
книги / Новые конструкционные материалы низкоуглеродистые мартенситные и порошковые стали
..pdfЯ. = ХВ( 1 - Ш Л ) , |
(5.11) |
где к - константа данного материала.
Существует также целый ряд зависимостей для вычисления прочно стных характеристик, учитывающих размеры и форму пор, неоднород ность распределения напряжений или предполагающих разрушение по межчастичным перешейкам, при этом только зависимостей экспоненци ального вида получено более 15 [26, 27].
Зарубежные исследователи часто связывают прочность не с общей пористостью, а с коэффициентом формы пор f используя уравнение рег рессии второго порядка [45], а влияние пористости на удлинение описы
вают зависимостями |
|
5 = (1-1,21П 2/3) 3/2( |
(5.12) |
6 = (1 -П )3/2(1 + СП2)1/2, |
(5.13) |
где 5 - относительное изменение удлинения; С - константа, мера чувстви тельности пластичности к концентрации пор.
В структуре порошковых материалов повышено содержание пор, включений метастабильных фаз, способствующих зарождению микротре щин в процессе нагружения. Это приводит к необходимости оценки свойств структурно-неоднородных материалов с помощью критериев ме ханики разрушения, учитывающих роль дефектов. В качестве основного критерия различные литературные источники и нормативные документы рекомендуют коэффициент интенсивности напряжений K\Q (вязкость раз рушения, трещиностойкость).
Этот коэффициент характеризует интенсивность поля напряжений пе ред вершиной трещины независимо от длины трещины и приложенных сил, учитывает способ нагружения, геометрию трещины и показывает, что локальные напряжения о всегда пропорциональны а1/2, где а - длина тре щины. Кроме того, механика разрушения предполагает существование ин дивидуального для каждого материала KQ, по достижении которого тре щина распространяется спонтанно [29, 30].
В широком интервале варьирования пористости для всех исследован ных марок порошкового железа [31, 32, 33, 34, 35] тенденции изменения механических свойств и вязкости разрушения не совпадают, что подтвер ждает недостаточность применения для оценки работоспособности только традиционных характеристик механических свойств. Более того, зависи мость A’ic(n) немонотонна с минимумом в интервале 3,5-8,0 % в зависи мости от размера пор и концентрации примесей.
Расчетное значение вязкости разрушения KQ определяют с учетом геометрии образца:
(5.14)
где b - функция геометрии образца.
Наименьшее из часто встречающихся на практике значений KQ полу чено для случая, когда трещина распространяется под действием напряже ний нормального отрыва. Вид испытаний, при котором трещина под дей ствием напряжений нормального отрыва, и принят за основной, а искомую величину в соответствии с ГОСТ 25.506-85 обозначают К\с. Указанный стандарт определяет условия испытаний и размеры образцов, однако кон кретно для порошковых материалов размеры образцов, гарантирующие корректное проведение эксперимента, могут значительно отличаться от принятых ГОСТом.
Наиболее жесткие требования ГОСТ 25.506-85 и зарубежные стан дарты предъявляют к толщине образцов. Хотя при испытании порошковых материалов толщина образца обычно меньше принятой по ГОСТ мини мально допустимой, другие факторы (отсутствие утяжки кромок и губ сре за, плоский излом ) указывают на достоверность результатов. Так, для же леза повышенной чистоты коэффициент пропорциональности 0 между
|
' Ч |
2 |
|
толщиной и отношением |
составляет 0,3-0,4; для порошковой Ni- |
||
,а 0,2 |
Mo-Cu стали Р = 1 ,6; для высокопластичной нержавеющей стали при по ристости 5 % Р = 0,04; для порошковых никелевых сталей р = 1,4 [33-42]. Поэтому пока не установлены размеры образцов, гарантирующие коррект ное проведение испытаний, достоверность полученных результатов необ ходимо проверять, сопоставляя данные испытаний образцов различных размеров. ГОСТ 25.506-85 рекомендует проводить испытания на образцах различной толщины или диаметра.
Для оценки сопротивления разрушению конструкции по испытанию стандартизированных образцов разработана следующая методика [43, 44]. Экспериментально определяют вязкость разрушения К\с и предел текуче сти <7Т образцов из исследуемого материала. Максимально допустимую ве личину напряжений для данного материала с заданным размером дефекта находят из выражения
|
|
- 1/2 |
О = |
^ С - Ы Л я а с |
(5.15) |
где о - напряжение, действующее перпендикулярно поверхности трещины; Ф - эллиптический интеграл второго рода; ас - критическая глубина тре щины. Полный эллиптический интеграл можно найти из номограмм или
таблиц [43, 44], связывающих длину трещины и отношение oloT. Из выра жения (5.15) следует, что если для конструкционного материала известны К\с и предел текучести Оо,2» то Для любого рабочего напряжения всегда можно определить максимально допустимый размер дефекта а. И наобо рот, по известным К\с, &о,2> а несложно вычислить разрушающее напря жение.
Таким образом, использование наряду с традиционными механиче скими свойствами вязкости разрушения позволяет более полно определить поведение материала в процессе нагружения, т.е. в условиях эксплуатации. Особенно важно знать К\с для материалов, имеющих большое число де фектов - концентраторов напряжений, к таким материалам безусловно от носятся порошковые стали и сплавы.
5.4.Калибрование порошковых деталей
Врезультате калибрования достигаются высокие значения точности размеров и класса шероховатости поверхностей деталей. Кроме того, про исходит упрочнение деформируемого поверхностного слоя деталей.
При калибровании для наружных поверхностей порошковых деталей припуск устанавливают больше, чем для внутренних, особенно в тех слу чаях, когда требуется сохранить поры на поверхности трения. Процесс осу ществляют в специальных пресс-формах, в качестве смазки применяют обычные масла или сухие смазывающие вещества. Оптимальная величина
угла наклона заходной части матрицы и пуансона 1 ,5-2,0°.
Калибрование обеспечивает получение 6—7-го квалитетов точности, 7-го класса шероховатости и выше, упрочняет поверхностный слой изде лий, отличается высокой производительностью и легко поддается автома тизации. При калибровании детали проталкиваются вниз (через прессформу) или выталкиваются вверх.
Значения калибровочных припусков представлены в табл. 5.3.
|
|
|
|
Таблица 5.3 |
|
Калибровочные припуски для обработки наружного диаметра втулки |
|||||
|
|
Калибровочный припуск, |
|||
Материал |
Порис |
% от калибруемого размера |
|||
тость, % |
минимальный |
средний |
максималь |
||
|
|||||
|
|
ный |
|||
|
15 |
0,5 |
|
||
Углероди |
0,8 |
0,8 |
|||
23 |
0,8 |
1,0 |
1,2 |
||
стая сталь |
|||||
30 |
1,0 |
1,2 |
1,5 |
||
|
|||||
Железо |
15 |
0,6 |
0,8 |
0,9 |
|
23 |
0,9 |
1,2 |
1,3 |
||
___________, |
30 |
1,2 |
______ 1Л______ _____ 1А_____ |
После калибровки следует термическая обработка. Упрочняющая термическая обработка порошковых сталей эффективна только при их от носительно невысокой пористости.
5.5. Термическая обработка порошковых сталей
Термическая обработка является эффективным методом улучшения физико-механических, технологических и некоторых других свойств по рошковых сталей.
Основные закономерности термической обработки порошковых мате риалов, процессы, протекающие при их нагреве и охлаждении, такие же, как и закономерности обработки компактных материалов. Однако из-за пористости, неоднородности структуры требуется корректировка, а в ряде случаев и изменение режимов, условий и приемов термической обработки спеченных сталей.
Наиболее часто применяются такие виды термической обработки по рошковых сталей, как закалка, отпуск, отжиг и нормализация.
Закалка. Для большинства компактных сталей температура закалки устанавливается на диаграмме состояния железоуглеродистых сплавов по критическим точкам Лс\ и Асу Положение критических точек порошковых сталей определяет не только химический составом, но и пористость, гомо генность структуры. Поэтому при отсутствии справочных данных для пра вильного выбора температуры закалки необходимо в каждом отдельном случае находить критические точки или устанавливать температуру по ре зультатам экспериментов. Оптимальная температура нагрева порошковых сталей под закалку, как правило, значительно выше температуры нагрева компактных материалов (табл. 5.4).
Таблица 5.4 Критические точки и оптимальные температуры закалки спеченных сталей
Марка стали |
Ас1 |
Асз |
Температура закалки |
Твердость, |
|
|
к |
HRC |
|
|
|
|
||
ПА-ЖГр1 |
988 |
1028 |
1113 |
56-60 |
ПА-ЖГр1Х2 |
1025 |
1059 |
1113 |
55-58 |
ПА-ЖГр1М2 |
1003 |
1036 |
1113 |
52-55 |
ПА-ЖГр1Х2М2 |
1033 |
1068 |
1133 |
48-52 |
ПА-ЖГр1Х5М5 |
1060 |
1153 |
1183 |
41-45 |
ПА-ЖГр1Х5М10 |
1073 |
1153 |
1193 |
38-45 |
ПА-ЖГр1Х12М2 |
1080 |
1156 |
1243 |
34-40 |
Как видно из табл. 5.5, при увеличении содержания легирующих эле ментов твердость сталей снижается, что обусловливается уменьшением ко личества углерода в твердом растворе.
Таблица 5.5 Содержание углерода в твердом растворе закаленных сталей
Марка стали |
Количество |
Марка стали |
Количество |
|
углерода, % |
углерода, % |
|||
ПА-ЖГр1 |
|
|||
0,77 |
ЖГр1Х5М5 |
0,36 |
||
ПА-ЖГр1Х2 |
0,74 |
|||
ЖГр1Х5М10 |
0,27 |
|||
ПА-ЖГр1М2 |
0,66 |
|||
ЖГр1Х12М2 |
0,28 |
|||
ПА-ЖГр 1Х2М2 |
0,68 |
|||
|
|
В связи с повышением температуры закалки порошковых сталей воз растает количество остаточного аустенита, который становится более од нородным и устойчивым.
Для уменьшения количества аустенита производится обработка холо дом в течение 0,5-1,5 ч непосредственно после закалки. Обрабатываются изделия из высокоуглеродистых и легированных сталей (табл. 5.6). Однако обработка холодом, несмотря на уменьшение количества остаточного ау стенита, не приводит к повышению твердости. Твердость материалов после обработки остается несколько ниже твердости беспористых сталей после закалки с оптимальных температур.
Таблица 5.6 Влияние обработки холодом на твердость и структуру порошковых сталей
|
Твердость, HRC |
Количество аустенита, % |
|||||||
|
|
при продолжитель |
|
при продолжи |
|||||
|
|
|
тельности обра |
||||||
Марка стали |
после |
ности обработки |
после |
||||||
ботки холодом, |
|||||||||
спека |
холодом, х 10 3 с |
спека |
|||||||
|
|
х 10 3с |
|
||||||
|
ния |
|
|
|
ния |
|
|
||
|
|
|
|
|
|
|
|||
|
|
1,8 |
3,6 |
5,4 |
|
1,8 |
3,6 |
5,4 |
|
ПА-ЖГр1Х5М5 |
33-40 |
36-45 41-45 40-45 |
35 |
27 |
24 |
14 |
|||
ПА-ЖГр1Х5М10 |
37-40 |
37-45 |
38-45 |
43-46 |
38 |
15 |
12 |
8 |
Продолжительность нагрева порошковых сталей, как и компактных, зависит от размеров изделий и скорости превращений аустенита в нагре том металле.
Нагрев спеченных сталей под закалку сопровождается их обезуглеро живанием и окислением, поэтому его рекомендуется производить в защит ной среде, в качестве которой используют инертные и восстановительные атмосферы (азот, аргон, эндогаз и др.), углеродсодержащие засыпки (дре весный уголь, графит и т.д.). Использование защитной атмосферы при на
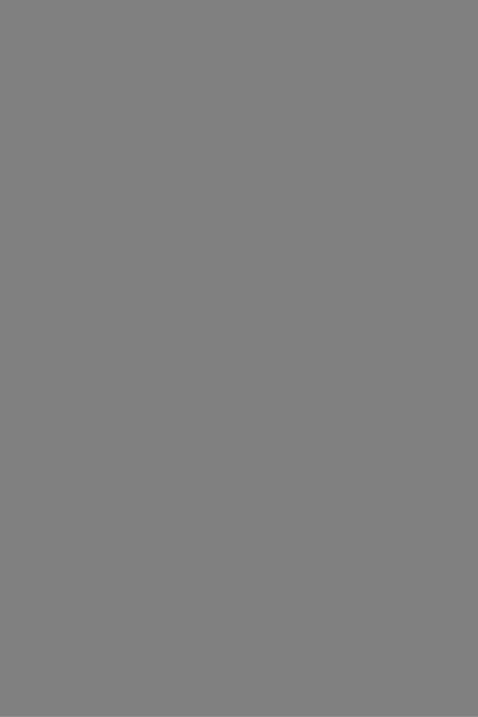
которая почта всегда ниже, чем у компактных сталей аналогичного хими ческого состава. Например, твердость HRC закаленных образцов из по рошковой стали У8 с пористостью 13 % составляет 48-52, из компактной кованной стали У8 - 61-63.
Однако основной причиной понижения твердости и прочности по ме ре роста пористости закаленных сталей является ускорение распада пере охлажденного аустенита, так как резко увеличивается удельная поверх ность; кроме того, при одинаковой пористости мелкие поры в большей степени ускоряют перлитное и бейнитное превращение, чем крупные [45, 46,47, 48].
В качестве закалочных сред при закалке порошковых сталей приме няют воду, водные растворы солей, масло и т.д. Пористость спеченных ма териалов приводит к снижению скорости их охлаждения в жидких средах, что необходимо учитывать при проведении закалки. Масло как закалоч ную среду рекомендуют для закалки мелких деталей, изготовленных из ле гированных сталей, имеющих низкую критическую скорость закаливания. Закалку железоуглеродистых порошковых сталей нужно производить в во де, причем наиболее высокая твердость материалов обеспечивается при интенсивном перемешивании воды. На поверхности спеченных образцов образуется мартенситно-бейнитная структура, которая переходит в трооститную, а затем в сорбитную. Однако уже при закалке в масле сталей с пористостью 10—15 % при тщательном микроскопическом исследовании их в структуре обнаруживают микротрещины [45], поэтому закалке в жид ких средах следует подвергать железоуглеродистые детали плотностью не ниже 7,2-7,4 г/см3. Величина пористости, с которой возможно применение закалки, определяется скоростью охлаждения: чем больше скорость охла ждения, тем выше минимальная плотность, позволяющая успешно закали вать сталь.
Индукционный нагрев (табл. 5.7) может быть рекомендован лишь для деталей плотностью 7,2-7,4 г/см3, но требования к скорости охлаждения принципиально не изменяются, более того, вероятность образования зака лочных трещин возрастает.
|
|
Таблица 5.7 |
Влияние параметров индукционного нагрева на твердость стали |
||
Скорость нагрева, К/с |
Температура, К |
Твердость, HRC |
353 |
1260 |
48 |
513 |
1300 |
48 |
823 |
1340 |
50 |
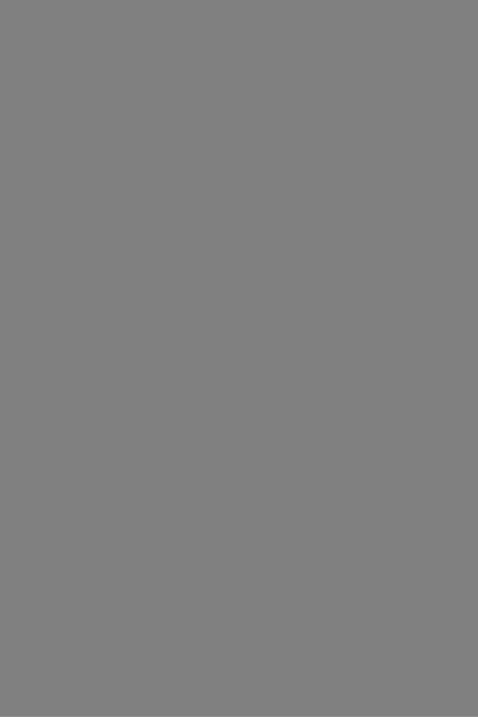
графитовых композиций подвергают изотермическому спеканию в защит ной атмосфере при температуре 1395-1455 К в течение 1 ч, затем охлаж дают в масле или воде и отпускают. В зависимости от назначения деталей и предъявляемых к ним требований отпуск производят в интервале темпе ратур от 475 до 975 К 1,5-2,0 ч. Это позволяет получить изделия с задан ным комплексом свойств. Структура зернистого перлита соответствует от пуску при температуре 925-975 К. Структура материала изделий однород ная, мелкозернистая, твердость НВ 760-850 МПа, предел прочности около 350 МПа.
Отпуск. Эта операция является обязательной, она формирует требуе мую структуру порошковых сталей. Так же, как у конструкционных низ колегированных сталей, его проводят после закалки, но оптимальные тем пературы отпуска традиционных сталей и пористых порошковых не совпа дают. В результате отпуска механические свойства порошковых сталей изменяются немонотонно (табл. 5.8).
Таблица 5.8
Влияние температуры отпуска на механические свойства стали ПА-ЖГр1
Плотность, |
Темпера |
Предел прочности |
Предел проч |
|
|
ности при из |
Твердость НВ |
||||
г/см3 |
тура от |
при растяжении |
гибе |
|
|
пуска, °С |
|
|
|||
|
|
МПа |
|
||
|
|
|
|
||
|
475 |
347 |
272 |
3210 |
|
6,43 |
575 |
357 |
44,2 |
2370 |
|
675 |
450 |
798 |
1920 |
||
|
|||||
|
775 |
423 |
668 |
1570 |
|
|
475 |
310 |
477 |
3290 |
|
6,45 |
575 |
369 |
492 |
2170 |
|
675 |
498 |
733 |
1680 |
||
|
|||||
|
775 |
382 |
700 |
1600 |
|
|
475 |
343 |
605 |
2440 |
|
6,47 |
575 |
422 |
709 |
210 0 |
|
675 |
498 |
715 |
1970 |
||
|
|||||
|
775 |
388 |
652 |
1570 |
Примечание: температура закалки 1145 К, выдержка 5 мин, охлаждение в воде.
Характер изменения твердости и ударной вязкости порошковых ста лей аналогичен характеру изменения этих характеристик компактных ста лей. Твердость и ударная вязкость у высоколегированных порошковых
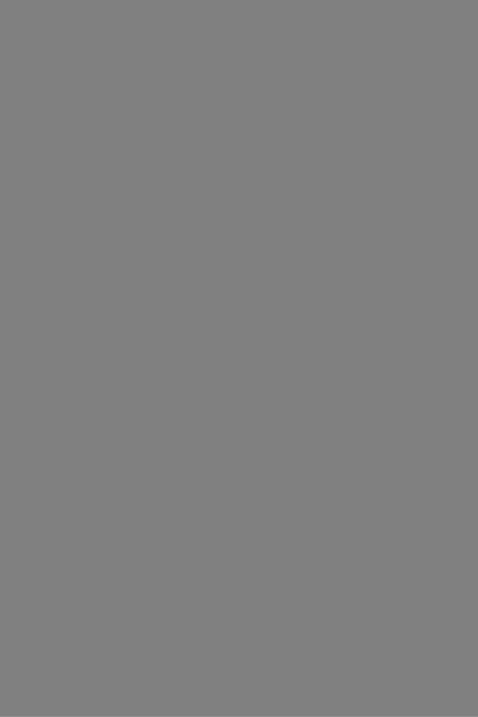