
книги / Новые конструкционные материалы низкоуглеродистые мартенситные и порошковые стали
..pdfи содержит мелкопластинчатый перлит с равномерно распределенными включениями цементита.
Отжиг пористых деталей предпочтительно осуществлять в защитной атмосфере.
Аналогичные режимы применяют и для инфильтрированных метал лами сталей.
Нормализацию порошковых материалов из-за их повышенной склон ности к окислению производят реже, чем отжиг, так как эта операция все гда требует защитной атмосферы или специального метода охлаждения.
Таким образом, пористость, негомогенность твердого раствора и не однородность структуры материалов оказывают значительное влияние на процессы термической обработки. Особенно сильно это проявляется при закалке порошковых сталей. Температура нагрева порошковых сталей под закалку увеличивается с повышением гетерогенности твердого раствора и неоднородности структуры.
С увеличением пористости материалов резко уменьшается их тепло- и температуропроводность, ухудшается закаливаемость и, следовательно, возрастает критическая скорость закалки. Поэтому даже легированные по рошковые стали часто необходимо охлаждать либо в воде, либо в водном солевом растворе. Для порошковых высокоплотных сталей с однородной структурой режимы термической обработки такие же, как и для компакт ных сталей. При выборе скорости охлаждения необходимо учитывать по ристость, и если плотность сталей менее 7 г/см3, то охлаждение в жидких средах следует исключить.
5.6. М аркировка порошковых сталей и бронз
Условное обозначение марок состоит из букв и цифр. Конструкцион ные порошковые стали маркируют по ГОСТу. Буквы указывают: П - на принадлежность материала к порошковому; К - на назначение материала - конструкционный; остальные буквы - на содержание легирующих компо нентов (Д - медь, X - хром, Ф - фосфор, К - сера, М - молибден, Г - мар ганец, Т - титан, Н - никель).
Основу материала в обозначении марок не указывают. Цифры, стоя щие после букв ГТК, указывают среднюю массовую долю углерода в сотых долях процента. Массовую долю углерода, равную 1 %, в обозначении марки материала не указывают.
Цифры, стоящие после букв, указывают массовую долю в материале легирующих компонентов в процентах; отсутствие цифры означает, что массовая доля компонента меньше единицы или равна единице.
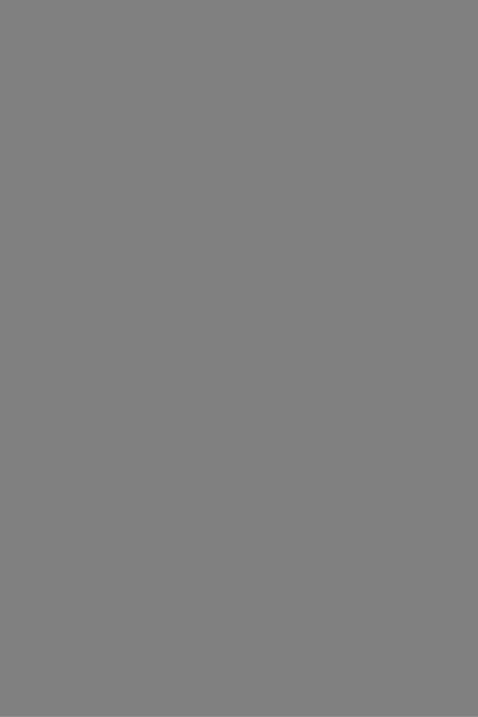
Марка |
с |
|
ПК10Н2М |
||
£0,30 |
||
ПК10Н2Д2 |
£0,30 |
|
ПК10Н4Д4 |
£0,30 |
|
ПК10Н2Д6 |
£0,30 |
|
ПК40НМ |
0,31-0,60 |
|
ПК40Н2М |
0,31-0,60 |
|
ПК40Н2Д2 |
0,31-0,60 |
|
ПК40ЮД2Х |
0,31-0,60 |
|
ПК40Н2Д2М |
0,31-0,60 |
|
ПК40Н4Д2М |
0,31-0,60 |
|
ПК70Н2Д2 |
0,61-0,90 |
|
ПК70ХЗ |
0,61-0,90 |
|
ПКХ6 |
0,91-1,20 |
|
ПК40Х2 |
0,31-0,60 |
|
ПК40Г2 |
0,31-0,60 |
|
ПК40ХН2Г |
0,31-0,60 |
|
ПКГ13 |
0,91-1,20 |
|
ПК10Х13М2 |
£0,10 |
|
ПК10Х25 |
£0,10 |
|
ПК20Х13 |
0,10-0,30 |
|
ПК40Х13М2 |
0,30-0,50 |
|
ПК10Х17М2 |
£0,15 |
|
ПК10Х18Н9Т |
£0,10 |
|
ПК10Х18Н15 |
£0,10 |
|
Массовая доля элементов |
Мл |
||
Си |
Ni |
Мо |
Сг |
|
- |
- |
0,3-0,7 |
- |
- |
1-3 |
1-3 |
- |
- |
- |
2-6 |
2-6 |
- |
- |
- |
4-8 |
1-3 |
0,3-0,7 |
- |
- |
- |
0,5-1,0 |
0,3-0,7 |
- |
- |
- |
1-3 |
0,3-0,7 |
- |
- |
1-3 |
1-3 |
- |
- |
- |
1-3 |
2-4 |
- |
0,5-1,5 |
- |
1-3 |
1-3 |
0,3-0,7 |
— |
— |
1-3 |
3-5 |
0,3—0,7 |
— |
— |
1-3 |
1-3 |
|
|
|
— |
— |
— |
2,0-4,0 |
_ |
|
|
|
||
- |
- |
- |
5,0-7,0 |
- |
- |
- |
- |
1,0-3,0 |
- |
- |
- |
- |
- |
1,0-3,0 |
- |
1-3 |
- |
0,5-1,5 |
0,5-1,5 |
- |
- |
- |
- |
12,0-14,0 |
- |
- |
1,0-3,0 |
12,0-14,0 |
- |
- |
- |
- |
24,0-26,0 |
- |
- |
- |
- |
12,0-14,0 |
- |
- |
- |
1,0-3,0 |
12,0-14,0 |
- |
- |
1,0-3,0 |
- |
16,0-18,0 |
- |
- |
8,0- 10,0 |
- |
17,0-19,0 |
- |
- |
14,0-16,0 |
- |
17,0-19,0 |
- |
|
|
|
|
*При необходимости легирования серой массовую долю указывают в норматив но-технической документации на конкретное изделие или на чертеже конструкторской документации.
П р и м е ч а н и е : необходимость контроля химического состава материалов должна быть указана в нормативно-технической документации или иа чертеже на кон кретное изделие.
Цифры, стоящие после букв, указывают содержание определенного элемента в материалах сходных композиций, отличающихся процентным содержанием одних и тех же элементов.
Примеры условных обозначений:
1. Сталь порошковая антифрикционная с содержанием углерода 0,5 до
1,2 %: |
|
ПА-ЖГр |
ГОСТ 26802-86. |
2. Сталь порошковая антифрикционная медистая с содержанием углеро
да 0,5 - 1,2 % и меди 2,5-3.5 %: |
|
ПА-ЖГрД |
ГОСТ 26802-86. |
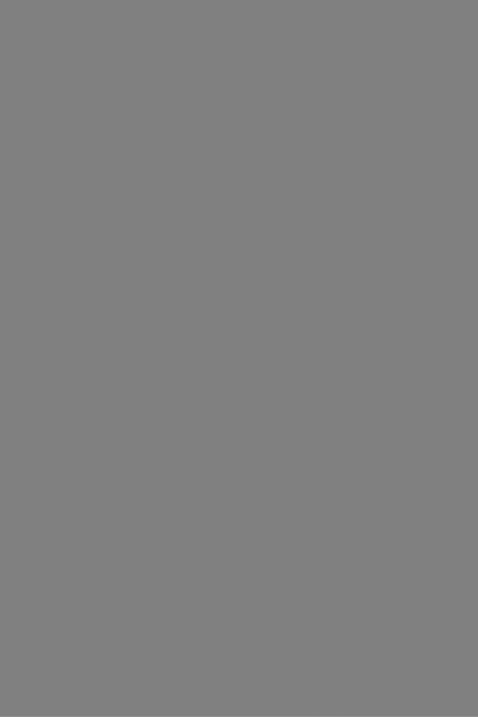
Контрольные вопросы к главе 5
1. Основные промышленные методы производства металлических по рошков.
2.Как связана структура и свойства частиц порошков с методами про изводства?
3.Технология приготовления порошковых смесей.
4.Уплотнение при прессовании, связь между плотностью и давлением прессования.
5.Движущая сила спекания.
6.Механизмы роста площади контакта между частицами.
7.Объемная усадка под действием сил поверхностного натяжения (уравнение Ивенсена).
8.Эффекты Френкеля и Киркендалла.
9.Основные легирующие элементы порошковых сталей.
10.Особенности выбора составов порошковых сталей (химический и гранулометрический состав, способ производства порошков).
11.Влияние пористости на механические свойства порошковых мате риалов.
12.Зависимость трещиностойкости от пористости, роль пор и примесей.
13.Припуски, точность и чистота поверхности при калибровании по рошковых сталей.
14.Основные методы и особенности термообработки порошковых ста
лей.
15.Принципы маркировки конструкционных порошковых сталей.
16.Принципы маркировки антифрикционных порошковых сталей.
15.Маркировка порошковых бронз.
Список литературы к главе 5321
1. Курилов П.Г. Производство конструкционных изделий из порошков на основе железа / П.Г. Курилов, В.М. Рыбаулин. М: Металлургия, 1992.
128с.
2.Порошковая металлургия. Материалы, технология, свойства, облас ти применения: Справочник / Под ред. И. М. Федорченко. Киев: Наук, думка, 1985. 624 с.
3.Роман О.В. Справочник по порошковой металлургии: порошки, ма териалы, процессы / О.В. Роман, И.П. Габриелов. Минск: Беларусь, 1988. 175 с.

21.Блантер М.Е. Теория термической обработки. М.: Металлурги
1984. 328 с.
22.Karlkeins К. Untersuchungen zur Optimierung der Festi keitskennwerte von schwach verdichteten Sinterwerkstoffen // Dort. - Ing. abt.
Maschinenbau Ruhr. Unt. Bochum. 1977. 106 p.
23.Hamiuddin Md. Role of Molybdenum in Sintered Steels // Powder Met allurgy International. Vol. 15. № 3. 1983. P. 7-12.
24.Особенности формирования структуры спеченных хромомолибде новых сталей / В.Н. Анциферов, Л.М. Гревнов, В.И. Овчинникова и др. // Исследование технологии металлических порошков и спеченных материа лов. Свердловск, 1980. С. 69-75.
25.Черепанова Т.Г. Особенности растворения карбидов хрома и мо либдена в железной матрице / Т.Г. Черепанова, В.И. Овчинникова // По рошковая металлургия / Перм. политехи, ин-т. Пермь, 1979. С. 56-62.
26.Балынин М.Ю. Научные основы порошковой металлургии и ме таллургии волокна. М.: Металлургия, 1972. 335 с.
27.Белов С.В. Пористые металлы в машиностроении. М.: Машино строение, 1981. 247 с.
28.Андреевский Р.А. Прочность тугоплавких соединений / Р.А. Анд реевский, А.Г. Ланин, Г.А. Рымашевский. М.: Металлургия, 1974. 232 с.
29.Мешков Ю.Я. Физические основы разрушения стальных конструк ций. Киев: Наук, думка, 1981. 240 с.
30.Нотт Дж.Ф. Основы механики разрушения: Пер с англ. М.: Метал
лургия, 1978. 256 с.
31. Жердин А.Г. Трещиностойкость и вязкохрупкий переход в порош ковых материалах / А.Г. Жердин, С.А. Фиртсов, Л.Г. Штыка // Технологи ческая и конструкционная пластичность порошковых материалов. Киев: Изд-во ИПМ АН УССР, 1988. С. 89-92.
32.Взаимосвязь трещиностойкости с долей межзеренного разрушения порошкового железа / А.С. Драчинский, А.В. Крейнов, А.Е. Кущевский и др. // Порошковая металлургия. 1986. № 1. С. 43-45.
33.Об оценке параметров вязкости разрушения пористых материалов / С.М. Платова, В.Г. Кудряшов, М.Л. Бернштейн и др. // Физико-химическая механика материалов. 1974. № 5. С. 20-24.
34.Влияние пористости на механические свойства спекаемых мате риалов / М. Шлесар, Л. Парилак, К. Пеликан и др. // Семинар по развитию
ииспользованию порошковой металлургии в машиностроении. Минск, 1985. 17 с.
35.Влияние пор на разрушение железа / В.Н. Анциферов, С.Н. Пещеренко, А.А. Шацов, Н.Н. Масленников // Проблемы прочности. 1989.
№ 2. С. 20-22.
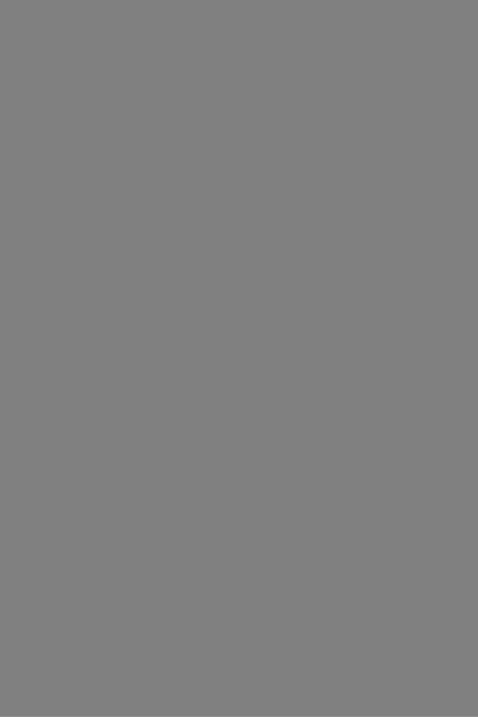
6. ИЗНОСОСТОЙКИЕ ПОКРЫТИЯ, МОДИФИ1ЩРОВАННЫЕ СЛОИ И ПРИНЦИПЫ КЛАССИФИКАЦИИ КОМПОЗИЦИОННЫХ
МАТЕРИАЛОВ
Удовлетворить противоречивые требования к поверхностным и объ емным свойствам можно путем создания композиций с послойным распо ложением материалов, выполняющих различные функции.
Нанесение покрытий на те или иные материалы не просто улучшает их характеристики, а приводит к образованию нового композиционного материала с присущим ему комплексом свойств, который должен быть уч тен при разработке конструкций машин и механизмов [1 ].
6.1. Покрытия, получаемые методами химического осаждения из газовой фазы
Методы химического осаждения из газовой фазы (или газофазные ме тоды) основаны на осаждении покрытия на нагретую подложку в результа те разложения относительно нестойких газообразных веществ или взаимо действия двух или более газообразных веществ (или переведенных в паро вую фазу твердых веществ) с образованием на поверхности слоя химиче ского соединения.
Наибольшее распространение получил метод осаждения покрытий из карбида титана на нагретые до высокой температуры (1000-1100 °С) детали и инструмент в результате химической реакция двух находящихся в газообразном состоянии веществ:
TiCl4 + СН4 -> TiC + 4НС1.
Получаемые таким образом покрытия в несколько раз повышают стойкость неперетачиваемого инструмента из твердых сплавов.
Из-за высоких температур, необходимых для прохождения реакции образования прочного соединения с подложкой, этот метод непригоден для закаленных углеродистых и быстрорежущих сталей. Однако можно наносить покрытия из износостойких соединений при значительно более низких температурах (табл. 6.1 ) или закаливать детали сразу после нанесе ния покрытий.
Существенным усовершенствованием процессов газофазного осажде ния покрытий явилось создание установок, работающих по замкнутому циклу, без выброса вредных веществ в атмосферу.
Термовакуумный метод нанесения покрытий основан на конденсации на поверхностях деталей пленки металла или химического соединения, пе реведенного в парообразное состояние нагревом наносимого вещества (на греванием сопротивления, электронным лучом, индукционным методом,
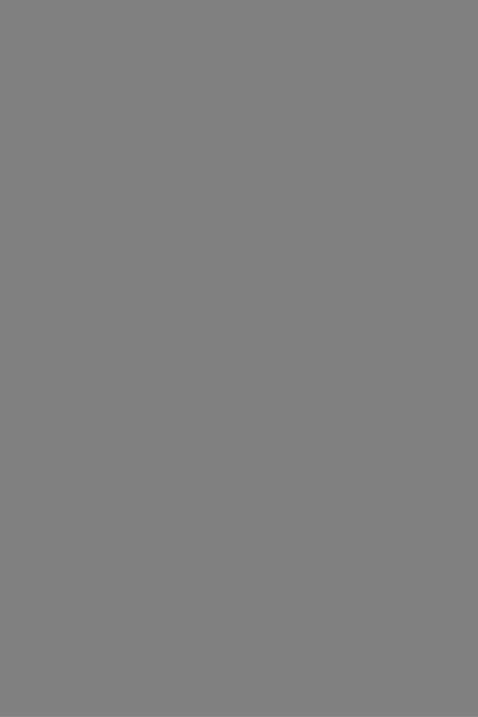