
книги / Основные новые разработки в технологии метанола
..pdfГаз, поступающий в верхнюю часть реактора 3, проходя через его адиабатический слой, нагревается за счет тепла реакции синтеза метанола до температуры не более 270 °C и далее проходит через изотермическую часть реактора. Ограничение повышения температуры в изотермическом слое катализатора реактора достигается за счет испарения котловой воды с получением пара среднего давления во встроенном пластинчатом теплообменнике. Давление по высоте реактора контролируется по высокому давлению (8,0 МПа). Температура в реакторе контролируется с помощью многозонных термопар с сигнализацией минимальных(200 °C) имаксимальных(280 °C) значенийтемпературы.
Газ, выходящий из реактора, поступает в трубное пространство рекуперационного теплообменника 5, где охлаждается до темпера-
туры 160–178 °C.
Затем отходящий синтез-газ поступает в трубное пространство подогревателя питательной воды 4. Температура газа 130 °C на выходе из подогревателя питательной воды поддерживается регулятором путем переброса части питательной воды по байпасу теплообменника. Давление после теплообменника замеряется по месту манометром и контролируется индикатором на центральном пункте управления (ЦПУ) с сигнализацией максимального значения 8,0 МПа.
Далее газ охлаждается до 105–119 °C в подогревателе продувочных газов 7. Продувочные газы, поступающие в межтрубное пространство подогревателя 7 от сепаратора 8, нагреваются до 95–106 °C и далее направляются на сжигание в основных горелках печей риформинга. Температура продувочных газов на входе в подогреватель (не более 65 °C) замеряется по месту термометром.
После теплообменника 7 газожидкостная смесь поступает на дальнейшее охлаждение в аппарат воздушного охлаждения (АВО) 6, где ее температура снижается до 45 °C, при этом происходит конденсация метанола-сырца. Регулирование температуры газожидкостной смеси после АВО осуществляется включением/выключением вентиляторовили степенью открытия жалюзипо месту.
Отделение метанола-сырца от несконденсировавшихся газов происходит в сепараторе 8. Давление в сепараторе 8 замеряется по месту манометром (3,0–8,0 МПа).
41
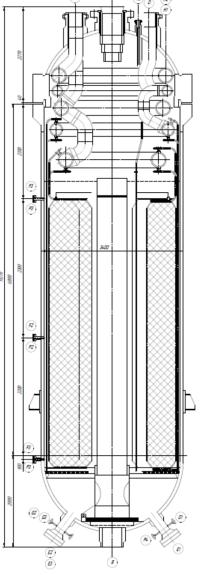
Рис. 10. Проточный реактор синтеза метанола
Циркуляционный газ из сепаратора 8 поступает на всас циркуляционного компрессора, смешиваясь с циркуляционным газом от сепаратора цикла синтеза и свежим (подпиточным) конвертированным газом. Отделившийся в сепараторе 8 мета- нол-сырец очищается от механических примесей на фильтрах (одинрабочий, одинрезервный).
Метанол-сырец после фильтров объединяется с метаноломсырцом от сепаратора основного синтеза и поступает в сборник метанола. Слив с дренажей фильтров направляется в подземную емкость.
На рис. 10 представлен эскиз проточного реактора синтеза метанола. Это вертикальный аппаратдиаметром3400 ммивысотой
11275 мм.
Аппарат изолирован и заполнен катализатором. Внутри слоя катализатора расположен внутренний теплообменник с плоскими теплообменными каналами для съема тепла реакции синтеза метанола. Всего имеется 160 каналов, из них 80 каналов широких и 80 узких. Ширина первых составляет 1,14 м, вторых – 0,8 м, толщина каналов 10 мм.
42
Площадь поверхности теплообмена встроенного теплообменника 1770 м2. Внутри теплообменных пластин циркулирует кипящая питательная вода. Объем загруженного катализатора 39,5 м3. Катализатор образует два слоя. Верхний объемом 9,5 м3 работает в адиабатическом режиме, нижний объемом 30 м3 (изотермический) работает с отводом тепла в пластинчатом теплообменнике.
Рабочие условия в реакторе: давление 7,4 МПа; температура 270 °C; среда токсичная, взрывоопасная – циркуляционный газ (CO,
CO2, H2, CH4, N2, H2O, CH3OH).
Рабочие условия в теплообменнике: давление 3,8–4,3 МПа; температура 233–240 °C; среда – питательная вода и пар.
За счет использования исходного технологического газа оптимального состава и оптимизированного температурного режима в проточном реакторе вырабатывается 46 т/ч метанола. Интенсивность работы реактора составляет 1,16 т/(м3·ч) (при интенсивности работы основных колонн синтеза 0,57 т/(м3·ч) после реконструкции).
Одним из важнейших элементов второго этапа модернизации производства метанола была реконструкция колонн синтеза. Недостатком существующих колонн синтеза, который ограничивал мощность отделения синтеза и всего производства, было использование в колоннах малоэффективного способа отвода тепла путем подачи холодного байпасного газа между полками катализатора. Интенсивность работы колонн синтеза составляла 0,375 т/(м3·ч).
В 2015 г. внутренняя конструкция колонн синтеза была полностью модернизирована в соответствии с предложениями фирмы
Methanol Casale SA.
Конструкция конвертера синтеза компании Casale основывается на аксиально-радиальном распределении газа на полках катализатора, при этом в конвертере располагаются три полки с двумя промежуточными теплообменниками, что характерно для новых конвертеров. Данный конвертер показан на рис. 11.
К основным преимуществам конструкции конвертера компании Casale относится следующее:
1. Высочайшая степень конверсии за проход благодаря конструкциистремяполкамиидвумяпромежуточнымитеплообменниками.
43
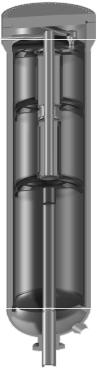
2.Легкая и стабильная эксплуатация благодаря простой и хорошо зарекомендовавшей себя конструкции внутренних устройств (как с точки зрения технологии, так и с точки зрения механики).
3.Гибкость эксплуатации при переходных условиях благодаря независимому управлению температурой навходена каждую полку.
4.Простая оптимизация, возможная благодаря очень равномерному распределению профиля температуры на входе на полку, что предотвращает неожиданное прекращение реакции.
5.Надежность, достигаемая за счет точного механического расчета внутренних устройств и надлежащего выбора материалов изготовления.
6.Легкая замена катализатора (загрузка / выгрузка) благодаря полному открытию верхней крышки и модуль-
|
ной конструкции внутренних уст- |
|
ройств. |
|
Большинство из вышеперечислен- |
|
ного уже хорошо известно. Здесь необ- |
|
ходимо подчеркнуть (применительно |
|
к пункту 4) то, что смесительное уст- |
|
ройство, установленное в конвертере |
|
для обеспечения равномерного распре- |
|
деления температуры на входе на полки |
|
катализатора, является результатом де- |
Рис. 11. Конвертер синтеза |
тального моделирования с помощью |
компании Casale |
программы расчета гидрогазодинами- |
|
ки. Уникальность данной разработки |
заключается в обеспечении практически идеального смешивания двух потоков, которые имеют существенные различия как с точки зрения расхода, так и с точки зрения температуры, что достигается при очень низком перепаде давления внутри данного устройства, поэтому это не влияет на общую потерю давления в конвертере.
44
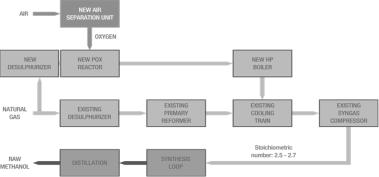
Для достижения конечной цели была спроектирована установ-
ка некаталитического парциального окисления углеводородов природного газа (установка POX).
Из практики известны два типа процесса неполного окисления углеводородов: каталитический и некаталитический. Оба процесса используются в производстве аммиака [7, 8]. Первый осуществляется на катализаторе при температуре 500 °C, второй – в отсутствие катализатора при температуре 1200–1400 °C.
В связи с тем что на ПАО «Метафракс» начались работы по
реализации строительства |
комплекса Аммиак-карбамид-меламин |
||||||||||||||||
(АКМ), в 2017 |
г. была запущена установка разделения воздуха |
||||||||||||||||
(ВРУ) и таким |
образом были подготовлены условия для пуска |
||||||||||||||||
в 2017 г. установки POX. |
|
|
|
|
|
|
|
|
|
|
|
|
|||||
|
|
Технологическая схема процесса показана на рис. 12. |
|
|
|||||||||||||
|
|
|
|
|
|
|
|
|
|
|
|
|
|
|
|
|
|
|
|
|
|
Установка |
|
|
|
|
|
|
|
|
|
|
|
|
|
|
|
Воздух |
|
|
|
|
|
|
|
|
|
|
|
|
|
||
|
|
|
разделения воздуха |
|
|
|
|
|
|
|
|
|
|
||||
|
|
|
|
|
|
|
|
|
|
|
|
|
|
||||
|
|
|
|
|
|
|
|
|
|
|
|
|
|
|
|
|
|
|
|
|
|
|
|
|
|
|
|
|
|
|
|
|
|
|
|
|
|
Десульфиризатор |
Реактор РОХ |
|
|
|
|
|
Бойлер |
|
|
|
|
|
|||
|
|
|
|
|
|
|
|
|
|
|
|
|
|
|
|
||
|
|
|
|
|
|
|
|
|
|
|
|
|
|
|
|||
|
|
Десульфири- |
|
|
Первичный |
|
|
Система |
|
|
|
Компрессор |
|
||||
|
Природный |
|
|
|
|
|
|
|
|
|
|||||||
|
газ |
|
затор |
|
|
риформинг |
|
|
охлаждения |
|
|
|
синтез-газа |
|
|||
|
|
|
|
|
|
|
|
|
|
|
|
|
|
|
|
|
|
|
|
|
|
|
|
|
|
|
|
|
|
|
|
|
|
||
|
|
|
|
|
|
|
|
|
|
|
|
|
|
|
|
|
|
|
|
Дистилляция |
|
|
|
Контур |
|
|
|
|
|
|
|
|
|
||
|
Метанол- |
|
|
|
|
|
|
|
|
|
|
|
|
|
|||
|
|
|
|
|
|
|
|
|
|
|
|
|
|
||||
|
сырец |
|
|
|
|
|
синтеза |
|
|
|
|
|
|
|
|
|
|
|
|
|
|
|
|
|
|
|
|
|
|
|
|
|
|
|
|
Рис. 12. Принципиальная технологическая схема РОХ
Из верхнего по течению главного клапана установки поток природного газа направляется в новую линию POX. После впрыска некоторого количества рециркулируемого водорода этот газ предварительно нагревается в новом теплообменнике для подачи сточных вод перед прохождением через новый специальный десульфиризатор. На выходе из нового десульфиризатора природный газ смешивается с паром высокого давления (соотношение S/C около 0,2 моль), а затем направляется в реактор POX.
45
Другой источник питания для реактора POX – кислород. Для его получения работает воздухоразделительная установка.
Перед входом в реактор POX поток кислорода смешивается с небольшим потоком пара для безопасности и предварительно нагревается до 200 °C (с помощью пара) в специальном кислородном нагревателе.
Вреакторе POX происходит частичное окисление природного газа без какого-либо катализатора, в результате чего образуется синтез-газ с очень низким содержанием метана.
На выходе из реактора POX синтез-газ очень горячий (около 1320 °C), поэтому он охлаждается в паровом котле. Газ, выходящий из котла, направляется в теплообменник подачи-отвода, где он используется для предварительного нагрева десульфиризатора. Затем технологический газ впрыскивается в существующую линию риформинга непосредственно перед технологическими ребойлерами колонн очистки продукта и в конечном счете идет на всасывание компрессора синтез-газа.
Результирующее стехиометрическое число подпиточного газа
вконтуре синтеза составляет 2,77 (при типичном чистом паровом риформинге примерно 3,0).
Взаключение рассмотрим, какую роль в модернизации производства метанола с доведением мощности до 1,2 млн т сыграла оптимизация состава синтез-газа.
Тот факт, что на эффективность синтеза метанола большое влияние оказывает состав исходного газа, в частности соотношение
H2/CO или так называемый функционал (H2–CO2)/(CO+CO2), очевиден как из теоретических соображений, так и из результатов последних исследований [4, 9].
Авторы работы [4] по результатам модернизации производства метанола на предприятии ПАО «Метафракс» приводят следующие данные о значениях функционала в реальном производстве: для исходного газа, поступающего в колонны основного синтеза, – 12,86; для газа, поступающего в реактор проточного синтеза, – 5,93; для газа из трубчатых печей конверсии – 2,88; для конвертированного газа после реактора POX – 1,69. Очевидно, что положительные ре-
46
зультаты, достигнутые при модернизации производства метанола, получены, в первую очередь, за счет снижения значения функционала и приближения его к оптимальной величине.
Оптимизация функционала в процессе синтеза метанола позволяет увеличить скорость процесса и положительно влияет на равновесие процессов, происходящих при синтезе. В литературе [10, 11] достаточно убедительно показано, что процесс синтеза метанола на цинк-медных катализаторах осуществляется по двум химическим реакциям:
СО2 + 3Н2 → СН3ОН + Н2О; СО + Н2О = СО2 + Н2.
Таким образом, в реальных условиях преобладает механизм непрямого синтеза метанола. Выведенное для этого механизма кинетическое уравнение показывает, что на скорость процесса положительно влияет увеличение концентраций оксидов углерода и отрицательно – увеличение концентрации водорода.
В работе [9] проведен анализ влияния состава газовой смеси на равновесный выход метанола и показано, что наибольший выход метанола может быть достигнут при значениях функционала, приближающихся к 2–2,3.
Опыт ОАО «Тольяттиазот» показывает, что эффективность процесса синтеза метанола может быть существенно повышена при подаче в цикл синтеза диоксида углерода. Это технологическое решение, по-видимому, также связано с оптимизацией значения функционала.
Однако количественную оценку оптимального значения функционала в настоящее время вычислить не представляется возможным вследствие невозможности учесть влияние кинетических и равновесных факторов на процесс синтеза, учитывая селективность катализаторов.
47
4. МЕГАМЕТАНОЛ – СОВРЕМЕННАЯ ТЕХНОЛОГИЯ МЕТАНОЛА
Одной из важнейших тенденций развития производств метанола является увеличение единичной мощности агрегатов. К 90-м гг. прошлого столетия агрегаты синтеза метанола достигли мощности
в500–750 тыс. т.
Всвязи с ростом потребности в метаноле и расширением сфер его применения в мире возникла задача разработки и строительства мегаустановок по производству метанола. За период с 1990 по 2006 г. на Ближнем Востоке и в Латинской Америке было построено несколько метанольныхустановокпроизводительностьюдо5000 т/сутки.
Основными разработчиками и поставщиками мегатехнологии метанола являются фирмы Johnson Matthey Catalysts, Davy Process Technology, Lurgi, Haldor Topsоe.
Как показал практический опыт эксплуатации метанольных установок повышенной мощности и, в частности, опыт модернизации М-750 на предприятии ПАО «Метафракс», основные проблемы, которые приходится решать при разработке мегаустановок, связаны с увеличением мощности секции получения синтез-газа и блока синтеза метанола.
Один из методов повышения производительности установки
парового риформинга без увеличения ее размеров заключается в использовании установки предриформинга.
Фирмой Haldor Topsоe разработана схема получения синтезгаза с применением предриформинга и автотермического риформинга (АТР), позволяющая исключить паровой риформинг. При этом увеличивается мощность отделения получения синтез-газа и оптимизируется величина функционала, что способствует интенсификации процесса синтеза метанола.
Фирма Lurgi в технологии мегаметанола использовала на стадии получения синтез-газа сочетание последовательно расположенных установокпарового риформинга иАТР сприменением кислорода.
Модернизация реакторного блока также позволяет существенно увеличить производительность завода.
48
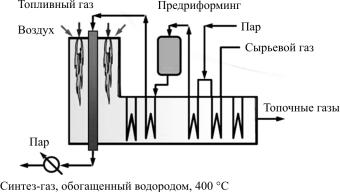
Компании Davy Process Technology и Johnson Matthey Catalysts
являются ведущими поставщиками технологий производства метанола, которые включают использование современных систем производства синтез-газа и реакторов синтеза.
В рекламном проспекте [12] и докладе [13] дано описание некоторых особенностей таких систем.
На стадии получения синтез-газа фирмой Davy Process Technology предлагаются: паровой риформинг (SMR), предриформинг, компактный риформинг (CR), автотермический риформинг (ATR), риформинг с газовым обогревом (GHR+ATR), комбинированный риформинг (SMR+ATR).
Описание некоторыхсхем получениясинтез-газа приведено ниже. На рис. 13 изображена блок-схема технологии получения син-
тез-газа из природного газа с добавлением предриформинга.
Рис. 13. Паровой риформинг с предриформингом
К основным достоинствам такой схемы относятся:
–простота конструкции (аппарат с неподвижным слоем катализатора);
–удаление тяжелых углеводородов перед входом в установку парового риформинга;
–обеспечение ~10 %-ной степени превращения в процессе риформинга природного газа;
49
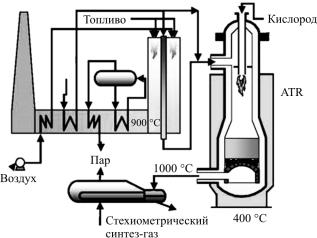
– снижение размеров установки парового риформинга за счет возможности поддержания более высоких температур на входе
иболее полной рекуперации тепла в конвективной секции;
–снижение потребления топливного газа.
Основными достоинствами комбинированного риформинга (рис. 14) являются: наименьшее потребление кислорода, исключение стадии производства пара, надежность, простота конструкции, пуска, эксплуатации, большая производительность однопоточной схемы (10 000 т/сутки), низкое потребление воды, наименьшее воздействие на окружающую среду, высокая эффективность процесса, сниженные капитальные затраты при более высокой производительности, возможность реконструкции.
Рис. 14. Получение синтез-газа комбинированным риформингом (SMR+ATR)
Одной из последних разработок компании Davy Process Technology в области производства синтез-газа является технология риформинга с газовым обогревом (GHR+ATR) (рис. 15).
Достоинством риформинга с газовым обогревом считается минимизация тепловой инертности установки.
В области разработки новых конструкций реакторов синтеза метанола предлагается следующее [13].
50