
745
.pdfКачество инъекционного закрепления оценивают по результатам испытаний контрольных скважин и по следующим критериям:
а) устойчивость стенок скважины — в течение 24 ч; б) остаточный дебит скважины — не более 0,5 л/мин на 1 м;
в) удельное водопоглощение (корректируется проектной организацией в зависимости от инженерно-геологических условий) — не более 0,01 л/мин-мм-вод. с.
При отборе кернов (образцов) физико-механические свойства укрепленного грунта должны соответствовать проектным требованиям.
Контроль качества и достаточности законченных инъекционных работ следует производить комиссией в составе представителей строительной организации заказчика и проектной организации.
Организация, выполняющая инъекционные работы, должна представить комиссии:
—проектную документацию производства инъекционных работ, дополнения и изменения к
ней;
—исполнительные чертежи по законченному участку работ;
—первичную документацию (журналы буровых и инъекционных работ, материалы автоматической записи технологических параметров инъекции);
—результаты определения характеристик цемента и других использованных инъекционных материалов, данные испытаний укрепляющих растворов и цементного камня, материалы определения физико-механических свойств укрепленных грунтов;
—документацию по контрольным работам;
—заключения проектной организации о результатах анализа исполнительной документации по производственным и контрольным работам и качества выполненных работ.
По результатам рассмотрения представленной документации комиссия составляет акт приемки работ и дает рекомендации на способы проходки закрепленного массива.
Окончательную оценку качества выполненных работ по укреплению грунтов комиссия представляет в акте после проходки зоны закрепления грунта.
2.4.6. Опыт применения инъекционного закрепления грунтов при строительстве подземных сооружений
Широкое применение инъекционные способы закрепления грунтов нашли при строительстве Северо-Муйского железнодорожного тоннеля, расположенного в сложных инженерно-геоло-гических условиях с водопритоком в несколько тысяч м3/ч и первоначальным напором подземных вод до 5,0 МПа [Метро и тоннели. 2005. № 2. С. 20– 21].
Одним из наиболее эффективных комплексных специальных способов работ при проходке тоннеля был способ инъекционного закрепления грунтов с дренажом подземных вод.
На первом этапе выполнялось инъекционное закрепление грунтов, а на втором — снижение напора подземных вод для уменьшения воздействия их на закрепленный грунт при проходке.
Необходимость снижения напоров подземных вод в локальных областях диктовалась не только требованиями к спецработам по сокращению затрат на их выполнение, но и требованиями фирмы «WIRTH» (Германия) по снижению напора подземных вод до 1,0 МПа, так как горнопроходческие комплексы этой фирмы, работавшие при сооружении разведочной транспортно-дре-нажной штольни (РТДШ) на Северо-Муйском тоннеле, могли выполнять свои задачи по механизированной проходке с условием, что напор подземных вод не превышает данного значения.
Вобщем виде схема локального дренажа представлена на рис. 2.33 (она может быть не обязательно замкнутой). При включении в работу дренажных скважин внутри контура 2 напор подземных вод Р1 снижается до некоторого значения Р2. Величину снижения можно регулировать количеством дренажных скважин. Для расчетов локального дренажа используется коэффициент фильтрации Кф.
Взарубежной практике специальные способы закрепления грунтов также получают все более широкое распростра-нение.
Вчастности, большой объем работ по закреплению грунтов был выполнен в ходе строительства станции Обер в Париже на скоростной линии восток–запад [14, III.7], а также при строительстве Манхэттенских тоннелей в США, проходимых с помощью ТПМК [Метро и тоннели. 2003. № 6. С. 18–21] при ограниченном применении буровзрывных работ. В процессе строительства этих тоннелей применили как опережающее инъектирование скальных грунтов, так и инъектирование после проходки.
Обычно методика опережающего инъектирования предпологает заполнение всех или возможно большего числа трещин, швов и пустот на расстоянии 10–25 м перед забоем тоннеля и в пределах верхних 180 или 360° вокруг тоннельной выработки. После завершения опережающего инъектирования на одном участке разработку грунта можно вести на 70–80 % длины этого участка. После завершения разработки проинъектированного участка перед забоем бурится рекогносцировочная скважина и определяется необходимость проведения инъектирования для следующего участка тоннельной выработки. Цикл повторяется до тех пор, пока этого требуют геологические условия. Для получения «сухого» тоннеля может потребоваться также осуществление инъектирования и после проходки.
Эффективность опережающего инъектирования в очень большой степени зависит от доступности тоннельного забоя для бурового и инъекционного оборудования. При использовании буровзрывного метода проходки доступ к забою обычно не затруднен. Для тоннелей, выполняемых с помощью ТПМК, затрудненный по понятным причинам доступ буровой техники ко лбу забоя является одной из основных причин неудачного инъектирования. ТПМК редко проектируют с учетом необходимости осуществления в зоне забоя бурения в инъекционных целях. Однако современные ТПМК предусматривают возможность осуществления опережающего бурения поверх щита и даже, хотя и редко, через планшайбу (технически весьма сложное решение).
Если планируется проведение опережающего инъектирования, важно четко знать границы и объем подлежащего укреплению грунта, а также его расположение относительно тоннельного забоя. С этой целью необходимо прежде всего выполнить рекогносцировочное бурение перед планшайбой и установить характеристики скального массива перед забоем, а также наличие грунтовых вод, места их выхода, скорости течения
ивеличины напора (рис. 2.34).
Проходка тоннелей в сильнотрещиноватых и раздробленных скальных грунтах с приемлемыми гидрогеологическими условиями требует лишь улучшения характеристик скального массива до величин, обеспечивающих его устойчивость. В таком случае чаще всего над щитом выполняют опережающее инъецирование в зоне верхней половины поперечного сечения (180°).
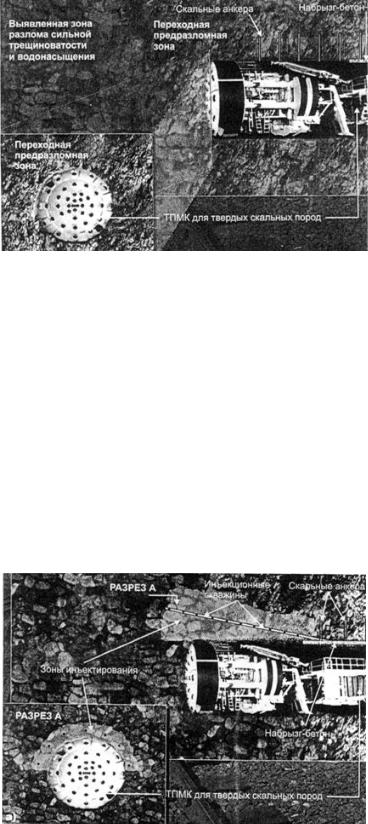
Рис. 2.34. Установление характеристик грунтового массива перед ТПМК
Глубина инъектирования определяется углом, под которым может работать буровой станок. Технические условия таких станков обычно устанавливают минимальный угол наклона скважин относительно оси тоннеля равным 50–10°. Чем больше этот угол, тем глубже войдет бур в стенку тоннельной выработки.
Если рекогносцировочное бурение показывает, что приток грунтовых вод превышает прогнозировавшиеся ранее величины, то с целью регулирования гидрогеологического режима может оказаться необходимым выполнить бурение инъекционных скважин по всему периметру осуществляемой с помощью ТПМК выработки. Иными словами, вероятность появления грунтовых вод является решающим фактором выбора типа оборудования и назначения его характеристик.
Расчетный приток грунтовых вод к каждому из четырех тоннелей определен в объеме 300–3000 л/мин на каждые 300 м длины тоннеля. На стадии строительства такой расход допустим, и в данном случае для предотвращения вывала скального материала позади щита ТПМК может оказаться достаточным лишь обеспечить устойчивость скального массива. С учетом этого на объекте было предусмотрено опережающее инъектирование лишь поверх планшайбы (рис. 2.35, а).
а)
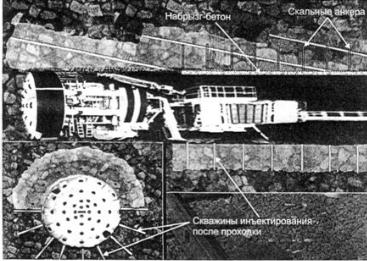
б)
Рис. 2.35. Схемы инъектирования:
а— первая серия опережающего инъектирования перед ТПМК;
б— инъектирование после проходки
Работы начинаются с бурения вблизи ожидаемой перед забоем зоны нестабильного скального образования или разлома первой рекогносцировочной скважины, имеющей длину до 30 м и выполняемой в месте поперечного сечения, соответствующем 12часовому положению стрелки часов. Если эта рекогносцировочная скважина свидетельствует о потенциальной опасности, такой как наличие слабой скальной породы (более высокий темп бурения), потеря бурильной жидкости, приток через рекогносцировочную скважину грунтовых вод темпом более высоким, чем ожидалось, то бурятся еще две скважины длиной до 30 м в местах, соответствующих 9- и 3-часовому положению стрелки часов. Если дополнительные скважины подтверждают наличие опасности, принимается решение о проведении опережающего инъектирования.
Скважины бурятся через забой тоннеля под углом от 5 до 10° к его оси на длине не менее 10 м от планшайбы. Расстояние между скважинами определяется местными характеристиками скального массива и пенетрационными параметрами инъектируемого вещества. Исходя из предыдущего опыта работы в аналогичных грунтовых условиях, рекомендуемое максимальное расстояние между инъекционными скважинами составляет 1,5 м, а в качестве инъектируемого вещества рекомендован цементный раствор. Цемент проникает в трещины толщиной до 0,3 мм, имеет такие же пенетрационные или фильтрационные характеристики, что и силикаты или акриловые смолы, его использование значительно долговечнее, экономически эффективнее и экологически благоприятнее. Основными компонентами цементного раствора являются вода и портландцемент. Свойства цементного раствора можно менять путем добавки цемента других типов, например быстротвердеющих с малым выделением тепла или устойчивым к химическому воздействию. Меняя водоцементное отношение, несложно изменить скорость появления на поверхности раствора цементного молока, его пластичность и прочность при полном затвердевании. Смешение основных компонентов с добавками, такими как бентонит, силикат натрия, дисперсанты, замедлители и ускорители схватывания, также меняет свойства раствора. Новой разновидностью цемента является цемент сверхтонкого помола, позволяющий преодолевать трудности использования портландцементных растворов в грунтах с низкой проницаемостью.
С целью уменьшения притока грунтовых вод, в дополнение к опережающему инъецированию, применяют инъектирование после проходки. Конечно, опережающая инъекционная защита всей поверхности тоннельной выработки, выполняемой с помощью ТПМК, более эффективна, чем инъектирование после проходки, однако устройство такой защиты значительно уменьшает темп проходки. Поэтому на объекте ИСП при строительстве Манхэттенских тоннелей применено инъектирование за забоем, выполняемое
одновременно с движением щита или на более поздних стадиях (рис. 2.35, б), проводить инъектирование только после проходки — это трудоемкое, дорогое и зачастую нерациональное решение, зато в сочетании с опережающим инъектированием оно может быть весьма эффективным. Необходимость в создании защиты обычно возникает, если измеренный приток грунтовых вод в тоннель находится в пределах от 0,5 до 10 л/мин на 100 м тоннеля. Эта необходимость определяется также чувствительностью окружающей среды к объекту строительства, что зачастую предъявляет к инъектированию высокие требования. Обычно в таких случаях рекомендуется сочетание опережающего инъектирования с инъектированием после проходки и мероприятиями по водоотводу.
3. СОВРЕМЕННЫЕ ТЕХНОЛОГИИ ЗАКРЕПЛЕНИЯ ГРУНТОВ
В последние годы при строительстве подземных сооружений в сложных инженерногеологических и градостроительных условиях наряду с традиционными технологиями закрепления грунтов (см. п. 2) все более широкое применение находят такие технологии, как струйная цементация грунтов, компенсационное нагнетание, термическая обработка грунтов.
3.1. Струйная цементация грунтов
Основы струйной цементации грунтов с помощью мониторов достаточно подробно изложены в работе [8, п. 2.7]. В настоящем пособии приводится зарубежный и отечественный опыт применения струйной технологии при устройстве противофильтрационных завес, дренажей, свайных фундаментов, стен подземных сооружений, ограждающих конструкций и т.п.
3.1.1. Основные сведения о работе струйного монитора
Работа струйного монитора заключается в превращении потенциальной энергии воды в кинетическую, которая используется для разрушения грунта. Формирование водяной струи происходит при истечении ее через сопла струйного монитора.
Так как потенциальная энергия воды должна быть возможно полнее преобразована в кинетичеcкую энергию струи, то в мониторе и соплах не должно возникать вихреобразных движений, а сама струя должна сохранять цилиндрическую форму и компактность на возможно большем расстоянии от сопла.
Как показывают исследования, наиболее компактную и энергоемкую струю дают конические сопла с углом конусности, равным 13°, и с цилиндрической направляющей частью на конце, служащей для уменьшения сжатия струи на вылете во избежание ее разбрызгивания (рис. 3.1). Такие сопла называют коноидальными.
Экспериментальным путем установлено, что длина цилиндрической направляющей части коноидального сопла должна равняться его четырем диаметрам. При большей длине цилиндрической направляющей части становится ощутимой потеря напора.
В зависимости от соотношения плотностей струи γст и окружающей среды γср
различают следующие виды струй: свободные незатопленные ( γст > γср ); свободные
затопленные ( γст = γср ); несвободные затопленные ( γст < γср ).
Мониторная струя в зависимости от условий ее работы может быть отнесена к одному из перечисленных видов. Если струя находится под защитой воздушной рубашки, то она работает в свободном незатопленном режиме. Если струя окружена подземной водой или пульпой, то она работает соответственно в свободном или несвободном затопленном режиме.
В связи с этим для мониторных струй справедливы многие гидравлические закономерности, установленные для свободных затопленных и свободных незатопленных струй.
На основании экспериментальных исследований сделан вывод, что скорость воздуха на выходе из сопла должна быть не менее 130–150 м/с; оптимальной можно считать скорость, равную примерно 300 м/с (скорости распространения звука).
При сверхзвуковых скоростях движения воздуха, несмотря на то, что в этом режиме интенсифицируется распад струи, величина предельной длины прорези все же получается несколько большей, чем при скоростях, близких к скорости звука.
Изменение диаметра воздушного сопла слабо влияет на предельную длину прорези. Однако при выборе размера воздушной щели в мониторе необходимо учитывать, что она должна обеспечить пропуск необходимого объема воздуха с заданной минимальной скоростью.
Длина образующейся в грунте прорези пропорциональна диаметру сопла и скорости истечения струи. Изменение одного из этих параметров ведет к пропорциональному изменению длины прорези.
Увеличение среднего размера частиц грунта или увеличение гидростатического давления подземной воды приводит к уменьшению длины прорези.
Длина прорези зависит от скорости подъема монитора: с увеличением скорости подъема длина прорези уменьшается, при этом уменьшается также ее ширина.
Гидравлическими струями можно разрабатывать и укреплять различные грунты. Для эффективного образования щелей или частичного разрушения необходимо знать прочностные характеристики грунта, показатели их размываемости. Установлено, что разрушение грунта начинается в тот момент, когда давление струи в контакте составляет (0,25–0,5)σсж, где σсж — предел прочности грунта на одноосное сжатие.
С целью увеличения эффективности действия водяной струи в нее можно вводить водорастворимые полимеры (например полиэтиленоксид или полиакриламид) в соотношении 0,005–0,1 % от массы воды.
Наличие в воде полимеров снижает гидродинамическое сопротивление трубопроводов, благодаря чему увеличивается скорость движения воды в мониторе и на вылете ее из сопла.
Скорость вылета струи в значительной степени зависит от качества обработки и состояния внутренней поверхности сопла. Материал сопла должен противостоять быстрой коррозии и износу, а внутренняя поверхность его должна быть отполирована, чтобы свести до минимума трение на контакте. С этой целью устраивают футеровку сопла из минералов, обладающих большой твердостью.
Хорошие результаты могут быть получены при нанесении на отполированную внутреннюю поверхность сопла кремнийорганичесих соединений, трение на такой поверхности по сравнению с простой полированной уменьшается в 3–5 раз.
3.1.2.Опыт применения струйной технологии
3.1.2.1.Зарубежный опыт
Впрактике зарубежного метро- и тоннелестроения в последние годы все более широкое применение находит метод струйной цементации грунтов.
Вчастности, в Милане (Италия) при строительстве метрополитена в неустойчивых грунтах проходку тоннелей осуществляют под защитой грунтобетонного контура, сооруженного по технологии Rodinjet — струйной цементации, разработанной фирмой «Rodio» (Италия). Сущность этой технологии — в использовании высокоскоростной струи стабилизирующей смеси для размыва и перемешивания грунта в массиве с целью получения его новых физико-механических свойств.
Взависимости от состояния, консистенции и размеров составляющих материалов грунта он может перемешиваться под воздействием воздушных и водяных струй с одновременным замещением закрепляющим составом.
По информации фирмы технология применима для обработки любых грунтов — от гравия до глины (даже посредством обычных цементных растворов). Принудительным перемешиванием стабилизирующим составом можно получить эффективное упрочнение грунтов, преодолевая проблемы проницаемости и неудобства режимов нагнетания другими способами. Считается, что технологией струйной цементации предложена
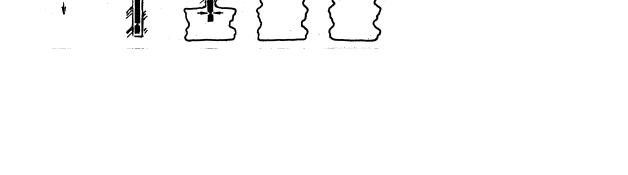
неплохая альтернатива обычной цементации, замораживанию и другим традиционным методам упрочнения грунтов.
Последовательность операций, необходимых для образования защитного контура, состоящего из вертикальных грунтобетонных столбов упрочненного грунта, показана на рис. 3.2.
Рис. 3.2. Последовательность работ для создания защитного контура
Первая операция — бурение скважины заданным способом. По достижении требуемой ее глубины, не прекращая вращение и не поднимая буровой став, переключают установку на работу в режиме струйной цементации (операция вторая). По буровому ставу от высоконапорной насосной установки подают водоцементный раствор под давлением до 70 МПа к одной или двум парам насадок, расположенных диаметрально на мониторе непосредственно за породоразрушающим инструментом. Высокоскоростные струи истекающего через насадки раствора размывают и перемешивают грунт (операция третья). Не прекращая вращения монитора, начинают поднимать из скважины, с определенной скоростью буровой став (операция четвертая). При этом подаваемый в скважину раствор действует одновременно как разрушающая среда стабилизирующий агент, образуя грунтобетонный столб (операция пятая) с размерами и физикомеханическими свойствами, зависящими от совместного влияния грунта и состава закрепляющей смеси: расхода смеси и давления, отнесенных к количеству и размеру насадок; скорости подъема и частоты вращения бурового става.
Диаметр грунтобетонных столбов — обычно 0,4–0,8 м, но может быть увеличен до 2 м и более посредством чередующегося технологического процесса. Он включает воздушные и водяные струи, истекающие из второй пары насадок, через которые нагнетается раствор.
Оборудование для производства работ выбирают в соответствии с грунтовыми условиями, особенностями строительной площадки, проектными данными по глубине и наклону скважин. Для проходки последних в тонко- и среднезернистых грунтах отдают предпочтение легким станкам вращательного бурения. Использование вращателя с гидропатроном в сочетании с автоподатчиком станка длиной 4–5 м позволяет бурить одной штангой скважины глубиной 16–17 м. В крупнозернистых грунтах с включением валунов целесообразнее ударно-вращательное бурение. Однако эта технология требует более тяжелых буровых станков с автоподатчиками такой же длины, как и буровые штанги.
В Италии по рассматриваемой технологии сооружено несколько стволов диаметром 8– 12 м, глубиной до 22 м и до 15 м ниже уровня грунтовых вод. Они заложены в обломочных грунтах с широким распределением по фракциям, включая валуны, и с проницаемостью от низкой до очень высокой.
Струйную цементацию неустойчивых грунтов применили также на строительстве в центре Милана двухпутных перегонных тоннелей третьей линии метрополитена. Конструкции подковообразного очертания пролетом 10,5 м и высотой 8,5 м заложены в гравийно-песчаных отложениях с прослойками ила и глины. Учитывая сложные условия, проходку вели под защитой опережающей крепи с пилот-тоннелем шириной 3 м и высотой 3,2 м, из забоя которого по контуру верхней части бурили наклонные скважины длиной 9 м с шагом 0,4 м, и устраивали конические своды из закрепленного грунта толщиной 0,7 м (рис. 3.3).
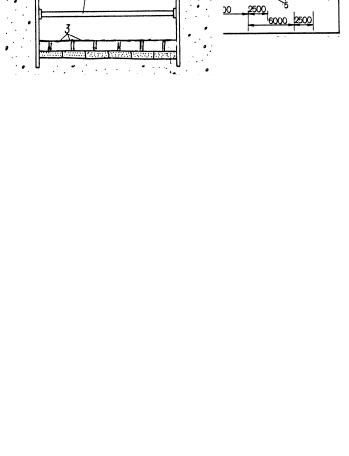
Рис. 3.3. Схема закрепления грунта по трассе перегонного тоннеля метрополитена:
1 — цементационная завеса; 2 — веерные скважины; 3 — опережающая крепь; 4 — пилот-тоннель; 5 — контур перегонного тоннеля
Широкое применение метод струйной цементации «jetgro-uting» находит в Японии. Общий объем работ по устройству противофильтрационных завес (ПФЗ) с использованием струйной технологии в этой стране превышает 200 тыс. м2, а несущих конструкций в виде
свай круглого сечения приближается к 100 тыс. м3. |
|
|
|
|
|||
Оригинален |
|
разработанный строительной фир- |
|||||
мой |
«Кайима» |
|
(Япония) |
способ |
сооружения |
||
|
|
|
противофильтрационных завес в |
||||
горизонтальной |
|
плоскости. |
Достигается |
это |
|||
устройством |
|
взаимно пересекающихся плоских |
|||||
доскообразных |
|
плит на проектной глубине путем |
|||||
вращения |
|
опущенного в скважину струйного |
|||||
монитора вокруг |
|
его вертикальной оси с подъемом |
|||||
на |
небольшую |
|
высоту (рис. 3.4). |
|
|
||
Широкие |
Рис. 3.4. Устройство |
возможности |
этой |
технологии |
|||
|
|
|
|
|
|
||
помогают |
противофильтрационной завесы в |
строителям |
разрешить |
следующие |
|||
проблемы: |
горизонтальной плоскости: |
|
|
|
|
||
— |
сооружение |
1 — шпунтовая стенка; 2 — распорки; |
стен ограждения котлована |
в |
|||
3 — скважины |
|||||||
условиях |
существующей плотной застройки |
||||||
|
городских центров. В качестве ограждения используются грунтоцементные вертикально секущиеся, соприкасающиеся либо отдельно стоящие (в зависимости от гидрогеологических условий) колонны, армированные стальными трубами;
—укрепление естественных оснований с целью повышения прочностных свойств природных грунтов;
—усиление любых типов фундаментов при реконструкции зданий и сооружений, реставрации памятников архитектуры при строительстве заглубленных и подземных сооружений в условиях существующей застройки густонаселенных городских центров.
В частности, при строительстве основного и сервисного тоннелей метрополитена под монументом на площади «Маргуис де Помбал» в столице Португалии г. Лиссабоне на линии между станциями «Ротунда» и «Рато» для закрепления грунтов в основании монумента с помощью струйной цементации было пробурено более 13,3 тыс. м скважин с углом наклона от 0 до 68° и сооружено 786 грунтоцементных колонн диаметром 1,0 м по двухкомпонентной (воздушной) системе и 102 грунтоцементные колонны диаметром 0,6 м по однокомпонентной системе (рис. 3.5).
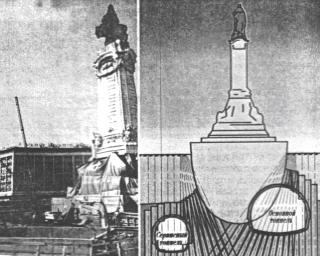
Рис. 3.5. Закрепление грунтов в основании монумента
3.1.2.2.Отечественный опыт
ВСоветском Союзе струйная технология впервые была применена в 1977 г. в Днепровском строительном управлении Всесоюзного объединения «Гидроспецстрой» Минэнерго СССР.
При разработке струйной технологии в СССР приняты технологические параметры, более оптимальные, чем за рубежом. Эти параметры (расхода и скоростей размывающей жидкости и воздуха) соответствовали параметрам серийно выпускаемого отечественного оборудования.
ВГидроспецпроекте сконструированы и изготовлены (на опытном заводе «Гидроспецстрой») струйные установки для сооружения противофильтрационных завес и ячеистых конструкций — «Струя-12», «Струя-25», «Струя-60» (цифры в названиях показывают глубину разработки в метрах).
Большой объем научно-исследовательских работ по внедрению новой технологии был выполнен специальными НИИОСП Госстроя СССР.
Вчастности, ими была создана установка, предназначенная для устройства противофильтрационных завес глубиной до 20 м в нескальных грунтах с использованием водяной струи высокого давления [см. 6, п. 2.7.2]. Наиболее предпочтительно (с точки зрения производительности) применение установки в песчаных, песчано-гравелистых, супесчаных и суглинистых грунтах, но она может работать и в более плотных грунтах. Допускаются твердые включения в грунте размером в поперечнике не более 100 мм.
Установка состоит из двух частей (рис. 3.6) — базовой машины и навесного оборудования. В качестве базовой машины могут быть использованы краны МКГ-25, ДЭК-251 с копровыми стойками или им подобные.
Навесное оборудование представляет собственно струйный монитор, состоящий из мониторной головки и опускной колонны. Верх опускной колонны прикрепляют к каретке, перемещающейся вертикально по копровой стойке, для чего на последней устраивают направляющие из металлических уголков.
Мониторная головка диаметром 150 мм выполнена в виде двух концентрических цилиндров. В полость внутреннего цилиндра подается вода, а в пространство между цилиндрами — сжатый воздух. В стенках цилиндров соосно установлены на резьбе соответственно водяные и воздушные сопла.
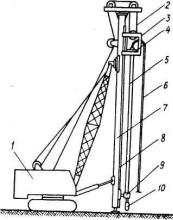
Рис. 3.6. Струйная установка:
1 — базовая машина; 2 — полиспастная подвеска; 3 — каретка; 4 — опорно-поворотный фланец; 5 — опускная колонна; 6 — напорные рукава; 7 — копровая стойка; 8 — направляющие
уголки; 9 — нижняя опора; 10 — головка монитора
Опускная колонна наружным диметром 114 мм состоит из трех труб, расположенных одна в другой. По внутренней трубе подается раствор, в кольцевом зазоре между стенками внутренней и средней труб — вода, а между стенками средней и внешней труб — сжатый воздух.
Конструкция струйного монитора рассчитана на рабочее давление воды 20 МПа и обеспечивает ее расход до 200 л/мин.
Установка позволяет прорезать в грунте щели длиной от 3 до 5 м (в одну сторону) при ширине 5–15 см. Скорость прорезания щели по высоте составляет 0,4–0,6 м/мин.
Струйную установку описанной конструкции можно рекомендовать строительным организациям для широкого применения при устройстве противофильтрационных завес (рис. 3.7).
При оснащении трехили четырехсопловой мониторной головкой (с размещением сопел соответственно через 120° и 90°) установка может быть использована для устройства соответственно трех- и четырехлопастных (крестообразных) свай, а при оснащении вертлюгом, обеспечивающим подачу воды, воздуха и раствора, и приводом вращения — для устройства цилиндрических и винтовых свай в качестве несущих конструкций [см. 8, п. 2.7.3]. В последнем случае установку можно использовать для ускоренного замачивания просадочных грунтов через скважину с целью их уплотнения.