
книги / Основные новые разработки в технологии метанола
..pdf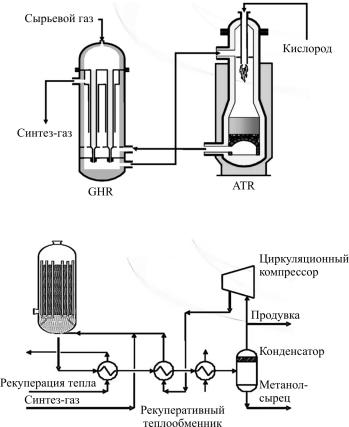
Рис. 15. Блок-схема риформинга с газовым обогревом
Рис. 16. Схема синтеза, включающая реактор с трубным охлаждением
Реактор с трубным охлаждением (рис. 16) представляет собой трубчатый реактор, в котором используется исходный газ для отвода тепла синтеза метанола и регулирования температуры в слое катализатора. Свежий сырьевой газ поступает в нижнюю часть реактора и нагревается по мере его движения вверх по трубам, помещенным в слой катализатора. Нагретый сырьевой газ выходит через верх труб и опускается вниз через слой катализатора, в котором протекает реакция. Теплота реакции отводится путем противоточного теплообмена с сырьевым газом, в итоге формируется темпера-
51
турный профиль, соответствующий близкой к максимальной скорости реакции. При такой конструкции реактора эффективно используется весь объем катализатора. Внутренняя оснастка реактора имеет относительно простую конструкцию, следует лишь учесть перепад давлений по высоте реактора. Толщина стенок труб сводится к минимуму, что упрощает изготовление трубной решетки на полное сечение аппарата. Таким образом, это недорогой реактор, в котором катализатор располагается в межтрубном пространстве, и его объем используется крайне эффективно.
В реакторе радиального типа с генерацией пара (рис. 17) катализатор также располагается в межтрубном пространстве, а кипящая вода проходит внутри труб. Свежий сырьевой газ поступает в нижнюю часть реактора через центральную распределительную трубу. Далее газ движется в радиальном направлении и выходит из слоя катализатора наружу. Вода из парового котла поступает в нижнюю часть реактора, движется по трубам вверх, где частично испаряется, отводя теплоту реакции, и затем поступает в паросборник. Температура реакции в слое катализатора регулируется за счет изменения давления пара внутри труб. Такая компоновка обеспечивает оптимальный температурный профиль в слое катализатора, сводя к минимуму необходимое количество катализатора. Радиальная схема потока позволяет увеличить высоту цилиндрической части реактора и, таким образом, повысить производительность реактора, не увеличивая его диаметр или перепад давления в контуре. В результате такой реактор может найти свое применение в установках большой мощности или на площадках, где существуют ограничения, связанные с перевозками аппаратов больших размеров.
Реактор аксиального типа с катализатором в трубах – еще одна разновидность реактора с генерацией пара. Как и в радиальном реакторе, данная конструкция обеспечивает хороший профиль температур в слое катализатора с минимально необходимым количеством катализатора, а также обеспечивает эффективную рекуперацию тепла в пар. Однако в таком реакторе необходимо установить «толстую» трубную решетку, которая ограничивает максимальный объем реактора. Кроме того, необходимо установить большое количество труб для размещения катализатора.
52
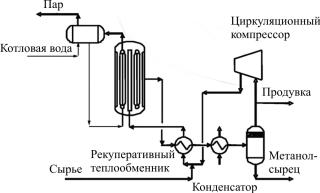
Рис. 17. Схема синтеза, включающая реактор радиального типа с генерацией пара
Примером разработки современного производства метанола
может служить производство метанола на заводе Atlas в островном государстве Латинской Америки Тринидад и Тобаго.
Завод Atlas по производству метанола мощностью 1,7 млн т в год, который считается одним из крупнейших в мире заводов по производству метанола с одной технологией, был запущен в 2004 г.
Завод Atlas был построен рядом с существующим заводом Titan, который работает по технологии кислородного риформинга для производства метанола мощностью 850 000 т в год. Среднее общее производство метанола на заводах составляет 2,5 млн т в год, что делает Тринидад иТобаго ведущимэкспортером метанола в мире.
Установка по производству метанола работает по технологии MegaMethanol, которая была разработана и поставлена немецким инженерным подрядчиком Lurgi. Считается, что это первый в мире завод по производству метанола, использующий эту технологию.
На заводе есть воздухоразделительная установка с производительностью 2800 т чистого кислорода в сутки. Технология разработана для мощностей по метанолу более одного миллиона тонн в год. При использовании технологии MegaMethanol природный газ конвертируется в метанол в больших количествах с меньшими затратами по сравнению с обычной технологией метанола.
53
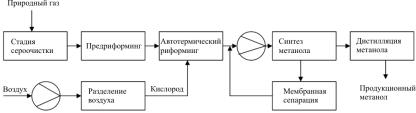
Производство метанола (рис. 18) включает в себя получение синтез-газа с использованием кислородного автотермического риформинга и двухстадийный синтез метанола по технологии фирмы Lurgi с изменением состава синтез-газа за счет рециркуляции водорода.
Рис. 18. Блок-схема производства метанола по технологии MegaMethanol компании Lurgi
Кислородный риформинг природного газа используется в режиме автотермического риформинга. Кислород используется в качестве агента риформинга, а предварительно подвергнутое риформингу и десульфуризированное сырье подвергается риформингу
спаром до синтез-газа под давлением около 40 бар.
Впроцессе производят синтез-газ с низким значением функ-
ционала (H2–CO2)/(CO+CO2), и его можно использовать с гибкостью работы для широкого диапазона требований. Температура на выходе из установки риформинга составляет примерно от 950 до 1050 °C. Синтез-газ затем сжимают с помощью одного компрессора до давления, необходимого для синтеза метанола.
Метанольный реактор аксиального типа содержит фиксированное количество трубных решеток, в которые загружается катализатор. Количество пара, образующегося в результате отвода тепла реакции, и его давление регулируются по мере необходимости. Изотермический реактор обеспечивает частичное преобразование син- тез-газа в метанол, снижает количество побочных продуктов, образующихся в процессе, и увеличивает выход при низких коэффициентах рециркуляции. Реактор с газовым охлаждением соединен последовательно с водоохлаждаемым реактором (рис. 19).
54
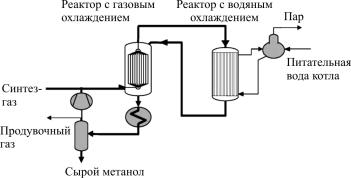
Газ, содержащий метанол, из первого реактора с водяным охлаждением переносится во второй реактор с газовым охлаждением, где происходит синтез с отводом тепла с помощью охлаждающих труб.
Продувочный газ направляется на выделение водорода, который используют для корректировки функционала синтез-газа.
Охлажденный метанол-сырец перерабатывается в ректификационной установке. Ректификация метанола-сырца происходит в энергоэффективной трехколонной ректификационной установке, благодаря которой экономится около 40 % греющего пара. Разделение колонн основной ректификации обеспечивает очень высокую производительность при использовании однолинейных систем.
Технология позволяет производить |
5000 т / сутки |
метанола |
в отличие от традиционных установок, |
производящих |
от 2000 |
до 2800 т / сутки. |
|
|
Используемый в технологии каскад реакторов синтеза метанола представлен на рис. 19, 20.
Рис. 19. Схема синтеза метанола с каскадом реакторов
Вработе [15] приведен анализ новых технологических решений
впроизводcтве MegaMethanol.
Эти решения касаются стадий получения синтез-газа и синтеза метанола. Отмечается, что традиционный способ парового риформинга природного газа становится экономически неэффективным для агрегатов мощностью 3000 т/сутки и более вследствие больших
55
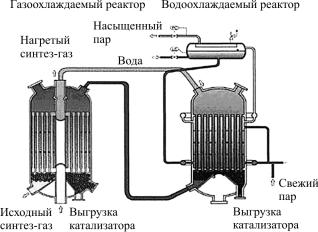
капитальных и энергетических затрат. Помимо этого, традиционный способ получения синтез-газа не позволяет обеспечить оптимальный для синтеза метанола состав исходного технологического газа, что приводит к значительному увеличению технологических потоков в цикле синтеза и, как следствие, к росту размеров реактора синтеза. Использующийся в технологии кислородный автотермический риформинг позволяет получать синтез-газ с функционалом, имеющим значение менее 2. Поскольку для синтеза метанола оптимальное значение функционала составляет 2,05–2,1, то в технологии предусмотрено выделение водорода на мембранной установке и его использование для корректирования состава исходного син- тез-газа.
Рис. 20. Схема работы каскада реакторов в производстве метанола
Цикл синтеза метанола, по мнению сотрудников компании Lurgi [14], имеет ряд достоинств и преимуществ по сравнению с циклом синтеза в традиционной технологии.
Синтез осуществляется в двух последовательно работающих реакторах. Первая стадия реакции протекает в трубчатом реакторе с водяным охлаждением, почти идентичном оригинальной
56
конструкции Lurgi. Тем не менее здесь происходит частичное преобразование синтез-газа на более высоких объемных скоростях и при более высоких температурах. Это приводит к значительному уменьшению размера реактора по сравнению с обычным процессом.
Газ, выходящий из реактора с водяным охлаждением, непосредственно направляется во второй реактор синтеза метанола – газоохлаждаемый реактор. Охлаждающей средой, проходящей через трубы этого реактора, является холодный исходный газ, предназначенный для первого реактора. Таким образом температура реагирующих газов в межтрубном пространстве постоянно снижается при прохождении через слой катализатора и поддерживается оптимальный профиль температуры. Каскадная схема синтеза метанола характеризуется степенью превращения выше 80 %. Таким образом, кратность рециркуляции может быть уменьшена на 50 % по сравнению с кратностью циркуляции в одноступенчатом реакторе с водяным охлаждением.
Поскольку свежий газ синтеза подается только на первую стадию, то катализаторные яды не поступают на вторую стадию, что приводит к практически неограниченному сроку службы катализатора для реактора с газовым охлаждением. Кроме того, двухступенчатое протекание реакции продлевает срок службы катализатора также и в реакторе с водяным охлаждением.
Если выход метанола в реакторе с водяным охлаждением будет снижаться в результате потери активности катализатора, то температура на входе реактора с газовым охлаждением будет возрастать. В результате скорость реакции синтеза и выход метанола на второй стадии будут возрастать, компенсируя снижение выхода на первой стадии синтеза.
В результате за счет 50 %-ного уменьшения объема катализатора для реактора с водяным охлаждением, уменьшения расхода тепла на предварительное нагревание исходного газа и экономии на другом оборудовании из-за более низкой кратности циркуляции достигается снижение затратна стадии синтезаприблизительнона 40 %.
57
Анализируя вышеизложенное и подводя итоги, можно отметить, что основные технологические решения, позволяющие существенно повысить мощность агрегатов синтеза метанола до 5000 и даже до 10 000 т/сутки, заключаются в использовании кислорода на стадии получения синтез-газа, оптимизации состава исходного синтез-газа, усовершенствовании конструкции реакторов синтеза с обеспечением оптимального температурного режима процесса синтеза и экономичного способа отвода тепла реакции синтеза, использовании усовершенствованных технологических схем цикла синтеза, в частности применении многореакторных схем синтеза метанола.
Отдельным направлением решения технологических, экономических и экологических проблем производства метанола является разработка комплексных схем совместного производства метанола и аммиака.
58
5. ТЕХНОЛОГИИ КОМБИНИРОВАНИЯ ПРОИЗВОДСТВ АММИАКА И МЕТАНОЛА
Комплексное использование сырья в химической промышленности не в последнюю очередь базируется на комбинировании производств продуктов, в основе технологии которых лежат одни и те же виды сырья, подобные технологические процессы и оборудование, одинаковые принципы и теоретические закономерности, на которых основываются технологии.
Комбинирование производств таких продуктов позволяет эффективно решать проблемы более полного использования сырья
иэнергетических ресурсов, уменьшения экологической нагрузки на окружающую среду, снижения капитальных затрат, оптимизации объемов производства продуктов и в целом улучшения экономических показателей предприятий, производящих данную продукцию.
Вышесказанное полностью относится к проблеме комбинирования производств аммиака и метанола. Эти производства базируются на использовании природного газа в качестве наиболее распространенного сырья. В технологиях аммиака и метанола применяют каталитические процессы на стадиях получения синтез-газа
ина стадиях синтеза самих продуктов. В основе получения аммиака
иметанола лежат обратимые каталитические процессы, равновесие которых сдвигается в сторону продуктов при понижении температуры и повышении давления. Продукты синтеза образуются в газообразном виде, сжижаются при охлаждении технологических газов
иотделяются от непрореагировавших газов в сепараторах.
Вработе Г.В. Мещерякова и др. [16] дан обстоятельный анализ проблемы комплексной переработки природного газа с использованием комбинирования производств аммиака, метанола и водорода. Анализ положений, касающихся комбинирования производств аммиака
иметанола, позволяет сделатьнекоторые выводыиобобщения.
Авторы совершенно обосновано привели в работе классификацию технологий комбинирования, в основе которой лежат парал-
59
лельное или последовательное расположение стадий синтеза аммиака и метанола после общих для обоих производств стадии подготовки природного газа и стадии получения синтез-газа. Для решения задачи экономичного использования сырья последовательная схема является предпочтительной. Далее в работе дается классификация последовательных технологий комбинирования. Технологии поделены на совместные производства, в которых синтез метанола проводится по стандартной схеме с рециклом газа, совместные производства, в которых синтез метанола производится в одном или нескольких последовательно расположенных реакторах с отбором метанола после каждого реактора, т.е. по схеме «за один проход», и совместные производства с комбинированной схемой синтеза метанола, где используются одновременно обе схемы.
На наш взгляд, в таком анализе не хватает рассмотрения конкретных случаев, которые возникают при решении задач выбора тех или иных технологических решений. В частности, на выбор технологии комбинирования производств аммиака и метанола большое влияние могут оказать различные факторы: каково соотношение мощностей продуктов, решается ли задача комбинирования при строительстве новых производств или при модернизации уже существующего производства одного из продуктов, предполагается ли в дальнейшем перенастройка уже действующих производств и т.п.
Кроме того, в работе [16] не сделан акцент на тех обстоятельствах, которые приводят к необходимости комбинирования производств аммиака и метанола, а также на особенностях и недостатках отдельных производств, которые обусловливают возможность и настоятельную необходимость комбинирования с достижением положительных результатов.
Анализ производств аммиака и метанола позволяет сделать вывод, что часто необходимость их комбинирования появляется в тех случаях, когда на предприятии возникают проблемы со сбытом продукции либо стоит задача расширения ассортимента выпускаемых продуктов в связи с меняющейся конъюнктурой рынка.
Особенностью производств аммиака и карбамида является наличие в циклах синтеза постоянной продувки, которая связана
60