
книги / Основные новые разработки в технологии метанола
..pdfДалее будут рассмотрены технологические схемы и оборудование важнейших стадий производства метанола по технологииМ-750 [4].
Поскольку на момент запуска агрегата М-750 в 1984 г. на «Метафраксе» природный газ поступал из магистрального газопровода с давлением 0,5 МПа, то в технологии было предусмотрено компримирование в центробежном компрессоре до давления 3 МПа. Перед компримированием природный газ разделяется на два потока. Один поток направляется в трубопровод топливного газа, который используется в трубчатых печах и огневом подогревателе. Второй поток после сепарации, предварительного нагревания в огневом подогревателе и смешивания с небольшим количеством циркуляционного газа направляется в компрессор с паровым приводом и затем в систему сероочистки. Система сероочистки включает в себя реакторы гидрирования и выделения серы на оксидном цинковом катализаторе.
Очищенный от соединений серы технологический газ смешивается с водяным паром среднего давления и подается в подогреватель парогазовой смеси, расположенный в конвективной части трубчатой печи (рис. 4). Парогазовая смесь нагревается до температуры 510 °C и распределяется по трубам печи с помощью системы коллекторов и пиктейлей, расположенных в верхней части печи. В радиационной зоне каждой печи размещено 496 реакционных труб с внутренним диаметром 102 мм, расположенных в 16 рядов по 31 штуке в каждом ряду. Трубы выполнены из хромоникелевого сплава, длина нагреваемого участка 12,19 м. Трубы заполнены никелевым катализатором. Общий объем загруженного катализатора составляет 55 м3 на одну печь. В реакционных трубах на никелевом катализаторе протекает реакция конверсии метана. Наряду с основной реакцией конверсии метана протекает ряд побочных реакций.
Система утилизации тепла дымовых газов (см. рис. 4) включает в себя следующее оборудование: паросборник 1; защитный котел радиантной зоны 2, в котором происходит образование пара за счет охлаждения дымовых газов до 900–970 °C; перегреватель пара высокого давления 3, где дымовые газы охлаждаются до 630–720 °C; подогреватель питательной воды 4; подогреватель парогазовой смеси 5, в котором температура дымовых газов снижается до 560 °C;
21
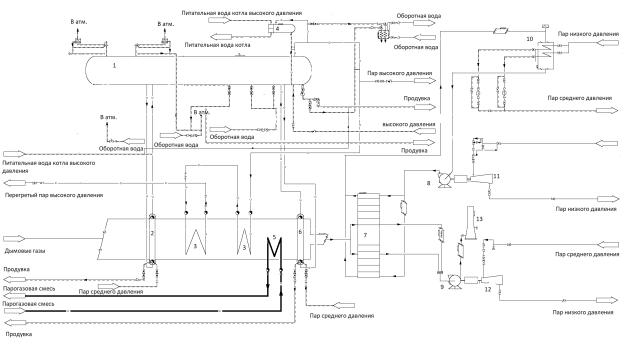
22
Питательная вода котла
Пар среднего давления
Рис. 4. Утилизация тепла дымовых газов трубчатой печи: 1 – паросборник; 2 – защитный котел; 3 – перегреватели пара высокого давления; 4 – подогреватель питательной воды; 5 – подогреватель парогазовой смеси; 6 – котелутилизатор дымовых газов; 7, 10 – подогреватели воздуха; 8 – воздуходувка; 9 – дымосос; 11 – паровая турбина
воздуходувки; 12 – паровая турбина дымососа; 13 – дымовая труба
22
котел-утилизатор 6, где получается пар за счет охлаждения дымовых газов до 375–405 °C; подогреватель воздуха для горелок 7, где нагревается воздух для горелок за счет охлаждения дымовых газов до 110–160 °C; воздуходувку 8; дымосос 9; подогреватель воздуха для горелок 10; паровую турбину воздуходувки 11; паровую турбину дымососа 12 и дымовую трубу 13.
Конвертированный газ, содержащий оксид углерода, водород, диоксид углерода, водяные пары, остаточный метан в количестве не более 2 %, направляется в систему утилизации тепла, конденсации водяных паров и выделения технологического конденсата (рис. 5).
Тепло конвертированного газа, выходящего из нижней части трубчатой печи двумя потоками, используется для получения пара в двух котлах-утилизаторах 1. В котлах производится пар высокого давления за счет охлаждения конвертированного газа до
300–420 °C.
После котлов-утилизаторов оба потока конвертированного газа направляются в нагреватель питательной воды 3, где конвертированный газ охлаждается до 320 °C. Конвертированный газ после нагревателя питательной воды поступает в отделение ректификации.
Охлаждение конвертированного газа до 140 °C происходит в испарителе колонны основной ректификации 2, в котором наряду с использованием физического тепла газа используется тепло конденсации водяных паров.
Технологический конденсат, образовавшийся за счет конденсации водяных паров в испарителе, отделяется от конвертированного газа в сепараторе 4.
После сепаратора 4 конвертированный газ поступает в испаритель колонны отгонки легких фракций 5, где охлаждается до 170 °C. В нагревателе деминерализованной воды 6 за счет охлаждения конвертированного газа происходит нагрев деминерализованной воды перед деаэрацией до 70–90 °C.
Технологический конденсат, образовавшийся за счет конденсации водяных паров в испарителе 5 и нагревателе 6, отделяется от конвертированного газа в сепараторе 7.
23
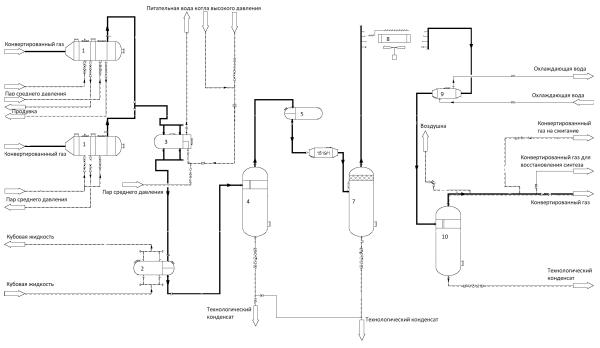
24
6
Рис. 5. Утилизация тепла, охлаждение и выделение водяного пара из конвертированного газа: 1 – котелутилизатор конвертированного газа; 2 – испаритель колонны основной ректификации; 3 – нагреватель питательной воды; 4, 7, 10 – сепараторы; 5 – испаритель колонны отгонки легких фракций; 6 – нагреватель деминерализованной
воды; 8 – аппарат воздушного охлаждения; 9 – водяной холодильник
24
Окончательное охлаждение конвертированного газа осуществляется сначала до 60 °C в аппаратах воздушного охлаждения 8, а затем до 40 °C в водяном холодильнике 9. В сепараторе 10 из конвертированного газа выделяется технологический конденсат, образующийся за счет конденсации водяных паров. Охлажденный конвертированный газ направляется на всас компрессора. Давление конвертированного газа в пределах 1,2–1,8 МПа поддерживается изменением числа оборотов компрессора.
После сжатия конвертированного газа (синтез-газа) до давления 2,0–3,8 МПа в семи ступенях корпуса низкого давления этот газ
стемпературой до 160 °C подается на охлаждение в промежуточный холодильник. Образовавшийся при охлаждении конвертированного газа конденсат отделяется в сепараторе. Затем конвертированный газ поступает на всас корпуса высокого давления компрессора, где сжимается в семи ступенях до 8,1 МПа и при этом нагревается до температуры 170 °C. Конвертированный газ направляется в холодильник 9, в котором охлаждается до температуры не выше 10 °C.
После сепаратора 10 (см. рис. 5) конвертированный газ подается на всас циркуляционного компрессора 1 (рис. 6).
Перед всасом циркуляционного компрессора 1 синтез-газ смешивается с циркуляционным газом. Циркуляционный компрессор однокорпусный с приводом от паровой конденсационной турбины 2. Давление газа на нагнетании компрессора не более 8,7 МПа. Производительность компрессора регулируется изменением числа оборотов турбины 2 и изменением расхода пара на ее регулирующую ступень.
Циркуляционный газ выходит из реакторов синтеза метанола
стемпературой 230–300 °C, охлаждается в подогревателях питательной воды, рекуперационных теплообменниках и объединяется в один поток с температурой 105–120 °C. Объединенный поток газа поступает в воздушный конденсатор-холодильник 6 (см. рис. 6), где происходит конденсация метанола-сырца и охлаждение газа до минимально возможной температуры, которая зависит от времени года. Управление процессом конденсации метанола-сырца в конден- саторе-холодильнике производится подачей охлаждающего воздуха
25
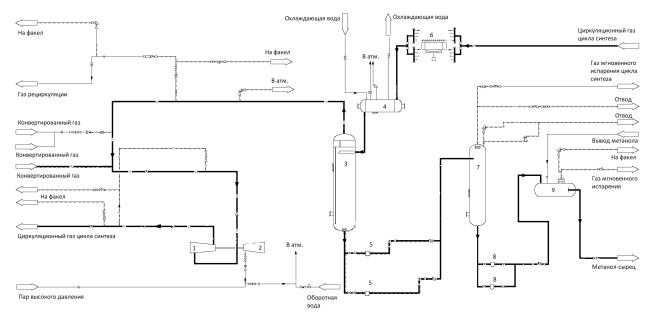
26
Рис. 6. Выделение метанола-сырца и компрессия циркуляционного газа: 1 – циркуляционный компрессор; 2 – турбина циркуляционного компрессора; 3 – сепаратор метанола-сырца; 4 – водяной конденсатор-холодильник метанола-сырца; 5 – фильтр метанола-сырца высокого давления; 6 – воздушный конденсатор-холодильник метанола-сырца; 7 – сборник метанола-сырца; 8 – фильтрметанола-сырцанизкогодавления; 9 – расширительныйсосудметанола-сырца
26
на трубные пучки через жалюзи и количеством включенных вентиляторов. При повышении температуры газа до 80 °C предусмотрена сигнализация. Далее газожидкостная смесь поступает в водяной холодильник 4, охлаждается до температуры не менее 20 °C и выдается в сепаратор 3, где происходит отделение метанола-сырца от непрореагировавшего газа.
Отделившийся в сепараторе 3 метанол-сырец поступает в сборник метанола-сырца7, а затемв расширительный сосуд9 идалее насклад.
После циркуляционного компрессора газ поступает в межтрубное пространство теплообменника 4 (рис. 7), где нагревается до температуры не менее 120 °C, затем циркуляционный газ подается в межтрубное пространство теплообменника 3, где нагревается до температуры 200–255 °C. Нагрев его осуществляется за счет теплообмена с газами, выходящими из реактора синтеза метанола 1.
Регулирование температуры по полкам колонны синтеза достигается подачей холодного байпасного циркуляционного газа через тороидальные распределители в смесители, где происходит смешение с горячим газом, вышедшим из слоя катализатора. После смесителей газ направляется на следующий слой катализатора.
Полученный на стадии выделения метанол-сырец направляется в отделение ректификации для выделения примесей и получения метанола-ректификата.
Метанол-сырец содержит метиловый спирт, воду и органические примеси: сложные эфиры простых жирных кислот, различные кетоны, этанол, высшие спирты, а также небольшое количество растворенных газов.
На стадии отгонки легких фракций от метанола-сырца отделяются легколетучие соединения – диметиловый эфир и растворенные
газы CO, CO2, H2, CH4, N2.
Метанол-сырец из склада метанола насосами подается в колонну отгонки легких фракций.
В линию метанола-сырца перед подачей в колонну дозируется 1–3%-ный раствор NaOH для нейтрализации избыточной кислотности, что предотвращает коррозию оборудования и трубопроводов установки ректификации.
27
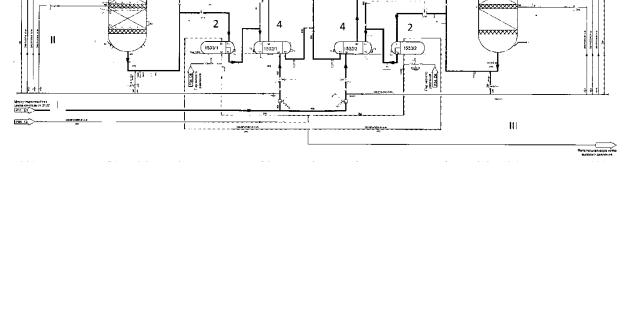
28
Рис. 7. Синтез метанола: 1 – колонна синтеза метанола; 2 – подогреватель питательной воды; 3 – промежуточный теплообменник цикла синтеза № 2; 4 – промежуточный теплообменник цикла синтеза № 1; I, IV – циркуляционный
газ цикла синтеза метанола; II – байпасный газ; III – питательная вода
28
Пары, выходящие с верха колонны, конденсируются в двух последовательно установленных конденсаторах. Основное количество метанола конденсируется в конденсаторе с воздушным охлаждением, оставшаяся часть несконденсировавшихся паров конденсируется в конденсаторе с водяным охлаждением.
Отборлегкихфракцийпроизводитсяпослеводяногоконденсатора. Флегма из конденсаторов поступает в сборник и затем насосами подается в колонну отгонки легких фракций. Из куба колонны отгонки легких фракций метанол насосами подается в колонны ос-
новной ректификации (рис. 8).
Пары из верха колонны 1 направляются в испарители 2, где конденсируются. Давление в верхней части колонны поддерживается посредством изменения положения жалюзи конденсаторов, а также количеством включенных вентиляторов.
Предусмотрено автоматическое регулирование содержания инертов по разности температур газа в верху колонны и при выходе из конденсатора. Инерты из системы удаляются через клапан, установленный на линии сброса инертов из сборника флегмы 4 на вспомогательные горелки трубчатой печи.
Сконденсированный метанол поступает в сборник флегмы 4. Уровень в сборнике 4 поддерживается постоянным отводом флегмы насосами5 на83-ю тарелку колонныосновнойректификации1.
Метанол-ректификат отбирается с тарелок 81, 79 и охлаждается в холодильнике 3 до температуры 35–40 °C. Отбор метаноларектификата производится автоматическим клапаном в соответствии с расходом метанола-сырца в колонну и с коррекцией по температуре на контрольной тарелке 10.
Через боковой штуцер нижней части колонны с одной из тарелок 6, 8, 10, 12, 14, 16, 18 (рекомендуется тарелка 10) отбирается сивушное масло (фракция метанол-масло-вода). Отбор фракции метанол-масло- вода производится через клапан пропорционально нагрузке колонны. Фракцияметанол-масло-вода подаетсяв резервуар на складе метанола. Для испарения кубовой жидкости и создания парового потока в колонне в качестве основного тепла (75 % от общего тепла) используется физическое тепло конвертированного газа при его охлаждении с 290 до 140 °C в испарителе 3 (см. рис. 5) и тепло конденсации водяных паров при температуре 155 °C в испарителе 2 (см. рис. 8).
29
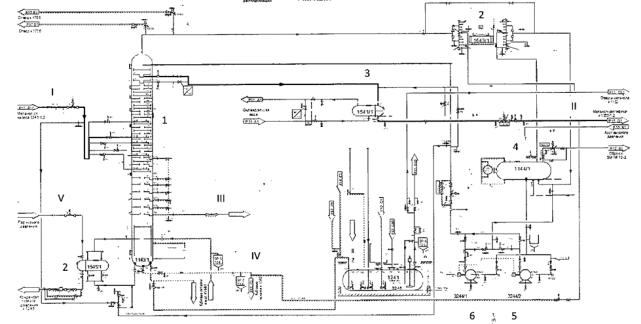
30
Рис. 8. Ректификация метанола-сырца (основная): 1 – колонна основной ректификации; 2 – паровой испаритель; 3 – холодильник метанола-ректификата; 4 – сборник флегмы; 5 – насос флегмы; 6 – насос дренажного резервуара; I – метанол-сырец; II – метанол-ректификат; III – сивушное масло; IV – кубовый остаток; V – пар низкого давления
30