
книги / Переработка нефти и газа
..pdfBy-products – liquid and soft paraffin used for producing synthetic fatty acids, synthetic fatty alcohols, detergents, protein-vitamin concentrates and surfactants.
Theoretical Background
X-ray-structural analysis showed that each crystal cell of urea (NH2CONH2) has four molecules, i.e. it is a tetragonal structure. To form a complex, it is restructured to hexagonal structure (6 molecules spirally located at 120 degree angle). A channel with effective diameter 5.25 angstrom is formed inside, and that is why the complex is formed by normal paraffins with radius 4.2 angstrom which are held by Van der Waals bond. Complex formation is dictated by hydrocarbon molecule configuration and size but not by chemical structure of substance.
Factors Affecting Urea Dewaxing
Urea dewaxing products and yield depend on feedstock quality, solvent structure and consumption, activator, aggregative state of urea, temperature and contacting methods.
Feedstock quality. Urea dewaxing efficiency becomes lower is boiling point of fractions is increased. Resinous substances and sulfur-containing compounds make complex formation more difficult as they are adsorbed on urea crystals.
Solvents. Alcohols, ketones, alkyl halides, water and aqueous alcohol solutions are used as solvents. They are added for:
1.close contacting between interacting;
2.reducing viscosity; and
3.creating conditions for fractioning dewaxed product. Activators.
Activators, being polar substances, promote homogenous medium formation, make paraffin bond with other components weaker. Ethyl, methyl and isopropyl alcohols, acetone and methyl ethyl ketone are used as activators. In addition, activators often act as solvent.
Aggregative state of urea. Urea can be used for waxing in crystal state, in the form of saturated alcohol, ketone, ester and water solutions.
Temperature. Urea dewaxing temperature is 20–45 ºС. The higher the molecular weight of feedstock, the higher the process temperature.
Contacting methods. The main contacting method is agitation. Usually, duration of agitation ranges from 30 up to 60 minutes at agitation rate 60 revolutions per minute.
41
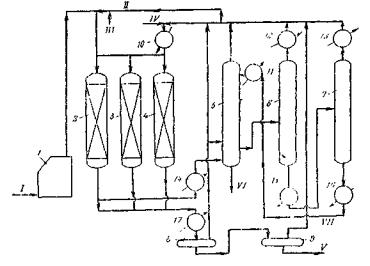
Dewaxing Performance of Watered Isopropyl Alcohol
Indicator |
Diesel Fuel |
Low-viscosity Oil |
Yield, mass % , dewaxed cut of |
82–83 |
85–86 |
feedstock |
|
|
Yield, mass %, wax |
10–12 |
6–10 |
Dewaxed cut pour point, ºС |
–45 |
–45 |
Wax melting point, ºС |
18–22 |
28–31 |
Zeolite Dewaxing
Purpose – to remove liquid normal paraffin from kerosene and diesel oil cuts. Advantage – normal paraffin purity is 98 – 99 %.
There are two groups of the commercial normal paraffin removal processes: Molex liquid-phase process, and Isosieve and Parex paraphrase processes.
The essence of Parex process is adsorption in hydrogen-containing gas medium. Ammonia is used as desorbent. Feedstock is hydrotreated kerosene and gasoil cuts with sulfur content not more than 0.01 % and olefin content not more than 2 %. 5AM zeolite zeosorb is used as adsorbent. Application of hydrotreating makes it possible to combine removing of normal paraffins with producing hydrotreated jet and diesel fuels with low pour point. Adsorption, desorption and purging temperature –380 ºС. Adsorber pressure is 0.5–1 MPa. NH3 – feedstock ratio is 4:1, and H2 – feedstock ratio is 5:1.
Fig. 9. Parex Process. Basic Process Flow Diagram
1 – preheater; 2–4 – adsorbers; 6, 7 – stripping tower; 8, 9 – separators; 10, 15, 16 – heaters; 11–14, 17 – coolers.
Process lines: I – feedstock; II – circulating Н2 – containing gas;
III – make-up H2 – containing gas; IV – desorbing gas; V – normal paraffins; VI – dewaxed product; VII – washing tower circulating water
42
Feedstock is heated in preheater 1 and mixed with circulating hydrogen-containing gas (fig. 9). The mixture comes to 1 from adsorbers (2, 3, 4) filled with zeolite and which are at adsorption stage while desorption takes place in other ones. The mixture of dewaxed cut, H2 gas and NH3 goes to washing tower 5 through cooler 14. In washing tower, dewaxed cut is separated from H2 gas and NH3, which is almost all absorbed by H2О, supplied to the top tray of the tower 5 after cooler 11. H2 containing gas comes out from the top of the tower 5, and mixed with feedstock. Before mixing, make-up H2-containing gas is added to circulating gas. NH3-saturated water comes out from the bottom of the washing tower 5 passes two-staged degassing in stripping towers 6 and 7, and after that it is recycled to the washing tower 5. Dewaxed cut is removed from the bottom of the washing tower 5. Mixture of normal paraffin strippants and NH3 comes to high pressure 8 and low pressure 9 separators through the cooler 17. NH3 coming out from the separators is directed together with NH3 from towers 6 and 7 to compressor and recycled to the adsorption system. The process product contains dewaxed cut (82 %) and paraffin (18 %).
Lecture 4
ADSORPTION REFINING AND FRACTIONATION
Adsorption refining is used for producing base oils, dearomatized liquid and solid paraffins, and special hydrocarbon liquids.
Adsorption refining is based on removal of polar components (resinous substances, oxygen and sulfur-containing compounds, and solvent refining agent residues). Activated carbon, natural clays, aluminosilicates, aluminogels and zeolites are used as adsorbent. All of them, except activate carbon, are polar adsorbents. Their molecules consist of silicon oxide and aluminum oxide. Adsorption of molecules of component to be removed takes place under orientation effect.
Asphaltic resinous substances has the highest adsorption ability from among all hydrocarbons, then come polycyclic aromatic hydrocarbons, bicyclic aromatic hydrocarbons, monocyclic aromatic hydrocarbons, naphthenes and parrafins.
The basic properties of adsorbent are adsorption activity, porosity, specific surface and dispersion ability. There are static and dynamic adsorption activity.
Static adsorption activity is determined by maximal amount of substance absorbed by unit of adsorbent weight at the given temperature, pressure and concentration of adsorbed substance.
43
Dynamic adsorption activity is determined by adsorption rate.
Specific surface of adsorbent depends on the adsorbent structure, and it is about 1000 m2/g for porous adsorbent (silica gel and aluminogel), and 1–500 m2/g for finely porous adsorbent.
Dispersion ability. The higher the dispersion ability, the higher the contact surface.
Adsorption Refining and Fractionation. Basic Processes
Advanced contact treatment of dewaxed oils by fine-divided adsorbent (refining earth) with subsequent filtration in disk and plate-and-frame filters.
Percolation filtration is oil treatment by filtration through fixed bed of granular adsorbent.
Continuous countercurrent processes with mobile bed of micro-spherical synthetic aluminosilicate (instead of solvent refining or advanced treatment of urea dewaxed paraffins).
Advanced Contact Treatment
Advanced contact treatment is the final stage of base oil production. It is aimed at improving oil color and storage property, removing solvent residues and decomposition products formed at previous stages, reducing sulfur content, reducing cokeability and increasing oil-flash temperature.
Bleaching clays are used for advanced contact treatment. Adsorbent grain size is about 0.1 mm, and process temperature is 150–300 ºС. Contact time is about 30 minutes. Yield of distilled oils is 96–98 %, and residual oils – 93–95 %.
Percolation is filtration through fixed adsorbent bed. Resins, oxygen and nitrogencontaining compounds, naphthenic acids and sulpho-acids are removed from filtered oil. High-viscosity oils are dissolved in gasoline or naphtha before filtration. Process temperature is 20–100 ºС. Silica gel or aluminosilicate is used as adsorbent. Adsorbent grain size is 0.5–2 mm for viscous oils, and 0.3–0.5 mm for lowviscosity oils.
Continuous adsorption refining is used for producing two oils: raffinate 1 – basic refined oil and raffinate П – aromatized oil desorbed from the adsorbent surface. By transformer distillate refining, 87–89 % raffinate 1 and 6–8 % aromatized oil (raffinate П) are produced.
44
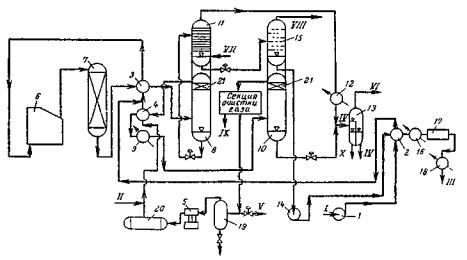
Oil Hydrogenation
Hydrogenation includes hydrotreating, hydroisomerization and hydrodewaxing.
The important advantages of hydrogenation, if compared to extraction, is environmenttal cleanness in terms of disposal of by-products – H2S, NH3, hydrocarbon gases and fuel cuts.
Hydrotreating
Purpose – to increase thermal stability, reduce cokeability and acidity, and improve color of base oils.
Feedstock – dewaxed distillate and residual raffinates. End product – distillate and residual base oils.
Hydrotreating results in reducing viscosity, increasing viscosity index (on 1–2 units), increasing desulfurization on 30–40 %n and improving oil color, but pour point becomes higher on 1–3ºС.
Catalyst – AKM or ANM, process temperature is 200–325 ºС, and pressure is 3.5–4 MPa, weight hour space velocity is 1.5–3 h–1, Н2 – containing gas circulation ratio is 250–500m³/m³ of feedstock. Н2 concentration in gas is 75–85 % vol.
Fig. 10. Oil Hydrotreating Unit
1 – feed pump; 2–4 – heat exchangers; 5 – compressor; 6 – pipe still; 7 – reactor; 8 – high temperature and high pressure separator; 9 – circulating gas cooler;
10 – low temperature high pressure separator; 11 – stripper; 12 – condenser-cooler; 13 – gas separator; 14 – oil pump; 15 – vacuum drying tower; 16, 18 – coolers; 17 – filter;
19 – separator; 20 – receiver tank; and 21 – knockout drum
Feedstock is mixed with make-up and circulating Н2-containing gas and directed to pipe still 6 (fig. 10), and at temperature 320–350 ºС and pressure 3–4 MPa, the mixture comes to reactor 7. Then, it is directed to the high temperature and high
45
pressure separator 8 (temperature is 210–250 ºС). Gases, through heat exchanger 4 and condenser-cooler 9, comes to low temperature high pressure separator 10 (temperature is about 40 ºС), and oil goes to the stripper 11. From the top of the stripper the mixture of gases and vapors is cooled in the condenser-cooler 12 and is directed to the separator 13. Water is discharged from the bottom left part of the separator, and distillate is removed from the bottom right part of the separator, gases are directed to the fuel line from the top of the separator. From the stripper 11 oil comes to the vacuum drying tower 15 which is operated under residual pressure 13.3 kPa, and goes off the unit through the filter 17. Condensate from the separator 10 comes to the gas separator 13. H2S is removed from circulating gas by ethanolamines.
Hydrocracking
Feedstock – asphalt-free oils and heavy vacuum distillates.
End product – base oils with improved physicochemical properties and performance characteristics.
Under hydrocracking, oil properties are changed by the following processes:
1.polycyclic and naphthenic hydrocarbon hydrogenizing and hydrocracking, which also cause cycle reduction; and
2.S, N and O-containing compound hydrogenizing.
Oil hydrocarbon content change under hydrocracking:
Hydrocarbon |
Feedstock, % |
Hydrogenation |
|
mass |
product, % mass |
Paraffin hydrocarbons |
1–2 |
4–5 |
Naphthenic aromatic monocyclic |
32–33 |
67–68 |
hydrocarbons |
|
|
Naphthenic aromatic polycyclic hydrocarbons |
20–21 |
26–27 |
Aromatic monocyclic hydrocarbons |
12–13 |
1–2 |
Aromatic polycyclic hydrocarbons |
28–29 |
менее 0,5 |
Sulfur-containing hydrocarbons |
5–6 |
0 |
TOTAL polycyclic hydrocarbons |
53–54 |
26–27 |
Reduction of polycyclic hydrocarbon content results in increased viscosity index from 40–60 to 110–130 units.
Basic process parameters: Temperature –360–450 ºС.
Pressure – 15–17 MPa, and 20 MPa for oil residue hydrocracking.
46
Weight hour space velocity is 0.2–0.5 h.
Н2-containing gas circulation ratio is 800–2000 m³ /m³ of feedstock. Catalysts are: Ro, Ru, Ir and Os oxides and sulfides on Si, Ti, Al, Mg and zirconium oxide support. Hydrocracked oils are high-quality base for all-weather motor oils, both turbine and industrial.
Hydroisomerization
One of the promising hydrogenation processes for oil production is hydrogenation of highmolecular paraffin hydrocarbons. Parrafins, slack waxes and petrolatum are feedstock. Hydroisomerization results in increasing viscosity index to 140–160 units, and lowering pour point from –20 to –35 ºС. Yield of hydroisomerization product is 40–60 % of feedstock.
Catalytic Hydrodewaxing
Purpose – to producer base oils with pour point lower than –50 ºС.
Feedstock – oil distillates, asphalt-free oils, oil raffinates, solid paraffins, petrolatum, slack wax and other.
Yield of dewaxed oil from isomerization product is 90–95 %.
Bitumen Production
Feedstock for bitumen production is heavy oil residues: tars, asphalts from deasphaltizing, extracts from solvent refining, cracked resides and other residual cuts. By production method, they are subdivided into residual, air-blown and compounded bitumen.
Residual bitumen. It is produced from cuts with high asphaltic resinous substances. Vacuum column feed temperature should be not higher than 425 ºС. Residual pressure at the bottom of the column should be maintained within the range 6.5 –13.3 kPa.
Air-blown bitumen. It is produced by oxidizing tar or residual bitumen with air oxygen. The basic factors of oxidation are temperature, air rate and pressure.
The higher the temperature, the higher oxidation rate. For high-viscosity oil residues, temperature in oxidizer is 250–270 ºС, and 270–290 ºС for paraffin oil. Temperature is controlled by air rate.
Air consumption depends on chemical composition of feedstock and required bitumen quality, and ranges from 50–400 m³ per ton of bitumen.
Bitumen quality becomes higher as pressure increases due to condensing of the part of oil vapor, and duration of oxidation is reduced. Usually, pressure fluctuates from 0.3–0.8 MPa.
47
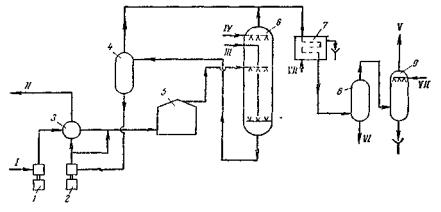
By application, bitumen is subdivided into road bitumen, construction bitumen and special bitumen. Construction bitumen is used for foundation waterproofing. Special bitumen includes roofing, insulating, high-melting (rubrax) bitumen and grahamite.
Final bitumen properties are monitored by special indicators:
Penetration (needle penetration depth, mm, in bitumen layer at temperature 25 and 0 ºС). Melting point is determined by ring-and-ball method. Stretching property (bitumen capability of stretching in thin filaments (stringiness) under standard load at temperature 25 and 0 ºС). Brittle point is indicative of bitumen freezing resistance. Adhesion – capacity of rigid adherence with mineral material.
Air-blown Bitumen Production Process Flow Diagram
Fig. 11. Continuous Oxidizer. Basic Process Flow Diagram:
1, 2 – pumps; 3 – heat exchanger; 4, 8 – separators; 5 – pipe still; 6 – oxidizer; 7, 9 – condensers. Process lines: I – feedstock; II – bitumen; III – air; IV – steam; V – gas to atmosphere; VI – solar; VII – water
Feedstock comes to the reaction space of the oxidizer 6 (fig. 11) through the heat exchanger and coil of the pipe still 5. Compressed air is blown to the bottom of the oxidizer. Air-blown bitumen overflows from the bottom of the oxidizer to the separator 4. The major part of the product is directed to the feedstock line, and the rest part comes through the heat exchanger to pouring unit. Gaseous products of oxidation, which left the oxidizer 6 at the top and separator 4, are sent to the condenser-cooler 7. Gas-liquid mixture is separated in the separator 8. Solar is drained from the bottom of the separator, and is used as boiler fuel oil component, and gases are used as pipe still fuel.
Compounded bitumen is produced by mixing air-blown bitumen with residual oil. It makes it possible to control commercial bitumen properties.
48
Laboratory course on
OIL REFINING AND OIL CUT TREATING
COMMERCIAL OIL PRODUCTION
Laboratory Work 1 (2 hours)
FRACTIONAL OIL CONTENT ANALYSIS
Fractionation is separation of oil and oil products into clean cuts based on of different boiling points.
Fractional content is one of the most important indices to be indicated in specifications on aviation and automobile gasoline, aviation and burning kerosene, diesel fuels and solvents. Fractional content is a very important performance characteristic as it characterizes fuel volatility.
Carburetor (gasoline) engine fuel volatility must provide easy start-up of cold engine, engine acceleration capability, i.e. easy transfer from one engine behavior to another, and even distribution of fuel to engine cylinders.
Air engine fuel, together with heavy fractional content for preventing fuel system vapor locking at high altitude, must be fast evaporated in combustion chamber. Diesel fuel fractional content must provide high evaporation rate and air mixture formation rate after injection. It must have sufficient ignition characteristics which becomes poorer if diesel fuel fractional content is lighter.
Fuel fractional content is evaluated by yield of cuts 10 % vol., and it depends on distillation temperature under standard conditions. As a rule, initial boiling point – first drop moment from the cooler end, 10, 50, 90 and 97.5 % vol., and end boiling point – maximum temperature at distillation stage completion, are monitored. Initial boiling point and final boiling point 10 % vol. characterize fuel startability. If such points are decreased, cold engine start-up becomes easier at low temperature. But steep decline of 10 % point is undesirable as fuel system can be vapor locked.
Final boiling point 50 % vol. impacts the cold engine warming-up time, fuel consumption for warming-up and acceleration of engine. Final boiling point decrease promotes fast engine warming-up at lower fuel consumption, and significant improving acceleration.
Point 90 and 97.5 % vol. and end boiling point characterize evaporation degree of fuel and possibility to bring a motor into full power. The higher such points, the lower the fuel evaporation degree, the higher fuel consumption, oil dilution and sooting, and it causes fast engine wear.
49
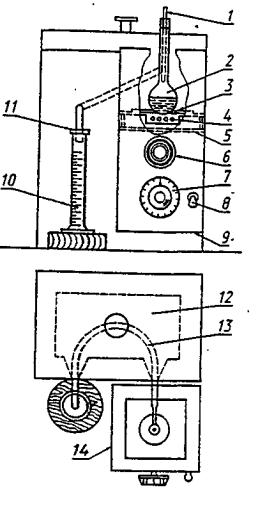
Fig. 1. Oil Fractional Distillation Apparatus: 1 – thermometer; 2 – flask; 3 – asbestos gasket; 4 – heating element; 5 – support; 6 – flask position adjuster; 7 – heating control; 8 – switch; 10 – measuring cylinder; 11 – filtration paper; 12 – cooling bath; 13 – cooler tube; 14 – case
Oil fuel fractional content is determined by special laboratory apparatus (see fig. 1). 100 ml of oil product with temperature 20 оС is poured in clean dry flask 2 from measuring cylinder 10. Then, thermometer 1 calibrated from 0 to 360 оС is inserted in the neck of the flask through properly attached cork. Axis of thermometer shall coincide with the flask neck axis, and top of mercury ball shall be at the level of the bottom end of the drain tube in soldering point. Cooler 13 tube is rubbed and connected to drain tube of the flask through cork. The drain tube of the flask must penetrate the cooler tube on 25–40 mm and shall not touch its walls. Under gasoline distillation, the cooler 12 is filled with ice and poured with water, maintaining temperature range 0–5 оС. Under distillation of oil products with higher boiling point, it is cooled by flowing water supplied from the bottom nozzle of the cooling bath. Cooling water temperature must not exceed 30оС. In the assembled apparatus, the flask must be placed true vertical on asbestos gasket 3.
The measuring cylinder, without drying, is placed under the bottom end of the cooler tube so that it penetrates the cylinder on for at least 25 mm. The cylinder opening is plugged with cotton wool.
When the apparatus is assembled, gradual heating of the flask starts. Oil product evaporates, condenses in the cooler and comes to the measuring cylinder. To observe the standard distillation conditions, Для соблюдения стандартit is necessary to control heating so that the time from the beginning of heating to the first distillate drop is not less than 5 minutes and not more than 10 minutes (for kerosene and light diesel fuel – 10–15 minutes). First drop temperature is recorded as initial boiling point. Further, heating rate shall provide gradual distillation rate with withdrawal 4–5 ml per minute, which is 20–25 drops per 10 seconds.
50