
книги / Особенности получения наноструктурированных ионно-плазменных плёнок с заданными свойствами
..pdf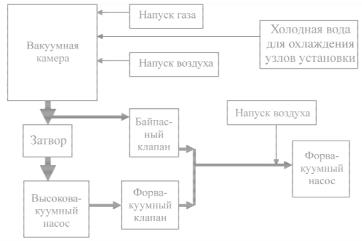
Рис. 11. Типовая схема вакуумной системы
Автоматизированная установка представляет собой 10 функционально обособленных блоков, связанных в одну информационную сеть (RS-485), управляемую персональным компьютером (ПК).
8. ИССЛЕДОВАНИЕ СТРУКТУРЫ И СВОЙСТВ НАНОСТРУКТУРИРОВАННЫХ ПЛЕНОК ZrN, ФОРМИРУЕМЫХ МЕТОДОМ ЭЛЕКТРОДУГОВОГО ИСПАРЕНИЯ
Одной из особенностей процесса износа при резании является то, что в трении, с одной стороны, участвует постоянная поверхность режущего инструмента (РИ), с другой – непрерывно обновляющийся слой обрабатываемого материала. Последнее приводит к тому, что на определенный объем инструментального материала действует многократно изменяющаяся нагрузка, причем закономерности изменения нагрузки обусловлены характеристиками контакта. Увеличить сопротивляемость РИ износу в условиях знакопеременных напряжений и адгезионно-
41
усталостных процессов возможно за счет осаждения многослойных износостойких пленок (в дальнейшем пленок), которые разрушаются в основном в результате хрупкого отрыва, а именно лучше сопротивляются разрушению в условиях усталости. За последние десятилетия исследователи добились значительного повышения надежности изделий с пленками, получаемыми различными методами; были выяснены и устранены многие факторы, ухудшающие их потенциальные возможности. Проблема пленок практически решена, однако проблема стабилизации их свойств находится на стадии совершенствования. Для повышения эффективности упрочнения РИ, получения пленок с контролируемой структурой и стабильными свойствами существует необходимость в экспериментальном изучении условий формирования пленок для установления влияния технологических параметров на температуру поверхности конденсации, фазовый состав, структуру и свойства пленок; оптимизации технологического процесса их получения. Формирование пленок на больших площадях подложек из инструментальных материалов возможно преимущественно ионно-плазменными методами. Комплексные структурные и механические исследования пленок, получаемых данными методами, показали, что для упрочнения инструментальных сталей и сплавов, работающих в сложных переменных температурно-динамических условиях, следует использовать пленки на основе соединений тугоплавких металлов с высокой энергоемкостью. Известно, что имеется связь между энергоемкостью последних и их износостойкостью при резании: чем выше энергоемкость соединения, тем выше его износостой-
кость [117].
Основные цели этапа исследования – изучение температурных условий формирования пленок на основе ZrN методом электродугового испарения (ЭДИ); установление влияния технологических параметров на температуру поверхности конденсации, фазовый состав, структуру и свойства получаемых пленок и повышение эффективности обработки аустенитных сталей.
42
8.1. Методика проведения эксперимента
Для повышения эффективности обработки аустенитных сталей на поверхность режущего инструмента из быстрорежущей стали Р6М5 методом электродугового испарения при различном сочетании технологических параметров осаждали износостойкую пленку на основе ZrN, обладающую высокой энергоемкостью.
Исследуемые пленки были получены последовательным осаждением электродуговым испарением подслоя из Zr и пленки на основе ZrN. Пленки на основе ZrN формировали электродуговым испарением трех однокомпонентных мишеней из Zr в газовой смеси аргона и азота на тестовых образцах из быстрорежущей стали Р6М5 и аустенитной стали 12Х18Н10Т (размеры образцов 10×10×3, 3×3×2) на модернизированной установке УРМЗ.279.048 с автоматическим управлением. Промышленные испытания упрочненных сверл проводились на ремонтном предприятии «Азотхимремонт» ОАО «Азот» (г. Березники).
Переменные технологические параметры:
• |
ток дуги, А |
– 80; 90; 100 |
• напряжение смещения, В |
– 80; 100; 150; 200; 250 |
|
• |
дистанция подложка – источ- |
|
|
ник плазмы (расстояние), мм |
– 270; 300; 330; 360 |
• |
соотношение газов газовой |
|
|
смеси (N2/Ar), % |
– 90/10; 70/30; 50/50; 30/70 |
• |
давление газовой смеси, Па |
– 0,6; 0,8; 1,0; 1,2; 1,4 |
Структуру и морфологические особенности формируемых пленок исследовали на атомно-силовом микроскопе «Наноскан», сканирующем туннельном микроскопе «Умка», металлографическом оптическом микроскопе ЕС МЕТАМ РВ-21. Микротвердость композиции пленка–подложка определяли на микротвердомере ПМТ-3 четырехгранной алмазной пирамидой с нагрузкой на индентере 50 г. Температуру поверхности конденсации в процессе ее осаждения на неподвижную подложку
43
определяли с помощью инфракрасного бесконтактного пирометра «Термикс». Рентгеноструктурный анализ производился
спомощью рентгеновского дифрактометра Shimadzu XRD-6000.
8.2.Влияние тока дуги на температуру поверхности конденсации, фазовый состав, структуру
и свойства наноструктурированных пленок на основе ZrN
Температура упрочняемой поверхности РИ является одним из наиболее значимых параметров технологического процесса, с которым в первую очередь связана адгезионная прочность, структура пленки, уровень остаточных напряжений и, соответственно, ее свойства. Известно, что температура поверхности конденсации отличается от температуры в объеме пленки [118]. По данным [119], разность температур составляет сотни градусов, время релаксации температуры – порядка 10–12 с.
Использование автоматизированного вакуумного оборудования для получения пленок методом электродугового испарения позволило получить текстурированные пленки при достаточно низких температурах подложки. Однако представляло большой интерес изучение взаимосвязи фазового состава, структуры и свойств пленок, их ориентаций с изменениями температурных и технологических условий их осаждения.
Температура поверхности конденсации определялась в процессе ионной очистки и осаждения подслоя Zr, технологические параметры процессов приведены в табл. 2. На рис. 12, а показана зависимость температуры исходной поверхности от продолжительности процессов подготовки поверхности перед осаждением пленки.
Экспериментально установлено, что начальная температура поверхности конденсации с осажденным подслоем Zr составля-
ет 613 К.
Температуру поверхности конденсации (Тп.к) определяли каждые 10 мин в течение процесса осаждения (tпр) пленки. Мик-
44
Таблица 2
Технологические параметры процесса ионной очистки и осаждения подслоя Zr
|
t, мин |
|
|
Дистан- |
|
|
|
Оконча- |
|
|
|
|
|
|
ция под- |
|
|
|
тельная |
Процесс/ |
ион- |
нане- |
Uсм, |
Р, |
ложка – |
Iд, |
Vвращ, |
Газ |
темпера- |
метод |
ная |
сение |
В |
Па |
источ- |
А |
об/мин |
|
тура, К |
ник |
|
|
|||||||
|
очист- |
под- |
|
|
|
|
|
|
|
|
|
|
плазмы, |
|
|
|
|
||
|
ка |
слоя |
|
|
|
|
|
|
|
|
|
|
мм |
|
|
|
|
||
|
|
|
|
|
|
|
|
|
|
Ионная |
|
|
|
|
|
|
|
|
|
очистка/ |
|
|
600 |
0,01 |
270 |
80 |
2,5 |
Ar |
651 |
ЭДИ |
5 |
3 |
|
|
|
|
|
|
|
Осаждение |
|
|
|
|
|
|
|
||
послоя/ |
|
|
200 |
1,0 |
270 |
80 |
2,5 |
Ar |
651 |
ЭДИ |
|
|
|
|
|
|
|
|
|
ротвердость композиции пленка–подложка измерялась после завершения процесса осаждения пленки (tпр = 30 мин).
В табл. 3 приведены технологические параметры, температура и скорость нагрева поверхности конденсации, микротвердость композиции пленка–подложка. На рис. 12, б–е и рис. 13 представлены зависимости температуры поверхности конденсации и микротвердости композиции пленка–подложка от продолжительности процесса осаждения пленки ZrN.
Установлено, что зависимость температуры поверхности конденсации от тока дуги и продолжительности процесса осаждения носит линейный характер. С увеличением продолжительности процесса осаждения пленки температура поверхности конденсации не только поддерживается, но и увеличивается на 90–120 К. Совместное увеличение продолжительности процесса осаждения пленки и тока дуги приводит к увеличению скорости нагрева поверхности конденсации и микротвердости композиции пленка–подложка.
45
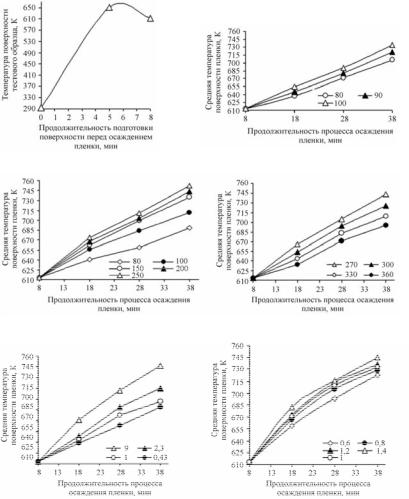
а |
б |
в |
г |
|
|
д |
е |
Рис. 12. Изменение температуры поверхности конденсации в процессе: а – 1–5 – ионной очистки, 5–8 – осаждения подслоя Zr; осаждения пленки ZrN при изменении технологических параметров: б – тока дуги; в – напряжения смещения на подложке; г – дистанции подложка– источник плазмы (расстояния); д – соотношения газов газовой смеси
N2/Ar, %: 90/10 = 9; 70/30 = 2,3; 50/50 = 1; 30/70 = 0,43; е – давления газовой смеси, Па
46
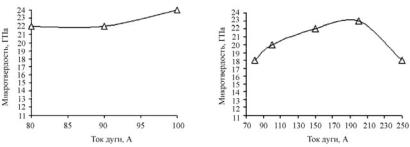
Таблица 3
Технологические параметры процесса осаждения (tпр), температура поверхности конденсации (Тп.к) и микротвердость композиции пленка–подложка (начальная Тп.к = 613 К; переменный технологический параметр – ток дуги)
Но- |
Соотно- |
|
|
|
|
Тп.к, К, при tпр |
|
|
||
мер |
шение |
Iд, А |
р, Па |
L, мм |
Uсм, В |
|
|
|
Vнагр, |
Н , |
опы- |
газов |
10 |
20 |
30 |
К/мин |
ГПа |
||||
та |
N2/Ar, % |
|
|
|
|
|
|
|||
|
|
|
|
мин |
мин |
мин |
|
|
||
|
|
|
|
|
|
|
|
|||
|
|
|
|
|
|
|
|
|
|
|
1 |
90/10 |
100в |
1,0 |
270 |
200 |
654 |
691 |
734 |
4,0 |
23,7 |
2 |
90/10 |
90в |
1,0 |
270 |
200 |
645 |
680 |
721 |
3,6 |
21,6 |
3 |
90/10 |
80в |
1,0 |
270 |
200 |
637 |
671 |
706 |
3,1 |
21,6 |
4 |
90/10 |
80г |
1,0 |
273 |
200 |
625 |
653 |
690 |
2,6 |
11,4 |
Примечание: в – вертикальная плоскость расположения тестового образца; г – горизонтальная плоскость расположения тестового образца.
а |
б |
Рис. 13. Микротвердость композиции пленка ZrN–подложка при изменении технологических параметров: а – тока дуги; б – напряжения смещения на подложке; в – расстояния (дистанции) подложка–источник плазмы; г – соотношения газов газовой смеси N2/Ar, %: 90/10 = 9; 70/30 = = 2,3; 50/50 = 1; 30/70 = 0,43; д – давления газовой смеси (см. также с. 48)
47
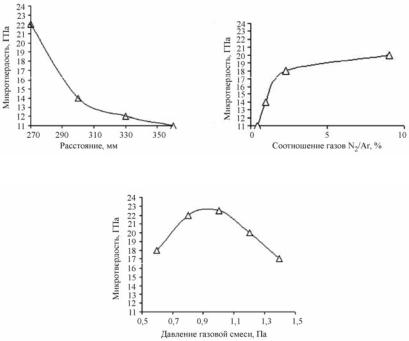
в |
г |
д
Рис. 13. Окончание
Металлографическое исследование морфологических особенностей поверхности пленки ZrN, полученной при токе дуги 100 А, tпр = 30 мин на оптическом микроскопе ЕС МЕТАМ РВ-21, показали, что несмотря на максимальную микротвердость композиции пленка–подложка (23,7 ГПа), на поверхности пленки присутствует большое количество капельной фазы (рис. 14). Ухудшение качества упрочняемой поверхности недопустимо для РИ, а максимальная температура ее нагрева до 734 К – для быстрорежущей матрицы. Установлено, что при токах дуги 80
и90 А микротвердость композиции сформированных пленок
иподложки, морфологические особенности поверхности пленки, размер и количество капельной фазы, фазовый состав
48
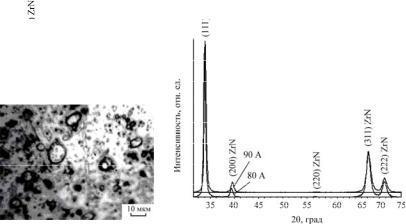
иструктура пленок ZrN практически не отличаются. При указанных технологических условиях и расположении подложки в вертикальной плоскости, перпендикулярной потоку пленкообразующих частиц, формируется монофазная пленка ZrN с ГЦКрешеткой симметрии Fm-3m (225) и а = 4,578 Å со столбчатой структурой и преимущественной ориентировкой по (111). На рис. 15 представлены рентгеновские дифрактограммы пленок ZrN. В табл. 4 приведены положения дифракционных максимумов и фазовый состав пленок ZrN на подложках из Р6М5, расположенных в вертикальной плоскости (ток дуги Iд равен 80
и90 А).
|
|
|
|
Рис. 14. Морфологические |
Рис. 15. Рентгеновские дифрактограммы |
||
особенности |
поверхности |
(Cu Кα-излучение) пленок ZrN, получен- |
|
пленки ZrN, полученной |
ных на подложке из Р6М5: при Iд = 80 А |
||
при Iд = 100 А (оптический |
(толщина пленки 15 мкм); Iд = 90 А |
||
микроскоп |
ЕС МЕТАМ |
(толщина пленки 18 мкм) (рентгеновский |
|
РВ-21) |
|
дифрактометр Shimadzu XRD-6000) |
Для уточнения полученных экспериментальных результатов были дополнительно исследованы морфологические особенности пленок с помощью сканирующей зондовой микроско-
пии (рис. 16–18).
49
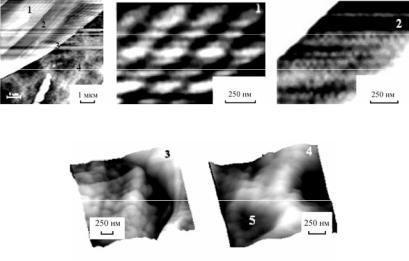
Таблица 4
Положение дифракционных максимумов и фазовый состав пленок ZrN на подложках из Р6М5, расположенных
в вертикальной плоскости (Iд = 80 А; Iд = 90 А)
|
|
р, |
Фазо- |
|
2θ/Интенсивность, отн. ед. |
|
||
Пленка |
Iд, |
вый |
|
|
||||
|
|
|
|
|
||||
|
|
|
|
|
||||
|
А |
Па |
состав |
(111) |
(200) |
(220) |
(311) |
(222) |
|
|
|
пленки |
|||||
ZrN |
80 |
1,0 |
ZrN |
33,95/100 |
39,55/6,8 |
56,92/0,3 |
67,70/26,2 |
70,95/9,4 |
|
|
|
|
|
|
|
|
|
ZrN |
90 |
1,0 |
ZrN |
33,80/100 |
39,35/5,8 |
56,78/0,3 |
67,65/30,0 |
71,00/10,2 |
|
|
|
|
|
|
|
|
|
а |
б |
в |
гд
Рис. 16. Морфологические особенности поверхности пленки ZrN, полученной при Iд = 90 А: а – образование полос волокнистого строения
снаправленностью в плоскости, параллельной поверхности подложки,
сдендритной (б) и фрактальной (в) поверхностной структурой; г – нарушение сплошности столбчатой структуры; д – образование фрактальной структуры на поверхности пустот (атомно-силовой микроскоп «Наноскан») (подложка расположена в вертикальной плоскости, перпендикулярной потоку пленкообразующих частиц)
50