
книги / Управление качеством технологии селективного лазерного спекания
..pdfКроме технологических режимов СЛМ и типа используемого порошка, на пористость конечных изделий влияет тип защитной атмосферы. В работе [32] было исследовано влияние защитного газа на пористость конечных изделий. Установлено, что плотность, прочность и пластичность образцов, полученных в среде азота и аргона, выше, чемуобразцов, изготовленныхвсредегелия.
Важную роль при получении плотных образцов в процессе СЛС играет сплавление соседних дорожек сканирования между собой. В работе [33] представлено экспериментальное определение оптимальных режимов получения образцов СЛС – методом порошков с увеличением расстояния между дорожками сканирования от 50 до 250 мкм. Было установлено, что плотность образцов уменьшалась с 98 до 77 %. При достижении расстояния между соседними дорожками 150 мкм появляются зазоры из нерасплавленного порошка. Образование зазоров связано с отсутствием перекрытия соседних дорожек. Таким образом, для получения образцов с высокой плотностью расстояние между дорожками сканирования должно быть не менее 100 мкм, что обеспечит полное расплавление порошковогоматериалаиоптимальноеперекрытиесоседних слоев.
В процессе СЛС скорость кристаллизации ванны расплава достигает 3,0·106 °C/c. Высокая скорость охлаждения приводит к возникновению остаточных напряжений. Для снятия внутренних напряжений применяют отжиг. Однако во время отжига может происходить существенное изменение микроструктуры. В работе [34] исследовались влияние температуры отжига на механические свойства и уровень остаточных напряжений образцов, полученных из порошка сплава Al-12Si. Показано, что повышение температуры отжига до 723 K приводит к увеличению относительного удлинения от 2 до 12 % и снижению предела текучести с 260 до 95 МПа. Изменение механических свойств возникает в результате изменения микроструктуры образцов в процессе термической обработки.
Термическое воздействие лазерного излучения на порошковый материал оказывает значительное влияние на качество изде-
31
лий и сопровождается достаточно сложными и разнообразными по своей природе физическими явлениями. Качественные изделия можно получить только в узком диапазоне режимов [35]. В большинстве случаев для улучшения качества спеченных изделий используют последующую обработку (постобработку). Применение отжига в качестве постобработки изделий, изготовленных СЛМ, целесообразно, если необходимо получить определенный комплекс механических свойств. В работе [36] изучалось влияние времени отжига на уровень механических свойств и установлено, что методом СЛМ с применением последующей термической обработки возможно получение ультратонкой структуры. Но методы постобработки не позволяют управлять геометрическими и микрогеометрическими параметрами поверхностей, поэтому необходимо добиваться высокого качества спеченного поверхностного слоя технологическими методами [37].
1.8. Качество и экологичность процесса СЛС
Проблема обеспечения экологичности и безопасности технологических процессов является наиболее важной с точки зрения обеспечения их качественных показателей и конкурентоспособности. Учитывая особенности реализации технологических процессов, вопросы экологичности и безопасности, минимизации воздействия на окружающую среду и на человека в основном решаются путем оценки отдельных составляющих этого воздействия.
Процесс СЛС не дает вредных выбросов в атмосферу и является ресурсосберегающей технологией. Эта технология повышает коэффициент использования металла до 97 % [38, 39]. Производство изделий методом СЛС предполагает отсутствие очистных сооружений и образования отходов. Также продукция, изготовленная методом СЛС, характеризуется как экологически чистая, с низким уровнем энергопотребления, без загрязнения окружающей среды.
32
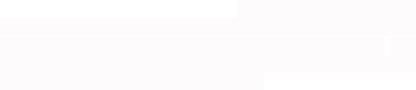
1.9.Технология селективного лазерного спекания
вконцепции бережливого производства
Одним из важнейших и современных направлений промышленного менеджмента является концепция бережливого производства, суть которой в ориентации предприятия на максимально эффективное использование ресурсов, с минимумом брака, отходов, повышением качества продукции [40]. Это позволяет компаниям получать максимальную отдачу от своих ресурсов, повышать производительность и прибыльность. Бережливое производство – это не просто бизнес-стратегия, это школа мысли, которая ценит качество, эффективность и инновационность. Идеологи бережливого производства выделяют восемь видов производственных потерь (перепроизводство, ожидание, лишняя транспортировка или перемещение, излишняя обработка, избыток запасов, лишние движения, дефект и переделка, нереализованный творческий потенциал сотрудников). До того как бизнес начал применять принципы бережливого производства, эффективность и прибыльность часто находились на противоположных концах спектра. Организациям обычно приходилосьвыбиратьмеждудвумясценариями:
•сокращение затрат и снижение эксплуатационных характеристик и качества или
•увеличение расходов для повышения производительности
исохранения качества.
Благодаря концепции бережливого производства компании не нужно выбирать между тем или иным сценарием. Бережливое производство позволяет одновременно оптимизировать свои операционные показатели и повысить прибыльность, т.е. быть эффективными и экономичными. Бережливое производство также может быть гибким, давая организациям конкурентное преимущество, помогая им стать более отзывчивыми и эффективными.
Организации используют широкий спектр концепций бережливогопроизводства, чтобыпомочьимдостичьтаких целей, как:
•устранение или сокращение отходов;
•повышение качества;
33
•сокращение времени выполнения заказа;
•минимизация ненужных расходов.
Поиск технологий, которые не только создают добавленную стоимость, но и снижают при этом потери, является важнейшим направлением концепции бережливого производства. К таковым относятся технологии селективного лазерного спекания [41, 42]. Методы бережливого производства не только могут, но и должны привести к повышению качества процессов и продукции.
34
ГЛАВА 2. ИСХОДНЫЕ МАТЕРИАЛЫ И МЕТОДИКИ ЭКСПЕРИМЕНТАЛЬНЫХ ИССЛЕДОВАНИЙ
2.1. Цель и задачи исследований
Цель: изучение эксплуатационных характеристик для прогнозирования качества изделий, полученных селективным лазерным спеканием, их долговечной работы в узлах конструкций авиационныхдвигателей, реализации бережливогопроизводства.
Для реализации поставленной цели решались следующие задачи:
–Изучить процесс получения изделий из порошковых материалов с металлической матрицей на установке Eosint M280 методом селективного лазерного спекания.
–Изучить аспекты формирования структуры и свойств порошковых и композиционных материалов при изготовлении изделий методом селективного лазерного спекания.
–Разработать программу экспериментальных исследований механических свойств заготовок, полученных селективным лазерным спеканием, из порошковых сплавов PH1.
–Определить характеристики кратковременной прочности и
пластичности (E,σ0,2, σВ, δ, ψ) при комнатной температуре (20 °С) при различных режимах отжига и отпуска образцов, полученных
селективным лазерным спеканием.
–Исследовать влияние режимов термообработки на свойства образцов из нержавеющей стали EOS Stainless Steel РН1, полученных методом селективного лазерного спекания, а также определить оптимальные направления выращивания образцов для испытаний.
–Дать сравнительную характеристику механических свойств сталейPH1 и12Х18Н10Т.
Установить факторы, влияющие на качество заготовки.
35
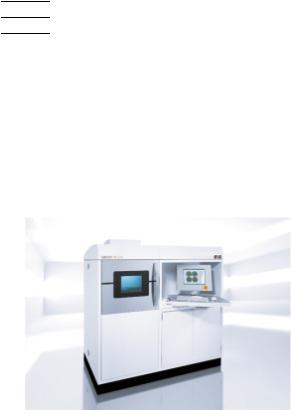
2.2. Методики экспериментальных исследований
2.2.1. Используемые материалы
Для исследования были выбраны импортные порошки фир-
мы EOS-PH1.
Сплав EOS StainlessSteel PH1 – нержавеющая сталь в форме мелкодисперсного порошка (табл. 1).
Таблица 1
Состав материала StainlessSteel PH1
Fe |
Cr |
Ni |
Cu |
Mn |
Si |
Mo |
Nb |
C |
Balance |
14–15,5 |
3,5–5,5 |
2,5–4,5 |
≤ 1 |
≤ 1 |
≤ 0,5 |
0,15–0,45 |
≤ 0,07 |
2.2.2. Методика изготовления образцов из заготовок
Экспериментальные исследования проводились на установке для селективного лазерного спекания фирмы EOSINT M 280 (рис. 6). Установка предназначена для прямого изготовления высококачественных изделий из металла. Может изготавливать изделия со сложной геометрической формой, без применения какой-либо оснастки, используя только данные CAD-модели.
Рис. 6. Установка лазерного спекания фирмы EOSINT M280
36
Высокотехнологичные производственные модульные машины создаются для механически и термически стабильной работы в процессе построения. Ключевыми компонентами машины являются следующие:
Устройство подачи материала или порошковый бункер – подает новый материал для нанесения слоя перед спеканием. В зависимости от функций машины устройства подачи материала могут иметь собственный термоконтроль для подогрева порошка перед подачей его в камеру.
Устройство для нанесения порошка – это лезвие, которое берет материал из устройства подачи порошка и распределяет его равномерно по поршню. Нужно иметь в виду, что любая неровность на наносимом порошке (например, тонкая линия по всему порошку из-за пыли либо мономерного нароста) покажется в конечных изделиях.
Поршень – это действующая часть СЛС-машины. Он состоит из квадратного контейнера с плоским движущимся основанием. Вначале он находится в самом верхнем положении. При нанесении каждого слоя поршень движется постепенно вниз (как правило, прирост 0,1–0,12 мм), так, чтобы устройство для повторного нанесения могло осадить новый материал для спекания. Поршень также нагревается в процессе работы, чтобы снизить любую деформацию из-за охлаждения, и медленно снижает температуру после окончания процесса.
Лазер, или оптический квантовый генератор – это устройство, преобразующее энергию в узконаправленный поток излучения. Устанавливается сверху поршня в лазерное окно, где лазер направляется при помощи гальванометров и зеркал для размещения порошка по соответствующей схеме.
Технологическая камера – закрывает окно с лазером, поршнем и устройством для нанесения порошка. Также она закрывает некоторые датчики температуры и нагреватели для обеспечения стабильной температуры.
37
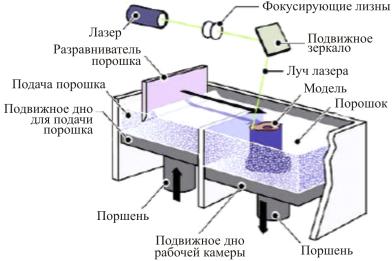
Бункеры – устройства для сбора материала, оставшегося после нанесения порошка. Лишний материал вместе с неспеченным материалом в технологической камере можно смешать с новым порошком и использовать повторно.
Периферийные компоненты – также требуют инертной среды, так как азот используется для удаления кислорода из всей машины. Баки азота поставляются вместе с СЛС-машинами. Также важно оборудование для последующей обработки, включающее вибрационную установку просеивания для регенерации порошка из процесса при разделении деталей и дробеструйный шкаф для полного удаления порошка из спеченных деталей.
Машина начинает работу с полными устройствами подачи порошка и пустым поршнем, и бункером для сбора неспеченного порошка. В фазе нагрева среда наполняется инертным азотом или аргоном, а4–6 ммпорошкананоситсянапоршеньпринагревании[43].
Принцип работы лазерного спекания в технологической камере показан на рис. 7.
Рис. 7. Принцип работы лазерного спекания в технологической камере
38
2.2.3. Анализ гранулометрического состава порошков
Гранулометрический состав порошка сплавов PH1 и In718 определяли методом ситового анализа согласно ГОСТ 18318-94 «Порошки металлические. Определение размера частиц сухим просеиванием» [44] с помощью виброгрохота Anaysette 3 модели
Pro, выпускаемого фирмой Fritsch GmbH, Manufacturers of Laboratory Instruments по стандарту ASTM. C диапазоном измерения от 5 до 63 мкм (ГОСТ 6613) [45]. Аналитические сита с диаметром 200 мм и высотой 50 мм. Плетеная ткань сит и рама изготовлены из нержавеющей стали.
Высокопроизводительный вибрационный грохот ANALYSETTE 3 PRO предназначен для быстрого определения количественного распределения размеров частиц. Электромагнитный привод приводит сита к вертикальной вибрации. При этом рассеиваемый материал периодически подбрасывается с ткани сита и в падении прогоняется через установленные аналитические сита.
2.2.4. Химический анализ
Химический состав определяли методом абсорбционно-спект- рального анализа (ААС) по ГОСТ 12344, ГОСТ 12345, ГОСТ 12354, ГОСТ 12361, ГОСТ 17745 [46–50]. Содержание элемента в пробе определяли с применением экспериментально установленной функциональной зависимости между аналитическим сигналом (оптическая плотность, абсорбция) и концентрацией элемента в образце, которыйнеобходимдляанализа.
ААС представляют собой высокоавтоматизированные устройства, необходимые для обеспечения высокой воспроизводимости измерений, автоматического введения проб, а также регистрации результатов измерений. Суть работы данного прибора заключается в излучении источником света характерной узкой спектральной линии, превращении данного вещества в атомный пар с помощью атомизатора и спектрального прибора, необходимых для выделения данной линии вещества, а также регистратора
39
для фиксирования данных и обработки аналитического сигнала поглощения [51].
2.2.5. Определение плотности
Насыпную плотность определяли для каждой партии в соответствии с ГОСТ 19440-94 «Порошки металлические: Определение насыпной плотности» [52].
В соответствии с требованием ГОСТа насыпная плотность определялась при помощи воронки. С помощью ложки порошок засыпался в воронку до тех пор, пока емкость, расположенная под ней, не была заполнена полностью. Далее массу порошка взвешивали на аналитических весах с точностью до второго знака.
Насыпную плотность вычисляли по формуле
γнас = |
М2 − М1 |
, |
(2) |
|
V |
|
|
где γнас – насыпная плотность, г/см3; М1 – масса емкости, г; М2 – масса емкости с порошком, г; V – объем емкости, см3.
Насыпная масса тем больше, чем крупнее частицы порошка и чем более компактную и правильную форму они имеют. Увеличение содержания тонких фракций уменьшает насыпную массу из-за образования пустот. Однако мелкие фракции, заполняя промежутки между крупнымичастицами, увеличиваютнасыпнуюмассу.
2.2.6. Определение текучести
Текучесть порошка определялась в соответствии с ГОСТ 20899-98 «Порошки металлические: Определение текучести с помощью калиброванной воронки (прибора Холла)» [53].
Для определения текучести использовали конусные воронки с калиброванными отверстиями. Просушенную навеску порошка (50 г) засыпали в воронку диаметром 80 мм и углом конуса 60° с носиком, срезанным под прямым углом на расстоянии 3 мм от конуса воронки. Диаметр выходного отверстия выбирался в зави-
40