
книги / Управление качеством технологии селективного лазерного спекания
..pdfзия являются первичными источниками выхода из строя большинства машин и конструкций.
1.5. Физико-механические свойства изделий, полученных селективным лазерным спеканием
После процесса СЛС материалы характеризуются анизотропией свойств, повышенной прочностью и пониженной пластичностью из-за наличия остаточных напряжений. Для получения более ровной структуры, повышенной вязкости и пластичности необходимо провести отжиг изделия.
Изделия, изготовленные методом СЛС, прочнее литых на 2–12 %. Прочность изделий обусловлена малым размером зерен и микроструктурных составляющих. Для повышения прочностных свойств металлов и сплавов можно широко изменять свойства изделия, изменяя температурные условия кристаллизации, используя легирование, введение в расплав модификаторов, термоциклирование и т.д. Механические свойства объектов, получаемых методом СЛС, дают возможность использовать их в авиастроении, автомобилестроении, биомедицине [13–15].
В работе [16] представлены исследования структуры и механических свойств изделий, изготовленных методом селективного лазерного спекания порошка стали. Экспериментально исследуются структура и механические свойства образцов из порошка стали 316L, изготовленных методом селективного лазерного спекания. Представлены результаты химического и гранулометрического анализа исходного материала и статических испытаний образцов на растяжение. Установлено, что порошок стали 316L имеет регулярную сферическую форму. Показано, что использование методов деструктивного контроля становится экономически неэффективным из-за высокой стоимости расходуемых материалов, используемых в производстве компонентов для селективного лазерного спекания. Рассмотрена проблема использования компьютерной томографии для исследования компонентов с целью вы-
21
явления внутренних дефектов. Наиболее часто встречающимися дефектами этого порошка являются дефекты спутников и «аморфная» броня. Обнаруженные на поверхности трещины после фрактографических испытаний поры диаметром до 50 мкм, вероятно, связаны с особенностями выбранных условий селективного лазерного спекания. Показано, что компоненты, изготовленные из порошка стали 316L, могут использоваться и при циклических нагрузках, что обусловлено высокой пластичностью материала. Было проведено несколько исследований по оптимизации параметров СЛМ для производства деталей 316L SS. Относительно 316L SS, изготовленных СЛМ (использовались оптимизированные параметры), предыдущие результаты имели в среднем более высокую прочность и более низкую пластичность по сравнению с литыми 316L SS. Нержавеющая сталь пластичная и универсальная. Результаты исследования [16, 17] также показали, что лазерное спекание одновременно повышает и прочность, и пластичность материала.
В работах [18–20] отмечено, что образцы, изготовленные по технологии СЛС, обладают комплексом свойств, к которым относятся низкая плотность, высокая прочность и предельная прочность. Это достигается путем активации и проектирования ее микроструктуры. Прочность на растяжение СЛС-образцов из нержавеющей сталиPH1 можетбытьувеличенана16–40 % соответственно.
Нержавеющая сталь не требует никакой покраски или оцинковки, не нуждается в дополнительной защите. Коррозионностойкая и прочная, она продолжает выглядеть замечательно год за годом, несмотря даже на самое жесткое обращение.
Многие марки нержавеющей стали также содержат никель и молибден и предназначены для специального применения. В работе [21] освещены основные характеристики и металлургические механизмы процесса селективной лазерной плавки. Морфология, микроструктура и элементный состав полученных в результате сканирования треков и образцов определяются с помощью оптического микроскопа, сканирующего электронного микроскопа (СЭМ) и энергодисперсионной рентгеновской спектроскопии соответствен-
22
но. Микроструктура показывает чешуйчатые фигуры сверху, что похоже на процесс сварки. Центральная зона расплавленного следа демонстрирует ячеистую микроструктуру, а краевая зона расплавленного бассейна представляет собой столбчатую структуру, которая обусловлена процессом теплопередачи. Поверхностная морфология части СЛМ в низком увеличении может показать multiвыровненную характеристику, и поверхностная морфология в высоком увеличении может отразить процесс затвердевания и кристаллизации. Микроструктура части СЛМ весьма точна, с множественными кристаллическими направлениями. Распределение элементов однородно, иникакиеагрегацииэлементовненайдены[22–24].
1.6. Организация контроля качества процесса селективного лазерного спекания
Комплексный подход системы управления качеством является основой повышения экономической эффективности предприятий. Чтобы оставаться конкурентоспособным, каждое предприятие нуждается в оценке качества его продукции и услуг для улучшения производства и поддержания его на рынке. Применение методов контроля качества улучшает производственные процессы предприятия, а современное оборудование является эффективным решением различныхзадачконтролякачествавпроцессепроизводства.
Одна из ключевых задач внедрения аддитивных технологий на предприятия – создание системы менеджмента качества.
Основными преимуществами селективного лазерного спекания являются экономия времени и возможность построения геометрий, которые были бы недостижимы с помощью традиционных методов. Селективное лазерное спекание произвело революцию в производстве, предложив большую свободу проектирования 3D-структур, которые могут быть построены непосредственно из исходных порошковбездополнительнойобработки.
Однако основными недостатками методов СЛС/СЛМ являются низкое качество поверхности и точности размеров, а также свойств материала (микроструктура и механическая прочность),
23
которые не отвечают необходимым требованиям для промышленного применения [25, 26].
Неспособность гарантировать качество детали, изготовленной СЛС, упоминается как одна из проблем, сдерживающих полное внедрение процесса изготовления деталей конечного использования. Эти детали должны обладать необходимыми механическими свойствами для конкретных нужд. Для внедрения этой технологии в производства с очень высокими стандартами качества необходимо повысить уровень управления качеством на всех этапах технологической цепочки.
На разных стадиях процесса селективного лазерного спекания существуют свои методы контроля. Чтобы понять, как это происходит, необходимо учитывать, что контроль качества каждой партии материала начинается с доставки (химические свойства, гранулометрический состав) и заканчивается анализом работы. Для достижения определенных параметров в отношении качества необходимо учитывать влияние таких факторов, как мощность лазера, величина пятна, толщина слоя, время воздействия луча лазера, направление треков движения, а также химические и механические свойства (рис. 4).
Для обеспечения высокого качества и высокой точности геометрических размеров изделий необходимо соблюдать следующие условия:
–высокая временная стабильность структуры мощности и режима лазерного излучения;
–высокая точность систем позиционирования и перемещения обрабатываемых деталей и изделий;
–стабильное пространственно-временное распределение теплоносителя на поверхности стекла;
–оптимальный размер лазерного луча и плотность мощности лазерного излучения;
–симметричное распределение термоупругих напряжений;
–оптимальные режимы лазерного термического или механического последующего растрескивания.
24
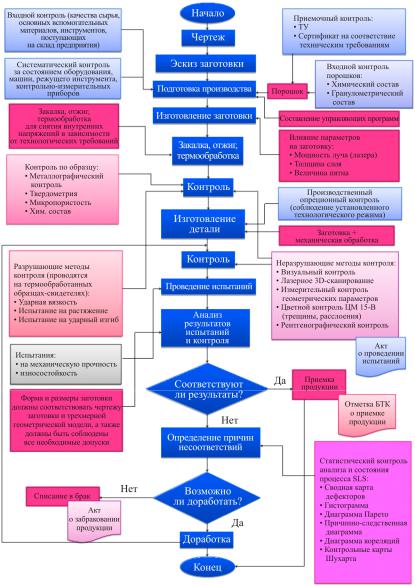
Рис. 4. Порядок контроля качества
25
В работе [26] для устранения этих недостатков были использованы методы постобработки, такие как полировка, покраска, термообработка и инфильтрация в печи. Вместе с тем эти методы постобработки удлиняют производственный цикл и увеличивают стоимость производства.
Чтобы исключить эти этапы последующей обработки, сократить время выполнения заказа и снизить производственные затраты, проводятся исследования соответствующих технологических и материальных параметров, необходимых для получения улучшенной отделкиповерхности, изготовленных деталейметодомСЛС/СЛМ.
Для процесса СЛС/СЛМ существует более 50 различных параметров, которые влияют на конечное качество готовой детали, создавая значительную проблему в понимании физики процесса и разработке эффективной стратегии управления процессом. Существуют основные аспекты процесса изготовления деталей, которые охватывают отдельные модули управления качеством (СМК). В широком смысле эти параметры могут быть отнесены к одной из четырех категорий: 1) параметры лазера и сканирования, 2) свойства порошковых материалов, 3) свойства порошкового слоя и 4) параметры сборки. Они могут быть далее классифицированы на управляемые параметры, которыми можно манипулировать в процессе сборки, и предопределенные параметры, которые определяются в начале сборки и остаются, по существу, заданными в течение всего процесса. Здесь мы определяем переменные как «управляемые», ими можно манипулировать во время типичного построения с текущими технологиями, даже если некоторые переменные, определенные здесь как фиксированные, теоретически также могут быть изменены. Некоторые из параметров являются группами переменных с конкретными значениями релевантности в зависимости от используемой конструкции.
Стоит отметить, что в отношении качества необходимо учитывать выбор исходного материала, его характеристику (химсостав, содержание влаги, старение), а также влияние таких факторов, как мощность лазера, величина пятна, толщина слоя, время
26
воздействия луча лазера, направление треков движения, а также химические и механические свойства. Зная всю цепочку процесса лазерного спекания, изучая механические и физические свойства, можно повысить качество изделий.
На сегодняшний день каждое предприятие промышленного производства имеет оборудование для применения методов неразрушающего контроля (компьютерная томография, рентгеновский контроль, лазерное 3D-сканирование, металлографический контроль, контроль геометрических параметров, твердометрия) [27].
Перед каждым предприятием, которое бы хотело выпускать качественную продукцию, должны стоять следующие задачи:
–проведение научных исследований в области управления качеством;
–реализация программ повышения квалификации для специалистов;
–проведение практических работ для получения результатов эффективности разработанных мер:
–организация специализированных обучений для предпри-
ятий;
–работа на высокотехнологичном оборудовании;
–непрерывный контроль измерительного оборудования, внесенного в госреестр и полностью соответствующего санитарным нормам;
–наличие соответствующих лабораторий;
–штат квалифицированных инженеров;
–организация научных советов по идентификации и оценке качества, локализации дефектов и определению причин их возникновения.
Селективное лазерное спекание позволяет инженерам создавать прототипы деталей в начале цикла проектирования, а затем использовать ту же машину и материал для производства деталей конечного использования. СЛС 3D-печать не требует такой же дорогостоящей и трудоемкой оснастки, как традиционное производство, поэтому прототипы деталей и узлов могут быть протес-
27
тированы и легко модифицированы в течение нескольких дней. Это резко сокращает время разработки продукта.
С учетом низкой стоимости одной детали и долговечности материалов, СЛС-печать является экономичным способом производства сложных, изготовленных на заказ деталей или серии небольших компонентов для конечных продуктов. Во многих случаях лазерное спекание является экономически эффективной альтернативой литью под давлением для ограниченного тиража или изготовления мостов.
1.7. Влияние лазерного излучения на качество изделий
Современные отрасли в основном ориентированы на достижение высокого качества, оперируя понятиями точности габаритной, поверхностной отделки и высокой скорости производства, с повышенной эффективностью, пониженным воздействием на окружающую среду.
Кроме технологических свойств порошковых материалов, используемых в технологии СЛС, на качество конечных изделий влияет большое число параметров самого процесса лазерного спекания. К ним относятся мощность лазера, величина пятна, скорость сканирования, шаг сканирования, толщина слоя, тип защитного газа, а также температура ванны расплава. Многие авторы [28, 29] для сравнения условий лазерной обработки используют единый параметр лазерной энергии ψ (Дж/мм3), который учитывает несколько характеристик лазерной плавки при определении количества затрачиваемой энергии на единицу объема одного слоя порошка и вычисляют его по формуле
ψ = |
P |
, |
(1) |
|
uhd |
||||
|
|
|
где P – мощность лазера, Вт; u – скорость сканирования, мм/c; h – шаг сканирования, мм; d – толщина слоя, мм.
28
Наиболее часто встречающийся структурный дефект при изготовлении изделий – пористость, которая связана с охлаждением капли расплава с высокой скоростью [30].
Влияние скорости сканирования лазерного луча на плотность изделий изучалась на примере сплава AlSi10Mg.
Увеличение скорости сканирования от 100 до 400 мм/c приводит к повышению скорости охлаждения ванны расплава.
Вработе [31] приводится исследование о влиянии скорости сканирования лазерного луча на плотность изделий. Установлено, что в образцах, полученных при низких скоростях сканирования, наблюдается газовая пористость (менее 100 мкм), а с увеличением скорости сканирования наблюдается появление крупных пор (более 100 мкм), которые образовались в результате усадки при кристаллизации ванны расплава. Установлено, что для получения беспористых изделий оптимальной скоростью сканирования лазерного луча является 250 мм/c.
Важным параметром, оказывающим влияние на газовую пористость образцов, является время существования капли расплава –
время между плавлением и затвердеванием Tm. Если параметр Tm имеет маленькое значение, водород, находящийся в ванне расплава, не успевает выйти на поверхность. Поэтому пористость таких образцов будет высокой.
Еще одним способом снижения пористости изделий является подогрев платформы, на которой происходит построение изделия. Это становится возможным за счет снижения скорости кристаллизации ванны расплава. Для успешного слияния как подложка, так и капля металла должны быть в жидком состоянии, когда они вступают в контакт. Это означает, что в случае лазерного спекания на подложку должна быть передана достаточная энергия для локального расплавления подложки, с одной стороны, и для полного расплавления соседнего порошка – с другой.
Вначале каждой сессии лазерный луч должен интенсивно расплавлять порошок. Далее при постоянной скорости сканирования вокруг пятна прямого лазерного падения луча развивается ста-
29
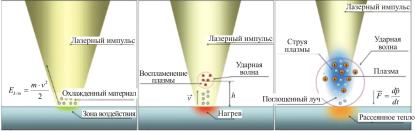
бильный горячий ободок, оплавляющий подложку, и часть порошка плавится в этой области за счет теплопередачи. При этом высокая теплопроводность материала подложки и достаточный контакт порошка с ним способствуют выполнению лазерного спекания с непрерывным излучением. Это влечет за собой высокую плотность порошка, от которой можно ожидать массивного спеченного тела с соответствующей высокой теплопроводностью.
На рис. 5 показана схема поглощения лазерного луча плазмой, которая генерируется в воздухе из-за высокой интенсивности в фокусе луча.
а |
б |
в |
Рис. 5. Схема поглощения лазерного луча плазмой, которая генерируется в воздухе из-за высокой интенсивности в фокусе луча
На рис. 5, а показано относительное поглощение импульсного лазерного излучения с различной средней мощностью. На рис. 5, б лазер выводит наружу силы, показана передача лазера через плазму, и излучение плазмы выходит на поверхность после истекшего времени импульса. Становится очевидным, что быстрый выход совпадает с самым быстрым выходом плазменного излучения (рис. 5, в), что свидетельствует об особенно высоком поглощении плазмы в состоянии опережающего возбуждения. Если плазма генерируется из испаренного материала, то должно происходить усиленное поглощение лазерного луча плазмой и одновременная ударная волна с центром ее над поверхностью нагретого лазером твердого тела.
30