
745
.pdf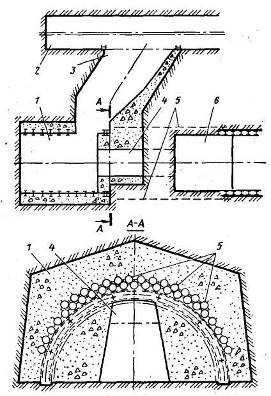
к тиксотропии обводненных глинистых грунтов предопределяет уменьшение устойчивости заполнения разлома при различных динамических воздействиях. Эти зоны обводнены со значительным гидростатическим давлением. Грунты находятся в неустойчивом состоянии. Мощность зон составляет от 1–1,5 м до 10–20 м.
Преодоление таких мест обычными способами с разработкой забоя по частям представляет большую трудность, связанную с опасностью работ, значительными затратами времени и вызывает остановки проходки на длительный период. Поэтому для преодоления разломов были проведены опытно-экспериментальные работы по сооружению опережающих экранов из труб и проходке под их защитой [Транспортное строительство. 1986. № 7. С. 20–22].
Параллельно основному тоннелю с некоторым опережением проходили транспортно- разведочно-дренажную штольню (ТРДШ) при помощи механизированного щита и обслуживающего комплекса по транспортировке и погрузке грунта и монтажу обделки.
При проходке разломов ТРДШ были разработаны два способа сооружения экрана и освобождения «застрявшего» в разломе механизированного щита.
Один из разломов преодолевали одновременно тоннелем и штольней. Для извлечения застрявшего механизированного щита 6 в теле разлома по трассе тоннеля прошли левую нижнюю штольню 2 и углубились в противоположный скальный борт разлома (рис. 4.7). Затем в скальном устойчивом грунте подходной выработкой 3 вышли на ось ТРДШ и соорудили буровую камеру 1 впереди щита в противоположном борте разлома. В камере смонтировали станок для бурения с обсадкой на клетке из бруса.
Навстречу щиту забурили скважины диаметром 165 мм и длиной 13 м в два ряда с заглублением в противоположный борт разлома. В скважины установили трубы 5 диаметром 132 мм с опиранием на смонтированную крепь. Шаг скважин верхнего ряда составлял 35 см, нижнего — 33 см, расстояние между рядами — 20 см. Всего было установлено 46 труб. Под трубы в камере были подведены опорные арки из двутавра, которые омонолитили бетоном. После сооружения экрана прошли подходную штольню 4 к ротору щита, расчистили его и начали проходку.
Рис. 4.7. Преодоление разлома с помощью защитного экрана из труб
В другом разломе ротор щита был зажат обрушенной массой неустойчивого грунта, что
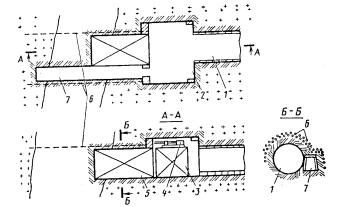
сделало невозможным работу горнопроходческого комплекса. Здесь щит из разлома также высвобождали при помощи опережающего экрана из труб. Для этого отцепили технологическую тележку от щита и отогнали ее на 50 м. Демонтировали четыре кольца обделки из железобетонных блоков и пяти полуколец. Буровзрывным способом разработали камеру длиной 9 м для сооружения экрана.
В камере 2 на подмостях 3 из брусьев установили буровой станок 4 (рис. 4.8). Забурили 56 скважин длиной 20–25 м и диаметром 165 см и в них установили трубы 6 диаметром 146 мм. Трубы перезакрывали разлом и обоими концами входили в скальные борта. Скважины расположили в два ряда: в верхнем — с шагом 35 см, в нижнем — 33 см; расстояние между рядами 20 см. Свод из труб был устроен в сводовой части ТРДШ 1 и по контуру боковой обходной штольни 7. Бурение скважин и установка в них труб экрана заняла 65 сут. Под прикрытием опережающего крепления прошли обходную штольню к ротору щита 5. Затем расчистили ротор и возобновили проходку штольни.
Рис. 4.8. «Освобождение» зажатого грунтовой массой щита с помощью экрана из труб
Последний способ практически стал типовым и был использован при преодолении штольней еще нескольких разломов.
При проходке основного тоннеля на одном из первых разломов был применен экран из труб (рис. 4.9). Для этой цели смонтировали подмости 3 из брусьев и на них поставили буровой станок 4. С шагом 50 см забурили скважины диаметром 89 мм (1) и в них установили трубы 2 экрана диаметром 76 мм. Трубы разместили в сводовой части тоннеля и заглубили в противоположный борт разлома.
До устройства экрана из труб по контуру тоннеля были забурены скважины, через которые провели цементацию разлома. Под защитой экрана прошли калотту с арочнобетонной крепью, подвели стены, и таким образом зона разлома была преодолена. При сооружении калотты случались отдельные вывалы, но экран остался неповрежденным.
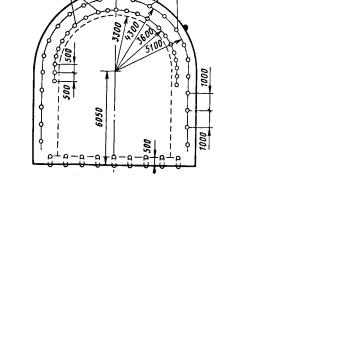
Рис. 4.9. Экран из труб при проходке через разлом основного тоннеля
Для закрытой прокладки труб возможно применение различных установок, в том числе: горизонтального бурения, грунтопрокладывающих установок, пневмопробойников (табл. 4.1).
Таблица 4.1
|
Установка для закрытой прокладки труб |
|||||
|
|
|
|
|
|
|
|
Диаметр |
Максимальная |
|
Скорость |
|
|
Марка установки |
глубина |
|
|
|||
скважины, м |
|
проходки, м/ч |
|
|||
|
скважины, м |
|
|
|||
|
|
|
|
|
|
|
|
|
|
|
|
|
|
У с т а н о в к а г о р и з о н т а л ь н о г о б у р е н и я |
|
|||||
|
|
|
|
|
|
|
УГБ-2 |
1220 |
|
40 |
8 |
|
|
УГБ-4 |
345; 426; 529; 630 |
|
60 |
15 |
|
|
УГБ-5 |
630; 720; 920; 1020 |
60 |
10 |
|
||
|
|
|
|
|
|
Окончание табл. 4.1 |
|
|
|
|
|
|
|
|
Диаметр |
Максимальная |
|
Скорость |
|
|
Марка установки |
глубина |
|
|
|||
скважины, м |
|
проходки, м/ч |
|
|||
|
скважины, м |
|
|
|||
|
|
|
|
|
|
|
|
|
|
|
|
|
|
УГБ-6 |
720 |
|
24 |
60 |
|
|
«Запорожье» |
820; 920; 1020 |
|
1000 |
10 |
|
|
ГБ-1421 |
1020; 1420 |
|
50 |
60 |
|
|
ГБ-500М |
529 |
|
30 |
60 |
|
|
ПМ (ПМ-1620М) |
426–1420 |
60 |
|
0,8–1,5 |
|
|
Г р у н т о п р о к л а д ы в а ю щ и е у с т а н о в к и |
|
|||||
|
|
|
|
|
|
|
ГПУ-600 |
До 630 |
|
80 |
|
3 |
|
ГПВУ-300 |
До 300 |
|
40 |
|
10 |
|
|
П н е в м о п р о б о й н и к и |
|
|
|
||
|
|
|
|
|
|
|
ПР-60М |
63; 85 |
|
— |
|
6–40 |
|
ИП-4603 |
130; 200; 300 |
|
50 |
|
10-80 |
|
ПР-400 |
152; 250 |
|
— |
|
5–60 |
|
П-135 |
135-250 |
|
50 |
|
— |
|
4.2.3.Устройство защитного экрана из труб
спомощью микротоннелепроходческих комплексов
Технологии, которые применяются сегодня при проходке подземных коммуникаций различного назначения, не требующие вскрытия дневной поверхности и не наносящие урон зеленым насаждениям, зданиям, коммуникациям, историческим памятникам и транспортным магистралям, — будущее городского строительства.
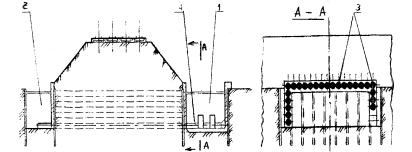
Механизированные комплексы для сооружения выработок малых диаметров (от 250 мм до 1500 мм — внутренние и от 340 мм до 1940 мм — наружные) в нашей стране в основном применяют для бестраншейной прокладки трубопроводов между стартовой и приемной шахтами (котлованами), находящимися на расстоянии до 100 м друг от друга (рис. 4.10).
Это расстояние может быть при необходимости увеличено в несколько раз путем ввода в состав микротоннелепроходческих комплексов (МТПК) специального дополнительного оборудования — промежуточных прессовых станций.
Бестраншейная прокладка трубопроводов с применением МТПК может производиться в нескальных и скальных грунтах, в том числе при смешанном забое и появлении в грунтовом массиве по трассе проходки крупнообломочных грунтов с включением гравия, гальки или щебня, иногда в виде прослоек, а также валунов. Она является наиболее эффективной в песках, в том числе водонасыщенных, а также в глинистых грунтах (глинах, суглинках, супесях). При прокладке трубопровода в малопрочных, средней прочности и особенно прочных скальных грунтах скорость проходки может существенно снизиться.
Рис. 4.10. Схема опережающего защитного экрана из труб, проложенного бестраншейным способом между стартовым и приемным котлованами с применением микротоннелепроходческого комплекса:
1 — стартовый котлован; 2 — приемный котлован; 3 — трубы экрана; 4 — МТПК
Работы по прокладке труб экрана с применением МТПК рекомендуется проводить при положительной температуре окружающего воздуха. При отрицательных температурах работы могут проводиться с обогревом агрегатов МТПК или устройством тепляка.
На стене стартового котлована выполняется маркшейдерская разметка осей труб экрана, по которой осуществляется закрепление лазерного кронштейна, установка лазера и наведение луча лазера в заданном направлении.
Бестраншейная прокладка трубопроводов с применением МТПК может производиться как под свободной территорией, так и в условиях, когда по трассе или вблизи нее располагаются здания, сооружения, подземные коммуникации, железнодорожные и трамвайные пути, автомобильные дороги с различного вида покрытиями, пешеходные дорожки и переходы, зеленые насаждения, водотоки и водоемы. Такая технология наиболее рациональна для условий строительства и реконструкции трубопроводов при проходке: протяженных линий для территорий с плотной застройкой или насыщением подземного пространства действующими коммуникациями; относительно коротких трубопроводов самотечных водонесущих коммуникаций под путями сообщения, водными и другими преградами; под территориями, являющимися памятниками истории и культуры или охранными зонами.
МТПК могут применяться для устройства сводов из труб в качестве временной и постоянной крепи при строительстве тоннелей под различными подземными сооружениями.
Минимальная глубина заложения верха трубопровода, прокладываемого с применением МТПК относительно земной поверхности, должна быть не менее 1,5–2 диаметров трубопровода, но в любом случае не менее 1 м; также не менее 1 м должен быть зазор между прокладываемым трубопроводом и расположенными в земле подземными коммуникациями и сооружениями.
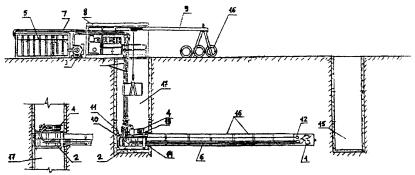
В общем случае МТПК представляет собой комплекс подземного, шахтного и поверхностного оборудования, обеспечивающий механизированное и дистанционно управляемое выполнение следующих операций: образование в различных грунтах подземной выработки для прокладки трубопровода с одновременным креплением забоя и стенок выработки; транспортирование разработанного грунта на поверхность с одновременным контролем его объема; укладка с заданной точностью и скоростью составного трубопровода между стартовой и приемной шахтами. Основными элементами МТПК являются: щитовая микромашина (ЩММ); прессовая станция; система транспортирования и приема разработанного грунта; управляюще-силовой контейнер; крановая установка; аппаратура системы маркшейдерского контроля за положением ЩММ; стартовое и конечное уплотнения, монтируемые на стенках соответственно стартовой и приемной шахт; установка для приготовления и нагнетания бентонитового раствора; составные коммуникационные шланги и кабели. МТПК, в зависимости от используемого в них способа транспортировки разработанного грунта, делятся на 3 вида:
—МТПК 1-го вида с гидравлическим транспортом грунта;
—МТПК 2-го вида с механическим шнековым транспортом грунта;
—МТПК 3-го вида с пневматическим транспортом грунта.
Основными производителями микротоннелепроходческих комплексов являются:
—германские фирмы «Херренкнехт», «Зольтау» (группа ВИРТ), «Ловат МТС», «Бортек», «Ноэль»;
—японская фирма «Исеки-Политех»;
—канадско-американская фирма «Аккерман»;
—английская фирма «Декон» (по лицензии фирмы «Зольтау»).
Сведения по номенклатуре микротоннелепроходческих комплексов, в том числе находящихся в распоряжении подрядных строительных организаций России, и их технические характеристики приведены в работе [25, прил. А].
Технология сооружения опережающего защитного экрана заключается в последовательном продавливании труб в грунтовый массив с одновременной разработкой грунта и выдачей его из трубы на поверхность. По мере продвижения трубы осуществляется пристыковка очередных секций к ранее уложенным. Транспортные трубопроводы, находящиеся в трубе, должны закрепляться от смещения.
При применении МТПК 1-го вида с гидравлическим транспортом (рис. 4.11), имеющего два трубопровода для подвода воды и отводы пульпы, соединение этих трубопроводов с помощью защелок осуществляется с двумя съемными патрубками с последующим подсоединением шлангов для подвода воды и отвода пульпы, отходящих от управляющего силового контейнера.
После наращивания стандартных отрезков коммуникационных шлангов и кабелей на муфтовых соединениях и их закрепления от смещения, с пульта управления включается лазер и проводится проверка функции приема луча лазерной мишенью. В случае перекрытия луча коммуникационными шлангами или кабелями их положение поправляется и они вновь закрепляются.
Для приведения в действие системы транспорта грунта открываются задвижки байпаса с одновременным закрытием питающей и транспортирующей задвижек в ЩММ и включаются водяные и грязевые насосы.
Рис. 4.11. Технологическая схема МТПК 1-го вида
сгидравлическим транспортом грунта:
1 — щитовая микромашина; 2 — процессовая станция; 3 — водяной насос; 4 — грязевой насос; 5 — контейнер для приема и осаждения пульпы;
6 — двойной транспортный трубопровод; 7 — гибкий соединительный
трубопровод; 8 — управляюще-силовой контейнер; 9 — крановая установка; 10 — лазер; 11 — лазерный кронштейн; 12 — лазерная мишень;
13 — курвиметр; 14 — стартовое уплотнение; 15 — приемный котлован; 16 — трубы прокладываемого трубопровода; 17 — стартовый котлован
Перед началом продвижения ЩММ с прицепными элементами и секциями трубы необходимо закрыть задвижку байпаса и открыть задвижки на ветвях транспортных трубопроводов для подачи воды и выдачи пульпы. Включается привод роторного рабочего органа ЩММ и в зависимости от грунтовых условий проводится регулировка числа оборотов с контролем величины крутящего момента. В зависимости от величины угла закручивания ЩММ выбирается направление движения ротора. При увеличении угла закручивания более 20 мм/м меняется направление вращения рабочего органа, замедляется скорость вращения, уменьшается объем подаваемой в ЩММ воды, применяется прием продвижения прокладываемой трубы на 1–2 см прессовыми гидроцилиндрами при отключенном рабочем органе.
Продвижение ЩММ с прицепными элементами и секциями труб на длину хода прессовых гидроцилиндров ведется с регулировкой скорости и обеспечения в гидромоторах рабочего органа давления не более 9–10 МПа и переводом работы прессовых цилиндров на автоматический режим. Продвижение ЩММ должно производиться при одновременной работе аппаратуры системы маркшейдерского контроля. Ведется постоянное наблюдение изображения на мониторе положения луча лазера на лазерной мишени, а также за регистрируемыми на мониторе данными о длине прокладки трубы, дате, времени, позиции по высоте центра машины относительно проектного положения, задаваемого лучом лазера. Кроме этого, ведется контроль за работой штоков управляющих гидроцилиндров и управлением движения ЩММ.
После выдвижения прессовых гидроцилиндров на величину их хода отключается привод вращения рабочего органа, прекращается подача рабочей жидкости в прессовые гидроцилиндры и открывается байпас с закрытием питающей и транспортирующей задвижек в ЩММ.
Прессовые гидроцилиндры отводятся в исходное положение, и повторяется процесс продвижения ЩММ с прицепными элементами и секциями трубы.
График прокладки трубы с помощью МТПК 1-го вида германской фирмы «Херренкнехт» приведен на рис. 4.12.
При применении МТПК 2-го вида с механическим (шнековым) транспортом грунта стыковка секций шнекового конвейера, находящегося в ЩММ или в последней секции прокладываемой трубы с выступающим центральным валом привода, укрепленного на нажимной плите прессовой станции, производится с помощью «пальца». Для приведения в действие системы транспорта грунта включается привод шнекового конвейера. При применении в щитовой машине привода рабочего органа от гидромотора используется система маркшейдерского контроля за положением ее по лазерному лучу, а при приводе от шнека — система контроля за положением светодиодной мишени, размещающейся в головке рабочего органа, с помощью теодолита.
Все остальные технологические операции выполняются аналогично с МТПК 1-го вида,
стем отличием, что разработанный грунт шнеком загружается в бадью и по мере ее заполнения бадья поднимается из стартового котлована наверх и разгружается.
При применении МТПК 3-го вида с пневматическим транспортом разработанного грунта стыковка транспортного трубопровода осуществляется с помощью защелок его концевого участка
снижним передним участком трубчатого угольника нажимной плиты прессовой станции. В зависимости от стадии продавливания стыковка ведется либо непосредственно с ЩММ или с прицепным элементом, либо с последней секцией трубы экрана.
Соединение коммуникационных шлангов и кабелей на муфтах, проверка их положения и закрепление от смещения проводится аналогично с МТПК 1-го вида.
Приводится в действие система транспортирования грунта включением дизельного двигателя вакуумно-вытяжного контейнера. Проверяется режим его максимального вращения, включение вытяжки и открытия транспортного трубопровода ЩММ и
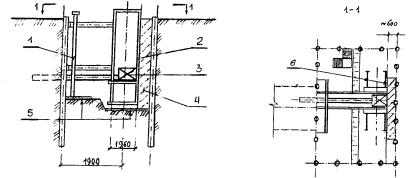
трубопровода притока воздуха.
Управление продвижением, выбор направления движения роторного рабочего органа ЩММ, контроль за закручиванием и мероприятия по устранению закручивания выполняются аналогично с МТПК 1-го вида.
После выдвижения прессовых гидроцилиндров на величину их хода отключается привод вращения рабочего органа ЩММ и прекращается подача рабочей жидкости в прессовые гидроцилиндры. Отключается воздуходувка вакуумно-вытяжного контейнера, и прессовые гидроцилиндры отводятся в исходное положение.
Проверяется заполнение грунтоприемного контейнера и, при необходимости, производится его разгрузка, после чего повторяется процесс продвижения ЩММ, прицепных элементов и трубы.
При сооружении экрана в песчаных грунтах естественной влажности, особенно при наличии гравелистых включений, рекомендуется во время продвижения трубы производить нагнетание бентонитового раствора за наружную поверхность ЩММ и трубы через насадки, имеющиеся в ЩММ или в последнем прицепном ее элементе. При сооружении экрана в водонасыщенных грунтах нагнетание бентонитового раствора целесообразно начинать и производить постоянно при достижении на середине длины прокладываемой трубы усилия продавливания, равного 50 % величины предельного усилия, которое может создать прессовая станция.
Для перемещения МТПК по периметру защитного экрана в каждом конкретном случае создаются вспомогательные механизмы, обеспечивающие быструю и низкозатратную перестановку комплекса к месту ввода очередного элемента экрана.
Одним из примеров такого вспомогательного механизма для ведения работ из котлована предлагается подъемник буровой установки, разработанный московской фирмой «Трансстройтоннель» (рис. 4.13).
Рис. 4.13. Схема устройства для перемещения МТПК по периметру возводимого защитного экрана:
1 — рама для опирания балки под буровое оборудование; 2 — подъемник для размещения бурового оборудования; 3 — буровое оборудование;
4 — упорная плита; 5 — бетонное основание; 6 — рельсы для перемещения подъемного оборудования
Подъемник размещается в котловане стартовой шахты на направляющих из рельсов для горизонтального перемещения домкратной станции. В лобовой части забоя монтируется рама, на которую опираются балки бурового оборудования. Горизонтальный ряд труб обуривается с одного заданного положения подъемника с шагом перемещения в плане, равным размеру между осями труб экрана. В этом положении подъемник фиксируется захватами. При бурении вертикальных рядов труб экрана площадка подъемника и балки, опирающиеся на раму, перемещаются по высоте при помощи гидравлических домкратов. Компактные размеры подъемника (2,7 × 2,2 × 6,0) и его небольшая масса позволяют свободно размещать его в небольших по площади котлованах.
Для устройства защитного экрана в теле насыпи с поверхности земли в качестве примера приводится специальное временное строительное устройство, разработанное СКТБ «Тоннельметрострой» для проходки тоннеля под железнодорожной насыпью Рижского направления в г. Москве (рис. 4.14).
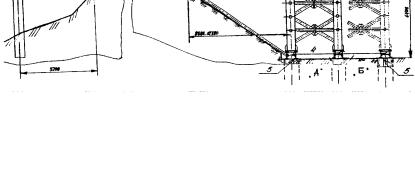
Рис. 4.14. Схема размещения бурового оборудования при устройстве защитного экрана в теле насыпи:
1 — опорная передвижная металлоконструкция; 2 — домкратная установка; 3 — стартовая площадка переменной длины; 4 — опорные балки для перемещения металлоконструкции; 5 — буронабивные сваи;
6 — приемная площадка
Со стартовой стороны с поверхности земли, примыкающей к насыпи, забуриваются расчетные буровые сваи, к которым крепятся опорные балки. По балкам передвигается опорная металлоконструкция. На металлоконструкции на нужной высоте закрепляется домкратная установка и стартовая площадка, которая имеет переменную длину. Вертикальное перемещение домкратной установки и стартовой площадки при бурении очередной трубы производится на величину «а». В металлоконструкции с этим шагом размещены закладные детали для их закрепления. Для продавливания нижних труб вертикальной стены экрана металлоконструкция из позиции «А» может быть переставлена на позицию «Б».
На противоположной стороне насыпи устраивается приемная площадка.
После завершения продавливания трубы ЩММ принимается в приемный котлован и перевозится в стартовый котлован для установки и продавливания очередной трубы. Из проложенной трубы извлекаются секции транспортных трубопроводов или шнекового конвейера, стандартных отрезков коммуникационных шлангов и кабеля с рассоединением соединительных муфт. Извлечение выполняется с помощью тельфера и блока, установленного на задней упорной плите прессовой станции. Извлекаемые детали поднимаются на поверхность и складируются для последующего использования.
В процессе продавливания труб экрана с применением МТПК маркшейдерская служба подрядной строительной организации должна систематически проводить наблюдения за возможными осадками поверхности земли, за состоянием наземных сооружений, рельсовых путей и дорожных покрытий. Все случаи недопустимых осадок должны фиксироваться с составлением соответствующего акта, а работы приостанавливаются для проведения мероприятий по предотвращению влияния осадок на сооружение.
При применении секций труб, длина которых превышает максимально возможный ход гидроцилиндров прессовой станции, рекомендуется применять инвентарные вкладыши. При этом все трубы экрана должны выступать внутрь стартового и приемного котлованов на величину, устанавливаемую проектом для установки временной крепи, которая будет использоваться при проходке подземного сооружения, возводимого под защитой экрана.
Перед установкой ЩММ для продавливания каждой последующей трубы экрана должны выполняться работы по осмотру и техническому обслуживанию МТПК, в том числе:
—очистка рабочего органа и дробилки и удаление застрявших в них камней;
—проверка состояния породоразрушающего инструмента и твердосплавных покрытий (при необходимости выполняются ремонтные работы);
—смазка уплотнений (расположение мест смазки и тип смазочных материалов приведены в инструкции по эксплуатации и техническому обслуживанию МТПК);
—проверка плотности соединений и устранение протечек масла и воды;
—очистка мертвого пространства шаровых кранов на трубопроводах, байпас и проверка включения и выключения задвижек на трубопроводах;
—проверка лазерной мишени и ее очистка;
—проверка электро- и гидросистемы (направление вращения, давление холостого хода, максимальное число оборотов рабочего органа, максимальное давление и работа управляющих цилиндров), проверка микрофона, системы измерений и освещения;
—промывка бентонитовых насадок.
Заслуживает внимания опыт строительства автодорожных тоннелей с использованием метода микротоннелирования в Перми [Метро и тоннели. 2004. № 4. С. 10–13].
Исторически сложилось, что Пермь — один из крупнейших промышленных центров России — разделен железнодорожной магистралью направления Киров – Пермь – Екатеринбург, проходящей через центральную часть города, что негативно отражается на транспортных связях между его районами.
На значительном протяжении железная дорога проходит в насыпи высотой до 10–12 м. Еще в 70-х гг. прошлого столетия генеральным планом города предусматривалось строительство автодорожных тоннелей под железной дорогой. Однако отсутствие надежной технологии и оборудования для прокладки тоннелей, позволяющих выполнить такую задачу без перерыва движения поездов, сдерживало принятие этого ответственного решения, поскольку малейшая неудача, способная привести к сбою в движении поездов
по Транссибирской магистрали, привела бы к колоссальным финансовым потерям.
Интенсивное развитие технологии бестраншейной прокладки коммуникаций в последнее десятилетие открыло новые возможности в строительстве тоннелей мелкого заложения закрытым способом в условиях ограничения деформации дневной поверхности и вышележащих сооружений (дорог, инженерных сетей, наземных зданий).
В 1996 г. было принято решение о сооружении автодорожных тоннелей под защитой экрана из металлических труб, продавливаемых через железнодорожную насыпь под Транссибирской железной дорогой микрощитом германской фирмы «Неrrеnknесht» по технологии, отличающейся следующим рядом несомненных преимуществ по сравнению с другими безусадочными способами строительства тоннелей:
•высокой несущей способностью защитного экрана из металлических труб, внутренние полости которых можно заполнять монолитным бетоном с установкой арматурных каркасов;
•высокой точностью продавливания труб с помощью микрощита, так как его положение при продавливании управляется оператором;
•возможностью использования защитного экрана в качестве элементов постоянной обделки с устройством его сразу на всю длину тоннеля.
В период 1998–2003 гг. в Перми были построены два автодорожных тоннеля с защитным экраном в теле насыпи двухпутной электрифицированной железнодорожной магистрали без перерыва движения поездов:
•тоннель под две полосы движения автотранспорта на 1435 км железнодорожной магистрали (рис. 4.15, а) в 600 м от железнодорожного вокзала в центральной части г. Перми (1998–2001);
•тоннель под четыре полосы движения автотранспорта (рис. 4.15, б) на 1442 км той же железнодорожной магистрали (2001–2003).
В связи с высокой интенсивностью движения поездов на указанном участке железной дороги (свыше 90 пар поездов в сутки) обязательным условием было выполнение строительных работ без перерыва движения поездов, с гарантированным обеспечением минимальных осадок железнодорожного полотна и верхнего строения пути.
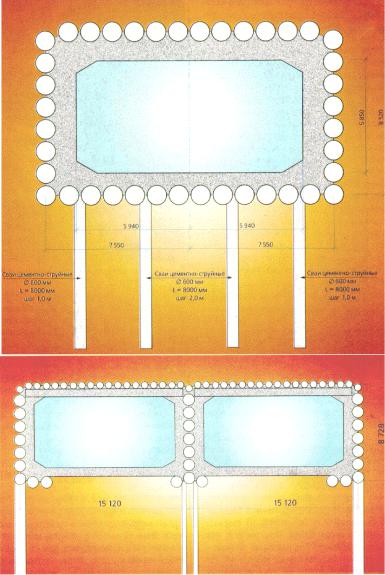
а)
б)
Рис. 4.15. Конструкции автодорожных тоннелей в г. Перми:
а — под две полосы движения; б — под четыре полосы движения
Выбор конструкции и технологии строительства тоннелей предопределен следующими основными факторами, неблагоприятное сочетание которых ранее не встречалось в практике отечественного тоннелестроения:
•необходимость сооружения тоннеля в теле железнодорожной насыпи, сложенной слабыми грунтами, неустойчивыми при проходке, с обеспечением бесперебойного и безопасного движения поездов с установленными скоростями;
•наличие в основании насыпи слабых водонасыщенных грунтов общей мощностью более 5 м;
•высокий уровень грунтовых вод, который невозможно понизить традиционными методами, не вызвав деформаций насыпи действующей железной дороги;
•напряженно-деформационное положение насыпей, характеризующееся состоянием предельного равновесия устойчивости откосов против круглоцилиндрического сдвига.
В связи с этим на обоих тоннелях были приняты общие принципиальные решения:
•закрепление откосов насыпи против круглоцилиндрического сдвига до начала строительства тоннелей;
•устройство защитного экрана из металлических труб, продавленных через тело насыпи микрощитами фирмы «Неrrеnknесht»;
•закрепление слабых грунтов в теле тоннелей до начала проходки;
•закрепление слабых грунтов основания грунтоцементными сваями, устраиваемыми