
книги / Новые конструкционные материалы низкоуглеродистые мартенситные и порошковые стали
..pdf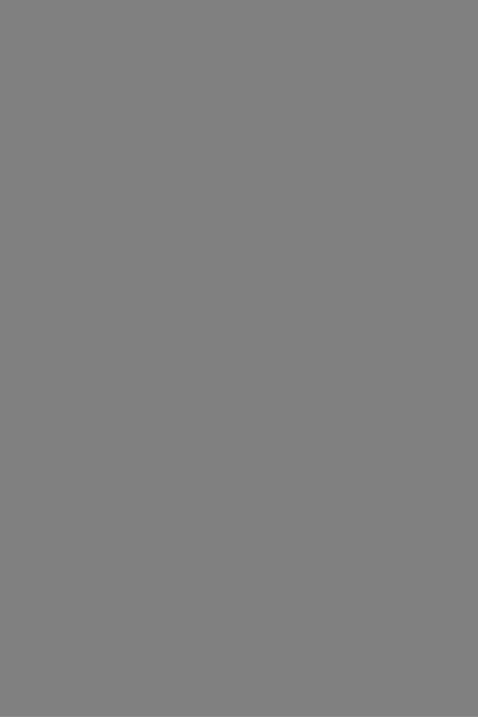
нетической энергией, о твердую поверхность освобождается большое ко личество теплоты и их температура может достигать 4000 °С.
Плазменный способ обеспечивает нагрев частиц до более высоких температур, чем детонационный. Ограничения по температуре при детона ционном способе нанесения покрытий компенсируются большей кинети ческой энергией частиц, что позволяет наносить покрытия и из тугоплав ких материалов. Благодаря высоким скоростям напыляемых частиц дето национные покрытия по сравнению с плазменными и тем более с обычны ми газопламенными имеют большие высокие плотность (98-99 %) и проч ность сцепления с основой. Существенным преимуществом детонационно го метода перед газопламенным и плазменным методами является его дис кретность, а вследствие этого и меньшая теплонапряженность. Нагрев об рабатываемой детали в процессе напыления может не превышать 200 °С.
Освоено нанесение детонационным методом покрытий самого разно образного состава: твердосплавных с использованием различных карби дов (вольфрама, хрома) и связок (Со, Ni, Ni + Сг); оксидных (из оксидов алюминия, титана и хрома); металлических. Это позволяет многократно повышать износостойкость деталей машин и инструмента.
6.3. Лазерные методы модифицирования и легирования поверхностных слоев, электроискровые и гальванические покрытия
Возможности значительного повышения износостойкости поверхно стей появились с разработкой промышленных лазеров. Благодаря высокой плотности энергии в луче лазера (до 109 Вт/см2) возможен быстрый нагрев тонкого поверхностного слоя металла, вплоть до его расплавления. После дующий быстрый отвод теплоты в объем металла приводит к закалке по верхностного слоя с приданием ему высокой твердости и износостойкости. (Процессы, происходящие в поверхностном слое, а следовательно, и его свойства определяются мощностью и длительностью действия лазерного луча.) Можно также легировать поверхностный слой, предварительно на нося на него каким-либо способом слой легирующего компонента и затем расплавляя его лучом лазера, а также наносить покрытия лазерным лучом, вводя в него порошок напыляемого материала.
Метод электроискрового легирования основан на переносе материала электрода (преимущественно материала анода) при импульсном искровом разряде в газовой среде на обрабатываемую поверхность. Для нанесения электроискровых покрытий применяют вибрирующие электроды.
Нанесение металлических покрытий сохраняет в материале основы исходный фазовый состав. При легировании соединениями (метал лоподобными) происходит, как правило, их химическое взаимодействие с
материалом основы и образуются соединения элементов, входящих в на носимый материал, с элементам основы. Нанесение электроискровых по крытий существенно повышает износостойкость и антифрикционность по верхностей. Представление о возможности детанационных покрытий дает табл. 6.2 .
Таблица 6.2 Относительная износостойкость детонационных покрытий
(толщиной 150-200 мкм) из твердых сплавов
Материал покрытия |
Относительный износ |
Относительная изно |
|
состойкость |
|||
ВТЗ-1 без покрытия |
|
||
1,00 |
1,00 |
||
ВК8 |
0,553 |
1,81 |
|
ВК15 |
0,350 |
2,86 |
|
ВК20 |
0,282 |
3,55 |
Дискретность и пористость покрытий, небольшая их толщина, низкая производительность процесса их нанесения, высокая шероховатость обра ботанных поверхностей, наличие остаточных напряжений растяжения пре пятствуют широкому внедрению этих покрытий.
Электроискровое легирование применяют для увеличения надежности деталей машин, приборов и механизмов, инструмента (режущего и дефор мирующего), кокилей для литья металлов, а также для размерного восста новления деталей машин.
Гальваническими методами можно наносить покрытия из металлов, сплавов и композиционных материалов. Введение в состав покрытий на основе хрома, железа и никеля частиц других материалов существенно по вышает триботехнические свойства этих покрытий. Введение порошков карбидов, оксидов, боридов, алмаза и т.п. позволяет существенно повысить износостойкость покрытий, а введение халькогенидов, графита, полиме ров - антифрикционность покрытий. Технология электролитического оса ждения дает возможность получать покрытия, содержащие до 40 % частиц
иимеющие толщину до 100 мкм.
Впокрытия вводят карбиды (WC, TiC, ZrC, HfC, SiC, B4C), бориды (ПВ2, ZrB2, HfB2, TaB2), силициды (TaSi2), нитриды (BN, SisN,*), оксиды
(А120 з, Sr2C>2, Si02, Zr0 2 , ТЮ 2), сульфиды (MoS2, WS2).
При одновременном введении в покрытие частиц с высокой твердо стью и частиц твердой смазки износостойкость и антифрикционные свой ства его повышаются. Наилучшими триботехническими свойствами обла дают композиционные покрытия на основе никеля.
Металлические и неметаллические коррозионно-стойкие покрытия являются распространенным средством повышения долговечности изделий при работе в коррозионной среде.
Металлические покрытия по механизму влияния делят на катодные и анодные.
Катодные покрытия изготовляют из более электроположительного металла. Они экранируют анодные участки металла и повышают электрод ный потенциал поверхности. Вследствие высокой коррозионной стойкости они долговечны, но не выносят механических повреждений. Если есть ца рапины, то основной металл при наличии покрытия - второго катода - корродирует быстрее, чем металл без покрытия.
Покрытия из свинца или олова (лужение) для железа и низкоуглеро дистой стали являются катодными. Свинец и олово - более электрополо жительные металлы, чем железо в атмосфере воздуха, неорганических и органических неокисляющих кислотах. Луженую сталь применяют в пи щевой промышленности, а покрытие свинцом - в химической.
Анодные покрытия изготовляют из более электроотрицательного ме талла. Разрушаясь, он предохраняет металл от коррозии. При механиче ских повреждениях такое покрытие играет роль дополнительного более электроотрицательного анода, который забирает большую долю коррози онного тока и тем самым защищает основной анод. Анодные покрытия применяют при атмосферной и морской коррозии. Анодными, например, для железа и углеродистых сталей являются покрытия из цинка или кад мия.
Неметаллические покрытия включают в себя вещества с ионным или молекулярным типом связи, являющиеся по своим электрическим свойст вам диэлектриками или полупроводниками. Из-за большого омического сопротивления коррозия в этих покрытиях не развивается. В качестве не металлических покрытии применяют оксиды, второпласты, краски, эмали, их основной недостаток - высокая хрупкость, т.е. они легко откалываются и ломаются.
6.4. Композиционные материалы
Композиционными называют сложные материалы, в состав которых входят сильно отличающиеся по свойствам нерастворимые или малорас творимые друг в друге компоненты, имеющие ярко выраженные границы раздела. Как видно из этого определения, большинство многокомпонент ных материалов являются композиционными.
Композиционные материалы (КМ) по удельным характеристикам прочности и жесткости, усталостной прочности, длительной прочности и другим свойствам превосходят все известные материалы. Принципы соз-
Дания КМ заимствованы у природы, а их свойства подчиняются общим за кономерностям, позволяющим проектировать изделия с заданными экс плуатационными характеристиками.
Всостав композиционного материала входят вязкие, пластичные фазы
иупрочнители. Упрочнитель обладает высокими прочностью, твердостью
имодулем упругости. Часто упрочнитель называют армирующим компо нентом или наполнителем. Наполнитель - более общее название, не кон кретизирующее целей его введения.
Формально композиционные материалы классифицируют в зависимо сти от схемы армирования. Существует три основные группы наполните лей. Нуль-мерные наполнители имеют в трех направлениях малые размеры одного порядка (частицы). Для одномерных наполнителей характерны ма лые размеры в двух направлениях и значительно превосходящий их размер
втретьем направлении (волокна); двумерные наполнители имеют один ма лый размер и два размера, значительно его превосходящие (ткани). Воз можности армирования не ограничены типом наполнителя. Например, из одномерных и двумерных наполнителей создают материалы с объемным, трехмерным расположением упрочняющего компонента.
Связь между составом и свойствам рассмотрим на примере волокни стых композиционных материалов (ВКМ) [2, 3]. Наибольшие свойства, достижимые для данного типа упрочнителя и матрицы подчиняются пра вилу аддитивности
£ С= £ В ГВ+ £ М(1-ГВ), |
(6.1) |
где £ с, £ в, Ем- модули Юнга композиционного материала, волокон и мат рицы; VB- объемная доля волокон.
Эксперименты, выполненные для алюминиевой матрицы (Е = 70 ГПа) с 50 об. % волокон бора (Е = 420 ГПа), показывают (70*0,5 + 420*0,5 = = 245 ГПа), что расчетный модуль упругости (245 ГПа) хорошо согласо вать с реальным модулем упругости КМ (240 МПа).
Наибольшую величину временного сопротивления КМ можно вычис лить путем совместного решения уравнений напряжений и деформаций:
<7с |
<Гм |
*** 0в(1 — Гв), |
( 6.2) |
е с ” |
е в V . + |
e M ( \ — Гв), |
(6.3) |
где ас, Ов, &м- предел прочности композиционного материала, волокон и матрицы и в момент разрушения волокон; 6С, ем, €в - деформация компози ционного материала, матрицы и волокон.
Из уравнений (6.2), (6.3) видно, что влияние волокон из-за их малой разрушающей деформации при относительно небольшой их доле (порядка 5-10 %) невелико, механические свойства у КМ могут быть даже ниже,
чем у матрицы. Затем прочность КМ линейно возрастает с увеличением содержания упрочнителя до 40-50 %. Стабилизация свойств КМ с 40-50 % упрочнителя и даже некоторое понижение характеристик прочности обу словлено повреждением волокон на стадии изготовления деталей. Количе ство поврежденных волокон тем выше, чем больше их объемная доля.
Особенно эффективно применение ВКМ для изготовления деталей, испытывающих усталостные нагрузки. Усталостная прочность ВКМ с алюминиевой матрицей, армированной борными волокнами, может втрое превосходить усталостную прочность матричного сплава. Но для реализа ции высоких свойств ВКМ необходимо добиться оптимальной связи меж ду компонентами. Поэтому КМ также классифицируют по характеру взаи модействия. По этому признаку ВКМ условно делят на три класса.
Первый класс - волокно и матрица взаимно не реакционноспособны и не растворимы. К этому классу относятся системы Си - AI2O3, Ag - AI2O3, А1 - В (покрытие BN), Mg - В, А1 - сталь (псевдопервый класс), А1 - В (псевдопервый класс), А1 - Si3N4 (псевдопервый класс). Композиты псев допервого класса способны к взаимодействию при изменении условий по лучения, например при повреждении окисной пленки.
Второй класс - компоненты взаимно не реакционноспособны, но рас творимы. Сюда относят ВКМ Си (Cr) - W, эвтектики, Nb - W, Ni - С, Ni - W (при низких температурах система реакционноспособна с образованием Ni4W).
Третий класс - волокно и матрица реагируют с образованием химиче ских соединений. Это самый обширный класс, к которому относят Ti - AI2O3, Ti - В, Ti - Si3N4, А1 - SiC>2 и А1 - С (при температуре выше 970 К).
Современный подход к разрушению КМ на первый план выдвигает взаимодействие на границе раздела и предполагает необходимым услови ем достижения оптимальных свойств КМ существование механического континуума, т.е. обеспечение хорошей механической связи между компо нентами, и химического дисконтинуума, прерывистого изменения состава за счет образования химических соединений на границе раздела. Но хими ческое соединение может вызвать катастрофическое разрушение, поэтому рассмотрим его роль на примере системы Ti - В.
Теоретическая прочность волокна в первом приближении равна £ в/10, где £в - модуль упругости волокна. Реальная прочность зависит от дефек тов волокна, влияние которых можно оценить с помощью коэффициента концентрации напряжений
А:в= £ в/(105в), |
(6.4) |
где SB- прочность волокна.
Типичные значения Къборных волокон - от 10 до 20, что соответству ет прочности 4200-2100 МПа. Наиболее значительными в данном случае являются внутренние дефекты, получаемые при выращивании волокон.
Меткалф [2] предположил, что химическое взаимодействие компо нентов, в результате которого формируется поверхностный слой из про дуктов реакции, приводит к образованию трещин в зоне этого взаимодей
ствия при деформации Б/, определяемой выражением |
|
8/ = Э Д , |
(6.5) |
где Si - прочность; £/ - модуль упругости вещества зоны взаимодействия. Разрушающая деформация диборида титана равна 0,25 %, а волокон
бора - 0,6 %. Соответствующий коэффициент концентрации напряжений
Ki = B(x/r)U2, |
(6.6) |
где В - коэффициент, определяемый распределением напряжений вокруг трещины. (В своих расчетах Меткалф принял В = 1); х - глубина трещи ны; г - радиус вершины трещины.
Первого критического значения зона взаимодействия достигает при
К, = КВ:
(*кр)1 = [£»/( ю^в)]2/-. |
(6.7) |
Если толщина слоя продуктов взаимодействия превосходит (лгкр)ь то разрушение начинает определяться трещиной в этой зоне. При разрушении
волокон в композите деформация |
|
8в = (1/10Д)(л/г)1/2. |
(6.8) |
Путем подстановки уравнения (6.5) в уравнение (6.8) несложно найти вторую критическую величину зоны взаимодействия, при которой волок но, а следовательно и ВКМ, разрушается в момент растрескивания боридного слоя:
(*Kp)ii = [M10S,)]2r . |
(6.9) |
Минимальное значение г не может быть меньше радиуса диборида ти тана (0,0003 мкм), но практически г находится в пределах от 0,001 до 0,0015 мкм. Если толщина диборида меньше критического размера (поряд ка 0,4 мкм), то трещина в боридном слое не влияет на характер разрушения волокон.
Итак, по критическому размеру зоны взаимодействия можно опреде лить максимально допустимые параметры технологического процесса по лучения КМ. Минимальную же величину определяет ее способность зоны взаимодействия перераспределять напряжения между компонентами КМ без разрушения [4].
Контрольные вопросы к главе 6
1.Технология получения газофазных покрытий и их свойства.
2.Технология получения, структура и свойства ионно-плазменных и детонационных покрытий.
3.Структура и свойства слоев, полученных лазерными методами.
4.Получение и свойства электроискровых покрытий.
5.Получение и свойства гальванических покрытий.
6. Принципы классификации композиционных материалов.
7. Связь между составом и свойствами.
8. Роль границ раздела между фазами.
Список литературы к главе 6
1. Конструкционные материалы: Справочник / Под ред. Б.Н. Арзамасова. М.: Машиностроение, 1990. 688 с.
2.Композиционные материалы: В 8 т.: Пер. с англ. / Под ред. Л. Браутмана и Р. Крока. М.: Мир, 1978. Т.1. Композиционные материалы с ме таллической матрицей / Под ред. А. Меткалфа. 1978. 438 с.
3.Композиционные материалы: В 8 т.: Пер. с англ./Под ред. Л. Браутмана и Р. Крока. М.: Машиностроение, 1978. Т.4. Композиционные ма териалы с металлической матрицей / Под ред. К. Крейдера. 1978. 503 с.
4.Шацов А.А. Оценка прочности продуктов взаимодействия в компо зиционных материалах Ti - В, А1 - В // Вестник ПГТУ. Порошковая метал лургия. Вып. 5. Пермь, 2001. С.85-86.
7.СОВРЕМЕННЫЕ ТЕХНОЛОГИИ ПРОИЗВОДСТВА ДЕТАЛЕЙ ИЗ КОНСТРУКЦИОННЫХ ПОРОШКОВЫХ СТАЛЕЙ
Ограниченность природных ресурсов, повышение цен на стратегиче ские материалы, с одной стороны, и необходимость поддержания темпов экономического развития и роста производительности труда, с другой - обусловили рост производства порошковых материалов в последние годы в Европейских странах и Северной Америке на уровне 7-10 % в год. Даль нейшие высокие темпы развития отрасли будут возможны, если одновре менно с повышением прочности, трещиностойкости, износостойкости и размерной точности сохранится низкая себестоимость производства. Для наиболее распространенных конструкционных сталей, применяемых для изготовления массовых деталей, следует в ближайшие годы ожидать дос тижения сочетания прочности на уровне 1,0-2,0 ГПа и трещиностойкости
40-50 МН/м3/2 Основными направлениями улучшения эксплуатационных характеристик деталей из спеченных сталей являются: повышение плотно сти изделий, упрочнение их за счет легирования металлической матрицы, термообработка.
Следует заметить, что каждый из приведенных методов имеет свои недостатки: в промышленных условиях не достижимы высокие давления прессования; использование легирующих добавок уже в количестве не скольких процентов часто приводит к снижению точности конечных раз меров изделий и к увеличению стоимости продукции; термообработка по ка не нашла широкого применения из-за несовпадения оптимальных ре жимов для традиционных и порошковых сталей и невысокой ее эффектив ности при повышенной пористости стали.
Принятые методы улучшения плотности на практике сводят к двум подходам: механическому и химическому. Самым простым является по вышение давления прессования, но в промышленных масштабах оно огра ничено и не превышает 800 МПа, при этом плотность составляет примерно 7,1 г/см3 [1]. Порошки высокой прессуемости, например марки АВС 100.30 [2], не нашли широкого применения из-за их высокой стоимости (для рос сийских потребителей на уровне 1050 USD за тонну). При повышении давления прессования плотность возрастает незначительно, поэтому ис пользуют доуплотнение. Себестоимость продукции, изготовленной по технологии, включающей допрессовку, примерно на 40 % выше. Однако при получении изделий с повышенной прочностью двойное прессование и спекание оправдывают себя.
Конкурирующее направление повышения механических свойств кон струкционных порошковых сталей - горячая штамповка (или динамиче ское горячее прессование - ДТП) пористых заготовок с последующей их термической обработкой. Горячештампованная термообработанная никельмолибденовая сталь (ПК60Н2М) характеризуется высоким уровнем прочностных свойств: прочность при испытании на растяжение а в = = 1300 1400 МПа, при испытании на изгиб а изг = 2200 2300 МПа, ударная вязкость ан = 185 кДж/м2 [3]. Применение горячей штамповки по зволяет повысить относительную плотность пористых заготовок, на при мере стали ПК40Н4Д2М, по сравнению с однократным прессованием с 85,9 до 98,9 %, двукратным - с 93,8 до 99,5 %.По механическим свойствам горячештампованные образцы мало отличаются от компактных: предел прочности (ав) - 1300 МПа, твердость (HRC) - 40, ударная вязкость (KCV) - 500 кДж/м2 [4]. Использование карбонильных порошков в неко торых случаях способствует улучшению механических характеристик и при ДТП. Карбонильные порошки активируют спекание, уменьшают сред ний размер пор, интенсифицируют диффузионные процессы. Оптимальное
сочетание механических свойств обеспечивает добавка 20 % карбонильно го порошка [5], но технологические характеристики шихты при этом ухудшаются. США является лидером по внедрению штамповки в техноло гии порошковой металлургии, и, хотя уровень в 90-х годах был невелик, оценки [6] показывают, что в начале следующего века в США, Японии и Западной Европе этим методом будут производить 30 % конструкционных порошковых изделий.
Внедрение динамического прессования сдерживается тем, что это на правление во многом лишает порошковую металлургию ее преимуществ, связанных с низкой себестоимостью продукции и высоким коэффициен том использования металла.
Одним из методов получения беспористых материалов является экс трузия. В работе [7] описаны результаты исследований, выполненных с целью определения оптимальных параметров экструзии мартенситностареющих сталей. Образцы изготавливали из порошка стали Н18М5К10, полученного восстановлением оксидов [8]. Опытные партии изделий име
ли механические свойства (ав= 2300 ... 2400 МПа, |
8 = 7 8 %, \|/ = 45 |
50 %, KCU = 350 ... 400 кДж/м2, HRC = 54 56), |
соответствующие стан |
дартным, а в некоторых случаях превосходили их. Ранее порошковые мар- тенситно-стареющие стали (ПМСС) производили только из особо чистых компонентов [9]. Оптимальные свойства ПМСС получены при содержании титана 2 %, причина повышенной концентрации титана состоит в непол ном растворении дисперсных порошков Ti при аустенизации (часть титана расходуется на образование устойчивых химических соединений). Пере ход к оксидной технологии означает несомненный прогресс, но количест во операций и параметры технологических процессов указывают на то, что по соображениям экономической целесообразности в ближайшее время в промышленности эти технологии реализованы не будут.
Особый интерес представляет высокотемпературная термомеханиче ская обработка (ВТМО), которая способствует повышению прочности при сохранении пластичности. Основными параметрами, определяющими «эффект» ВТМО, являются степень, скорость и температура деформации, а также последеформационная выдержка, за которой следует закалка (если выдержка исключается, закалка - немедленная). С помощью этих парамет ров подавляется (или частично задерживается) процесс рекристализации, так как ВТМО осуществляется в высокотемпературной области. Влияние этих параметров на возврат, полигонизацию, рекристаллизацию и фазовые превращения сталей детально описано в работах М.Л. Бернштейна. В табл. 7.1 сопоставлены результаты ВТМО порошковых сталей гомоген ного состава и аналогичных стандартных. Различие в степени деформации