
книги / Переработка нефти и газа
..pdfCourse of lectures on
GAS PROCESSING
Lecture 1
PROCESSING OF HYDROCARBON GASES
1. Fractionation of Gases
Secondary gases are resulted from oil thermochemical refining processes. Saturated hydrocarbon gas is obtained by means of the following production processes:
•oil preliminary distillation;
•gasoline catalytic reforming;
•isomerization of light gasoline (pentane-hexane) cut;
•hydrotreating of light distillates and vacuum gasoil;
•hydroisomerization of kerosene cut;
•hydrodearomatization of jet fuels;
•hydrotreating of oils.
All the above processes generate gas containing hydrocarbons from methane to pentane with a small admixture of hexane. The gas is gathered and directed to gasfractionation unit.
Gas-fractionation unit normally divides the incoming gas into the following cuts:
•dry gas (С1-С2);
•propane cut (purity degree of 90–94 % in terms of propane);
•butane cut representing the sum of n-butane and iso-butane (purity degree of 92–96 % in terms of this sum);
•residual pentane-hexane cut (С5) containing n-pentane and n-hexane with isomers.
Gas-fractionation plant is shown in fig. 1.
Primary material from catalytic reforming unit (I) and primary material from other units of a refinery (isomerization units, kerosene, diesel fuel and vacuum gasoil hydrotreating units; kerosene hydroisomerization and diesel cut hydrodearomatization units) (II) enters skim pile E-1. Boil-off gas from the skim pile is cooled down in cooler X-1 and enters tank E-2, from which the both products are directed to various levels of absorption tower. Then, usual fractionation takes place to obtain cuts С1-С2, С3, С4 and С5+.
81
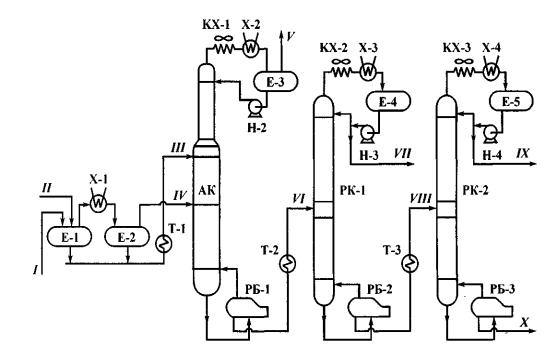
Dry gas is normally used by the plant as a process fuel and sometimes is directed to hydrogen-generation unit.
Propane and butane cuts are used as monomers for petrochemical industry but most often serve as a component of a mixture used to obtain liquefied gas (propane-butane mixture) used as fuel of carburetor engine or as household gas.
Fig. 1. Gas Fractionation Unit Layout:
АК – absorption tower; РК-1 and РК-2 – propane and butane towers; Е – tanks; РБ– reboilers; Т– heat exchangers; КХ– condensing-coolers; X – coolers; Н– pumps; streams: I – cut С1-С5 from reforming unit; 11 – cut С1-С5 from other units; III – liquid primary material; IV – gaseous primary material; V – dry gas С1-С2; VI – cut С3-С5; VII – propane cut; VIII – cut С4-С5; IX— butane cut; X – cut С5+
Cut С5+ is used as a light component of lowand mid-octane gasolines and directed to isomerization to obtain high-octane light component of gasolines.
Hydrocarbon gas containing unsaturated components is obtained by means of the following production processes:
•catalytic cracking;
•thermal cracking;
•pyrolysis;
•coking;
Unsaturated gases are fractionated by means of a unit similar to that used to fractionate saturated gases. The unit is shown in fig. 2.
82
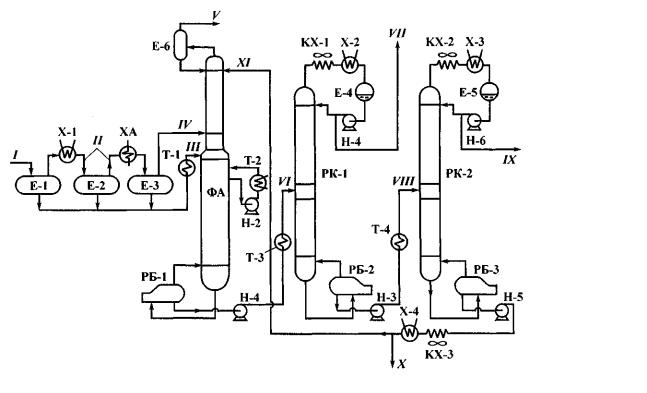
Fig. 2. Layout of Unsaturated Gas Fractionation Unit:
ФА – fractionation absorption tower; РК-1 and РК-2 – rectification towers; ХА – ammonia cooler; other symbols – see fig. 1;
streams: I – catalytic cracking gas; II – boil-off gases from tanks Е-1 and Е-2; III – liquid residue of gas; IV – gas phase; V – dry gas С1-С2; VI – deethanized stream; VII – propanepropylene cut; VIII – depropanazed stream; IX – butane-butylene cut; X – pentane-amylene cut; XI – absorbent from fractionation absorption tower
Gas obtained from catalytic cracking plant is directed to tanks E1 through E3, where vapor phases precipitate (II) primarily in water (X-1) and then in ammonia (XA) coolers. Warmed liquid phase (III) and cold vapor phase are directed to tower 1 i.e. fractionation absorption tower that separates dry gas С1-С2 due to feeding up an absorbent i.e. cut С5+.
Withdrawn from the top of tower РК-1 is propane-propylene cut (PPC) and from that of tower РК-2 – butane-butylene cut (BBC). Withdrawn from the bottom of tower РК-2 is heavy residue С5+ – pentane-amylene cut (PAC) that is partly fed as an absorbent to the top of tower ФА, while the rest of it is withdrawn as balance stream.
Recently, cut С5+ has been used as a primary material for petrochemical industry. Therefore, gas fractionation unit obtains three end products i.e. PPC, BBC and PAC. PPC is used to obtain polymer-gasoline, it is partly added to BBC to obtain alkyl gasoline or directed to pyrolysis.
BBC is the major primary material for alkylation (obtaining of alkyl gasoline), obtaining of methyl t-butyl ether (MTBE) and polyisobutylene (lubricant thickener).
83
PAC is a primary material for the alkylation of amylenes and obtaining of methyl t-amyl ether (MTAE).
According to the above information, all end cuts of GFU are used for obtaining motor fuels, but BBC is used wider.
BBC contains three unsaturated hydrocarbons:
butene-1 СН2 = СН — СН2 — СН3 butene-2 СН3 — СН — СН — СН3 iso-butylene СН2 = С (СН3) — СН3
Out of the above hydrocarbons, butene-1 and butene-2 are very reactive in alkylation process, whereas iso-butylene is less reactive. But iso-butylene displays high activity in reaction used to obtain MTBE, while butene-1 and butene-2 on the contrary never enter into such reaction. Therefore, these two processes are combined so that initially to use iso-butylene (to obtain MTBE) and then to alkylate more active primary materials containing only n-butenes.
2. Isomerization of Pentane-Hexane Cut
Used as primary material for isomerization process could be:
•cut С5+ from GFU (if not involved into gasoline);
•cut С5+ obtained from natural gas liquids (NGL);
•tops with initial boiling at 62 °Сfollowing re-distillation of gasoline (straight-run).
All these cuts are concentrates of n-alkanes С5 and С6. The higher the content of the sum of n-С5 and n-С6 in primary material, the more favorable the isomerization process.
Requirements for primary materials in terms of impurities:
sulfur – no more than 1 10–4 % (of weight) or 1 microgram per kilogram; nitrogen – no more than 0.5–10–4 % (of weight);
moisture – no more than 0.5–10–4 % (of weight).
Process catalysts are represented by bifunctional metal-deposited catalysts either platinum or palladium on aluminum oxide or zeolites.
Russia for the time being uses 3 brands of catalysts:
•IP-62 containing 0.5 % of platinum on aluminum oxide and fluorineactivated; operates at 380–450 °С;
•NIP-66 containing 0.6 % of platinum on aluminum oxide and chlorineactivated, operates at 150–180 °С, i.e. is a low-temperature catalyst;
84
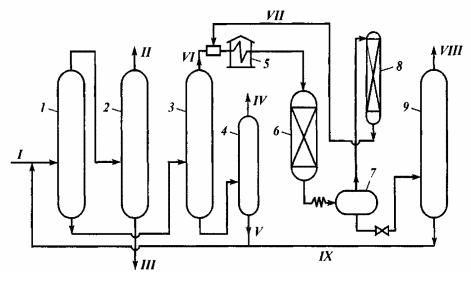
• ITsK-2 containing 0.8 % of palladium on zeolite SaU and chlorine-activated; operates at 250–320 °С.
Process flow chart is based on the separation of primary material into concentrates of n-pentane and n-hexane and the sum of the remaining hydrocarbons, and on the subsequent catalytic isomerization of n-alkanes. There are two primary material separation options such as distillation separation and adsorption separation on zeolites.
Process flow chart of a commercial unit having capacity of 150 thousand tons of primary material a year (in terms of n-pentane – 80–100 thousand tons a year) is shown in fig. 3.
Fig. 3. Layout of Pentane-Hexane Cut Isomerization Unit:
1–4 – gas-processing towers; 5 – furnace; 6 – reactor; 7 – separator; 8 – hydrogen-rich gas cleaning adsorber; 9 – stabilizer;
streams: I – pentane-hexane cut; II – n-butane; III – iso-pentane; IV – iso-hexanes; V – n-hexane; VI – n-pentane concentrate to reaction; VII – hydrogen-rich gas; VIII – gas and stabilization heads; IX – stable isomerization product
The unit can operate according to fractionation principle, when tower 4 is absent, hexanes will come out from the bottom of tower 3.
Operation mode of catalyst NIP-66:
•temperature of 150–180 °С (conversion of n-pentane 65 %), as the catalyst coking progresses, the temperature grows;
•pressure of 1.4–3.0 MPa depending on catalyst type (as for the basic reaction, the lower the pressure, the better, while partial pressure of hydrogen is required to suppress coke formation);
85
•usual hydrogen-rich gas circulation ratio is 900–1,000 nm3/m3;
•primary material space velocity is 1.2–2.0 hr–1, depending on catalyst type and process temperature;
•flow rate of 100 % hydrogen is 0.1–0.3 % of primary material.
The process yields stable isomerization product, stabilization heads and hydrocarbon gas.
Stable isomerization product yield accounts for 80–85 % and contains a sum of isomers, iso-С5 + iso-С6 accounting for 50–60 %. Its octane number is 85–87 %. The stable isomerization product is used as a light component of motor gasolines capable of enhancing their true vapor pressure and no affecting their octane number.
Stabilization heads yield accounts for 15–18 % and are used as a component of GFU primary material.
Hydrocarbon gas yield accounts for 2–3 % and is used as fuel gas.
There is a trend towards the combination of adsorption and isomerization processes. In late seventies, the USA was first to introduce a unit combining adsorption (Isosieve) and isomerization called Hizomer. Such units also operate in Japan, Germany and Sweden.
The combined (adsorption and izomerization) process flow sheet is shown in fig. 4. A distinctive feature of it consist in the fact that hydrogen-rich gas in this process serves as a common process stream both for isomerization and adsorption module (desorbent).
A mixture of hydrogen-rich gas with n-alkanes, once brought in the furnace to 300–350 °С, will pass through isomerization reactor, cools down in regenerative heat exchanger and enters adsorber 2, where zeolite swallows unreacted n-alkanes, while iso-compounds are condensed and leave for stabilization.
In adsorber 3 operating for the time being as a desorber, n-alkanes previously swallowed by zeolite are displaced with hydrogen-rich gas delivered by compressor 6 and heated up in heat-exchanger 8; and this mixture enters the furnace to be heated and then to the reactor.
The unit includes 3 or 5 adsorbers-desorbers operating in turn as the zeolite tank is filled with n-alkanes.
86
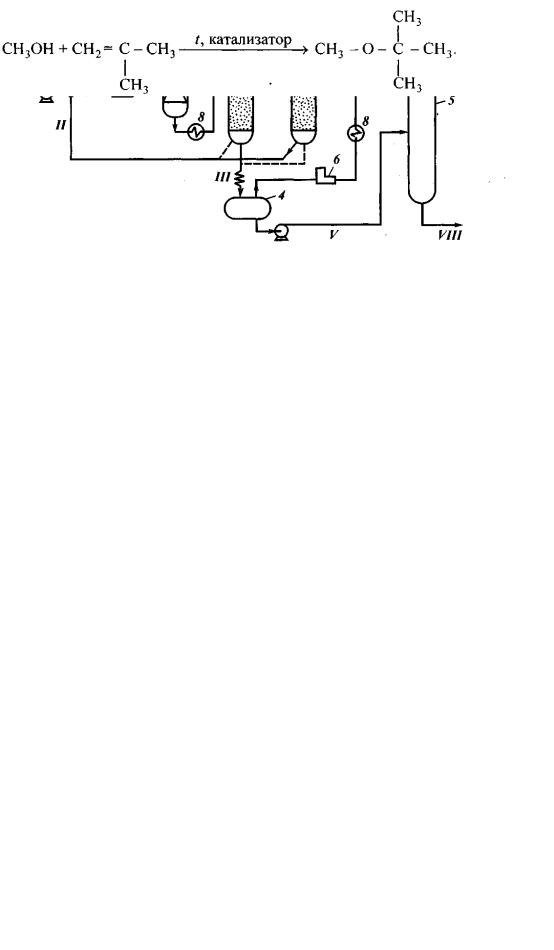
Fig. 4. Adsorption Isomerization Process Flow Sheet:
1 – reactor; 2, 3 – adsorbers-desorbers; 4 – separator; 5 – stabilizer; 6 – hydrogen compressor; 7 – furnace; 8 – heat exchangers;
streams: I – pentane-hexane cut; II – hydrogen-rich gas mixed with n-alkanes; III – reaction products free from n-alkanes; IV – hydrogen-rich gas; V – liquid to be fractionated; VI – hydrocarbon gas; VII – stabilization heads; VIII – isopentane and higher
The unit’s operating properties: adsorption cycle lasts 5 minutes, desorption cycle – 10 minutes, pressure 3 MPa, hydrogen-rich gas circulation ratio – 3.5 mole/mole (900 nm3/m3), zeolite tank capacity per cycle is 0.9 %.
Stable isomerization product’s octane number is about 87, whereas n-alkanes’s share in it is no more than 1.5 %.
3. Processing of Unsaturated Gases
Out of all GFU products, butane-butylene cut (BBC) is in most common use to obtain components of motor fuels.
BBC is converted into components of motor fuels by means of units that alkylate isobutane with olefins and produce methyl t-butyl ether (MTBE).
3.1. Obtaining MTBE
Methyl t-butyl ether is a product of isobutylene synthesis with methanol:
catalyst
87
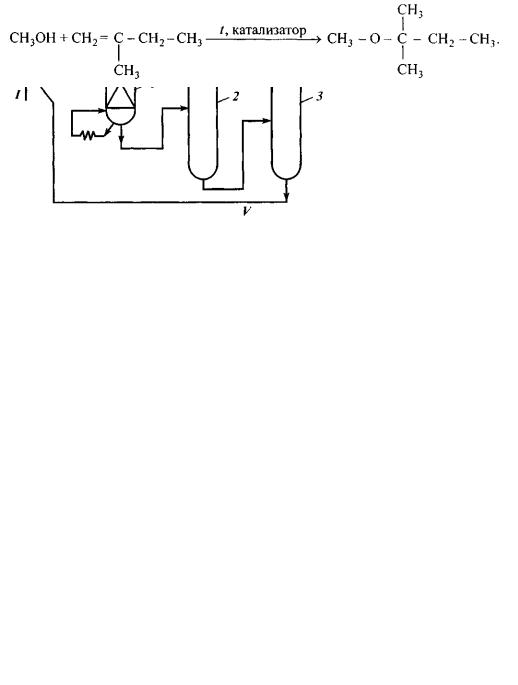
Primary material could be represented by any BBC containing more than 15 % of isobutylene, but no butadiene. Buten-1 and buten-2 in such synthesis constitute a ballast.
At present, the world’s annual production amount of methyl t-butyl ether approximates 25 million tons (including 12 million tons in the USA); total number of such units is about 100.
The process flow sheet is very simple (fig. 5): primary material components, once heated up in the heat exchanger, pass through the reactor, where excessive heat is withdrawn (exothermal reaction), and are separated in two towers.
Fig. 5. MTBE production process flow sheet: 1 – reactor; 2, 3 – distillation towers;
streams: I – isobutylene; II – methanol; III – butane and butylenes; IV – MTBE; V – methanol recirculate
Distillation tower I separates reaction mixture from n-butane and butylenes leaving subsequently for alkylation, whereas the top of distillation tower II obtains finished MTBE, and its bottom releases excessive methanol that returns into primary material mixture.
Ion exchange resin serves as a catalyst. Conversion degree approximates 94 % (in terms of isobutylene). The finished MTBE purity is 99 %.
1 ton of MTBE needs 360 kg of methanol and 690 kg of 100 % isobutylene.
The same process flow sheet is used to synthesize methyl t-amyl ether (MTAE).
catalyst
88
Their quality properties: |
|
MTBE |
MTAE |
|
|
||
Boiling point, °С |
|
55 |
87 |
Research octane number/motor |
octane |
118/100 |
110/99 |
number |
|
||
|
|
|
|
Combustion heat, MJ/kg |
|
35.1 |
37 |
Combustion heat of MTBE and MTAE is lower than that of gasolines. MTBE and MTEA are used as high-octane additives to gasolines to enhance their true vapor pressure and improve the distribution of octane numbers over low-boiling cuts (this, however, slightly decreases gasoline combustion heat).
3.2. Isobutane Alkylation with Butylenes
This is a process of obtaining high-octane gasoline component by chemical synthesis of isomers С8 on the BBC basis.
The process is accompanied by release of heat: actual thermal effect (including side reactions) is 85–90 kJ/mole of reacted olefins.
The process consists of the following reactions:
•major reaction – addition of butylenes to isobutene with the formation of 2,2,4-trimethylpentane;
•side reactions – decomposition with the formation of hydrocarbons having the number of carbon atoms not dividable by 4, butylenes polymerization that could take place due to lack of isobutene and heightened temperature; this is accompanied by growth of deficient butylenes and formation of undesirable products.
All these reactions between the products give rise to five basic hydrocarbons: trimethylpentanes, dimethylhexanes, light cut С4-С8, heavy cut С9 and higher, and acid-soluble high-molecular hydrocarbons (polymers).
Requirements for the process primary materials: maximum content of butanes 1 and 2 that mainly enter alkylation reaction to generate 2,2,4-trimethylpentane.
The most suitable primary material for the process is BBC obtained in catalytic cracking process with isobutene-to-butylene ratio as high as 1.2:1. BBC could also be obtained from delayed coking and thermal cracking processes.
In order to extend alkylation primary material basis, BBC has been supplemented with a small amount of PPC (under 20 % of the total amount of primary materials).
It is advisable that primary material contains no hydrocarbons С2 and С3 responsible for pressure growth.
89
N-butane as the process ballast is not preferable too. Detrimental impurities – divinyl, moisture and sulfur.
Presence of divinyl is harmful for the fact that it contributes to increase of the sulfuric acid flow rate: by about 10–20 kg per 1 kg of divinyl. Primary material is made free from divinyl by hydrogenation. Divinyl residue should never exceed 0.3 %.
Moisture reduces acid concentration, therefore it should never exceed 0.05 %. Sulfur content should not exceed 0.02 %.
Serving as process catalysts are strong acids i.e. sulfuric and hydrofluoric acids. Initial concentration of sulfuric acid is 96–98 %, its final concentration is 85–88 %. Concentration is reduced by its deactivation with water and olefins:
СnН2n + Н2SО4 → СnН2nSО2 + 2Н2О.
Acid continuously undergoes replacement i.e. part of spent acid is withdrawn and compensated for by an appropriate amount of fresh acid, or the whole acid, once spent, would from time to time be replaced.
Sulfuric acid flow rate is from 100 to 250 kg per ton of alkylate depending on primary material composition and quality, on reactor performance etc. (hydrofluoric acid flow rate is from 0.3 to 0.9 kg per ton of alkylate). Regeneration of sulfuric acid naturally reduces its flow rate to 10–30 kg per ton of alkylate.
Fig. 6 shows basic layout of the unit used to alkylate isobutene with butylenes that contains the following modules:
•module used to feed primary material that undergoes moisture removal;
•module of reactor 1, where acid circulates, excessive isobutene is delivered, and reaction excessive heat is withdrawing by means of evaporating reaction products;
•module used to make acid free (by settlement) from reaction products 2 that, once dried, are used to cool down the reactor;
•module used to withdraw propane from the reactor by pumping out vapors with compressor 7 and separating propane in tower 9;
•module used to single out circulating isobutene from reaction products in tower 4 and deliver it back to the reactor, once dried;
•light alkylate separation module consisting of towers 5 and 6, where initially (in tower 5) n-butane is separated, and then (in tower 6), light and heavy alkylates are separately obtained.
90