
книги / Микроэлектроника. Гибридные интегральные функциональные устройства
.pdf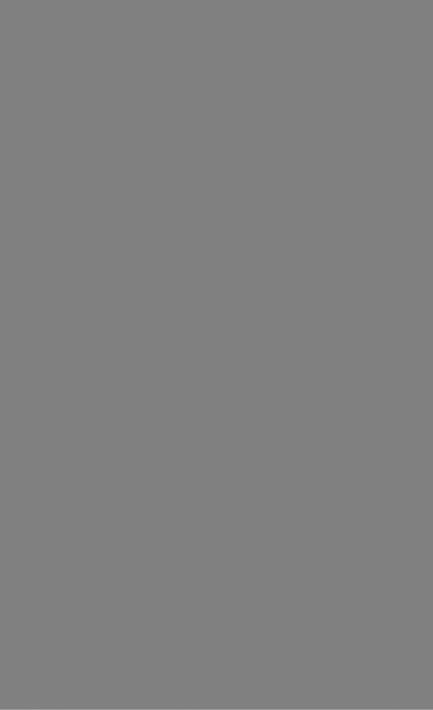
Следует отметить, что после надрезания пластины ее подвергают жидкостной очистке с последующей сушкой; часто для этого применяют и специальные щетки, особенно для лазерного разделения, так как для устранения послед ствий попадания продуктов испарения на поверхность пла стины ее защищают органическими пленками, которые тре буют последующего тщательного удаления.
Наибольшее применение в последнее время находит ме тод механического фрезерования с помощью специальных дисков, толщиной 19—60 мкм, имеющих высокую скорость вращения (36 000—50 000 об/мин). Образующаяся в процес се фрезерования кремниевая пыль легко удаляется струей деионизованной воды, подающейся на поверхность пла стины.
Установка (крепление) кристаллов ИМС на коммута ционную плату ГИФУ зависит от необходимости электрического соединения основания посадки с телом кри сталла и эффективного теплоотвода. Если такая необходи мость возникает, то для крепления кристаллов используют ся методы пайки. В других случаях применяются приклеи вание, причем для создания теплоотвода в состав клея вводят порошки диэлектриков с высокой теплопроводно стью (А120 3, ВеО), а для электрического контакта — по рошки благородных металлов с минимальным объемным удельным сопротивлением (серебро, золото).
Установка навесных элементов на коммутационную плату во многом зависит от способов присоединения выводов к кон тактным площадкам, например пайка выводов микроконден саторов и микрорезисторов не требует дополнительного ук репления. Обычно размеры устанавливаемых кристаллов ИМС (и других радиокомпонентов) составляют не менее
0,3 х 0,3 мм и не более 10 X 10 мм.
Обязательным требованием к клеям и компаундам, ис пользуемым для приклейки навесных элементов, является механическая прочность и хорошая адгезионная способность
как |
к поверхности подложек, |
так и к навесным элемен |
там |
(после их обезжиривания |
и очистки); адгезия — не |
менее 0,2—0,3 ГПа. Кроме того, нужно, чтобы рабочий ин тервал температур составлял 60— 125° С; удельное объемное сопротивление — более 1014 Ом см; tgfi ^ 1 Ю"3 вплоть до 100 МГц; ег ^ 3,5. Важно отсутствие в герметизирован ных объемах при температурах эксплуатации существенных выделений летучих компонентов клея, которые могли бы взаимодействовать с элементами микросборок и других ком понентов. При этом клей должен обеспечить легкий демон
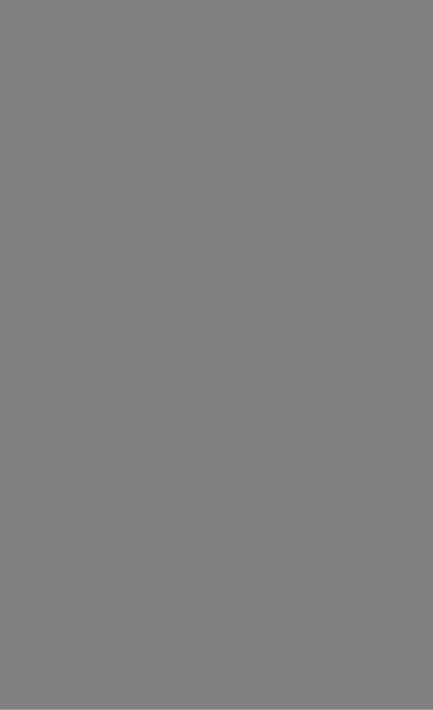
Характеристики |
|
Эпоксиды |
Силиконы |
Полиуретаны |
||
Максимальная |
темпера |
125 |
200 |
125 |
||
тура работы, °С |
|
|
||||
ТКЛР, 10 -6 К -' |
|
|
40—90 |
200—290 |
100—200 |
|
Теплопроводность, |
Вт/мК |
0,6-0,8 |
0,6—1,0 |
0 ,6 - 0,8 |
||
|
|
|
|
(без напол- |
(без напол |
(без напол |
|
|
|
|
нителя) |
нителя) |
нителя) |
|
|
|
|
0,8—2,2 |
1,0—2,5 |
|
|
|
|
|
(с напол |
(с напол |
|
Удельное объемное сопро |
нителем) |
нителем) |
|
|||
|
|
|
||||
тивление, |
Ом-см |
|
(25 °С, |
|
|
|
50% влажности) |
|
|
•10м—10‘6 |
1015— 1017 |
10м—10,в |
|
Относительная |
диэлект |
|
|
|
||
рическая |
проницаемость |
|
3,5—4,2 |
3 ,5 -4 ,0 |
||
(без наполнителя) |
|
|
3,5—4 |
|||
Электрическая прочность |
|
|
|
|||
(кратковременная) |
|
при |
8 0 -9 0 |
70—80 |
100— 120 |
|
23 °С, В/мм |
|
|
|
|||
tg6 |
|
|
|
0,002—0,05 |
0,001—0,007 |
0,015-0,07 |
Адсорбция воды |
за 24 ч, |
0,08—0,15 |
0,04—0,08 |
0,02—0,15 |
||
% |
|
|
воды |
|||
Поглощение паров |
|
|
|
|||
при 40°С и 90%-ной влаж |
|
88—125 |
2,8—6,0 |
|||
ности, 10_б г-мм/мм2 |
|
2,2—3,6 |
Для этого на основание корпуса или посадочного места на плате наносят золотое покрытие толщиной не менее 2,5 мкм. Меньшая толщина приводит к недопустимому уменьшению эвтектического спая, а также к тому, что на границе эвтек тики с материалом подложки (например, ковара) появля ются интерметаллические соединения (например, железа и кобальта). Наличие сплава железо — кобальт вблизи гра ницы раздела и в самой эвтектике может оказать неблаго приятное воздействие на качество эвтектики — произойдет охрупчивание и даже разрушение соединения. Оптималь ным соединением золото — кремний является равномерное соединение с толщиной электрического спая 5—7 мкм, со держанием кремния 2,4—2,8 % и площадью эвтектики под кристаллом не менее 70 %. Температура пайки составляет 630—700 К, давление на кристалл — около 0,1 ГПа.
Для улучшения смачивания паяемой стороны кристалла на нее наносят золотое покрытие с подслоем из никеля, которое вжигают перед пайкой при температуре 700— 720 К. При пайке кристаллов больших размеров в зазор до полнительно вводят фольгу из золота толщиной около
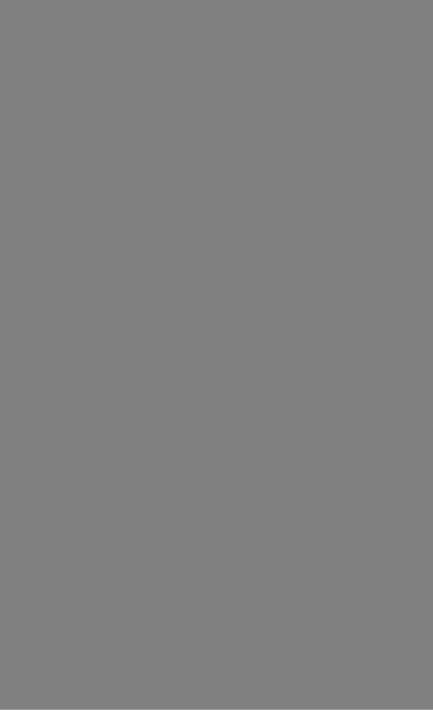
Алюминиевая проволока может изготавливаться как твердой, так и мягкой. Проволока из алюминия чистоты 99,999 % делается только мягкой. Сплавы алюминия (А1 — 4 % Си, А1— 1 % Si, А1 — 2 % Mg) более предпо чтительны для изготовления проволоки, чем чистый алю миний из-за повышенной прочности сварного соединения. Содержание легирующей добавки должно выдерживаться с большой точностью ( ± 15 %) при однородном ее распреде лении в проволоке. Содержание примесей в сплаве — не
Рис. 4.3. Диаграмма состояния системы
AI— Аи
более 0,1 %. При сварке золотой проволоки к алюминиевой контактной площадке кристалла или алюминиевой проволо ки к золоченой контактной площадке вследствие взаимодиффузии золота и алюминия образуются интерметаллические соединения типа Аих, А1У, которые снижают механические свойства сварного соединения. На рис. 4.3 представлена диаграмма состояния системы А1 — Аи. В зоне контакта образуются интерметаллиды типа AU4A1; AU5A12; AuAI; AUA12, причем зоны их распространения от золотой прово локи к алюминиевой контактной площадке находятся в той же последовательности, в которой они указаны в тексте. При повышенной температуре сварки, значительном времени воздействия, а также в присутствии фазы свободного крем ния образуется соединение АиА12 (пурпурная чума).
Для присоединения проволочных выводов к контактным площадкам кристаллов используется термокомпрессионная (в основном для золотых проводников) и ультразвуковая (для алюминиевых) сварка, а к контактным площадкам
ГИФУ — термокомпрессионная сварка или пайка (золотых проводников).
Термокомпрессионная сварка может проводиться встык (с образованием шарика) или внахлест (клином) — рис. 4.4. При термокомпрессионной сварке материал проволоки дол жен обладать высокой пластичностью (деформация при та
кой |
сварке |
составляет |
для |
1 |
|
1 |
||||||
золота 50 — 70 %, |
для алю |
|
||||||||||
миния 60—80 %). Ширина |
|
|
|
|||||||||
деформированной |
зоны |
про |
|
|
|
|||||||
водника |
в |
месте сварки |
2— |
|
|
|
||||||
3 диаметра |
проволоки. Наи |
|
|
|
||||||||
более приемлемой |
для обра |
yv |
у ** * |
|||||||||
зования |
прочного |
|
соедине |
|||||||||
ния |
с |
хорошей |
воспроизво |
а) |
|
б) |
||||||
димостью |
|
свойств |
(преж |
|
||||||||
|
|
|
|
|||||||||
де |
всего на |
автоматах) |
яв |
Рис. 4.4. Схема сварки шариков |
||||||||
ляется |
сварка |
шариком |
||||||||||
встык (а) и клином внахлест (б): |
||||||||||||
встык. |
Шарик |
формируется |
/ — проволоке; |
2 — пуансон; |
3 — под |
|||||||
в обычной среде с помощью |
ложка |
|
|
|||||||||
|
|
|
||||||||||
водородной |
горелки или элек |
|
|
в за |
||||||||
троискровым методом для золотой проволоки и |
||||||||||||
щитной |
среде |
азота |
или |
аргона — для |
алюминиевой. |
Автоматизированное присоединение золотых проводни ков термокомпрессионным способом производится в такой последовательности (рис. 4.5). Кончик проволоки, проходя-
Рис. 4.5. Последовательность операций |
термокомпрессионного |
|
присоединения золотой проволоки встык: |
|
|
а — |
образование ш арика; б — приварка ш арика; |
в — вторая сварка; г — отре |
зание |
проволоки |
|
щей через капилляр 2, расплавляется пламенем водородной горелки 1 до образования шарика (диаметр шарика 2—3 диа метра золотой проволоки). Кончиком капилляра шарик при жимается к нагретой приблизительно до 573 К контактной площадке на кристалле 3, при этом необходимый тепловой импульс подается и на капилляр. После сварки капилляр передвигается, образуя проволочную петлю, которая вытя-
гивается. Присоединение к выводу корпуса осуществляется тем же способом (с помощью оплавленного шарика) или сваркой (внахлест). Капилляр поднимается, проволока зажимается и обрезается. Однако такой микромонтаж в большинстве случаев не может быть осуществлен при мон
|
|
|
|
|
|
таже ГИФУ, так как процент |
||||||||||
|
|
|
|
|
|
выхода |
годных |
после |
опера |
|||||||
|
|
|
|
|
|
ций сборки кристаллов с вы |
||||||||||
|
|
|
|
|
|
соким |
уровнем |
интеграции |
||||||||
|
|
|
|
|
|
недостаточно |
высок. |
Кроме |
||||||||
|
|
|
|
|
|
того, |
после завершения сбор |
|||||||||
|
|
|
|
|
|
ки |
на кристалле следует про |
|||||||||
|
|
|
|
|
|
водить |
электротермическую |
|||||||||
|
|
|
|
|
|
тренировку |
(ЭТТ) |
ИМС. Не |
||||||||
|
|
|
|
|
|
обходимость |
электрической |
|||||||||
|
|
|
|
|
|
проверки прибора после сбор |
||||||||||
|
|
|
|
|
|
ки |
заставляет |
использовать |
||||||||
|
|
|
|
|
|
при |
|
монтаже |
|
бескорпусных |
||||||
|
|
|
|
|
|
БИС специальный технологи |
||||||||||
|
|
|
|
|
|
ческий |
корпус |
или промежу |
||||||||
|
|
|
|
|
|
точные |
диэлектрические под |
|||||||||
|
|
|
|
|
|
ложки |
с нанесенным |
слоем |
||||||||
|
|
|
|
|
|
коммутации |
|
(кроваткой), |
к |
|||||||
|
|
|
|
|
|
которым присоединяются вы |
||||||||||
|
|
|
|
|
|
воды |
от устанавливаемых |
на |
||||||||
|
|
|
|
|
|
них |
|
кристаллов, |
что |
позво |
||||||
|
|
|
|
|
|
ляет |
производить |
измерение |
||||||||
|
|
|
|
|
|
кристалла |
и |
его монтаж |
на |
|||||||
|
|
|
|
|
|
коммутационную |
плату вме |
|||||||||
Рис. 4.6. Конструкции бескор |
сте |
с |
«кроваткой» |
(рис. 4.6). |
||||||||||||
пусных |
ИМС |
с |
проволочными |
Применение |
технологическо |
|||||||||||
|а) и объемными (б) выводами, |
||||||||||||||||
го корпуса не позволяет авто |
||||||||||||||||
а также на полимерном носи |
||||||||||||||||
теле (в): |
|
|
|
|
матизировать |
процессы при |
||||||||||
О: / — кристалл; 2 — гибкие выводы; |
соединения |
проволочных |
вы |
|||||||||||||
3 — КП ; |
4 — |
плата; |
5 — клей; б : / — |
водов БИС к коммутационной |
||||||||||||
кристалл; |
2 |
— |
О В; |
3 — плата; |
4 — |
|||||||||||
КП ; о: / — КП |
для |
измерения на |
но |
плате. |
Использование |
«кро |
||||||||||
сителе; 2 — балочные выводы; 3 — |
||||||||||||||||
краевая перфорация; |
4 — кристалл |
|
ваток» |
дает |
|
возможность |
||||||||||
|
|
|
|
|
|
осуществлять |
|
автоматизиро |
ванную сварку проволочных выводов путем присоединения к «кроватке» выводов кристаллов, а затем к коммутацион ной плате. Вместе с тем использование промежуточных «кроваток» приводит к увеличению посадочного места крис талла на плате, а следовательно, к уменьшению плотности монтажа. Полная автоматизация процессов монтажа бескор пусных кристаллов на плату ГИФУ достигается применени-
ем организованных жестких выводов или беспроволочного соединения.
Для автоматического оборудования наиболее пригодна золотая проволока с относительным удлинением 3—7 %. При меньшем удлинении она становится очень жесткой, и перемычка формируется плохо, так как изгиб проволоки происходит вблизи шарика на участке, подвергнутом воз действию высоких температур в момент его образования. В проволоке возникают напряжения, которые при цикли ческих испытаниях приводят к разрушению перемычек. Проволока с удлинением свыше 7 % из-за высокой пластич ности в процессе скоростного формирования межсоединений провисает, что приводит к частым остановкам оборудова ния и заправкам проволоки в инструмент. Выбор проволоки зависит также от конструкции платы ГИФУ Если контакт ные площадки кристалла и платы расположены близко и имеют большой перепад по высоте, то, используя мягкую проволоку, можно избежать ее замыканий на край кристал ла и наоборот.
При работе на автоматическом оборудовании исполь зуется сварочный инструмент с большим диаметром капил лярного отверстия (1,5— 1,6 диаметра проволоки), чем при ручной сварке. Предпочтение отдается керамическим и ру биновым капиллярам, которые имеют более высокую чис тоту поверхности отверстия, не требуют нагрева и обеспечи вают возможность 0,5 и 1,0 млн. соединений.
Для расчета размеров и шага расположения контактных площадок кристалла необходимо определить площадь зоны присоединения с учетом деформации и смещения шарика от номинального положения. В этой зоне В не должны распола гаться открытые металлизированные дорожки проводников и активные области кристалла:
+ Д0 + Дс, |
(4.1) |
где йш — размер шарика после присоединения; Д0 — по грешность оборудования; Дс — погрешность, вносимая опе ратором при совмещении. Размер dit = dm + Adin, где dm — диаметр шарика, равный 2,0—3,0 диаметра присое диняемой проволоки; Adm—деформация шарика при сварке.
Погрешность оборудования Д0 зависит от погрешности центрирования шарика в сварочном инструменте (от типа используемого капилляра), а также погрешности расчета, задания и отработки программы координатными столами; она составляет 12— 15 мкм. Погрешность, вносимая опера тором при совмещении, Дс = 20-f-25 мкм.
Минимальный шаг между контактными площадками
кристалла |
|
Д/г ^ 0,55 + dKt |
(4.2) |
где dK— диаметр торца капилляра. Уменьшение шага Д/г увеличивает вероятность повреждения капилляром смонти рованных перемычек изделия. Размеры металлизации кон тактных площадок кристалла при выполнении условий (4.1) должны составлять не менее трех диаметров присоеди няемой проволоки.
Ультразвуковая сварка часто также требует нагрева свариваемых металлов, что благоприятно сказывается на образовании соединения, сокращает время процесса. К до стоинствам этого метода по сравнению с термокомпрессион ным следует отнести меньшую деформацию проводника при сварке (40—50 %), снижение вероятности образования ин терметаллических соединений (для золотого проводника), меньшую зависимость от состояния поверхности сваривае мых металлов. Часто одновременно с созданием танген циальных колебаний на пуансон подается импульс тока (импульсный косвенный нагрев).
Оптимальные амплитуды колебаний сварочного инстру мента составляют 1,5—2 мкм (частота колебаний порядка 60 кГц), а относительные смещения — около 1 мкм. Ультра звуковая сварка сопровождается увеличением температуры в зоне сварки.
Выход годных на операциях присоединения выводов по лупроводниковых приборов ультразвуком зависит от систем контроля, который может быть как прямым (на только что образованное сварное соединение подается контрольная нагрузка), так и косвенным (контролируется при сварке амплитуда скорости механических колебаний, напряжение или ток во входной цепи ультразвуковой колебательной системы и др.).
Следует отметить, что косвенные методы контроля не дают полной гарантии качества процесса, так как большое значение в процессе ультразвуковой сварки имеет состояние поверхностей соединяемых деталей. Изменение микрогеометрии поверхности контактных площадок кристалла, выз ванное условиями осаждения пленок алюминия, наличие на цих пленок поверхностно-активных веществ и загрязне ний (остатки защитных органических покрытий, жировые пятна и т. п.) влияет на коэффициент трения, что приводит к колебаниям от сварки к сварке максимального уровня амплитуды в начале процесса. Кроме того, этот уровень