
745
.pdfсоответственно: более 103 МПа, 4×102–103 МПа, 20–4×102 МПа, менее 20 МПа.
Относительное удлинение при разрыве жестких пленок гораздо меньше, чем эластичных. Деформация эластичных пленок исчезает после снятия нагрузки при нормальной температуре почти мгновенно.
Для изготовления пленок применяется полиэтилен, поливинилхлорид, полипропилен, полиизобутилен. Пленочные полимерные материалы обладают комплексом физикомеханических свойств, из которых для противофильтрационных целей наиболее существенны прочность, деформационность, плотность, твердость, водостойкость, морозостойкость, длительная прочность, химическая стойкость, свариваемость.
Наиболее широкое распространение получили пленки из полиэтилена низкой плотности.
Из поливинилхлорида (ПВХ) производят пленки толщиной от 0,01 до 1 мм.
Для противофильтрационных конструкций используются только пластифицированные мягкие пленки толщиной от 0,1 до 1 мм, шириной 1,2 м, длина пленки в рулоне 30 м и более. Полипропиленовые пленки относятся к мягким пленкам, но по сравнению с полиэтиленовыми они обладают большей кристалличностью и твердостью. В их состав могут входить различные наполнители, стабилизаторы и красители.
Из полиизобутилена (ПИБ) производят в основном листовой материал. Полиизобутиленовые листы марки ПСГ с успехом используются для гидроизоляции различных сооружений, а также нашли широкое применение в химической промышленности.
Сополимер этилена с винилацетатом является очень хорошим материалом для изготовления пленок, которые отличаются повышенной прочностью, деформационной способностью и морозостойкостью.
Пленки из сополимера этилена с пропиленом (СЭП) обладают высокой морозостойкостью и хорошей сопротивляемостью к растрескиванию в поверхностноактивных средах. Исследования по определению фильтрационных утечек через пленочные экраны свидетельствуют, что величина утечек воды через пленочные экраны чрезвычайно мала и, по всей вероятности, не превышает точности измерений. При достаточно высоком качестве выполнения работ пленочные полимерные противофильтрационные экраны становятся абсолютно непроницаемыми для воды. Однако при большой площади экранируемой поверхности в последней могут иметь место случайные порезы, проколы и другие повреждения, оценивать утечки через которые не представляется возможным, так как кроме пленки в траншее всегда имеется глинистый раствор или комовые глинистые породы.
Наряду со случайными повреждениями слабыми местами пленочных экранов являются их соединения внахлест. По расчетам, проведенным для подпорных сооружений высотой 30–50 м, пленочный экран которых толщиной 0,2–0,4 мм образован полотнищами размером 12×50 м, уложенными на песчаный слой без их сварки, фильтрационные потери через экран имеют тот же порядок, что и потери, которые произошли бы при замене пленочного полимерного экрана экраном из глины с коэффициентом фильтрации 10-4–10-5 см/с.
Впрактике строительства широко применяются заполнители на основе вяжущих веществ, в первую очередь различных цементов. Последний представляет собой тонкоразмолотую смесь термически активизированных глин и мергелистых известняков (клинкер) часто с различными тонкомолотыми добавками. Цемент является дорогостоящим материалом, в связи с чем в растворы добавляют глинистые породы, песок, щебень, шлаки и др. В зависимости от вида добавок получают грунтобетон, шлакобетон, бетон.
Выбор материала-заполнителя базируется на требованиях, предъявляемых к сооружению, и его целевом назначении.
Втом случае, когда барраж служит только для защиты объекта от притока подземных вод, в качестве заполнителей целесообразно использовать обычный глинистый раствор, извлеченные из траншеи и обогащенные глиной породы, местные комовые суглинки и
глины, пасты, приготовленные на суглинистой и глинистой основе, и различного вида пленки.
Если же барраж кроме противофильтрационных функций выполняет функции несущих конструкций, то заполнители приготавливают на основе цементов и силикатов (бетонные, асфальтобетонные, глиноцементные, глиноцементно-песчаные и др.).
Выбор материала-заполнителя зависит также от требований, предъявляемых к эффективности работы сооружения, на основе которых при заданной ширине траншеи определяется максимально допустимый коэффициент фильтрации. Возможно решение и обратной задачи: при заданном коэффициенте фильтрации определить минимальную ширину траншеи.
5.3.2. Устройство и технология укладки в траншею материала-заполнителя
Разнообразие материалов-заполнителей, специфические особенности укладки их в траншею, заполнение глинистым раствором при незначительных поперечных размерах и достаточной глубине траншей обусловливают многообразие способов производства работ на заключительной стадии сооружения барража. Перед укладкой материала-заполнителя траншея должна быть определенным образом подготовлена.
Если сооружение барража выполняется в виде отдельных, впоследствии смыкающихся участков или «захваток», то перед укладкой материала должен быть решен вопрос надежного их сочленения. При укладке материала в непрерывную траншею возникает необходимость разделения ее на отдельные секции или заходки. Диктуется это тем, что размещаемый в траншее заполнитель укладывается под углом естественного откоса, величина которого зависит от состава заполнителя и достигает 15–30°. Растекание заполнителя вдоль траншеи требует поддержания определенного расстояния между машиной, проводящей траншею, и местом укладки материала, что, естественно, удлиняет коммуникации, повышает расход глинистого раствора и увеличивает вероятность обрушения стенок траншеи. Стремление ограничить растекание заполнителя по траншее обусловливает необходимость устройства поперечных перегородок по всей ее глубине с определенным шагом, т.е. деление траншеи на отдельные секции.
Из обогащенного глинистого раствора на дно траншеи за период времени между ее проведением и укладкой заполнителя выпадает большое количество песчаных фракций. Если их не удалить, то у самой подошвы водоносного горизонта, там, где в процессе эксплуатации сооружения будет максимальный перепад давлений, противофильтрационные свойства преграды будут иными, чем предусматривается проектом.
Кроме разделения траншеи на секции и ее очистки, при сооружении несущей преграды из монолитного железобетона в траншею предварительно должны быть установлены арматурные каркасы. После очистки траншеи проверяется ее глубина, определяется угол наклона стенок, а также наличие каверн на них. При необходимости заменяется глинистый раствор.
Очистка траншеи от выпавших в осадок песчаных и недиспергированных частиц породы, которые снижают противофильтрационный эффект барража, является вынужденной технологической операцией, которая четкой организацией работ и использованием качественного глинистого раствора может быть исключена. Удаление осадка осуществляют в основном отсасыванием совместно с глинистым раствором. Раствор от частиц породы очищают на специальных установках (например, СГУ) и вновь возвращают в траншею.
В зависимости от промежутка времени между проведением траншеи и ее заполнением водонепроницаемым материалом, осадок имеет различную уплотненность, что обусловливает разнообразие способов его удаления или рыхления перед транспортировкой на поверхность. Рыхлый, неслежавшийся осадок может быть удален скоростным потоком глинистого раствора, который отсасывается грунтовым насосом или
эрлифтом. Пульповод подвешивают на канате для обеспечения его перемещения сверху вниз на высоту, равную мощности осадка, и поступательного, цикличного движения вдоль траншеи в процессе очистки. В исходном положении входное отверстие пульповода располагается на расстоянии 5–10 см от осевшего грунта. С включением в работу насоса пульповод постепенно опускают и поднимают, перемещая затем его вдоль траншеи на расстояние, не превышающее его диаметра, и цикл повторяется.
Более плотный осадок предварительно разрыхляют потоком очищенного глинистого раствора, который, обогащаясь частицами грунта, вновь отсасывают на поверхность. При значительном уплотнении осадка для его удаления используются машины, с помощью которых проводили траншею, причем ковшовые барражные машины дополнительно укомплектовываются средствами, обеспечивающими отсос и очистку глинистого раствора.
На рис. 5.10 показана принципиальная схема устройства, которое в сочетании с другими агрегатами и механизмами обеспечивает рыхление осадка и его отсос на поверхность. На нижнем конце полого вала 4, пропущенного через пульповод 3, крепятся рыхлитель 6 и винт-толкатель в виде витка шнека 5. Последний в процессе работы предотвращает возможное залипание входного отверстия пульповода и выполняет роль плавающей опоры. Верхний конец вала через вертлюг 2 соединяется с приводом 1. Устройство подвешивается на канате подъемного устройства, смонтированного на ходовой платформе, и взаимодействует с ней через направляющие или крепится посредством гидравлических домкратов, обеспечивающих его перемещение вверх и вниз с амплитудой до 1 м. На платформе кроме подъемного устройства (или домкратов) монтируется узел очистки раствора, а при работе без эрлифта — грунтовой насос.
На отдельные секции траншея делится при помощи поперечных перегородок (разделительных шаблонов), служащих для предотвращения перетока материала-за- полнителя из одного участка в другой. Ввиду разности давлений между смежными секциями, на шаблон действуют усилия, стремящиеся переместить его или деформировать.
После выполнения своих функций шаблон должен легко извлекаться из траншеи. Выполняют перегородки обычно из труб круглой или серповидной формы сечения, с двух сторон вдоль трубы приваривают металлические пластины. Расстояние между кромками пластин на 50–100 мм превышает ширину траншеи.
В практике применяются шаблоны из плоских или изогнутых шпунтин, а также различные конструкции со специальными разжимными устройствами. В некоторых случаях в качестве шаблонов используются железобетонные серийно изготовляемые сваи, диаметр которых превышает ширину траншеи. Длина шаблона должна быть равна глубине траншеи. Шаблоны в виде плоских или фигурных шпунтин применяются реже из-за недостаточной их жесткости, а шаблоны со специальными разжимными устройствами — из-за сложности изготовления, недостаточной надежности в работе разжимных устройств, трудности их извлечения. Установка шаблонов в траншею осуществляется с помощью кранов или специальных установок, используется кондуктор.
После подготовки траншеи и приема ее по акту переходят к заключительному этапу устройства барража — укладке в траншею материала-заполнителя. Технологические приемы укладки в траншею заполнителя определяются его видом и свойствами, а в некоторых случаях и типом барражных машин, используемых для проведения траншей. Так, например, если в качестве заполнителя берется извлеченный в процессе проведения траншеи грунт, то технологические приемы его укладки будут зависеть от типа применяемых барражных машин и свойств усредненной массы грунта.
Обратная укладка такого грунта может осуществляться с помощью бульдозера или грейфером. Укладка породы ведется с противоположного забою торца траншеи. Под действием гравитационных сил она размещается под углом естественного откоса, которым определяется расстояние между барражной машиной и механизмом, производящим укладку грунта.
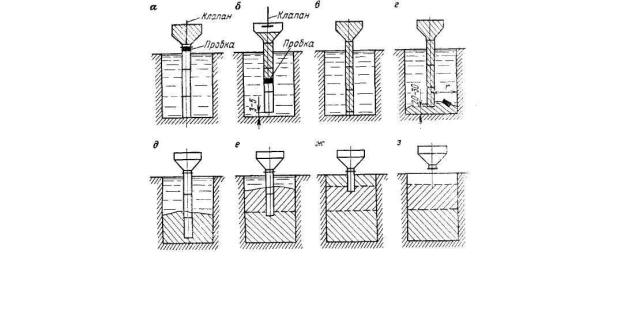
Укладка породы, удаляемой из забоя гидротранспортом, может осуществляться обратным намывом, если ее усредненный состав удовлетворяет предъявляемым требованиям.
Когда усредненный грунт не удовлетворяет предъявляемым требованиям, его перед укладкой предварительно обогащают глинами или вяжущими добавками. Технологические приемы укладки при этом определяются консистенцией приготовленного заполнителя.
Укладка в траншею в качестве заполнителя комовых глин и суглинков осуществляется обычно путем их выгрузки из кузова самосвала или других транспортных средств с последующей отсыпкой бульдозером. При укладке комовых заполнителей необходимо учитывать возможность образования арочного эффекта.
При укладке пастообразного заполнителя на основе вяжущего траншею обычно разделяют на отдельные секции с помощью извлекаемых или неизвлекаемых шаблонов. Пастообразный заполнитель без вяжущего может укладываться как в отдельные секции, так и без их выделения. Разделительные шаблоны в этом случае, как правило, извлекаются.
Глинистый раствор как материал-заполнитель в зависимости от его фильтрационной прочности укладывается в траншею различными способами. Если фильтрационная прочность глинистого раствора, используемого для временного поддержания стенок траншеи в процессе ее проведения, удовлетворяет требованиям, то его оставляют в траншее в качестве постоянного заполнителя. В том случае, когда фильтрационная прочность недостаточна, а ее требуемое значение может быть достигнуто путем улучшения параметров нового глинистого раствора, глинистый раствор, находящийся в траншее, заменяется. Замена осуществляется путем вытеснения старого раствора новым, который подается на дно траншеи по специальной трубе насосом. Плотность нового глинистого раствора обычно выше находящегося в траншее, так как повышение фильтрационной прочности достигается в основном за счет увеличения количества глины, приходящегося на 1 м3 раствора.
Бетонные смеси укладывают в траншею восходящим потоком методом ВПТ (вертикальное перемещение трубы). Бетонирование этим методом ведут в следующей последовательности (рис. 5.11). На поверхности земли собирают бетонолитную трубу длиной на 1–1,5 м больше глубины траншеи. С помощью крана ее переводят в вертикальное положение и при закрытом заглушкой нижнем конце проверяют на герметичность путем заполнения ее водой, после чего ее опускают в траншею.
а) |
б) |
|
в) |
|
г) |
д) |
е) |
|
ж) |
|
з) |
|
|
|
|
|
|
Рис. 5.11. Схема бетонирования траншеи способом ВПТ:
а— исходное положение трубы перед бетонированием; б — выпуск бетона
втрубу; в — выход пробки из трубы; г — начало заглубления трубы в бетон;
д, е, ж, з — этапы бетонирования с последовательным удалением секций бетоноводной трубы; r — радиус действия
С помощью быстросъемного соединения верхний конец трубы сочленяют с приемной воронкой, имеющей форму опрокинутой усеченной пирамиды. Обычно приемную воронку монтируют в опорную вышку таким образом, чтобы имелась возможность перемещения в ней вверх и вниз отдельных звеньев труб. В верхней части трубы установлен поршень, выполненный в виде шара из куска мешковины с опилками или металлического круглого (по диаметру трубы) диска, к которому со стороны контакта с бетоном вертикально крепятся несколько направляющих уголков, ориентирующих поршень от перекосов в трубе. До начала бетонирования поршень удерживается в исходном положении с помощью тонкой проволоки.
Горловину воронки выше поршня, установленного в трубе, перекрывают коническим клапаном. Под действием массы столба бетона в воронке, воздействующего на поршень, обрывается проволока, удерживающая его, и поршень перемещается по трубе совместно с бетоном вниз, вытесняя глинистый раствор. Как только пробка упрется в дно траншеи, бетонолитную трубу приподнимают на 20–30 см, чем обеспечивается выход в траншею пробки и бетона. Последний растекается вдоль секции траншеи и поднимается над нижним торцом трубы. После опорожнения воронки бетонолитная труба, во избежание ее полного опорожнения, вместе с воронкой опускается в уложенную бетонную смесь. Следующие порции подают без изменения положения трубы до необходимого заглубления, после чего бетонирование ведут по обычной схеме.
Когда перерыв в бетонировании превышает время начала схватывания смеси, работы возобновляют после набора прочности уложенного бетона до 3,0–5,0 МПа. Вначале производят очистку поверхности уложенного бетона от осадка и глинистой корки способом воздушной или гидравлической промывки из трубы (шланга), подключаемой к компрессору или насосу. После очистки бетонирование ведут по описанной схеме.
При укладке бетона в зимних условиях работы рекомендуется вести круглосуточно по скользящему графику. Бетонную смесь в этом случае следует подавать в бункер подогретой. Температура ее в момент укладки должна быть не ниже 5 °С. При необходимости обеспечивается электроподогрев бетонной смеси в верхней части конструкции.
В тех случаях, когда бетон используется в качестве несущих стен, его укладывают на всю глубину траншеи и после окончания бетонирования удаляется до 30 см верхнего слоя смеси, загрязненного глинистым раствором. Если же бетон выполняет только противофильтрационные функции, то в целях его экономии он укладывается выше водоносного горизонта на 1,5–2 м. Остальная часть траншеи до поверхности может быть заполнена любым местным материалом.
За последнее время интенсивно развивается метод заполнения траншей сборным железобетоном. Этот метод перспективен при устройстве неглубоких (10–12 м) и тонких (20–30 см) стенок, главным образом в местах, где необходимо сразу же получить готовую облицовку несущей стены, например при строительстве подземных проездов и переходов.
Сборные железобетонные стены менее экономичны, чем монолитные, и в практике защиты объектов от притоков подземных вод (без выполнения функции несущих конструкций) они не находят широкого применения, в связи с чем вопросы устройства стен в грунте из сборных элементов в настоящем разделе не рассматриваются.
Полимерные пленки используются только совместно с другим видом заполнителя — комовыми глинами, суглинками и т.д. Укладка дополнительного сопутствующего материала диктуется необходимостью заполнения полости между стенкой траншеи и пленкой, а также прижатия стыков полотнищ пленки и экрана в целом к противоположной стенке траншеи.
Укладка двух видов заполнителей обусловливает технологически необходимые процессы, которые включают опускание или установку полотнищ пленки в траншею, заполненную глинистым раствором, установку разделительных шаблонов и заполнение полости «сопровождающим» материалом.
ЗАКЛЮЧЕНИЕ
Взаключение данной работы необходимо отметить следующее. В зависимости от характера воздействия на водоносные грунты, времени осуществления мероприятий, а также типа оборудования, применяемого для выполнения работ, все специальные способы работ и сооружения тоннелей, предусматривающие предварительное закрепления грунтов различными инъекционными составами путем тампонажа полостей и трещин грунтов; снижение подвижности грунтов на определенный период времени путем замораживания, строительного водопонижения, создания повышенного давления воздуха и др.; применение ограждений и подвижных крепей без изменения физико-химических и механических свойств грунтов (шпунт, ограждения из буронабивных свай, «стена в грунте», опускная крепь, проходческие щиты и пр.); применение специального оборудования и физических процессов воздействия на грунтовый массив (бурение, размыв, использование энергии взрыва и т.д.).
Вобщем случае для укрепления грунтов и снижения их водопроницаемости применяют растворы на основе: цемента — чистые цементные, цементно-песчаные, цементноглинистые, цементно-песчано-глинистые, цементно-полимерные, цементно-силикатные и аэрированные цементные растворы; битумные мастики и эмульсии, глинистые и глиносиликатные растворы; силикатные, силикатно-органические растворы; растворы смол (мочевиноформальдегидных, эпоксидных смол, хромлигниновых соединений). Области применения различных растворов зависят от: характеристик растворов и грунтов (степени дисперсности раствора — суспензия, коллоидный или истинный раствор, тип грунта — скальный или нескальный, трещиноватость, пористость, коэффициент фильтрации и т.д., минералогический и химический состав — карбонатность, загипсованность, содержание глинистых частиц, показатель рН и др.); назначения инъекции (повышение прочности или водонепроницаемости).
Все более широкое применение для укрепления грунтов находит термический способ, одной из разновидностей которого является технология, разработанная учеными института Гидродинамики СО РАН. Сквозь грунт, словно через фильтр, пропускают смесь газов и поджигают их. В процессе горения почва прогревается до 1500 градусов, спекается и превращается в очень плотную твердую «подошву». Такая «подошва» позволяет обойтись без традиционных свай и втрое уменьшить расходы.
Фундамент, созданный по новой технологии, сокращает сроки возведения зданий и сооружений, и помогает избежать появления в них возможных трещин при просадках грунта.
Опыт применения струйной цементации для устройства опережающей крепи тоннелей свидетельствует, что эта технология может достаточно успешно использоваться для закрепления широкого класса грунтов, от несвязных крупнообломочных до мелкодисперсных глинистых, независимо от степени их проницаемости. Она имеет существенные преимущества по сравнению с традиционными методами искусственного замораживания и химического закрепления грунтов и является эффективной при строительстве тоннелей различного назначения в неустойчивых грунтах.
Преимуществами конструкций, устраиваемых с помощью струной технологии, являются повышенная несущая способность; высокая скорость сооружения; уменьшение расходов материалов; возможность устройства под существующими зданиями и сооружениями; возможность устройства только в необходимых по высоте слоях грунта. В перспективе струйная технология может найти применение при устройстве стен котлованов, тоннелей, коллекторов емкостей, крепей шахтных стволов, подводных оснований и т.п.
Диапазон специальных способов работ при строительстве подземных сооружений постоянно обновляется, что необходимо учитывать при проектировании новых, ремонте и эксплуатации действующих тоннелей и метрополитенов.
Библиографический список
1.Боярский В.А., Киров И.П. Водоотлив и осушение на горных предприятиях: Учеб. пособие. М.: Высш. шк., 1980. 304 с.
2.Власов С.Н., Торгалов В.В., Виноградов Б.Н. Строительство метрополитенов: Учеб. для ПТУ / Под ред. С.Н. Власова. М.: Транспорт, 1987. 278 с.
3.ВСН 127-91. Инструкция по проектированию и производству работ по искусственному понижению уровня грунтовых вод. М., 1991. 120 с.
4.ВСН 189-78. Инструкция по проектированию и производству работ по искусственному замораживанию грунтов при строительстве метрополитенов и тоннелей. М.: Минтрансстрой СССР, 1978. 115 с.
5.ВСН 190-78. Инструкция по инженерно-геологическим изысканиям для проектирования и строительства метрополитенов, горных железнодорожных и автодорожных тоннелей / Минтранстрой СССР.
М., 1978. 72 с.
6.Главатских В.А. Технология строительства метрополитенов. Ч. 1. Развитие метрополитенов в России: Учеб. пособие. Новосибирск: Изд-во СГУПСа, 2003. 168 с.
7.Главатских В.А. Технология строительства метрополитенов. Ч. 2. Строительство станций метрополитена закрытым способом: Учеб. пособие. Новосибирск: Изд-во СГУПСа, 2004. 213 с.
8.Главатских В.А. Технология строительства метрополитенов. Ч. 3. Строительство станций метрополитена открытым и полузакрытым способами: Учеб. пособие. Новосибирск: Изд-во СГУПСа, 2005. 233 с.
9.Главатских В.А. Технология строительства метрополитенов. Ч. 4. Строительство шахтных стволов и эскалаторных тоннелей: Учеб. пособие. Новосибирск: Изд-во СГУПСа, 2006. 215 с.
10.Главатских В.А., Молчанов В.С. Строительство метрополитенов: Учеб. пособие для вузов железнодорожного транспорта / Под ред. В.А. Главатских. М.: Маршрут, 2006. 680 с.
11.Главатских В.А., Поправко А.К. Стена в грунте: Лекции для слушателей ФПК. Новосибирск: Изд-во НИИЖТа, 1986. 50 с.
12.Давыдов В.В., Белоусов Ю.И. Химический способ укрепления горных пород. М.: Недра, 1977. 228 с.
13.Дорман Я.А. Безопасная технология раскрытия горизонтальных выработок из шахтных стволов и существующих выработок в сложных инженерно-геологических условиях. М.: ТИМР, 1997. 132 с.
14.Дорман Я.А. Специальные способы работ при строительстве метрополитенов. М.: Транспорт, 1981.
302 с.
15.Калмыков Е.П. Тампонирование горных пород при сооружении вертикальных стволов. М.: Недра, 1979. 280 с.
16.Маковский Л.В. Городские подземные транспортные сооружения: Учеб. пособие для вузов. М.: Стройиздат, 1985. 439 с.
17.Основания, фундаменты и подземные сооружения: Справ. проектировщика / Под ред. Е.А. Сорочана
иЮ.Г. Трофименкова. М.: Стройиздат, 1985. 480 с.
18.ПБ 03-428-02. Правила безопасности при строительстве подземных сооружений. Серия 03. Вып. 12. М.: ГУП НТЦ «Промышленная безопасность» Госгортехнадзора России, 2002. 432 с.
19.ПБ 13-407-01. Единые правила безопасности при взрывных работах. М.: Госгортехнадзор, 2001. 248
с.
20.Пневмопробойники / К.С. Гурков, В.В. Климашко, А.Д. Костылов, В.Д. Плавских и др. / Под ред. В.В. Каменского. Новосибирск: ИГД СО АН СССР, 1990. 218 с.
21.Подземные сооружения, возводимые способом «стена в грунте» / Под ред. В.М. Зубкова. Л.: Стройиздат, 1977. 200 с.
22.Пособие по химическому закреплению грунтов инъекцией в промышленном и гражданском строительстве (к СНиП 3.02.01–83) НИИОСП им. Герсеванова. М.: Стройиздат, 1986. 128 с.
23.ППБ 01-93. Правила пожарной безопасности в Российской Федерации. М.: МВД России, 1993.
24.Применение пневмопробойников в транспортном строительстве // Экспресс-информация. Вып. 2. М.: ВПТИТрансстрой, 1984. 19 с.
25.Рекомендации по проектированию и устройству опережающих защитных экранов из труб с применением микротоннелепроходческих комплексов при строительстве тоннелей. М.: ОАО Корпорация «Трансстрой», 2003. 95 с.
26.Рекомендации по производству работ при сооружении тоннелей метрополитена методом продавливания. М.: Минтрансстрой СССР, 1988. 49 с.
27.Ржаницын Б.А. Химическое закреплении грунтов в строительстве. М.: Стройиздат, 1986. 264 с.
28.Рудиков В.С., Бабаянц Г.М. Защита горных предприятий от подземных вод. М.: Недра, 1986. 288 с.
29.Руководство по производству и приемке работ при устройстве оснований и фундаментов. М.: НИИОСП им. Н.М. Герсеванова Госстроя СССР, 1977. 241 с.
30.СНиП ІІІ–44–77*. Тоннели железнодорожные, автодорожные и гидротехнические. Метрополитены. М.: Госстрой СССР, 1977. 88 с.
31.СНиП 12–01–2004. Организация строительства. М.: Госстрой России, 2005. 23 с.
32.СНиП 3.03.01–87. Несущие и ограждающие конструкции / Минстрой России. М.: ГУП ЦПП, 1996.
192 с.
33.СНиП 10.01–2003. Система нормативных документов в строительстве. Основные положения. М.: Госстрой России,
34.СНиП 12–03–2001. Безопасность труда в строительстве. Ч. 1. Общие требования. М.: Госстрой России, 2001.
35.СНиП 12–04–2002. Безопасность труда в строительстве. Ч. 2. Строительное производство. М.: Госстрой России, 2002.
36.СНиП 32–01–95. Железные дороги колеи 1520 мм. М.: Госстрой России, 1995. 20 с.
37.СНиП 32–04–97. Тоннели железнодорожные и автодорожные. М.: Госстрой России, 1997. 21 с.
38.СНиП 32–02–2003. Метрополитены. М.: Госстрой России, 2004. 33 с.
39.Справочник инженера-тоннельщика / Под ред. В.Е. Меркина, С.Н. Власова, О.Н. Макарова. М.: Транспорт, 1993. 389 с.
40.СП 32–104–2004. Оценка шума при проектировании, строительстве и эксплуатации объектов метрополитена. М.: Госстрой России, 2004.
41.СП 23-105-2004. Оценка вибрации при проектировании, строительстве и эксплуатации объектов метрополитена. М.: Госстрой России, 2004.
42.СП 32–105–2004. Метрополитены. М.: Госстрой России, 2004.
43.СП 32–106–2004. Метрополитены. Дополнительные сооружения и устройства. М.: Госстрой России,
2004.
44.Строительство подземных сооружений: Справ. пособие / М.Н. Шуплик и др. М.: Недра, 1993. 384 с.
45.Строительство стволов шахт и рудников: Справ. / Под общ. ред. О.С. Докукина и Н.С. Болотских. М.: Недра, 1991. 516 с.
46.Строительство тоннелей и метрополитенов: Учеб. для техникумов транспортного строительства / Д.М. Голицынский, Ю.С. Фролов, Н.И. Кулагин и др. Под ред. Д.М. Голицынского. М.: Транспорт, 1989. 319 с.
47.Технология строительства подземных сооружений. Специальные способы строительства: Учеб. для вузов / И.Д. Насонов, В.А. Федюкин, М.Н. Шуплик, В.П. Ресин. М.: Недра, 1992. 351 с.
48.Тоннели: Справ.-метод. пособие в помощь строителям БАМа / Под ред. Д.И. Федорова. М.: Транспорт, 1979. 176 с.
49.Трупак Н.Г. Замораживание грунтов при строительстве подземных сооружений. М.: Недра, 1979. 344
с.
50.Трупак Н.Г. Замораживание пород при сооружении вертикальных шахтных стволов. М.: Недра, 1983.
270 с.
51.Туренский Н.Г., Ледяев А.П. Строительство тоннелей и метрополитенов. Организация, планирование, управление: Учеб. для вузов / Под ред. Н.Г. Туренского. М.: Транспорт, 1992. 264 с.
52.Уплотнение грунтов обратных засыпок в стесненных условиях строительства / ЦНИИОМТП. М.: Стройиздат, 1981. 252 с.
53.Фролов Ю.С., Крук Ю.Е. Метрополитены на линиях мелкого заложения. Новая концепция строительства. М.: ТИМР, 1994. 244 с.
54.Чураков А.И. Производство специальных работ в гидротехническом строительстве: Учеб. пособие для вузов. М.: Стройиздат, 1976. 256 с.
55.Ширай Г.Т., Щепетков А.П., Литинский Ю.В. Проходка шахтных стволов с применением опускных сооружений. М.: Недра, 1984. 260 с.
56.Шталь Т.М., Теличенко В.И., Феклин В.И. Технология возведения подземной части зданий и сооружений: Учеб. пособие для вузов. М.: Стройиздат, 1990. 288 с.
Оглавление |
|
Введение .................................................................................................................... |
3 |
1. Общие сведения о свойствах грунтов ................................................................. |
5 |
1.1. Классификация грунтов................................................................................ |
5 |
1.2. Строительные свойства грунтов по отношению к воде............................. |
8 |
2. Традиционные способы закрепления и стабилизации грунтов....................... |
13 |
2.1. Общие положения ....................................................................................... |
13 |
2.2. Искусственное водопонижение.................................................................. |
14 |
2.3. Замораживание грунтов.............................................................................. |
22 |
2.4. Инъекционное закрепление и тампонирование грунта............................ |
32 |
3. Современные технологии закрепления грунтов............................................... |
55 |
3.1. Струйная цементация грунтов ................................................................... |
55 |
3.2. Компенсационное нагнетание.................................................................... |
70 |
3.3. Термическая обработка грунтов ................................................................ |
77 |
3.4. Электроразрядная технология для геотехнического строительства ....... |
83 |
4. Строительство подземных сооружений под защитой опережающей |
|
крепи ........................................................................................................................ |
85 |
4.1. Общие положения ....................................................................................... |
85 |
4.2. Защитный экран из труб ............................................................................. |
85 |
4.3. Бетонная крепь в опережающих выработках.......................................... |
118 |
4.4. Принцип предварительного щелеобразования ....................................... |
120 |
4.5. «Плита в грунте»....................................................................................... |
126 |
5. Защита подземных сооружений от грунтовых вод с помощью барража ..... |
129 |
5.1. Общие сведения о барражах..................................................................... |
129 |
5.2. Барражные машины .................................................................................. |
130 |
5.3. Заполнение траншей водонепроницаемым материалом ........................ |
139 |
Заключение............................................................................................................ |
146 |
Библиографический список.................................................................................. |
147 |
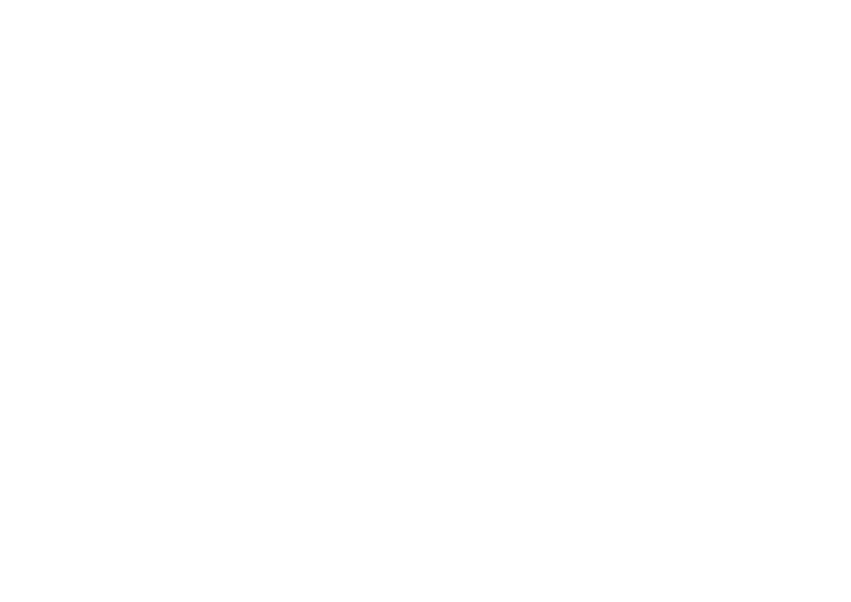
Рис. 4.12. График прокладки трубы длиной 36,0 м 820 мм защитного экрана методом продавливания микротоннелепроходческим комплексом AVN-600