
книги / Основные новые разработки в технологии метанола
..pdf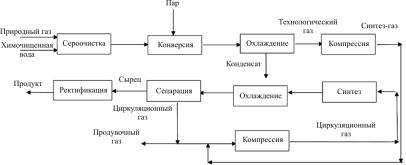
рах каталитического гидрирования и адсорбционного улавливания сероводорода. Основной стадией получения синтез-газа является стадия конверсии природного газа, в данном случае паровой.
Рис. 3. Блок-схема современного производства метанола
Процесс паровой конверсии в технологии метанола имеет много общего с таковым в технологии аммиака [6].
Основные реакции, протекающие при паровой конверсии природного газа, таковы:
CH4 H2O CO 3H2 206,19 кДж;
CO H2O CO2 H2 41,17 кДж.
При содержании в природном газе гомологов метана (этан, пропан) происходит их взаимодействие с водяным паром с образованием компонентов синтез-газа. В отличие от процесса паровой конверсии в производстве аммиака важнейшей задачей этого процесса в производстве метанола является как можно более полное превращение углеводородов в оксид углерода и водород. С учетом теоретических закономерностей процесса это достигается повышением температуры, понижением давления и применением избытка водяного пара. В производстве метанола на выходе из аппарата каталитической паровой конверсии природного газа (трубчатой печи) температура газа 860 °С (в производстве аммиака 760 °С), давление 1,86 МПа (в производстве аммиака 37 МПа), соотношение пар/газ составляет 2,9 (для аммиака 3,7).
11
Паровая конверсия природного газа в производстве метанола, как и в производстве аммиака, является наиболее энергозатратной стадией. На этой стадии природный газ расходуется в качестве сырья и в качестве топливного газа, идущего на возмещение энергии, затрачиваемой на протекание основных эндотермических реакций. Энергия топливного газа в виде горячих дымовых газов расходуется также на получение пара и нагревание технологических потоков (парогазовой смеси, воздуха горелок).
Конвертированный в реакционных трубах на никелевом катализаторе горячий технологический газ проходит ряд теплообменных устройств для утилизации тепла и охлаждения, а также три ступени сепарации для выделения технологического конденсата.
Кроме задачи снижения затрат на природный газ, на стадии конверсии должна решаться задача получения синтез-газа оптимального состава. Для синтеза метанола стехиометрическое соотношение Н2/СО равно 2.
В случае паровой конверсии метана теоретическое соотношение Н2/СО равно 3, практически же это соотношение несколько более 3 и составляет 3,2–3,6.
Поскольку соотношение в реальном синтез-газе выше стехиометрического, а синтез метанола проводится по циклической схеме, то в газе, поступающем в колонну синтеза, это соотношение увеличивается до 12 и более. Следовательно, в процессе синтеза метанола водород выступает в роли инерта, отрицательно влияя на выход метанола за один проход газа через катализатор.
Поэтому при проектировании новых производств часто выбирают способ конверсии природного газа с применением более активного и эффективного с точки зрения состава синтез-газа окислителя, например смеси пара и диоксида углерода, пара и кислорода, пара и воздуха.
Технологический газ после охлаждения и выделения воды поступает на компрессию. Центробежный компрессор синтез-газа с приводом от паровой турбины с противодавлением включает две ступени – низкого давления и высокого давления. После сжатия до давления 2,0–3,8 МПа в семи ступенях корпуса низкого давления
12
конвертированный газ с температурой до 160 °C подается на охлаждение в промежуточный холодильник. Далее после промежуточного сепаратора и сжатия в семи ступенях корпуса высокого давления до 8,1 МПа газ нагревается до температуры 170 °C и направляется в концевой холодильник.
Затем конвертированный газ подается на линию циркуляционного газа на всас однокорпусного циркуляционного компрессора с приводом от паровой конденсационной турбины. Давление газа на нагнетании компрессора не более 8,7 МПа, температура не более 90 °C. С этими давлением и температурой газ после нагревания в двух теплообменниках газом, выходящим из колонны синтеза, направляется на синтез метанола.
После компрессора циркуляционный газ распределяется на два потока и направляется в реакторы синтеза метанола. В каждый реактор загружается по 130,8 м3 медь-цинк-алюминиевого катализатора синтеза метанола. Далее в реакторах из оксидов углерода (CO, CO2) и водорода при давлении 6,0–8,5 МПа (при 100%-ной нагрузке по конвертированному газу) и температуре200–300 °C образуется метанол.
Реакция синтеза метанола экзотермична и обратима, поэтому необходимо ограничивать повышение температуры в зоне реакции. Это достигается подачей холодного циркуляционного газа через тороидальные распределители в смесители, где происходит смешение с горячим газом, вышедшим из слоя катализатора. После смесителей газ направляется на следующий слой катализатора. В реакторах синтеза метанола расположены три полки со смесителями, которые делят катализатор на четыре слоя.
В соответствии с теоретическими закономерностями в колонне синтеза протекают обратимая реакция образования метанола и побочные реакции образования примесей. Выход метанола и его содержание в газе после синтеза определяются условиями равновесия основной реакции (состав исходного газа, температура, давление), активностью и селективностью катализатора по отношению к основной и побочным реакциям. Активность и селективность катализатора зависят от химического и фазового состава, пористой структуры, размеров и формы гранул катализатора, а также от технологического режима его эксплуатации.
13
Прореагировавший газ выходит из реактора синтеза метанола
стемпературой 230–300 °C и содержанием метанола 5–6 %, охлаждается в подогревателях питательной воды, рекуперационных теплообменниках и объединяется в один поток с температурой 105–120 °C. Объединенный поток газа поступает в воздушный холодильник-кон- денсатор, где происходит конденсация метанола-сырца и охлаждение газа до минимально возможной температуры, которая зависит от времени года.
Далее газожидкостная смесь поступает в водяной холодильник, охлаждается до температуры не менее 20 °C и выдается в сепаратор, где происходит отделение метанола-сырца от непрореагировавшего газа.
Циркуляционный газ после сепаратора смешивается с конвертированным газом и поступает на всас циркуляционного компрессора. Давление в цикле синтеза метанола поддерживается путем постоянной продувки газа в отделение конверсии на сжигание через клапан, расход газа для продувки регулируется количеством газа, отводимого в топливную систему каждой из печей. Одновременно продувка обеспечивает заданный уровень инертов в цикле синтеза.
Отделившийся в сепараторе метанол-сырец поступает в сборник метанола-сырца, затем в расширительный сосуд и на склад.
Метанол-сырец содержит метиловый спирт, воду и органические примеси, к которым относятся сложные эфиры простых жирных кислот, различные кетоны, этанол, высшие спирты, а также небольшое количество растворенных газов.
Схема ректификации метанола включает две стадии – отгонку легких фракций и основную ректификацию. На стадии отгонки легких фракций от метанола-сырца отделяются легколетучие соедине-
ния: диметиловый эфир, растворенные газы CO, CO2, H2, CH4, N2. На стадии основной ректификации отделяются метанол-
ректификат, фракция метанол-масло-вода (сивушное масло), вода
ссодержанием метанола 0,02 мас. % (кубовый остаток).
Метанол из куба колонны отгонки легких фракций насосами подается в колонны основной ректификации на одну из тарелок (17, 20, 24, 26, 33-ю). Обе колонны основной ректификации работают
14
при следующем режиме: температура в верхней части колонны 71–77 °C, давление 0,125–0,16 МПа; температура в нижней части колонны 115–128 °C, давление 0,225–0,27 МПа.
Пары из верха колонны направляются в конденсаторы воздушного охлаждения, где конденсируются. Сконденсированный метанол поступает в сборник, а затем насосами в виде флегмы возвращается в колонну.
Метанол-ректификат отбирается с тарелок 81, 79 и охлаждается в холодильнике до температуры 35–40 °C. Этот отбор производится автоматически в соответствии с расходом метанола-сырца в колонну и с коррекцией по температуре на контрольной тарелке.
Фракция метанол-масло-вода (сивушное масло) отбирается с одной из тарелок в нижней части колонны.
Кубовый остаток колонн основной ректификации – вода с содержанием до 0,02 мас. % метанола – после охлаждения в теплообменнике направляется на биологическую очистку или в емкость сточных вод, из которой она периодически откачивается также для биологической очистки.
Важнейшим технико-экономическим показателем производства метанола являются энергозатраты, основную часть которых составляют затраты на природный газ. Как уже отмечалось выше, по технологии природный газ расходуется в качестве сырья, а также в виде топливного газа, сжигаемого в основных горелках трубчатой печи. Экономия сырьевого природного газа возможна либо за счет увеличения степени превращения метана в процессе конверсии, либо за счет повышения селективности катализатора синтеза метанола. Увеличение степени превращения метана ограничено влиянием технологических параметров на равновесие основной реакции конверсии и определяется в первую очередь температурой на выходе из реакционных труб. В настоящее время эта температура зависит от термостойкости материала труб: трубы, изготовленные из никелевого сплава с добавлением хрома, никеля, молибдена, ниобия, могут работать при температуре не выше 900 °C.
Экономия же топливного газа может быть достигнута за счет более полного и эффективного использования тепла топочного газа
15
вконвективной части трубчатой печи или за счет снижения соотношения пар-газ в исходном технологическом газе.
Энергетические затраты производства метанола снижаются при более полном превращении компонентов синтез-газа в метанол, т.е. при увеличении содержания метанола в газе после колонн синтеза. Это достигается при увеличении активности катализатора синтеза, оптимизации температурного режима в колонне синтеза, при использовании более близкого к стехиометрическому соотношения водород/оксид углерода. Перечисленные мероприятия способствуют увеличению количества тепла, выделяемого в процессе синтеза метанола
вединице объема катализатора, и дают возможность более эффективно использовать тепло экзотермической реакции синтеза.
Одним из радикальных способов снижения энергозатрат в производстве метанола является использование полностью или частично при получении синтез-газа вместо эндотермического процесса паровой конверсии углеводородов экзотермического процесса, т.е. замена в качестве окислителя водяного пара на воздух или кислород. Эта замена приводит к тому, что энергетические затраты на конверсию переходят в затраты на криогенное разделение воздуха на азот и кислород и при этом снижаются.
Еще один энергозатратный процесс в производстве метанола – это компрессия синтез-газа. Затраты на сжатие газов определяются давлением природного газа, поступающего на предприятия от магистрального газопровода, и разницей между давлением конверсии и синтеза метанола.
Известно, что удельные затраты в производстве химических продуктов снижаются при увеличении единичной мощности. Эта тенденция, как об этом говорилось ранее, сохраняется в метанольной отрасли по настоящее время.
При создании крупных производств (мегаметанол) разработчикам приходится сталкиваться с рядом сложных проблем, в частности с проблемами технологическими, проблемами изготовления, транспортировки, монтажа крупногабаритного оборудования. Как эти проблемы решаются на реконструируемых и вновь создаваемых
предприятиях по производству метанола, будет рассмотрено в последующих разделах пособия.
16
Большие возможности с точки зрения решения технологических задач дает комбинирование производства метанола с другими производствами, в частности с производством аммиака. Это направление также будет рассмотрено далее.
Отдельной проблемой в производствеметанолаявляется проблема рационального подбора и совершенствования катализаторов, на базе которых происходят основные процессы технологии: сероочистка природного газа, конверсия природного газа, синтезметанола.
В настоящее время в мире работают несколько крупных фирм, занимающихся разработкой, поставкой и научно-техническим сопровождением катализаторов для производств метанола.
Лидерами по производству катализаторов для синтеза метанола являются три известные в мире крупные компании: Johnson Matthey Catalysts (Великобритания), Sud-Chemie AG (Германия) и Haldor Topsoe (Нидерланды) [7].
Последней разработкой компании Johnson Matthey Catalysts являются катализаторы Katalco 51-8 и Katalco 51-9, которые содержат помимо основного носителя – алюмоцинковой шпинели – оксид магния, который способствует распределению кристаллитов меди с образованием большой площади реакционной поверхности.
Особенностью последнего катализатора C 79-7 GL компании SudChemie AG является оптимальный баланс между высокой активностью, селективностью и значительным (до 7 лет) сроком службы катализаторав широком диапазоне технологическихпараметров.
Компанией Haldor Topsoe предлагается катализатор марки МК-121, обладающий большими на 10 % активностью и на 15 % селективностью по сравнению с катализатором марки МК-101.
Положение с катализаторами для синтеза метанола в России и странах СНГ было практически катастрофическим, пока не возникла международная компания АЛВИГО (Россия – Украина – Эстония – Узбекистан), которая приобрела предприятия в Северодонецке и Новомосковске и наладила там производство катализатора СНМ-У, почти не уступающего зарубежным аналогам.
17
2.ТЕХНОЛОГИЧЕСКИЕ РЕШЕНИЯ
ВПРОИЗВОДСТВЕ МЕТАНОЛА НА УСТАНОВКАХ М-750
В России одним из ведущих предприятий по производству
ипереработке метанола является ПАО «Метафракс».
В2019 г. отмечено 60-летие производства метанола на Губахинской земле. На Губахинском химическом заводе в 1959 г. было построено и запущено крупное для того времени производство метанола с использованием в качестве сырья коксового газа, получаемого при коксовании угля Кизеловского угольного бассейна Пермской области. Коксовый газ после сероочистки и компримирования в поршневых компрессорах подавался на синтез метанола. Синтез метанола проводили в колоннах синтеза при давлении 300 атм на высокотемпературном цинк-хромовом катализаторе. Затем производство было переведено на природный газ и работало вплоть до 1979 г., когда было начато проектирование нового крупнотоннажного агрегата, запущенного в 1984 г.
Перед предприятием в 1979 г. стояла сложная задача выбора перспективного экономичного производства метанола большой единичной мощности. Эта задача была решена с помощью Дзержинского филиала Государственного института азотной промышленности (ГИАП), специализированного в СССР на производствах, связанных с метанольной отраслью химической промышленности. Был проведен сравнительный анализ возможностей отечественной индустрии и предложений крупных зарубежных фирм, в частности японской Mitsubisy Gas Chemical и английскойInternal Chemical Industries (ICI).
ВСССР в то время не было опыта проектирования и строительства крупных агрегатов по производству метанола. Были разработаны и запущены в Щекино и Новомосковске агрегаты М-200, спроектированные Дзержинским филиалом ГИАП. Однако технический уровень этих агрегатов не соответствовал мировому уровню.
Сравнение предложений японской и английской фирм показало преимущества последней. К тому времени фирмой ICI была освоена
18
схема синтеза метанола под давлением 5 МПа при температуре 220 °С, в которой была решена задача эффективного использования избыточного водорода, образующегося в процессе паровой конверсии метансодержащего природного газа. По предложению фирмы Davy Pauer Gas продувочный газ цикла синтеза метанола использовался в качестве топлива в трубчатой печи конверсии наряду с природным газом. Это позволило повысить энергоэффективность производства за счет экономии топливного природного газа.
Таким образом, был заключен контракт с фирмой ICI на проектирование и поставку оборудования для производства метанола мощностью 750 тыс. т.
В состав установки входят агрегат сероочистки природного газа, две параллельно работающие трубчатые печи, две колонны синтеза метанола, одна колонна отгонки легколетучих примесей, две колонны основной ректификации. Кроме того, предусмотрено строительство вспомогательного парового котла высокого давления, установки получения деминерализованной воды, факела для сжигания горючих газов во время пуска и остановок, склада метанола с насосной станцией и эстакадой для налива, емкостидляхранения сивушного масла.
Помимо утилизации продувочных газов, в технологии М-750 предусмотрено максимальное на то время использование энерготехнологического принципа – наиболее полное полезное использование тепла экзотермических химических процессов и тепла высокотемпературных технологических потоков. Так, предусмотрено использование тепла дымовых газов трубчатых печей паровой конверсии природного газа для получения пара высокого давления, нагревания смеси природного газа и водяного пара, перегрева пара, нагревания воздуха для горелок трубчатой печи. Тепло технологического газа после трубчатых печей используют в котле-утилизаторе 1-й ступени, нагревателе питательной воды 2-й ступени, испарителе основных ректификационных колонн, испарителе колонны отгонки легких фракций и нагревателе питательной воды 1-й ступени.
Особенностью трубчатых печей агрегата М-750 является использование реакционных труб, изготовленных из специального никелевого сплава, обладающего жаростойкостью и высокими пределами теку-
19
чести. Трубы изготавливаются центробежным литьем и имеют длительный срок службы. При работе печи контролируются степень нагрева труб по их относительному удлинению и появление белых и черных пятен, свидетельствующих о неравномерности их нагревания.
Еще одна особенность трубчатых печей в производстве метанола состоит в том, что в их работе в качестве топлива используют, помимо природного газа, продувочный газ цикла синтеза, а также образующиеся в производстве другие горючие газы и жидкости, в частности газ отдувки легких фракций и сивушные масла, выделяемые при ректификации метанола-сырца.
Технологический газ после трубчатых печей, охлажденный и освобожденный от паров воды, поступает на компрессию и далее на синтез метанола, присоединяясь к циркулирующему газу.
Синтез метанола в агрегате М-750 осуществляется в колоннах синтеза полочного типа. Используются колонны синтеза английской фирмы Davy Pauer Gas с четырьмя полками катализатора. Полки катализатора работают в адиабатическом режиме с охлаждением между полками путем подачи байпасного циркулирующего газа. Фирмой разработаны и использованы в колонне эффективные смесители выходящего после полки газа и холодного байпасного газа. Надежное смешение газовых потоков обеспечивается распределительными трубами, снабженными ромбовидными элементами с металлическими сетками. Газ из колонны синтеза отводится через специальный собирающий коллектор. Конструкция колонны позволяет поддерживать оптимальный температурный режим и обеспечивает минимальное гидравлическое сопротивление.
В целом конструкция колонны синтеза отличается простотой, надежностью и эффективностью работы.
После охлаждения газа синтеза с утилизацией его тепла, конденсации и выделения в сепараторах метанола-сырца промежуточный продукт направляется на ректификацию для выделения примесей с получением метанола-ректификата.
Особенностями стадии ректификации в агрегате М-750 являются применение эффективных с точки зрения массо- и теплопередачи колонн с ситчатыми тарелками и использование тепла технологического газа в испарителях колонн ректификации.
20