
книги / Технологические расчеты по получению различных видов целлюлозы
..pdfТаблица 1 . 3
Итоговый материальный баланс для периода варки (на 1 т целлюлозы)
|
Приход |
|
Расход |
|
Осталось |
||
Вещества |
отхими- |
сперепуск- |
сосду- |
нахими- |
|
||
ческих |
нойжидко- |
вочными |
ческие |
всего |
вкотле |
||
|
|||||||
|
реакций |
стью |
газами |
реакции |
|
|
|
Вода(ипар), л(кг) |
– |
1790 |
40 |
– |
1830 |
6660 |
|
Древесина (целлю- |
– |
– |
– |
650 |
650 |
880 |
|
лоза), кг |
|||||||
|
|
|
|
|
|
||
Органическиевеще- |
|
|
|
|
|
|
|
ства, кг: |
|
|
|
|
|
|
|
– газообразные |
|
|
|
|
|
|
|
илетучие |
72 |
– |
72 |
– |
72 |
– |
|
– растворенные |
578 |
178 |
– |
– |
178 |
848 |
|
SO2 |
– |
64 |
218 |
– |
282 |
100 |
|
Na2O |
– |
4,1 |
– |
14,7 |
18,8 |
6,7 |
Конечная сдувка (спуск давления). При конечной сдув-
ке давление снижается с 0,6 до 0,2 МПа (с 6 до 2 кгс/см2). За время конечной сдувки из котла уходит значительное количество SO2: титр щелока снижается с 1,5 до 0,3 % SO2 (см. рис. 1.1). Можно с небольшим приближением считать, что в конечный момент спуска давления в газовом пространстве котла не будет содержаться SO2, а будет находиться только водяной пар. Давлению насыщенного пара 0,2 МПа (2 кгс/см2), т.е. 0,30 МПа (3,03 кгс/см2) абсолютного давления, отвечает температура около 133 °С (см. табл. П1 приложения). Следовательно, будем считать, что в конце спуска давления температура содержимого котла равна 133 °С. Снижение температуры содержимого котла вызывает выделение водяного пара, уходящего с конечной сдувкой.
Если принять теплоемкость целлюлозы и органических растворенных веществ щелока равной 1,34 кДж/(кг·°С), то при снижении температуры содержимого котла со 140 до 133 °С выделится всего тепла
21
[6660 · 4,19 + (880 – 848) · 1,34] · (140 – 133) = 211 410 кДж.
Средняя температура жидкости в котле за время конечной сдувкиравна(140 + 133) : 2 = 136,5 °С. Этойтемпературепотаблицам насыщенного пара отвечает теплота испарения 2158,8 кДж/кг (515,6 ккал/кг). Следовательно, пара при конечной сдувке выде-
лится211 410 : 2158,8 = 98 кг.
Жидкости в котле в конце спуска давления будет
6660 – 98 = 6562 л.
В щелоке после спуска давления останется SO2
6562 – 0,003 = 20 кг.
При конечной сдувке уходит из котла SO2 100 – 20 = 80 кг. Итоговый баланс конечной сдувки приведен в табл. 1.4. Концентрация органических веществ в щелоке к моменту
выдувки равна
848 6562 = 129 г/л.
Таблица 1 . 4
Концентрацияорганическихвеществ вщелоке кмоменту выдувки
|
Находилось |
Уходит |
Остаетсявкотле |
|
Вещества |
вкотле |
сконечной |
кмоменту |
|
|
кконцу варки |
сдувкой |
выдувки |
|
Жидкость(ипар), л(кг) |
6660 |
98 |
6562 |
|
Целлюлоза, кг |
880 |
– |
880 |
|
Органические растворенные |
848 |
– |
848 |
|
вещества, кг |
||||
|
|
|
||
SO2 |
100 |
80 |
20 |
|
Na2O |
6,7 |
– |
6,7 |
Выдувка. Во время выдувки избыточное давление падает со 196 кПа (с 2 кгс/см2) до 0 и температура соответственно со 133 до100 °С. Засчетохлаждениясодержимогокотлавыделяетсятепла
[6562 · 4,19 + (880 + 848) · 1,34] · (133 – 100) = 983 090 кДж.
22
При среднем избыточном давлении (196 + 0) : 2 = 98 кПа, или 199 кПа (2,03 кгс/см2) абсолютного давления, теплота испа-
рения равна 2205,3 кДж/кг. Пара выделится 983 090 : 2205,3 |
= |
= 445 кг/т целлюлозы. Остается щелока в сцеже 6562 – 445 |
= |
= 6117 л/т целлюлозы. |
|
Концентрация органических веществ в щелоке равна
848 10006117 = 139 г/л.
Количество SO2, уходящего с парами вскипания, примем равным 50 % от SO2, содержавшегося в щелоке, т.е. 20 · 0,5 = 10 кг. Остальные20 – 10 = 10 кгSO2 останутсявщелоке.
Суммарный материальный балансдля разобранного примера сульфитной варки приведен в табл. 1.5. Общее количество сдувочной и перепускной жидкости, уходящей из котла, с учетом конденсата водяных паров (см. табл. 1.5) составит 2240 + 138 = 2378 л/т целлюлозы.
Процент регенерации жидкости по отношению к количеству варочной кислоты в котле составит
Rжидк = 75602378100 = 31,4.
Общее количество SO2, уходящего в регенерационную систему, равно 91 + 332 = 423 кг/т целлюлозы.
Процент регенерации SO2 (по отношению к количеству SO2 в варочной кислоте)
RSO2 = 605423100 = 70.
Общий расход SO2 на варку (химические реакции плюс потери в конечном щелоке) составит 162 + 20 = 182 кг/т целлюлозы, что эквивалентно 91 кг серы на 1 т целлюлозы.
23
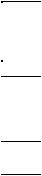
|
|
|
Таблица |
1 . 5 |
|
Суммарный баланс сульфитной варки (приход) |
|
||||
|
|
|
|
|
|
Вещества |
Со |
Скислотойи |
Сконденса- |
Отхими- |
|
перепускной |
ческих |
Всего |
|||
|
щепой |
жидкостью |
томпара |
реакций |
|
|
|
|
|
||
Вода(ипар), л(кг) |
1200 |
7560 |
180 |
– |
8940 |
Древесина(целлюлоза), кг |
1800 |
– |
– |
– |
1800 |
Органическиевещества, кг: |
|
|
|
|
|
газообразныеилетучие |
– |
– |
– |
72 |
72 |
растворенные |
– |
190 |
– |
848 |
1038 |
SO2 |
– |
605 |
– |
– |
605 |
Na2O |
– |
68,0 |
– |
– |
68,0 |
Таблица 1 . 6
Суммарный баланс сульфитной варки (расход)
|
Сосдувоч- |
Сосду- |
Нахи- |
Свыду- |
Оста- |
|
Вещества |
нойипе- |
миче- |
Всего |
|||
репускной |
вочными |
ские |
вочными |
лось |
||
|
газами |
газами |
всцеже |
|
||
|
жидкостью |
реакции |
|
|||
Вода(ипар), л(кг) |
2240 |
138 |
– |
445 |
6117 |
8940 |
Древесина(целлюлоза), кг |
– |
– |
920 |
– |
880 |
1800 |
Органическиевещества, кг: |
|
|
|
|
|
|
газообразныеилетучие |
– |
72 |
– |
– |
– |
72 |
растворенные |
190 |
– |
– |
– |
848 |
1038 |
SO2 |
91 |
332 |
162 |
10 |
10 |
605 |
Na2O |
7,1 |
– |
54,2 |
– |
6,7 |
68,0 |
Направив на улавливание 10 кг SO2, выделяющегося из сцежи с парами вскипания, можно уменьшить расход серы до 86 кг/т целлюлозы.
24
2. МАТЕРИАЛЬНЫЙ БАЛАНС ПЕРИОДИЧЕСКОЙ ВАРКИ СУЛЬФАТНОЙ ЦЕЛЛЮЛОЗЫ
Приведем пример расчета материального баланса варки целлюлозы марки НС-1 в варочных котлах периодического действия вместимостью 180 м3 с непрямым обогревом и принудительной циркуляцией щелока [3]. Варочный цех входит в состав целлюлозного завода, вырабатывающего 250 000 т товарной целлюлозы в год. Схема варочного цеха изображена на рис. 2.1. Исходные данные для расчета приведены в табл. 2.1 [3, 5, 6].
Расчеты ведутся на 1 т воздушно-сухой целлюлозы по варке с влажностью 12 % (коэффициент сухости 0,88), независимо от фактической влажности вырабатываемой целлюлозы.
Таблица 2 . 1
Исходные данные для расчета материального баланса периодической сульфатной варки
Наименованиепоказателя |
Величина |
|
показателя |
||
|
||
БазиснаяплотностьдревесиныАзо, кг/м3 |
425 |
|
Влажностьдревесины(относительная), % |
35 |
|
Выходцеллюлозыиздревесины, % |
48 |
|
Степеньобъемногонаполнениякотлащепойg |
0,43 |
|
Расходпарана уплотнениещепы, тна1 тв.с. целлюлозы |
0,20 |
|
Расходактивнойщелочи, кгNa2Она1 тцеллюлозы |
315 |
|
Плотностьоборотногочерногощелока(при15 °С), кг/дм3 |
1,09 |
|
Количествожидкостив1 м3 котла, дм3 |
550 |
|
Параметрыбелогощелока: |
|
|
– концентрацияактивнойщелочи, кгNa2О/м3 |
110 |
|
– степеньсульфидности |
0,25 |
|
– степенькаустизации |
0,88 |
|
– степеньвосстановления |
0,95 |
|
Температураварки, оС |
172 |
|
Концентрацияволокнистоймассы, направляемойизвыдувно- |
4,0 |
|
горезервуаравпромывнойотдел, % |
||
|
25
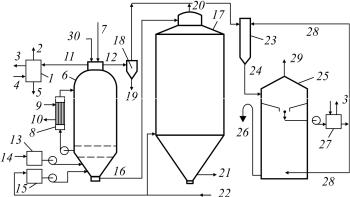
Рис. 2.1. Технологическая схема варочного цеха:
1 – терпентинный конденсатор; 2 – несконденсировавшиеся газы; 3 – горячая вода; 4 – чистая холодная вода; 5 – конденсат (сырой скипидар и вода) во флорентину; 6 – варочный котел; 7 – щепа;
8 – теплообменник (подогреватель щелока); 9 – греющий водяной пар; 10 – конденсат водяного пара; 11 – терпентинная сдувка; 12 – конечная сдувка; 13 – бак-мерник белого щелока; 16 – выгружаемая из котла волокнистая масса; 17 – выдувной резервуар; 18 – циклон-ловушка; 19 – волокна и щелок в бак черного щелока; 20 – пары самовскипания
щелока; 21 – волокнистая масса в промывной отдел; 22 – черный щелок из промывного отдела; 23 – струйный конденсатор; 24 – горячий конденсатор; 25 – бак-аккумулятор; 26 – грязный конденсат в сток; 27 – спиральный теплообменник; 28 – охлажденный конденсат;
29 – вентиляция (в атмосферу или на газоочистную установку); 30 – пар для уплотнения щепы
Базисную плотность древесины и другие исходные данные можно выбирать по справочным материалам (например, в [5] или в табл. П2 и П3 приложения).
Температурно-временной график варки приведен на рис. 2.2. На этом же рисунке изображена примерная кривая выхода целлюлозыиздревесины, соответствующая условиямварки.
Для удобства расчета процесс варки разделен на стадии:
–загрузка щепы и заливка щелоков;
–заварка (подъем температуры и терпентинная сдувка);
26
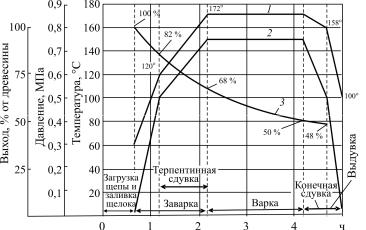
–варка (стоянка на конечной температуре);
–спуск давления (конечная сдувка);
–выдувка.
В расчетах приняты следующие обозначения:
Х– количество твердых веществ (древесины, целлюлозы)
впотоке, тонны абсолютного сухого вещества на 1 т воздушносухой (0,88 т абсолютно сухой) целлюлозы;
Y – количество жидкости (воды) в потоке, т/т;
Z – количество растворенных органических веществ, т/т;
N – количество содопродуктов в пересчете на Na2O, т/т; с – концентрация (массовая доля) вещества.
Рис. 2.2. Температурно-временной график периодической сульфатной варки [3, 5]: 1 – температура; 2 – давление; 3 – выход целлюлозы из древесины
На рис. 2.3 изображена расчетная (для наглядности «расчлененная» на узлы) технологическая схема цеха. Каждому узлу присвоен номер (из одного числа), который далее используется для обозначения (идентификации) материальных потоков в виде индексов из двух чисел, разделенных точкой. Первое из этих чисел является номером устройства, из которого выходит поток,
27
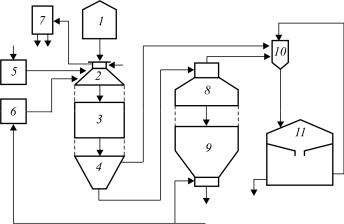
второе – номером устройства, в который входит поток. Цифра 0 присвоена устройствам за пределами схемы. Обращаем внимание на то, что номера устройств и материальных потоков на этом рисунке иные, чем на рис. 2.1, они используются только в пределах текущего подраздела.
Рис. 2.3. Расчетная схема варочного цеха [3]: Устройства: 1 – складщепы; 2 → 3 → 4 – варочныйкотел; 5 – бакбелогощелока; 6 – бак-мерникчерногощелока; 7 – терпентинныйконденсатор; 8 → 9 – выдувнойрезервуар; 10 – струйныйконденсатор; 11 – бак-аккумулятор
Потоки: 0.2 – пар для уплотнения щепы; 0.6, 0.9 – черный щелок из промывного отдела; 1.2 – щепа; 4.8 – выгружаемая из котла волокнистая масса; 4.10 – конечная сдувка; 5.2 – белый щелок из цеха каустизации; 6.2 – черный щелок; 8.10 – пары самовскипания щелока;
9.0– волокнистаямассавпромывнойотдел; 10.11 – горячийконденсат;
11.0– грязный конденсат в сток; 11.10 – охлажденный конденсат
Загрузка щепы и заливка щелоков
Абсолютную влажность древесины с принятой относительной влажностью 35 % (см. табл. 2.1) вычисляют по формуле
W |
= |
|
100Wотн |
= |
100 35 |
= 53,8 %. |
|
100 − W |
100 − 35 |
||||||
абс |
|
|
|
||||
|
|
|
отн |
|
|
|
28
Так как Waбc > 30 %, содержание абсолютно сухой древесины в 1 м3 плотной древесины может быть принято равным базисной плотности А30, т.е. 425 кг/м3.
Количество а.с. древесины, загружаемой в 1 м3 котла (при степени объемного наполнения котла щепой g = 0,43),
А30 · g = 425 · 0,43 = 182,75 кг.
Выход целлюлозы из 1 м3 котла (при принятом выходе целлюлозы из древесины 48 %):
а.с.
182,75 · 0,48 = 87,72 кг;
в.с.
87,72 : 0,88 = 99,68 кг.
Для получения 1 т в.с. целлюлозы Х4.8 в котел нужно загрузить а.с. древесины
Х1.2 = 880 : 0,48 = 1833 кг;
с этой древесиной поступит воды в виде влаги
|
Wотн |
35 |
|
|
|
Y1.2 = X1.2 |
|
= 1833 |
|
|
= 987,0 кг; |
100 − W |
100 − |
35 |
|||
|
отн |
|
|
|
|
на 1 м3 котла поступит воды со щепой
182,75 |
35 |
|
= 98,4 |
кг(дм3 ). |
|||
|
|
|
|
||||
100 |
− |
35 |
|||||
|
|
|
Расход пара на уплотнение щепы принят 0,20 т/т целлюлозы, т.е.
99,68 · 0,20 = 19,94 кг (дм3)
на 1 м3 котла. Можно принять, что 90 % этого пара конденсируется и остается в котле, что составит
19,94 · 0,90 = 17,9 кг
29
на 1 м3 котла, или
Y0.2 =17,9 99,681000 = 179,6 кг(дм3 )
на 1 т целлюлозы.
Общее количество воды, поступающей в котел со щепой и конденсатом пара на 1 т целлюлозы,
Y1.2 + Y0.2 = 987,0 + 179,6 = 1166,6 дм3;
объем щелоков, закачиваемых на 1 м3 котла (см. табл. 2.1), 550 – 98,4 – 17,9 = 433,7 дм3,
или на 1 т целлюлозы
433,7 1000 = 4351 дм3 ,
99,68
в том числе белого щелока (при расходе активной щелочи 315 кг/т и ее концентрации 110 кг/м3, см. табл. 2.1):
= 315 1000 = 3 Y5.2 110 2864 дм ,
что составляет
2864 100 = 65,8 %
4351
от общего объема щелоков; черного щелока
Y6.2 = 4351 – 2864 =1487 дм3,
что составляет
100 – 65,8 = 34,2 %
от общего объема щелоков.
Расчет состава белого щелока приведен в табл. 2.2.
30