
книги / Управление качеством технологии селективного лазерного спекания
..pdfPolyjet RP. Хирургический план, включающий в себя подбор правильного имплантата, предварительное формирование имплантата и решение положения фиксации определяется путем физического моделирования с использованием физической модели. Для изучения применимости и эффективности технологии хирургического планирования были проведены два тематических исследования – дистальный оскольчатый перелом большеберцовой кости и перелом крыла подвздошной кости таза. Результаты проведенного исследования показали, что РП и РЭ могут применяться не только для ортопедического хирургического планирования, но и для создания эффективного хирургического инструмента.
Имеется положительный опыт использования технологий для ремонта дорогостоящих изделий, например рабочих органов турбин ГТД, валов и т.д., а также для нанесения защитных и износостойких покрытий.
Институт лазерных и сварочных технологий (ИЛИСТ) в Санкт-Петербурге, ФГУП «ВИАМ» в Москве пользуются аддитивными технологиями изготовления из отечественных порошков стали и никеля деталей авиадвигателей.
Среди многочисленных методов аддитивных технологий для восстановления функциональных покрытий наиболее перспективным является метод коаксиальной лазерной наплавки (преимущества: получение композитных покрытий из разнообразных материалов, минимальное термическое воздействие на подложку, произвольная форма покрытия).
Уже сегодня АТ движутся в направлении создания гибких, прочных, эластичных материалов с необычными свойствами, при этом с весьма малым весом, что является огромным преимуществом в области развития материалов и технологий во всем мире. Процесс выращивания не дает вредных выбросов в атмосферу, поэтому он относится к «зеленым технологиям». Также АТ имеют ряд экологических преимуществ, в том числе отсутствие очистных сооружений и места складирования отходов, выпуск эко-
11
логически чистой продукции с низким уровнем энергопотребления при ее производстве и эксплуатации,
Это создает уникальное преимущество для предприятия, формирует общественно благоприятный имидж.
1.2. Получение заготовок с использованием технологии селективного лазерного спекания
Селективное лазерное спекание – это технология аддитивного производства, которая использует мощный лазер для спекания мелких частиц порошка в твердую структуру на основе 3D-модели.
Вотличие от быстрого прототипирования селективное лазерное спекание имеет целью изготовление продукции для более длительного пользования. Аддитивное производство сплавления порошкового слоя на основе лазера или технология трехмерной печати вызывает огромный интерес благодаря своему контролируемому, цифровому и автоматизированному производственному процессу, который может обеспечить утонченную микроструктуру и превосходную прочность. Однако аддитивное изготовление металлических деталей с удовлетворительной пластичностью и ударной вязкостью представляет собой серьезную проблему.
На ранней стадии СЛС-материалы изготавливались с использованием различных материалов, таких как нейлон, поликарбонат, нейлоново–стеклянный композит, керамику, металлополимерные порошки [6, 7], В дальнейшем были предприняты усилия по изготовлению высокопрочных металлов с использованием порошко-
вых смесей Fe-Cu, WC–CO, TiB2–Ni, TiC–Ni/Co/Mo, Fe3C–Fe и др.
Вэтих порошковых смесях на основе металлов порошки с низкой температурой плавления выступали в качестве связующих.
Суть изготовления деталей по технологиям СЛС заключается в плавлении порошковых частиц лазером и формировании детали слой за слоем согласно текущему сечению CAD-модели.
Наглядная схема процесса СЛС представлена на рис. 1. Лазер расплавляет порошок не только по оси X и Y, но и по
оси Z для создания трехмерной детали. По завершении печати
12
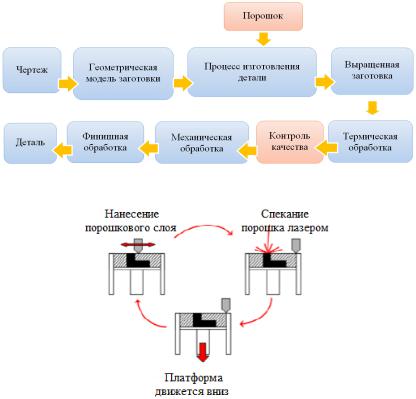
каждого слоя модель опускается на доли миллиметра, и новая порция порошка наносится сверху и подвергается температурному воздействию. В технологии СЛС применяются многокомпонентные порошки или порошковые смеси из разных химических материалов, в отличие от технологии DMLS (прямое металлическое лазерное спекание), где в основном используются однокомпонентные порошки. Схема изготовления изделий методом селективного лазерного спекания представлена на рис. 2. Таким образом, можно создавать детали, отвечающие специальным техническим требованиям геометрии и требуемым характеристикам.
Рис. 1. Схема процесса СЛС
Рис. 2. Изготовление изделий методом селективного лазерного спекания
13
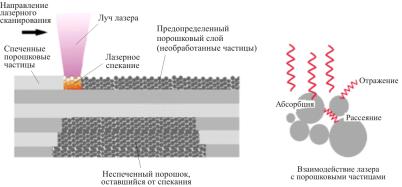
Во время лазерного спекания лазерный луч диаметром 100 мкм локально расплавляет верхний слой порошка на порошковом полотне. Лазер будет частично поглощен металлическими порошковыми частицами, создавая расплавленный слой, который очень быстро застывает (рис. 3). Мощность лазера обычно варьируется от 200 до 1000 Вт [8].
Рис. 3. Взаимодействие лазера с порошковыми частицами
Спекание между частицами порошка осуществляется путем повышения температуры выше температуры плавления. Консолидация достигается путем обработки выбранных участков с использованием тепловой энергии, подаваемой сфокусированным лазерным лучом.
Процесс СЛС характеризуется глубоким взаимодействием между передачей тепла, массы, химическими взаимодействиями, которые приводят к изменениям механических и теплофизических свойств материалов. Консолидация достигается путем обработки выбранных участков тепловой энергией, сфокусированной лазерным лучом [9].
Структура металла изделия получается неравновесной за счет высокоскоростной кристаллизации в процессе затвердевания. Поэтому для получения требуемых свойств конечного изделия требуется проведение термической обработки. Вместе с тем
14
во многих областях применения существует потребность именно в свойствах неравновесного материала [10].
Процессы СЛС/СЛМ, где СЛМ – селективно-лазерное плавление, разделяют на четыре основные категории механизма спекания, а именно твердофазное спекание, химически иницированное спекание, жидкофазное спекание – частичное плавление и полное плавление.
Жидкофазное спекание. Спекание в СЛС в основном происходит в жидком состоянии, когда частицы порошка образуют микроплавкий слой на поверхности, что приводит к снижению вязкости и образованию вогнутого радиального моста между частицами, известного как «шейка», из-за реакции материала на снижение его поверхностной энергии. В случае порошков с покрытием целью лазера является расплавление поверхностного покрытия, которое будет действовать как связующее.
Твердофазное спекание. Твердофазное спекание – это термический процесс, протекающий при температурах спекания 0,6–0,9 °C, температуры плавления порошка однокомпонентной системы или основного материала композиции. Уплотнение при нагреве в основном происходит за счет объемной деформации частиц, осуществляемой путем объемной самодиффузии атомов. Она включает в себя формирование «шейки» между соседними частицами порошка. Основной движущей силой спекания является снижение свободной энергии, когда частицы растут вместе. Твердофазное спекание также является способствующим фактором, хотя и с гораздо меньшим влиянием, и происходит при температурах ниже температуры плавления материала. Под процессом твердофазного спекания понимают спекание, происходящее без перехода материала в жидкую фазу. Обычно оно осуществляется при температурах ниже температуры плавления вещества исходного порошка. Основной движущей силой этого процесса является снижение свободной энергии для развития связей между частицами спекаемого порошка, что приводит к формированию «шеек» между ними и образованию межчастичных границ. Рост
15
«шеек», который происходит в результате переноса массы порошка в области межчастичного контакта, приводит к формированию порошкового тела с неупорядоченной открытой пористостью. Дальнейшее развитие и образование новых «шеек» приводит к возникновению закрытых пор. При дальнейшем переносе вещества в области межчастичного контакта поры округляются и становятся сферическими.
Химически инициируемое спекание. Этот способ синтеза на подложке осуществляется благодаря запуску управляемых реакций компонентов порошковой смеси друг с другом и/или с атмосферой процесса. Такиереакциизапускаютсявоздействиемтемпературы.
Полное плавление. При полном селективном лазерном плавлении как полимеры, так и металлы могут быть полностью расплавлены лазерным лучом. В последние годы была реализована идея полного плавления металлических порошков, подкрепленная постоянно улучшающимися параметрами процесса (меньшая толщина слоя, меньший размер пятна и т.д.). В результате механические свойства были намного лучше, чем у ранних селективных лазерных спеченных деталей, и сравнимы с объемными свойствами металла.
Механизм спекания в значительной степени влияет на скорость процесса и свойства получаемой детали. При увеличении скорости сканирования лазерного луча можно увеличить скорость процесса диффузии. Лазерная обработка приводит к выравниванию различных кристаллографических направлений, а также постепенному структурному укрупнению [11].
1.3. Требования к материалам, используемым в процессе селективного лазерного спекания
Основным требованием, предъявляемым к материалам данной категории, является сочетание повышенных физикомеханических свойств и экономичности. Правильность выбора материалов прямо зависит от того, насколько верно учтены осо-
16
бенности их применения. Важно иметь подходящий химический состав и необходимые физико-механические свойства.
К физико-механическим свойствам, зависящим от внутренней структурыихимическогосоставаматериала, относятзначения:
•прочности;
•плотности;
•твердости;
•тепло-, электропроводности;
•теплоемкости;
•температуры плавления;
•пластичности/вязкости/упругости;
•хрупкости.
К технологическим свойствам, определяющим степень способности материала поддаваться термомеханической обработке, относят значения:
•деформируемости (ковкости);
•свариваемости;
•обрабатываемости резанием и давлением;
•обрабатываемости термическими способами;
•обрабатываемости методами литья.
К эксплуатационным (служебным) свойствам, востребованным в тех или иных рабочих условиях, относят значения:
•сопротивляемости износу;
•устойчивости к воздействию коррозии;
•устойчивости к температурным факторам (хладоустойчивость, жароустойчивость, жаропрочность и т.п.).
В новых материалах современной техники преобладают состояния, далекие от термодинамического равновесия, которые обеспечивают большое разнообразие свойств, поскольку возрастает число независимыхпараметров, влияющих насостояниесистемы.
В технологии селективного лазерного спекания используются мелкозернистые порошки, которые позже образуют модель с помощью лазера. Материал для селективного лазерного спекания
17
используют в виде порошка. Выбор правильного порошкового материала является наиболее важным фактором технологии селективного лазерного спекания.
Поэтому самым первым этапом на пути к качеству изделий является определение качества порошка.
Порошки должны отвечать следующим требованиям:
•по морфологии;
•гранулометрическому составу;
•фракционному составу;
•технологическим свойствам (текучесть, плотность);
•химическому составу и газовым примесям.
Как правило, в СЛС можно использовать все материалы, которые плавятся под воздействием лазерного луча. Сегодня селективное лазерное спекание позволяет использовать очень широкий спектр материалов в виде порошков, сплавов или смесей. Металлические материалы, используемые в этой технологии, включают: сталь, суперсплавы на никелевой основе, титан и его сплавы, тугоплавкие металлы, никель сплавы с бронзой, металлокерамику, кобальт-хром-молибденовые сплавы, медные сплавы [12].
1.4. Механические явления в твердых телах
Одним из важных требований, предъявляемых к материалам, работающим в электро- и теплоэнергетических установках, в самолето- и ракетостроении, является высокая прочность при повышенных температурах. Иногда к материалам, работающим в мощных реактивных двигателях, наряду с требованием высокой кратковременной прочности предъявляются требования высоких теплопроводности и коррозионной стойкости. Для характеристики жаропрочности используют величины пределов ползучести и длительной прочности. Однако и они не всегда в достаточной степени характеризуют жаропрочность материалов. Иногда для практического использования необходима дополнительная характеристика их коррозионнойиэрозионнойстойкости, атакжетермостойкости.
18
Деформация и разрушение материалов – основные явления, определяющие механическое поведение материалов под действием приложенных сил. Они возникают во взаимодействии с другими явлениями: тепловыми, электрическими, магнитными, химическими и оптическими. На эти эффекты и их взаимодействие влияет структура материала. В металлах при условиях, благоприятствующих ползучести, часть деформации после снятия нагрузки исчезает гораздо медленнее, чем чисто упругая деформация. При циклическом деформировании все виды неупругой деформации приводят к появлению петли гистерезиса на диаграмме деформации. Наличие петли гистерезиса свидетельствует о диссипации энергии.
Больше всего металла расходуется на изготовление конструкций, основное назначение которых – сопротивление деформации. Сопротивление пластической деформации материала, как правило, определяют испытанием на растяжение или на твердость. Для описания результатов испытания на растяжение материала в диаграмму деформации вводят специальные термины: например, предел текучести называют напряжением, которое требуется для создания некоторой заданной пластической деформации (обычно порядка десятых долей процента). Это значение используется в конструкторских расчетах, где требуется, чтобы пластическая деформация по порядку величины не превосходила упругую деформацию. Если нужно определить максимальную несущую способность детали, испытание растяжением продолжают. По мере удлинения образца напряжение, необходимое для его пластического деформирования, также возрастает. При этом площадь поперечного сечения образца уменьшается. В некоторый момент влияние уменьшения перекрывает прирост деформирующего напряжения, и кривая нагрузки проходит через максимум. Если достижение максимальной нагрузки вызвано локальным уменьшением сечения образца (образованием шейки), то, как правило, деформация продолжается дальше, до разрушения. При испытании некоторых материалов нагрузка может увеличиваться и после начала разрушения, где предел прочности является мерой сопротивления деформации.
19
Изменить механические и физические свойства материала без изменения химического состава можно в результате термообработки.
Другие свойства материалов связаны с пластическим разрушением образца при пластическом течении до наступления разрыва. Мерой пластичности материала является относительное уменьшение площади поперечного сечения (в процентах) при разрушении во время испытания на растяжение [13].
Проектировщик опирается на пластичность для ряда аспектов проектирования, включая перераспределение напряжений в предельном состоянии для снижения риска распространения усталостных трещин.
У хрупкого материала поперечное сужение равно нулю. При разрыве оно составляет 100 %. У большинства металлов и сплавов поперечное сужение имеет значение от 30 до 70 %. Но даже в пластичных материалах может наступить разрушение при повторном приложении к нагрузкам, которые при однократном приложении не вызывают макроскопической пластической деформации материала. Разрушение может наступить и после ползучести в результате образования пор в материале (по границам зерен или вблизи включений) и их смыкания. Коррозия – фактор, существенно влияющий на механическое поведение материалов, потому что коррозия и напряжения, действуя совместно, иногда неожиданно приводят к опасному виду разрушения, называемому коррозией под напряжением. Это может вызвать гораздо меньшее образование трещин при статическом и при повторном приложении напряжений, чем при напряжениях, которые приводят к разрушению при отсутствии коррозии. Трение и износ также являются процессами, которые в большой степени зависят от характера поверхности материала, особенно от степени загрязненности и наличия смазки. Хотя повреждения, вызванные износом, не столь заметны, как повреждения, вызванные большой пластической деформацией или разрушением, тем не менее износ и корро-
20