
- •1. Вода как основной компонент пищевых продуктов. Свободная и связанная вода
- •2. Состав и свойства пищевых продуктов (белки, жиры, углеводы, минеральные вещества, витамины), их роль, ценность, нормы употребления
- •3. Причина порчи пищевых продуктов. Микрофлора пищевых продуктов. Ферменты. Зависимость активности микроорганизмов и тканевых ферментов от внешних условий
- •4. Влияние физических внешних факторов на активность микроорганизмов и тканевых ферментов
- •5. Влияние химических внешних факторов на активность микроорганизмов и тканевых ферментов
- •6. Влияние биологических внешних факторов на активность микроорганизмов и тканевых ферментов
- •7. Принципы и основные методы консервирования пищевых продуктов. Консервирование пищевых продуктов холодом. Применение холода в сочетании с другими методами консервирования
- •8. Основные понятия холодильной технологии (холодильная обработка и холодильное хранение). Понятие режима холодильной обработки и холодильного хранения
- •9. Охлаждающие среды. Их свойства и параметры
- •10. Автолитические изменения в мясе: сущность, стадии, их продолжительность и зависимость от температуры. Причины порчи мяса, их зависимость от температуры
- •11. Автолитические изменения и причины порчи рыбы, их зависимость от температуры
- •12. Виды плодов и овощей. Стадии развития продуктов растительного происхождения, их зависимость от температуры. Причины порчи продуктов растительного происхождения, их зависимость от температуры
- •13. Сущность и характер протекания процесса охлаждения. Параметры, определяющие режим процесса охлаждения. Факторы, влияющие на их выбор
- •14. Особенности технологии охлаждения пищевых продуктов (мяса, колбасных изделий, птицы, рыбы, плодов и овощей, яиц, молока и молочных продуктов)
- •16. Определение количества теплоты, отводимой в процесса охлаждения
- •17. Усушка продуктов при холодильной обработке, пути ее снижения
- •19. Изменение теплофизических свойств (плотности, удельной теплоемкости, теплопроводности, температуропроводности продукта при замораживании)
- •20. Структурные и качественные изменения в продуктах при замораживании. Параметры, определяющие режим замораживания, и факторы, влияющие на их выбор
- •21. Понятие «простого» замораживания. Определение продолжительности процесса замораживания. Понятия средней температуры процесса холодильной обработки, средней объемной конечной температуры продукта
- •22. Определение количества теплоты, отводимой в процессе замораживания
- •23. Особенности технологии замораживания пищевых продуктов (мяса, птицы, рыбы, плодов и овощей)
- •24. Сущность, значение, способы осуществления и процесса подмораживания. Параметры, определяющие режим процесса подмораживания. Факторы, влияющие на их выбор
- •25. Сущность, значение, способы осуществления и процесса домораживания. Определение количества теплоты, отводимой от продукта в процессе домораживания
- •26. Сущность, значение, способы осуществления процесса отепления пищевых продуктов. Способы отепления охлажденных продуктов
- •27. Сущность, значение и способы размораживания пищевых продуктов. Определение продолжительности процесса размораживания. Определение количества теплоты, подводимой при размораживании
- •28. Сущность и значение холодильного хранения. Изменения, происходящие в продуктах при хранении
- •29. Факторы, влияющие на выбор режима хранения продуктов в охлажденном, подмороженном и замороженном состоянии
- •30. Усушка продуктов при хранении. Методы борьбы с усушкой
- •31. Сущность и значение процесса сублимационной сушки пищевых продуктов. Условия сублимационной сушки. Подготовка продуктов к сублимационной сушке. Осуществление процесса сублимационной сушки. Хранения сублимированного продукта
- •32. Физические основы концентрирования жидких пищевых продуктов вымораживанием. Технология производства: кристаллизация, сепарирование. Технологическая схема получения концентрированного сока
- •33. Понятия технологии, технологического процесса, технологического режима, способа производства, технологической схемы производства. Классификация технологических процессов. Сравнительные показатели способов производства
- •34. Применение искусственного холода в химической промышленности. Классификация химико – технологических процессов
- •35. Охлаждение в экзотермических процесса химического взаимодействия. Технология некоторых производств с экзотерическими процессами химического взаимодействия
- •36. Абсорбция. Физико – химические основы и виды абсорбции. Абсорбция при низких температурах в химической технологии
- •37. Дистилляция и ректификация. Физико – химические основы процесса. Особенности низкотемпературной ректификации. Низкотемпературная ректификация в процессах химической технологии
- •38. Конденсация. Основные понятия, виды и способы осуществления процесса конденсации. Применение конденсации в химической технологии
- •39. Адсорбция. Физико – химические методы адсорбции. Низкотемпературная адсорбция в технологии некоторых производств
- •40. Применение холода в нефтяной и газовой промышленности
- •41. Применение искусственного холода в строительстве
- •42. Применение искусственного холода в медицине
- •43. Применение искусственного холода в машиностроении и металлургии
- •45. Искусственный водный лед, достоинства и недостатки. Виды производимого искусственного водного льда. Применение искусственного водного льда
- •46. Льдосоляное охлаждение. Виды льдосоляного охлаждения. Удельная массовая холодопроизводительность льдосоляной смеси и рассольного льда. Системы льдосоляного охлаждения
- •47. Сухой лед, его свойства. Стадии производства сухого льда. Источники сырья и методы извлечения из них углекислого газа. Применение и хранение сухого льда
- •49. Фазовая диаграмма углекислоты. Способы получения жидкой двуокиси углерода из газообразной
- •50. Фазовая диаграмма углекислоты. Способы получения твердой двуокиси углерода из жидкой
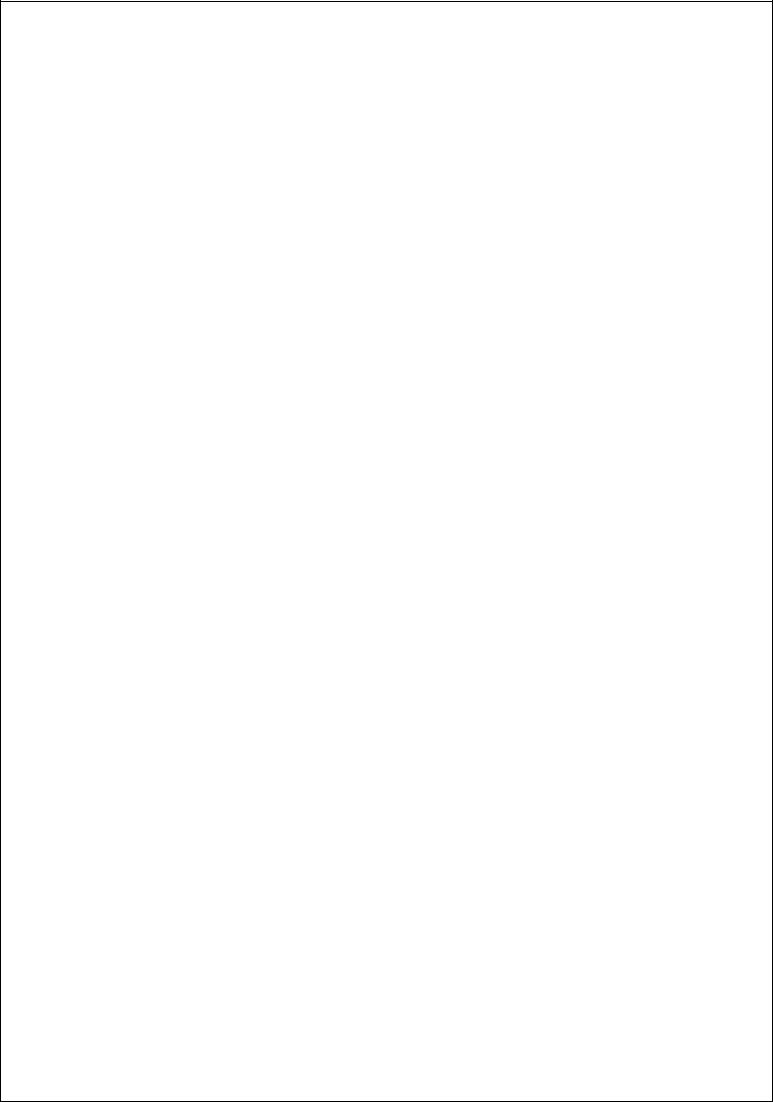
37. Дистилляция и ректификация. Физико – химические основы процесса. Особенности низкотемпературной ректификации. Низкотемпературная ректификация в процессах химической технологии
Ректификацией называется процесс разделения гомогенной жидкой смеси на составляющие компоненты или фракции путем сочетания последовательных стадий испарения и конденсации. Ректификация – это сложный вид перегонки, основанный на различной летучести компонентов смеси при одной и той же температуре. В процессе перегонки пар содержит большее количество легколетучего (низкокипящего) компонента, чем исходная смесь, следовательно, в процессе перегонки состав пара и жидкости неодинаков: паровая фаза богаче легкокипящим компонентом, чем жидкость. Оставшаяся жидкая фаза называется
остатком, а конденсат паров – дистиллятом, илиректификатом.
Однократный процесс частичного испарения жидкой смеси и конденсации образующихся паров носит название простой перегонки, или дистилляции. Простая перегонка применяется для разделения компонентов жидкой смеси, летучести которых существенно различаются. На практике такой процесс используется для очистки сложных смесей от нежелательных примесей или для предварительного разделения на фракции.
При ректификации обеспечивается более четкое разделение компонентов в результате многократного или непрерывного противоточного контакта образующихся при перегонке паров с жидкостью, которая получается при конденсации пара.
Ректификация известна с начала XIX века как технологический процесс спиртовой и нефтяной промышленности. В современной химической технологии ректификацию используют для разделения газовых смесей, например, воздуха, для получения изотопов, полимеров, в производствах органического синтеза и т.д.
Разделяемая смесь в количестве G с параметрами xg, hg поступает в среднюю часть колонны в виде сухого насыщенного или влажного пара или в виде жидкости. В испарителе, расположенном в нижней части колонны, к жидкой смеси Ж подводится тепло Qи, в результате чего часть жидкости испаряется, а часть выводится из колонны в виде кубового остатка W с параметрами xw, hw. Образовавшийся пар П поднимается по колонне. В конденсаторе, установленном над верхней частью колонны, отводится тепло Qк, что приводит к конденсации поднимающегося пара. В конденсаторе в жидкость переходит практически чистый низкокипящий компонент. Часть его выводится в виде готового продукта Р с параметрами xр, hр, а часть в виде флегмы обратно поступает на орошение верхней части колонны. Таким образом в колонне образуются непрерывно движущиеся в противоположных направлениях потоки пара П и жидкости Ж.
Контакт между жидкостью и паром осуществляется на контактных устройствах, расположенных на разных уровнях. На каждом уровне создается постоянный слой жидкости, сквозь который барботирует пар. При этом в пар переходит больше низкокипящего компонента, а находящаяся на контактном устройстве жидкость обедняется по этому компоненту. Таким образом, проходя по колонне сверху вниз, жидкость обогащается высококипящим компонентом, и выводимая из нижней части колонны кубовая жидкость W является практически чистым высококипящим компонентом.
Так как пар, поднимающийся вверх, обогащается низкокипящим компонентом, температура конденсации его понижается. Жидкость, стекающая в нижнюю часть, обогащается высококипящим компонентом, и температура кипения ее повышается, вследствие чего верхняя часть колонны оказывается холоднее, а нижняя теплее. В результате на каждом уровне колонны температура восходящего пара П несколько выше температуры движущейся навстречу жидкости Ж. Таким образом, за счет подвода тепла в испарителе и отвода в конденсаторе по всей высоте колонны создается разность температур и концентраций, что обусловливает тепло- и массообмен между паром и жидкостью.
61
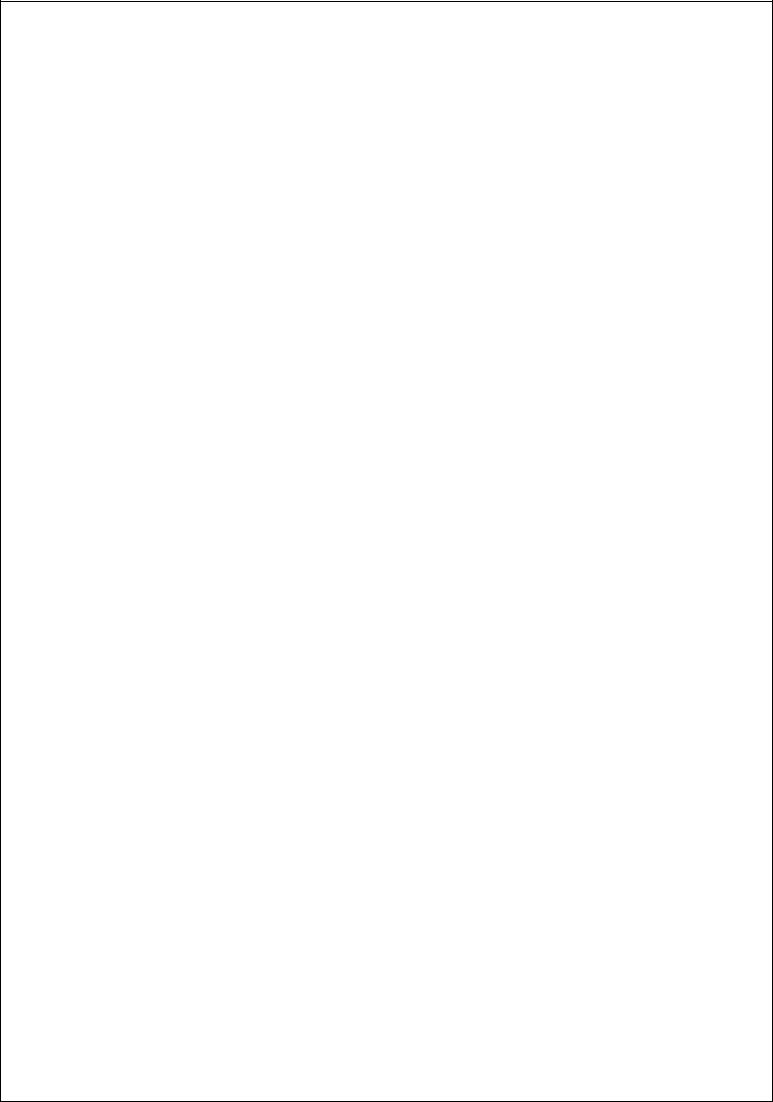
Низкотемпературная ректификация – это процесс разделения газовых смесей при низких температурах. Метод нашел широкое применение в промышленности для разделения воздуха с целью получения кислорода, азота и инертных газов (неона, криптона, ксенона, аргона); для получения водорода, дейтерия, гелия, окиси углерода, а также некоторых предельных углеводородных газов. Из числа непредельных углеводородов указанным методом выделяются мономеры для органического синтеза и, прежде всего, этилен и пропилен. Метод ректификации при низких температурах успешно применяется для очистки некоторых газов.
Низкотемпературная ректификация в большинстве случаев позволяет провести разделение с меньшей затратой работы, чем при других способах, и получить достаточно чистые продукты. Такие методы разделения газовых смесей как диффузионный, термодиффузионный, адсорбционный, магнитный, основанные на различии в свойствах молекул газов, являются достаточно энергоемкими и имеют ограниченное применение.
Низкотемпературная ректификация, в отличие от высокотемпературной, имеет ряд особенностей и в осуществлении самих технологических процессов, и в конструкции ректификационных аппаратов. Так, при ректификации смесей, кипящих при температурах выше температуры окружающей среды, тепло для подогрева испарителя колонны подводится извне специальным теплоносителем, например, водяным паром. При низкотемпературной ректификации для поддержания в системе низкой температуры затрачивается работа, и приток теплоты извне вызывает резкое увеличение энергозатрат. Поэтому подогрев испарителя в этом процессе осуществляется за счет энергии разделяемой смеси или продуктов разделения.
В высокотемпературных ректификационных установках охлаждение конденсатора и образование флегмы в колонне происходит за счет непосредственного теплообмена с окружающей средой (с охлаждающей водой). В процессе, идущем при низкой температуре, тепло конденсации должно отводиться хладагентом, а для получения хладагента необходимо затратить работу в холодильнойустановке.
Низкотемпературная ректификация в процессах химической технологии
Производство этилена и его выделение методом ректификации. Этилен (СН2=СН2)
является представителем ненасыщенных углеводородов, имеющих формулу СпН2п. Это бесцветный газ, почти не имеет запаха, горит светящимся пламенем; плохо растворим в воде, немного лучше в спирте и эфире. С воздухом и кислородом этилен образует взрывоопасные смеси. Соединения этилена с хлором и бромом представляют собой маслянистые жидкости, не смешивающиеся с водой.
Поскольку связи в этилене не насыщены, он обладает большой реакционной способностью и особенно склонен к реакциям присоединения и полимеризации. Присоединение атомов и молекул происходит, как правило, по месту разрыва двойной связи к обоим углеродным атомам. Например, при окислении этилена по реакции получается этиленгликоль, который в смеси с водой широко используется в качестве охлаждающих и незамерзающих растворов. Используя высокую реакционную способность этилена, из него получают многие ценные продукты: полиэтилен, этиловый спирт, этиленгликоль, хлористый винил, стирол и др.
В промышленном масштабе этилен и другие ненасыщенные углеводороды получают путем глубокого разложения углеводородного сырья (жидкого или газообразного) при достаточно высоких температурах. Этот процесс называется пиролизом (от греческого слова pyros – огонь). В газах пиролиза преобладают непредельные углеводороды, а в жидких продуктах (смолах) – ароматические углеводороды. Количественный выход газообразных олефинов зависит от характера сырья, а также от температуры и времени контакта. Наибольшее количество этилена получается при пиролизе этана (до 33 мол.%); при пиролизе пропана и газового бензина выход этилена составляет 24%; при пиролизе керосина – 18% и т. д. В газе пиролиза помимо этилена содержатся водород, метан, этан, ацетилен и некоторые другие компоненты.
62
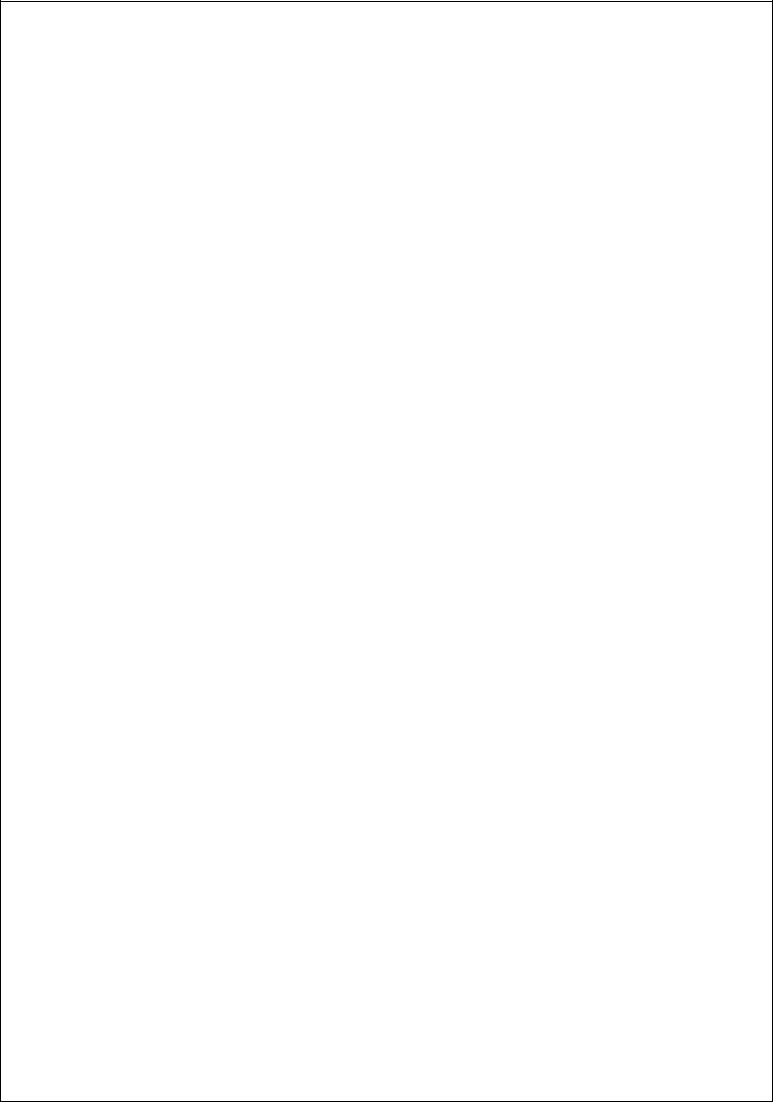
Выделение этилена из осушенного газа пиролиза возможно только при низких температурах, так как критическая температура его равна 282,7 К. Разделение газа пиролиза можно осуществить при низком и высоком давлениях. В нашей стране применяется, главным образом, способ разделения при высоком давлении, как более экономичный и менее трудоемкий. Разделение можно провести двумя методами: конденсационноректификационным и абсорбционноректификационным. В первом методе деметанизация, выделение и разделение этанэтиленовой фракции достигается конденсацией газа с последующей ректификацией его под давлением с применением аммиачного, метанового, этиленового (или пропанового) холодильных циклов. Во втором методе все компоненты тяжелее метана извлекают из газа абсорбцией при низких температурах и затем выделяют низкотемпературной ректификацией. Метановодородную фракцию конденсационноректификационным методом выделяют при температурах 183÷173 К, а абсорбционноректификационным – при 253÷243 К.
Получение хлористого винила и его выделение методом ректификации. Хлористый винил (СН2=СНСl) при обычных условиях представляет собой бесцветный газ. Его также называют винилхлорид или монохлорэтилен. Он находит широкое применение в технике, так как полимеризуется при действии катализаторов с образованием ценных пластических масс. Полимеризацию хлорвинила проводят обычно в водных эмульсиях в присутствии перекисей как катализаторов. Будучи дешевыми, доступными и негорючими, пластмассы из поливинилхлорида используются для изготовления искусственной кожи, линолеума, плащей, накидок, сумок и других предметов домашнего обихода. Пластифицированный поливинилхлорид в больших количествах расходуется на изоляцию кабелей и проводов связи, причем он одновременно заменяет каучук, свинец и хлопчатобумажную пряжу. Путем переработки поливинилхлорида получают винипласт. Эта твердая пластическая масса легко сваривается и поддается механической обработке, поэтому винипласт применяется для изготовления вентиляционных труб, насосов и различных частей аппаратуры. Хлорированием поливинилхлорида получают перхлорвиниловую смолу. В виде лаков и клеев ее применяют для поверхностных покрытий. Из перхлорвиниловой смолы производят волокно хлорин.
Продукты реакции содержат 93% хлористого винила, 6% хлористого водорода, 0,3% дихлорэтана и около 0,2% ацетальдегида, который образуется за счет гидратации ацетилена. Этот газ проходит систему очистки, состоящую из водяного 4 и щелочного 5 скрубберов для удаления хлористого водорода. После осушки и охлаждения в холодильнике 7 газ направляется на низкотемпературную ректификацию в колонну 9, которая орошается жидким хлористым винилом, охлажденным до 243 К в дефлегматоре 8. Кубовая жидкость выводится из куба 10 и используется в качестве растворителя, а хлористыйвинил с примесью ацетилена и инертных газов из верхней части колонны поступает в конденсатор 11, охлаждаемый рассолом с температурой 238 К. Конденсат самотеком поступает в куб колонны 12, верхняя часть которой охлаждается аммиаком, испаряющимся при разряжении и температуре 218 К. В этой колонне из хлористого винила отгоняются растворенные ацетилен и инертные газы, а жидкий хлористый винил перетекает в насадочную колонну 13 для окончательной очистки от ацетилена. Верхняя часть колонны 13 охлаждается рассолом с температурой 243 К; несконденсировавшиеся газы содержат 1÷5% ацетилена и возвращаются в колонну 12. В кубовой части колонны 13 находится хлористый винил, представляющий товарную продукцию этого производства. На получение одной тонны хлористого винила расходуется 450 кг ацетилена, 670 кг хлористого водорода и 0,2÷0,5 кг хлористой ртути.
63
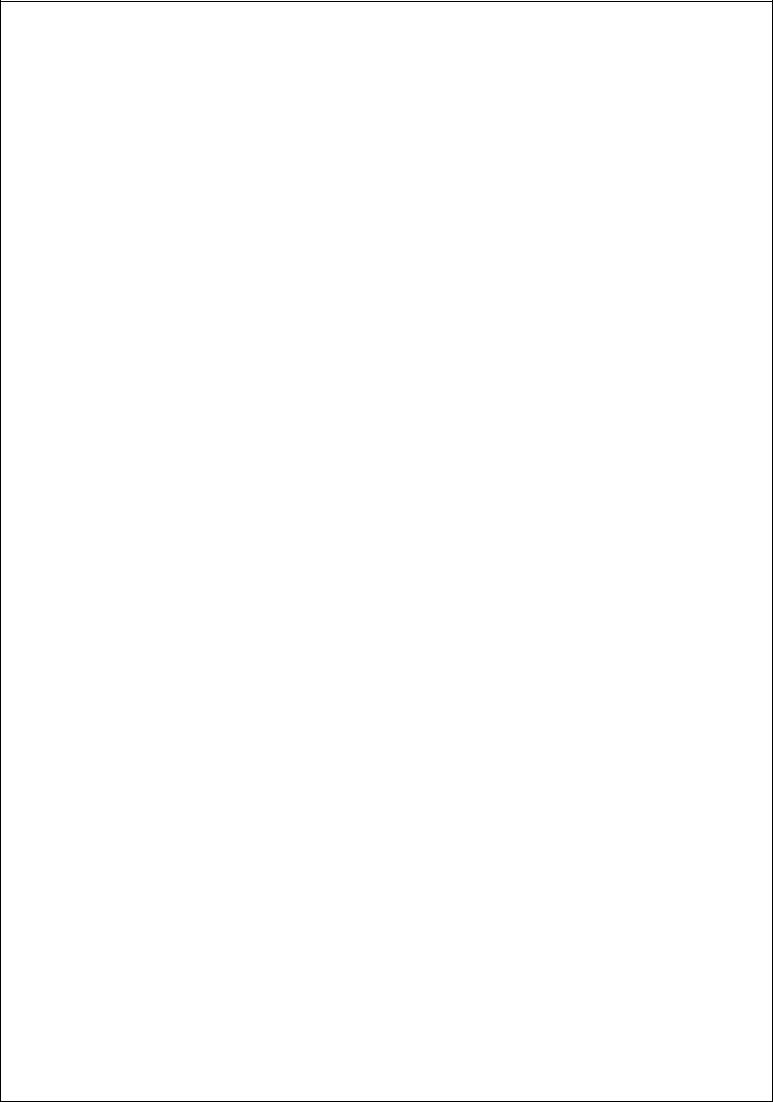
38. Конденсация. Основные понятия, виды и способы осуществления процесса конденсации. Применение конденсации в химической технологии
В технике конденсацией называют процесс перехода вещества из газообразного состояния в жидкое или твердое в результате его охлаждения. Конденсация паров возможна только при температурах ниже критической.
Конденсация, как и обратные процессы – испарение и возгонка, является примером фазовых превращений вещества. При конденсации выделяется то же количество теплоты, которое было затрачено на испарение (возгонку) сконденсированного вещества. Жидкость, образующаяся при конденсации, называется конденсатом. Конденсация широко применяется в технике: в энергетике (например, в конденсаторах паровых турбин), в химической технологии (в производстве аммиака, разделении газов методом фракционной конденсации), в холодильной и криогенной технике, в опреснительных установках и т. д.
Различают три вида конденсации: 1) поверхностная (или просто конденсация), при которой конденсирующиеся пары и охлаждающий агент разделены стенкой, и конденсация паров происходит на стенке; 2) контактная (конденсация смешением), при которой конденсирующиеся пары непосредственно соприкасаются с охлаждающим агентом; 3) объемная, происходящая внутри объема парогазовойсмеси.
Поверхностная конденсация осуществляется на охлаждаемых поверхностях и может быть пленочной (конденсат осаждается в виде сплошной пленки) и струйной или капельной (конденсат осаждается в виде капель). В большинстве случаев происходит пленочная конденсация, капельная наблюдается в том случае, если конденсат не смачивает поверхность стенки или если пар конденсируется с примесью масла или подобных ему веществ. Во всех случаях при капельной конденсации интенсивность теплообмена значительно выше, чем при пленочной, так как сплошная пленка конденсата затрудняет теплообмен. Конденсация начинается только тогда, когда пар у поверхности охлаждения достигает парциального давления и температуры, соответствующих состоянию насыщения (точке росы). Скорость конденсации тем выше, чем ниже температура поверхности по сравнению с температурой насыщения пара при заданном давлении. Наличие несконденсированного газа уменьшает скорость поверхностной конденсации, так как она зависит от скорости диффузии конденсирующегося пара через газовую пленку.
Если конденсации подвергаются пары нерастворимых в воде жидкостей или пар является отходом того или иного процесса (который в дальнейшем не будет использоваться), охлаждение и конденсацию этих паров можно проводить путем непосредственного смешения с водой.
Конденсация может происходить также внутри объема парогазовой смеси. Для осуществления объемной конденсации пар необходимо резко расширить. Начало конденсации зависит от содержания в парогазовой смеси мельчайших пылинок (аэрозолей), которые являются центрами конденсации (зародышами каплеобразования). Чем чище парогазовая смесь, тем труднее добиться объемной конденсации.
Для разделения газовых смесей применяют методы ректификации и фракционированной конденсации. Особенность процессов разделения таких газовых смесей как воздух, коксовый газ, метан, газы крекинга нефти и других состоит в том, что для сжижения их необходимо охлаждение до очень низких температур. Следует помнить, что процессу низкотемпературной ректификации сжиженных газов часто предшествует процесс низкотемпературной конденсации. Так, например, при фракционированной конденсации коксового газа при давлении 1÷1,2 МПа выделяют пять фракций: пропиленовую, этиленовую, метановую, окись углерода и водород. Дальнейшее разделение фракций на чистые компоненты производят методом низкотемпературной ректификации.
64
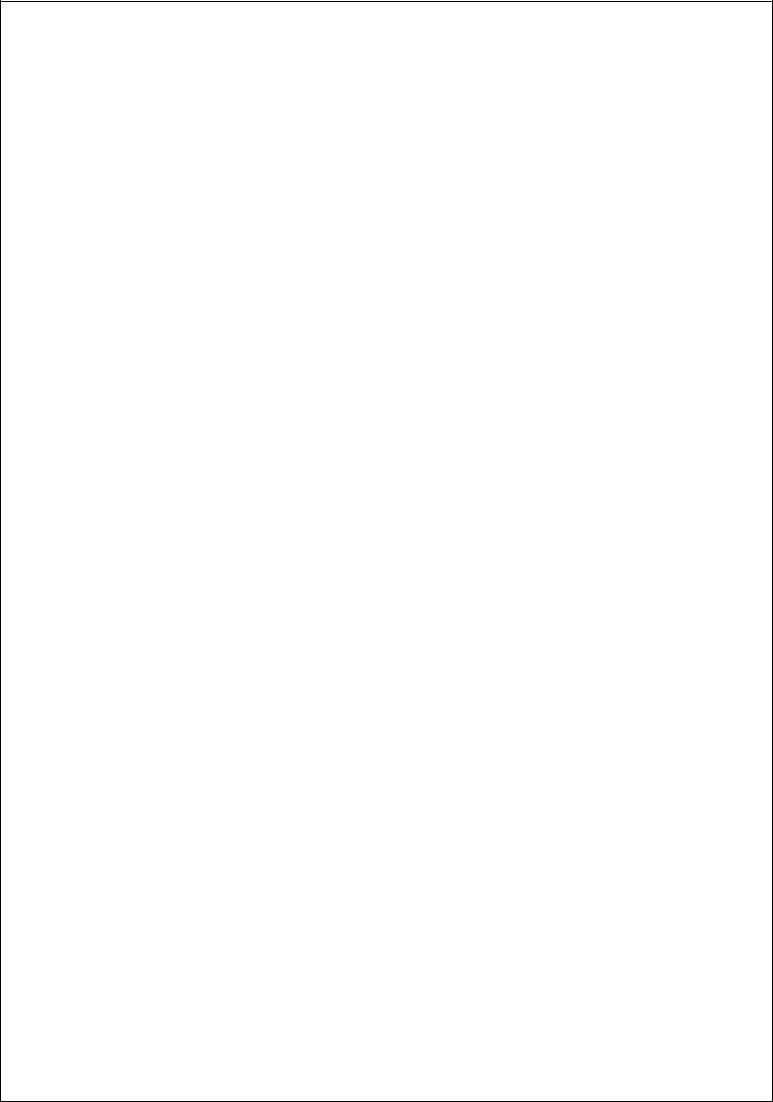
Применение конденсации в химическойтехнологии
Синтез аммиака. Простейшим и важным исходным продуктом для получения соединений, содержащих азот, является аммиак. Из аммиака получают азотную кислоту, азотные и сложные удобрения, различные соли, мочевину и др. Аммиак и соединения азота широко применяются в холодильной технике, в производстве соды, красителей, пластмасс, химических волокон, взрывчатых веществ и т. д., однако подавляющее количество соединений азота расходуется на производство удобрений.
Этот процесс экзотермический и протекает с уменьшением объема, поэтому с увеличением давления и понижением температуры равновесие реакции сдвигается вправо. Однако на практике синтез проводят при повышенной температуре (673÷773 К), так как с понижением температуры резко снижается скорость процесса. Для проведения реакции синтеза аммиака используется железный катализатор с добавками Аl2О3, К2О, CuO и SiO2. С повышением давления выход аммиака резко увеличивается. Так, при 673 К и 0,1 МПа выход аммиака равен 0,1%; при 20 МПа увеличивается до 17,6%; при 50 МПа выход может быть доведен до 33%, а при 100 МПа – до 60÷80%. Промышленные способы синтеза аммиака в зависимости от применяемого давления можно разделить на три группы: 1) под низким давлением (до 10 МПа); 2) средним (20÷30 МПа); 3) высоким (75÷100 МПа). 70% установок в мире – установки среднего давления.
Сырьевыми компонентами для получения аммиака являются атмосферный воздух, из которого выделяют азот, и природный или коксовый газ, являющийся источником водорода. Для приготовления азотоводородной смеси азот получают методом сжижения воздуха с последующей его низкотемпературной ректификацией (см. раздел 2.5.3), а водород – в основном методами конверсии метана с водяным паром или путем разделения коксового газа низкотемпературной фракционированной конденсацией.
Полученные газы – азот и водород – смешивают в определенном соотношении (N2:H2=1:3) и подают в цех синтеза аммиака. Предварительно азотоводородная смесь тщательно очищается от примесей кислорода, окиси и двуокиси углерода, воды и др., поскольку эти примеси отравляют катализатор. Особенно сильными ядами для катализатора являются сероводород и органические соединения серы. Очистку газа осуществляют различными методами: 1) низкотемпературной конденсацией; 2) каталитическим гидрированием примесей; 3) абсорбцией примесей жидкими и твердыми сорбентами.
65