
книги / Переработка нефти и газа
..pdfmaterials as coal, shale, heavy resin of coal distillation and tar-type oil residues. The process temperature is 420–500°С. Catalysts contain iron, tungsten, molybdenum and nickel. Final product is normally represented by gasoline, but even heavier distillates (e.g. diesel and boiler fuel) could be obtained.
3. Hydrocracking. The process applies diluents of heavy liquid raw materials, as well as new efficient catalysts. This enables to significantly reduce reaction zone pressure (to 30–150 atmospheres) and hydrogen consupmtion.
Catalytic Treatment of Hydrocarbon Gases
and the Lightest Gasoline Cuts
1.Polymerization of olefinic gaseous hydrocarbons;
2.Alkylation of gaseous and liquid isoparaffin hydrocarbons with olefins;
3.Alkylation of aromatic hydrocarbons with olefins;
4.Dehydrogenation of butane and pentane cuts.
5.Isomerization of normal butane and light gasoline hydrocarbons.
All these processes aim at obtaining either fuel components or raw material for petrochemical industry. Application modes of the above light hydrocarbons treatment options and catalysts vary so widely, that it seems no possible to generalize such processes. Some of them will be described later.
Lecture 2
PETROLEUM CHEMISTRY
No one can imagine oil treatment process chemistry without information about properties of hydrocarbons contained in oil.
Atoms and Molecules
Properties of matters depend on atoms they consist of and on how are the atoms connected with one another within groups termed molecules. The most important rules relate to valency and chemical bonds.
Valency. Each kind of atoms (element) is capable of combining with other atoms in accordance with its structure. For example, an atom of carbon always wants to annex four other atoms to itself, while an atom of hydrogen – only one.
Definition: Valency of a certain element’s atom is equal to the number of hydrogen atoms (or their equivalent), with which such atom can combine.
Chemical bond. Type of connection between two atoms is termed chemical bond.
61
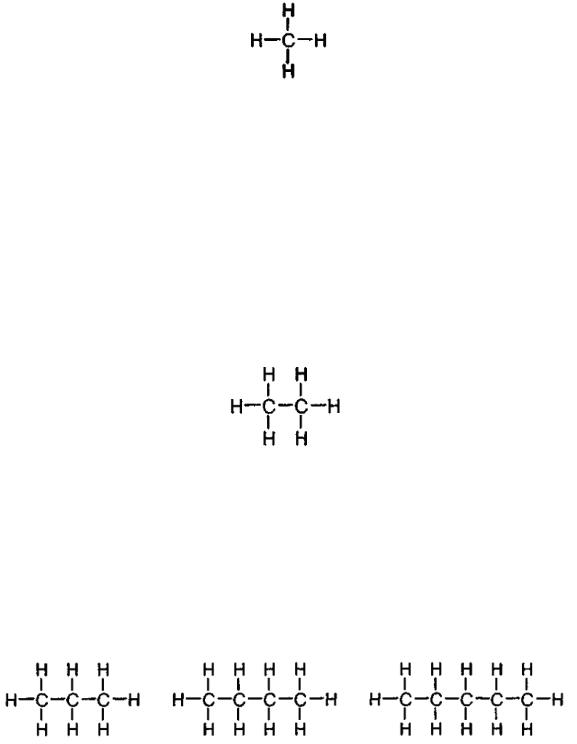
Hydrocarbons
The simplest example capable of describing all the three terms i.e. valency, chemical bond and hydrocarbon, is methane consisting of a single atom of carbon and four atoms of hydrogen, known as СН4. Have a look at its structure to see that valency rules are observed (fig. 1).
Fig. 1. Methane
The subsequent elementary hydrocarbon, ethane, reveals a certain complication. Ethane’s chemical formula is С2Н6 (fig. 2). We see that each carbon atom is surrounded by four bonds, while each hydrogen atom – by a single bond. Mind that one carbon atom is combined with another carbon atom. It’s quite a usual thing. By the way, when hydrogen is mentioned as an individual compound, its formula always looks as H2 because hydrogen always occurs like this: a single hydrogen atom is combined with another hydrogen atom, and so would valency rule be complied with for the both atoms.
Fig. 2. Ethane
An entire class of hydrocarbons could be imagined by obtaining new compounds exactly as ethane has been obtained from methane. Such compounds are termed unsaturated hydrocarbons (alkanes) or paraffins having common formula that looks like СnН2n+2 (fig. 3). Examples of such hydrocarbons are propane, normal butane (n-butane) and normal pentane (n-pentane).
1 – (С3Н8) |
2 – (С4Н10) |
3 – (С5Н12) |
Fig. 3. |
Propane (1); normal butane (2); normal pentane (3) |
62
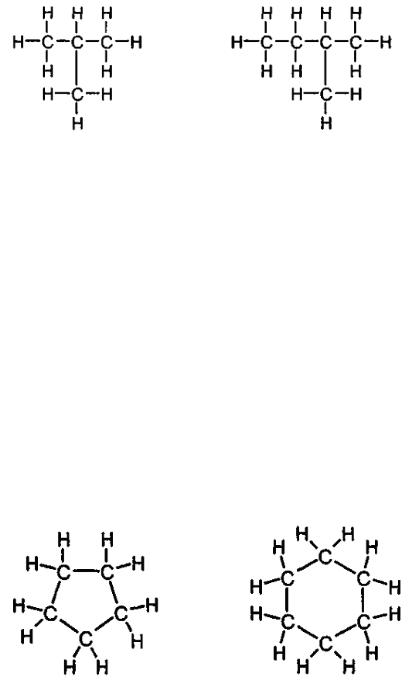
What is the meaning of word “normal” prior to words butane and pentane? The matter is that atoms of hydrocarbons С4Н10 and С5Н12 could be distributed in various ways. One of such ways is shown in the figure below, but besides we could have drawn a branch from one of the carbon inner atoms. Compounds, i.e. С4Н10 and С5Н12 resulted from this are paraffin hydrocarbons with isometric structure termed as iso-butane and iso-pentane (fig. 4).
1 – (С4Н10) |
2 – (С5Н12) |
Fig. 4. Iso-butane (1); iso-pentane (2)
Although gross formulas of n-butane and iso-butane are similar, they behave differently. They have various boiling points, various density (for their various packages), as well as differently react, which will be described in alkylation section.
Naphthenes
Another class of hydrocarbons is cyclic compounds usually containing more than five carbon atoms. A ring made of a chain with five carbon atoms is cyclopentane (С5Н10). Worth mentioning is that cyclopentane contains less atoms of hydrogen than n-pentane or iso-pentane. There are also large cycles such as cyclohexane. This class of compounds is termed naphthenes or naphthene hydrocarbons (fig. 5).
1 – (С5Н10) |
2 – (С6Н12) |
Fig. 5. Cyclopentane (1); cyclohexane (2)
63
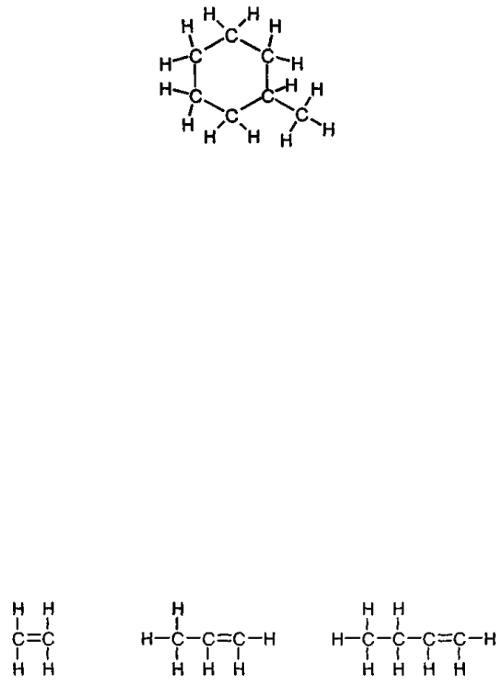
(С7Н14)
Fig. 6. Methylcyclohexane
Apart from simple paraffin and cyclic hydrocarbons, an endless number of opportunities is offered due to linkage of molecules of these two types between one another. The simplest example is methylcyclohexane С7Н14 resulting from the attachment of CH3 group (termed methyl group) to cyclohexane instead of one of its hydrogen atoms (fig. 6).
Olefinic and Aromatic Hydrocarbons
It is possible to obtain a molecule with two atoms of carbon and only four atoms of hydrogen. At first glance, this violates the rules of valency that you have considered just a few minutes ago. But a chemical compound known as ethylene С2Н4 is arranged so that carbon atoms are linked by double bond, which compensates for lack of hydrogen atoms (fig. 7).
1 – (С2Н4) |
2 – (С3Н6) |
3 – (С4Н8) |
Fig. 7. Olefinic hydrocarbons: 1 – ethylene; 2 – propylene; 3 – butylene
The double bond holding two carbon atoms together is not stronger than an ordinary bond but weaker. One can imagine that two bonds exist where a single bond could have been. Therefore, the compound proves chemically unstable, fairly easily reacts with other substances turning into a new compound with no double bond. Therefore, ethylene is frequently used to synthesize more complex chemical compounds. For example, many ethylene molecules connected to each other produce polyethylene.
64
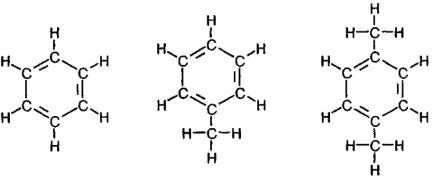
A principal property of olefins is that they have by two hydrogen atoms less than an appropriate saturated hydrocarbon (i.e. paraffin hydrocarbon containing a full package of hydrocarbon atoms), which means that their common formula looks like СnН2n.
There are no natural olefins. They would come into being created by people with the help of cracking process.
Other olefins that are of interest from oil refining viewpoint are propylene (С3Н6) and butylene (С4Н8). Like ethylene, such compounds could be caused to react with other substances, therefore they are suitable as raw materials for a number of chemical and oil refining processes.
Aromatic hydrocarbons constitute another exception to valency rules. Let us consider a cyclic compound – cyclohexane. Each carbon atom is linked to two other carbon atoms and carries two atoms of hydrogen. Removing one hydrogen atom from each atom of carbon will violate valency rules. Valency could be reestablished by binding carbon atoms with a number of double bonds. To do this, each second atom of carbon should have double bond (fig. 8). We have just obtained a molecule of С6Н6, i.e. benzene. It is very simplistic to think that each second bond in benzene ring is double bond. Closer to reality are the terms of resonance structures and jumping bonds.
Replacement of a single hydrogen atom of benzene molecule with group СН3 will produce a hydrocarbon with composition С7Н8, i.e. toluene (CH3 group is termed methyl radical, and C2H3 group – ethyl radical. Names of the radicals are similar to the names of appropriate paraffins i.e. methane an ethane). Replacement of two hydrogen atoms in benzene ring with two methyl radical will produce a molecule with composition С8Н10 – i.e. xylene.
1 – (С6Н6) |
2 – (С7Н8) |
3 – (С8Н10) |
Fig. 8. Aromatic hydrocarbons: 1 – benzene; 2 – toluene; 3 – xylene
65
Double bonds in benzene ring are fairly unstable and chemically active. Therefore, benzene is widely used as a building block for obtaining new substances in chemical industry. Toluene and xylene are valuable too.
Lecture 3
OIL REFINING THERMAL PROCESSES
Thermal Cracking
Thermal cracking means the decomposition of hydrocarbon molecules usually olefins as the system lacks hydrogen. Paraffins with long chain could break in any place. Cyclic compounds would normally break in the place of attaching a side group, if any. As a result, heavy cracking products would usually be rich with olefins, naphthenes and aromatics.
Thermal cracking raw material would usually be represented by vacuum distillation residue, sometimes by heavy gasoil and gasoil recycle stock from cracking unit.
If products used for thermal cracking widely differ in terms of boiling temperatures, volatile raw material would never be mixed up with higher boiling hydrocarbons, since volatile raw material requires more severe conditions (higher temperatures).
Furnaces bring the raw material to temperatures ranging from 520 to 550 °С. The raw material is kept in coils passing through furnaces for relatively short time to undergo no excessively deep chemical transformations. Failing this will give rise to coke that will quickly clog the coils, which could stop the whole process. Then, hot raw material enters soaking section that should remain under sufficiently high pressure (about 140 psi or 10 atmospheres) favorable to cracking but never to coking.
Leaving the soaking section, the product will be mixed up with the colder recirculating flow, which stops cracking process. The both flows enter distillation section, where volatile products will at once go up as the section pressure is low (as it takes place in straight-run residue vacuum distillation tower) (fig. 1).
66
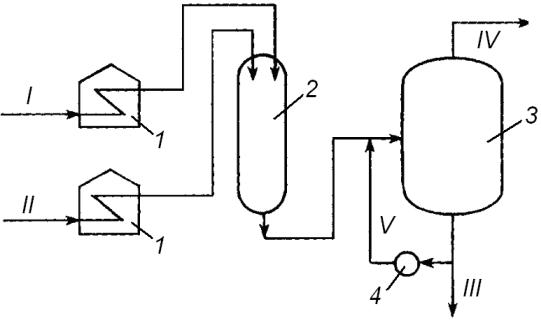
Fig. 1. Thermal cracking unit reaction module:
1 – furnaces; 2 – reactor; 3 – distillation section; 4 – cooler;
I – raw material (gasoil); II – raw material (residue); III – cracking residue; IV – gas, gasoline; V – recirculation flow
The bottom will contain heavy cracking residue to be partly re-directed into soaking chamber as recirculation flow; while the rest would normally be used as a component of residual fuel.
Coking
Coking is a thermal cracking of heavy oil under more severe conditions used to obtain solid residue i.e. coke as one of the products. Long-year information about thermal cracking fairly clearly indicates that due to high temperatures and very high raw material feed rates no coke formation takes place unless the raw material starts leaving narrow coils of the furnaces for surge drum. Keeping the hydrocarbon mixture for a certain period in this isolated tank termed coke drum would enable to control high-conversion cracking and coking processes. There is a method adequate to efficiently carry out this process making it a stage of the continuous cracking. Although coking idea is simpler than that of cracking, the former requires more complicated equipment capable of handling coke. As coke is a solid matter, this creates additional problems.
Coking raw material (the same as that used for cracking) is heated in furnace (I) nearly to 540 °С and fed to the lower part of coking drum (II). Volatile cracking
67
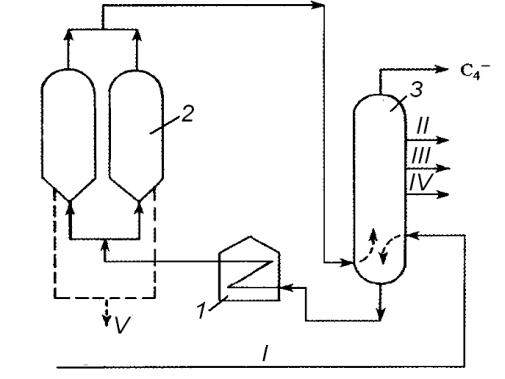
products go up and enter tower (III) for separation. High-boiling products remain, and as heating continues, decompose to form coke that represents a solid matter similar to coal.
Coking unit layout is shown in fig. 2.
Fig. 2. Coking unit layout:
1 – furnace; 2 – coke drums; 3 – distillation tower;
I – raw material; II – gasoline; III – light gasoil; IV – heavy gasoil; V – coke
Coke removal at present is a daily routine performed by means of water jet under the pressure of 140 atmospheres. At first, a hole is drilled from top to bottom in coke cake in the drum. Then, a rotating rod is lowered to the hole, which makes water jet swing. High pressure breaks the coke cake into pieces that fall from the lower part of the tower into cars carrying them to a warehouse. The drums normally operate in the 48-hours cycle: during 24 hours the drum is filled with coke, while switching over, cooling down and removal of coke take about 22 hours, during which the other drum is filled with coke.
Products leaving coking and thermal cracking units are sensitive to process conditions primarily represented by temperature in furnaces and raw material properties. Range of boiling temperatures, group and relative density of raw material usually enables to predict the process results.
68
Coke. Coke deserves a couple of words. Bulk of coke produced by a refinery looks like sponge and is therefore termed spongy coke. Major applications of such coke are manufacture of electrodes, obtaining of calcium carbide and mineral carbon. Spongy coke is not strong enough to be used in blast furnaces for making cast iron or in foundry production.
Form II of coke is needle coke termed like this for its long pointed microcrystals. Obtaining such coke requires a specific raw material and more severe operation conditions. In terms of its quality, such coke is more preferable for making electrodes than spongy coke. Therefore, needle coke is significantly more expensive than spongy coke.
Coke contains a certain amount of water and liquid hydrocarbons. Therefore, prior to its use it should be dried. Coke grinding with subsequent heating in order to remove the above impurities is termed calcination.
Apart from this, coke could be used as refinery fuel just in the same way as any other solid fuel, for example, coal.
Light Cracking (Visbreaking)
Target product of processing oil residues i.e. flux oil and tar is normally represented by boiler fuel obtained as a result of initial residue viscosity reduction. Such a process of raw material superficial decomposition is termed light cracking or visbreaking.
Visbreaking is thermal cracking for the poor. Visbreaking unit uses heavy residue of vacuum distillation process, part of which undergoes thermal cracking in it. The product could again be divided into cuts, which reduces residue amount. Then, the residue is supplemented with cutter oil (diluter), which makes the residue suitable for use as a residual (boiler) fuel. Amount of the cutter oil added for the dilution is lower than the amount of cracking products leaving the unit. Therefore, the residual fuel amount as a whole becomes lower.
Used as the diluter could be heavy cracking gasoil, recirculation gasoil or a cut obtained as a result of products separation at the same unit.
Visbreaking looks like thermal cracking, but differs from the latter in terms of intensity. In the present case, equipment is simpler and whole process is cheaper. On the other hand, only 20–30 % of vacuum distillation heavy residue undergoes transformation.
69
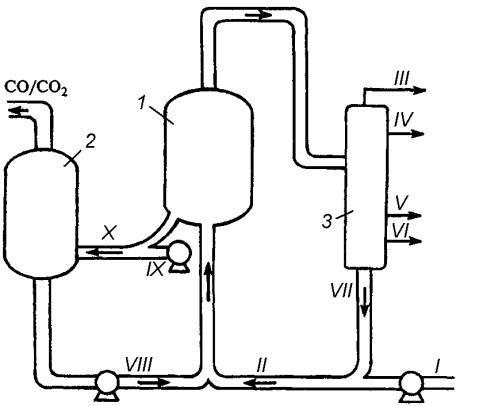
Lecture 4
CATALYTIC CRACKING
Production Process
Catalytic cracking (fig. 1) raw material is normally represented by straight-run heavy gasoil, as well as light cut of vacuum distillation. Cracking raw material boiling temperature should range from 340 to 590 °С. The process would never start, should the reactor temperature during cracking be under 480 °С.
Fig. 1. Catalytic Cracking Unit:
1 – reactor; 2 – regenerator; 3 – fractionating tower;
I – clean cracking feed; II – raw material with recycle; III – hydrocarbon gases; IV – gasoline; V – light gasoil; VI – heavy gasoil; VII – recycle;
VIII – fresh catalyst; IX – air; X – dead catalyst
The process is designed so that to specifically facilitate cracking progress. The task consists in transforming heavy cuts into gasoline. Ideally, cracking products boiling temperatures should range within an interval corresponding to gasoline, but no technology could ever be ideal. The unit provides a number of processes. When large molecules disintegrate, hydrogen would be not sufficient to saturate all the
70