
книги / Управление качеством технологии селективного лазерного спекания
..pdf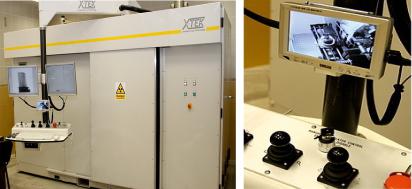
симости от крупности порошка. Выходное отверстие воронки закрывалось специальной заслонкой, а снизу подставляли приемник. После наполнения воронки порцией исследуемого порошка заслонку открывали и одновременно включали секундомер. Время необходимо округлить до 0,1 – это и есть текучесть порошка.
2.2.7. Рентгеновская и компьютерная томография
Исследования посредством рентгеновской и компьютерной томографии проводились на установке XT H 450 LC фирмы Nikon Metrology (рис. 8). Данная установка применялась для обнаружения дефектов в структуре материала, а также для контроля геометрических параметров внутренних полостей детали.
Рис. 8. Установка рентгеновской и компьютерной томографии
2.2.8. Металлографический анализ
Металлографический анализ осуществлялся на сканирующем электронном микроскопе с возможностью локального элементного анализа фирмы TESCAN (MIRA 3 LMH) (рис. 9). Данный прибор применялся для фрактографического исследования изломов образцов после испытаний по определению кратковременных характеристик прочности и пластичности образцов.
41
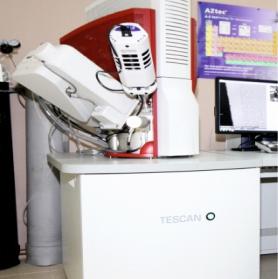
Рис. 9. Сканирующий электронный микроскоп с возможностью локального элементного анализа фирмы TESCAN (MIRA 3 LMH)
2.2.9. Определение твердости
Испытания на твердость проводили по методу Роквелла с помощью твердомера HR-150A в соответствии с ГОСТ 9013 «Металлы. Метод измерения твердости по Роквеллу» [54]. Данный метод состоит во вдавливании алмазного конуса в предварительно зашлифованную поверхность образца. Суть данного метода заключается в определении глубины вдавливания алмазного конуса в исследуемый материал.
2.2.10. Определение пористости
Объемная доля пор определялась с использованием про-
граммы ThixometPro в соответствии с ASTM E1245-03(2016) «Стандартная методика определения содержания включений или компонентов вторичной фазы в металлах методом автоматического анализа изображений» [55] в ячейке размером 1 мм площа-
42
ди шлифа при 100х. Поры выделялись по уровню яркости, определялись их размеры.
2.2.11. Контроль остаточных напряжений
Контроль остаточных напряжений проводили на дифракто-
метре D8 Advance Bruker.
Дифрактограмма показывает распределение пиков определенной формы и интенсивности исходя из энергии специфического излучения конкретной фазы. В связи с этим можно сделать заключение о параметрах пробы [56].
2.2.12. Определение шероховатости
Шероховатость измеряли профилографом-профилометром в соответствии с ГОСТ 19300-86 «Средства измерений шероховатости поверхности профильным методом. Профилографы-профи- лометры контактные. Типы и основные параметры» [57]. Профи- лограф-профилометр – это комбинированный прибор для измерения шероховатости исследуемой поверхности, состоит из профилографа и профилометра.
Профилометр и профилограф относятся к группе контактных методов. Суть метода: игла перемещается по нормали по оцениваемой поверхности, в местах неровностей – колеблется; от иглы идет сигнал на преобразователь, а в это время на электронный усилитель поступает сигнал, который отображается графически. Усиливающиеся колебания вызывают возбуждение ЭДС и малых токов, а затем регистрируются с помощью гальванометра. С помощью этих данных можно судить о характере исследуемой поверхности (высоте микронеровностей) [58].
2.2.13. Испытания на растяжение
Испытания на растяжение проводили на установке LFMZ100 в соответствии с ГОСТ 1497-84 «Металлы. Методы испытаний на растяжение» [59]. Схема испытания приведена на рис. 10.
43
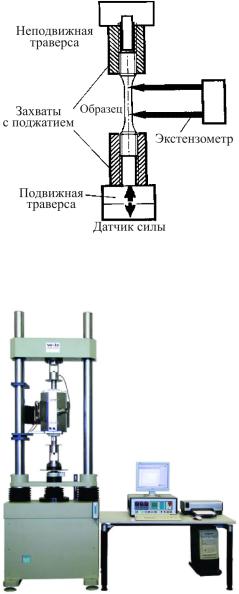
Рис. 10. Принципиальная схема испытания на растяжение на установке LFMZ-100
Рис. 11. Высокотемпературный экстензометр LFMZ-50
44
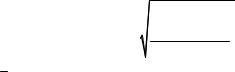
По данным, зафиксированным в ходе испытаний, с помощью алгоритма, заложенного в программном обеспечении установки LFMZ100 в соответствии с ASTM 8M [60], автоматически вычислялись механические характеристики (E,σ0,2, σВ, δ, ψ). Определение модуляупругости в пределах линейного участка диаграммы растяжения с фиксированными границами проводилось методом регрессии.
2.2.14. Испытания на малоцикловую усталость (МЦУ)
Испытания на МЦУ проводились на высокотемпературном экстензометре LFMZ-50 с базой 12,5 мм в соответствии с ГОСТ 25.502 [61], ASTM E606 [62] (рис. 11).
2.2.15. Статистическая обработка результатов
Статистическая обработка результатов испытаний сплава PH1 при температуре 20 °С заключалась в определении средних значений характеристик механических свойств, среднеквадратических отклонений (С.К.О.), значений нижних границ средних характеристик механических свойств с доверительной вероятностью 95 % по формулам [63]
|
|
|
|
|
1 |
N |
|
||
|
|
|
|
|
Xi ; |
(3) |
|||
|
X |
= |
|
||||||
|
|
|
|||||||
|
|
|
|
|
N i=1 |
|
|||
|
|
|
N |
|
|
|
|
|
|
S = |
|
|
(X I − X |
)2 |
(4) |
||||
|
|
i=1 |
, |
||||||
|
|
|
|
|
|
|
|
N − 1
где X – среднее значение характеристики механических свойств сплава; Xi – значение характеристики механических свойств от-
дельныхобразцов; N – количествоэлементоввыборки; S – С.К.О. Значения минимальных характеристик механических свойств
сплавасвероятностью99 % определялисьпоформуле
Xmim = X − 3S. |
(5) |
45
2.2.16. Использование электронно-вычислительной техники и оборудования испытательной лаборатории
Использование электронно-вычислительной техники для проведения исследований и экспериментов по выбранной тематике включало в себя использование интернет-ресурсов, поисковых систем мировых научных баз данных (Google Scholar, Web of Science, Science Direct), программного обеспечения, производящего статистическую обработку данных при измерении, и программного продукта Microsoft Excel 2007. Обработка графических данных проводилась на компьютере с использованием про-
граммных пакетов Grapher и Sigma Plot.
Испытания были проведены аккредитованной испытательной лабораторией прочности материалов и деталей авиационных двигателей с целью формирования базы данных характеристик механических свойств металлических материалов. Универсальные электромеханические, сервогидравлические и электрорезонансная испытательные установки обеспечивают испытания образцов для определения следующих характеристик: при статическом нагружении – кратковременных свойств; при циклическом нагружении – малоцикловой усталости (МЦУ).
46
ГЛАВА 3. ИЗУЧЕНИЕ ВЛИЯНИЯ ТЕРМИЧЕСКОЙ ОБРАБОТКИ НА СВОЙСТВА СТАЛИ
Рассмотренный в литературном обзоре материал позволяет сделать вывод о том, что процесс СЛС охарактеризуется глубоким взаимодействием между передачей тепла и массы вместе с химическими взаимодействиями, которые приводят к изменениям механических и теплофизических свойств материалов. Модели и прототипы, созданные методом СЛС, имеют превосходные механические характеристики: они отличаются прочностью, гибкостью, хорошей детализацией и термической стабильностью. Лазерная обработка приводит к выравниванию различных кристаллографических направлений и направлением сборки в среднем и верхнем слоях, а такжекпостепенному структурномуукрупнению.
Анализ также показал, что лазерное спекание одновременно повышает и прочность, и пластичность материала. Это достигается путем активации и проектирования ее микроструктуры. Прочность на растяжение СЛС-образцов из нержавеющей стали PH1 может быть увеличена на 16–40 %. Во многих работах отмечено, что образцы, изготовленные по технологии СЛС, обладают комплексом свойств, к которым относятся низкая плотность, высокая прочность и предельная прочность на растяжение.
Исследования структуры и физико-механических свойств материалов показали, что данный сплав имеет более высокие прочностные характеристики по сравнению с аналогами, полученными с использованием технологий литья, проката и твердофазного спекания. Свойства детали, полученной методом селективного лазерного спекания, зависят как от технологических параметров процесса (величина лазерного пятна, мощность лазерного излучения, толщина порошкового слоя, защитная атмосфера, шаг лазерного луча, скорость сканирования
иинтервал), так и от физико-химических характеристик металлических порошков жаропрочных сплавов на основе никеля
игранулометрического состава.
47
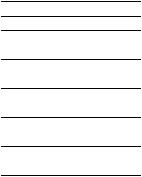
Поскольку сплав EOS StainlessSteel PH1 является интересным и перспективным объектом для селективного лазерного спекания, необходимо проведение дополнительных исследований.
3.1. Изучение характеристик механических свойств образцов из сплава PH1, полученных методом селективного лазерного спекания
Для исследования был выбран сплав EOS StainlessSteel PH1 – нержавеющая сталь в форме мелкодисперсного порошка. Этот тип стали характеризуется высокой коррозийной стойкостью и превосходными механическими свойствами, особенно в диспер- сионно-твердеющем состоянии. Физико-химические свойства порошкового материала PH1 представлены в табл. 2.
Таблица 2 Физико-химические свойства порошкового материала PH1
|
Железо |
|
Основа |
|
Хром |
|
14–15,5 |
|
Никель |
|
3,5–5,5 |
|
Медь |
|
2,5–4,5 |
Химический состав, % |
Марганец |
|
≤ 1 |
|
Кремний |
|
≤ 1 |
|
Молибден |
|
≤ 0,5 |
|
Ниобий |
|
0,15–0,45 |
|
Углерод |
|
≤ 0,07 |
Плотность |
|
7,8 |
г/см3 |
Гранулометрический |
45 мкм |
|
≤3 |
состав, % |
63 мкм |
|
≤0,5 |
Термообработка |
Старение при температуре 482 ± 10 °С; |
||
(тип, среда, температура) |
выдержка 4 ч; охлаждение на воздухе (аргоне) |
Частицы порошка имеют сферическую форму (рис. 12, а). что обеспечивает «текучесть» порошковой композиции в системах подачи материала с минимальным сопротивлением. Это как раз достигается при сферической форме частиц. Такие частицы более компактно укладываются в определенный объем. Также в
48
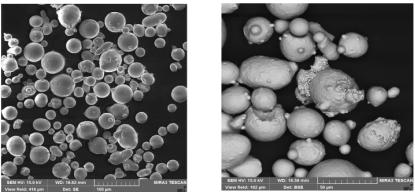
порошках выявлены частицы неправильной формы (рис. 12, б). В материале частиц порошка PH1 микропор не выявлено.
а |
б |
Рис. 12. Порошок PH1: а – вид порошка PH1; б – порошок PH1 с наличием сателлитов и частицами неправильной формы
Испытания проводились в соответствии с ГОСТ 1497-84 «Металлы. Методыиспытаний, нарастяжение» [63].
Параметры, при которых были выращены заготовки для испытаний представлены в табл. 3.
Таблица 3 Основные параметры для выращивания деталей из сплава PH1
Модель |
Рабочая |
Шаг |
Мощность, |
Производи- |
Материал |
зона, мм |
построения, |
Вт |
тельность, |
||
|
|
мкм |
|
см³/ч |
|
EOSINT M280 |
250×250×350 |
20–200 |
400–1000 |
20–35 |
PH1 |
Детали получаются полностью сплавленные при стандартных параметрах и 20 мкм толщине слоя построения.
Физические и механические свойства материала можно изменить благодаря применению термообработки, не изменяя химический состав материала. Заготовки прошли термообработку по следующим режимам:
49
Режим 1: Отжиг при температуре 1050 °С в течение 1,5 ч, затем отпуск при температуре 480 °С в течение 1 ч.
Режим 2: Отжиг при температуре 1050 °С в течение 1,5 ч, затем отпуск при температуре 525 °С в течение 4 ч.
Режим 3: Отпуск при температуре 480 °С в течение 1 ч. Режим 4: Отпуск при температуре 525 °С в течение 4 ч. Твердость образцов после термообработки составила боль-
ше 40 HRC.
Испытания цилиндрических образцов из сплава PH1 на кратковременную прочность были проведены при температуре 20 °С в соответствии с ГОСТ 1497-84 «Металлы. Методы испытаний на растяжение» [64]. Испытания на модуль упругости по ГОСТ 25.502-79 «Расчеты и испытания на прочность в машиностроении. Методы механических испытаний металлов. Методы испытаний на усталость» [65]. Скорость нагружения при определении прочности составляла 1,25 мм/мин. Скорость нагружения при определении характеристиктекучестисоставляла0,125 мм/мин.
Полученные по формулам (3), (4) и (5) средние значения, С.К.О. и минимальные значения характеристик механических
свойств (Ε, σ0,2, σВ, δ, ψ) сплава PH1 при температуре 20 °С представленывтабл. 4.
Таблица 4
Результаты статистической обработки характеристик механических свойств сплава PH1 при температуре 20 °С
Режимы |
Параметр |
Тип значений |
Значение |
|
E, ГПа |
Среднее |
208,92 |
Режим 1: Отжиг при тем- |
σ0,2, МПа |
Среднее |
1244,21 |
пературе 1050 °С |
Минимальное |
1224,90 |
|
в течение 1,5 ч, затем от- |
|
С.К.О. |
6,44 |
пуск при температуре |
σВ, МПа |
Среднее |
1391,604 |
480 °С в течение 1 ч. Вер- |
Минимальное |
1369,19 |
|
тикальное направление |
|
С.К.О. |
7,41 |
выращивания образцов |
δ, % |
Среднее |
8,88 |
|
ψ, % |
Среднее |
25,17 |
50