
745
.pdf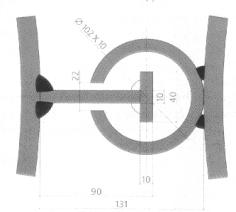
по «джет-технологии».
Поперечные сечения тоннелей приняты с учетом габарита приближения строений и оборудования.
Длина тоннелей определилась шириной железнодорожных насыпей в месте пересечения. Постоянные конструкции тоннелей также однотипны: в тоннеле на 1435 км лоток, стены и перекрытие выполнены из монолитного железобетона класса ВЗО, морозостойкостью F-200, водопроницаемостью марки W10. В отличие от первого для перекрытия тоннеля на 1442 км использованы в качестве конструкций трубы защитного экрана, заполненные монолитным бетоном с установкой арматурных каркасов и поперечные металлические балки рам временного крепления.
Конструкции фундаментов несколько различаются:
•разные инженерно-геологические условия;
•различная высота насыпей;
•наличие бурового оборудования для изготовления грунтоце-ментных свай. Фундамент тоннеля на 1435 км выполнен из монолитного железобетонного лотка,
сплошного защитного экрана из металлических труб диаметром 1020 мм, заполненных монолитным бетоном, грунтоцементных свай диаметром 0,6–0,7 м, устроенных с шагом 2 м через отверстия, вырезанные в замках труб защитного экрана. Защитный экран в лотковой части тоннеля был выполнен для предотвращения выдавливания слабых грунтов основания (торфов) внутрь тоннеля при его проходке.
Расчетная величина выпучиваемых грунтов в случае отсутствия экрана составляла 80 см. Грунтоцементные сваи, армированные металлической трубой диаметром 59 мм, прорезали слабые грунты и опирались на галечник и твердые аргиллитоподобные глины. Несущая способность одиночной сваи по данным испытаний составила 63 т.
Фундаменты тоннеля на 1442 км из грунтоцементных свай большей частью были выполнены до устройства защитного экрана одновременно с усилением грунтов тела тоннеля и его основания. Под крайние стены тоннелей было предусмотрено два ряда вертикальных и наклонных свай, под средней — три ряда, кроме опережающих грунтоцементных вертикальных и наклонных свай, расположенных под 60 % лотка тоннеля на участках слабых текуче- и мягкопластичных суглинков. Более слабое основание южного пролета тоннеля было усилено двумя рядами горизонтальных грунтоцементных свай при проходке тоннеля. Дополнительные вертикальные сваи выполнялись при проходке тоннеля по результатам освидетельствования грунтов основания при их обнажении.
Конструкции защитных экранов также несколько различаются. Защитный экран тоннеля на 1435 км устроен из металлических труб диаметром 1020 мм по всему контуру тоннеля. Трубы связаны между собой шпунтовым соединением (замком). Замок сконструирован из разрезанной трубы диаметром 102 мм, приваренной вдоль трубы диаметром 1020 мм, с противоположной стороны — сварной тавр (рис. 4.16).
Узел замка труб
Рис. 4.16. Шпунтовое соединение труб
При сооружении тоннеля на 1442 км защитный экран задавлен только в стенах и перекрытии: в стенах — из труб диаметром 1020 мм, в перекрытии — из труб диаметром 600 мм в связи с недостаточным расстоянием до верхнего строения пути железной дороги.
Влотковой части тоннеля продавлено только по две трубы у наружных стен и по одной
вкаждом пролете у центральной. Эти трубы предназначены для опирания колонн рам временного крепления и пропуска коммуникаций.
Рамы временного крепления были запроектированы и выполнены из сварных индивидуальных балок. При расчете шаг рам был назначен 2 м, величина заходки — 2 м, угол заложения откоса забоя — 45°.
C учетом необходимости проходки в слабых неустойчивых грунтах в обоих случаях предусматривалось закрепление грунтов в теле проектируемых тоннелей.
При сооружении тоннеля на 1435 км его тело было предложено крепить с использованием химических реагентов на основе карбамидной смолы, отверждаемой щавелевой кислотой. Для инъекции скрепляющего состава в тело насыпи была запроектирована сеть скважин, состоящая из горизонтальных и наклонных перфорированных труб, забитых в песчаный грунт на глубину 15 м с помощью пневматических ударных машин. Трубы забивали со стороны портала навстречу друг другу. В связи с ограниченностью длины труб, «мертвую» зону грунта инъектировали с помощью вертикальных труб, которые предполагалось забивать после проходки верхнего уступа. Непосредственному выполнению работ предшествовали лабораторные и опытно- промыш-ленные работы по подбору оптимальных инъекционных составов для фактических грунтов насыпи. Эти мероприятия позволили успешно выполнить проходку тоннеля.
Крепление грунтов в теле тоннеля на 1442 км было предусмотрено с учетом опыта строительства предыдущего тоннеля, а также новой технологии и оборудования, имеющихся в наличии у генподрядчика. Данной технологией являлось устройство как вертикальных, так и горизонтальных грунтоцементных свай.
Учитывая более сложные геологические условия грунтов, залегающих в основании тоннеля, закрепление их в теле тоннеля предполагалось производить в два этапа.
На первом, когда осуществлялось продавливание труб в стены защитного экрана, производилось закрепление грунтов вертикальными грунтоцементными сваями, устанавливаемыми с поверхности железнодорожной насыпи. На втором — устанавливались горизонтальные грунтоцементные сваи, которые бурились как из портальных частей тоннелей, так и непосредственно из забоя во время проходки тоннеля. Помимо этого, горизонтальные сваи частично армировались фибергласовыми анкерами. Их установка ограничивала длину заходки по закреплению грунтов, из-за чего были предусмотрены три технологические остановки при проходке тоннеля для закрепления грунтов. В этот период выполнялись иные подготовительные работы, сопутствующие проходке. В процессе производства закрепления грунтов уточнялись только составы смесей и регламент выполнения работ. Все это позволило осуществить проходку обоих тоннелей на все сечение высотой 8,5 м без проведения дополнительных мероприятий.
Сооружение защитного экрана — одна из наиболее ответственных и дорогостоящих операций в строительстве тоннелей по рассматриваемой технологии. Для ее выполнения требуется ряд сложных вспомогательных приспособлений и устройств:
•упоры для восприятия горизонтальной нагрузки от домкратов продавливания;
•торцевая стенка крепления откоса насыпи для врезки микрощита;
•приемные подмости на откосе насыпи для приема микрощита;
•подмости для установки рамы продавливания длиной 11,6 м при продавливании труб верхнего ряда (перекрытия) защитного экрана;
•продольная упорная рама для размещения рамы при продавливании стеновых труб защитного экрана;
•поперечная упорная балка для передачи горизонтальной нагрузки от домкратной станции на стеновые трубы и затем на упор;
• стартовые и приемные котлованы при необходимости.
Основной конструкцией для восприятия нагрузок от домкратов является упор.
При строительстве тоннеля на 1435 км для первоочередного задавливания труб в лотке тоннеля был сооружен один общий упор, представляющий собой свайный ростверк на сваях сечением 35×35 см (размеры в плане). В соответствии с техническими условиями фирмы «Herrennecht» упор был запроектирован на горизонтальное смещение не более 0,5 мм при нагрузке от домкратов продавливания 600 т. Фактическая максимальная нагрузка составила 390 т, а после корректировки состава бентонитового раствора, исполняющего роль смазки между задавливаемой металлической трубой и грунтом, — не более 240 т.
Продавливание стеновых труб велось снизу вверх, начиная с лотковых труб. Трубы задавливались через откосы насыпи с устройством микроуступов под каждую трубу. Усилия от домкратов передавались на железобетонный упор через специальную продольную раму, на которой устанавливалась рама продавливания с домкратной
станцией, |
далее |
через |
подмости |
из |
труб |
диаметром |
1020 мм, приваренных к предыдущим продавленным, и затем — на упор. |
|
Для задавливания труб верхнего ряда защитного экрана были выполнены сплошные подмости из металлических балок, опирающиеся на ранее продавленные стеновые трубы,
ипоперечная упорная балка, также передававшая нагрузку от домкратов на стеновые трубы, затем — на железобетонный упор.
Данная технология исключила необходимость изготовления и монтажа мощного упора высотой 10 м или передвигающихся подмостей заводского изготовления, примененных на аналогичном объекте в Москве.
Задавливание труб в тоннеле на 1442 км осуществлялось в следующем порядке: в первую очередь продавливались стеновые трубы с уровня дневной поверхности вверх, затем — трубы по перекрытию. После приступали к задавливанию оставшихся стеновых труб сверху вниз в стартовых котлованах.
Сучетом опыта задавливания труб на первом тоннеле на втором тоннеле были выполнены упоры максимально облегченной конструкции. Было сооружено три небольших упора, расположенных по оси каждой стены защитного экрана. Упоры выполнены из грунтоцементных свай, армированных двумя рядами металлических двутавровых балок. Это позволило значительно уменьшить размеры упоров, эффективно использовать пассивный отпор грунта для восприятия горизонтальной нагрузки и в результате существенно сократить затраты на сооружение упоров.
Проходка тоннеля на 1435 км осуществлялась с помощью комбайна ГПКС двумя уступами: верхний высотой 3,5 м, нижний — 3,9 м.
Проходку верхнего уступа вели заходками длиной 2 м, после чего устанавливали раму временного крепления, и далее цикл повторялся.
Для опирания рам временного крепления верхнего уступа внутри контура тоннеля дополнительно были задавлены четыре трубы в уровне подошвы верхнего уступа: две — по оси тоннеля для опирания временной средней колонны рамы крепления и по одной у стен защитного экрана — для крайних колонн. Наблюдения за деформациями и напряжениями в элементах временного крепления показали, что фактическая максимальная нагрузка на рамы при проходке меньше расчетной, так как инъекционное закрепление массива обеспечило устойчивость забоя при угле заложения 90–75°. Это дало возможность при сооружении нижнего уступа увеличить длину заходки до 4 м.
Последнее обстоятельство также повлияло на принятие проектных решений при строительстве тоннеля на 1442 км. Проходка здесь была запроектирована на полное сечение заходками длиной по 2 м. После разработки грунта на длину заходки устанавливалась рама временного крепления, и далее цикл повторялся. Ввиду сложности исполнения, поддомкрачивание ригеля не проектировалось. Разработка грунта осуществлялась проходческим комбайном «Alpine Westfalia» фирмы «Tamrok» (рис. 4.17)
исразу на полное сечение.
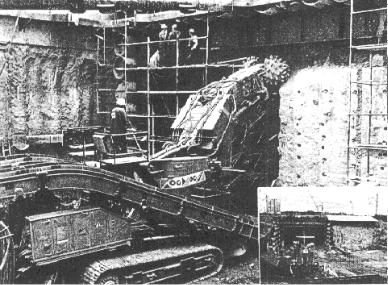
Рис. 4.17. Разработка грунта
Из-за большого удельного давления на грунты лотка тоннеля от проходческого комбайна предусматривалось устройство временного бетонного лотка на каждую заходку.
Для обеспечения безопасности движения поездов во время строительства тоннелей на всех этапах осуществлялся:
•геодезический контроль над деформациями железнодорожной насыпи, верхнего строения пути, возводимых временных и постоянных конструкций тоннеля;
•мониторинг напряженно-деформированного состояния рам временной крепи. Сооружение тоннеля под железнодорожной насыпью без перерыва движения поездов
на напряженной магистрали предъявляло повышенные требования к обеспечению надежной работы крепи. В этих условиях мониторинг рассматривался как неотъемлемая часть технологии строительства тоннеля.
Таким образом, в Перми российскими специалистами, использовавшими современные технологии и оборудование, эффективные материалы, построены автодорожные тоннели под действующей железнодорожной магистралью в сложных инженерно-геологических условиях. Отдельные решения, реализованные на этом объекте, не имеют аналогов не только в российском, но и мировом тоннелестроении.
4.2.4.Устройство защитного экрана
сиспользованием бурошнековой установки
Наряду с известными микротоннелепроходческими комплексами определенного внимания заслуживает опыт применения бурошнековой установки типа РВА-200 на объектах «ГПР-1» в Москве [Метро и тоннели. 2004. № 3. С. 26–31].
ОАО «ГПР-1» до приобретения установки РВА-200 применяло для продавливания труб диаметром 1200 и 1400 мм немеханизированные установки, которые состояли из двух гидродомкратов ГД-170 (ГД-175) общим усилием 340 т, установленных на сварной раме, маслостанции с насосом высокого давления и контрольных приборов. Грунт в забое разрабатывался отбойными молотками или ручным инструментом с погрузкой его в опрокидные вагонетки и ручной откаткой к рабочему котловану с дальнейшей выдачей на поверхность краном.
Разработки по созданию установок с технологией по продавливанию труб и шнековой транспортировкой разбуренного грунта как альтернатива немеханизированной и различным механизированным технологиям были начаты в середине 80-х гг. С тех пор эта технология постоянно совершенствуется.
Использование установки РВА-200 позволило расширить область распространения способа продавливания труб в различных грунтах, увеличить длину и скорость проходки, сократить применение ручного труда.
В отличие от метода ведения работ открытым способом, она не нарушает поверхность по всей трассе прокладки коммуникаций и тем самым не влечет за собой закрытие

транспортного и пешеходного движения, вырубку садово-парковых насаждений и пр. Преимущество этой технологии перед подземной проходкой щитами, применяющейся
в настоящее время при строительстве коллекторов, состоит в том, что она не требует длительного подготовительного и основного этапов, связанных со строительством шахт и тоннелей.
Основное отличие от микротоннелирования заключается в отсутствии герметичной буровой головки, роль которой выполняет режущая головка, и в откатке грунта шнеками, для которых сама труба задавливания является кожухом. Установка шнекового бурения лишена большой части сложного и дорогостоящего оборудования, имеющегося на установках микротоннелирования, и соответственно более проста в обслуживании.
Среди технических решений, позволивших шнековым установкам приблизиться к установкам микротоннелирования, можно выделить автономность работы, шнековый шлюз для продавливания труб при высоком уровне грунтовых вод, различные режущие головки, позволяющие их заменять в ходе работы, управление траекторией проходки, возможность применения ударного механизма при работе в твердых и скальных породах.
Немецкая компания «SCHMIDT, KRANZ & CO GMBH» производит ряд установок горизонтального шнекового бурения от РВА-10 до РВА-320, которые применяются для бестраншейной прокладки трубопроводов или футляров диаметром от 100 до 1600 мм (табл. 4.2).
Таблица 4.2
Технические характеристики РВА-80/100/160/200/240/320
Показатели |
РВА-80 |
РВА-100 |
РВА-160 |
РВА-200 |
РВА-240 |
РВА-320 |
|
|
|
|
|
|
|
Домкратная станция: |
|
|
|
|
|
|
рабочее давление, бар |
250 |
250 |
250 |
250 |
200 |
250 |
ход штока, мм |
600 |
600 |
600 |
600 |
600 |
600 |
усилие подачи, кН |
800 |
1000 |
1570 |
2000 |
2450 |
3200 |
усилие тяги, кН |
600 |
600 |
1175 |
600 |
1175 |
2300 |
|
|
|
|
|
|
|
Бурильный агрегат: |
|
|
|
|
|
|
рабочее давление, бар |
200 |
240 |
220 |
220 |
200 |
250 |
крутящий момент, Нм |
15000 |
20000 |
30000 |
35000 |
50000 |
31500/63000 |
скорость вращения, |
|
|
|
|
|
|
об./мин |
30/60 |
22/44 |
30/60 |
22/44 |
25 |
9/32 |
|
|
|
|
|
|
|
Размеры: |
|
|
|
|
|
|
длина машины, м |
5,005 |
5,005 |
5,525 |
5,525 |
6,300 |
7,780 |
длина удлинителя, м |
4,0/6,0 |
4,0/6,0 |
4,0/6,0 |
4,0/6,0 |
4,0/— |
3,12/4,16 |
ширина, м |
1,26 |
1,42 |
1,70 |
1,7/1,9 |
2,160 |
2,240 |
|
|
|
|
|
|
|
Масса: |
|
|
|
|
|
|
без инструмента, кг |
2550 |
2800 |
3760 |
4000 |
8200 |
11700 |
удлинителя рамы 4 м / |
|
|
|
|
|
|
5 м, кг |
800/1100 |
880/1180 |
1430/1890 |
1580/2000 |
8200/2360 |
2250/2650 |
|
|
|
|
|
|
|
Впервые в России такие установки были применены при строительстве коммуникационного тоннеля под трамвайными путями под 1-м Боткинским проездом в Москве [Метро и тоннели. 2004. № 5. С. 40–42].
Сотрудниками Специализированного управления № 19 ОАО «ГПР-1» была проведена грамотная инженерная подготовка для выполнения этой работы. Созданы бригады по обслуживанию бурошнековой установки из квалифицированных работников различных специализированных управлений ОАО «ГПР-1». Изготовлены приспособления для перемещения машины поперек котлована без отклонения от заданных маркшейдером осей, направляющие для продавливания трубы между двумя уже пройденными, специальные леса и тележки и многое другое, что позволило максимально устранить ручной труд и сократить время проведения одного цикла.
Персонал заранее был обучен немецкими специалистами с выдачей удостоверений и сертификатов.
После всех принятых мер, работа была организована в две смены. Необходимо отметить, что отклонения в плане и профиле труб длиной 21,5 м не превышало ±3 см. Качество работ в большой степени зависело от квалификации обслуживающего персонала и сварочных соединений стальных труб.
Во время проходки под дорогой неоднократно встречались непредвиденные препятствия: кирпичный колодец, бетон, камни и т.д. Но несмотря на это были получены высокие показатели. Так, например, время, затрачиваемое на один цикл, включающий в себя продавливание трубы длиной 21,5 м со сварными соединениями через каждые 3 м, бурение пилотштанги и перестановку машины на новую ось, занимало 24 ч. Непосредственно проходка без других технологических операций осуществлялась со скоростью от 32 до 100 мм/мин.
Бурошнековая установка РВА-200 эксплуатировалась с 24 апреля 2003 г. по 24 апреля 2004 г. За этот период в Москве было сделано 1 736 м проколов различного назначения, в том числе для канализации, водостока, водопровода и т.д.
Из них стальных труб диаметром 600 мм — 450 м, диаметром 800 – 1111 м, диаметром 1200 –175 м.
Всего в ОАО «ГПР-1» за год продавили 5351,4 м труб-фут-ляров, из них на долю бурошнековой установки пришлось 32 %.
Вконце апреля 2004 г. ОАО «ГПР-1» закупил и ввел в эксплуатацию более мощную бурошнековую установку РВА-320 с усилием подачи 320 т.
Принцип действия таких установок основан на сочетании разработки грунта режущей головкой или расширителем и транспортирования его шнеком с одновременным вдавливанием трубы-футляра.
Конструкция рамы и домкратной станции дает возможность выполнять работы из стартовых шахт как круглого, так и прямоугольного сечения.
Перед производством работ по продавливанию футляров (труб) предварительно оборудовался рабочий (стартовый) и приемный котлованы (камеры, шахты).
Размеры котлованов определялись в зависимости от их расположения в застроенной части города или на свободной территории с учетом грунтовых условий и размеров бурошнековой установки.
Встесненных условиях городской застройки котлованы, как правило, разрабатывали с предварительным забуриванием вертикальных труб диаметром 219 мм и креплением деревянной затяжкой между ними, поясами через 2 м, состоящими из двутавров № 30–40, укосин и расстрелов из труб или двутавров.
Размеры камер для продавливания футляров длиной 3 м были равны 6,5×4,0 м, а для 6 м составляли 10,5×4,0 м.
Кроме того, для проколов сооружались стволы (шахт) диаметром 5,5 и 7,5 м. Крепление осуществлялось инвентарной крепью из швеллерных колец с деревянной затяжкой.
При проходке стволов диаметром 5,5 м в основании шахты устраивался карман (приствольная камера) с углублением 2 м под бурошнековую установку для задавливания труб длиной 3 м. Карман крепился швеллерами или двутаврами.
Приемные шахты строились диаметром 3 м и крепились инвентарной крепью из швеллерных колец и деревянной затяжки.
Котлованы разрабатывались гидравлическими экскаваторами с обратной лопатой или с грейферным ковшом, а также вручную отбойными молотками, бадьями и краном СПК-1000 (СПК2000).
Глубина котлованов, камер, шахт колебалась от 3 до 9 м.
К установке разработали и сварили опорную плиту длиной 2,5 и высотой 2 м, представляющую собой пакет из сваренных металлических балок № 20 и стального листа δ = 20.
Опорная плита служит для равномерного распределения реактивных усилий от продавливающих гидродомкратов на упорную стенку рабочего котлована, в котором днище бетонировалось по отметкам в соответствии с применяемым оборудованием или укладывались железобетонные плиты
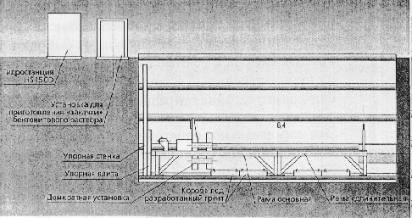
под раму установки для продавливания. В торце котлована устраивалась упорная стенка из двух-трех забуренных стальных труб диаметром 219×12 мм с шагом 1,2–1,4 м и защемлением в грунте днища камеры 0,5–1,5 м, двух вандрутов из металлических двутавров № 22 с омоноличенным пространством между ними и установленной упорной плитой.
На днище рабочего котлована монтировалась буровая установка. При этом рама монтировалась с соблюдением проектного уклона, а упорная плита должна быть строго перпендикулярна к уклону продавливания (рис. 4.18). Данные работы производились с привлечением маркшейдерской службы.
Рис. 4.18. Разрез стартовой камеры
Технологическая последовательность работы бурошнековых установок одна и та же: проходка пилотной скважины, направляемой с помощью лазерной системы наведения, расширение скважины до необходимого диаметра рабочим органом со шнековой транспортировкой грунта в котлован и задавливание рабочей трубы.
Существует управляемое бурение 2- и 3-ступенчатым способом.
Первый этап — направленное задавливание пилотных штанг. Для этого используется оптико-электронная навигационная система ОЭН. Передний конец пилотной трубы оснащен управляющей головкой со скошенным наконечником, поворот которого позволяет осуществлять движение в заданном направлении. Кроме того, в первой бурильной штанге имеется лазер с мишенью (перфолюкс) и две форсунки для подачи бентонита вперед по направлению продавливания и назад.
Для улучшения наблюдения за целью сзади за ригельным мостиком предусмотрена камера на специальной подставке, не подверженной вибрациям. Она должна быть зафиксирована или установлена на песчаной подушке поверх бетонной плиты.
В удобном для наблюдения за мишенью месте монтируется стол, на котором крепится монитор, соединенный с пультом управления. С его помощью оператор последовательно контролирует и регулирует параметры проходки в вертикальном и горизонтальном направлениях.
Система управления обеспечивает точность проходки с допусками ±30 мм.
Далее осуществляется пилотное бурение. Для этого используются пилотные трубы РВ37 диаметром 114,3 мм и длиной 1 м, которые соединяются с помощью резьбовых соединений.
Важный элемент пилотных штанг — водонепроницаемость за счет резиновых прокладок.
При пилотном бурении следят за резким увеличением давления и внезапным отклонением от цели. Работу установки прекращают, если пилотная штанга, встретив препятствие в виде камня, может изогнуться и деформироваться. За счет проворачивания и легкого нажима стараются пройти препятствие или направляют промывочную струю через форсунку на камень так, чтобы размочить грунт и вытеснить камень.
Проходка осуществляется до выхода пилот-штанги в приемочный котлован. Проверяется точность прокола, демонтируются направляющая головка плотных труб и
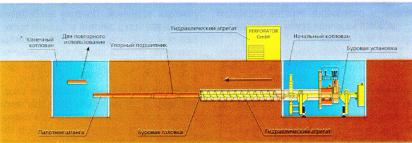
система ОЭН.
Затем буровая установка переоснащается для продавливания стальных или бетонных труб.
Второй шаг заключается в усилении режущей кромки трубы или применении различных расширителей.
Для этого на стальную обсадную трубу наваривается стальная обечайка толщиной 10– 15 мм и шириной 8–10 см. Внутрь торца трубы вваривается крест («вертолет») с переходником для пилот-штанг. Толщина листа 2 см.
Возможно использование расширяющей головки с ребрами жесткости и переходником для пилотных штанг. Это приводит к уменьшению сил трения, возникающих при продавливании.
При применении буровой головки (рис. 4.19, а) в крепких породах в качестве переходника используется упорный подшипник. Для снижения усилия вдавливания диаметр фрезерной головки делают на 10–50 мм больше диаметра продавливаемой трубы. Длину первой секции подбирают таким образом, чтобы фрезерная головка выходила из футляра на 5–10 см. Для снижения сопротивления грунта по боковой поверхности продавливаемого футляра за расширителем или режущим кольцом устанавливается полудюймовая труба с 6 мм отверстиями через 20 см для нагнетания раствора бентонита в затрубное пространство.
Затем к пилотной штанге через переходник присоединяется расширитель и стальной футляр с проложенными внутри шнеками. Начинается продавливание обсадных труб с непрерывным удалением породы шнеком из забоя в стартовый котлован. Колонна пилотных штанг, по мере проходки, выдавливается стальным футляром с помощью домкратов в приемную камеру. Штанги отвинчиваются и складируются для дальнейшего использования.
Прокол осуществляется на длину 3 или 6 м, после чего на домкратную станцию помещается следующий отрезок стального футляра той же длины, трубы свариваются и процесс повторяется.
Трубы должны быть обрезаны ортогонально, а сварные швы выполнены качественно.
Путем наращивания футляров отрезками по 3 или 6 м производится дальнейшая проходка выработки до выхода расширителя в приемный котлован. Расширитель срезается для повторного использования, из трубы извлекаются шнеки, установка демонтируется.
Грунт из стартовой камеры выдавался автокраном поддонами размером 1,4×1,4×0,3 м, которые размещались под установкой во время прокола или грейферным экскаватором с погрузкой в автосамосвалы.
В проложенные стальные футляры вставляются полимерные трубы, свариваются и забутовываются цементным раствором.
Третий этап при трехступенчатом способе заключается в расширении диаметра трубы с повторно используемыми буровыми трубами или замещении стальных труб-футляров выдавливанием железобетонными трубами. При продавливании рабочих железобетонных труб использовались различные расширители и переходники (рис. 4.19, б).
а)
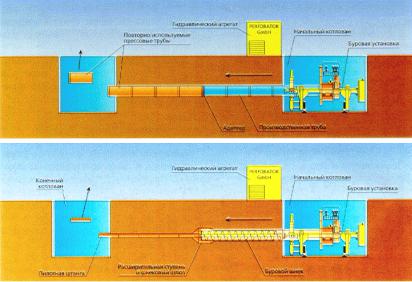
б)
в)
Рис. 4.19. Схемы продавливания производственных труб
сприменением бурошнековой установки:
а— расширительная ступень с использованием подшипника и буровой головки для двухступенчатого метода при
крепких породах; б — продавливание труб
содновременным извлечением прессовых при трехступенчатом методе;
в— расширительная ступень и шнековый шлюз для двухступенчатого метода ниже уровня грунтовых вод
Особо следует отметить применение шнекового шлюза, потому что бурошнековые установки в силу конструктивных особенностей не всегда обеспечивают надежную работу в обводненных условиях (рис. 4.19, в).
При работе ниже уровня грунтовых вод шнек открывает переднее «окошко» и грунт с водой поступает в шнековый став, при этом заднее «окошко» закрыто.
Затем шнек перекрывает переднее «окошко», а заднее открывает и грунт с водой, находящийся в шнековой камере, отводится шнеками в трубу и далее в рабочий котлован.
Вэтот момент вода в камеру шнекового шлюза не поступает. Затем процесс повторяется.
Рекомендации фирмы — перед заталкиванием трубы в грунт ее следует обмазывать вручную бентонитом сметанообразной консистенции, но при этом сводятся на нет все преимущества механизированного способа проходки.
Использованию бентонитовой смазки при продавливании футляров долгое время не придавалось особого значения. Как следствие, это приводило к слишком высокому поверхностному трению, что нередко заканчивалось повреждением трубопровода или остановкой работы бурошнековой установки. Приходилось навстречу из приемного котлована осуществлять прокол трубой большего диаметра или проходить шахту на месте предполагаемой остановки расширительной (буровой) головки.
Втечение нескольких последних лет были осуществлены разработки, направленные на уменьшение поверхностного трения. Оно уменьшается при использовании смесительных установок, выдающих бентонит, готовый к употреблению, и передающих его далее в
места трения.
Бентонитовый узел состоит из емкости 1 м3, смесителя шнекового типа, насоса для
подачи бентонитового раствора производительностью до 30 л/мин и давлением до 100 кг/см2.
Привод смесителя и насоса идет от гидравлической станции. Плотность и вязкость бентонитового раствора подбирается в зависимости от грунтов.
С помощью автоматических установок возможно уменьшение поверхностного трения до величины 1 т/м2. В то время как при плохой смазке нередки случаи, когда поверхностное трение достигает величины 2 т/м2, а иногда и более — в сухих песках и твердых глинах.
Бентонит нельзя применять в пучащих глинах, потому что происходит резкое
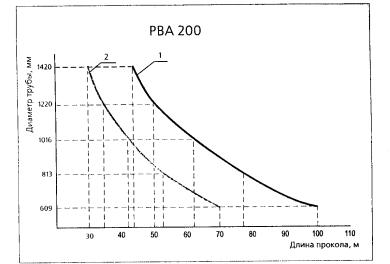
увеличение обжима трубы и остановка работы машины.
Зависимость длины прокола от диаметра трубы с применением бентонита и без него представлена на рис. 4.20.
Рис. 4.20. Зависимость длины прокола от диаметра трубы: 1 — с применением бентонита; 2 — без применения бентонита
Определенный интерес представляет опыт сооружения защитного экрана из труб на ст. «Маяковская» в Москве [Метро и тоннели. 2005. № 2. С. 16–19].
Строительство второго выхода станции Московского метро «Маяковская» велось в сложных инженерно-геологических условиях, обновленных наличием толщи песков и известняков, являющихся водообильными горизонтами грунтовых вод. Тоннель возводился в водонасыщенных грунтах закрытым способом [9, п. 3.2.2].
По данным инженерно-геологических изысканий 1949 г. свод тоннеля 4-го коридора располагается в юрских глинах. Поэтому в проекте было принято решение сооружать 4-й коридор под защитой сплошного экрана из 21 трубы диаметром 325 мм с замками. По расчетам НИЦ ТМ осадки в самом неблагоприятном месте на поверхности в этом случае должны составить 16 мм. Кроме того, заказчик директивно принял решение, что в малом наклонном ходе, который примыкает к 4-му коридору, будет установлен эскалатор Е25Т вместо Е900Т. Поэтому в чугунной обделке на длине будущего машинного помещения появлялись негабаритные места ниже горизонтального диаметра, что требует дополнительных работ по выемке трех тюбингов в каждом кольце в непосредственной близости от действующих тоннелей. Специалисты, проводившие экспертизу раздела «Промышленная безопасность», согласились с решением применить экран из труб с опиранием их на грунтовый массив. Устройство экрана было решено выполнять из торцевой части среднего зала ст. «Маяковская».
Сооружение защитного экрана на ст. «Маяковская» сводилось к горизонтальному забуриванию 21 трубы диаметром 325 мм, соединяемых между собой замками, вглубь породы на длину 22,5 м. В качестве опор экрана выступали кровля существующей чугунной обделки диаметром 9,5 м со стороны станции и грунтовый массив с противоположной стороны. Каждый элемент экрана соединен с соседним посредством Т- и П-образных замков, выполненных из уголка на всю длину экрана (рис. 4.21). Перепад высотных отметок осей защитного экрана составляет 1360 мм, а ширина его — 7146 мм между центрами бурения крайних осей. Исходя из конструктивных особенностей экрана и его размера, задача его сооружения потребовала незамедлительного решения нескольких технических вопросов.
Прежде всего необходимо было выполнить комплекс подготовительных мероприятий, способствующих будущему сооружению защитного экрана. Из подходной штольни околоствольного двора шахты № 76, находящейся вблизи ст. «Маяковская», прошли фурнель сечением 2200×2400 мм в свету высотой 14 м. Далее — подходную штольню таким же сечением