
книги / Основные новые разработки в технологии метанола
..pdfВ табл. 2 приведены характеристики основных аппаратов технологии метанола М-750.
Таблица 2
Технологические параметры и характеристики основного оборудования в технологии метанола М-750
Вид |
Основное |
Технологические |
Технические |
оборудования |
назначение |
параметры |
характеристики |
Трубчатая |
Конверсия при- |
Рабочие условия: |
Количество реакци- |
печь парового |
родного газа во- |
температурагазана |
онных труб 496; |
риформинга |
дяным паром |
выходеизреакцион- |
диаметр реакцион- |
(конверсии) |
с получением |
ныхтруб888 C; |
ных труб (внеш- |
|
синтез-газа |
давление на выходе |
ний/внутренний) |
|
|
из реакционных |
124/102 мм; |
|
|
трубРизб = 1,9 МПа |
общаядлинареакци- |
|
|
(19 кгс/см2); |
онныхтруб13,9 м; |
|
|
объемная скорость |
общий объем за- |
|
|
2380 ч–1 |
груженного катали- |
|
|
|
затора 55 м3 |
Циркуляци- |
Сжатие смеси |
Производительность |
Коэффициент сжа- |
онный ком- |
синтез-газа и |
2345820 м3/ч; давле- |
тия 1,382; частота |
прессор |
циркуляционно- |
ниенавсасе8,1 МПа, |
вращения ротора |
|
го газа до давле- |
нанагнетании |
5980 об/мин; мощ- |
|
ния синтеза ме- |
8,8 МПа; температу- |
ность паровой тур- |
|
танола |
ранавсасе45 C, на |
бины 5980 кВт |
|
|
нагнетании100 C |
|
Колонна |
Синтез метанола, |
Рабочие условия: |
Диаметр 4380 мм, |
синтеза |
поддержание |
температура на вхо- |
высота 17 150 мм, |
|
оптимального |
де 200–255 °C, на |
объем загруженного |
|
температурного |
выходе 200–255 °C; |
катализатора 139 м3 |
|
режима |
давление 8,5 МПа; |
|
|
|
объемная скорость |
|
|
|
6135 ч–1 |
|
Колонна ос- |
Выделение при- |
Рабочие условия: |
Диаметр 5000 мм, |
новной рек- |
месей из метано- |
температура в верх- |
высота 59500 мм, |
тификации |
ла-сырца, полу- |
ней части 78 °C, |
число ситчатых та- |
|
чение метанола- |
в нижней части |
релок 83 |
|
ректификата |
88 °C; давление |
|
|
|
в верхней части |
|
|
|
0,18 МПа, в нижней |
|
|
|
части 0,22 МПа; |
|
|
|
флегмовое число 3,0 |
|
31
После того как Губахинский химический завод в 1993 г. был переименован в АО «Метафракс» и в основном успешно преодолел сложные 90-е гг., стала очевидной большая опасность узко ориентированного на метанол производства и зависимости предприятия от экспортной продажи метанола (70 % прибыли). Программа, которую «Метафракс» начал реализовывать в 2001 г., была направлена на увеличение ассортимента выпускаемой химической продукции, более глубокую переработку метанола, модернизацию и увеличение объема его производства.
Анализируя представленную выше технологию М-750 и учитывая ее достоинства и недостатки, можно предположить, в каком направлении должна была развиваться эта технология для решения основной задачи, связанной с модернизацией технологии, увеличением объема производства метанола и улучшением техникоэкономических показателей. Такой анализ показывает следующее.
Проектная величина основных энергетических затрат на природный газ составляла 1195 м3/т, что по сравнению с действовавшими на то время производствами метанола было значительно меньше (например, 1300 м3/т в агрегатах М-200). Снижение затрат природного газа было достигнуто, в основном, за счет применения энерготехнологической схемы (утилизация тепла конвертированного газа и дымовых газов), использования тепла конвертированного газа в испарителях колонн ректификации и использования в качестве топливного газа в трубчатой печи продувочного газа цикла синтеза и горючих компонентов, выделенныхприректификацииметанола-сырца.
Основными узкими местами в технологии М-750, которые ограничивают мощность, являются печи конверсии природного газа, колонны синтеза метанола, колонны основной ректификации, компрессорное оборудование.
Основное направление увеличения производительности и эффективности работы трубчатых печей связано с увеличением диаметра реакционных труб и использованием труб, изготовленных из более жаропрочного материала. Такая модернизация позволяет увеличить количество загружаемого в трубы катализатора и повысить тепловую нагрузку. Это, в свою очередь, приводит к возрастанию
32
времени контактирования и степени превращения метана, а также позволяет понизить соотношение пар/газ. Помимо этого, при модернизации трубчатых печей необходимо обратить внимание на оптимизацию утилизации тепла дымовых газов.
Недостатком используемой в технологии М-750 колонны синтеза фирмы Davy Pauer Gas является использование для оптимизации температурного режима по высоте колонны байпасного газа, который вводится между полками с катализатором. Проблемы заключаются в том, что возникают трудности со смешением горячего
ихолодного потоков и с равномерным распределением газа по диаметру колонны перед его подачей на следующую полку с катализатором. При увеличении мощности такой способ отвода тепла реакции становится малоэффективным и не позволяет решить задачи оптимизации температурного режима, а следовательно, снижает скорость процесса синтеза метанола.
При модернизации колонн синтеза метанола следовало решить проблему эффективного использования байпасного газа, а в перспективе решить вопросы с заменой существующего способа отвода тепла на более эффективный.
При реконструкции отделения ректификации нужно было обратить внимание на использование более эффективных тарелок, в частности клапанных, которые повышают скорость массопередачи
ипозволяют сохранять надежную работу колонн при изменяющейся, в том числе увеличивающейся, нагрузке.
Модернизация компрессорного оборудования должна предусматривать совершенствование оборудования привода (паровые турбины) и ротора самого компрессора.
Эффективным направлением модернизации производства М-750 является разработка технологических решений, обеспечивающих получение синтез-газа, оптимального по составу для синтеза метанола.
Каким образом проблемы модернизации производства метанола на установках М-750 решались в ОАО «Метафракс», будет рассмотрено в следующем разделе.
33
3. ТЕХНОЛОГИЧЕСКИЕ РАЗРАБОТКИ ПРИ РЕКОНСТРУКЦИИ ПРОИЗВОДСТВА МЕТАНОЛА
НА УСТАНОВКАХ М-750 С УВЕЛИЧЕНИЕМ МОЩНОСТИ ДО 1,2 МЛН Т
В2019 г. исполнилось 35 лет со дня пуска крупнотоннажного агрегата по производству метанола М-750 на Губахинском химическом заводе, ныне ПАО «Метафракс».
Уже при проектировании М-750 были заложены определенные предпосылки для дальнейшего развития производства. В частности,
втехнологии заложено дублирование аппаратов на лимитирующих стадиях производства – стадиях конверсии природного газа и синтеза метанола, что придало ей гибкость и возможность варьирования объема производства.
На стадии синтеза метанола выбраны колонны синтеза простой и надежной конструкции, позволяющей использовать различные варианты модернизации с минимальными затратами.
Уже в 1994 г. была проведена реконструкция колонн синтеза метанола по проекту фирмы Methanol Casale SA и Института катализа Сибирского отделения АН СССР. Вместо демонтированных ромбовидных распределителей газа были смонтированы устройства, обеспечивающие размещение четырех радиальных слоев катализатора. Между слоями катализатора были установлены смесители горячего циркуляционного и холодного байпасного газа. Конструкции корзин с катализатором обеспечивали более равномерное распределение газа по слою и повысили скорость процесса синтеза при меньшем количестве загруженного катализатора. Результатом явилось повышение выхода метанолаи снижение количества побочных продуктов.
Вцелом модернизация производства метанола была реализована в два этапа: первый – с 1994 по 2006 г. с доведением мощности до 1 млн т/год, второй – с 2006 по 2017 г. с увеличением мощности до 1,2 млн т/год.
Основные этапы модернизации представлены в табл. 3.
34
Таблица 3
Хронология этапов модернизации производства метанола на установках М-750 с доведением мощности до 1,2 млн т [4]
Год |
Объект |
Сущность модернизации |
модернизации |
модернизации |
и ее результат |
1994 |
Колонны |
Установка 4 полок с радиальным ходом |
|
синтеза |
газа и новых смесителей. Улучшение каче- |
|
|
ства смешения горячего и холодного пото- |
|
|
ков циркуляционного газа, увеличение вы- |
|
|
хода метанола, повышение качества мета- |
|
|
нола-сырца |
1995 |
Вторая печь |
Замена реакционных труб на трубы с |
|
конверсии |
большим внутренним диаметром (106 мм) |
|
|
и повышенной жаростойкостью. Улучше- |
|
|
ние распределения потока дымовых газов. |
|
|
Увеличение времени контактирования |
|
|
и степени конверсии метана |
1995 |
Компрессор |
Модернизация ротора турбины. Увеличение |
|
конвертиро- |
производительности компрессора на 9 % |
|
ванного газа |
|
1999 |
Реакторы гид- |
Совмещение стадий гидрирования и выде- |
|
рирования при- |
ления сероводорода в одном реакторе. |
|
родного газа и |
Уменьшение тепловых потерь, высвобож- |
|
выделения се- |
дение реактора |
|
роводорода |
|
2000 |
Компрессор |
Исключение из технологической схемы |
|
природного |
компрессора природного газа и сопутст- |
|
газа |
вующего оборудования. Подача природно- |
|
|
го газа непосредственно из магистрального |
|
|
газопровода. Снижение затрат пара, повы- |
|
|
шение надежности производства |
2001 |
Первая печь |
Замена реакционных труб на трубы с |
|
конверсии |
большим внутренним диаметром (106 мм) |
|
|
и повышенной жаростойкостью. Улучше- |
|
|
ние распределения потока дымовых газов. |
|
|
Увеличение времени контактирования и |
|
|
степени конверсии метана |
2004 |
Колонны рек- |
Замена ситчатых тарелок колонн отгонки |
|
тификации |
легких фракций и основной ректификации |
|
|
на более эффективные двухпоточные кла- |
|
|
панные тарелки с фиксированными мини- |
35
|
|
Продолжение табл. 3 |
|
|
|
Год |
Объект |
Сущность модернизации |
модернизации |
модернизации |
и ее результат |
|
|
клапанами. Увеличение КПД тарелок, сни- |
|
|
жение флегмового числа, увеличение мощ- |
|
|
ности отделения ректификации на 20 % |
2005 |
Аппараты воз- |
ПодачапаранизкогодавлениявАВОсотво- |
|
душного охла- |
домконденсатавдеаэратордеминерализо- |
|
ждения (АВО) |
ваннойводы. Исключениепотерьпарават- |
|
узла конденса- |
мосферу, возвратконденсатавводооборот |
|
ции |
|
2006 |
Установка |
Пуск в эксплуатацию установки проточного |
|
проточного |
синтеза метанола. Установлены дополни- |
|
синтеза |
тельный изотермический реактор синтеза |
|
|
метанола, работающий на смеси свежего |
|
|
синтез-газа и части циркуляционного газа, |
|
|
конденсаторы и сепаратор метанола, реку- |
|
|
перационные теплообменники и паросбор- |
|
|
ник с циркуляционными насосами для по- |
|
|
дачи воды в пластинчатые теплообменники |
|
|
для отвода тепла синтеза. Увеличение про- |
|
|
изводительности агрегата до 1 млн т/год. |
|
|
Снижение затрат на природный газ |
2006 |
Печи конвер- |
Заменачаститепловойаппаратурывтракте |
|
сии природного |
топочных газов, установкапластинчатых |
|
газа |
теплообменниковдляподогревавоздуха, |
|
|
добавлениетеплообменникадляподогрева |
|
|
топливногопродувочного газа. Использова- |
|
|
ние пара, полученноговпроточномреакторе, |
|
|
дляконверсииприродногогаза. Увеличение |
|
|
производительноститрубчатыхпечей, по- |
|
|
вышениеэнергоэффективностипроизводства |
2006 |
Вторая печь |
Замена труб с увеличением внутреннего |
|
конверсии |
диаметра до 110 мм, установка потолочных |
|
|
горелок нового типа. Увеличение объема |
|
|
загруженного катализатора, понижение |
|
|
соотношения пар/газ, снижение остаточно- |
|
|
го содержания метана в газе |
2009 |
Компрессор |
Реконструкция паровой турбины и ком- |
|
конвертиро- |
прессора синтез-газа. Рост производитель- |
|
ванного газа |
ности компрессора на 10 %, увеличение |
|
|
мощности турбины до 35 МВт |
36
|
|
Окончание табл. 3 |
|
|
|
Год |
Объект |
Сущность модернизации |
модернизации |
модернизации |
и ее результат |
2014 |
Компрессор |
Замена ротора компрессора, использование |
|
циркуляцион- |
сухих уплотнений вместо масляных. Повы- |
|
ного газа |
шение надежности работы производства |
2015 |
Колонны син- |
Изменение внутренней конструкции с уста- |
|
теза метанола |
новкой двух полок катализатора. |
|
|
Ввод байпасного газа на вторую полку. |
|
|
Катализатор на второй полке разделен на |
|
|
два слоя: верхний – адиабатический, ниж- |
|
|
ний – изотермический. Отвод тепла осуще- |
|
|
ствляется во встроенном пластинчатом теп- |
|
|
лообменнике с помощью кипящей воды. |
|
|
Увеличение объема загруженного катализа- |
|
|
тора до 212 м3, снижение затрат природного |
|
|
газа, увеличение производительности агре- |
|
|
гата до 3060 т/сутки |
2015 |
Первая печь |
Замена труб с увеличением внутреннего |
|
конверсии |
диаметра до 110 мм, установка потолочных |
|
|
горелок нового типа. Увеличение объема |
|
|
загруженного катализатора, понижение |
|
|
соотношения пар/газ, снижение остаточно- |
|
|
го содержания метана в газе |
2017 |
Установка по |
Вводвдействиекриогеннойустановкиразде- |
|
производству |
лениявоздуха(ВРУ) KDONA- |
|
кислорода, азо- |
12000(300)26000(120)/5500. Обеспечениецеха |
|
та и сжатого |
ипроизводствакомплексаАКМпредприятия |
|
воздуха |
газообразнымкислородом(установкаPOX), |
|
|
газообразнымазотомисжатымвоздухом. |
|
|
Производительностьповоздуху62400 м3/ч |
2017 |
Отделение |
Вводвдействие установкипарциального |
|
конверсии при- |
окисленияприродного газа(POX). Снижение |
|
родного газа |
расходаприродного газа, увеличениепроиз- |
|
|
водительностиагрегатадо1,2 млнт/год |
2017 |
Отделение |
Замена насосов отделения ректификации, |
|
ректификации |
установка дополнительных аппаратов воз- |
|
|
душного охлаждения. Увеличение произ- |
|
|
водительности агрегата до 1,2 млн т/год |
37
Анализируя данные табл. 3, можно отметить следующее. На каждом этапе модернизации производства метанола были соблюдены принципы последовательности и наибольшей эффективности принимаемых технологических решений. Эти принципы позволили сохранить нормальную работу агрегата на протяжении достаточно длительного периода модернизации и обеспечили гарантированное достижение положительных результатов по окончании каждого этапа.
Так, на начальных стадиях каждого этапа модернизации совершенствование было направлено на отделения конверсии природного газа, компрессии и ректификации. Это дало возможность в дальнейшем перейти к реконструкции отделения синтеза метанола и, следовательно, к завершению этапа модернизации.
Конечно, при модернизации всего производства пришлось так же решать вопросы реконструкции и совершенствования вспомогательных узлов и оборудования, например отделения деминерализованной воды, водооборотного цикла (градирни), системы КИПиА и АСУ ХТП, насосов и др.
Далее рассмотрим подробнее наиболее важные и крупные элементы модернизации, которые сыграли значительную роль при достижении конечных результатов, – это установка проточного синтеза метанола, колонны синтеза метанола по проекту фирмы Methanol Casale SA и установка высокотемпературного некаталитического парциального окисления углеводородов природного газа.
Проектирование и пуск установки проточного синтеза метанола
стали завершением первого этапа реконструкции производства. Предварительно были модернизированы колонны синтеза, трубчатые печи и колонны ректификации, что обеспечило создание резервов по производительности на этих стадиях. Оставалось увеличить мощность отделения синтеза метанола, так как существующие колонны синтеза не моглиобеспечить производства 1 млнтметанола вгод.
Идея использования дополнительного реактора, работающего на синтез-газе, ранее была предложена фирмой Udhe для производства аммиака. Однако применить ее для производства метанола в том же виде не представлялось возможным вследствие сложностей, связанных с проблемами образования примесей и обеспечения эффективного отвода выделяющегося при синтезе метанола тепла.
38
Специалистами ПАО «Метафракс» было принято компромиссное решение использовать дополнительный реактор синтеза с подачей в него смеси части синтез-газа и определенного количества циркуляционного газа. Состав смешанного газа был подобран так, что обеспечивал увеличение скорости синтеза в два раза по сравнению со скоростью синтеза в существующих колоннах за счет увеличения концентрации оксидов углерода и оптимизации состава и температурного режима. Одновременно это позволило выбрать конструкцию и размеры реактора, обеспечивающие при необходимой производительности эффективный отвод выделяющегося при протекании реакций тепла.
На рис. 9 представлена технологическая схема блока проточного синтеза.
Часть конвертированного газа с линии нагнетания компрессора
сдавлением не более 8,1 МПа и температурой 160 °C поступает
вблок проточного синтеза (БПС).
Циркуляционный газ, поступающий в БПС, отбирается после теплообменников, объединяется в один поток, а затем смешивается с конвертированным газом в определенном соотношении, зависящем от активности (срока службы) катализатора, загруженного в реактор 3.
Смесь конвертированного и циркуляционного газа поступает
вмежтрубную часть рекуперационного теплообменника 5 (температура газа на входе 120 °C). В теплообменнике 5 свежий газ подогревается до температуры 200–235 °C за счет тепла газа, выходящего из реактора 3 с температурой 220–280 °C.
Подогретый свежий газ поступает в реактор проточного синтеза 3. В реактор проточного синтеза загружен катализатор Katalco 51-8
вколичестве 48,89 т (39,5 м3). Часть катализатора ( 25 % от обще-
го объема) работает в адиабатическом режиме, остальная часть ( 75 % от общего объема) – в изотермических условиях. Разделения между адиабатическим и изотермическим слоями нет. Внутри слоя катализатора расположен внутренний теплообменник с плоскими теплообменными каналами для съема тепла реакции синтеза метанола.
39
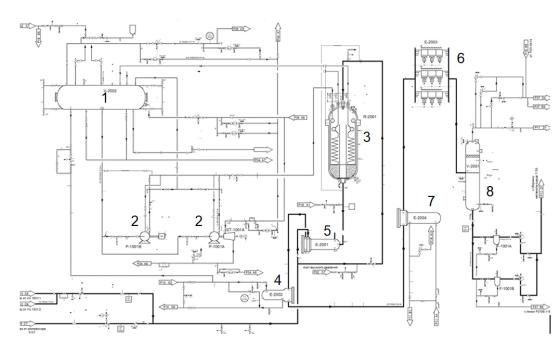
40
Рис. 9. Технологическая схема установки проточного синтеза: 1 – паросборник; 2 – насосы; 3 – реактор проточного синтеза; 4 – подогреватель питательной воды; 5 – рекуперационный теплообменник; 6 – аппарат воздушного
охлаждения; 7 – подогреватель продувочных газов; 8 – сепаратор
40