
книги / Технологические расчеты по получению различных видов целлюлозы
..pdfи растворенных сухих веществ
R7.2+7.0 = 1580,0 – 20,0 = 1560,0 кг;
концентрация щелока становится равной
с7.2 = с7.0 = |
|
1560,0 100 |
=19,9 %. |
|
|
||
1560,0 + 6272,3 |
Теперь принятая концентрация используемого щелока точно соответствует расчетной концентрации, в дополнительных циклах итерациинетнеобходимости.
За вычетом веществ, возвращаемых в варочный котел, в систему регенерацииотбираетсякрепкийчерный щелоквколичестве:
– воды
Y7.0 = Y7.2+7.0 – Y7.2 = 6272,3 – 1028,5 = 5243,8 кг;
– растворенных сухих веществ
R7.0 = R7.2+7.0 – R7.2 = 1560,0 – 255,5 = 1304,5 кг;
– всего щелока
Y7.0 + R7.0 = 5243,8 + 1304,5 = 6548,3 кг.
Доля всего Na2O в сухом остатке щелока после варки составляет 0,2256 (см. расчет перед табл. 3.4). Можно принять, что такую же долю составляет Na2O в сухом остатке щелоков, отбираемых в циклоны (R4.6) и на регенерацию (R7.0) и щелоков зоны промывки (R4.5 и R5.4) соответственно:
1580,0 · 0,2256 = 356,5 кг;
1304,5 · 0,2256 = 294,3 кг;
832,1 · 0,2256 = 187,7 кг;
799,8 · 0,2256 = 180,4 кг.
Суммарный материальный баланс зоны отбора щелока приведен в табл. 3.5.
61

Таблица 3 . 5
Материальный баланс зоны отбора щелока, кг/т
|
|
Приход |
|
|
Расход |
|
Вещество |
|
сослабым |
|
сотоб- |
перешло |
|
иззоны |
щелоком |
итого |
ранным |
итого |
||
|
варки |
иззоны |
крепким |
взону |
||
|
|
промывки |
|
|||
|
|
промывки |
|
щелоком |
|
|
|
|
|
|
|
||
Вода |
4824,3 |
7197,8 |
12 022,1 |
7197,8 |
4824,3 |
12 022,1 |
Сухиевещества |
1612,3 |
799,8 |
2412,1 |
1580,0 |
832,1 |
2412,1 |
вщелоке |
|
|
|
|
|
|
Итогощелока |
6436,6 |
7997,6 |
14 434,2 |
8777,8 |
5656,4 |
14 434,2 |
ВсегоNa2O |
363,8 |
180,4 |
544,2 |
356,5 |
187,7 |
544,2 |
Целлюлоза |
880,0 |
– |
880,0 |
– |
880,0 |
880,0 |
Промывка и выдувка массы
Количество жидкости (разбавленного щелока), выгружаемой из котла при концентрации волокнистой массы 10 %,
880(100 − 10) = 7920,0 кг. 10
Взону промывки подается слабый щелок из диффузора
вколичестве (см. табл. 3.5)
7997,6 + 7920,0 – 5656,4 = 10 261,2 кг.
При содержании в нем 4 % растворенных веществ (см. табл. 3.1) количество последних составит
R9.5 = 10 261,2 · 0,04 = 410,4 кг,
в том числе всего Na2O
410,4 · 0,2256 = 92,6 кг,
количество воды
Y9.5 = 10 261,2 – 410,4 = 9850,8 кг.
62
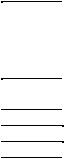
Количество растворенных веществ в выгружаемой из котла волокнистой массе
R5.9 = R4.5 + R9.5 – R5.4 = 832,1 + 410,4 – 799,8 = 442,7 кг,
в том числе всего Na2O
442,7 · 0,2256 = 99,9 кг;
количество воды
Y5.9 = 7920,0 – 442,7 = 7477,3 кг;
концентрация растворенных веществ
с5.9 = |
R5.9 100 |
= |
442,7 100 |
= 5,4 %. |
|
R |
+ Y |
442,7 + 7477,3 |
|||
|
5.9 |
5.9 |
|
|
|
Материальный баланс зоны промывки и выдувки отражен в табл. 3.6, сводный материальный баланс котла – в табл. 3.7.
Таблица 3 . 6
Материальный баланс зоны горячей промывки и выдувки, кг/т
|
|
Приход |
|
|
Расход |
|
Вещество |
иззоны |
сослабым |
|
сослабым |
выдува- |
|
отбора |
итого |
итого |
||||
|
крепкого |
щелокомиз |
щелокомв |
етсяиз |
||
|
диффузора |
|
зону отбора |
котла |
|
|
|
щелока |
|
|
|
|
|
Вода |
4824,3 |
9850,8 |
14675,1 |
7197,8 |
7477,3 |
14675,1 |
Сухиевещества |
832,1 |
410,4 |
1242,5 |
799,8 |
442,7 |
1242,5 |
вщелоке |
|
|
|
|
|
|
Итогощелока |
5656,4 |
10261,2 |
15917,6 |
7997,6 |
7920,0 |
15917,6 |
ВсегоNa2O |
187,7 |
92,6 |
280,3 |
180,4 |
99,9 |
280,3 |
Целлюлоза |
880,0 |
– |
880,0 |
– |
880,0 |
880,0 |
63

Таблица 3 . 7
Сводный материальный баланс варки, кг/т
Статьибаланса |
|
Вода |
Твердыеираство- |
|
ренныевещества |
||
|
|
|
|
|
Приход |
|
|
Древесинаизпропарочнойцистерны |
|
1323,0 |
1829,0 |
Белыйщелок |
|
2472,8 |
407,8 |
Черныйщелокизнижнегоциклона |
|
1028,5 |
255,5 |
Слабыйщелокиздиффузора |
|
9850,8 |
410,4 |
Всегоприход |
|
14 675,1 |
2902,7 |
|
Расход |
|
|
Черныйщелоквверхнийциклон |
|
7197,8 |
1580,0 |
Массавдиффузор |
|
7477,3 |
880,0 |
|
442,7 |
||
|
|
|
|
Всегорасход |
|
14 675,1 |
2902,7 |
Потери сухих (растворенных) веществ с промытой массой составляют
R5.9 – R9.5 = 442,7 – 410,4 = 32,3 кг,
в том числе содопродуктов (всего Na2O)
32,3 · 0,2256 = 7,3 кг.
При принятой концентрации массы после домывки в диффузоре 10 % (см. табл. 3.1) в бассейн промытой массы (под диффузором) поступает волокнистой суспензии
880,0(100 − 10) = 7920,0 кг, 10
в том числе воды
Y9.10 = 7920,0 – 880,0 – 32,3 = 7007,7 кг.
Расход свежей воды на промывку в диффузоре
Y0.9 = Y9.10 + Y9.5 – Y5.9 = 7007,7 + 9850,8 – 7477,3 = 9381,2 кг.
64
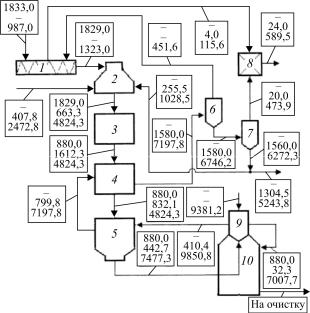
Рис. 3.4. Сводный материальный баланс варочного цеха, кг/т целлюлозы (первое число – твердые вещества, Х; второе – растворенные и летучие вещества, Z + N; третье – вода и водяной пар)
Сводный материальный баланс варочного цеха отражен на рис. 3.4.
4. БИСУЛЬФИТНАЯ ПЕРИОДИЧЕСКАЯ ВАРКА
4.1. Материальный баланс варки
Приведем пример расчета материального баланса бисульфитной варки в варочных котлах периодического действия с непрямым обогревом и принудительной циркуляцией раствора. Варочный цех входит в состав целлюлозного завода, вырабатывающего 150 000 т в год целлюлозы высокого выхода. Дре-
65
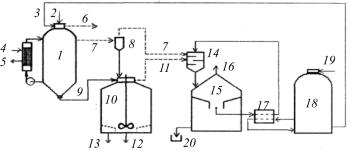
весное сырье – сухостойная лиственница (пораженная шелкопрядом). Основание магниевое. Подъемные сдувки и отбор щелока из котла в ходе варки не производятся.
Принципиальная схема варочного цеха изображена на рис. 4.1 [3]. Она включает варочные котлы периодического действия, вертикальные цилиндрические сцежи для приема массы из котлов и систему утилизации тепла, в которой пар, выделяющийся при конечной сдувке и выдувке, используется для нагревания бисульфитного варочного раствора.
Рис. 4.1. Принципиальная схема варочного цеха: 1 – варочный котел; 2 – древесина (щепа); 3 – горячий бисульфитный варочный раствор; 4 – греющий водяной пар; 5 – конденсат водяного пара; 6 – газовая сдувка (в абсорбер кислотного цеха); 7 – конечная сдувка; 8 – ловушка переброса; 9 – выгружаемая из котла масса (целлюлоза и щелок); 10 – вертикальная цилиндрическая сцежа для выдувки; 11 – пары вскипания при выдувке массы; 12 – целлюлоза и щелок в промывной отдел; 13 – отбор крепкого щелока в цех регенерации серы и магния; 14 – конденсатор смешения; 15 – бак-аккумулятор горячей воды; 16 – сернистый газ в абсорбер кислотного цеха: 17 – теплообменник; 18 – цистерна горячей варочной кислоты; 19 – бисульфитный раствор из кислотного цеха; 20 – цеховая канализация
Исходные данные для расчета приведены в табл. 4.1 [1–4]. Расчеты ведутся на 1 т в.с. целлюлозы с влажностью 12 % (коэффициент сухости 0,88), независимо от фактической влажности вырабатываемой целлюлозы.
66
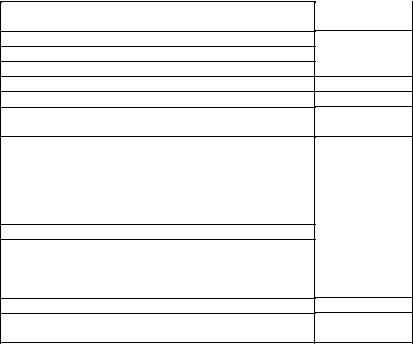
Таблица 4 . 1
Исходные данные для расчета материального баланса периодической бисульфитной варки
Наименованиепоказателей
Породадревесины
БазиснаяплотностьдревесиныА30, кг/м3
Влажностьдревесины(относительная), %
Выходцеллюлозыиздревесины, %
Степеньобъемногонаполнениякотлащепойg, м3/м3
Расходбисульфитамагниянахимическиереакции, кгSO2 на1 та.с. древесины
Температура, °С:
–варки
–воды, поступающейвструйныйконденсатор
–воды, покидающейструйныйконденсатор
–сточнойводыизбака-аккумулятора
–бисульфитногораствораизкислотногоцеха
Титрщелокавконцеварки, весьSO2, г/дм3
Количествогазаипара, удаляемыхсгазовойсдувкойвконце варки, кгна1 тцеллюлозы:
–SO2
–Н2О
Давлениевкотлепослеконечнойсдувки, МПа
Концентрацияволокнистойсуспензиивсцежепослеотбора отекающегощелока, %
Величина
показателя
Лиственница
482
15
52
0,36
160
160
40
90
40
20
6,0
30
6
0,2
16
В расчетах приняты следующие обозначения:
Основные
X – количество твердых веществ (древесины, целлюлозы) в потоке, килограммы а.с. вещества на 1 т воздушно-сухой (880 кг абсолютно сухой) целлюлозы;
Y– количество жидкости (воды) в потоке, кг/т;
Z– количество растворенных органических веществ, кг/т;
S– количество диоксида серы, бисульфита магния, едини-
цы SO2, кг/т;
с – концентрация (массовая доля) вещества;
67
t – температура, °С;
q – теплоемкость вещества;
j – теплота парообразования воды; G – масса вещества;
Q – количество тепла;
Подстрочные индексы
ц – целлюлоза; щ – щелок;
р – растворенные вещества; п – водяной пар;
н, к – начальные и конечные значения параметров. Полный оборот варочного котла складывается из следую-
щих технологических операций (правая колонка чисел – про-
должительность операций, минуты) [2–4]: |
|
|
– загрузка щепы и варочного раствора |
............................ |
85; |
– подъем температуры до 160 °С ................................... |
|
240; |
– варка при температуре 160 °С..................................... |
|
180; |
– конечная сдувка.............................................................. |
|
30; |
– опорожнение котла (выдувка) ....................................... |
|
50; |
– осмотр и подготовка котла к следующей ...........варке |
15; |
|
– полный оборот котла................................... |
600 мин (10 ч). |
Для удобства расчета процесс варки разделен на стадии:
–загрузка и варка;
–конечная сдувка и выдувка.
На рис. 4.2 изображена расчетная технологическая схема цеха. Каждому узлу присвоен номер (из одного числа), который далее используется для обозначения (идентификации) материальных потоков в виде индексов из двух чисел, разделенных точкой. Первое из этих чисел является номером устройства, из которого выходит поток, второе – номером устройства, в который входит поток. Цифра 0 присвоена устройствам за пределами схемы. Обращаем внимание на то, что номера устройств и материальных потоков на этом рисунке иные, чем на рис. 4.1.
68
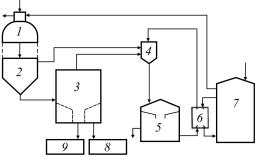
Рис. 4.2. Расчетная схема варочного цеха. Устройства: 1→2 – варочный котел; 3 – сцежа; 4 – ловушка
переброса; 5 – бак-аккумулятор горячей воды; 6 – теплообменник; 7 – цистерна горячей варочной кислоты.
Стадии варки: 1 – загрузка и варка; 2 – конечная сдувка и выдувка. Потоки: 0.1 – щепа; 0.7 – бисульфитный раствор из кислотного цеха;
1.0– газовая сдувка; 2.3 – выдуваемая масса; 2.4 – конечная сдувка;
3.4– пары вскипания при выдувке массы; 3.8 – отбор крепкого щелока в цех регенерации серы и магния; 3.9 – целлюлоза и щелок в промывной отдел; 4.5 – горячий конденсат; 5.0 – сброс воды в цеховую канализацию; 5.6, 6.4 – циркулирующий конденсат;
7.1– горячий бисульфитный раствор
Результаты вычислений целесообразно наносить на схему по мере выполнения расчетов аналогично тому, как представлено на рис. 4.2. Это значительно облегчает выполнение и контроль правильности вычислений.
Загрузка и варка
Базисная плотность лиственничной древесины A30 = 482 кг/м3 (см. табл. П2 приложения).
Так как в исходных данных указана относительная влажность древесины (как это принято в практике предприятий) Woтн = 15 %, следует вычислить абсолютную влажность Wa6c:
W |
= |
|
100 Wотн |
= |
100 15 |
= 17,6 %. |
|
|
|
100 − 15 |
|||||
абс |
|
100 |
− W |
|
|
||
|
|
|
|
отн |
|
|
|
69
Вычислим плотность древесины А при этой абсолютной влажности [3] (при Wa6c < 308):
А= А30 + 0,808 (30 – Waбc) + 0,0396 (30 – Wабс)2 =
=482 + 0,808 (30 – 17,6) + 0,0396 (30 – 1 7,6)2 = 498 кг/м3.
Это означает, что в 1 м3 плотной древесины лиственницы с относительной влажностью 15 % содержится 498 кг абсолютно сухой плотной древесины.
Количество а.с. древесины в виде щепы, загружаемой в 1 м3 варочного котла без принудительного уплотнения (из-за высокой плотности лиственничной древесины), при степени объемного наполнения котла щепой g = 0,36 (см. табл. 4.1)
А · g = 498 · 0,36 = 179,3 кг.
Выход целлюлозы из 1 м3 котла (при принятом выходе целлюлозы из древесины 52,0 %, см. табл. 4.1):
– абсолютно сухой
179,3 52,0 = 93,2 кг;
100
– воздушно сухой
93,2 : 0,88 = 105,9 кг.
Для получения 1 т в.с. целлюлозы (Х2.3 = 880 кг а.с. целлюлозы) с выходом 52,0 % в котел нужно загрузить а.с. древесины
X0.1 = 880 100 = 1692,3 кг. 52,0
С этой древесиной поступит воды в виде влаги: на 1 т целлюлозы
Y0.1 = |
|
X0.1Wотн |
= |
1692,3 15 |
= 298,6 кг (0,2986 м3 ); |
|
|
|
100 − 15 |
||||
|
100 |
− W |
|
|
||
|
|
|
отн |
|
|
|
70