
745
.pdf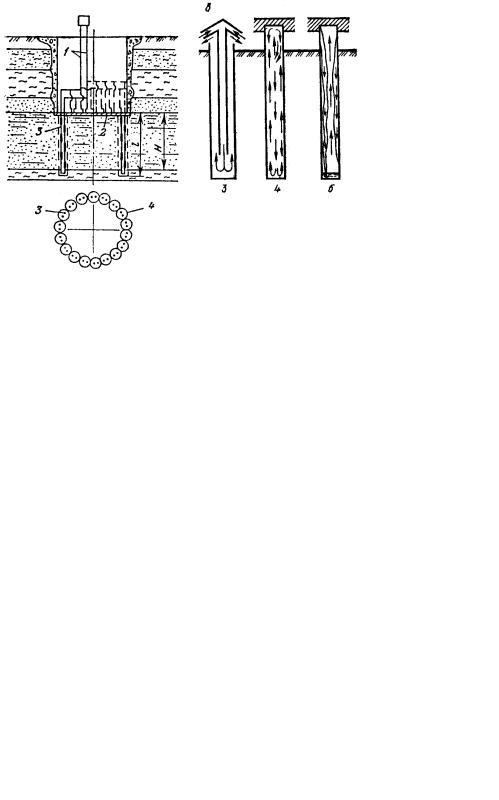
где 0,5 — заглубление электронагревателей в подстилающий прочный грунт, м.
Рис. 3.28. Схема электроплавления плывунов: 1 — электросеть; 2 — настил;
3 — П-образные электронагреватели;
4 — расплавленный плывун
При прохождении электрического тока через нагреватель последний быстро нагревается (в течение 8–10 мин) до температуры 1800–2500 °С и расплавляет окружающий его грунт. Цилиндры из расплавленного грунта вокруг каждого нагревателя смыкаются, образуя после его остывания монолитную оболочку.
При электроплавлении про-исходит интенсивное испарение воды из плывуна. Образовавшийся пар частично выходит в атмосферу, а частично перемещается в сторону от нагревателя, отжимая при этом грунтовую воду от него. Превращения кремнезема и его модификаций сопровождаются увеличением их объема на 10–20 %, вследствие чего поры грунта заполняются расплавом, обеспечивающим ему высокую плотность.
Процесс электроплавления плывунов сопровождается выделением окиси углерода, углекислого газа, метана, водорода и паров кремния, что требует непрерывного и усиленного проветривания забоя выработки.
Прочность остывшего расплава достигает 26–43 МПа и зависит от температуры нагревания плывуна.
Радиус плавления R, м, ориентировочно можно
определить по формуле
R = 0, 06 + 0,02t, (3.2)
где t — продолжительность нагрева плывуна при данной температуре плавления, ч. Обычно на 1 м3 упрочняемого плывуна расходуется 1200–1500 кВт ч электроэнергии. Определенный интерес в условиях северной климатической зоны представляет
технология возведения термосвай с помощью сезонно действующих саморегулирующихся охлаждающих устройств, предназначенных для охлаждения и замораживания грунтов естественным холодом за разности температур наружного воздуха и грунта в зимнее время без дополнительных затрат.
Установки по способу подачи хладагента в охлаждающие колонки подразделяют на установки с принудительной и естественной конвекцией хладагента.
По фазовому состоянию хладагента можно выделить воздушные, жидкостные и парожидкостные установки (рис. 3.29).
а) |
б) |
Рис. 3.29. Принципиальные схемы охлаждающих установок:
а — с принудительной конвекцией хладагента; б — с естественной конвекцией хладагента; 1 и 3 — воздушные; 2 и 4 — жидкостные; 5 — парожидкостная
Наиболее эффективными по холодопроизводительности, простоте эксплуатации и экономичности являются термосваи с замкнутой конвекцией жидкостного или парожидкостного хладагента. Конвекцию в них обеспечивает разность плотностей хладагента в «холодной» надземной и «теплой» подземной частях. Эти термосваи обладают более совершенными теплопередающими свойствами, чем воздушные, так как
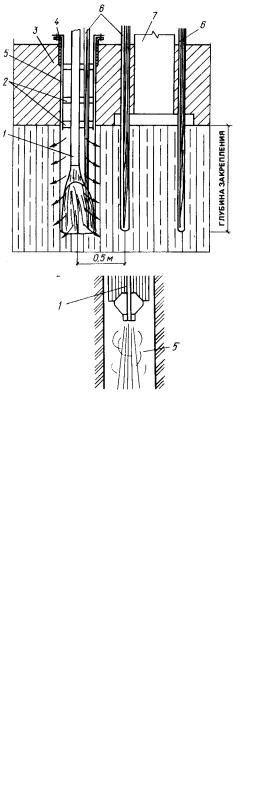
теплоемкость жидкости во много раз превышает теплоемкость воздуха. Термосваи являются саморегулирующимися установками и не требуют энергетических затрат и постоянного обслуживания персоналом. Они просты и дешевы в изготовлении.
Широкое применение в практике получили термосваи с керосином в качестве хладагента.
|
Из парожидкостных термосвай следует отметить |
||||||||||||
|
термосваи, которые представляют собой стальную |
||||||||||||
|
герметическую трубу, заполненную пропаном. Труба |
||||||||||||
|
входит в состав свайного фундамента. |
|
|
|
|
||||||||
|
В некоторых случаях обжиг грунтов может |
||||||||||||
|
применяться также для закрепления оснований |
||||||||||||
|
деформированных зданий и сооружений. |
|
|
|
|
||||||||
|
Основными |
составными |
частями нагревательной |
||||||||||
|
установки в этих случаях являются генератор сжатого |
||||||||||||
|
воздуха |
и форсунка. |
В качестве |
генератора |
сжатого |
||||||||
|
воздуха при больших объемах работ используют |
||||||||||||
|
воздуходувки |
производительностью |
26 м3/мин, а |
при |
|||||||||
|
небольших объемах |
работ — |
компрессоры типа |
РК |
|||||||||
|
производительностью |
9 м3/мин |
с |
рабочим |
давлением |
||||||||
|
0,15 МПа. |
|
|
|
|
|
|
|
|
|
|
||
|
Форсунка (горелка) представляет собой трехполостный |
||||||||||||
|
рабочий орган (рис. 3.30). В первой полости находится |
||||||||||||
|
запорная игла, которая регулирует расход топлива, вторая |
||||||||||||
|
полость служит для подачи воздуха, предназначенного для |
||||||||||||
|
распыления топлива и отбрасывания факела; третья полость |
||||||||||||
|
предназначена для охлаждения корпуса форсунки воздухом. |
||||||||||||
|
Обжиг скважин начинается с разогрева ее верхнего |
||||||||||||
|
участка, |
что |
необходимо |
для |
создания |
фронта |
|||||||
Рис. 3.30. Конструкция форсунки: |
воспламенения |
топлива. После |
|
этого |
постепенно |
||||||||
1 — запорная игла; 2 — полость для |
|
|
|
|
|
|
|
|
|
|
|
|
|
подачи воздуха для распыления топлива; увеличивается |
расход газа |
и |
воздуха |
до |
расчетных |
||||||||
3 — полость для охлаждения корпуса |
значений, создавая рабочий режим: давление 0,01–0,03 |
||||||||||||
форсунки; 4 — труба; 5 — скважина |
МПа, температуру 800–1000 °С. |
|
|
|
|
|
|
|
|||||
Проект производства работ по термическому укреплению оснований должен содержать |
|||||||||||||
следующие материалы: технологи-ческие |
карты и схемы, график производства ра-бот, |
||||||||||||
|
расчет технологи-ческих параметров об-жига, проект |
||||||||||||
|
временного газопровода и временной электросети, методику |
||||||||||||
|
контроля качества тер-мической обработки грун-тов и |
||||||||||||
|
мероприятия по технике безопасности. |
|
|
|
|
|
|||||||
|
Обжиг выполняется по следующей технологи-ческой схеме |
||||||||||||
|
(рис. 3.31). Затвор устанавливают в устье скважины непос- |
||||||||||||
|
редственно с поверхности. Фильтрация газообразных продуктов |
||||||||||||
|
в верхние слои грунта предотвращается путем экранирования |
||||||||||||
|
стенок скважин на глубину ниже подошвы фундамента. |
||||||||||||
|
Экранирование |
осуществляют |
|
установкой |
эластичной |
||||||||
|
воздухонепроницаемой оболочки из стеклоткани, поджимаемой |
||||||||||||
|
к стенам в двух–трех местах по высоте распорными кольцами. С |
||||||||||||
|
помощью удлиненной форсунки обжиг обеспечивают в нижней |
||||||||||||
|
части скважины. По мере обжига нижних слоев грунта |
||||||||||||
|
удлинитель форсунки укорачивают путем снятия верхних |
||||||||||||
|
секций труб, и факел поднимается по скважине для обжига |
||||||||||||
Рис. 3.31. Устройство термостолбов: |
вышерасположенных слоев. Процесс обжига контролируют с |
||||||||||||
помощью термопар, установленных |
в |
рабочей |
скважине |
и в |
|||||||||
1 — форсунка; 2 — распорные кольца; |
|||||||||||||
контрольных |
шпурах. Температура |
нагрева |
слоя |
грунта, |
|||||||||
3 — грунт; 4 — кран; 5 — эластичная |
|||||||||||||
оболочка; 6 — термопара; |
подстилающего подошву фундамента, не должна превышать 300 |
||||||||||||
7 — усиляемый фундамент |
|
|
|
|
|
|
|
|
|
|
|
|
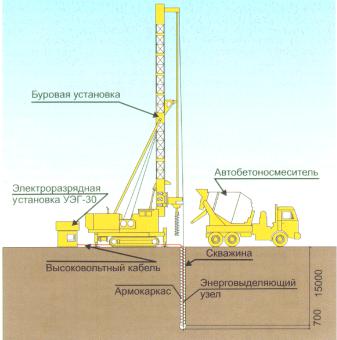
°С. Диаметр столбов составляет около 2,0 м, а расстояние между скважинами для обжига 3–5 м.
3.4. Электроразрядная технология для геотехнического строительства
Внастоящее время общеизвестно и доступно применение добавок по ускорению набора прочности бетона и экономия вяжущих. Специалистами ООО «Тоннельдорстрой»
снаучными лабораториями ВПК ведется поиск технологии использования электроактивирования воды для затворения бетонных смесей и повышения активности цемента за счет дополнительного измельчения с целью повышения прочности бетона [Метро и тоннели. 2003. № 6. С. 12–15].
Вэтом плане сделаны первые шаги — приобретена геотехническая электроразрядная установка УЭГ-30, которая разработана совместно со специалистами Международного института прикладной физики и высоких технологий и Российского научного центра «Курчатовский институт». Она предназначена для обработки скважин и бетона в процессе изготовления буронабивных свай с улучшенными характеристиками (рис. 3.32).
Принцип действия установки основан на использовании мощных импульсных электрических разрядов в бетонной смеси для создания электрогидравлических ударов. При этом происходит уплотнение грунтовых стенок скважин, развитие боковой поверхности свай, повышение прочностных характеристик бетона на 40–60 % в сравнении с контрольными образцами и сцепления бетона с арматурой.
На основании проведенных специалистами НИИОСП им. Герсеванова расчетов по оценке несущей способности буронабивных свай, изготовленных по традиционной и электроразрядной технологиям в глинистых грунтах, несущая способность последних выше в 1,8–4,0 раза, чем у обычных. С учетом требований Мосгорэкспертизы, проведенных сметных расчетов и анализа полученных данных, стоимость 1 м погонной длины сваи ЭРГ выше, чем обычных буронабивных свай на 29 %, тогда как стоимость одной тонны несущей способности в среднем ниже в 2,3 раза.
Рис. 3.32. Технологическая схема устройства буронабивных свай с помощью электроразрядной установки УЭГ-30
Работы на УЭГ-30 выполняются бригадой из двух человек: оператора установки и электрика.
Установка смонтирована в утепленном металлическом корпусе-контейнере, в котором располагаются узлы генератора импульсных токов, осветительные и нагревательные приборы. Переносной электроразрядный (энерговыделяющий) узел (ЭВУ) подвешивается на лебедку бурильной машины для спуска в скважину. ЭВУ соединяется с установкой высоковольтным коаксиальным кабелем передачи энергии.
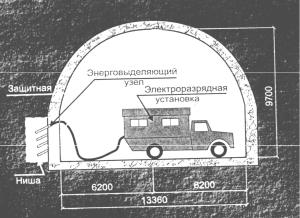
К достоинствам данной технологии можно отнести следующее:
—разработанная и научно обоснованная геотехническая технология не имеет аналогов
вмире. Она позволяет производить конструкции с высокими эксплуатационными характеристиками при сравнительно низких удельных затратах;
—отнесенная к объему несущая способность свай, устраиваемых с помощью ЭРГ, выше, чем у свай, устраиваемых традиционными методами;
—технология и оборудование для устройства свай с помощью ЭРГ являются безопасными и надежными, обеспечивают высокое качество производимых конструкций;
—уникальная технология даст возможность устраивать в водонасыщенных песчаных грунтах уширение пяты и ствола свай или уплотненные забои;
—электроразрядная обработка повышает эксплуатационные характеристики бетонной смеси, используемой для заливки сваи, а также окружающих ее грунтов. Набор прочности бетона после обработки происходит быстрее, значительно возрастает активность его составляющих при твердении, что приводит к увеличению прочности бетонов в 1,5 раза при неизменном расходе вяжущей составляющей;
—электроразрядная технология может также использоваться для устройства анкеров повышенной несущей способности.
Наряду с вышеприведенным институтом прикладной физики и высоких технологий совместно с Российским научным центром «Курчатовский институт» создан опытно-промышленный образец мобильной электроразрядной установки для разрушения горных пород и железобетона УЭМ-200 (рис. 3.33). Суть электрогидравлического метода (известного также как электроразрядный, или плазменный) состоит в использовании электроэнергии, выделяемой в плазменном канале электрического разряда в конденсированных средах при протекании через него мощного импульса тока. Применительно к разрушению блоков горных пород или бетона электрический разряд создается в заполненных водой шпурах, пробуренных в блоке (рис. 3.34).
Рис. 3.33. Разрушение пород с применением мобильной электроразрядной установки УЭМ-200
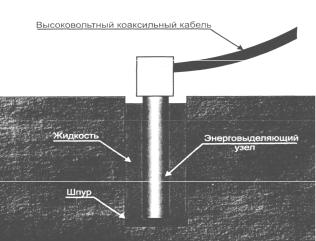
Рис. 3.34. Энерговыделяющий узел электроразрядной установки
Неоспоримые достоинства метода — это отсутствие выделения вредных веществ, разрушительных акустических и сейсмических ударных волн, наличие контроля над этим процессом вложения энергии.
УЭМ-200 успешно прошла испытания на объектах ООО «Тоннельдорстрой» при разрушении временной подпорной стены. При этом разлет обломков породы составил 5–7 м. Производительность установки до 20 м3/ч. Стоимость внедрения — 3,2 млн р.
4. СТРОИТЕЛЬСТВО ПОДЗЕМНЫХ СООРУЖЕНИЙ ПОД ЗАЩИТОЙ ОПЕРЕЖАЮЩЕЙ КРЕПИ
4.1. Общие положения
Возрастающие масштабы подземного строительства обусловливают необходимость совершенствования существующих, разработки и внедрения новых, нетрадиционных конструктивных и технологических решений, обеспечивающих повышение темпов, снижение трудоемкости и стоимости строительно-монтажных работ при минимальных нарушениях окружающей среды.
Проходка тоннелей в слабоустойчивых грунтах, а также в трещиноватых и сильно раздробленных водонасыщенных скальных грунтах сопряжена со многими сложностями, в частности трудоемкостью разработки грунта и необходимости незамедлительного крепления образовавшегося пространства. В результате — низкие скорости проходки и ее высокая стоимость. В последние годы в метро- и тоннелестроении появился ряд инженерных решений, дающих возможность осуществлять проходку в слабоустойчивых грунтах значительно более высокими темпами и механизировать строительный процесс. Суть этих решений заключается в том, что из забоя выработки устраивают опережающую крепь и под ее прикрытием разрабатывают грунт. При этом используются различные виды опережающей крепи: защитные экраны из анкеров или труб, инъекционное закрепление, бетонная крепь, устраиваемая в прорези по контуру тоннеля и т.п.
Опережающее крепление — превентивная мера, гарантирующая безопасное раскрытие тоннельной выработки и устойчивость окружающего грунтового массива. Его применяют преимущественно на участках нарушенных скальных, слабоустойчивых и неустойчивых мягких водоносных грунтов, которые встречаются по трассе горных, подводных и городских тоннелей, сооружаемых закрытым способом. Выбор того или иного вида опережающей крепи и технологии ее устройства определяются протяженностью нарушенных зон, типом и свойствами пересекаемых грунтов, расположением уровня грунтовых вод и пр.
4.2. Защитный экран из труб
Способ проходки с устройством защитного экрана из труб получил довольно широкое распространение, особенно при преодолении зон тектонических разломов, а также при
строительстве городских тоннелей мелкого заложения, когда необходимо обеспечить минимальные осадки земной поверхности.
4.2.1. Зарубежный опыт применения экрана из труб
Под защитой экранов из труб диаметром от 0,2 до 2,5 м за рубежом построено большое количество тоннелей длиной до 80 м, различных размеров и форм поперечного сечения. Увеличение длины может быть достигнуто созданием промежуточных шахт или котлованов задавливания.
Вбольшинстве случаев трубы задавливают вдоль оси тоннеля с зазорами в 10–50 см, заполняя их цементным раствором или бетоном. Например, на строительстве метрополитена в Гамбурге участок перегона в 40 м под жилым домом прошли под защитой экрана из 14 стальных труб диаметром 1750
мми длиной звеньев 6 м с толщиной стенок 14 мм. Промежутки между трубами шириной 20 см перекрывали при разработке грунта привариваемыми стальными листами, затем заполняли цементным раствором. Таким же образом заполнили 50-сантиметровые зазоры между трубами над строившимся в Париже перегонным тоннелем метрополитена.
В1976 г. способ защитного экрана из труб применили при строительстве ст. «Хама-тё» колонного типа Токийского метрополитена (Япония). На этом объекте металлические трубы диаметром 1220 мм продавливали над сводом будущей станции на длину 75,6 м. При этом трубы имели соединения типа шпунтового. Таким образом был создан непрерывный водонепроницаемый экран и упрощена проблема соблюдения точности продавливания (положения труб), поскольку достаточно было обеспечить точность продавливания первой трубы, которая в дальнейшем послужила в качестве направляющей. Недостатками данного варианта являются: применение ручного труда и необходимость использования труб диаметром не менее 1200 мм, что сопряжено с большим объемом земляных и бетонных работ и трудоемкостью операций с тяжелыми секциями труб. Для устранения этих недостатков применяют другую разновидность способа: свод сооружают из стальных труб диаметром 750–1000 мм с удалением из них грунта (шнеком, наращиваемым одновременно с задавливаемой трубой) и последующим заполнением бетоном или железобетоном.
При строительстве метрополитена в г. Атланта (США) такой способ применяли для сооружения экрана на участке длиной 24 м и заложением 4,0 м под железнодорожными путями. При помощи станка горизонтального бурения проложили 48 стальных труб диаметром 760 мм с последующей установкой в них арматурных каркасов и заполнением бетоном. Существенные трудности были связаны с наличием в насыпи обломков дерева и старых шпунтовых стенок. В таких случаях шнек извлекали, и препятствия удаляли вручную. Тем не менее успевали сооружать одну трубу в день. Там же при сооружении перегонных тоннелей метрополитена под насыпью скоростной автомагистрали с интенсивностью движения около 260 тыс. автомобилей в сутки применили опережающую крепь из пройденных по контуру микротоннелей, закрепляемых стальными трубами и заполненных бетоном (рис. 4.1).
Другие варианты проходки тоннелей без прекращения движения по автомагистрали: продавливание прямоугольных секций, новоавстрийский способ, закрепление грунта струйной цементацией или замораживанием в процессе проектирования были по разным причинам отвергнуты.
При строительстве наклонных эскалаторных тоннелей ст. «Мо-нумент» в г. Ньюкасле (Англия) защитный экран длиной 18 м устроили в глине. Здесь использовали стальные трубы диаметром 760 мм с замковыми соединениями. Диаметр заранее пробуриваемых скважин составлял 785 мм. После установки трубы 25-мил-лиметровый зазор между ней и грунтом заполняли цементным раствором. При бурении скважин в глине встречались многочисленные валуны, что приводило к преждевременному износу режущей головки шнека, а иногда и к срыву замковых соединений. Удалять валуны приходилось вручную. В связи с этим на прокладку одной трубы затрачивали около недели.
Японская фирма Нисимацу разработала и внедрила еще один вариант способа, отличающийся большей универсальностью. Для забуривания труб диаметром 210–260 мм использовали малогабаритный буровой станок вращательного действия, который может быть установлен на опорной платформе с портала тоннеля (рис. 4.2, а) или во вспомогательной шахте (рис. 4.2, б). Стальные трубы с толщиной стенок 13 мм после
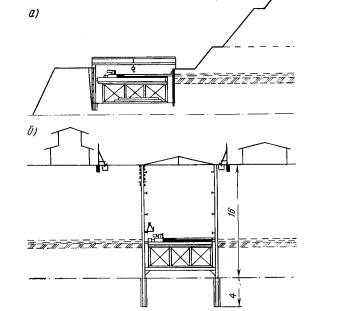
забуривания в грунт заполняли цементным раствором.
Грунт выбирали шнеком, на конце которого установлена сменная режущая головка, рассчитанная на разрушение как слабых, так и скальных грунтов. Это дает возможность в зависимости от прочности грунта либо разбуривать скважину увеличенного диаметра с последующим проталкиванием трубы, либо проталкивать ножевую секцию трубы в грунт с последовательной отборкой грунта шнеком. В более устойчивых грунтах экран делают из одного, в менее устойчивых — из двух рядов труб с замковыми соединениями и цементацией промежутка между трубами и рядами. Для дополнительного усиления экрана замковое соединение также может быть зацементировано. Такой вариант способа опережающего экрана впервые опробовали в 1976 г. при строительстве станции метрополитена в песке и иле. Трубы диаметром 279 мм и длиной 11 м забуривали в поперечном направлении, используя шнек с электрическим приводом и два гидродомкрата усилием по 150 кН.
а)
б)
Puс. 4.2. Бурение скважин под трубы защитного экрана с помощью малогабаритного бурового станка, установленного на опорной платформе
Достаточную точность прокладки труб описанным способом можно обеспечить при длине забуривания примерно до 50 м. Учитывая возможность продавливания труб с двух сторон, можно строить таким способом тоннели любой протяженности, используя промежуточные котлованы, устраиваемые через 100 м. Защитный экран рекордной длины применен при сооружении портальных участков автодорожных тоннелей Аобаяма длинной 2,2 км в г. Сэндай (Япония). Эти участки длинной 220 и 452 м залегали на глубине от 5 до 14 м в мягком вулканическом туфе с песком и гравием прочностью 500– 600 Н/см2. Защитный экран строили из 32 стальных труб диаметром 216 мм, расположенных с промежутками по 40 мм без замковых соединений. Всего соорудили шесть экранов. Номинальное усилие продавливания бурового станка составляло 1500 кН. Под защитой трубчатого экрана вели проходку калоттной части тоннелей с арочной и набрызг-бетонной крепью. По причине большой длины забуривания потребовалось несколько видов контроля направления, в частности — по лазерному лучу, с использованием промышленного телевидения. Контрольные съемки производили после задавливания каждой секции трубы длиной 5,5 м; максимальное отклонение составило 24 см. Сооружение одного защитного экрана занимало от 70 до 100 дней.
На этом объекте после устройства защитных экранов оставалось пройти еще участки длиной 27 и 81 м, на которых мощность прикрываемых крепких грунтов была менее 1,5 м. Поскольку разработать дополнительные котлованы оказалось невозможно, применили модификацию способа: сооружение экрана из забоя выработки наклонными под углом 4° трубами длиной 10 м, перекрывающими друг друга на 1 м. Грунт разрабатывали под защитой готовой секции с креплением стальными арками и набрызг-бетоном. Для забуривания труб из забоя использовали
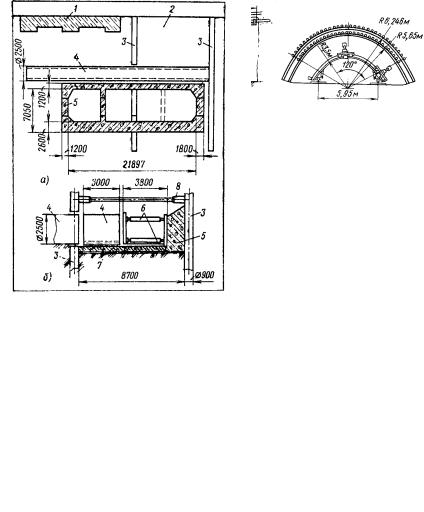
передвижные установки на рельсовом ходу, состоящие из портальной рамы кругового очертания с двумя перемещающимися по ней буровыми механизмами и силовой станции (рис 4.3).
Рис. 4.3. Устройство экрана из труб с помощью портальной рамы с буровыми механизмами
В отдельных случаях защитный экран устраивают, продавливая трубы в поперечном к оси тоннеля направлении. Таким образом устраивали экраны из труб диаметром 2500 мм на участке метрополитена во Франкфурте-на-Майне (Германия) вблизи фундаментов зданий (рис. 4.4, а).
а)
б)
Рис. 4.4. Схема экрана из труб (а) и установки для их задавливания (б): 1 — фундамент здания; 2 — котлован; 3 — буровые сваи;
4 — трубы; 5 — упор; 6 — домкраты; 7 — бетонное основание; 8 — расстрел
В котловане, раскрытом рядом с фундаментами, забетонировали упоры и смонтировали установки для задавливания труб с четырьмя домкратами грузоподъемностью по 3000 кН (рис. 4.4, б). Звенья длиной от 1 до 3,5 м соединяли сваркой. Общая длина труб с учетом ширины обделки и длины участков опирания составляла от 13 до 25 м. Ножевую часть головного звена изготавливали из листа толщиной 5 см и усиливали дополнительным кольцом, чтобы снизить усилия задавливания. Грунт в головной части труб разрабатывали вручную, задавливая их со средней скоростью 2 м в смену. Положение труб корректировали по лучу лазера путем несимметричной разработки грунта по торцу.
Заслуживает внимания опыт применения защитного экрана из труб при строительстве автодорожных тоннелей Malenchini (Италия) на автостраде Livorno-Civitavecchia в 1990– 1991 гг. Проходка осуществлялась в мягких грунтах под защитой опережающей крепи (зонтиков) в калоттах из грунтоцементных колонн диаметром 0,6 м, армированных стальными трубами диаметром 88,9×10 мм со стороны южного портала и диаметром 76×10 мм — со стороны северного (рис. 4.5).
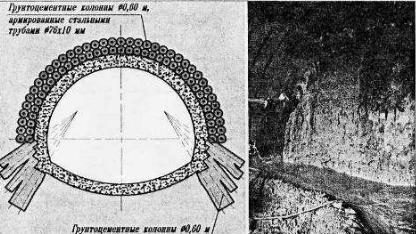
Рис. 4.5. Поперечное сечение и выполнение работ в зоне нахлеста грунтоцементных колонн зонтика опережающей крепи
на строительстве автодорожного тоннеля
Грунтоцементные колонны зонтиков формировались из забоев однокомпонентной струйной цементацией с наклоном скважин в 6 % по отношению к продольным осям тоннелей и шагом примерно 60 см. Длина грунтоцементных колонн зонтиков составляла 13 м, а их нахлест с учетом 10 м фронта экскавации — 3 м.
Пяты грунтоцементных сводов из соприкасающихся колонн зонтиков подкреплялись рядами неармированных грунтоцементных колонн диаметром 0,6 м шагом 60 см и длиной 3,0–3,5 м, наклоненных под углами от 29 до 54° к вертикали.
Северный и южный порталы укреплялись четырьмя рядами грунтоцементных колонн диаметром 0,6 м с шагом 1 м и длиной 18 м, выполняемых однокомпонентной струйной цементацией с армированием упомянутыми стальными трубами. Ряды портальных колонн имели наклон 5, 10, 15, 20 % по отношению к вертикали соответственно. Поверху эти колонны объединялись монолитными железобетонными обвязочными балками.
На строительстве этих тоннелей выполнено 69 000 м погонной длины грунтоцементных колонн зонтиков. При проходке тоннелей опережающая крепь подкреплялась стальными двутавровыми арками из профиля НЕВ160, устанавливаемыми с шагом 1 м. Затем арки омоноличивались бетоном временной обделки.
4.2.2. Отечественный опыт применения экранов из труб
Одним из наиболее сложных видов работ при строительстве подземных сооружений закрытым способом является открытие фронта работ, связанное с необходимостью перехода от проходки вертикальных выработок к горизонтальным, сооружением новой выработки под углом к существующей и т.п. Такие работы в большинстве случаев осуществляют горным способом, предполагающим: проходку передовых штолен, пробивку фурнелей, разработку калотты до проектного очертания будущего свода выработки, раскрытие на деревянном креплении полного сечения выработки с последующим монтажом так называемых прорезных колец из сборных элементов, как правило, чугунных тюбингов.
Наряду с чрезвычайно высокой трудоемкостью таких работ, выполняемых вручную, весьма остро стоит вопрос обеспечения их безопасности, особенно в нарушенных грунтах. Анализ альтернативных решений показал, что можно выполнять рассечки с помощью прорезных колец по измененным технологиям, обеспечивающим снижение трудоемкости и повышение безопасности. В частности, проф. И.Я. Дорман предложил свой способ устройства прорезанных колец с помощью защитных арок, в том числе защитного экрана из труб (рис. 4.6), технология которого приведена в работе [13].
В зависимости от геологических условий и в случае необходимости через трубы экрана может быть проведена укрепительная цементация грунтового массива.
Использование опережающих защитных экранов позволяет избежать вывалов и обрушений грунта внутрь выработки в процессе проходки, стабилизировать окружающий
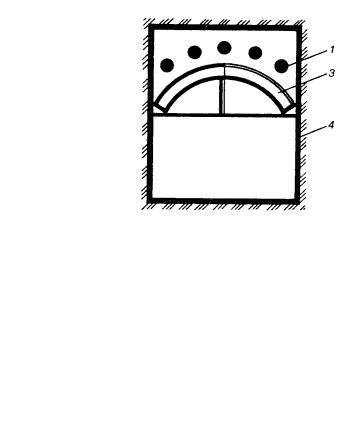
выработку грунтовый массив, значительно снизить его деформации и нарушения.
Рис. 4.6. Схема экрана из труб над строящимся тоннелем:
1 — труба защитного экрана; 2 — тюбинговое кольцо; 3 — тюбинговые арки; 4 — обделка ствола
Защитный экран состоит из труб и поддерживающих элементов. Для создания защитных экранов используют преимущественно стальные трубы диаметром 95–500 мм, полые и заполненные бетоном или цементным раствором.
Труба требуемой длины составляется из отдельных звеньев длиной 1,5–6,0 м, соединенных между собой сваркой или свинчиванием. Смежные трубы могут объединяться при помощи замковых устройств и направляющих. Трубы защитного экрана размещают с зазором одна относительно другой или вплотную. При наличии значительного горного давления возможно создание защитного экрана из нескольких рядов труб.
Для закрепления крупнопористых грунтов используют перфорированные трубы. Нагнетая в них цементный раствор, создают в грунте несущую трубоцементно-грунтовую оболочку. Трубы защитного экрана для нашего случая размещают по своду выработки.
В качестве поддерживающих элементов используют:
—стальные арки;
—арки, омоноличенные бетоном;
—монолитную бетонную или железобетонную обделку;
—сборную железобетонную или чугунную обделку.
Параметры элементов защитного экрана (диаметр и толщина стенок труб, величина зазора между трубами, номер профиля и шаг поддерживающих элементов) определяется расчетом. При использовании защитных экранов из труб при сооружении рассечек стволов по предлагаемой технологии опорой для труб в стволе может служить обделка ствола, а в удаленном конце — грунт. В связи с этим длина труб для надежности закрепления в грунте должна быть не менее 2 м.
Новая технология была успешно впервые применена при строительстве комплекса подземных сооружений ст. «Площадь Ильича», где коллективом научно-исследовательской лаборатории НИЦ ТМ был выполнен комплекс расчетных и конструктивных работ, а строителями СМУ-5 Мосметостроя осуществлены строительно-монтажные работы.
По инженерно-сейсмогеологическим условиям Северо-Муй-ский тоннель является одним из сложнейших железнодорожных тоннелей в мире. Он строился в узле пяти рифтогенных разломов, в том числе «Перевального» с зоной трещиноватых и раздробленных гранитов мощностью 400– 600 м. Разломы и зоны дробления заполнены продуктами физического и гидрохимического выветривания — так называемыми рыхлыми тектонитами, в частности глиной. Наличие склонных