в том числе для ОАО «РЖД» 4778 комплектов, или 86 % от выпуска).
На 2012 г. корпоративный заказ ОАО «РЖД» составляет — более 10,5 млн шпал.
В ОАО «БэтЭлТранс» (БЭТ) входит 10 филиалов по всей стране, в том числе и Горновский завод.
Основными видами деятельности БЭТ являются производство и реализация (табл.):
–железобетонных шпал Ш1, Ш3, Ш3-Д, ШС-АРС, Ш5-ДФ («Vossloh») и их модификаций;
–комплектов железобетонных брусьев стрелочных переводов;
–мостовых безбалластных плит;
–общестроительных железобетонных изделий и товарного бетона;
–элементов рельсовых скреплений: болтов закладных с гайкой, болтов клеммных с гайкой, клеммы ЖБР, скобы ЖБР.
На территории Российской Федерации на данный момент сертифицированы и используются только пропитанные деревянные или железобетонные шпалы, следовательно реальным конкурен-
124
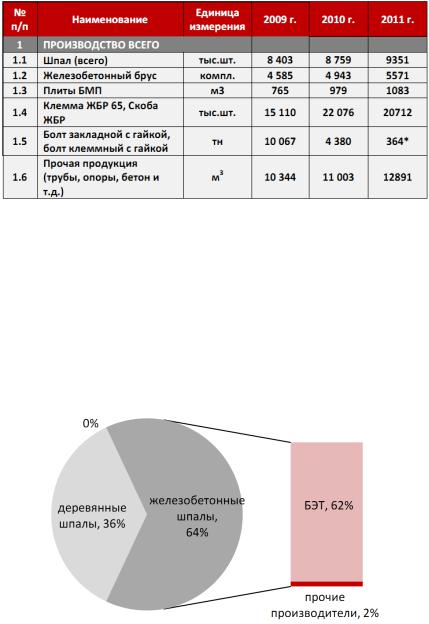
том для железобетонных шпал являются их деревянные аналоги. Стоит отметить, что структура рынка неуклонно изменяется в сторону снижения доли деревянных пропитанных шпал в пользу железобетонных, поскольку характеристики последних значительно превосходят характеристики деревянных шпал.
Таблица
Тенденции роста производство
Основным рынком присутствия продукции общества является рынок шпал (оценивается порядка 14 млн шт. в год), на котором «БетЭлТранс» занимает около 62 % (рис. 1).
Загрузка производственных мощностей за 2011 г. по железобетонным шпалам составляет 97,7 %, по железобетонным брусьям для стрелочных переводов — 111,4 %, по плитам БМП — 15 %. Производство болтов закладных и клеммных с мая2011 года прекращено.
Рис. 1. Доля рынка ОАО «БетЭлТранс»
В связи с переходом при производстве капитальных видов ремонта пути на упругие виды скреплений(рис. 2), изменилась номенклатура шпал в общем объеме поставки. Доминирующее ранее
125
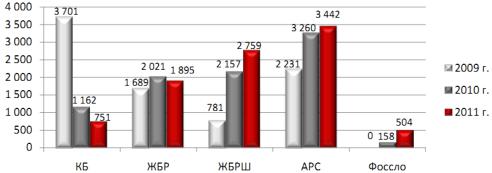
скрепление КБ, уменьшилось в объемах укладки, при этом увеличился объем укладки железобетонных шпал с упругими видами скреплений — АРС, ЖБР и ЖБР-Ш. С целью дальнейшего перевода железнодорожного пути на упругие виды скреплений в 2011 г. БЭТом:
–освоено серийное производство шпал мостовых, челноковых со скреплением АРС и шпал для кривых участков пути радиусом менее 300 м со скреплением АРС и ЖБР-65Ш;
–выпущена установочная партия шпал Ш5-ДФ под рельсовое скрепление типа «Vossloh» в количестве 504,3 тыс. шпал.
Рис. 2. Структура производства шпал по типу скреплений, тыс. шт.
В2012 г. планом научно-технического развития «БетЭлТранс» предусмотрено освоение производства шпал со скреплением фирмы «Pandrol», мостовых и челноковых со скреплением ЖБР-65Ш,
ЖБР-65.
Для удовлетворения потребности ОАО«РЖД» в железобетонных шпалах к 2015 г. необходимо увеличить существующие мощности заводов по производству железобетонных шпал с 9,57 млн до 11 млн в год, при этом необходимо приобрести и смонтировать дополнительно не менее 4 технологических линий производительностью 500 тыс. шпал в год каждая.
В2012–2013 гг. запланировано приобретение двух автоматизированных технологических линий производительность по500 тыс. железобетонных шпал в год. Изготовление шпал на данных технологических линиях предусмотрено в четырехместных формах с армированием стержневой арматурой.
126
Технология модернизации пути
с использованием ГНСС (ГЛОНАСС/GPS)
А.С. Пикалов
Западно-Сибирская дирекция по ремонту пути, Новосибирск
Реконструкция (модернизация) и капитальный ремонт железнодорожного пути направлены на повышение прочности, несущей способности, стабильности, долговечности и других показателей надежности как железнодорожного пути в целом, так и его составных частей и элементов, обеспечивающих продление продолжительности жизненного цикла, сокращение трудоемкости и стоимости технического обслуживания пути и получение экономического эффекта при его эксплуатации.
Безусловно, одним из ключевых моментов выполнения -ре конструкции (модернизации) и ремонтов железнодорожного пути является реализация проектных решений, в том числе постановка пути в проектное положение.
В настоящее время постановка пути в проектное положение выполняется с использованием проектных данных в относительных величинах, как правило, это расстояние между осями проектируемого и соседнего пути, превышение относительно исходной точки.
Методика постановки пути в проектное положение заключается в расчете сдвижек и подъемок относительно соседнего пути и с использованием специальной рейки с делениями для определения фактического положения и сдвижки пути на расчетную величину. Данная методика проста в реализации и организации работ и поэтому является наиболее распространенной в настоящее время в ОАО «РЖД». Недостатки данной методики и технологии поста-
новки пути в проектное положение давно известны и являются проблемой, напрямую связанной с использованием относительных методов выправки пути.
Внедрение спутниковых технологий, в том числе запуск национальной системы ГЛОНАСС, дает широкие возможности для решения инженерных задач с высокой точностью и производительностью. Важно отметить, что ошибочно будет рассматривать лишь только один из этапов работ (к примеру, выправку пути) для достижения проектных параметров пути после ремонта. Необходимо рассматривать процесс производства работ по реконструкции и ре-
127
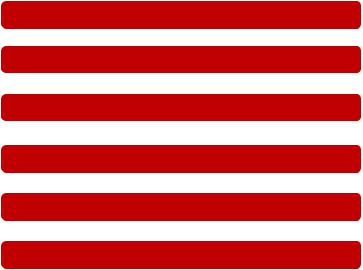
монтам пути в комплексе. Так без достижения проектных отметок по вырезке, в связи с необходимостью обеспечить нормативную толщину щебеночного балласта под шпалой не возможно будет достигнуть проектных отметок при выправке пути.
Особенностью данной технологии является принцип сохранения существующей цепочки технологических операций без изменения их последовательности, реализация происходит путем внедрения на определенных этапах техники и технологий, позволяющих точно контролировать исполнение проектных решений и автоматизировать производственный процесс.
Технология затрагивает всю технологическую цепочку, от стадии проектирования, до стадии сдачи пути в эксплуатацию, с использованием оборудования на основе ГНСС. Работа всех машин задействованных в технологии основана на едином принципе сравнения текущих координат заданных параметров с проектными и дальнейшим приведении существующих показателей к проектным.
Рассмотрим этапы внедрения спутникового оборудования в технологию реконструкции (модернизации) и ремонтов железнодорожного пути (рисунок).
1 этап — Проектирование и создание ЦМП
2 этап –Ведомственная экспертиза
3 этап — Переход к координатному методу кон-
4 этап — Переход на координатный метод по-
5 этап — Переход на координатный метод вы-
6 этап — Съемка пути АПК «Профиль», выдача
Рисунок. Этапы внедрения в технологию реконструкции (модернизации) и капитального ремонта пути
В целях контроля качества выполняемых работ на всех этапах технологического процесса предусмотрена программа формирования отчетных данных по работе путевых машин. Так после вырезки
128
(очистки) загрязненного балласта машиной РМ формируется отчет в графической и табличной форме. На основе таких данных будет производиться заключение о соответствии выполненных работ проектным решениям и объемах выполненных работ. Аналогичным образом формируются данные по работе машин ЭЛБ и Дуоматик.
Итогами применение данной технологии будет являться:
–переход на качественно новый уровень проектирования и выполнения путевых работ с использование ЦМП;
–увеличение производительности выполняемых работ;
–единые стандарты на всех этапах работ(проектирование- выполнение-сдача);
–контроль качества выполняемых работ в режиме«реального времени».
Применение фрактального анализа для оценки циклической прочности рельсов
А.К. Остапчук
Курганский институт железнодорожного транспорта филиал УрГУПС, Курган
Самое устойчивое положение на рынке перевозок занимает железная дорога. На первый план выходит экономическое поддержание инфраструктуры при оптимальных затратах на техническое содержание ее компонентов. Наиболее важным компонентом с нашей точки зрения является верхнее строение пути. Основным элементом верхнего строения пути являются рельсы в которых возникают многократно повторяющиеся напряжения, приводящие к их износу и возникновению усталостных явлений. Усталостью называется процесс постепенного накопления - по вреждений материала под действием переменных напряжений, приводящих к изменению свойств, образованию трещин, их развитию и разрушении. Процесс усталостного разрушения заключается в появлении, распространении и росте трещин с последующим выходом из строя узла или детали. Современный путь испытывает высокие нагрузки различных видов. Скорость движения пассажирских поездов достигает300 км/ч, грузовых при больших осевых нагрузках120 км/ч. Линии для тяжеловесных поездов должны выдерживать осевые нагрузки 30 т и более.
129
Главной проблемой в этом контексте является нахождение однозначного критерия потери работоспособности поверхности катания, а, следовательно, и возможности оперативно и качественно предвидеть разрушение. Также немаловажным аспектом является и то, что нужно стремиться по-возможности, более точно определить так называемый «остаточный ресурс» работы рельса. Встает проблема выработки этого самого критерия работоспособности(или потери работоспособности), который бы максимально точно отражал текущее состояние, а также зависимость данного критерия от различных факторов. В этом случае большое применение может получить методика, применяемая в нелинейной динамике, так как разрушение процесс внезапный и быстропротекающий. Одним из инструментов нелинейной динамики является фрактальный ана-
лиз, который в последнее время начинает использоваться и для оценки циклической прочности [2]. Целью данной работы является выяснение применимости данного методологического аппарата для оценки циклической прочности металлических материалов.
Моделировалось динамическое воздействие на деталь с -раз личной интенсивностью. Металлические образцы повергались действию циклических нагрузок, после чего производилась съемка поверхности образца. По полученным цифровым фотографиям поверхностей образцов вычислялись значения фрактальной размерности при помощи показателя Херста в специально разработанной компьютерной программе [1].
Были проведены расчеты для различных металлов с ОЦКрешеткой и для случая металла с ГЦК-решеткой (рис. 1, рис. 2).
Данная зависимость хорошо объясняется с точки зрения классической теории выносливости: первоначально происходит стадия циклического упрочнения, а дальше зарождение усталостной трещины, после чего материал начинает терять свою прочность и происходит распространение усталостной трещины. С точки зрения нелинейной динамики характер кривых рис. 1. и рис. 2. можно объяснить следующим образом: в начальный период нагружения происходят интенсивные изменения в структуре металла, как описано выше может происходить как упрочнение, так и потеря прочности, вследствие чего значения показателя интенсивно снижается, далее состояние системы упорядочивается, но система уже
130