
744
.pdf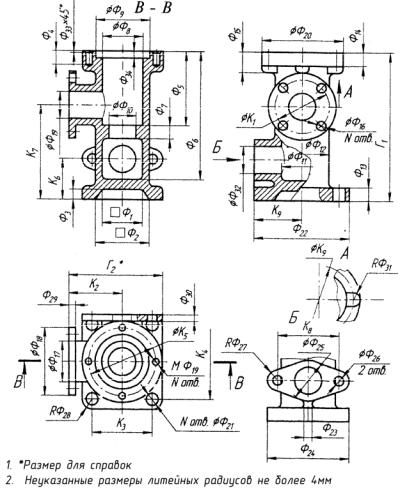
Рис. 3.13. Пример нанесения размеров на чертеже детали
Выбор системы простановки размеров относится к одному из самых сложных этапов разработки чертежа детали, что обусловлено взаимными связями при решении конструкторских и технологических задач. Основное условие, которое должно быть выполнено при этом, – наибольшая простота процесса изготовления детали при наименьшей стоимости ее изготовления.
В системе простановки размеров от конструкторских баз размеры на чертеже детали проставляются от поверхностей, которые определяют ее положение в собранной сборочной едини-
111
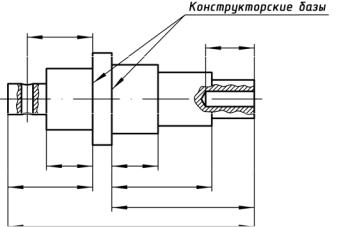
це. Причем простановку размеров не связывают с технологическими вопросами изготовления детали, и конструкторских баз может быть несколько, одна из которых будет основной, остальные – вспомогательные (рис. 3.14).
Рис. 3.14. Простановка размеров от конструкторских баз
Преимущества системы конструкторских баз: короткие размерные цепочки, повышающие точность изделия; длительный срок годности чертежа, содержащий минимум технологических требований. Недостатки: необходимость подготовки технологической документации для изготовления детали; большое число контрольно-измерительных операций, так как заказчик прини-
мает деталь по конструкторскому чертежу.
Система простановки размеров от технологических баз характеризуется тем, что все размеры на чертеже проставляют от поверхностей, определяющих положение детали (заготовки) при ее обработке (рис. 3.15). Для удобства простановки и измерения размеров введена вспомогательная база. Простановка размеров в системе технологических баз обусловлена необходимостью учета технологии изготовления детали.
Наилучшим вариантом является использование конструкторских баз в качестве технологических.
В зависимости от избранной базы для простановки размеров можно применить один из трех методов: цепной, координатный и комбинированный.
112
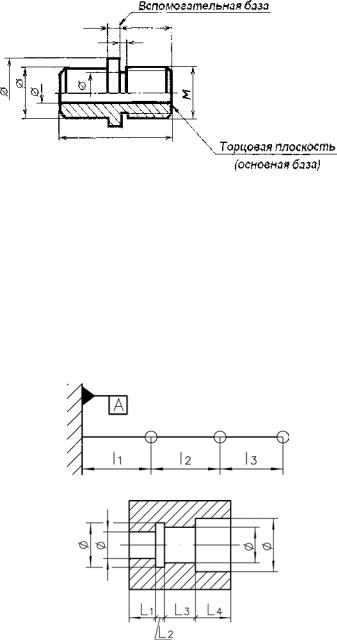
Рис. 3.15. Простановка размеров от технологических баз
Цепной метод – размеры отдельных элементов наносятся последовательно, как звенья цепи, которая не должна быть замкнутой (рис. 3.16), за исключением случаев, когда один из размеров указан как справочный – «*». Ошибки в предыдущих размерах l1 и l2 не влияют на размер l3, но ошибка в ориентации относительно базы А накапливается. Таким образом, основной недостаток цепного метода – постепенное накопление суммарной погрешности ориентации конструктивных элементов относительно базы.
а)
б)
Рис. 3.16. Цепной метод простановки размеров на чертеже
113
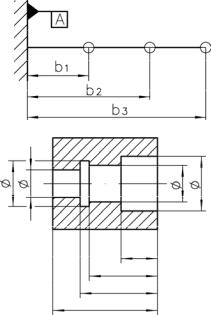
Координатный метод – в этом случае размеры являются координатами, определяющими положение конструктивных элементов детали относительно одной и той же базовой поверхности (рис. 3.17). Данный метод обеспечивает высокую точность ориентации элементов относительно базы, но в этом случае ошибка размера между элементами равна алгебраической сумме ошибок соответствующих координатных размеров.
а)
б)
Рис. 3.17. Координатныйметод простановки размеров на чертеже
Комбинированный метод представляет собой сочетание координатного и цепного методов и является наиболее предпочтительным (рис. 3.18), так как обеспечивает достаточную точность и удобство изготовления, измерения и контроля деталей.
Основные указания по рациональной простановке размеров
на рабочих чертежах деталей:
– количество размеров должно быть достаточным для изготовления и контроля детали;
114
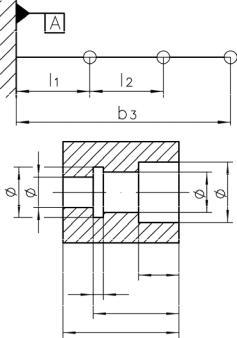
а)
б)
Рис. 3.18. Комбинированныйметод простановки размеров на чертеже
–каждый размер следует наносить на чертеже лишь один раз; не допускается также повторять размеры элемента в технических требованиях;
–цепь размеров на чертеже не должна быть замкнута. Замыкающий размер должен получаться автоматически при формообразовании детали. В качестве замыкающего выбирают наименее ответственный размер детали, так как в нем накапливаются погрешности изготовления детали по составляющим размерам;
–проставлять размеры надо так, чтобы наиболее точный размер имел наименьшую накопленную ошибку при изготовлении детали;
–на чертежах деталей, представляющих собой тела вращения, осевые размеры следует располагать под изображением;
–при наличии у деталей фасок или канавок для выхода инструмента размеры следует проставлять до буртиков или торцов
115
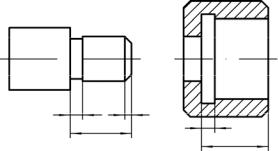
детали, так как эти элементы, как правило, обрабатываются после получения основных поверхностей (рис. 3.19);
– для всех размеров на чертежах деталей указываются предельные отклонения, правила нанесения которых установлены ГОСТ 2.307–68. Допускается не указывать предельные отклонения размеров, определяющих зоны одной и той же поверхности с различной шероховатостью, термообработкой, покрытием, накаткой и т.п.
Рис. 3.19. Нанесение размерных линий на чертеже для фасок и проточек
Предельные отклонения линейных размеров указываются на чертежах сразу после номинальных значений соответствующих размеров в виде: числовых величин (в миллиметрах); условного обозначения полей допусков; условного обозначения полей допусков с указанием справа в скобках числовых значений предельных отклонений (рис. 3.20). Предельные отклонения свободных размеров рекомендуется оговаривать в технических требованиях, например: «Допуски на свободные размеры Н14, h14». Предельные отклонения угловых размеров указываются только числовыми величинами, например, «60° + 2°».
При необходимости на чертеже указываются допуски на от-
клонения формы поверхностей (прямолинейности, плоскостно-
сти, цилиндричности, круглости, конусности) и допуски расположения (перпендикулярности, соосности, радиальных, осевых и торцевых биений и т.д.) в соответствии с ГОСТ 2.308–79 и
ГОСТ 24642–81.
116
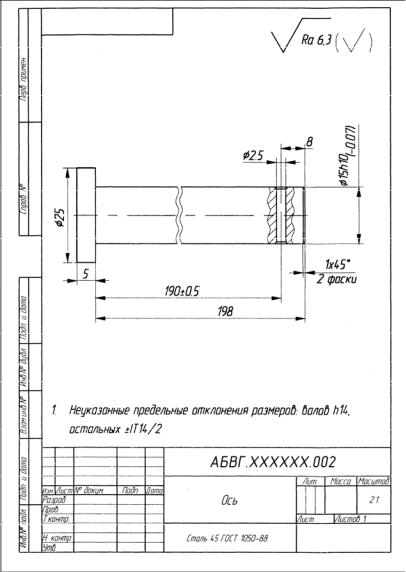
Рис. 3.20. Пример чертежа детали с указанием допусков
117
Предельные отклонения линейных и угловых размеров деталей, допуски формы и расположения поверхностей устанавли-
ваются Единой системой допусков и посадок.
3.5.4.Обозначение шероховатости поверхностей деталей
Впроцессе обработки деталей на их поверхностях появляется шероховатость – ряд чередующихся выступов и впадин малых размеров.
Шероховатость поверхности – это одна из основных характеристик детали. От величины шероховатости поверхностей деталей во многом зависят эксплуатационные показатели машин, механизмов, приборов и т.д.
Всоответствии с ГОСТ 2789–73 шероховатость поверхности измеряется в микрометрах (мкм). Для деталей из металлов она подразделяется на 14 классов. Чем выше класс шероховатости, тем меньше микронеровности и, следовательно, чище поверхность.
Для количественной оценки и обозначения на чертеже шероховатости поверхностей используются следующие параметры:
Ra – среднее арифметическое отклонение профиля в пределах базовой длины, мкм;
Rz – высота неровностей профиля по десяти точкам (пяти высшим точкам выступов и пяти низшим точкам впадин) в пределах базовой длины, мкм;
Rmax – наибольшая высота неровностей профиля в пределах базовой длины, мкм;
Sm – средний шаг неровностей по вершинам, мкм;
tp – относительная длина профиля, %, где p – числовое значение уровня сечения профиля.
На учебных чертежах по дисциплине «Инженерная графика» при обозначении шероховатости поверхностей достаточно использовать только параметры Ra и Rz.
Шероховатость устанавливают для всех поверхностей, вы-
полняемых по данному чертежу, независимо от методов их образования, кроме поверхностей, шероховатость которых не обусловлена техническими требованиями.
118
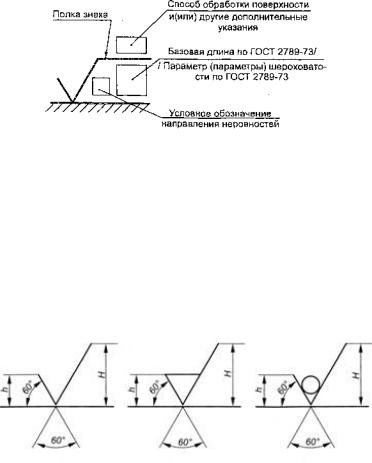
Правила условного обозначения и нанесения шероховатости поверхностей на чертежах деталей установлены ГОСТ 2.309–73. Данный стандарт полностью соответствует международному стандарту ИСО 1302. Форма графического знака и структура обозначения шероховатости приведены на рис. 3.21.
Рис. 3.21. Структура обозначения шероховатости
Если параметр шероховатости или способ обработки поверхностей на чертеже не указывается, знак шероховатости изображается без полки.
В конкретных случаях при обозначении шероховатости поверхности применяется одна из разновидностей знака (рис. 3.22). Знаки выполняют сплошной тонкой линией. Толщина этой линии приблизительно равна половине толщины основной линии, примененной на чертеже. Высота h знака должна быть приблизительно равна высоте цифр размерных чисел на чертеже, а высота H = (1,5…5,0) h.
а) |
б) |
в) |
Рис. 3.22. Разновидности знака обозначения шероховатости:
а – без указания способа обработки; б – с обязательным удалением слоя материала; в – без удаления слоя материала
Поверхности детали, изготовляемой из материала определенного профиля и размера (сортамента), не подлежащие обработке по данному чертежу, отмечаются знаком по рис. 3.22, в – без указания параметра шероховатости.
119
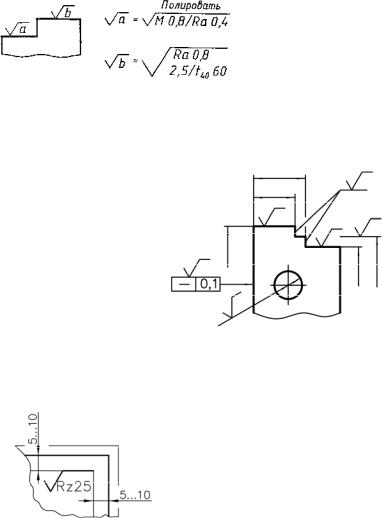
Параметр шероховатости и его численное значение устанавливают по ГОСТ 2789–73, а на чертеже указывают в виде записи символа и числа, например: Ra 1,25; Rz 20; Sm 0,63. Примеры вариантов обозначения шероховатости показаны на рис. 3.26.
В обозначении шероховатости может указываться вид обработки поверхности. Это делается в случаях, когда вид обработки является обязательным или единственным, позволяющим полу-
чить требуемое качество данной поверхности (рис. 3.23). Знаки обозначения шероховатости поверхностей на чертежах
деталей располагают: на линиях контура изображения; на выносных линиях по возможности ближе к размерной линии; на полках линий-выносок. При недостатке места допускается располагать обозначения шероховатости на размерных линиях или их продолжениях (например, для отверстий), на рамке допуска формы, а также разрывать выносную ли-
нию (рис. 3.24).
При указании шероховатости, одинаковой для всех поверх-
ностей детали, знак шероховатости с указанием параметра помещают в правом верхнем углу чертежа, а на изображения детали не наносят (рис. 3.25). Это значит, что все поверхности детали должны быть одной и той же указанной шероховатости.
120