
книги / Микроэлектроника. Гибридные интегральные функциональные устройства
.pdfКоммутационные платы (чаще всего одно-или двухслойные) на металлическом основании с диэлектрической изоляцией имеют большое значение при формировании мощных схем.
Основными технологическими вопросами при формиро вании таких плат является подбор пары «металл—диэлект рик» по ТКЛР, обеспечение необходимой адгезионной проч ности сцепления диэлектрического слоя к металлу по всей поверхности платы, достижение хорошего качества покры тия на металле (отсутствие шероховатости, трещин и других дефектов поверхности, отрицательно влияющих на качество наносимых пленочных покрытий). Большое применение находят металлические пластины из стали, покрытые эпок сидной смолой или легкоплавким стеклом. Однако опти мальные показатели имеют подложки из анодированного алюминия (табл. 3.1). Чаще всего для оснований исполь зуется не чистый, сравнительно мягкий алюминий (напри мер, марки АД-1), а механически прочные алюминиевые сплавы. Однако основные легирующие добавки в этих сплавах должны, как и алюминий, легко подвергаться анод ному оксидированию. Сплавами, которые обеспечивают необходимую прочность пластины (не менее 20 ГПа), явля ются сплавы алюминия с магнием (типа АМГ). Кроме того, для доведения поверхности пластины до 13— 14-го классов чистоты отработки (например, шлифовкой, полировкой или резкой алмазными кругами) с последующим анодированием второго рода сплавы должны иметь хорошую однородность структуры и состава по всей пластине. Поэтому большое содержание легирующих добавок магния нежелательно; оп тимальным является использование сплава АМГ-3, который содержит 3,2—3,8 % магния, 0,3—0,6 % марганца и 0,5— 0,8 % кремния. Для анодирования приемлемым является комбинированный электролит на основе щавелевой кислоты, с помощью которого получают менее рыхлые пленки с при емлемыми изоляционными свойствами по сравнению с сильнорастворяющим электролитом (на основе серной кислоты). Однако этот электролит в отличие от малорастворяющего (на основе сульфасалициловой кислоты) позволяет созда вать большие толщины оксида (40—60 мкм) при плотности тока 1—2 А/дм2. Значительная плотность пор диэлектрика, присущая методу анодирования второго рода, является и положительным моментом — предохраняет от растрескива ния слой А120 3 при повышении (понижении) температуры, когда возникают значительные ВН из-за большого разли чия в ТКЛР сплава алюминия и А120 3. Для того чтобы подложки выдерживали температуру 250—300° С, плотность
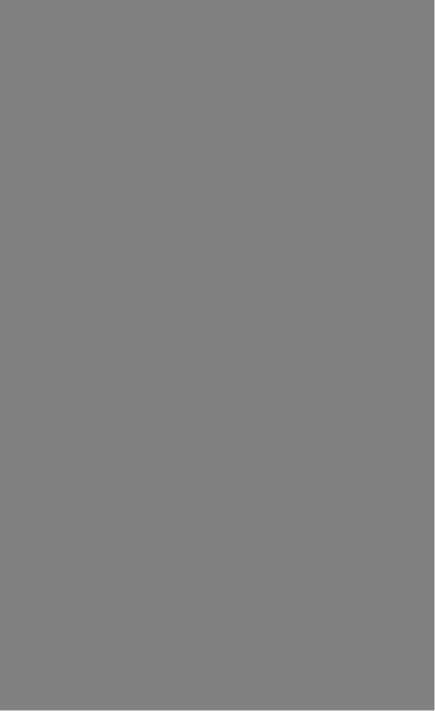

для толщины диэлектрического слоя hx |
|
||
K M = r k h J + ~ ' |
+ |
sU l + 2 - b ^ - ) - ‘ + /7-^!> |
(3.5) |
где a, bt с, г, s, р, |
k, |
t — нормирующие коэффициенты; |
/ — длина подложки; р2 — плотность металла; р0 — макси мально допустимая сила воздействия на диэлектрический слой; К19 К2 — теплопроводность диэлектрика и металла; ег, е0 — относительная диэлектрическая проницаемость ди электрика и диэлектрическая постоянная. Минимум функ ций Кх и К2 достигается при следующих значениях Л2 и hx:
h2 min Г chl |
(\ l \ f \ |
1 W o / 1 п - к2) М р1 |
(3.6) |
|
|
i±L |
|
|Vt.2 Я,| + |
рее0 (^+1) j |
t+ 2 |
(3.7) |
h1 min |
|
|
В табл. 3.2 приведены значения оптимальных и реальных толщин некоторых металлических плат.
|
|
Оптимальная |
|
Тип и |
|
толщина |
|
|
|
|
|
|
|
мкм |
мм |
Анодированный алюминий |
10,5 |
0,7 |
|
Сталь со стеклянным |
по |
5,6 |
1,45 |
крытием |
по |
||
Медь с полимерным |
|
0,35 |
|
крытием |
|
6 |
Т а б л и ц а |
3.2 |
|
Реальная |
толщина |
|
мкм | |
мм |
|
J0— 60 |
1 со О |
CN |
20-150 |
0 1 to о |
|
3— 15 |
0,2 —1 ,5 |
Согласно табл. 3.2 на практике толщины слоев не всегда являются оптимальными, что в ряде случаев может привести к увеличению массы и габаритов ГИФУ или к ухудшению электрических и тепловых характеристик.
§ 3.3. Многослойные керамические платы
Многослойные керамические платы для ячеек МЭА из готавливаются спеканием алунда со стеклом при температу ре около 1500° С. Поэтому проводники делают из паст, со держащих тугоплавкий материал — молибден, хотя он име-
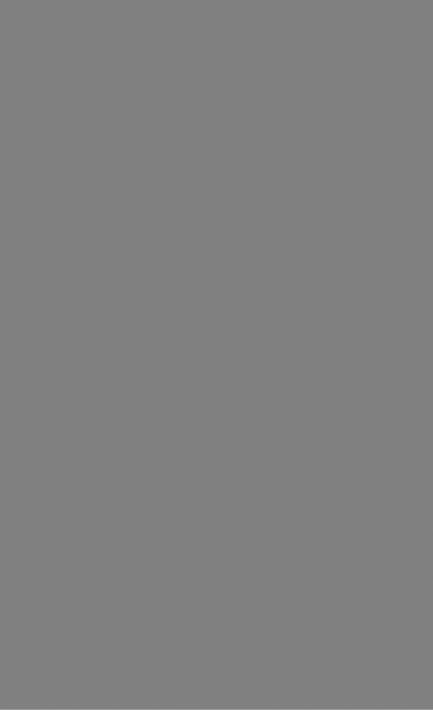
объем становится меньше приблизительно на 40 %. С учетом того, что размеры окончательного изделия должны быть вы держаны с жесткими допусками, степень уменьшения ли нейных размеров должна быть точно известна при первона чальном нанесении рисунков на сырые листы. После завер шения изготовления платы она контролируется на целост ность цепей на автомате. Открытые участки металлизации покрывают электрохимическим слоем никеля или золота и облуживают. В табл. 3.3 приведены основные параметры многослойных керамических плат.
|
|
|
|
|
|
Т а б л и ц а 3.3 |
Параметры |
|
Керамические |
Прецизионные |
|||
|
платы массового |
керамические |
||||
|
|
|
|
|
выпуска |
платы |
Минимальная |
ширина |
ли |
|
|
||
ний и зазоров, мм |
|
0,2—0,4 |
0,125 |
|||
Минимальный |
диаметр |
|
|
|||
переходных |
отверстий, мкм |
0,3-0 .4 |
0,125 |
|||
Минимальный |
шаг отвер |
|
|
|||
стий, мм |
|
|
|
|
2 ,0 -2 ,5 |
0,5—1,25 |
Толщина подложки, мм |
2,0—4,0 |
5,5 |
||||
Максимальные |
размеры |
До 100X120 |
90X90 |
|||
подложки, ммХмм |
|
|||||
Максимальное |
число сло |
|
До 33 |
|||
ев коммутации |
|
|
6 - 8 |
|||
Удельное |
сопротивление |
|
|
|||
проводников |
(погонное), |
|
5— 10 |
|||
Ом/см |
|
|
|
|
5 - 1 0 |
|
Удельная |
(погонная) |
па |
0,9—2,0 |
0,9—2,0 |
||
разитная |
емкость, пФ/см |
|
||||
Адгезия |
|
металлизации |
к |
|
Более 0,5 |
|
керамике, |
ГПа |
|
|
Ьолее 0,5 |
Отметим, что технология получения многослойной кера мики является по существу модификацией технологического процесса изготовления толстопленочных схем. При этом соз дают многоуровневую коммутацию, что затруднено в клас сической толстопленочной технологии. Дело в том, что последовательное нанесение неотожженных паст на керами ческую подложку через трафареты с последующим единым отжигом невозможно; в условиях же нанесения каждой пасты с последующим вжиганиём необходимо обеспечить стабильность состава предыдущих слоев при температурах, равных температурам вжигания последующих слоев. Тем пературы вжигания последующих паст меньше предыдущих и для каждого металлического и диэлектрического слоев
Нужна паста со своим составом. Кроме того, при создании толстопленочных схем возможно коробление и растрески вание подложек большого размера. Поэтому толщина под ложек размером до 60 х 48 мм составляет 0,8—1,5 мм, а бо лее — от 2 до 4 мм. Однако и в этом случае процент выхода плат размером около 100 X 100 мм еще недостаточно высок, так как в отличие от технологии получения многослойной керамики, особенно МПП — ПМ, каждый слой после его изготовления (хотя бы промежуточного) отбрасывать не возможно без удаления в брак низлежащих годных слоев и подложки. При этом уменьшение процента выхода годных плат с увеличением числа слоев коммутации подчиняется степенному закону.
§3.4. Эффективность методов создания многоуровневой коммутации ГИФУ
Для получения коммутационных плат ГИФУ, кроме отмеченных ранее, используют многоотверстный поликор и прецизионные МПП. Двусторонние коммутационные платы из многоотверстного поликора формируются на базе поликоровых подложек (99,7 % А120 3) толщиной 0,5 и 1,0 мм, в которых лучом лазера по программе создаются отверстия диаметром 80— 130 мкм, причем для формирования благо приятной формы отверстий (как в полиимидной пленке) луч лазера действует на одно и то же место подложки с двух ее сторон. Перед получением отверстий обе стороны под ложки защищаются тонким слоем (0,5— 1,0 мкм) материала, который впоследствии легко удаляется вместе с частицами керамики, выброшенной энергией луча лазера из отверстий на поверхность подложки. После создания отверстий осу ществление двууровневой коммутации на обеих сторонах подложки аналогично образованию двусторонней коммута ции на полиимидной пленке.
Многослойные печатные платы, как указывалось, в ос- ( новном используются для конструкций ГИФУ с большим относительным содержанием корпусных ИМС и микро сборок. Однако ввиду повышаемой плотности монтажа та1кие МПП изготавливают с предельными показателями по плотности рисунка линий коммутации и соединительных отверстий, шага контактных площадок и числа сигнальных слоев. Предельную плотность монтажа МПП характеризуют
показателем
Y = iN l( jd ) , |
(3.8) |
где i — число проводников в шаге координатной сетки; N — число сигнальных слоев; / — шаг координатной сетки переходных отверстий; d — диаметр переходных отверстий.
Бессмысленно уменьшать ширину линий и зазоров, в то время как диаметр переходного отверстия, создаваемый ме ханическим сверлением, составляет не менее 400—500 мкм, а укрепляющая отверстие контактная площадка имеет раз мер 700 X 700 и 800 X 800 мкм (около пяти отверстий на 1 см2). Несмотря на то что субтрактивные методы формиро вания ПП по-прежнему преобладают, аддитивные методы находят все большее распространение. В связи с все возрас тающими требованиями увеличения плотности коммутации при субтрактивном методе формирования используется «тонкая» (9 мкм) и «сверхтонкая» (5 мкм) фольга. Это позво ляет уменьшить боковое подтравливание линий, равное тол щине слоя меди. В качестве основного материала ПП для высоконадежной аппаратуры применяется стеклоэпоксид ная основа, а также другие композиции, полиимид. Для установки ИМС в микрокорпусах используются слоистые платы (табл. 3.4).
• |
Относитель |
Коэффициент |
Материал |
ная диэлект |
термического |
рическая |
расширения, |
|
|
проницае |
ю -5 К |
|
мость |
|
Т а б л и ц а 3.4
Теплопроводноэть, Вт/(м- К) |
Коэффициент стоимости |
Эпоксидная |
смола- |
14— 18 |
0,16 |
1 |
|
стекловолокно |
|
4,5—5,0 |
|||
Полиимид-стекловолок- |
15—18 |
0,38 |
2,5 |
||
но |
|
4,5—5.0 |
|||
Фторопласт-стеклово |
8 |
0,25 |
15 |
||
локно |
|
2,5—3,5 |
|||
Эпоксидная смола-кев |
5,3—5.6 |
0,12 |
3 |
||
лар |
|
4,0—4,5 |
|||
Полиимид-кевлар |
3,5—3,6 |
5,6—5,8 |
0,15 |
8 |
|
Эпоксидная |
смола- |
5,0 |
0,17 |
10 |
|
кварц |
|
3,6 |
|||
Полннмнд-кварц |
3,4 |
6 - 8 |
0,2 |
14 |
|
Термопластики |
2,8—3,2 |
20 |
0,16 |
1,2 |
|
Оксид алюминия |
(по- |
6,5 |
20 |
6 |
|
лнкор) |
|
9—10 |
|||
Оксид бериллия |
(бро- |
8,0 |
200 |
10 |
|
кернт) |
|
9—10 |
Повышение качества МПП происходит по следующим направлениям: учет усадки основы платы и отдельных слоев
в ходе процесса изготовления платы; локализация сильного влияния влагопоглощения и температуры на материал ос новы; исключение расслаивания структуры основы; приме нение методов лазерного сверления отверстий.
В табл. 3.5 приведены основные характеристики МПП, изготавливаемых в массовом и опытном производстве.
|
|
Т а б л и ц а |
3.5 |
|
|
|
Способ изготовления |
|
|
|
субтрактив |
|
прецизион |
|
Параметры |
аддитивный |
ный (с при |
||
ный (в том |
менением |
|||
|
числе с тон |
(полуаддн- |
лазера |
для |
|
кой |
тнвный) |
прошивки |
|
|
фольгой) |
|
отверстий) |
Минимальная ширина ли нии и зазоров, мм
Минимальный диаметр переходного отверстия, мм Минимальный шаг отвер
стий, мм
Максимальный размер платы, ммХмм
Минимальная толщина изоляции между проводни ками, мкм
Максимальное число сло
ев Относительная трудоем
кость изготовления Толщина платы, мм Шаг внешних выводов,
мм
Максимальное удельное (погонное) сопротивление проводников, Ом/см
Удельная (погонная) па разитная емкость, пФ/см
0,2—0,4 |
0,15—0,3 |
||
0,3—0,5 |
0 со |
1 о сл |
|
|
|
||
to сл |
сл о |
2,5 |
|
|
1 |
|
|
600X350 |
300X300 |
||
100—200 |
' 60— 100 |
||
4—6 |
6— 12 |
||
|
1,0 |
2,0—4,0 |
|
3 - 5 |
2 - 5 |
||
2,5X 2 ,5 |
2,5 X 2,5 |
||
Менее |
0,01—0,001 |
||
0,001 |
|
|
|
0,3—0,5 |
0 СЛ |
о 00 |
|
|
|
|
1 |
0,12—0,15
0,15
1,25 (внут ренних — 0,5)
600X700
50
До 20
10— 15
4,6
1,25X2,5
0 |
g |
1 |
о о |
0,8— 1,0
МОНТАЖ ГИФУ
§4.1. Микромонтаж кристаллов бескорпусных ИМС в ГИФУ
Микромонтаж кристаллов ИМС начинается после созда ния ИМС в пластине (после электрического зондового конт роля ИМС в составе пластин и контроля по внешнему виду). Основными операциями микромонтажа являются: 1) раз деление пластин на модули; 2) контроль по внешнему вид> и разбраковка; 3) посадка кристаллов ИМС в корпус или на коммутационную плату; 4) электрическое соединение выводов КП кристалла с КП корпуса или платы. Дополни тельной операцией, которая производится при микромонта же кристаллов ИМС, является их защита органическими компаундами.
Разделение пластин на кристаллы осуществляется тремя способами: 1) механическим скрайбированием (алмазным резцом); 2) фрезерованием (дисковой резкой); 3) с помощью лазерного луча. Несмотря на простоту и производительность процессов механического скрайбирования, от них в произ водстве МЭА практически отказались из-за большой ширины реза, значительной зоны нарушенного слоя, а также из-за достаточно большой вероятности возникновения микротре щин (рис. 4.1, табл. 4.1). Принципы разделения пластин на модули с помощью лазерного луча основаны на локальном взаимодействии луча лазера с материалом полупроводнико вой пластины, расплавлении и испарении его на линии раз дела. К преимуществам такого процесса следует отнести: универсальность (если для механического разделения необ ходимо освобождение от слоев оксида кремния, металлиза ции и т.п., для лазерного разделения это не обязательно), достаточную производительность, малую ширину реза, от сутствие механических повреждений. Недостатком процесса является большая вероятность попадания продуктов испа рения на поверхность пластины, которая тем больше, чем больше глубина реза. Существует и прямо пропорциональ