
книги / Особенности получения наноструктурированных ионно-плазменных плёнок с заданными свойствами
..pdf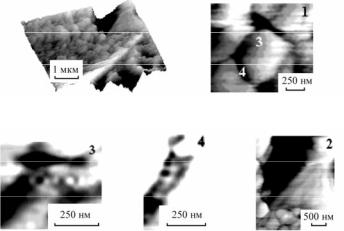
аб
в |
г |
д |
Рис. 17. Морфологические особенности поверхности пленки ZrN, полученной при Iд = 80 А: а – высокая анизотропия скоростей формирования пленки по различным направлениям; б – объединение нанокристаллитов со столбчатой текстурой в ансамбли и сохранение когерентности границ (наночастиц); в, г – образование трубчатых структур на поверхности столбчатой структуры (в) и в промежуточных зонах между участками плотной пленки столбчатого строения (г); д – твердотельное образование в виде конуса (атомно-силовой микроскоп «Наноскан») (подложка расположена в вертикальной плоскости, перпенди-
дикулярной потоку пленкообразующих частиц)
Результаты исследований морфологических особенностей пленок показали, что неравновесные условия электродугового испарения и изменение одного из основных параметров данного метода приводят к высокой анизотропии скоростей формирования пленки по различным направлениям и, как следствие, формированию структурно неоднородных пленок, а именно:
1. Для пленок, сформированных при токах дуги 80 и 90 А, проявляется характерная особенность ионно-плазменных процессов – своеобразный «недостаток» материала для заполнения межстолбчатых пустот (см. рис. 16, д, рис. 17, а).
51
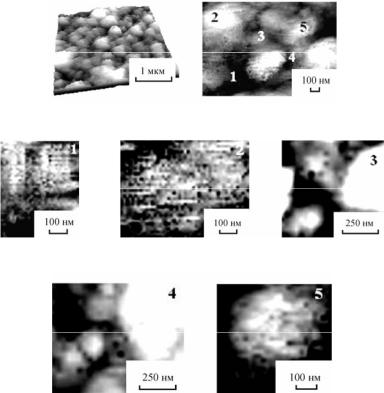
аб
в |
г |
д |
еж
Рис. 18. Морфологические особенности поверхности пленки ZrN, полученной при Iд = 80 А: а – образование столбчатой (волокнистой) структуры с переменной шероховатостью поверхности; б – объединение ансамблей нанокристаллитов со столбчатой текстурой в макросистемы с некогерентными границами и нарушением сплошности; в – объединение нанокристаллитов в ансамбли c сохранением когерентности границ (наночастиц); образование поверхностной трубчатой структуры: г – на поверхности столбчатой структуры; д, е – и в промежуточных зонах между участками плотной пленки столбчатого строения; ж – образование ансамблей трубчатой структуры, ориентированной под углом к поверхности подложки (сканирующий туннельный микроскоп «Умка») (подложка расположена в горизонтальной плоско-
сти, под углом 2,5° к потоку пленкообразующих частиц)
52
2.На поверхности пленки столбчатого строения при токе дуги 90 А обнаружены полосы волокнистого строения с направленностью в плоскости, параллельной поверхности подложки (см. рис. 16, а, г). Следует отметить, что поверхность светлых волокон покрыта дендритной структурой (см. рис. 16, б), шероховатость более темных волокон (а также и поверхность межстолбчатых пустот) развивается до фрактальной геометрии (см.
рис. 16, в, е).
3.На большей части поверхности пленки (ток дуги 80 А) прослеживается объединение нанокристаллитов со столбчатой текстурой в ансамбли и сохранение когерентности границ (наночастиц) (см. рис. 17, б, рис. 18, в), а самих ансамблей –
вмакросистемы с некогерентными границами и с нарушением сплошности в конечном итоге (см. рис. 17, а, рис. 18, б) [115]. На поверхности ансамблей нанокристаллитов также образуются неравновесные структуры в виде трубчатых образований (см. рис. 17, в, г, рис. 18, д, е). В случае расположения подложки в вертикальной плоскости, перпендикулярной потоку пленкообразую-
щих частиц, и Iд = 80 А на поверхности пленки обнаружены единичные твердотельные образования в виде конуса (см. рис. 17, д).
8.3. Влияние положения подложки относительно направления потока пленкообразующих частиц на фазовый состав
инаправление кристаллографической ориентации наноструктурированных пленок на основе ZrN
Для установления оптимального положения подложки относительно потока пленкообразующих частиц изучались пленки ZrN на тестовых образцах, расположенных в горизонтальной плоскости, которая составляла 2,5° относительно центральной оси потока пленкообразующих частиц. Технологические параметры процесса осаждения были приведены в табл. 3. На рис. 19 представлены рентгеновские дифрактограммы пленок ZrN, в табл. 5 приведены положения дифракционных максимумов
53

а
б
Рис. 19. Рентгеновские дифрактограммы участков пленок ZrN толщиной 10 мкм, полученных при Iд = 80 А: а – на подложке из Р6М5, расположенной в горизонтальной плоскости; б – на подложках Р6М5, расположенных в вертикальной и горизонтальной плоскостях (дифракто-
метр Shimadzu XRD-6000)
54
Таблица 5
Положение дифракционных максимумов и фазовый состав пленок ZrN на подложках из Р6М5, расположенных в различных плоскостях
Пленка/плос- |
|
Фазо- |
|
2θ/Интенсивность, отн. ед. I111/h, |
|
|
||||
Р, |
|
|
отн. ед./мкм |
|
|
|
||||
кость распо- |
вый |
|
|
|
|
|
||||
|
|
|
|
|
|
|
|
|||
ложения |
Па |
сос- |
|
|
|
|
|
|
|
|
подложки |
|
тав |
(111) |
(200) |
(220) |
(311) |
(222) |
(400) |
||
|
|
|
|
|
|
|
|
|
|
|
ZrN/верти- |
|
|
33,95/ |
39,55/ |
56,92/ |
67,70/ |
70,95/ |
|
– |
|
1,0 |
ZrN |
100/ |
6,8 |
0,3 |
26,2 |
9,4 |
|
|
|
|
кальная |
|
|
5,6 |
|
|
|
|
|
|
|
|
|
|
|
|
|
|
|
|
|
|
|
|
ZrN |
33,85/ |
39,50/ |
56,77/ |
67,85/ |
71,20/ |
84,64/3,2 |
||
ZrN/горизон- |
|
100/10 |
47,5 |
36,9 |
21,1 |
9,6 |
|
|
|
|
1,0 |
|
|
|
|
|
|
|
|
|
|
|
(100) |
(002) |
(101) |
(102) |
(103) |
(004) |
|
(202) |
||
тальная |
|
Zr |
|
|
|
|
|
|
|
|
|
31,85/ |
34,75/ |
36,50/ |
48,00/ |
63,43/ |
73,23/ |
77,55/ |
|||
|
|
|||||||||
|
|
|
7,0 |
30,8 |
18,7 |
4,0 |
4,4 |
4,4 |
|
2,9 |
и фазовый состав пленок ZrN на подложках из Р6М5, расположенных в различных плоскостях (Iд = 80 А).
С уменьшением температуры подложки (см. табл. 3) с 706 до 690 К и изменением положения подложки относительно потока пленкообразующих частиц путем перемещения подложки из вертикальной плоскости в горизонтальную увеличивается интенсивность отражений (111) ZrN, приведенная к толщине
пленки I111/h с 5,6 до 10 отн. ед./мкм, что свидетельствует об изменении механизма формирования пленки. Установлено, что
изменение положения подложки относительно потока пленкообразующих частиц вследствие двумерного механизма формирования и большой свободной энергии приводит к образованию пленки ZrN с плотно упакованной структурой, представляющей собой смесь фаз: ZrN с ГЦК-решеткой симметрии Fm-3m (225) и параметром решетки а = 4,578 Å и Zr с гексагональной решеткой с симметрией P63/mmc (194) и параметрами а = 3,232 Å
55
ис = 5,147 Å. Образование указанной структуры объясняется тем, что энтальпия обеих фаз мало отличается друг от друга
[116].
Уменьшение микротвердости композиции пленка–подлож- ка с 21,6 до 11,4 ГПа при горизонтальном расположении подложки объясняется не только увеличением дистанции и скорости осаждения, но и наличием фазы Zr с меньшей микротвердостью.
Выявлено, что при формировании пленок с наклонным потоком пленкообразующих частиц образуется анизотропное распределение структурных дефектов. Ось текстуры может быть как перпендикулярной поверхности подложки соответствующей пленки, полученной при нормальном падении потока пленкообразующих частиц, так и отклоненной – при наклонном падении. Хотя пленка с четко выраженной волокнистой структурой должна иметь разные упругие константы вдоль оси текстуры
ивдоль перпендикулярного направления, такие различия не могут объяснить наблюдаемую анизотропию напряжений. Анизотропия возникающих напряжений обусловлена совместным влиянием особенностей процесса зарождения и анизотропии процесса формирования пленки [120]. Анизотропия возникающих напряжений обусловлена совместным влиянием особенностей процесса зарождения и анизотропии процесса формирования пленки. Установлено, что анизотропия при наклонном напылении возникает вследствие анизотропии структурных дефектов, а не в результате волокнистой структуры [120].
8.4. Влияние напряжения смещения на подложке на температуру поверхности конденсации и свойства наноструктурированных пленок на основе ZrN
В табл. 6 приведены технологические параметры, в том числе величина напряжения смещения на подложке, а также температура и скорость нагрева поверхности конденсации, микротвердость композиции пленка–подложка, на рис. 12, в, 13, б –
56
Таблица 6
Технологические параметры процесса осаждения (tпр), температура поверхности конденсации (Тп.к) и микротвердость композиции пленка–подложка (начальная Тп.к = 613 К)
Но- |
|
Соотно- |
|
|
|
|
|
Тп.к, К, при tпр |
|
|
|
|
|
||
мер |
|
шение |
|
|
|
|
|
V |
нагр |
, |
|
Н , |
|||
|
|
|
Uсм, В |
Iд, А |
|
L, мм |
р, Па |
|
|
|
|
|
|
|
|
опы- |
|
газов |
|
10 |
20 |
30 |
К/мин |
ГПа |
|||||||
та |
|
N2/Ar, % |
|
|
|
|
|
мин |
мин |
мин |
|
|
|
|
|
Переменный технологический параметр – напряжение смещения |
|||||||||||||||
|
|
|
|
|
на подложке |
|
|
|
|
|
|
|
|
||
4 |
|
90/10 |
80 |
80 |
|
270 |
1,0 |
641 |
659 |
688 |
2,5 |
|
|
18,0 |
|
5 |
|
90/10 |
100 |
90 |
|
270 |
1,0 |
656 |
684 |
712 |
3,3 |
|
|
19,6 |
|
6 |
|
90/10 |
150 |
90 |
|
270 |
1,0 |
663 |
699 |
735 |
4,1 |
|
|
21,6 |
|
7 |
|
90/10 |
200 |
90 |
|
270 |
1,0 |
668 |
703 |
743 |
4,3 |
|
|
23,0 |
|
8 |
|
90/10 |
250 |
90 |
|
270 |
1,0 |
674 |
711 |
752 |
4,6 |
|
|
12,4 |
|
|
|
Переменный технологический параметр – дистанция |
|
|
|
||||||||||
|
|
|
источник плазмы – подложка (L) |
|
|
|
|
|
|
||||||
9 |
|
90/10 |
270 |
1,0 |
|
90 |
200 |
666 |
705 |
742 |
4,3 |
|
|
22,0 |
|
|
|
|
|
|
|
|
|
|
|
|
|
|
|
|
|
10 |
|
90/10 |
300 |
1,0 |
|
90 |
200 |
654 |
694 |
725 |
3,7 |
|
|
14,0 |
|
|
|
|
|
|
|
|
|
|
|
|
|
|
|
|
|
11 |
|
90/10 |
330 |
1,0 |
|
90 |
200 |
643 |
683 |
709 |
3,2 |
|
|
12,0 |
|
|
|
|
|
|
|
|
|
|
|
|
|
|
|
|
|
12 |
|
90/10 |
360 |
1,0 |
|
90 |
200 |
634 |
671 |
695 |
2,7 |
|
|
11,0 |
|
|
|
|
|
|
|
|
|
|
|
|
|
|
|||
|
Переменный технологический параметр – соотношение газов |
|
|||||||||||||
|
|
|
|
газовой смеси |
|
|
|
|
|
|
|
|
|||
13 |
|
90/10=9,0 |
270 |
1,0 |
|
90 |
200 |
671 |
712 |
747 |
4,5 |
|
|
19,6 |
|
14 |
|
70/30=2,3 |
270 |
1,0 |
|
90 |
200 |
648 |
686 |
715 |
3,4 |
|
|
18,0 |
|
15 |
|
50/50=1,0 |
270 |
1,0 |
|
90 |
200 |
643 |
678 |
697 |
2,8 |
|
|
14,2 |
|
16 |
|
30/70=0,43 |
270 |
1,0 |
|
90 |
200 |
639 |
663 |
689 |
2,5 |
|
|
10,7 |
|
Переменный технологический параметр – давление газовой смеси |
|||||||||||||||
17 |
|
90/10 |
0,6 |
270 |
|
90 |
200 |
659 |
693 |
723 |
3,7 |
|
|
18,0 |
|
|
|
|
|
|
|
|
|
|
|
|
|
|
|
|
|
18 |
|
90/10 |
0,8 |
270 |
|
90 |
200 |
667 |
705 |
729 |
3,9 |
|
|
22,0 |
|
19 |
|
90/10 |
1,0 |
270 |
|
90 |
200 |
671 |
710 |
733 |
4,0 |
|
|
22,5 |
|
20 |
|
90/10 |
1,2 |
270 |
|
90 |
200 |
673 |
713 |
736 |
4,1 |
|
|
20,0 |
|
|
|
|
|
|
|
|
|
|
|
|
|
|
|
|
|
21 |
|
90/10 |
1,4 |
270 |
|
90 |
200 |
683 |
716 |
745 |
4,4 |
|
|
17,0 |
57
зависимости температуры поверхности конденсации и микротвердости композиции пленка–подложка от продолжительности процесса осаждения.
Экспериментально определено, что увеличение напряжения смещения до 200 В способствует увеличению микротвердости композиции пленка–подложка, скорости нагрева и максимальной температуры поверхности конденсации. Уменьшение микротвердости композиции пленка–подложка при напряжении смещения 250 В могло быть вызвано, как отпуском аустенитной матрицы тестового образца, так и изменением структурного состояния осаждаемой пленки.
8.5. Влияние дистанции источник плазмы – подложка на температуру поверхности конденсации и свойства наноструктурированных пленок на основе ZrN
В табл. 6 приведены технологические параметры, в том числе дистанция источник плазмы – подложка, а также температура и скорость нагрева поверхности конденсации, микротвердость композиции пленка–подложка, на рис. 12, г, 13, в – зависимости температуры поверхности конденсации и микротвердости композиции пленка–подложка от продолжительности процесса осаждения.
Выявлено, что увеличение дистанции (расстояния) источник плазмы – подложка свыше оптимального значения 270 мм приводит к уменьшению как скорости нагрева, максимальной температуры поверхности конденсации, так и микротвердости композиции пленка–подложка, что вызвано снижением коэффициента использования испаряемого материала, скорости осаждения пленки и ее толщины, изменением условий зарождения и формирования пленок.
58
8.6. Влияние соотношения реакционного и инертного газов на температуру поверхности конденсации и свойства наноструктурированных пленок на основе ZrN
В табл. 6 приведены технологические параметры, в том числе соотношение газов в газовой смеси, а также температура и скорость нагрева поверхности конденсации, микротвердость композиции пленка–подложка, на рис. 12, д, 13, г – зависимости температуры поверхности конденсации и микротвердости композиции пленка–подложка от продолжительности процесса осаждения.
Результаты экспериментальных исследований показали, что уменьшение содержания азота в газовой смеси, как и в случае с увеличением дистанции источник плазмы–подложка, приводит к уменьшению как скорости нагрева, максимальной температуры поверхности конденсации, так и микротвердости композиции пленка–подложка. Микротвердость пленки непосредственно определяется концентрацией реакционного газа азота в газовой смеси и возрастает с увеличением содержания азота, так как поступление большего объема реакционного газа способствует более полному протеканию плазмохимических реакций.
8.7. Влияние давления газовой смеси на температуру поверхности конденсации и свойства наноструктурированных пленок на основе ZrN
В табл. 6 приведены технологические параметры, в том числе давление газовой смеси, а также температура и скорость нагрева поверхности конденсации, микротвердость композиции пленка–подложка, на рис. 12, е, 13, д – зависимости температуры поверхности конденсации и микротвердости композиции пленка–подложка от продолжительности процесса осаждения.
Полученные результаты позволили заключить, что увеличение давления газовой смеси при соотношении газов N2/Ar = = 90/10 % способствует увеличению скорости нагрева и макси-
59
мальной температуры поверхности конденсации. Давление газовой смеси с максимальным содержанием азота оказывает непосредственное влияние на микротвердость пленок ZrN в процессе их формирования. Зависимость микротвердости композиции пленка–подложка от давления газовой смеси носит экстремальный характер, из рис. 13, д видно, что с увеличением давления до 1,0 Па, микротвердость пленок возрастает, так как увеличение давления газовой смеси при максимальном содержании реакционного газа способствует повышению скорости протекания плазмохимических реакций. Однако при дальнейшем увеличении давления микротвердость пленки снижается, что обусловлено образованием пленок, имеющих в своем составе повышенную концентрацию химических элементов реакционного газа, приводящих к дефектности структуры формируемых пленок и снижению их микротвердости.
На основании многочисленных экспериментальных исследований установлено, что равновесные и однофазные пленки на основе ZrN с микротвердостью 19,6–23,0 ГПа формируются при оптимальных технологических параметрах: соотношение газов в газовой смеси N2/Ar = 90/10 %, дистанция источник плазмы– подложка L = 270 мм, ток дуги Iд = 90 А, напряжение смещения на подложке Uсм = 200 В, давление газовой смеси Р = 1,0 Па.
8.8. Результаты промышленных испытаний
Установлена эффективность обработки аустенитных сталей упрочненными сверлами из быстрорежущей стали Р6М5.
Промышленные испытания упрочненных сверл проводились на ремонтном предприятии «Азотхимремонт» ОАО «Азот» (г. Березники) при различных режимах обработки с целью определения экстремальных условий работы технологического инструмента из быстрорежушей стали.
Установлено, что нанесение пленок ZrN при соблюдении сочетания оптимальных технологических параметров позволило увеличить стойкость режущего инструмента из быстрорежущей
60