
книги / Переработка нефти и газа
..pdfGasoline stabilization dry hydrocarbon gas. It is that part of light hydrocarbons
С1–С3, which is still dissolved in gasoline. Yield is fairly low (0.1–0.2 mass %). It can be processed in gas frationation unit (under pressures up to 1.0 MPa). However, since its amount is small, it is sent to gas line and used asfuel gas in pipe still.
Top cut of gasoline stabilization (liquefied). It consists mainly of C3 and C4, with C5. Yield is 0.2–0.3 mass %. It is used as component of liquefied household gas or gas motor fuel.
Light top cut of gasoline. Initial boiling point of the cut is 85°C. Oil yield is 4–6 mass %. Its octane number, depending on the chemical composition, does not exceed 70 (more frequently, 60–65) as determined by motor method test (MMT). It is used for producing oil solvents or sent for catalytic isomerization to have its octane number increased to 82–85 and added to commercial motor gasoline.
Gasoline cut, 85–180 °C. Oil yield depends on the cut composition and it can range from 10 to 14 mass %. The octane number is low (45–55, by MMT). Therefore, this cut is sent for catalytic reforming to have its octane number raised to 88–92 (by MMT) by converting n-alkanes and naphthenes into aromatic hydrocarbons. Reforming catalyzate is used as basic component of motor gasoline.
Kerosene cut can be stripped by the following two processes. The first process is stripping of aviation kerosene (cut of 140–230 °C). The yield is 10–12 mass %. After hydrotreating and adding necessary additives it is used as commercial jet fuel. The second process is production of winter-time or arctic diesel fuels (cut of 140–280 °C or 140–300 °C). The yield is 14–18 %. It is used as component of winter-time or arctic diesel fuels after hydrotreating and dewaxing (as required, if it does not satisfy the requirements for sulfur and temperatures of cloud point and chilling point).
Diesel cut. Yield is 22–26 %, if aviation kerosene has been stripped earlier, and 10–12 mass %, if component of winter-time or arctic diesel fuels has been stripped. It is used as component of winter-time and summer-time diesel fuels. If nece, it is subject to hydrotreating and dewaxing.
Light gasoil cut. Yield is 0.5–1.0 mass %. Boiling range is 100–250 °C. It is product of fuel oil destruction, when it is heated in the pipe still before injection into vacuum tower. It contains both saturated and unsaturated alkanes. It is used as component of diesel fuels (after hydrotreating) or light fuel oil.
Light vacuum gasoil. Cut of 240–380 °C. Oil yield is 3–5 mass %. Side cut of vacuum tower. It is used as component of summer-time diesel fuels.
Vacuum gasoil. Basic distillate of vacuum distillation of fuel oil in fuel segment. Boiling range is 350–500 °C (350–550 °C). Oil yield is 21–25 mass % (26–30 mass %).
21
It is used as raw product for catalytic cracking or hydrocracking to produce highoctane gasoline, aviation kerosene, high-viscosity oils, and other products. If oil makes it possible to produce high-index base oils, then oil distillates are removed as side cuts, e.g.: 350–420 °C (oil yield 10–14 mass %) and 420–500 °C (oil yield 12–16 mass %). Oil cuts are sent for solvent refining from asphaltic and resinous substances and for dewaxing, to produce base distillates of (medium-viscosity and viscous) oils.
Tar. Residue of fuel oil vacuum distillation. It is boiled off at temperature over 500 or 550 °C. Oil yield is from 10 to 20 mass % depending on the content of asphaltic and resinous substances and heavy hydrocarbons. Tar is used:
–as acomponent of heavy boiler fuels;
–as residual bitumen or raw product for producing air-blown and compounded bitumen;
–as raw product for the coking; and
–as raw product for producing base residual oil.
7. STRAIGHT OIL DISTILLATION UNIT
Straight oil distilleries are termed called pipe stills. Depending on applied pressure they can be atmospheric or vacuum (AT or VT) or combined (AVT). Combination with electric desalting unit (ELOU) is termed ELOU-AVT (electric desalting unit – atmospheric-vacuum pipe still).
The process flow of desalting unit – atmospheric-vacuum pipe still (ELOU-AVT ) is shown in fig. 5. The unit includes 4 modules: ELOU, AT, VT, and modules for stabilization and rerun distillation of gasoline(to produce narrow gasoline cuts: raw products for reforming and isomerization).
Capacities of the existing atmospheric-vacuum pipe stills range from 0.5 to 10 million ton per year. Intensive construction of electric desalting unit – atmospheric-vacuum pipe still (ELOU-AVT) have started since 1960s. Their capacity is 3.6 and 8 million ton per year. The biggest vacuum pipe still (AVT) with annual capacity 11 million tons was put into operation in Antwerp (Belgium). At the same time, two units with annual capacity 10.5 million tons were built in USA. Later, units with annual capacity 6–8 million tons were built.
22
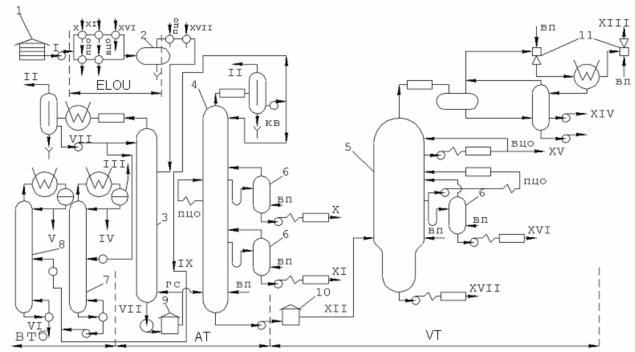
Fig. 5. Basic process flow diagram of electric desalting unit – atmospheric-vacuum pipe still (ELOU-AVT): 1 – oil tank, 2 – electric dehydrators, 3, 4, and 5 – gasoline extraction, atmospheric, and vacuum tower, 6 – stripping, 7 and 8 – stabilization and rerun distillation tower, 9 and 10 – atmospheric and vacuum pipe stills; 11 – double-stage steam ejection pumps;
I – oil, II and III – low pressure and high pressure hydrocarbon gas, IV – liquefied gas, V – gasoline top cut (C3 – 85 °C), VI – gasoline cut (85–180 °C), VII – unstable benzene, VIII – topped oil, IX – heavy component of gasoline (100–180 °C), X – kerosene (140–240 °C), XI – diesel fuel (200–350 °C), XII – fuel oil, XIII – mixture of non-condensable gases, XIV – light gasoil cut (up to 300°C), XV – light vacuum gasoil (280–360 °C), XVI – (350–500 °C), XVII – tar (over 500 °C), ВПand КВ– water steam and its condensate, ГП– hot steam, ВЦОand ПЦО– top and intermediate circulation reflux.
At modern refinery, AVT units are the head units of the entire oil processing chain, and total capacity of the refinery depends on them.
The total number of distillates extracted from oil in AVT units ranges from 7 to 10.
8. COMBINED ATMOSPHERIC-VACUUM PIPE STILLS (AVT)
WITH SECONDARY PROCESSES
Process efficiency can be improved by three ways:
–process upgrading (process flow, or application of new catalysts and agents);
–increasing feedstock unit capacity; and
–combining interrelated processes.
23
Let us consider the third way in more detail. The advantages of the second way, i.e. increasing labor productivity and reducing specific costs (water supply, electric power, etc.) have disadvantages: the process becomes less flexible, and big processing units have lower output parameters if there are troubles with oil delivery.
At the same time, combining processes has become an important way to improve the processing unit performance, especially for solving the problem of deepening oil processing.
Combining oil production processes is usually understood as combination of several technologies on one site, when products of one production chain are raw materials for another without intermediate tank farms. In its turn, it gives many advantages. The main of them are:
–reducing number of tank farms for intermediate products;
–eliminating intermediate product pumping, and, consequently, reducing number of pumps, pipelines, and lowering power consumption;
–reducing processing unit areas;
–saving heat power due to better arrangement of heat recovery(re-laying of flows, eliminating necessity to cool products before tank farm, or to heat them before the next process);
–more rational layout of equipment of the same type; and
–reducing number of service personnel and growing labor productivity.
The first combined units were atmospheric-vacuum pipe stills: combination of atmospheric pipe still (AT) and vacuum pipe still (VT) modules. Later on, atmospheric-vacuum pipe still combining was as follows:
1)gasoline stabilization module was added to atmospheric-vacuum pipe still unit, in which heat of hot flows is used to produce liquefied hydrocarbon gas and stable gasoline;
2)In 1960s, the modules for secondary distillation (rerun distillation) of gasoline and electric desalting units (ELOU) were added to the processing units.
Since 1970s, a new stage in combining straight distillation processes has started. Nowadays, it is developed in two trends:
– straight oil distillation with distillate upgrading;
– deep refining of fuel oil into motor fuels.
24
The combined unit for non-deep (low-level) oil processing LK-6u, which is most widely used in Russia, combines 6 processes: AT, gasoline rerun distillation, gasoline cut reforming (cut of 85–180 °C), hydrodearomatization of kerosene, hydrotreating of diesel fuel and gas fractionation of saturated hydrocarbon gas mixture to produce dry gas and concentrate of hydrocarbons С3, С4 and С5.
In combination with deep processing of fuel oil, the units may include modules for catalytic cracking, visbreaking, hydrotreating, vacuum gasoil, coking (optional process) and hydrovisbreaking.
Considering the advantages of processes combining, we may state that further development of oil processing is impossible without combining various processes.
25
Course of lectures on
OIL REFINING AND OIL CUT TREATING
COMMERCIAL OIL PRODUCTION
Lecture 1
OIL REFINING PROCESSES
Product of primary and destructive process is a complex mixture of hydrocarbons and non-hydrocarbon compounds. Some of such non-hydrocarbon compounds can affect the properties of commercial oil products, and must be removed. Such processes are one of the final stages of commercial oil production.
Some refining processes are based on interaction of undesirable impurities with chemical reagents (alkali treatment, sulfuric acid treatment, hydrotreating and other). The essence of other processes is oil cut fractionation without changing the structure of hydrocarbons (deasphaltizing, preferential solvent treatment, dewaxing and adsorption refining).
The most undesirable impurities that greatly affect the properties of fuels are sulfur compounds. So, it is necessary to remove sulfur compounds from fuel.
Oil distillates and residues produced by vacuum distillation contain paraffin hydrocarbons, cyclic hydrocarbons, aromatic hydrocarbons, naphtheno-aromatic hydrocarbons with paraffin chains, asphaltic resinous substances, sulfur, oxygen and nitrogen-containing organic substances.
To reduce setting (pour) point, paraffin and cyclic hydrocarbons with long lateral chains are removed by dewaxing processes.
Resinous-asphaltenic materials are mainly contained in high-boiling fractions. They are undesirable and must be removed by deasphaltizing processes.
Sulfur-containing compounds accumulated in tars are removed by hydrotreating, selective and adsorption refining.
Oxygen-containing compounds – naphthenic acids and phenols – are removed by alkali treating and solvent refining.
26
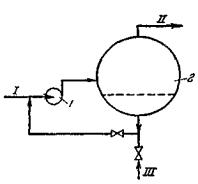
CHEMICAL TREATMENT
Alkali Refining
Alkali refining is used for removing oxygen-containing compounds (naphthenic acids and phenols) and some sulfur-containing compounds (hydrogen sulfide and mercaptan), as well as for removing sulfuric acid and products produced by interaction between sulfuric acid and hydrocarbons (sulpho-acids and sulfuric acid esters).
A part of sulfur compounds contained in light oil products can react with alkalis. Hydrogen sulfide can react with alkalis and form, under excess of alkali, sodium sulfide, and, under alkali stress, sodium hydrosulfite. Mercaptans, naphthenic acids and phenols can react and form salts.
Thus, H2S, partially mercaptans, naphthenic acids and phenols can be removed by treating oil with NaOH solution.
Alkali Refining of Light Oils
The unit (fig. 1) is comprised of agitator and settling tank. Centrifugal pump 1 is used as agitator. Before treating, distillate and alkali are mixed in the agitator and the mixture is pumped to the settling tank 2. The treated oil flows at the top of the settling tank and settled alkali solution is discharged from the bottom of the settling tanks and recycled to the agitator 1.
Fig. 1. Light Oil Product Alkali Treatment Unit: 1 – pump; 2 – settling tank. Process lines: I – untreated product; II – treated product; III – alkali solution
Oil Distillate Alkali Refining
Oil distillate is treated with alkali solution under pressure (fig. 2). Oil is pumped by the pump 10 to the shell side of the heat exchanger 2, and heated with treated oil supplied from the settling tank 7 to 40 – 50 ºС.
27
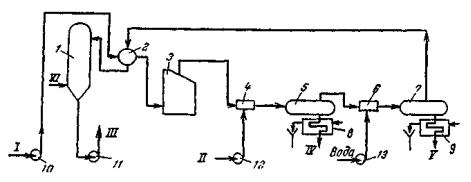
Fig. 2. Alkali Refining. Basic Process Flow Diagram:
1 – tower; 2 – heat exchanger; 3 – pipe still; 4, 6 – agitators; 5, 7 – settling tanks; 8, 9 – coolers; 10, 11 – pumps. Process lines: I – untreated oil; II – alkali solution;
III – treated oil; IV – waste alkali; V – washing water; VI – air
From the heat exchanger distillate comes to the pipe still 3 under pressure 0.6–1 MPaG, and heated to 150–170 ºС. Then, it is directed to the agitator 4, to which 2.5 % alkali solution is pumped by the pump 12. Oil and alkali mixture comes into the settling tank 5, where alkali waste is settled from oil. Wastes are discharged from the bottom of the settling tank, cooled in the submerged cooler 8, and directed to the receivers for naphthenic acid removal.
Treated oil is directed from the top of the settling tank 5 to the agitator 6 for washing, to which water at temperature 60–65 ºС is pumped by the pump 13. From the agitator the oil and water mixture comes to the settling tank 7. From the bottom, washing water is cooled in the submerged cooler 9 to 70–80 ºС and directed to the receivers for naphthenic acid removal. After alkalization and washing at 90–100 ºС oil is directed from the top of the settling tank 7 to the shell side of the heat exchanger 2, cooled to 70–80 ºС, and comes to the drying tower 1 for compressed air drying. Then, treated oil is removed from the unit by the pump 11.
Oil Alkali Refining in Electric Field
Alkali treatment of oil products in electric field is a continuous, easily automated process. It is based on applying electric settling tank operated by combining chemical oil product treatment with subsequent particle enlargement in electric field. Efficiency of electric refining depends on temperature, pressure, hydraulic conditions of agitating and precipitation, and electric field intensity.
28
Temperature. The higher the molecular weight and melting temperature of product to be treated, the higher temperature shall be. Most often, refining temperature is 30–45 оС.
Pressure. Pressure should be sufficient for keeping the product to be treated in liquid state. Usually, it is ranged within 0.2–2 MPa. The first magnitude relates to heavy oil products, and the second – to light oil products, including gases.
Hydraulic conditions of agitating and precipitation. They depend on oil product properties, natural emulsifier content, surface tension of phases and reagent flow rate. Electric field intensity. It depends on voltage applied to the electrodes, the distance between the electrodes and their form. Usually, the distance between the electrodes is ranged within 0.8–0.12 meter, and electrode supplied voltage is 10–15 kV.
Oil Distillate Alkali Refining with Catalysts
With increasing the share of sour oil in refining, it became impossible to produce high-quality fuels without removing active sulfur compounds (mercaptans). Sour sulfur causes equipment corrosion and catalyst fouling. It accumulates in liquefied gas and gasoline. In addition to hydrotreating, Bender and Merox processes have received wide recognition. Under Bender process, all mercaptan is converted into less active sulfides on fixed-bed PbS catalyst in circulating alkali solution. Merox process is used for liquefied gas and gasoline demercaptanization. Cobalt phthalocyanide is used as catalyst in alkali solution. Merox process has three stages:
RSH + NaOH= RSNa + H2O
2 RSNa + ½ O2 + H2О = RSSR + 2/NaOH 2 RSH + ½ O2 = RSSR + H2O
Sulfuric Acid Treating
Sulfuric acid treating is used for removing unsaturated and heterorganic hydrocarbons, asphaltic resinous substances and polycyclic aromatic hydrocarbons from oils (oil cuts and paraffin). They affect the properties of oils (storage property, color and other). Under sulfuric acid treating, unsaturated hydrocarbons are sulfurized to form acid esters and mid esters. Aromatic hydrocarbons are sulfurized to form sulpho-acids and sulfones. Resinous-asphaltenic substances interact with sulfuric acid to form asphaltene and sulpho-acids. Naphthenic acids are partially dissolved in sulfuric acid and partially
29
sulfurized. Sulfuric acid, as reagent, is used for transformer oil production, used oil recovery, paraffin treatment for food industry, white oil and albuminous substance production. Treating efficiency depends on temperature, contact time, sulfuric acid consumption rate and concentration, and sulfuric acid loading procedure.
Temperature. Depending on oil viscosity, the temperature of sulfuric acid treating process should be maintained at the range from 30 up to 80оС.
Acid concentration. Usually, 92–96 % acid is used. For producing colorless oils (medicinal and perfume oils) fuming sulfuric acid is used.
Acid consumption. The higher the acid consumption, the higher quality of undesirable component removal. For transformer oil refining, it is necessary to provide 6–15 % of acid. Consumption of fuming sulfuric acid for producing colorless oils should be 50–60 %.
Acid treating procedure. To enhance efficiency of treating, it is necessary to remove reaction products and batch acid.
Contact time. Usually, duration of air agitation ranges from 30 up to 70 minutes, depending on agitator capacity and distillate properties.
Lecture 2
PHYSICAL TREATMENT
Physical fractionation is mainly used for oil cut treating. The essence of physical fractionation is separation of oil cut by components without changing chemical structure.
Extraction based on different solubility of oil components in solvent is the most widely used technique from among all mass exchange fractionation processes of multi-component mixtures.
It is aimed at removing low-index coke-forming components, such as resinousasphaltenic substances, polycyclic aromatic hydrocarbons and high-melting paraffin hydrocarbons which affect low-temperature properties of commercial oils. There are three types of extraction processes: oil tar deasphaltizing, solvent refining and dewaxing.
The most important extraction process parameters are extraction temperature and ratio of solvent to oil which depend on critical solution temperature.
30